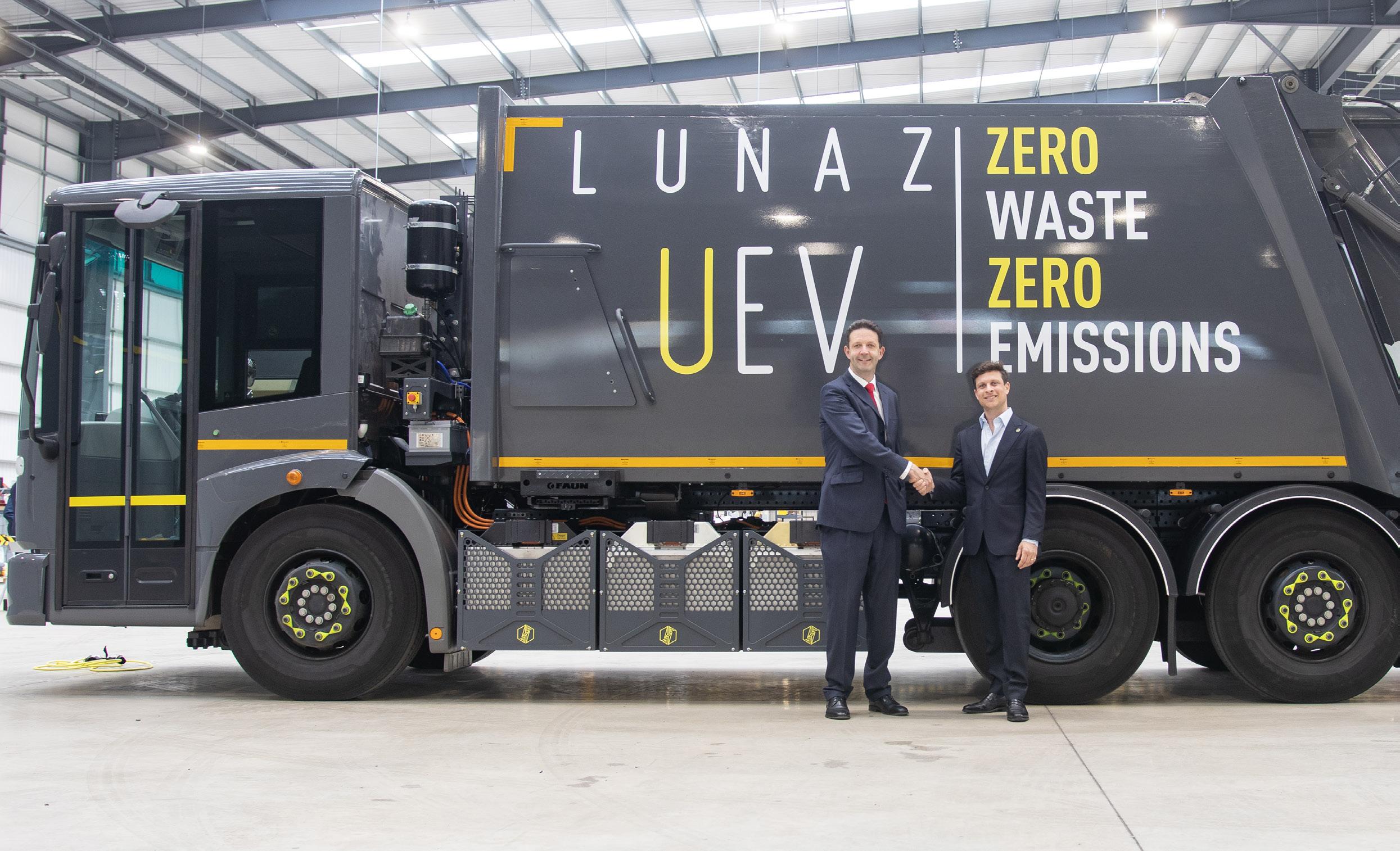
9 minute read
Lunaz confirms local government fleet electrification programme with Buckinghamshire Council
Lunaz is delighted to announce the next phase in a landmark fleet electrification partnership with Buckinghamshire Council. Following the conclusion of a competitive tendering process, Lunaz has committed to the first phase of upcycling and electrification of a municipal refuse fleet.
This follows the signing of a Fleet Electrification Agreement at a COP Event hosted at the company’s Silverstone HQ. This started a programme of detailed technical and economic assessment, which enabled them to assemble a highly credible proposal for the competitive tendering process leading to confirmation of the first order.
The first Buckinghamshire bin lorry to become fully electric will begin its up-cycling and electrification process as part of the pioneering partnership between Buckinghamshire Council and Silverstone-based, clean-tech company Lunaz.
The 26-t refuse vehicle will be converted from its existing diesel power to electric, with delivery to be made in the autumn. The work is being funded with a grant from DEFRA (Department for Environment, Food and Rural Affairs).
All Lunaz vehicles are completely stripped down and all components inspected, up-cycled and replaced as required. This includes the removal of the current diesel engine and replacing it with a fully electric drivetrain. The cab, driver functions and bin-lift equipment will also be fully refurbished and upgraded to latest technological and safety standards.
This week, Gareth Williams, Buckinghamshire Council’s Cabinet Member for Climate Change and Environment oversaw the delivery of the first diesel refuse vehicle to the team at Lunaz’ HQ on the Silverstone Technology Park. He said: “This is a very exciting moment for Buckinghamshire Council and a big milestone in our journey to cutting our carbon emissions and meeting our climate change strategy ambitions.
“It marks the first step in our desire to run a more sustainable fleet of vehicles by using a renewable energy source and has multiple additional benefits including improving air quality and saving money both in terms of cheaper everyday running costs, and the retention of more than 80% of the embedded carbon versus scrapping an existing vehicle and replacing with new. In this regard, our partnership with Lunaz represents the best possible outcome for both the planet and the taxpayer. It also reflects our commitment as a council, to supporting local business and employment in the area.”
This announcement follows the signing in April 2023 of a seven-year fleet electrification programme between Biffa, the UK’s leading sustainable waste management company and Lunaz confirming a commitment to allocating a significant proportion of its 1,110 vehicle per year production capacity.

Better for the planet, better for the taxpayer
For UK councils, the procurement of these vehicles represents a dramatic saving for the taxpayer, with more than £1m in public money saved for every 20 vehicles upcycled and electrified versus buying new EV equivalents.
The British economy further benefits as Lunaz is pioneering growth in circular practices at a critical time by supporting more than 300 jobs and a new green capability.
Every up-cycled electric vehicle produced by Lunaz saves 82% of the embedded carbon within that vehicle. For context, at full capacity, Lunaz’ factory in Silverstone, UK, will save the equivalent weight of the Eiffel Tower every year in embedded carbon by upcycling rather than scrapping existing fleet vehicles.
Furthermore, Lunaz stands alone in subtracting a polluting vehicle from the global car park with every vehicle it electrifies. This is through its one for one policy, which ensures the decommissioning of every fossil fuel engine before recycling its components. This practice ensures existing polluting engines are completely eradicated and replaced with clean-air equivalents.
The Waste Management industry is at the frontline of a critical requirement to reduce carbon emissions from road logistics. According to a report by the World Economic Forum: “For the industry to limit temperature increases to no more than 1.5 degrees centigrade, twothirds of trucks sold this decade must be zero-emissions.”
However, this must not come at the cost of scrapping millions of perfectly serviceable vehicles, in doing so increasing the carbon burden in waste and the manufacturing process. The Lunaz approach, in line with the principles of the circular economy, answers this and also creates major economic benefits.
A Lunaz UEV represents a significant Total Cost of Ownership (TCO) saving versus either existing diesel equivalents or new EVs. This accelerates the adoption of clean air vehicles by creating a more economically viable route to fleet transition.
Lunaz investor, David Beckham said: “This is a strong endorsement of Lunaz’ innovative approach to finding sustainable solutions and I’m delighted to be an investor in this fast growing and exciting British company.”
Designed from the ground up for waste management
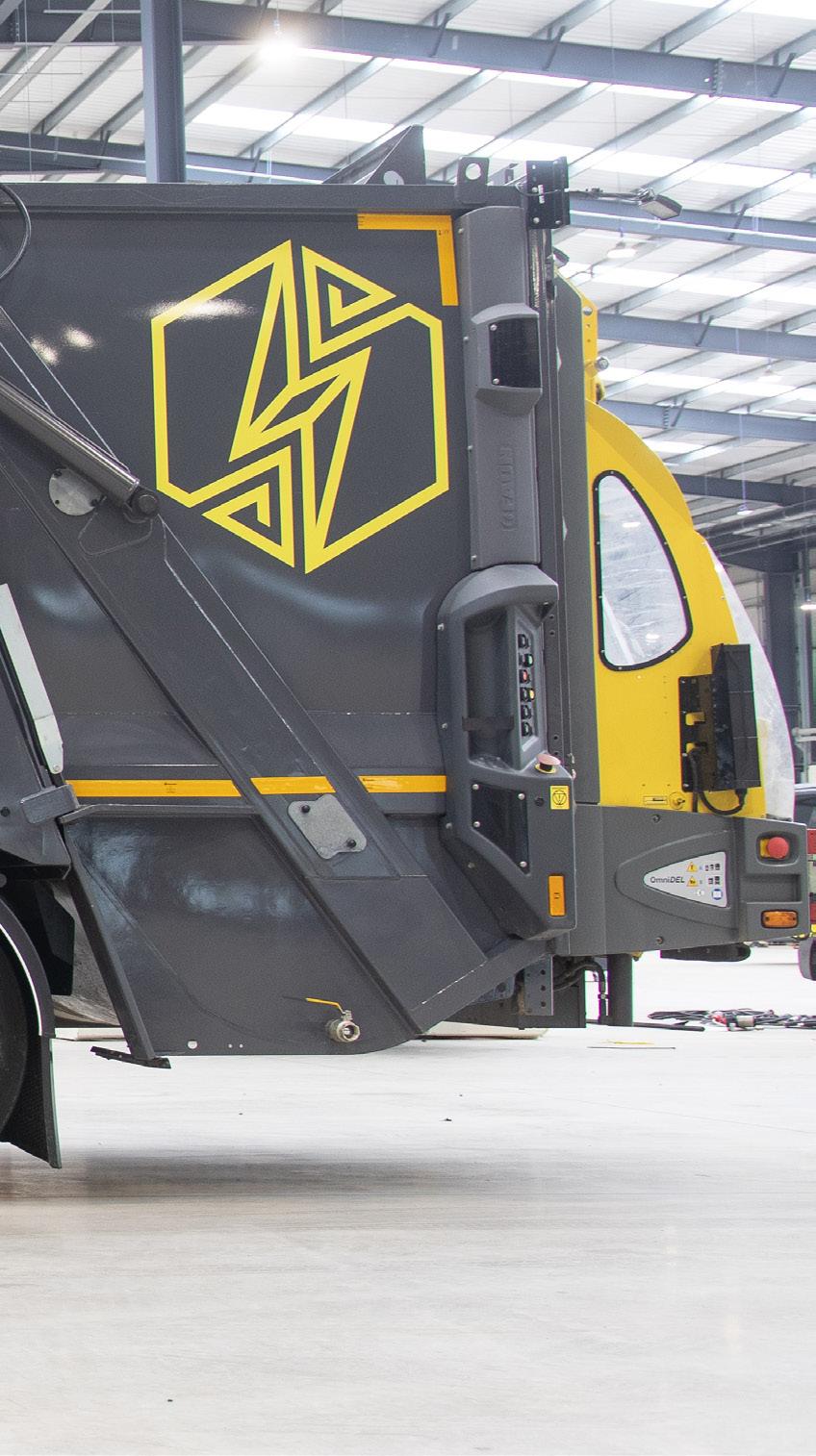
Each UEV by Lunaz has been designed based on primary research in the field, dramatically improving the carbon impact of these vehicles and contributing to quieter and cleaner communities in which they operate.
The upcycling process also creates significant functional and operational advantages. Lunaz’ 150 specialist engineers are developing key modifications exactly tailored for each local authority’s user requirements.
This includes the ability to tailor the size of the powertrain to a specific route profile, enabled by the Lunaz modular proprietary powertrain. This means for shorter, more urban routes, the user is not burdened with the extra cost and weight of an overspecified battery pack.
Critical enhancements to the cabin augment significant safety improvements.
This includes the use of 360° cameras with person and cyclist detection and the relocation of the handbrake to ensure drivers never need to take their hands off the wheel.
The camera monitoring system also dramatically improves driver awareness. Two assemblies containing three cameras are mounted on the top corners of the UEV, feeding digitised rear-view mirrors.
The screens also feature object detection, highlighting cyclists, pedestrians and potential hazards to the driver. Unlike standard mirrors, these operate under all conditions, including rain, snow and total darkness, dramatically increasing safety.
Lunaz UEV refuse trucks have been developed following live operator feedback with Lunaz engineers frequently taking part in refuse truck rounds to ensure an intimate understanding of frontline requirements. Critical enhancement to driver comfort and operation have been included, ensuring crews feel the benefit of the latest technology and innovations.
Every UEV by Lunaz undergoes an exhaustive process of remanufacturing, re-engineering and electrification. This takes place at the company’s state-of-the art upcycling and electrification campus on the Silverstone Technology Park. This will support more than 300 highly skilled jobs by 2025.

Flannery’s Cat Vision Personnel Detection product development trial proves successful
Finning UK & Ireland, the world’s largest dealer of Cat machines and equipment, has teamed up with one of the UK’s largest plant hire companies to reduce construction fatalities and injuries by trialling a smart detection system capable of alerting operators if someone is too close to their machine.

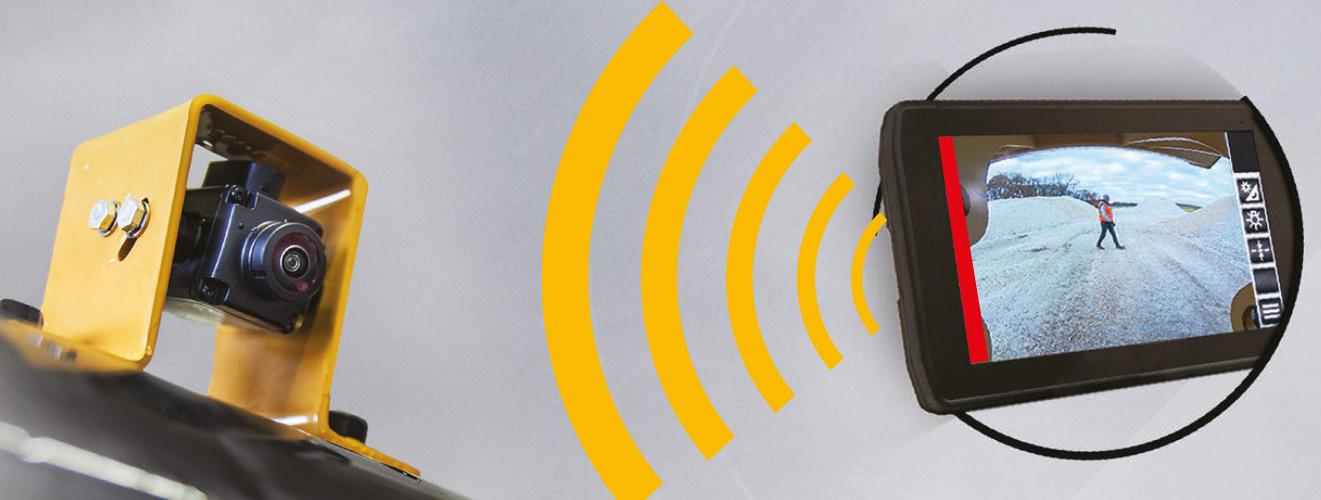
Flannery Plant Hire has completed a two-year product development trial of Cat Personnel Detection, the latest system to be launched from the Cat Vision range. The system reduces the risk of injury to ground personnel working around machinery by alerting an operator dynamically based on the person’s proximity to the machine.
The product development trial involved the smart camera system being fitted to eight of their machines which were a mixture of excavators and dozers involved in work on HS2 sites, with feedback being collated by the team at Finning and forwarded to the product team at Cat to support its further development.
Patrick Flannery, Director at Flannery Plant Hire, said: “We were delighted to be approached by Cat to be a testbed for this new product thanks to our relationship with Finning. Keeping people safe on and around sites where our machines are working is something we factor into every company decision.
“Health and safety first is an approach that everyone at Flannery Plant Hire is expected to take. So any product innovation which helps our employees and our client base to do this effectively is something we always consider seriously.
“We found the Cat Vision Personnel Detect system to be a robust piece of kit which has clearly been manufactured to a high standard, and smart detection systems like this are likely to become standard soon so are something our sector will have to invest in.”
The system, which can be installed on most medium-size machines including non-Cat wheel loaders, graders, tractors, and track loaders, includes a single rear facing camera together with a 10-inch high resolution touchscreen display with smart detection.
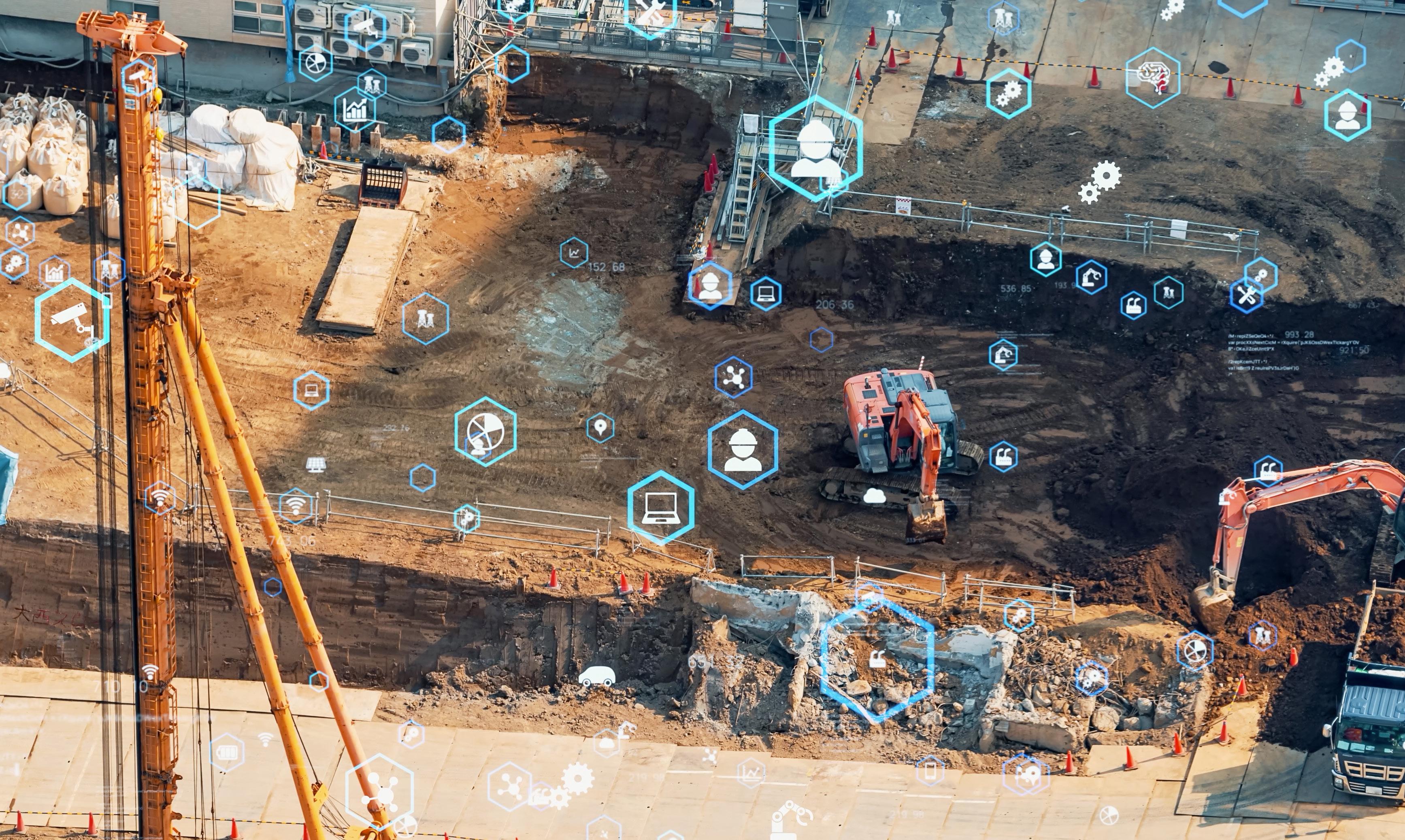
It allows an operator to zoom in and has a 170-degree field of vision with target areas set at 20, 10 and 5 m, which relate to three colour zones. Yellow is low risk so while the system will detect the person there is no audible alert, but if they step closer into the Orange zone this triggers an intermittent alarm, then there is a nonstop solid alarm for someone detected in the Red zone.
Chris Phillips, product manager and quality engineer for Finning, said: “While many machines come with cab cameras fitted, where Cat Personnel Detection differs is that it can specifically identify people from objects and will trigger an operator response because it sounds either an intermittent or solid alarm depending on how close they are to the machine.
“The system creates a boundary box around the person making them easy to spot, but if they step out of the field of view of the screen the system can still detect them and will give the operator a red or orange bar or ‘bumper’ on-screen depending on how close they are.
“It can be physically fitted to machines with a minimum height of 1.75 m, up to maximum of 3.5 m, so is suitable for typically mid-range machines. There are plans to expand it to a greater range of machines in the future, including articulated trucks. The algorithm and the capability of the system is also being developed so it will be able to offer recording capability as well.”
Doosan Construction Equipment is now

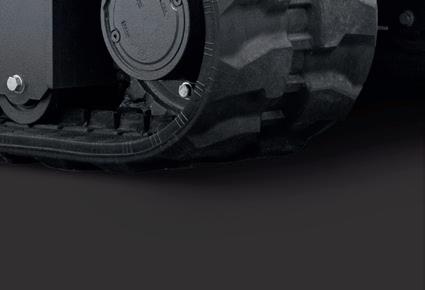

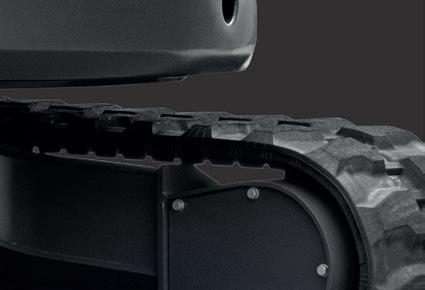

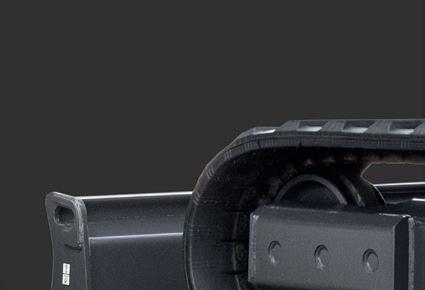
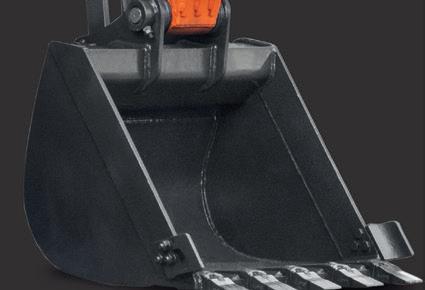
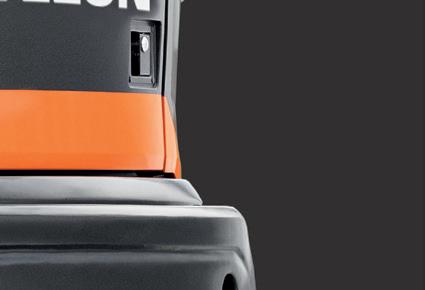
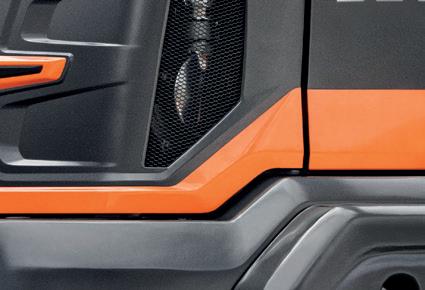
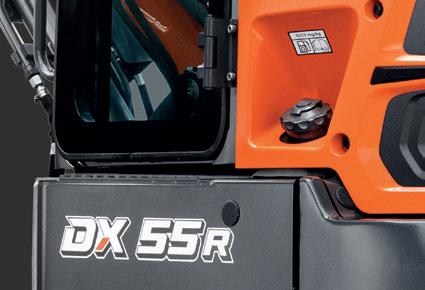
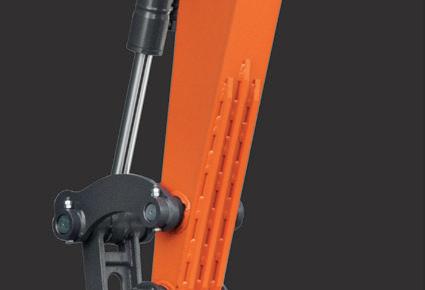


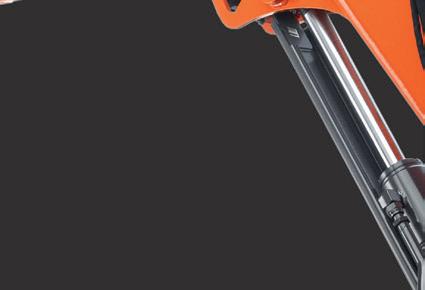

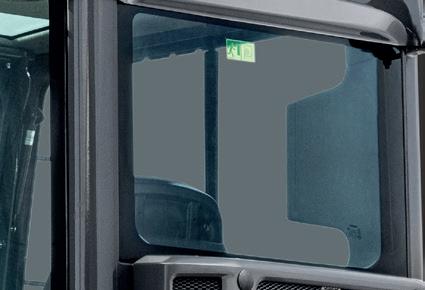
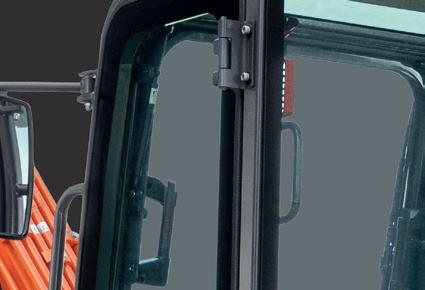

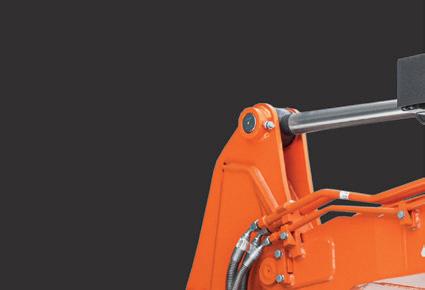
Same quality products maximum productivity outstanding value continuous innovation
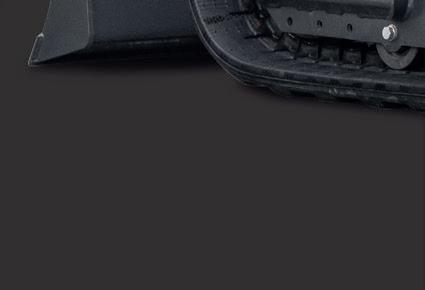
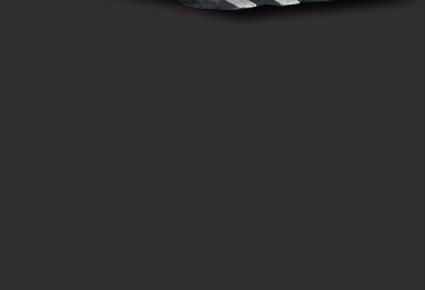


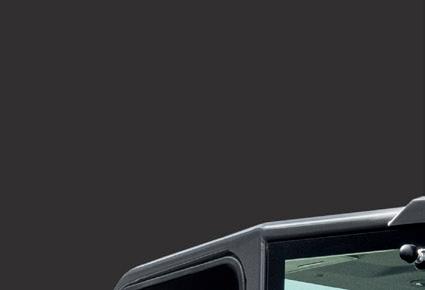
Find out more: eu.develon-ce.com
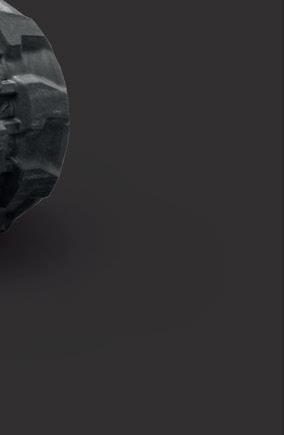
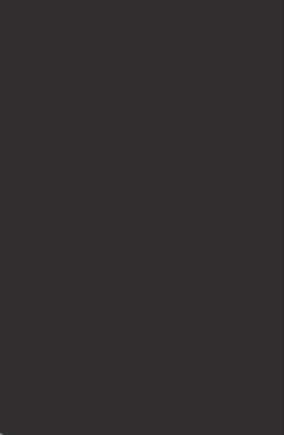
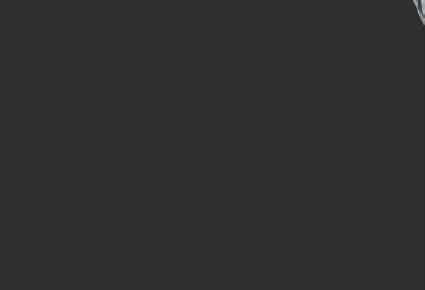


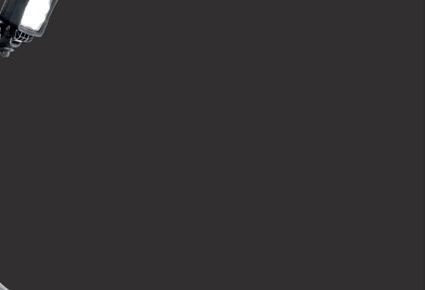

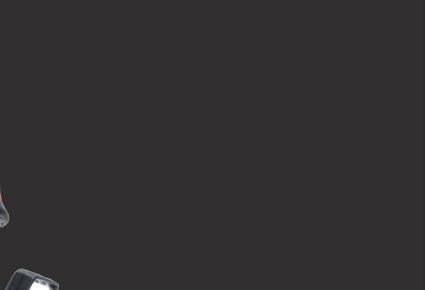
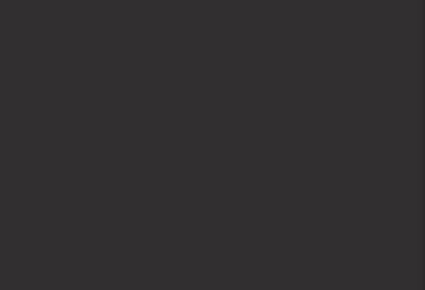
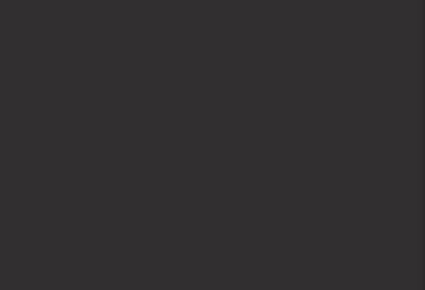
The new Cat 836 Landfill Compactor leverages Caterpillar’s decades of experience in maximising machine performance and reliability in the harshest working environments. Engineering upgrades to the axles and transmission of the new landfill compactor help to increase durability of the heavy-duty main structures that support multiple life cycles. New standard technologies increase machine efficiency by allowing the operator to meet compaction targets in fewer passes to save on fuel.
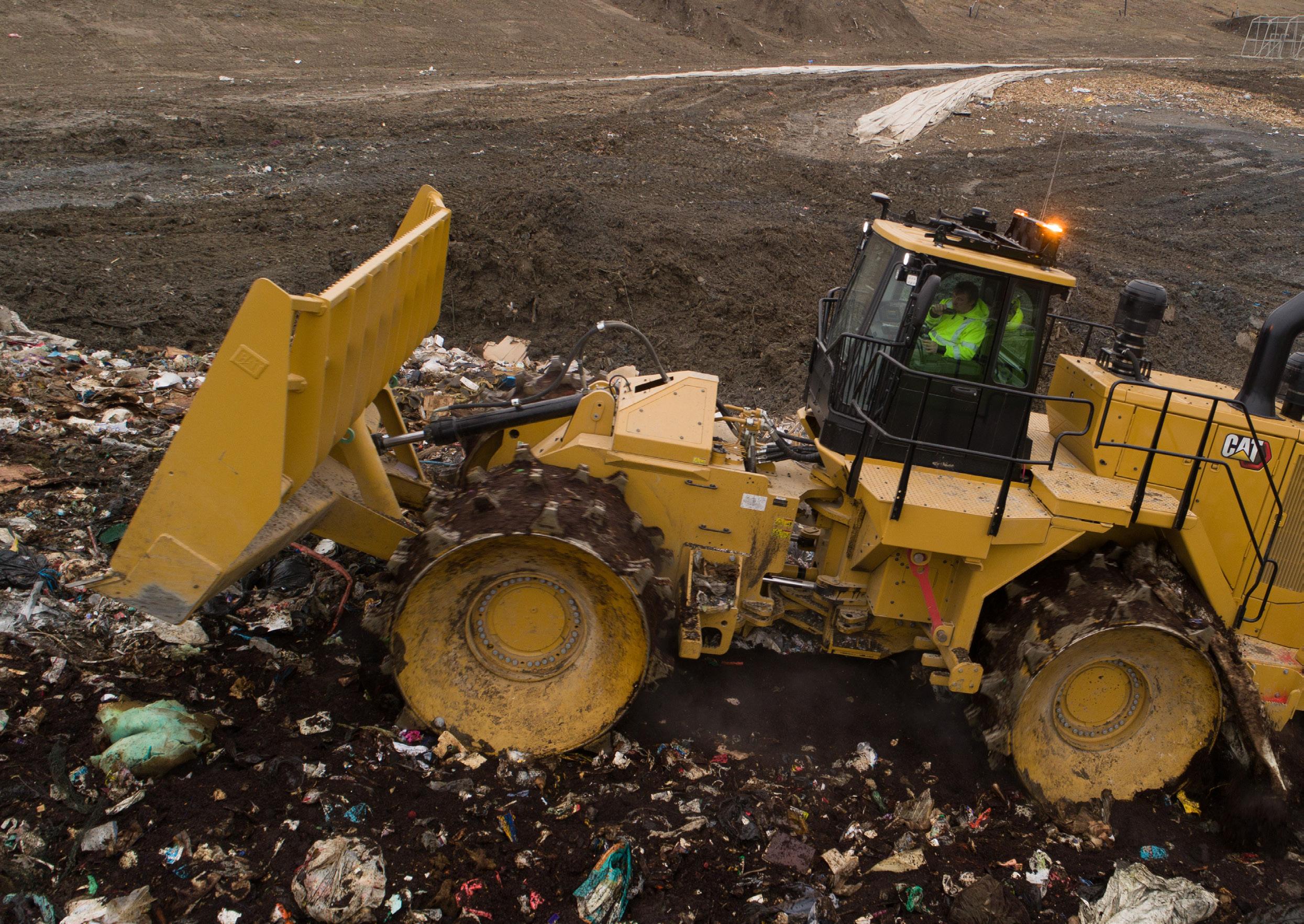
The Cat torque converter with lock-up clutch eliminates torque converter losses while lowering system heat and transfers more power to the ground for improved traction. Its advanced productivity electronic control system (APECS) transmission control helps the compactor to achieve greater momentum on grades and delivers fuel savings by carrying momentum through shift points.
Two configuration options for the Cat C18 engine powering the 836 allow the compactor to meet local emissions regulation requirements around the world. Improved radiator air inlet door sealing and carry over pressure hood enclosure help to reduce the need for
Net power advertised is the power available at the flywheel when the engine is equipped with fan at minimum speed, air intake system, exhaust system and alternator engine compartment cleanout. Helping to facilitate maintenance planning, data captured alerts key personnel to the remaining useful life of the engine air filter.
Advanced compaction technologies
Cat Compact technologies combine advanced compaction measurement, in-cab guidance and reporting, so compaction targets are met quickly, uniformly and in fewer passes to save on fuel. The system includes a global navigation satellite system (GNSS) receiver on top of the 836 and mapping display inside the cab.
Standard Cat Compact with Pass Mapping delivers high-accuracy pass counting, allowing operators to monitor areas of coverage and number of passes on the 10-inch display. Optional Compact Elevation Mapping combines both pass counting and elevation monitoring of slopes to plan, control layer thicknesses and achieve better density.
Visualised remotely via VisionLink® to improve fleet management, standard Cat Link technology provides access to machine location, hours, fuel consumption, idle time, events and diagnostic codes. Operators are kept informed about machine operating conditions through a 3G touchscreen with user-friendly interface for viewing the vital information management systems (VIMS™) data to optimise machine uptime.
Rugged reliability, simplified maintenance


The new Cat 836 features larger diameter shafts and Cat locker differentials for enhanced drive system longevity, improved direction shift speed and increased traction in the waste stream. Updates to the final drive gear set reduce stress and enhance pitting life of the gear. A new fan motor guard helps to prevent bag wrapping, while a new, 127-mm higher efficiency fuel filter delivers cleaner fuel to the engine.



The new compactor is designed for ease of service and inspection with a focus on safety, as most major components are accessed from ground level or on the machine’s platform. Minimising fluid contamination, sight gauges for coolant, transmission and hydraulic oil provide a quick visual inspection. Increased guarding around the axles mitigates risks of damage to components. Leveraging VIMS data allows operators and technicians to resolve machine issues prior to failure.
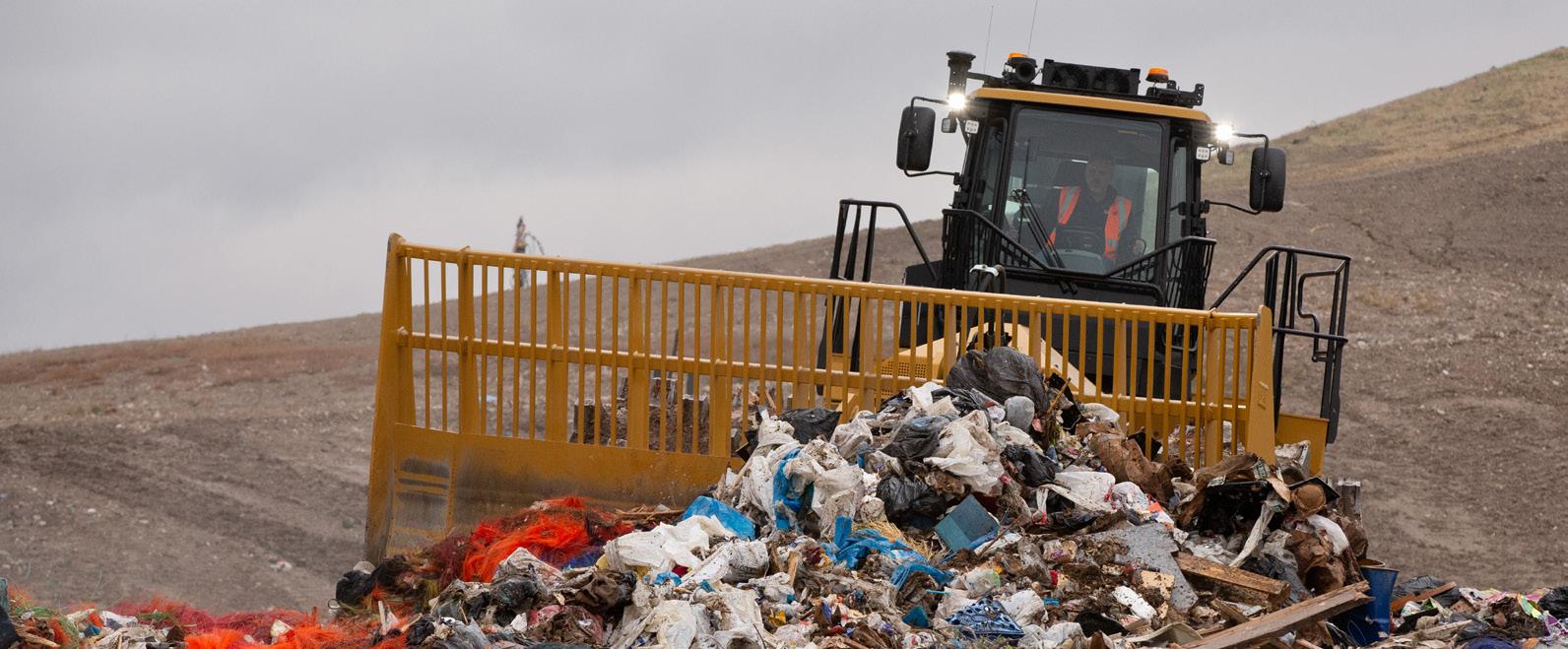
Efficient performance
The enhanced operator’s environment of the 836 includes better forward visibility to the blade and wheels via the lowered glass design. Its standard rearview camera increases visibility to the machine’s rear, helping to advance safe operation. A pressurised, climate-controlled cab is built for operator comfort and provides low, 72 dBA interior sound levels. Combining steering, gear selection and other functions into a single lever, the Cat STIC™ (steering and transmission integrated control) delivers maximum responsiveness and control to reduce operator fatigue and increase performance. Designed specifically for Cat landfill compactors to optimise compaction, five wheel and tip configurations are available for the new 836. The lighter paddle tip design delivers high performance and traction with less fuel burn, while the plus tip traditional design increases stability on side slopes. The combination tip wheel incorporates both the paddle and plus tips to provide the best compromise of performance and fuel economy with side slope stability. Caterpillar’s exclusive diamond tip wheel delivers the longest tip life on the market, and the chopper tip design excels at compacting wet/soft waste material.