
11 minute read
How is chemicals management software adapting to meet professionals’ changing needs?
From aggregating data to creating safety data sheets, there are software solutions for almost every chemicals management challenge. Elaine Burridge reports on the latest product developments for the sector and the business needs they aim to address.
The complexity of global chemicals regulations, combined with a huge number of software packages, can make choosing the right solution difficult.
As always, new and upcoming rules are the primary drivers of demand from customers, but two particular regulatory obligations stand out this year – notably, Europe’s substances of concern in products (Scip) database (covered in detail on page 21 of this Software Guide) and the new EU poison centre notifications. Both of these are challenging companies in areas such as aggregating data and compiling notifications.
Of course, there are also ongoing requests for assistance with more longstanding regulations such as EU REACH, K-REACH, restriction of hazardous substances (RoHS), California’s Prop 65, the Globally Harmonized System (GHS) of classification and labelling of chemicals and the US’s TSCA. In addition, there are new industry and productspecific rules, such as the end-of-life vehicles (ELV) Directive and changes to the automotive industry’s international material data system (IMDS) with regard to deactivating Recommendation 019 (REC 019) standardised datasheets.
Other increasing areas of demand include the European Green Deal, which the European Commission adopted in December 2019 and which contains the circular economy action plan, further new and revised regulations such as the waste framework Directive (WFD), which includes the Scip reporting requirement, and changes to the EU battery Directive. Software providers are seeing a variety of trends from their customers. Perhaps the biggest one is an increasing focus on combining and integrating many different platforms and data sources into one system.
Integration trend According to Sanna Perkiö, founder and president of Finland-based service provider Ecobio, “more and more, customers are looking for one platform for a broad range of operations and locations in chemical management, fulfilling the requirements of several states and areas such as the EU and the federal USA”. She says the option of international corporations is to organise chemical control globally or locally, which means country-specific features, but notes that ”few suppliers can provide a solution that covers both goals perfectly”.
Service design, too, is an ongoing trend, says Ms Perkiö, adding that a playful and narrative design, smooth and intuitive use along with mobile use, are examples for design thinking that come from consumer applications.
Artificial intelligence (AI) is also an excellent opportunity for any software but here, Ms Perkiö says, the software provider must have enough data in their system and it must be ”available and useful”. While software solutions already provide automated procedures, AI can offer chemical risk forecasts, cost forecasts, and aids for monitoring and decision making.
Maaike Bilau, senior product stewardship consultant with design and consultancy group Arcadis, believes that during the next 12–18 months, software companies will increasingly try to use AI to better predict changes in regulations, based on trending developments. For example, AI can use key words and screen articles in scientific literature to pick up on the substances likely to be restricted. Ms Bilau says customers will need help with AI, in areas such as data mining and making connections.
Netherlands-based Chemycal is an example of one such organisation that can identify and predict trends and upcoming regulatory changes. Chemycal uses machine learning technologies to monitor key information sources such as governments, agencies, corporations, NGOs, research institutes, scientific journals, standardisation bodies, among many others.
Material disclosure Greensoft Technology’s president, Larry Yen, says software providers are moving into working with full material declaration (FMD) data wherever possible. Rather than just being a tool to submit and collect compliance certificates, programmes are expanding to collect FMD data and analyse and report on the details of each product and component.
Recent releases by the US-based firm include a Hosted GreenData Manager version, which GreenSoft hosts securely online for customers so they do not have to manage the software’s technical installation. Greensoft has also released add-on integration modules for the Scip database and a component disclosure module, which allows firms to set up a company-wide FMD database to meet reporting requirements for Scip and IMDS.
Mr Yen explains that the component disclosure module allows companies to provide customers with real-time and downloadable compliance data, which will automatically update when the substance data in materials change.
GreenSoft has developed an intelligent unique article ID assignment and management system in its software to keep companies’ trade secrets private. The GreenData Manager Scip software generates a displayable name for articles that allows companies to supply the required component information, article location and bill of materials (BOM ) hierarchy without exposing sensitive data, Mr Yen explains.
Manuela Dukeshire, executive with DRSoftware in Canada, believes there are two areas of focus on CBI – namely, protecting database data and knowing/ understanding specialised legislative requirements.
As companies become increasingly worried about having information accessible to external sources, Mys Dukeshire says there is a move to webbased systems based on companies’ own IT infrastructure so they can integrate their own safety measures. The information held in software is safest in the hands of the company that owns that data, she says, adding that cloud computing and servers can be very beneficial to ensure that data is distributed company-wide.
In addition, she says there needs to be a way to present substance listing data on safety data sheets (SDSs) which ensures legal requirements are covered without giving more information than necessary. Strong software is fully capable of such a balance, she adds.
Poison centre notification
The EU’s new harmonised system for poison centre notification (PCN) is an area where DR-Software has seen the biggest developments in recent months. The company launched a new integrated module in August 2019 that automates the ”highly complicated” PCN process – the first notification deadline (for consumer use) is 1 January 2021.
Ms Dukeshire describes the amendment to the classification, labelling and packaging (CLP) regulations, which introduces Annex VIII, as “a prime example of the need for automation and efficiency with regard to chemicals management software”. She adds: “The legal requirements are extensive and detailed and the act of notification encompasses so many nuances, it is very important to software users that their programme provides an end-to-end solution.” Echa’s central PCN notification portal went live in April and DR-Software has provided an option to automate bulk notifications from its ChemGes interface. SDS harmonisation is another area of focus for the software provider, which offers various modules based on language (for country-specific SDSs), as well as others for custom programming, allowing data exchanges with other software and ERP systems, and one for labels. In March, regulators from the US and Canada laid out plans to coordinate their GHS standards, with the goal to have one label and one SDS in both countries. The EU also amended in June the information required under REACH and CLP regulations for SDSs, and Japan and Russia are also bringing in ”drastic structural” SDS changes.
Denmark’s Chymeia offers software for creating SDSs, as well as forms for workplace instructions, and released a redesigned product last year. Launched after five years in development, Chymeia partner and business developer, Lars Bugge, says the cloud-based ALMEGO product is much more user-friendly than its predecessor, as well as being very
flexible. Mr Bugge says the company wanted to build a system with a high degree of logic and automation to make difficult tasks easier and use IT in a smart way. For example, by using smart rules phrasing, control, look-up and advanced calculations to produce SDSs, the manual input needed is reduced. He notes it is not AI, but a step in that direction. Mr Bugge adds that a revamped pricing model based on usage, rather than paying for a licence, has attracted smaller companies to invest in the software.
Chymeia continues to work on enhancing its workplace software and Mr Bugge anticipates that an updated model will be in place and worked into its ALMEGO brand within the next two years. He says that the company will focus on customers in Denmark and specific countries/legislation in Europe.
Cross-functional collaboration Gensuite is another provider of software for environmental health and safety (EHS) applications, including SDS, product stewardship and responsible sourcing. Donavan Hornsby, Gensuite’s vice president and strategy executive, says the company has had a big focus on cross-
functional collaboration/workflows and data digitisation, particularly in relation to Echa’s Scip notification requirements, developing an extension to their broader product steward solution for aggregating incoming supplier data, and either reporting manually or doing a system-tosystem transfer to Echa’s Iuclid system.
Other areas of Gensuite’s work have centred on product and supply chain sustainability, in particular what companies are doing with regard to using recycled and sustainable content in their products. “Over the past two years, some of our more pioneering work is digging into the supply chain to help organisations understand supplier risk, material composition and supplier sustainability programme efforts. That will grow and we will likely start evolving what we are doing there,” says Mr Hornsby.
Another customer need that Gensuite highlights is an enhanced ability to respond to requests for information from customers, which Mr Hornsby says has probably outstripped demands on the regulatory side.
Verisk 3E’s Alan Johnson, director of portfolio management and strategic alliances, says he is seeing two major trends in relation to software. Firstly, an explosion in the global population and the rise of a middle class in Asia, especially China, means that more money is being spent on products and services than ever before. Additionally, companies are creating products faster and getting better at globalisation. “The need for data products and services is growing, as is a need for us to do more with that data,” says Mr Johnson.
Speed is another requirement. As companies strive to get products to market faster, he says any upcoming regulatory changes have to be built into their data systems. Verisk 3E says its regulatory research and monitoring tools, and systems-integrated product safety and compliance content, can provide instant access to chemical data, as well as decision support throughout the product lifecycle and across the enterprise.
Last year, Verisk 3E launched its 3E Notify for Poison Centres cloud-based engine, which integrates with customers’ SAP EHS or S/4HANA (SAP’s ERP for large enterprises) platforms, as well as its own 3E Generate SDS and label authoring platform. Verisk 3E also provides services including acting as an EU legal entity for voluntary submissions on behalf of manufacturers outside the EU.
Having purchased SAP’s Content as a Service (CaaS) business and entered into a long-term strategic development agreement in February 2019, Verisk 3E is working closely with SAP in developing and delivering next-generation solutions with instant access to regulatory data to ensure global product safety, marketability and compliance.
During the past 12 months, iPointsystems has extended both the functionalities of existing products and added new ones to iPoint Suite. These include iPoint Product Sustainability, iPoint Approval, iPoint MSC Connector, iPoint SCIP Connector, CarbonBlock and SustainBlock.
CEO of iPoint-systems, Joerg Walden, says the newly released products enable customers to incorporate regulatory compliance and sustainability indicators in the early design phase.
Taking iPoint Sustainability as an example, this product allows engineers to use and analyse lifecycle information, comparing materials or parts on their carbon footprint or other environmental impacts during design, ultimately contributing to more sustainable products.
Blockchain-based solutions Both CarbonBlock and SustainBlock are blockchain-based solutions connected to data exchange platform iPoint SustainHub. With CarbonBlock, companies can communicate real data on the CO2 emissions of components along the supply chain in a standardised format. SustainBlock enables companies to track the provenance of certain raw materials sourced from conflict-affected or high-risk areas, for example minerals such as tin, tungsten, tantalum and gold.
Mr Walden says iPoint-systems is further exploring and enhancing blockchainbased solutions as customers continue to seek traceability and transparency from their suppliers. He believes nextgeneration products will carry an ”ecosystem-in-the-cloud theme”, backed by technologies such as blockchain, adding that an ecosystem approach has proven to be successfully deployed in the automotive industry with IMDS.
Cloud software company, Veeva Systems, sees a major trend in increasing awareness and demands regarding sustainability, transparency and global regulatory compliance. Knowledge about the origin and composition of raw materials is crucial to ensure any finished products can meet the regulatory and sustainability demands of the future, says Veeva Systems’ director strategy regulatory, Shawn Steuer.
He adds that clients are seeking unifying, connecting and easy-to-use tools in order to get closer to global compliance of all raw materials, formulations and products. Veeva RegulatoryOne is such a tool. It helps manage regulatory compliance, gain real-time insights and make informed decisions. Transparency is a precondition for sustainability, Mr Steuer concludes.
There is a definite trend among customers to integrate and simplify their systems, but the reality is that it is very hard, possibly nigh impossible, for one piece of one software to provide a single solution for everyone and everything.
There is, however, a growing acceptance of cloud-based systems and a preference for working with just one software provider that can consolidate systems – in essence, a one-stop shop.

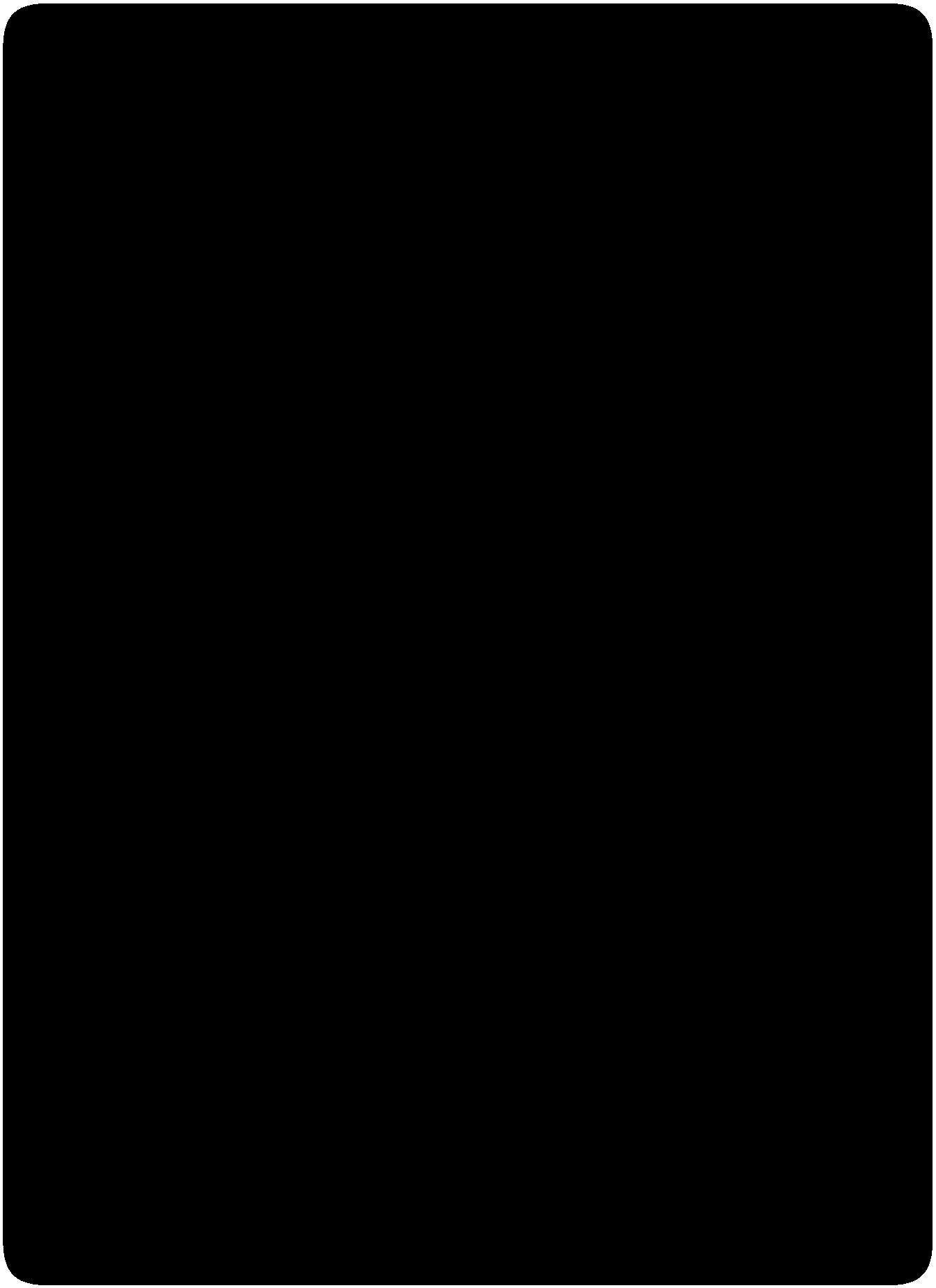