
5 minute read
Digitisation comes to US petrochemicals
SHOCK OF THE NEW
DIGITISATION • NEW TECHNOLOGIES ARE TRANSFORMING CHEMICAL SUPPLY CHAINS AROUND THE WORLD BUT THE US PETROCHEMICAL INDUSTRY FACES SOME PARTICULAR ISSUES
E-COMMERCE HAS WROUGHT a revolution in customer behaviour in recent years – but largely so far in the consumer sector. Individuals have come to expect that they can order goods online, wherever they are in the world, and they will be delivered promptly (even on the same day in some cases) to a specified point. During the delivery, the customer can keep track of where the goods are and get a definitive estimated time of delivery (ETD) that, in all but a few cases, is met.
Those same consumers are often also working in industry so it is no surprise that they are coming to expect the same degree of visibility for their industrial products. And while some producers in the chemicals sector are responding to that call, there are challenges to be faced. Those challenges will be discussed during the Petrochemical Supply Chain and Logistics conference, due to take place in Houston on 10 and 11 June, coronavirus permitting.
Ahead of the event, the organisers gauged the tenor of the industry with interviews with three specialists in the sector to get their views on the pace of implementation of the digital technologies necessary to create an ‘Amazon effect’ in the US petrochemical industry, the barriers that are holding up that implementation, and what a broad application of digitised systems will mean. DIGITISATION IN PRACTICE As digitisation arrives in industry, it is beginning to become apparent that there are three areas where it can make a difference: - In purely internal terms, through improvements in enterprise resource planning (ERP) systems, accuracy of forecasting and planning, and automating the order-to-cash cycle - In inter-company communication, improving accuracy and delivering improved customer service, and - In the application of digitised hardware, such as ‘smart’ equipment in the process industries, drones in delivery applications and completely global mobile tracking. Each of these delivers similar outcomes: enhanced visibility throughout the supply chain, the availability of real-time information to all parties, a reduction in errors, and better accuracy.
But, as is also becoming apparent, corporations adopting digitised systems need to keep the human factor in mind. Digitisation cannot replace the organisation or individuals within it, and must be designed in such a way
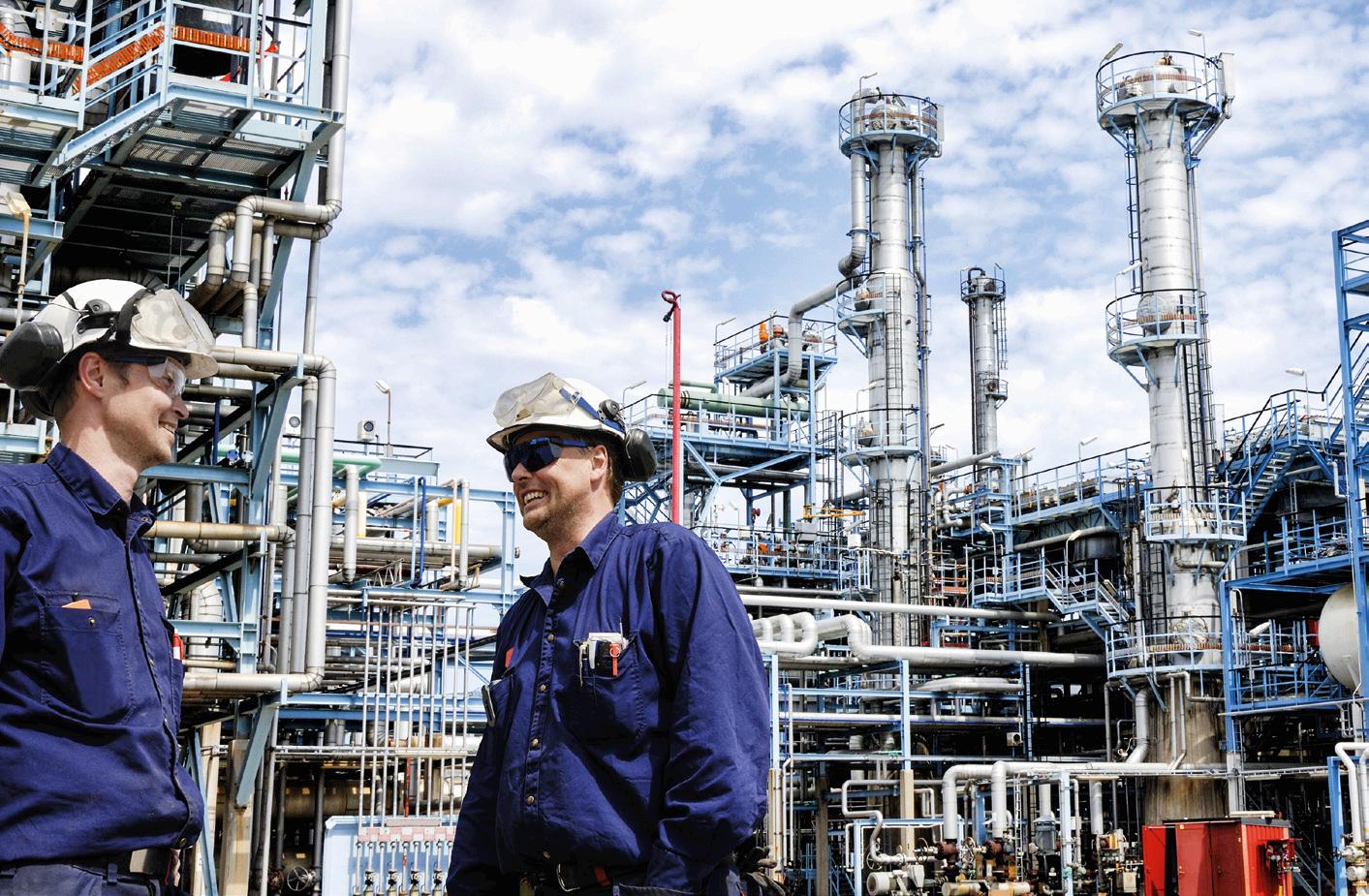
as to complement and enhance their efforts. It is people that are going to have to work with these emerging technologies and their needs must be also taken into account.
Businesses are, though, often faced with a major problem early on in the path towards digitisation: the need to deal with legacy systems. Upgrading to a newer ERP system is comparatively straightforward – although often expensive - and something that is happening across the petrochemical industry right now; that process is also helping to simplify software structures across larger corporations and is tending to use cloud-based applications to ensure that all locations are working from the same version.
However, that process is also making it very apparent that there are some legacy applications, perhaps decades old, that have to either be replaced or be incorporated in some way into the new systems.
BARRIERS TO BELIEF Those interviewed prior to the conference were keen to point out that, while many petrochemical companies have the financial resources to build digital supply chains, the process of actually doing so is hampered by the industry’s conservative mentality. To some extent, that reluctance to adopt new technologies is simply a reflection of the potentially gigantic risks if something goes wrong as a result. So, while most petrochemical companies have installed automated systems to replace manual labour, moving towards automated control is widely seen as risky.
Then again, while that approach might be advantageous, it also leaves manufacturers vulnerable to the emergence of new competitors or disruptors in the industry, more open to the idea of using new technologies to find new ways to meet customer needs. That risk is rather more apparent in the supply chain than in chemical manufacturing, but as logistics represents a significant part of the delivered price of chemicals, there is a margin available for those willing to think outside the traditional means of supplying customers.
Some systems are already being taken up by existing players in the field. Predictive analysis is being more widely used to fill in the gaps in visibility and to determine how interruptions in the supply chain can be managed. It is inevitable that a supply chain will not work perfectly all the time – traffic delays, strikes and breakdowns can all cause delays and are out of the control of the supplier.
Internet of Things (IoT) platforms can be applied here to improve predictive analysis by linking all data inputs in a single system; this can then sense and react to actual conditions along the supply chain and recommend – or even implement – changes in routing or dispatch activity to compensate.
Those IoT platforms can also be used to add visibility to goods in transit and, at the same time, feed data into management systems and into other analytics processes to improve the quality of decision-making.
WHAT’S NEXT The US petrochemical sector also seems eager to leverage the potential provided by blockchain systems to keep track of shipments along international supply chains and to share that information among the various participants. This will prove particularly useful given the recent upsurge in new investment in polymer production capacity as a downstream outlet for the huge new wave of feedstocks emerging out of the shale gas bonanza.
More prosaically, transportation management systems (TMS) are being increasingly used and developed through new technologies. Producers have been showing themselves increasingly willing to boost their TMS’s utility by importing data from other sources to help in making decisions. That may involve the use of blockchain techniques, coupled with artificial intelligence or machine learning, to replace a lot of the manual input into routing and scheduling.
From a European perspective, it does feel as though the US petrochemical industry is a couple of years behind its European counterpart, as the same conversations have been staples of conferences in Europe for a while now. But at least the conversations are the same: that suggests that the sector is facing the same hurdles wherever it is located and each region could usefully learn from the experiences of others.
As with everything in this most unusual of years, however, the impact of the coronavirus pandemic on industry’s ability or willingness to invest in change is as yet unknown. That will undoubtedly form part of the conversation at the June conference and at other events that will be held once the worst of the outbreak is over.
ADOPTION OF DIGITISED SYTEMS IN THE PETROCHEMICAL
SECTOR HAS BEEN SLOW BUT, ESPECIALLY IN THE US,
THE EMERGENCE OF NEW PRODUCT STREAMS AND
ADDITIONS TO PRODUCTION CAPACITY ARE MAKING THEIR