
13 minute read
Will China’s coal push delay its dual carbon targets
VOX POP Will China’s coal push delay its dual carbon targets
China
A coal mine in Hailar, Inner Mongolia, China (Photo by Herry Lawford)
David Fishman Senior Manager, The Lantau Group:
In 2021, we’ve seen China continue to build coal plants and expand its coal mining capacity. This is something that is still possible to do under China’s current energy planning. China’s decarbonisation plan calls for a carbon peak to be reached in 2030. But since there is a coal consumption peak declared for 2025, it means that before 2025, the amount of coal consumed in the economy or to keep the economy moving for any purpose—including power generation or steel production—could still be increased and then must be peaked in 2025. For building coal-fired power inside of China, the important question to consider is not just whether the capacity is being built, but also how much is going to be used because building a coal plant does not necessarily mean it is going to be used all the time. We’re still seeing coal being built in China, which will be used in provinces building a lot of renewables, but that will still need some other form of firm supply to meet their needs in the evening or other periods when variable generation is unavailable. In terms of meeting its milestones for 2025 and 2030, these milestones should not be affected. They would still plan to cap at that time, it could mean that the level that it caps at will be a little bit higher than it was previously, if you chose to set that cap in 2021 or 2022.
Carlos Torres Diaz Head of Power Research, Rystad Energy:
International coal prices have increased significantly this year so China is trying to reduce its dependency on imports. API 5 prices, which is a reference for the region, have increased from a level of US$160 per tonne in the third quarter of 2021 to more than US$400 per tonne recently. China is also trying to reduce imports of LNG as prices remain at a record-high level. Further, China is currently prioritising its energy security and aiming to limit power generation costs to the extent possible. This means using more coal in the power mix. As a result, it is likely that carbon emissions from the power sector will increase this year and next at a faster pace than previously expected. However, most investments in new energy capacity are still for solar and wind technologies so the long-term target for net-zero and carbon neutrality could remain unchanged. We see a similar trend across the world where countries are prioritising energy security above climate. European coal power generation has increased 11% this year. India has also aimed to increase domestic coal production and is currently studying the slower retirement of aging coal power plants.
Pavan Vyakaranam Analyst, GlobalData:
Energy security is the key reason for China pushing for coal. China is facing a severe electricity crisis because of tight supply and high demand for power, which is a result of the worst heat wave the country had witnessed in the last 60 years. Industrial users producing metals, chemicals, and other industrial goods in China’s Sichuan region are forced to shut down for a week to prioritise residential supply. Sichuan province ordered the suspension of industrial production during August 15 to 21 to avoid blackouts. The current economic conditions and growth predictions make it highly unlikely for China to achieve its dual carbon targets. The current electricity crisis led China to lift restrictions on coal production domestically and imports from Russia. This will derail efforts made with respect to emission reduction in the short term. There will be an increase in coal-based electricity generation in the region to overcome the current energy crisis. Of the total coal capacity under construction in the world, the Asia region has over 94.5% capacity. China alone accounts for over 48% of the total under construction coal capacity in the world and has a share of over 51% of coal capacity under construction in the region. China is followed by India which accounts for 20.6% of under construction coal capacity in the Asian region.
What future-proofing looks like for the energy market
EthosEnergy’s suite of life extension and emissions compliance solutions aims to make energy affordable, available, and sustainable for its clients.
ECOMAX® combustion tuning platform
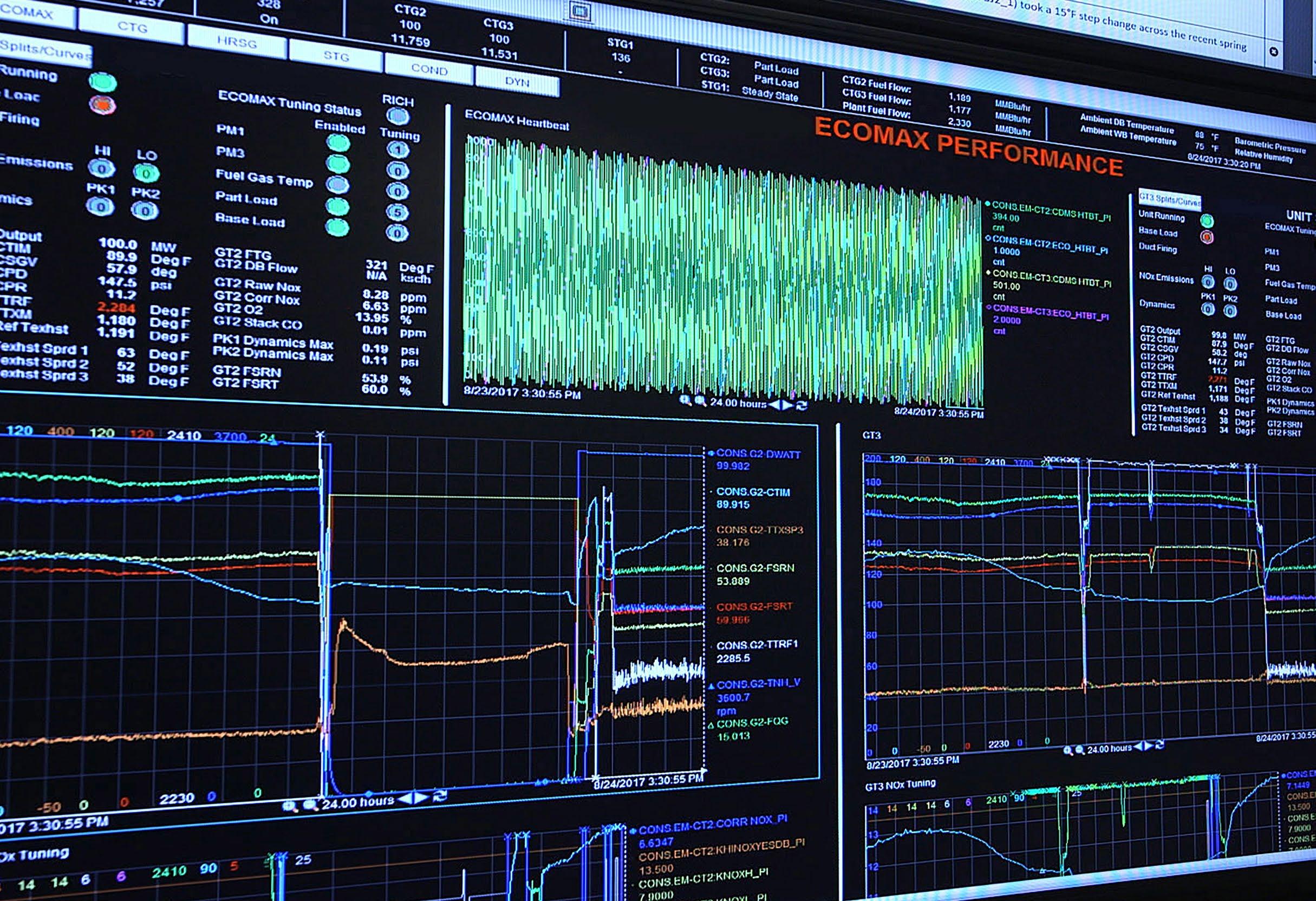
In a world of changing expectations and soaring energy prices across the globe, customers are facing a challenging future. The energy industry is exploring options for increased sustainability, emission control, and reduction.
Industry players need to improve and adapt operations in order to be future-proof.
Climate concerns have already placed pressure on traditional ‘take, make, dispose’ business models, i.e. a linear approach whereby we buy new, use, and get rid once we are done. Whilst the industry has utilised this traditional model in the past, it will not hold up to the changing landscape of today.
Moving to a circularity approach, in contrast, decouples economic activity from the consumption of materials and energy by creating closed-loop cycles in which waste is minimised and resources are reused. Even sectors such as oil & gas can introduce elements of circularity in their operations.
The uptake of reuse in the energy industry is not as good as it should be. There’s a real opportunity for reusing instead of disposing when equipment is close to decommissioning. EthosEnergy’s value is to provide economic, social, and environmentally beneficial solutions to extend the life of existing equipment. Utilising this leads to significant cost savings for businesses, as well as critical CO2 savings.
To transition from a linear economy to a circular one, industry players need to look across three key areas: how to maximise product use; prioritise renewable inputs; and how to recover by-products and waste.
EthosEnergy has already developed a suite of life extension and emissions compliance solutions to support current assets in meeting critical targets. Operating in over 100 countries, it relies on the potential to deliver services and solutions globally for rotating equipment to make energy affordable, available and sustainable.
“Customers are looking for a localised strategy. Certain services and technologies are not made available from the region’s perspective. However, a number of assets are quite mature in [the power, oil & gas, industrial and aerospace markets] which clients have good knowledge of and are comfortable exploring alternative services,” said Ken Peerapong Hansakwong, Regional Sales Director APAC at EthosEnergy.
For them, there is a need for more collaboration and alignment between business, social, and environmental factors to work through the energy crisis and achieve success.
EthosEnergy’s solutions also have a significant impact on CO2 emissions across two fronts: first, they avoid the production of new equipment and therefore avoid emissions during the manufacturing process; second, they can avoid or postpone the recycling of aged assets, reducing CAPEX expenditure.
EthosEnergy offers gas turbine solutions across manufacturers

Gas Turbines
EthosEnergy also offers gas turbine solutions across a range of original equipment manufacturers (OEMs). Its solutions and services are known to reduce emissions, increase reliability and availability, and reduce capital expenditure.
At the same time, EthosEnergy has extensive experience in services for multiple gas turbine product lines—derivatives, light and heavy industrial gas turbines, and components and accessories. The company also provides gas turbine repair services in the power generation, industrial and oil & gas markets, where its advanced technology repair and coating facilities are committed to developing solutions that keep customers within their budgets and timescales.
Its ECOMAX® combustion tuning platform provides an automated, fully customisable solution to achieve customer-determined operational objectives. This patented technology continually monitors and adjusts key combustion control parameters to maintain NOx and CO compliance, flame stability, and acceptable combustion dynamics. It also provides operators with customisable operational goals, emissions management and compliance, combustion dynamics control and mitigation, and increased fuel flexibility, amongst others.
For EthosEnergy, achieving operational flexibility is critical to maximising output and environmental effects.
ECOMAX® has helped save in the region of $15m in capital expenditure. It has also increased reliability and has helped power plants to maximise their output, better manage emissions, as well as reduce the risk of human error through manual tuning. Furthermore, EthosEnergy’s end-of-life rotor solutions have been engineered to meet or exceed the OEM’s recommended end-of-life specifically targeted to ageing fleets. Only the life-limiting components of a rotor are replaced, thereby minimising the overall project cost for the user.
“Our rotor program is centred around commercially flexible solutions that provide a customised approach to meeting your needs. Through the evolution of our manufacturing process, we have developed innovative solutions to extend the life of GE rotors,” added Ken.
There are significant advantages to extending the life of existing assets compared to replacement, most notably in cost and reducing carbon footprint. It also has a reduced turnaround time and it is flexible versus other rigid OEM offerings.
With the current energy transition, energy companies should look for a solutions partner to support them in navigating this complex landscape.
“Everyone plays an important role in this transition. What companies should be looking for is a partner that could provide technology [or] solutions suited to their existing assets, or the ability to develop one. This will assist in [the] transition and sustainability point of view,” said Ken. In the coming years, energy companies will be challenged on how they handle ageing or existing assets through the transition period to net-zero. EthosEnergy’s solutions will help companies take advantage of the opportunities brought by this transition.

EthosEnergy’s end-of-life rotor solutions
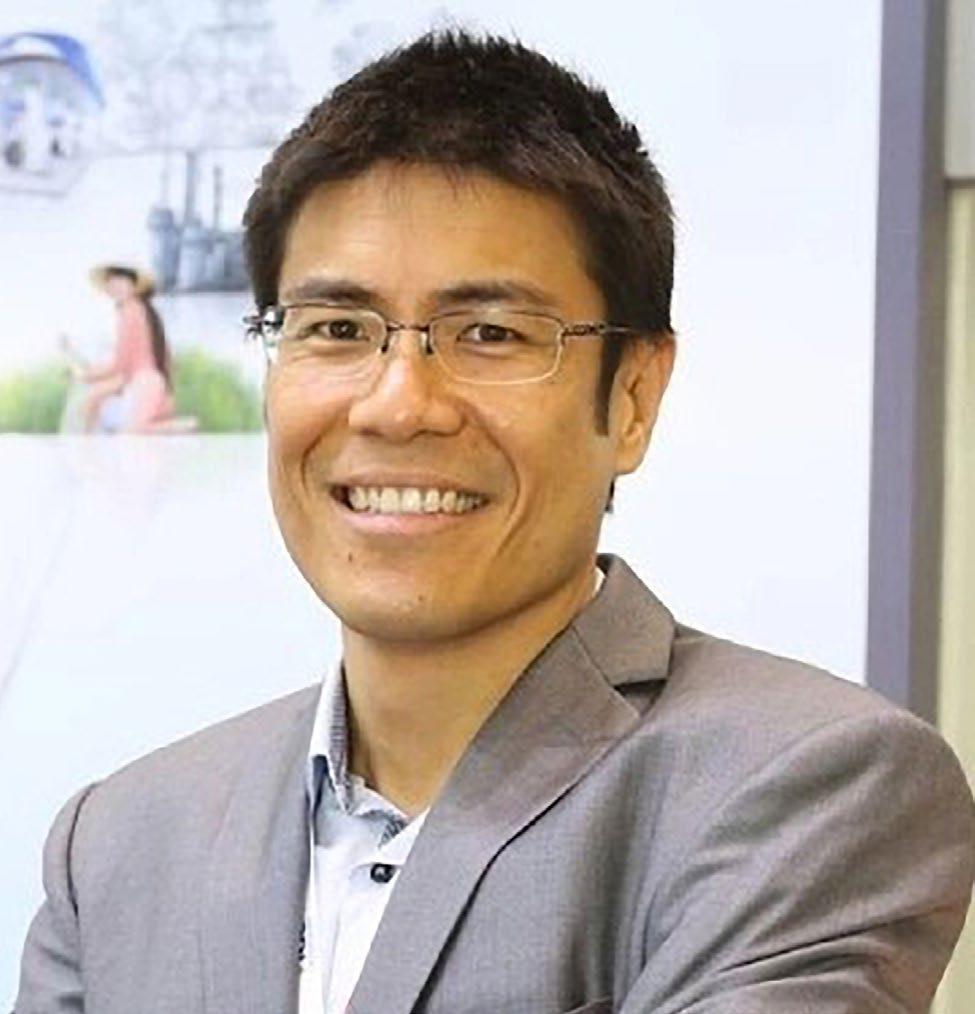

Rapid industrialisation, the increased energy demand and the energy transition present operators in the Asian power generation sector with multiple challenges. Ensuring that critical equipment in these applications can operate reliably is imperative for safeguarding the energy supply.
With a local presence in the region for over a quarter of a century, Sulzer has supported players in Asia’s power generation sector with market-leading services and solutions. An established expert, Sulzer provides around-the-clock engineering support, including speciality turbomachinery services, enabling operators to maximise equipment uptime.
Asia’s evolving energy landscape
Asia’s economic growth has driven a 200% increase in power demand over the past two decades.1 In response to this, coal, oil, gas and renewable energy infrastructure has developed rapidly. Concurrently, Asia is moving towards a low carbon future. As grid system adapts to the integration of renewables, equipment in power stations is having to adapt to different duty requirements and operating points. To reliably meet these demands takes in-depth engineering knowledge and experience.
One-stop-shop for rotating equipment
Throughout the development of Asia’s energy markets, Sulzer has proved itself as the premier onestop engineering partner for major utility-scale power plants and independent power producers (IPPs). It provides 24/7 repair and upgrade services for all types of rotating equipment, including steam turbines, gas turbines, generators, pumps, compressors, motors, and more. With over two centuries of power generation engineering heritage, Sulzer’s knowledge of legacy and modern equipment operational across the sector is unrivalled.
This is especially true for turbomachinery. Sulzer’s service centres in Purwarkata, Balikpapan, Nantong, Maitland and Vadodara offer more than 18,000 m2 of turbomachinery-focused workshop space, over 500 technical staff and seamless access to the wider Sulzer global network. These facilities are adept at servicing all types and brands of steam and gas turbines.
Providing an expanded offering to customers, Sulzer’s other 14 service centers in the region supply expert pump and electromechanical repair and upgrade services. As a global pump OEM, Sulzer delivers leading maintenance support and retrofits for critical equipment such as high-energy pumps. Complete rewinds and refurbishments of motors and generators are also available in-house.
These capabilities provide operators with a responsive, turnkey approach to repairs and upgrades for equipment from any brand.
Advanced turbomachinery capabilities
Thanks to Sulzer’s commitment to continuous modernisation of facilities across the region, stateof-the-art equipment is available for turbomachinery of all sizes. Precision machine tools and 3D laser
Energising power generation in Asia throughout Asia. This year, for example, Sulzer is supporting the major turnkey restoration of a 600 MW steam For over 25 years, Sulzer has supported Asia’s growing energy sector with turbine and generator, the biggest capacity ever advanced turbo services. managed by Sulzer. It entails replacing 31 rows of turbine rotor blades within a short timeframe to minimise customer downtime. To complete the scanning equipment support the reverse engineering repair, the turbine stator, generator stator, and and manufacture of replacement parts. Large- generator rotor are to be overhauled, supported by capacity submerged arc welding systems with specialist weld repairs, on-site commissioning, and multiple heads allow high-quality dimensional high-speed balancing. The repair required shipping restoration. The very latest CNC vertical lathes and equipment from Vietnam to Indonesia, a testament milling machines combine with a wide range of of confidence in Sulzer’s capabilities. portable equipment to support any repair. The ability Meanwhile, in China, Sulzer’s combustion autoto service big turbines is guaranteed with a cranage tuning system contributed to a 30% reduction in capacity of up to 60 tonnes and portable dynamic nitrogen oxide (NOx) emissions from gas turbines balancing for equipment up to 100 tonnes. To prove at a Jiangsu-based power plant. Furthermore, the turbine performance, non-destructive testing (NDT) project delivered a combined capital expenditure and and load testing capabilities are available too. This maintenance cost saving of more than USD 2 million completes the lifecycle of a servicing project, ensuring to the operator. a turnkey approach for customers. Recently, Sulzer’s service centre in Indonesia Specialist, technically advanced turbomachinery conducted a swift in-house repair of a 14-tonne capabilities, a global network of experts, and a steam turbine rotor for a power plant in the century of turbomachinery engineering heritage Philippines. The team minimized the lead time for are what differentiate Sulzer. Customers can benefit the repair by chartering Antonov cargo planes to from on-site troubleshooting and overhauls, material transport the large rotor to the service centre and upgrades for equipment, and digital preventative back. This ensured that the 150 MW generator, maintenance solutions. The business can also which supplied 100’000 homes with power, was manufacture or reverse engineer spare parts, reinstated as quickly as possible. including complex items such as turbine blades, using CNC machines and additive manufacturing. Asia’s energy expert This supports Sulzer’s comprehensive retrofit As the power generation landscape in Asia services, which enable existing equipment to be continues to evolve, Sulzer provides wide-ranging cost-effectively enhanced to meet new efficiency and capabilities to respond to any new demand placed on performance standards within the same footprint. turbomachinery and rotating equipment in energy This reliably extends the lifecycle of legacy equipment applications. Progressive innovation has positioned too, including steam and gas turbines. Generator the company to adapt to different requirements rewinds are another Sulzer specialism. Additionally, across the industry, enabling it to support evolving Sulzer offers turnkey coil manufacturing in-house, operational demands placed on power players due supported by its database of over 10,000 coil designs. to the energy transition. As a result, energy suppliers can effectively respond to industrialisation, population Proven in turbomachinery projects growth, and the increasing flexibility requirements of Sulzer has successfully serviced over 1’500 gas and the electrical grid – improving energy security. steam turbines, 400 plus compressors, and more By partnering with an experienced, best-in-class than 300 turbo generators in Asia. All in all, Sulzer engineering services partner like Sulzer, operators has supported over 53 GW of turbine capacity, which can continue to reliably keep pace with Asia’s energy is a sizeable contribution to regional energy security. demands well into the future. Building on this impeccable track record, Sulzer is Find out more about Sulzer’s capabilities in Asia adding to its reputation by breaking new ground here: (Link to view or download interactive PDF)
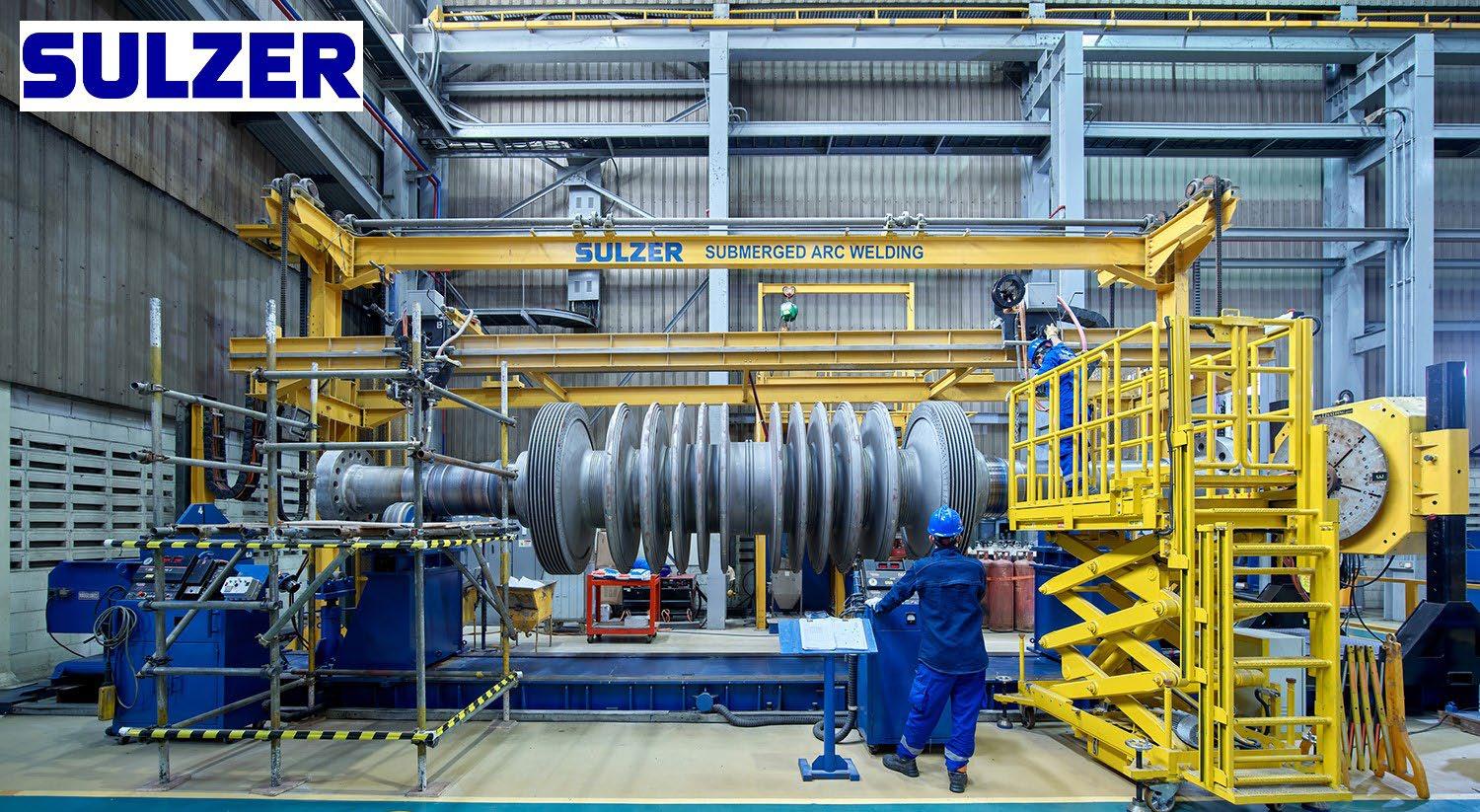