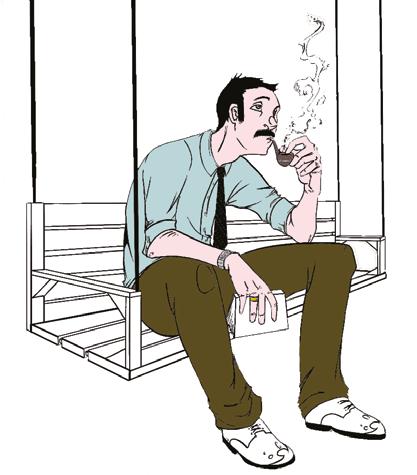
8 minute read
View from the Porch Swing
FROM THE PORCH SWING
THE ELECTRONIC BABYSITTER
Once upon a time, for a couple years, I was a single dad. It was exhilarating work most of the time. I really like my kids. They were (and are) interesting people, starting from when they were very young. Even chores weren’t so bad. We chatted about pre-school, my work, or third grade while I prepared dinner. They read to me while I folded clothes. We grocery shopped together, creating menus on the fly. And of course, fun time was fun.
But every once in a while, I needed a little help. Sometimes, I could do adult-only work after their bedtime, like paying bills. But getting a bad cold or the flu was inconvenient at best, and bringing home a project from work sometimes required my full concentration before their bedtime. Television and recorded children’s movies were my salvation. I could plop my children down in front of the electronic entertainment for a couple minutes and, voila, they’d be hooked on the Power Rangers or The Lion King for as long as I napped or worked. It was easy and magical. So easy, in fact, that sometimes it required a thoughtful, concerted effort to avoid overusing it. I wanted to be the one to raise my children, not to have Disney do it for me. TV and VCR needed to be my tools, not a substitute for me.
Electronic tools are quite helpful to me at work these days, too. At some point, I’ll transcribe these words from ink on paper into my laptop, wave my magic wand, er, um, uh…, hit the magic SEND button, and this column will instantaneously appear a quarter of the way around the world. Pretty cool, and quite helpful.
Pretty pictures on PowerPoint and projectors assist me in getting points across during training courses. During those courses, less and less time is spent on documentation because electronic tools, such as software packages, sequence, format, send, and print bills, manifests and declarations. Classifications are stored in electronic memories somewhere, instead of in binders and paper mSDSs. My smarter-than-i-am phone even has an app with comprehensive emergency response information, which I suppose makes my phone WISER-than-i-am, too.
In warehouses, Artificial Intelligence (AI) allows unmanned lift trucks (forklifts) and robotic arms to retrieve stuff from shelves and put it onto conveyance systems, which then package the stuff up and mark it without human intervention. We have some incredible tools to help with compliance.
Do I think someday AI, robots, software, conveyors, and automated assembly lines will do it all for us, all of the DG functions, without a human being for miles around?
Someday? Some day? Heck, that day was supposed to have been in our past already. About a decade ago, I interviewed for a job where the expectation was that I’d lead them into a human-less DG warehouse. I gave them a list of reasons why it couldn’t be done yet, but that I could get them 80–90% of the way there. They didn’t want to hire anyone who ‘accepted failure as his starting point’ and I didn’t want to take a job that would measure my performance against an unachievable standard. So we mutually parted. But, I keep thinking about those objections, and as DG software gets more sophisticated, wondering about how close we could be to a human-less DG warehouse. • There are two major problems with transport classifications. Some Section 14s are flat out wrong. And some classifications, mainly 9 and 6.1 (although technically 2.3 also) include subjective criteria. Each re-shipper of a DG/HazMat is independently responsible for arriving at a compliant transport classification, even if the manufacturer or upstream distributor got it wrong.
CAN’T: How do we expect a computer to determine a subjective transport classification? How do we expect a computer to fix incoming classification errors?
CAN: Use OCR (Optical Character
Recognition) to scan SDSs and use the same algorithms that a human classifier uses. Just as one example: methemoglobinemia (chocolate blood) and cyanosis (blue lips) are sufficient warnings for many classifiers to subjectively put a material into 6.1, and a computer could use the same reasoning. • I have a photo of a specialty organic solid in three different bottles, two round glass and one square plastic, yet all are the same product in the same grade in the same quantity with the same SKU number.
One of the round glass bottles is fuller than the other.
CAN’T: How does one choose just one UNspecification box-based packaging system if the inner container is sometimes short and sometimes tall, sometimes glass and sometimes plastic, sometimes round and sometimes square? A human being has to look at each particular inner, and choose from among several different, potentially appropriate packaging systems.
CAN: With some sort of optical scanning (maybe laser?) visualization and measuring system, a computer could examine the inner packagings, and be programmed to choose packaging systems appropriately.
And even easier, how about a loose fillbased V-box system? • Some products can occasionally have more than one accurate, specific, and compliant transport classification. One example includes products that can legally be offered for shipment by air as ID8000, Consumer
Commodity, or as fully regulated. Another example includes materials that don’t have to be Environmentally Hazardous
Substances (EHS) in the USA but are allowed to be treated as EHS if a shipper wants to.
CAN’T: In addition to the intrinsic properties of the products and the potential uses of the products, a person needs to consider how much is being shipped, by which mode, and to where, before the most efficient/effective classification can be chosen.
CAN: Of course, a computer system could always default to the most restrictive (fully regulated), but this isn’t always the most cost-effective. So why not program the computer/AI with the same algorithm for decision making that a human uses in the same situation? • Some products come pre-packaged and pending an inspection for damage can be re-shipped in that same packaging.
CAN’T: A human being needs to look over the package for dents, tears, stains, damage, deterioration, signs of leakage, and so forth.
CAN: Rather than the cost-ineffective approach of re-packing everything, cameras and lasers can do the inspections, comparing dimensions (such as dents in drums or crushed corners on boxes) with pre-programmed standards of acceptability.
While they’re at it, the color-detecting imaging tools could verify the compliance of the marks and labels, too. • Many packages suitable for surface transport are non-compliant for air transport. How is one to know whether the inner packagings are air compliant?
CAN’T: Heck, people still screw this one up all the time. But, often, a phone call to the original manufacturer can answer questions about use of cushioning, presence or absence of absorbent, and inner containers of liquids meeting the pressure test or not.
CAN: Re-pack all air shipments of liquids (not necessarily solids), or forbid all liquids from air transport, and/or flag these upon receipt to have a peon human in some remote location make the phone call to the original manufacturer before any air orders are accepted. The results of the phone call would be stored in an accessible DG database. • Some products are compliant in one classification in one country, but noncompliant when they arrive at another country, with no one classification suitable in both countries. Some examples include
Combustible Liquids to and from the US, and other examples include materials that react with water to release toxic gas but have no other regulated hazards.
CAN’T: People screw this one up all the time, too. But the most common fix for IBCs or portable tanks of Combustible Liquids is to have marks and labels either applied or removed at the destination seaport, depending upon which direction the product is moving.
CAN: Create a standing arrangement with various destination seaports to ‘fix’ the types of incoming shipments that cause problems, and then for each new problem order have the warehouses’ automated systems send to the affected seaport a pre-written email template with the shipment details filled in. • Drone deliveries?
I can’t believe you went there. Don’t go there. At least not now. Maybe in some future column.
Many of the reasons why we CAN’T have human-free shipping operations are capable of being turned into reasons we CAN, if only we have the right e-tools. And though we already have some problems that people have difficulty handling, such as multiple classifications and different packaging requirements for air, we’ll either get those ironed out (hopefully sooner rather than later, especially 4.3 ≠ 4.3 worldwide), or we’ll just apply the same pattern of thinking (decision trees) that a person would use, to the new electronic tools. And I’m sure we’ll continue to develop new e-tools for DG, but they’ll be phased in as costs allow, just as the cost of using e-babysitting tools is factored into how frequently and how often they are used. It’s easier to measure the costs of DG e-tools though, as they are primarily monetary. For child-rearing, the costs of using those e-tools may not be apparent until long after they’ve been over-used. Eventually, prices will drop and I most certainly can envision a time when almost all of the DG shipping functions will be performed by robots and other e-tools. How fast that happens, I’m not sure, but it is happening.
That’s way different than e-tools to occupy children, though, because as a grandparent I’m as opposed to their overuse as I was when I was a mere parent.
This is the latest in a series of musings from the porch swing of Gene Sanders, principal of Tampa-based WE Train Consulting; telephone: (+1 813) 855 3855; email gene@wetrainconsulting.com.