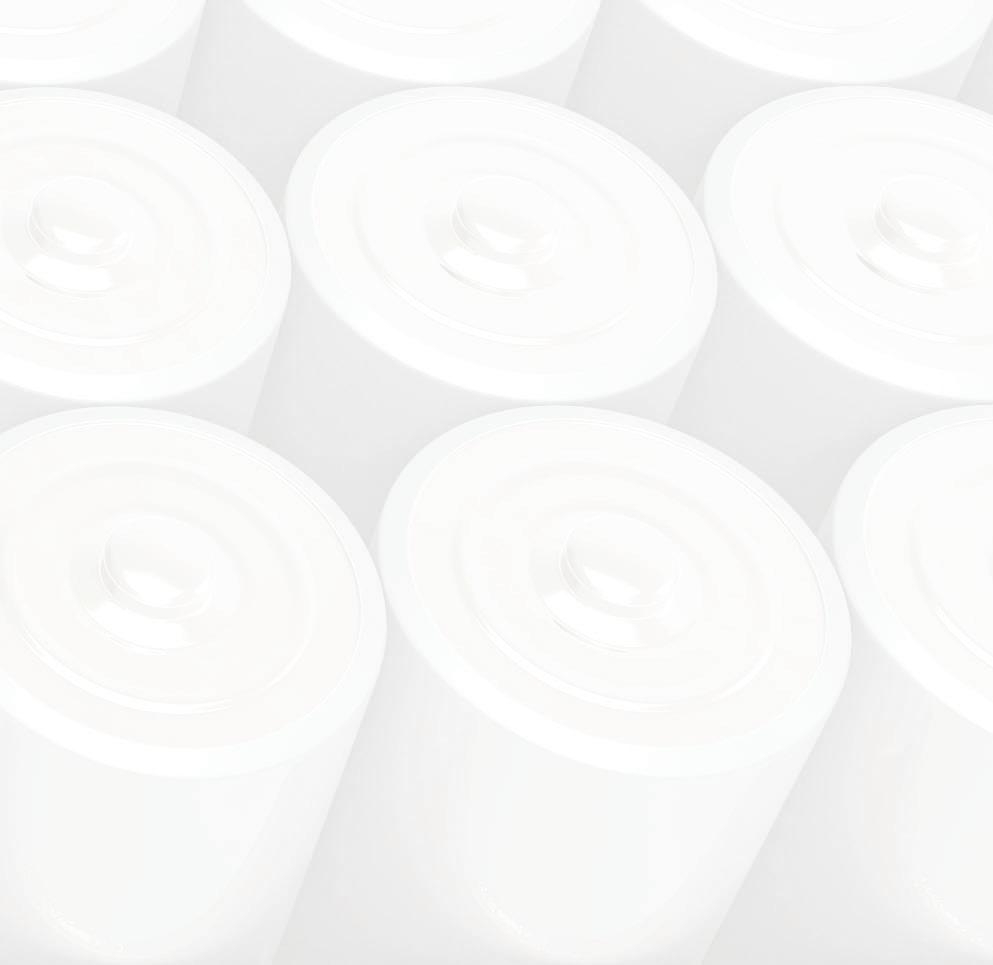
11 minute read
New battery production in record time
6 tips for creating high-throughput battery production in record time
By Tom Lombardo
Batteries represent nearly one third of the total price of a typical EV, and there’s a push to get that down to 20% or less by the end of this decade. In an e ort to lower costs and accelerate production, the EV industry has been searching for ways to make the assembly process more e cient and to decrease the time it takes to create a battery assembly line.
New highly-automated battery assembly lines usually take months to develop. Can that be accelerated?
In 2020, precision automation company DWFritz needed to develop a complex battery production line for a leading North American battery manufacturer. e requirements included high speeds, a tight footprint and an accelerated development time.
Considering the complexity of the project and the short development time, DWFritz decided to form a strategic partnership with automation supplier Bosch Rexroth. Together, the two companies operated in a concurrent engineering environment, allowing for rapid design iteration and accelerated execution.
“In the past, we would have used several di erent suppliers,” explained DWFritz President Mukesh Dulani, “but just to start the collaboration between di erent suppliers, in this case, would have taken us at least 10 to 15 weeks. For this project, we only had 12 weeks of design and engineering time and 8 weeks for procurement, so we had to work with a partner like Bosch Rexroth who could supply the technology and the engineering support for us to be successful.”
No matter the cell size or form factor, battery manufacturing is a complex, multistep process that brings together dissimilar materials to form the battery’s cathode and anode, then combines them with the insulator into a nished package.
“ e line had to operate at very high speeds,” said DWFritz VP of Sales Chris Povich. “Space was also a challenge. Even though the line is more than a hundred feet long, it had to be designed to t into a very tight
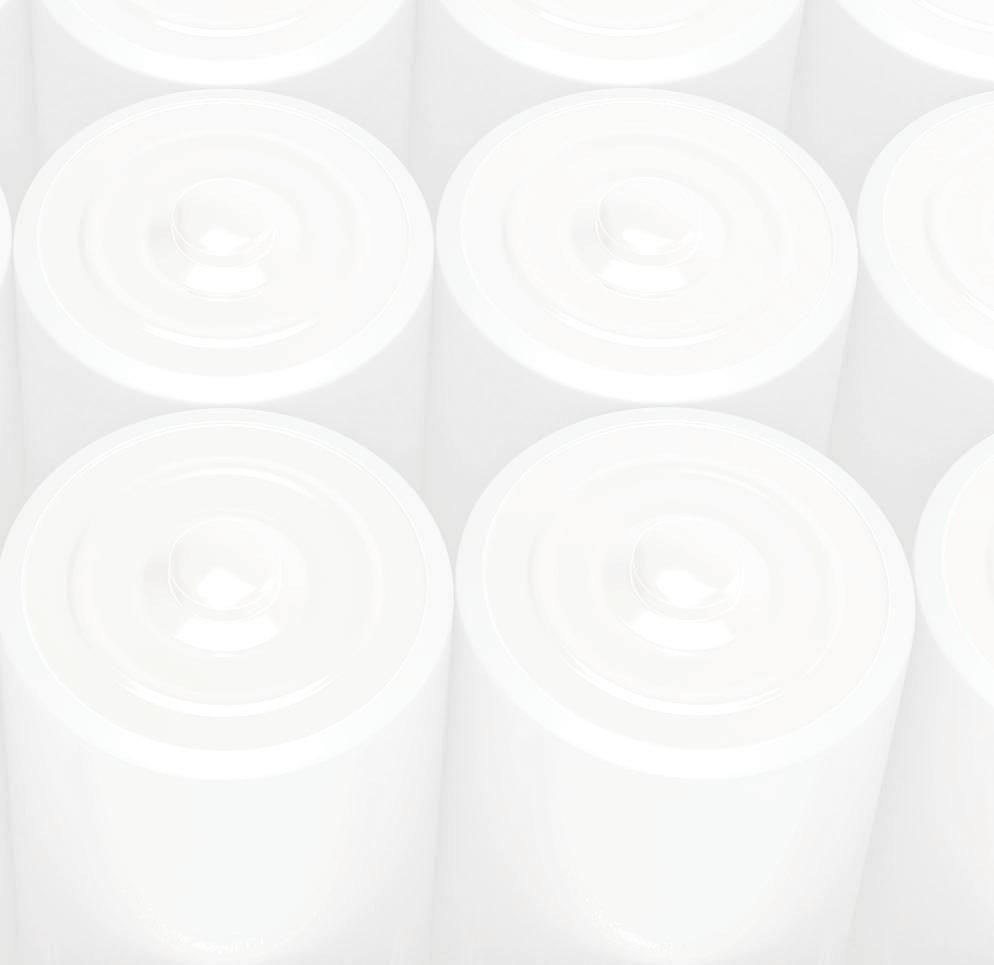
footprint. And the motion platform had to handle very robust motion-control demands—one system alone had in excess of 50 axes of motion.”
Together, the two partners say they managed to create a new battery manufacturing line that met the client’s requirements and set a new benchmark for building out production capacity.
To learn some tips for creating new production lines quickly, Charged recently chatted with Bosch Rexroth’s Mark Ziencina.
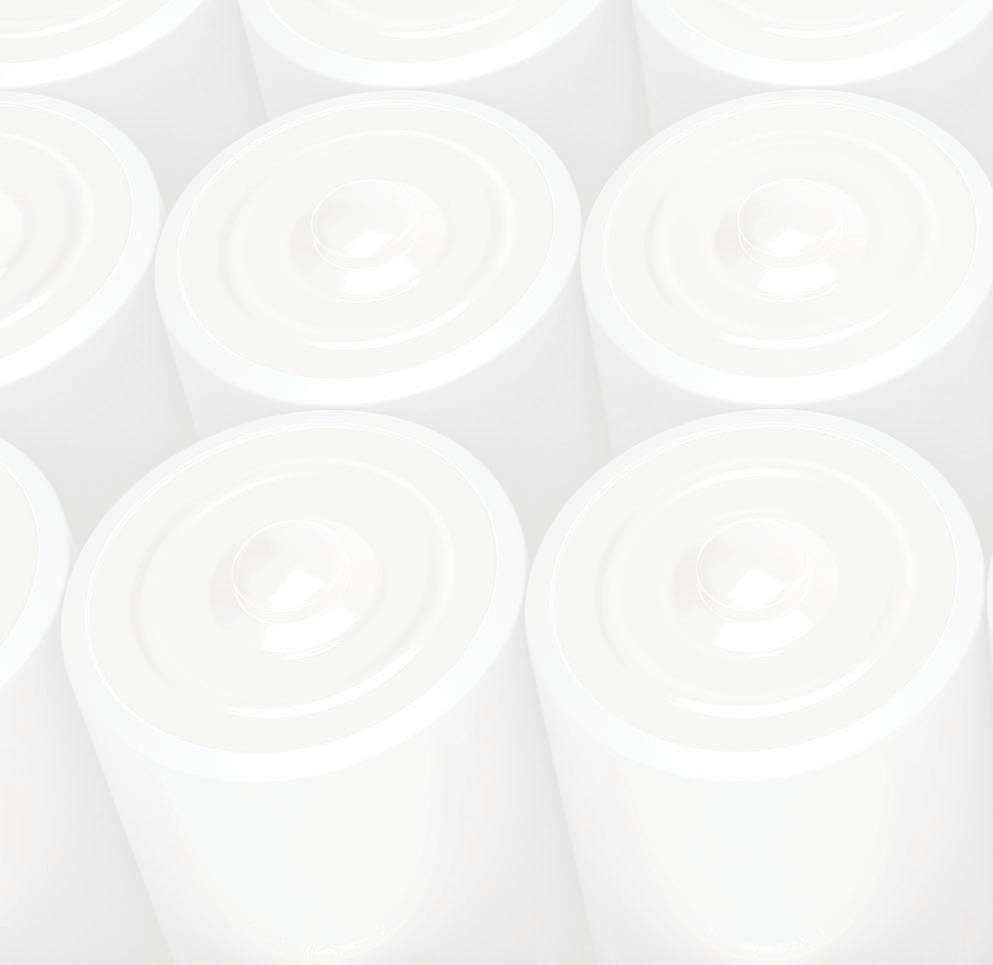
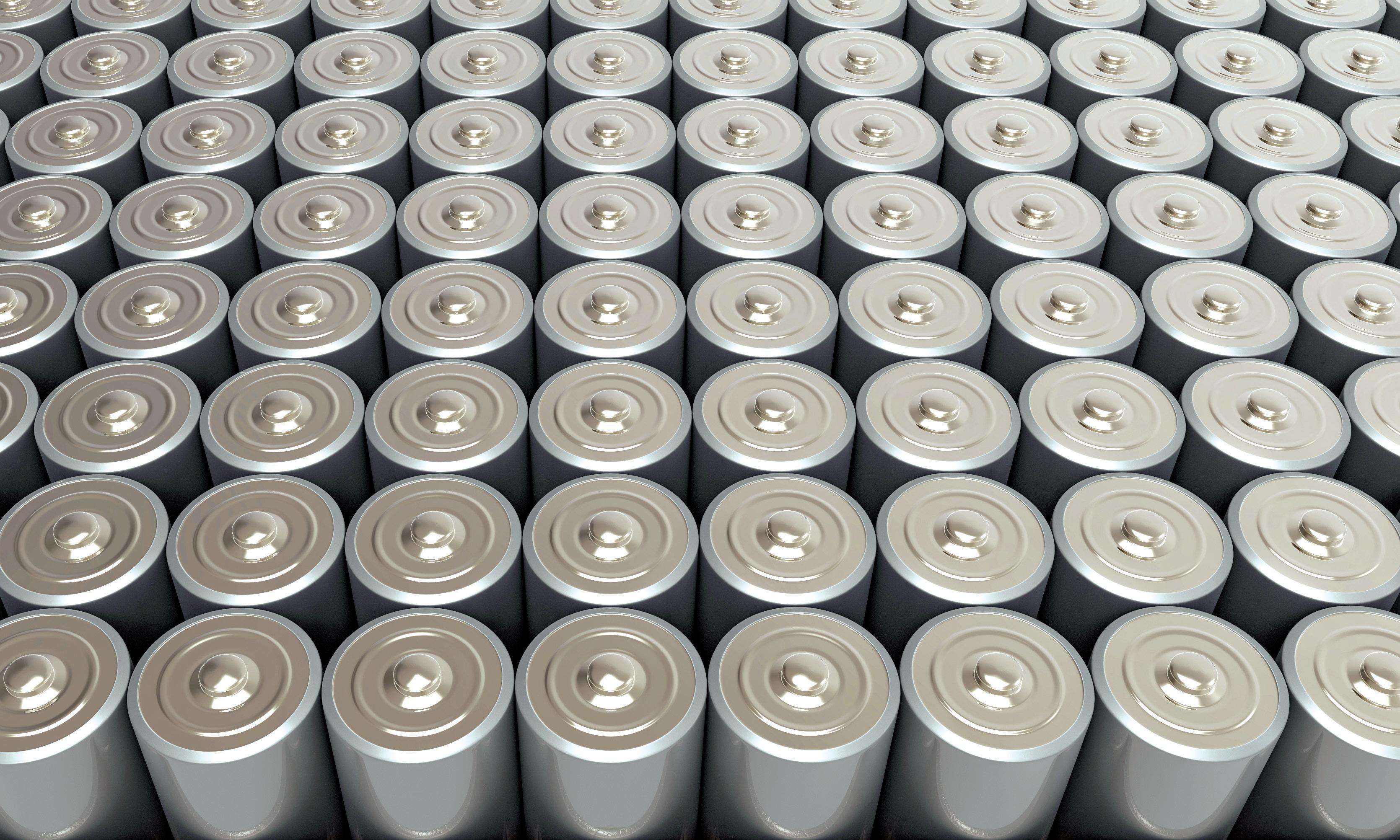
Q Charged: With all the new activity and incentives for local production in EV manufacturing, demand must be pretty high for your automation expertise.
A Mark Ziencina: e demand is absolutely incredible. I’m the Vertical Manager for Battery and EV at Bosch Rexroth, the automation division of Bosch. I have 28 years of factory automation experience in components and capital equipment, and what we’re experiencing now is through the roof. Our group specializes in solutions for the battery and EV segments, drawing from our past experience with battery technology and working with a variety of partners and customers in the battery and EV markets. e challenge is to keep up with the demand, and I’m not even talking about the chip shortages and other supply chain issues. Everyone agrees that globally, this market is going to be growing at about a 23% compound annual growth rate. However, in North America, we see it growing a lot faster than this, because we’re trying to catch up with China and other Asian countries who jumped into the market early.
With all the incentives and new requirements, as well as all the money pouring into the EV market, everybody needs equipment now. Everybody wants batteries. ey all want it at the same time. So, it’s a good problem to have, and with enough experience you can learn how to get it done with available resources.
Tip #1: Limit the number of strategic partners and suppliers to form a small group with experience operating in a concurrent engineering environment to allow for rapid design iteration and accelerated project execution.
Q Charged: Rexroth recently published a case study
about its partnership with DWFritz, detailing how you were able to cut time to implementation for new cell production. What do you think are the most important tips to accelerate time to market?
A Mark Ziencina: DWFritz was looking for an automation supplier for that cell project that had all of the various solutions that they needed, such as material transfer conveyors, Cartesian systems, and linear actuators that had high precision, extreme reliability, and the ability to work in cell assembly environments. ey were also looking to execute the project in a very short time frame, as opposed to the standard 12-month execution time. ey chose us, and we became an extension of their engineering department. Our applications engineers worked side-by-side with their design engineers to shrink the design time through concurrent engineering, multiple iterations, and a lot of back and forth.
Tip #2: Use a digital twin design that allows you to test the systems while you’re waiting for the hardware to arrive and be installed.
For all of these manufacturers, time to market is critical right now. Partnering with the right equipment builder and the right automation supplier will help to meet those goals, as opposed to managing a basket of di erent suppliers who do not have the holistic view of the project and may or may not have the depth of experience in these applications and processes.
On this project, a completely virtual development environment enabled the team to create a digital twin of the communication platform between Manufacturing Execution System (MES), the so ware that runs manufacturing operations in a factory, and automation controllers, saving an enormous amount of time.
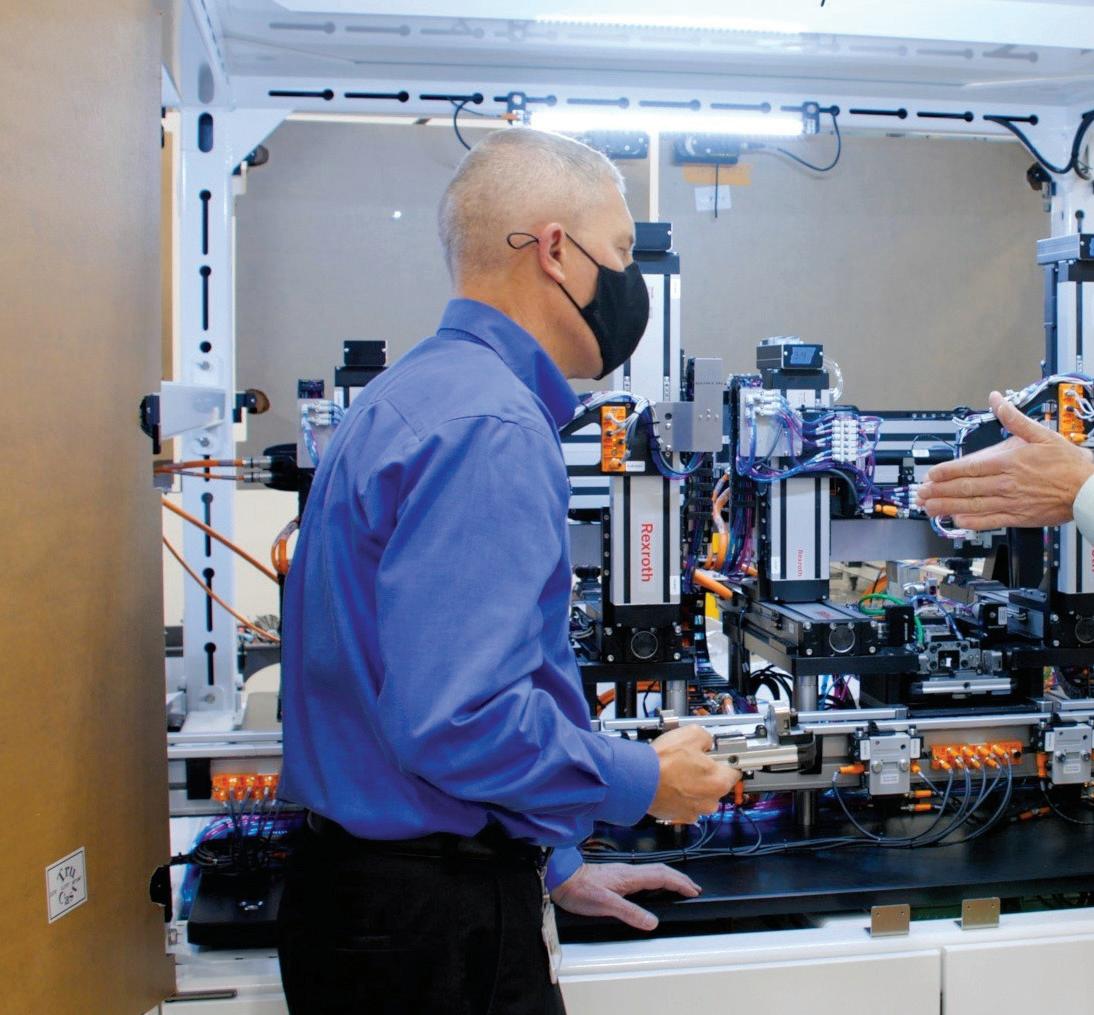
Q Charged: How did the footprint requirements of the
manufacturing line a ect the development time?
A Mark Ziencina: Small footprints can create a lot of challenges that delay design time if the team doesn’t have the right experience. For example, we used our MTpro layout so ware to design conveyors that t into the tight machine footprint and also provided the machine-to-machine connection. In some instances, the machine was so jammed with automation—40 to 50 axes of motion in one frame—that there was not enough space for a control enclosure to t all of the drives. So, we went with our cabinet-less technology, which has motors with onboard servo drives, to eliminate the need for a huge box full of servos. Everything was distributed throughout, which facilitated a more compact system.
Q Charged: In terms of length of the projects, what
has been the historical development time for a standard cell line, and what is the industry pushing towards now?
A Mark Ziencina: Depending on the complexity of the project, typically, it was 12 to 14 months to execute an entire line, maybe a year and a half. Now everyone wants to
Using a concurrent engineering process, DWFritz Automation and Bosch Rexroth worked together to design and install a flexible, high-throughput and fully automated battery production line in record time.
Tip #3: Use an open machine control architecture that allows real-time data access and machine-to-machine communication. This keeps all of the production modules in sync and allows operators to monitor and control the processes.
shrink this down to 6 to 8 months or less. So the challenge is, what can we pull from our past experience? What modules and solutions do we have in our product portfolio that could shrink that design time?
We work on the design side as well to o oad that from the customer’s and the manufacturer’s plates. Drawing from our knowledge of cell, module and pack assembly applications, we choose solutions, customize them for the particular product, and shrink that down.
We also pool all of the raw materials required for our products. We can closely estimate how many conveyors, for example, will be required for a project and have them in stock so we’re not waiting on parts. So, while the design is still ongoing, we bring in the materials, and then as soon
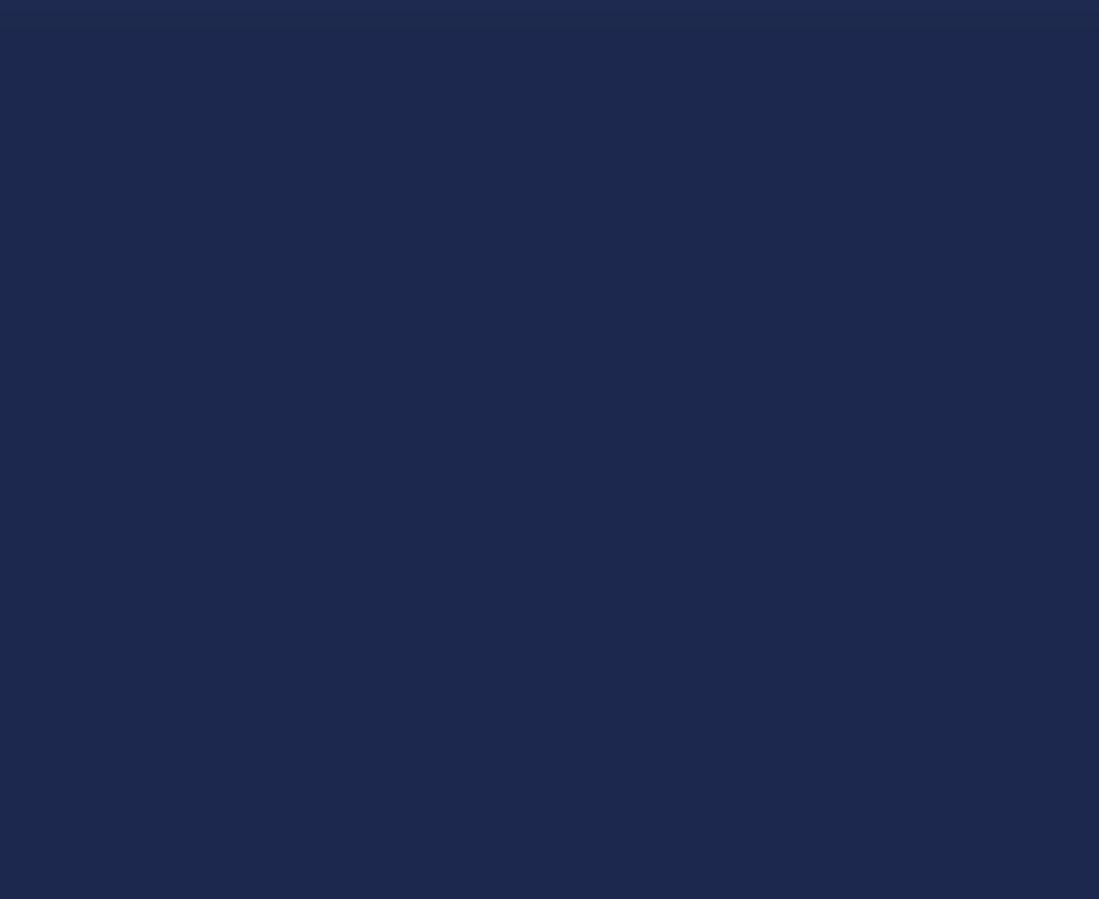

Tip #4: Work with automation and equipment suppliers during the product design stage to address the subtle design details that affect the assembly development process.
as the design is complete, we can start sending the nal drawings to the manufacturing oor. We do everything we can to shrink the design window and the production execution window by working very closely with the customer.
Q Charged: What are the most common material bottlenecks that typically delay a project?
A Mark Ziencina: Everything is in short supply—even small
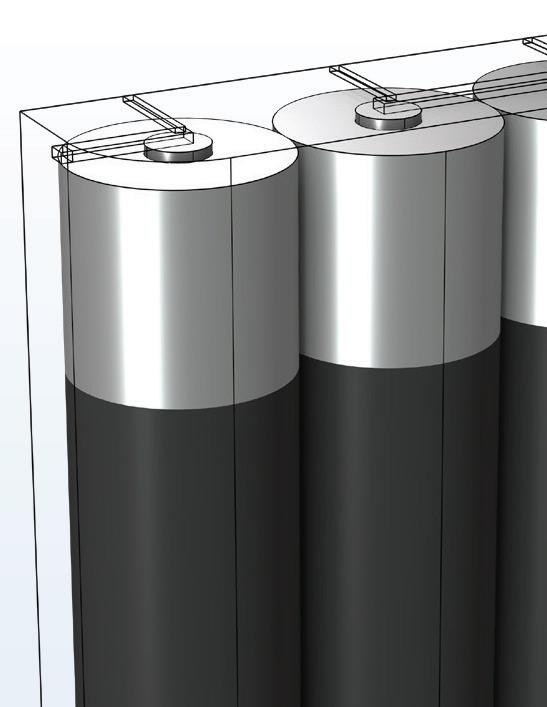
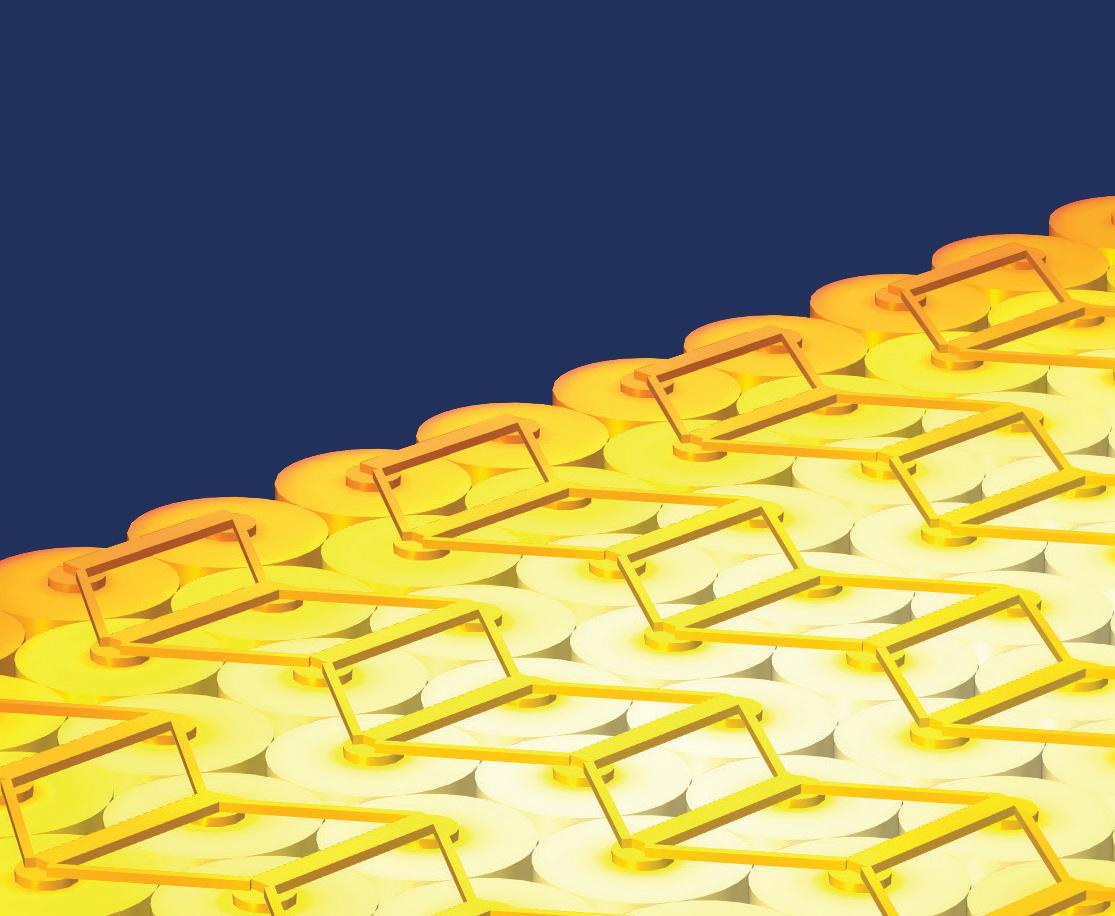
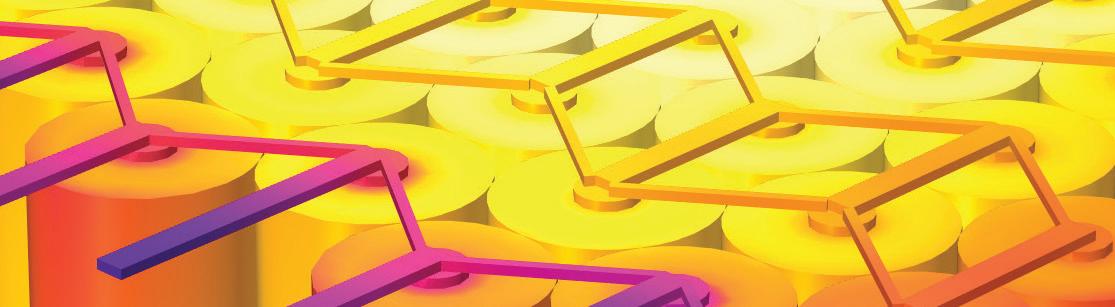
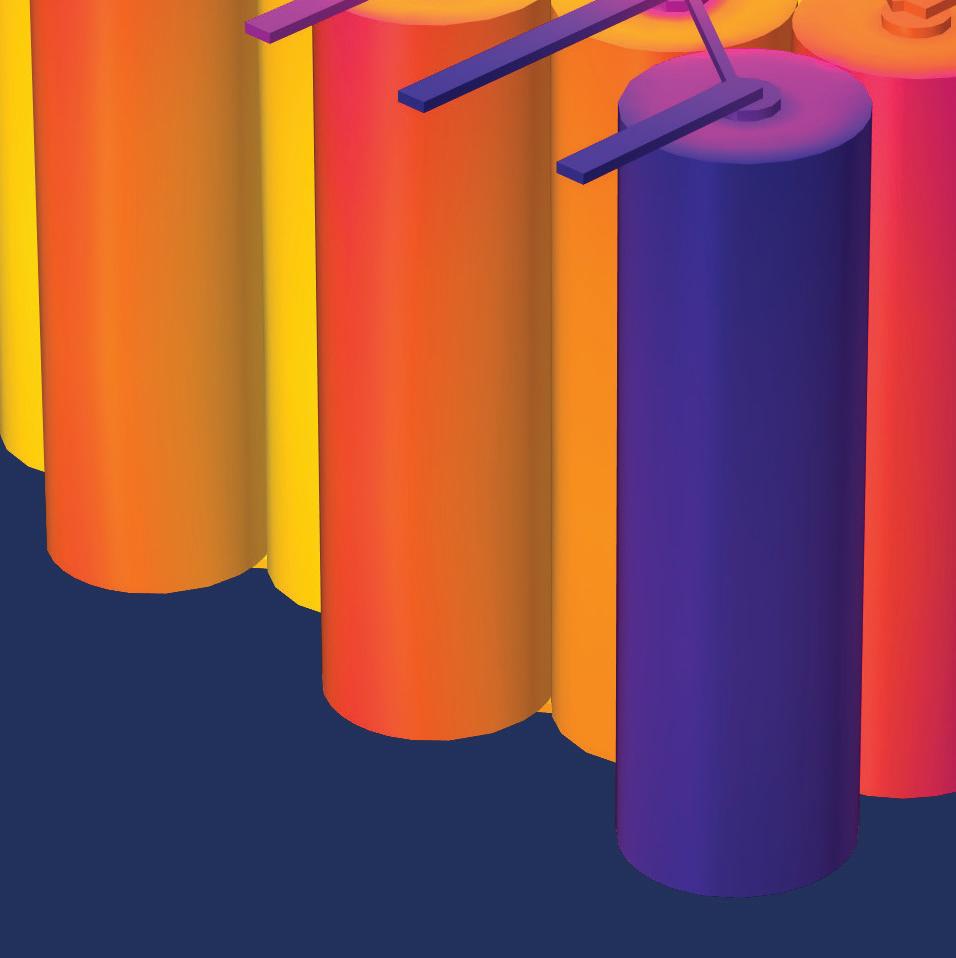
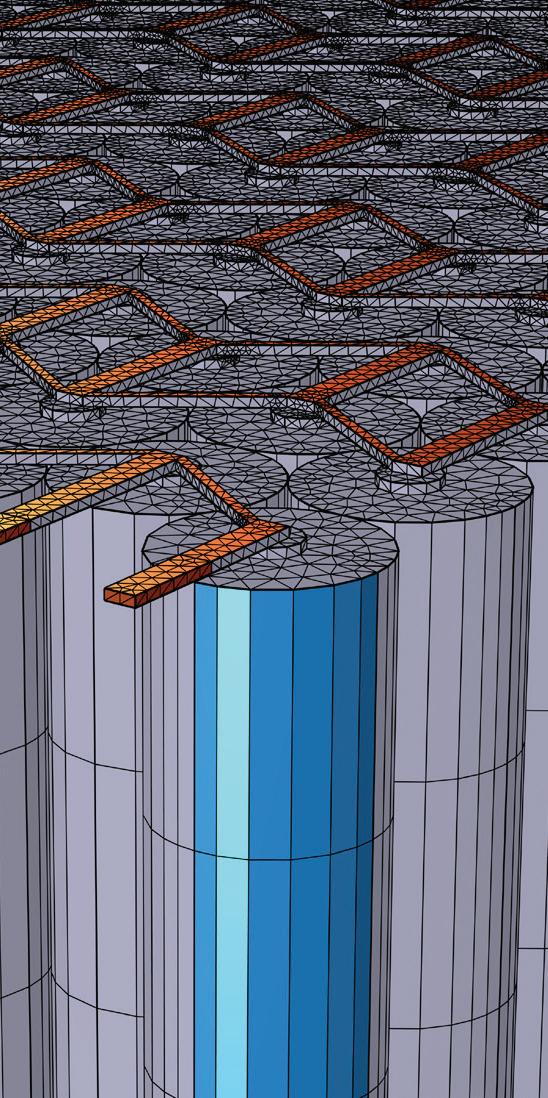

Charge Ahead in Battery Design
with COMSOL Multiphysics®
Multiphysics simulation helps in the development of innovative battery technology by providing insight into mechanisms that impact battery operation, safety, and durability. The ability to run virtual experiments based on multiphysics models, from the detailed cell structure to battery pack scale, helps you make accurate predictions of real-world battery performance.
» comsol.com/feature/battery-design-innovation
Using the Rexroth ctrlX AUTOMATION platform and its ctrlX CORE controller not only made this project successful, but it enabled the DWFritz to build future production lines using the same software and hardware platform.

Tip #5: Choose suppliers that are well-versed in multiple open-protocol technologies and customizable offthe-shelf modules. This allows users to write their own application-specific modules, avoids the need to design everything from scratch, and provides the ability to reuse the modules in future product lines.
things like T-nuts for aluminum framing. But most commonly, it’s the chip shortage that’s really impacting all the automation suppliers. Lead times on motor controllers can be 12 months or more. Worldwide, there is no manufacturing sector that is isolated from the chip shortage. Preparing, planning ahead, and reserving that capacity ahead of time is key, because it can really impact the installation and ramp up of these new lines and new capacity.
Q Charged: What other factors are important to
assure a successful execution?
A Mark Ziencina: It’s really important to pick reputable suppliers that have a global footprint and a local presence, plus experience in the battery manufacturing space. Additionally, experience with standardization to open protocols is key because you have to bring many solutions under the same umbrella. is assures compatibility without tying you to one particular supplier. ere are so many manufacturers with di erent platforms for control architectures, and every manufacturer tries to lock their customers into their speci c ecosystem. We went directly against that with our ctrlX open architecture controller design, for example, which can be programmed in any of the common languages. It’s compatible with anyone’s products. It includes apps that users can write themselves, so they’re not locked into a certain programming environment. You don’t have to nd specialists who know a speci c language or development platform—you can get programmers to program in Python, C/C++, Java, or whatever they like, to get the entire automation executed. Our controls directly communicate all the way up to the MES. It’s important to pick the right architecture and standardize so you don’t have to support and stock a lot of di erent products.
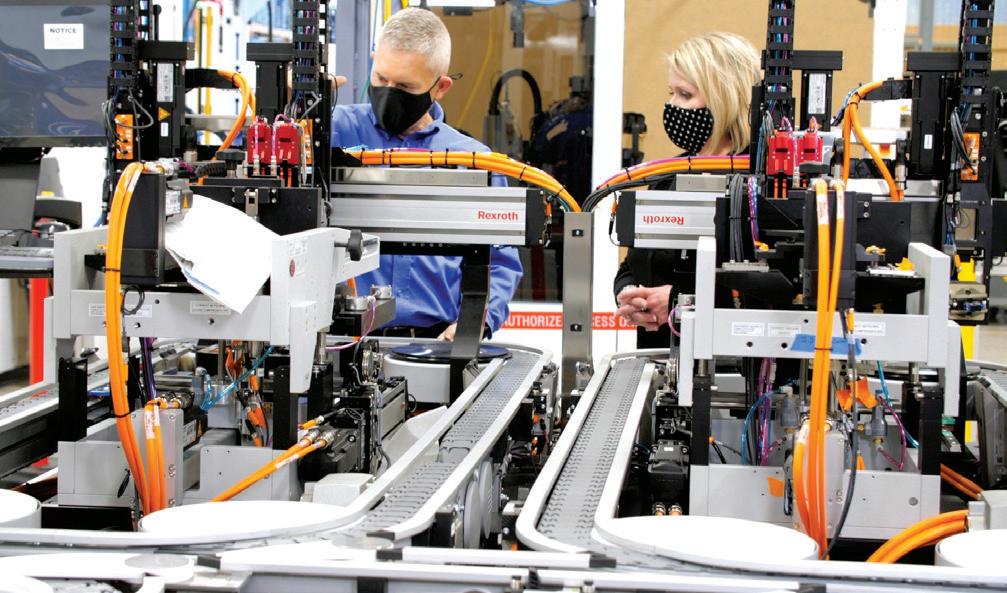
Tip #6: Use Industry 4.0 technology such as smart sensors, vision algorithms and component tracking systems to perform inspections throughout the assembly process. This helps to pinpoint problematic areas and provides upstream feedback that can bring about production line changes to account for incoming material variability, precision assembly tolerances and high-throughput demands.
Learn more
Considering the extent of current e orts to ramp up EV production capabilities and source battery components made in North America, we can expect to see a number of manufacturers trying to fast-track their assembly lines. ey may want to take a lesson from the DWFritz/Bosch Rexoth partnership. ese two companies recently presented at the 2022 Charged Virtual Conference on EV Engineering. To learn more about the project, check out the webinar recording.
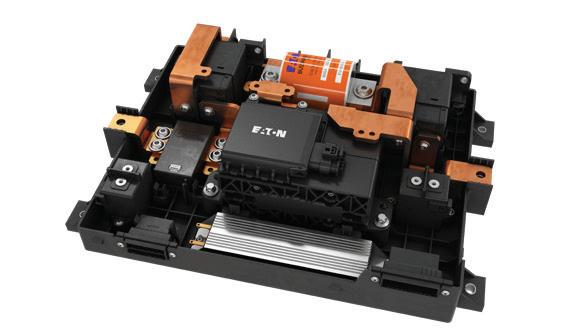
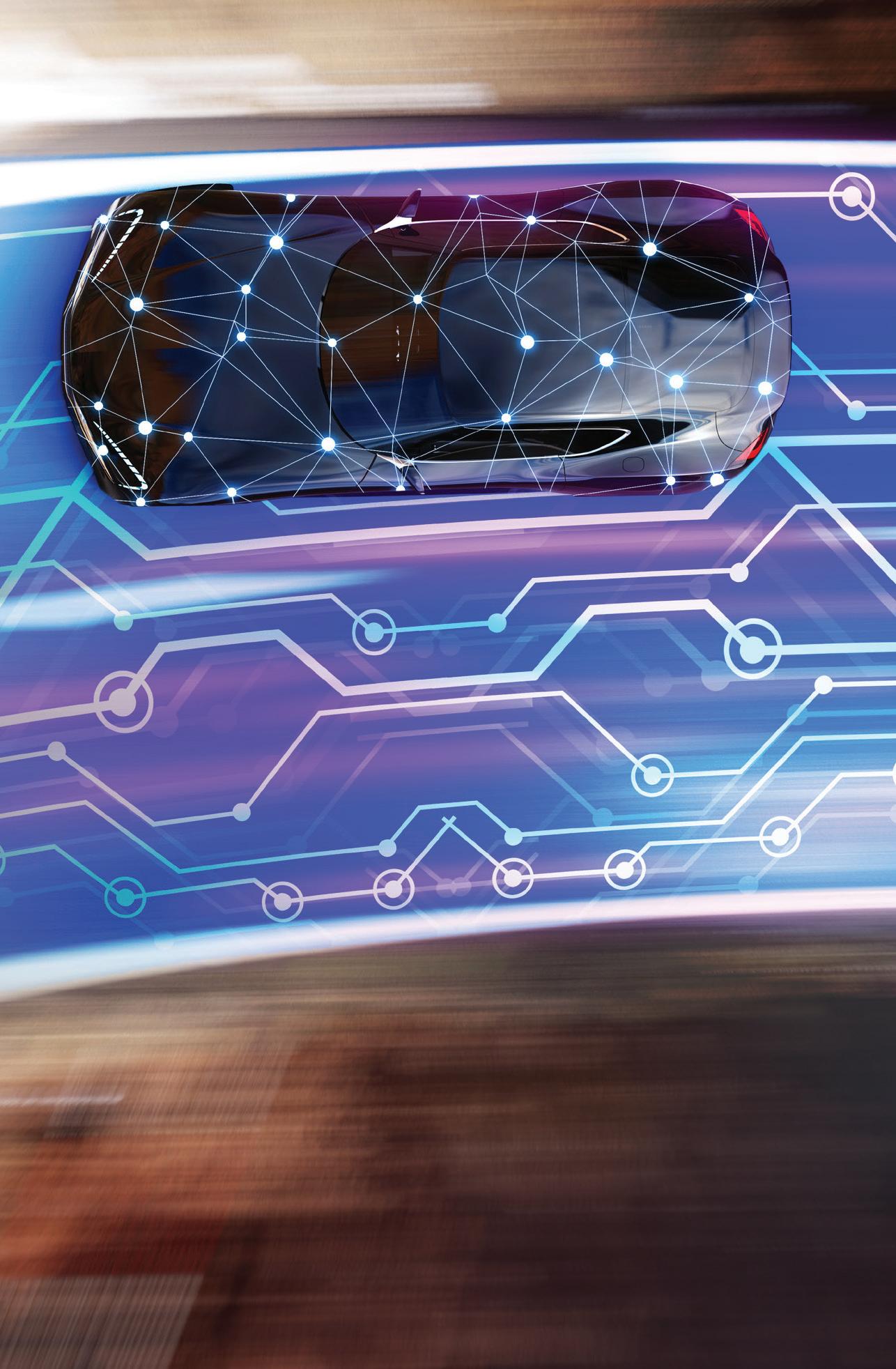
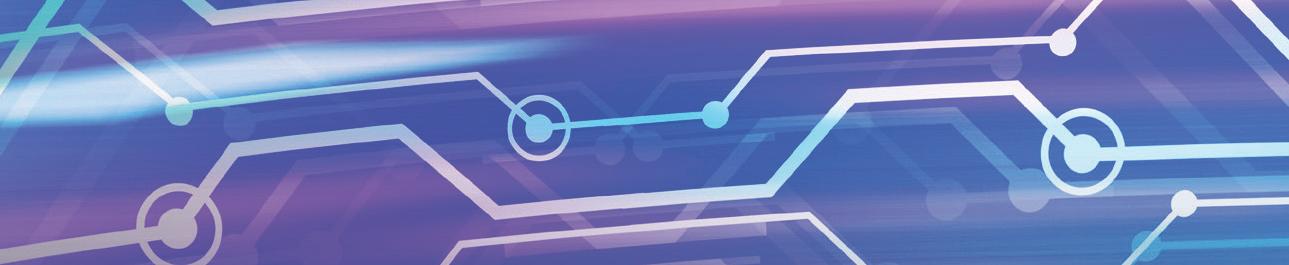
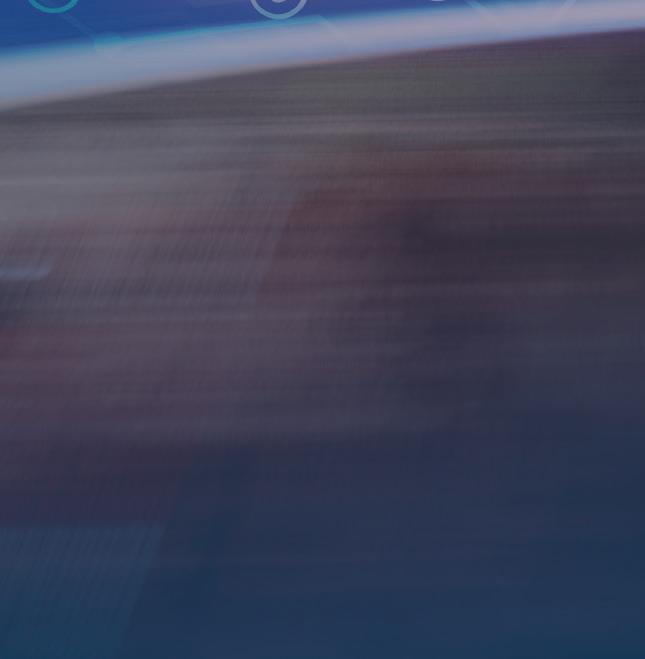
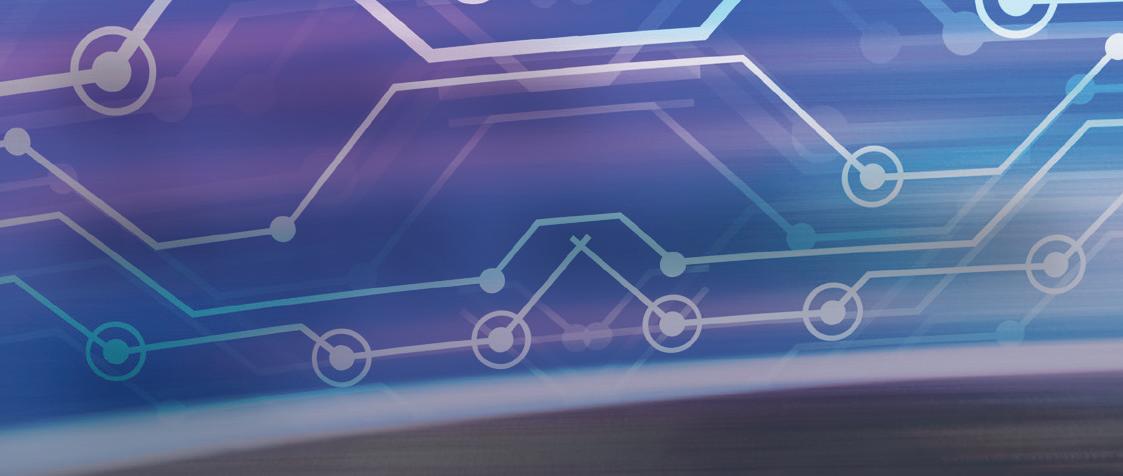
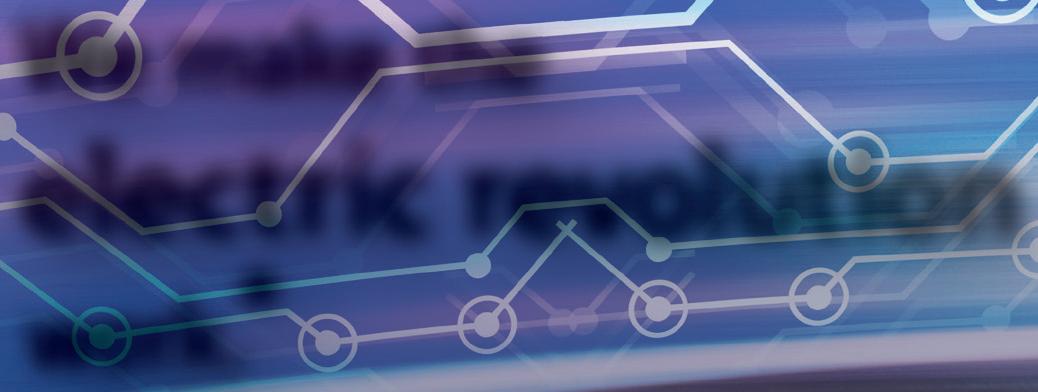
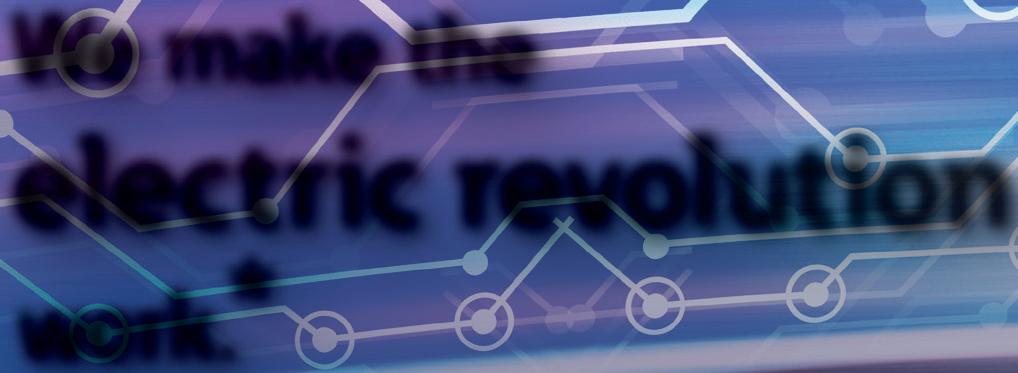

Battery disconnect unit featuring Breaktor®
Power levels in electric vehicles are increasing. EVs need to drive farther and charge faster. What does this mean for system safety? Expertise is critical when managing, distributing and protecting electrical systems. Eaton’s advanced battery disconnect units (BDUs) feature integrated Breaktor® circuit protection technology, enabling EV manufacturers around the globe deliver the safest vehicle systems possible. Because that’s what matters.
Learn more at: Eaton.com/eMobility We make what matters work.