
1 minute read
Darting Anthropomorphic Plywood
ACADEMIC | ARC381
TECHNOLOGY STUDIO IV
Advertisement
Instructor: Tom Bessai
Studio Partner: Afsah Ali
April 2019
In this studio, we were challenged to create deployable architecture using various techniques of bending plywood. My partner and I combined the geometry of Lawrence Lek’s work and the darting techniques of “fabricwood,” developed by PRODUCE Workshop for Herman Miller as the main techniques of fabrication into our concept.
We decided to create a meditation pavilion atop a mountain whose form was generated through a series of Rorschach tests and built with modules using darted geometries akin to Lek’s. Our triangular modules were created parametrically and are assembled with zip-ties in a way that allows for complete modules to be easy to transport to the site.
It induces the sense of touch through the atypical bending of plywood caused by the darting technique and the uncut zip ties at the nodes where multiple modules connect to each other.
“Kangaroo,” a Grasshopper plug-in, and 3-D scanning were used to develop a threedimensional model of our pavilion. CNC-milling was used to carve the mountainous landscape that the pavilion rests upon. A 1:1 component of the pavilion was made to test if the fabrication methods were translatable at larger scales.
There are four modules used in our design: a small triangle, a medium triangle, a big triangle, and an anthropomorphic module we nicknamed as the “alien.” For each “lung” there are 2 small triangles, 4 medium triangles, 3 big triangles, and 6 aliens. After learning that the wood grain was affecting how the module was skewing the bending, we broke the modules into 3-4 pieces so that the grain would be parallel to the bending direction. As the width of the triangles increases, the interior darting angles increases by 5°. Once darted and assembled, the modules become anthropomorphic, looming over viewers.
Between the modules is a translucent stretchy fabric that is gradually layered to create a notion of privacy the further north one travels, before they arrive at the lookout point over the mountain. The image on the left of one of our initial models best demonstrates the effect of the layered fabric inside the pavilion.
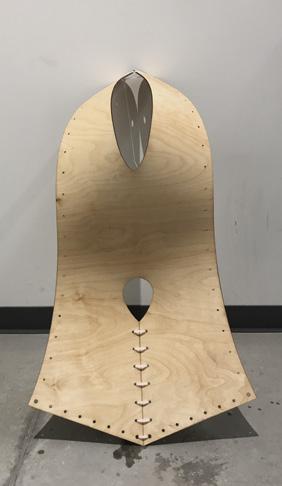
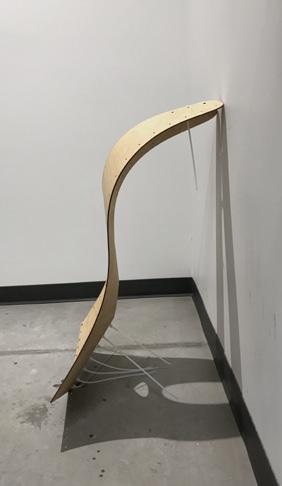
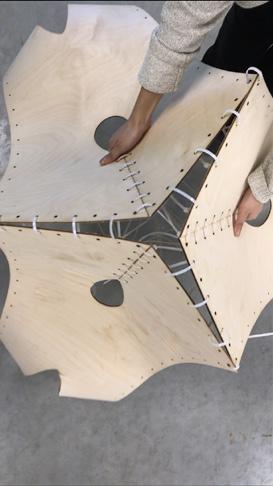
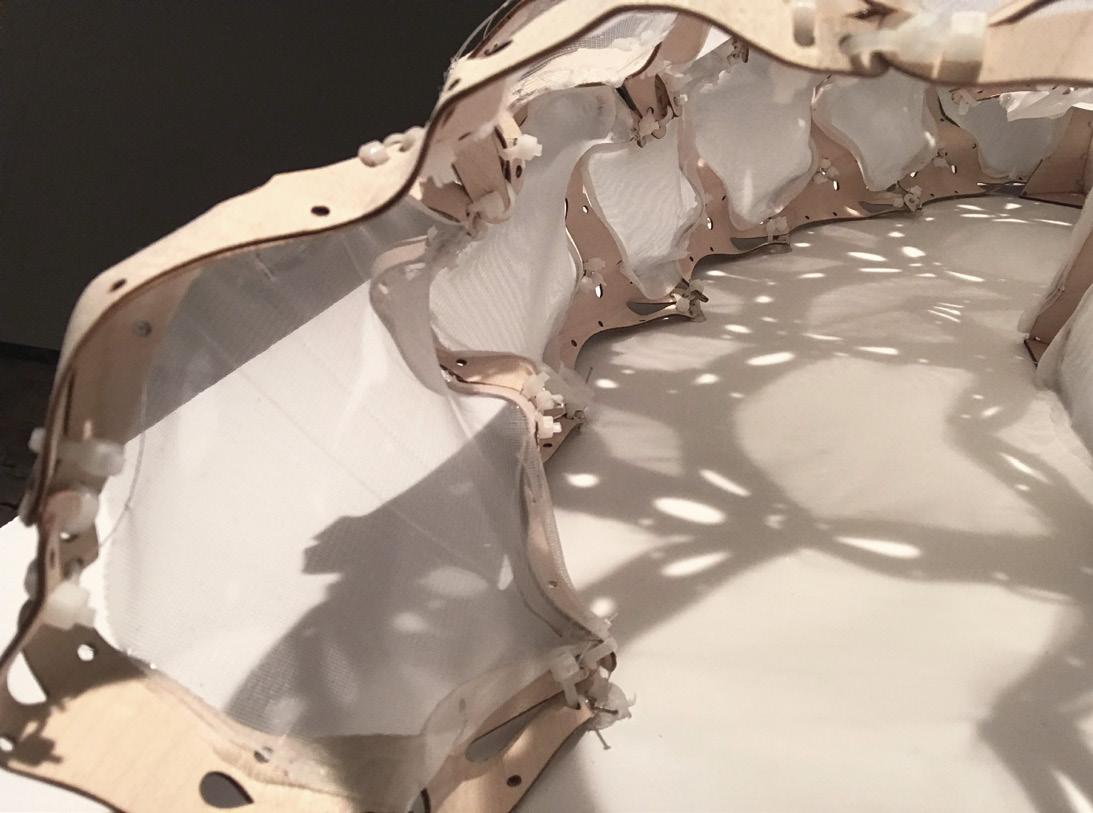
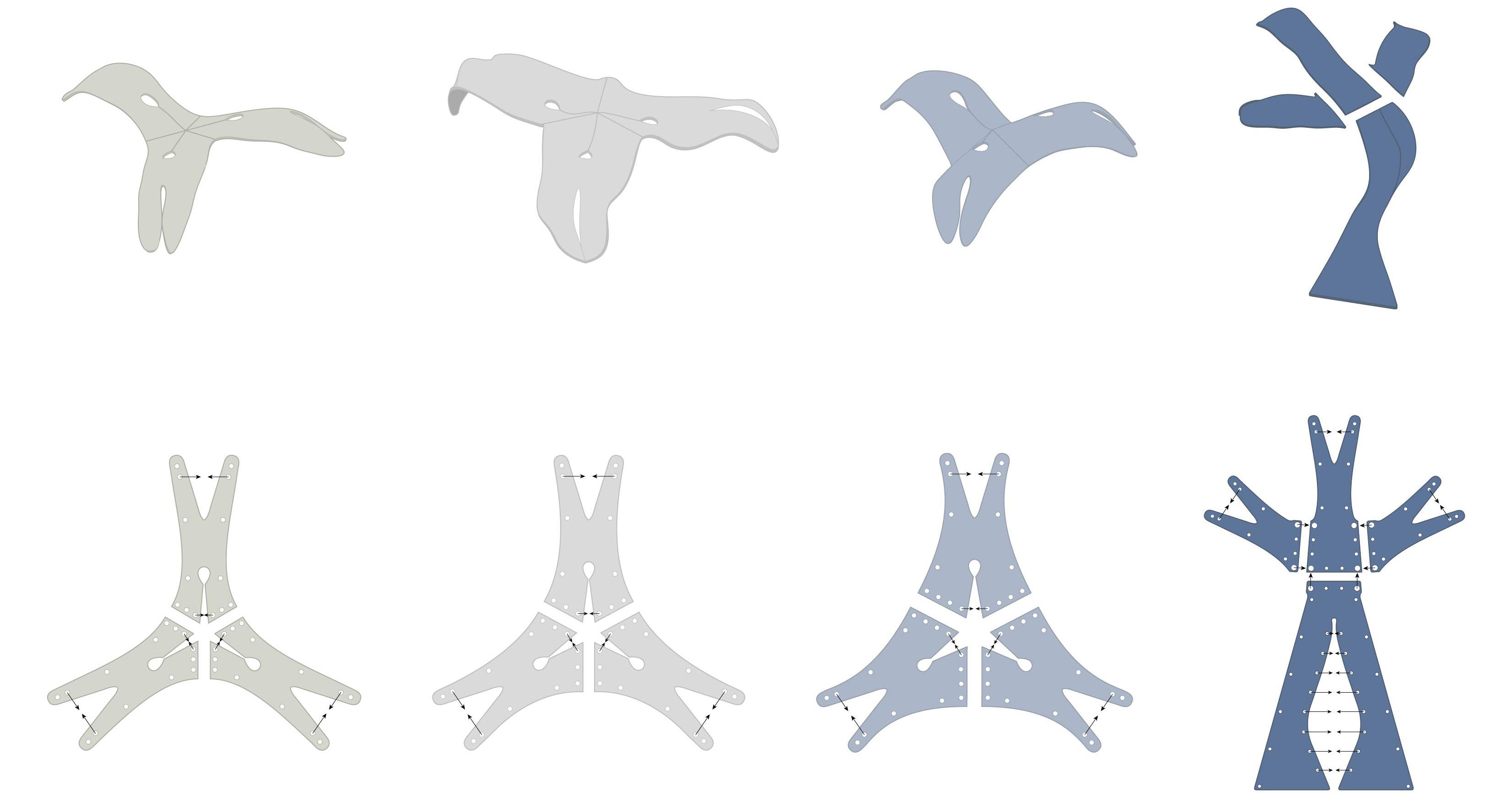
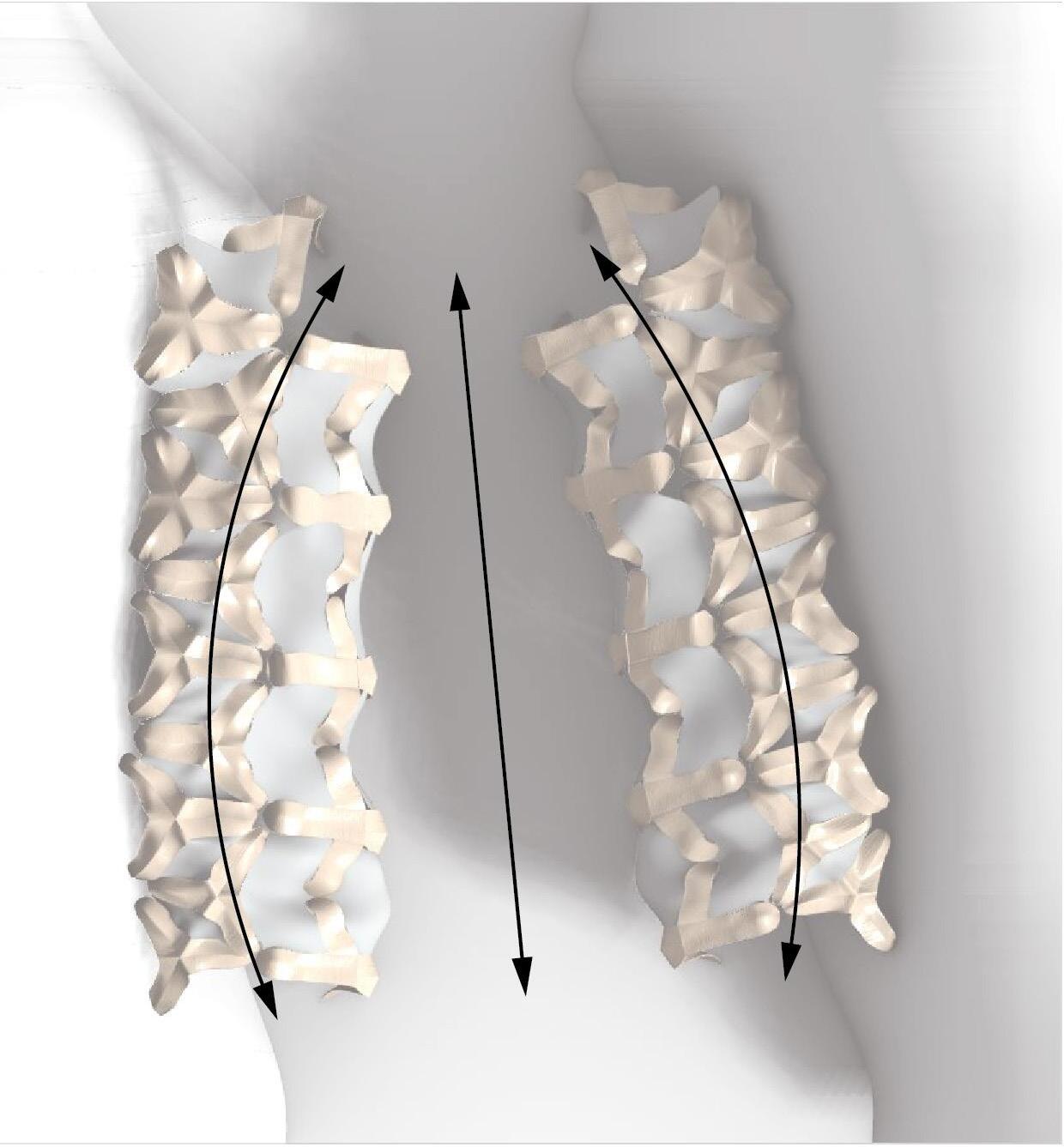
Each piece of the module is first soaked in warm water for 10-15 minutes before zip-tying Then the 3-4 pieces are loosely zip-tied to make the module collapsible for transport. Once on-site, the zip-ties can be tightened.
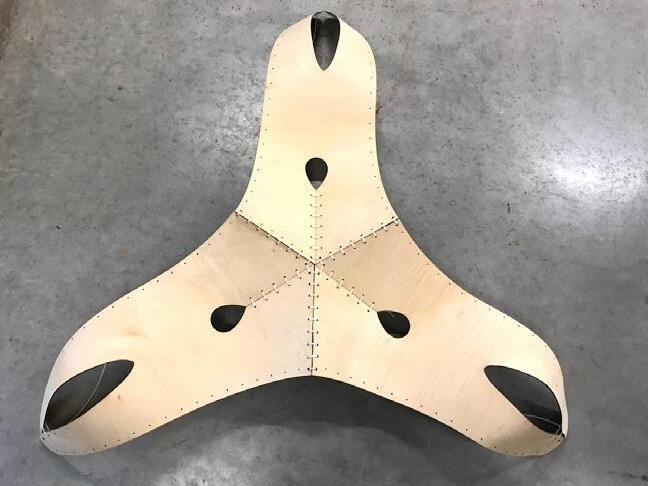
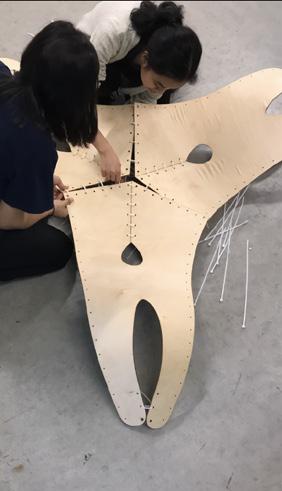
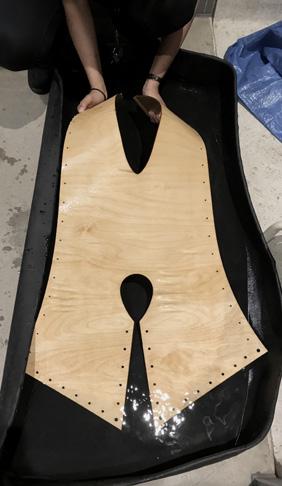