CFPR STAFF CAREER STORIES 0.5
Mike White
TECHNICAL SPECIALIST IN FABRICATION
Mike White joined the Centre For Print Research (CFPR) in 2021. He applied to work here because he had attended an open day and was excited by the multi-disciplinary work being undertaken, the creative environment, and he was looking for job stability.
After completing his degree in Product Design at UWE in 2017, Mike worked in the technical facilitation team at UWE’s Bower Ashton campus. He also spent four years co-running a design and fabrication company that provided services to businesses such as Oracle, Penguin Random House, Disney, Hodder & Stoughton, and Zubr VR.
During his time at the CFPR he has collaborated with numerous companies and individuals on prototyping projects including:
A&R House, with Associate Professor David Huson, redesigning an elevator bucket to form a stronger food grade bucket.
Sculptor Peter Randall-Page, with Associate Professor Tavs Jorgensen, proving the concept for a novel workflow for calculating angle and position for slicing large stone boulders.
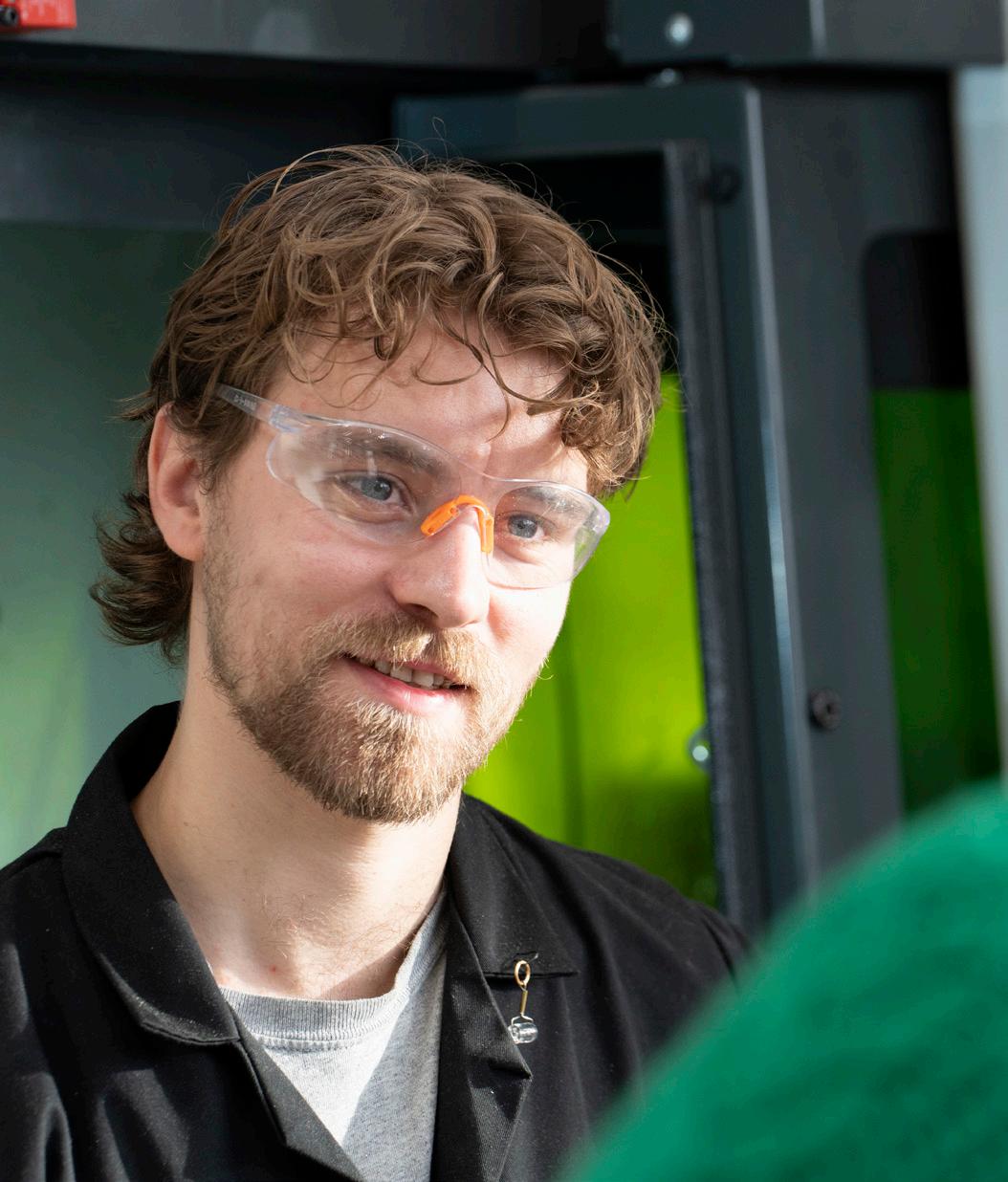
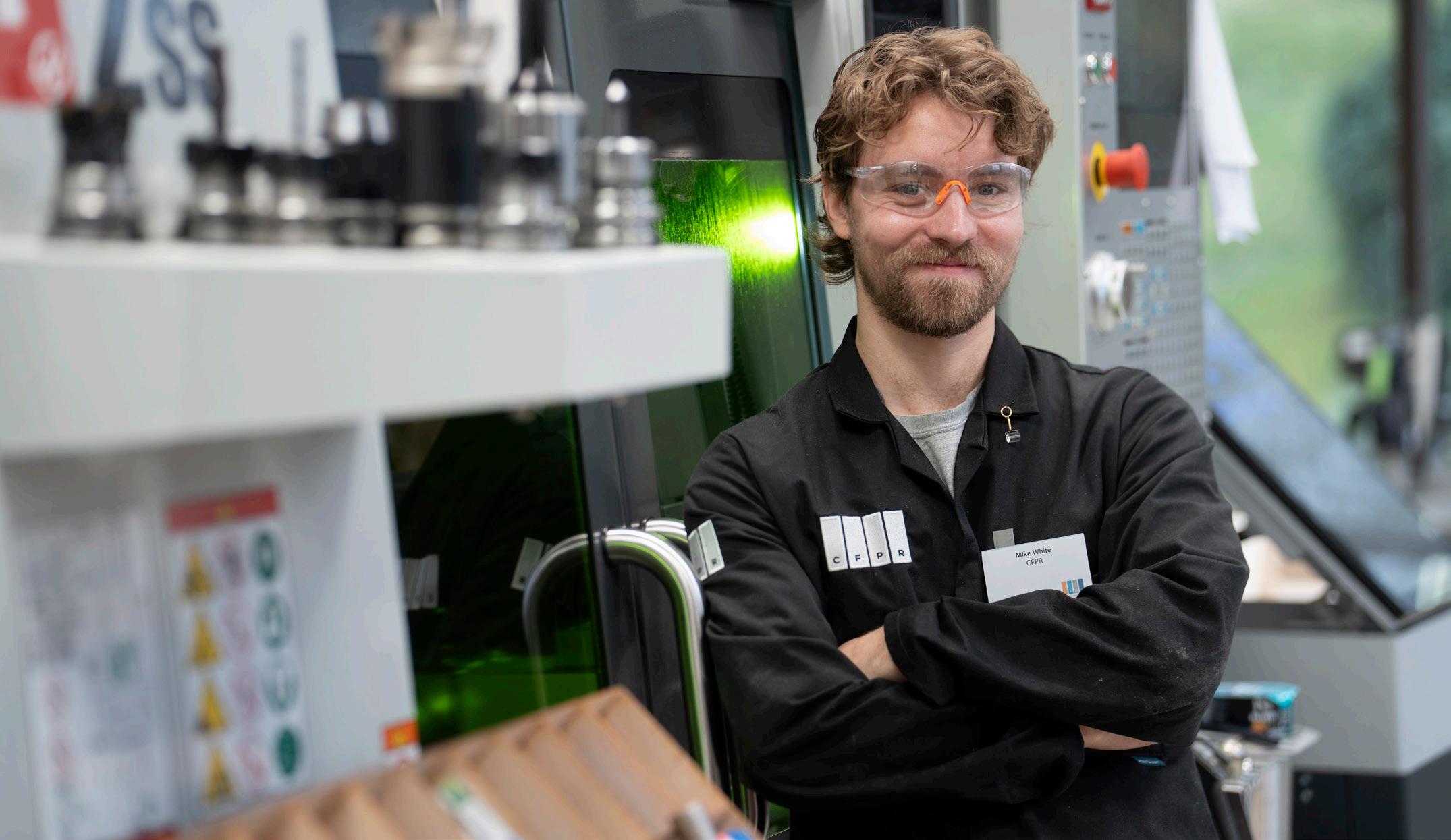
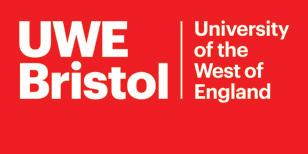
Bristol Nano Dynamics, developing a working prototype for a sample holder allowing a microscope to be more user-friendly and robust.
Disruptive Prototyping Limited with Associate Professor David Huson, testing materials for 3D printing a self-levelling seat for a 3-wheel mobility scooter.
True to Nature, with Associate Professor Fabio D’Agnano, designing and printing a 3D filter mount for drone filters.
CFPR Artists-in-Residence, fabricating new editions and the pop-up exhibition ‘Cabinet of Curiosities’, which has toured to Woolwich Contemporary Print Fair, Lancaster University and schools in the Bristol area.
Most recently, Mike has been working with Professor Carinna Parraman and the company Books and Pieces on baby safe inks for printing onto plasticsbased papers. And he is collaborating with Associate Professor Tavs Jorgensen and the brick company Ibstock on an Accelerated Knowledge Transfer project funded by Innovate UK developing a zero waste process using bio plastics for die making which can be recycled back into filament.
Mike’s skills include general fabrication, laser cutting, scanning, carpentry, joinery, metal fabrication, mouldmaking and casting, upholstery, electronics and 3D modelling. Whilst at the CFPR, he has extended his skills and knowledge in areas which include writing G-code for rapid iteration of ceramic paste augers, 5-axis computer controlled numeric machining, 3D printing in metal deposition, and design algorithms such as Grasshopper for integration into workflow. He has also written a professional development course, aimed at users who have little to no experience of digital manufacturing.
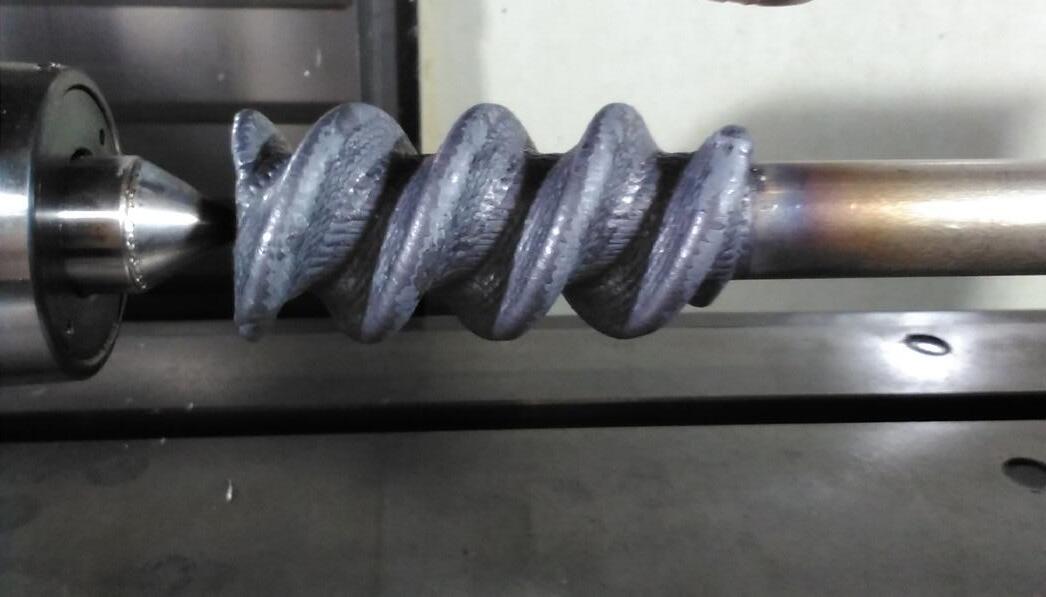
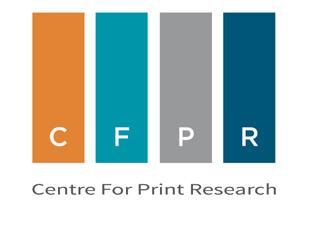
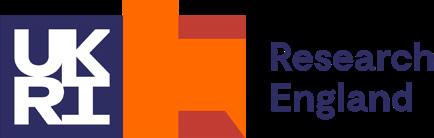
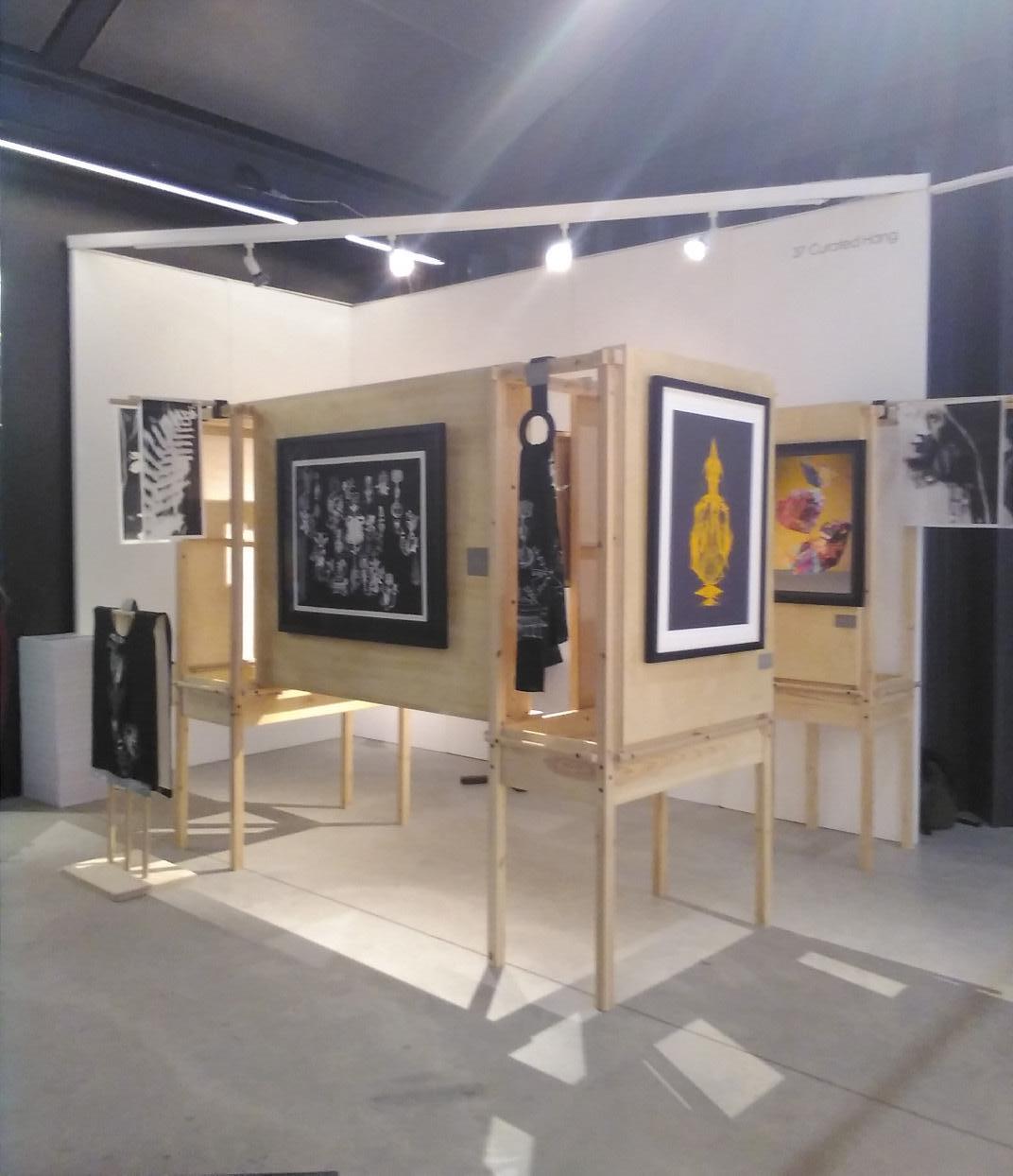
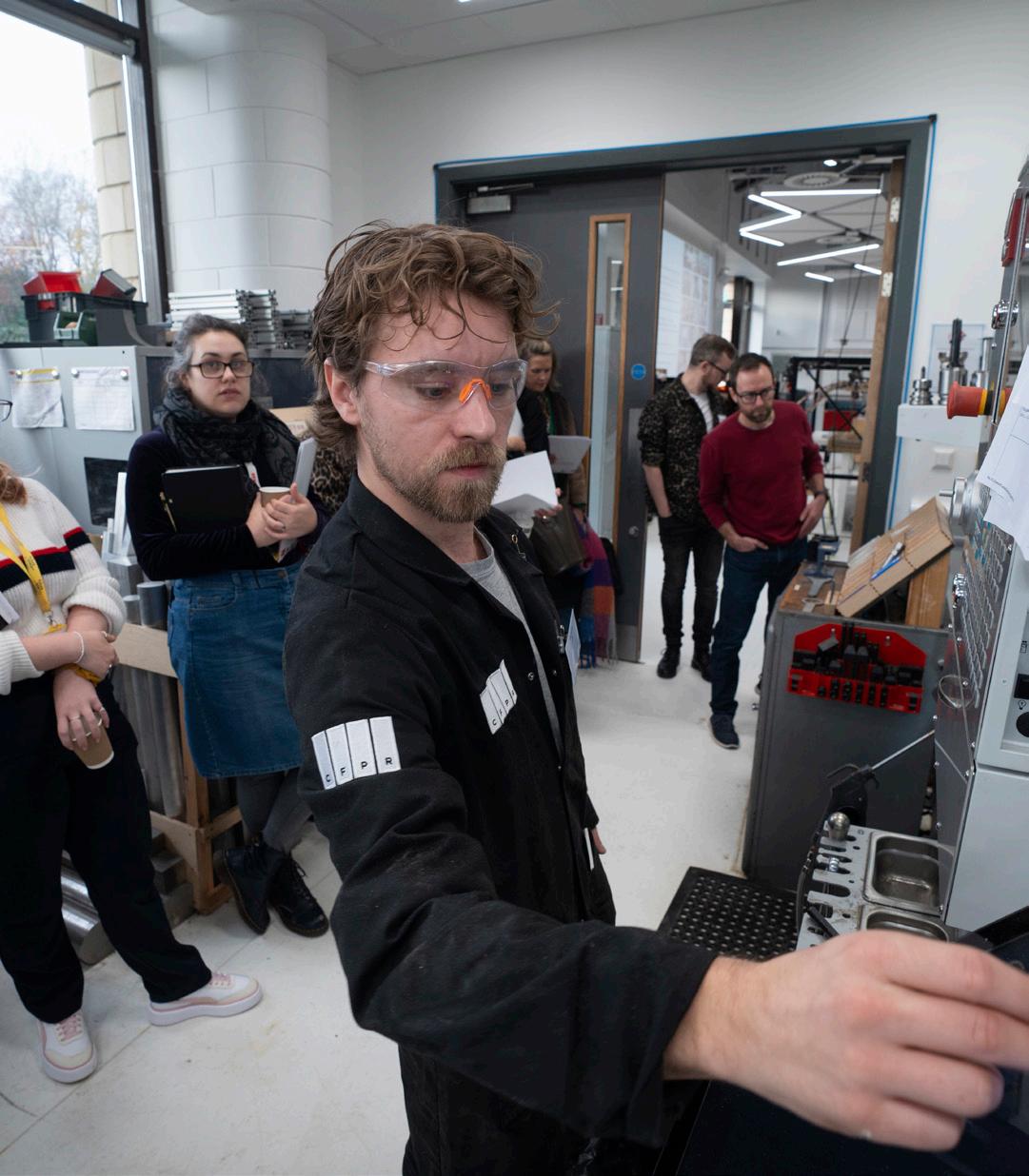