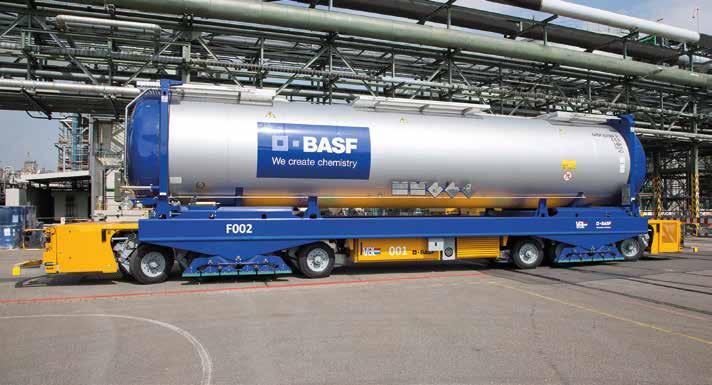
10 minute read
ITCO programmes to promote tank use
REVVING UP
MEETING REPORT • ITCO IS ACCELERATING ITS PROGRAMMES TO HELP PROMOTE TANK CONTAINER USE, WHILE GETTING TOGETHER MORE REGULARLY TO DISCUSS IMPORTANT ISSUES
THE INTERNATIONAL TANK Container Organisation (ITCO) has re-elected Reginald Lee to serve another two-year term as president. The decision was taken at ITCO’s Asia Regional Meeting in Singapore last month, and followed on from a period of intense activity following the merger of ITCO and the Asian Tank Container Organisation (@tco), formerly led by Lee, at the start of 2018.
In a letter to ITCO members, Lee highlighted some of the achievements of his initial tenure. Apart from the consolidation of ITCO and @tco, the profile of the Organisation has been raised through a series of meetings in Europe and Asia and the publication of several articles, not least in HCB. The ITCO board has also agreed to continue its campaign against the use of flexibags by the chemical industry, on environmental and safety grounds.
Lee also highlighted the expanded use of the ITCO e-learning programme, with two free licences given to each ITCO member; it is also now a condition that each member company should have at least one of its senior management team take and pass the online course.
In addition, Lee reported that he has established a good working relationship with the Association of International Chemical Manufacturers (AICM), the Shanghai-based body that represents overseas chemical producers working in China. Furthermore, it has been arranged for a tank container to be provided to the Shanghai Maritime University; this will be used by its supply chain students as part of a focused course on bulk liquids distribution, based on a version of the ITCO e-learning course.
“I believe there is still a lot of work to do if we are to continue expanding the safe use of tank containers as one of the most costeffective modes of shipping bulk liquids when used as a part of a company’s liquid supply chain,” Lee said in his letter.
A BIGGER TANK The Singapore meeting came hard on the heels of ITCO’s Antwerp member meeting, held in late September. The two-day event offered the opportunity for ITCO’s divisional boards and working groups to speak faceto-face and there were a number of keynote presentations on topics of interest.
Dr Thorsten Bieker, vice-president of rail and site services at BASF, updated participants on his company’s current project in the use of high-volume tank containers for in-plant and intra-plant logistics. There may well have been some in the audience who had heard Dr Bieker talk about the same topic a few years ago at the European Chemical
BASF’S NEW ULTRA-LARGE TANKS OFFER THE
Transport Association (ECTA) annual meeting and would have been interested to hear about the progress being made. Indeed, so much progress is being made that the UN Subcommittee of Experts on the Transport of Dangerous Goods is now having to figure out how to describe the specifications for this new breed of ultra-large tanks.
The new tanks designed for BASF offer a volume of up to 73,000 litres and payload of 66 tonnes – more than double the comparative figures of a standard tank container or even swap tank and comparable to that of a rail tank car. As a result, more product can be moved around the massive Ludwigshafen plant more efficiently – especially when the tanks are being moved by autonomous vehicles.
Until the introduction of the new tanks, BASF was spending a lot of time building and moving trains within the boundary of the Ludwigshafen plant. It could take 22 hours from the point where product was loaded to its destination. That process has been cut to one hour, from ordering the tank until its delivery at the loading point.
BASF now has three manufacturers approved to produce what are known as ‘BASF Class’ tanks – Van Hool, Magyar and CIMC – and two operating companies, Hoyer and Bertschi. Tanks are available in L4BH, L4DH, L10BH and L10DH specifications. It has also bought specialised rail wagons from Tatravagonka and Greebrier/Astra.
BASF is now working on a risk analysis for the transport of chemicals in bulk by tank containers on rail, the results of which are expected next year. After that, BASF has plans to build a new terminal network capable of handling these large tanks; it also sees opportunities in intermodal transport, even in long-haul rail lanes between Europe and China. GET PLUGGED IN Also at the Antwerp meeting was Tim Mertens, assistant in the logistics processes – technology and infrastructure department at Evonik Degussa Antwerp. He looked at the evolution of cloud solutions in chemical clusters, focusing on Antwerp, where Evonik employs more than 1,000 people. The process of digitisation is raising new opportunities and everyone wants change – but it is hard to find anyone to lead that change, he noted.
Mertens used as an example of change the development of the electronic European Cleaning Document (e-ECD), a project in which Evonik was involved through its membership of Essenscia, the Belgian chemical industry association, which was one of four groups working together to develop the concept and is now a partner in Eclic, the body managing e-ECD.
How does this differ from the process of digitisation that companies have been working »
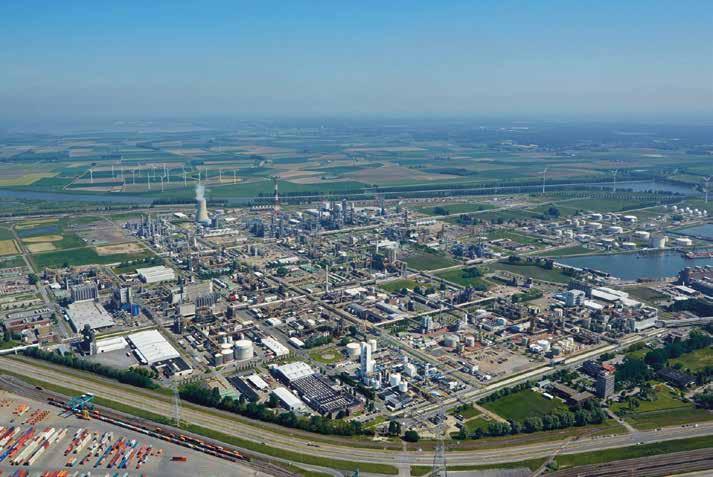
with for years? Most companies now have integrated information flows using EDI and ERP systems, but they have not changed the way that businesses work. Indeed, Mertens suggested, they have in fact entrenched the old habits. There is still a ‘silo mindset’ in many companies, focusing on day-to-day transactions. New systems have the ability to foster more intelligent processes – but are employees (and managers) ready to engage more actively with information?
The chemical industry is excellent with process technology but as digitisation takes hold there is a multiplicity of new and very intelligent tools out there that can make use of the data already available to enhance business efficiency. Established providers such as SAP and DHL are now making use of some of those techniques, while new software systems exist that can foster collaboration between employees. And blockchain technology will open up yet further possibilities.
Some companies appear overwhelmed by those possibilities; they are still struggling with IT security and perhaps they believe that establishing information-optimised processes will take too long and cost too much. However, Mertens said, the e-ECD project shows what can be done when there is the will to see it through.
He urged the audience to get involved and take advantage of those new technologies that will speed up global systems implementation. Companies need to be open to different skill sets among their employees, who will need to react fast and spot opportunities early. They also need to be open to a collaborative model, involving the sharing of information across and outside the organisation.
LOCAL BOY MAKES GOOD Also giving a local perspective was Paul Wauters, the Port of Antwerp’s Harbour Master. His department is responsible for taking all measures necessary to safeguard public order, peace, environmental integrity and security in all port activities. That includes the regulation of the handling, loading and unloading of goods, and access to and traffic within the port area.
In terms of dangerous goods, the Port of Antwerp relies on the International Maritime Dangerous Goods (IMDG) Code for seagoing transport, ADR, RID and ADN for hinterland transport, the port’s own Municipal Port Regulations and Port Instructions.
Before dangerous goods can be moved in the Port of Antwerp, a declaration must be submitted to the Antwerp Port Information and Communication System (APICS); this applies to goods being loaded, discharged or kept on board. The person responsible for making the declaration must be properly trained. Containers carrying dangerous goods must be kept at a recognised container terminal with a maximum 10 days dwell time. An extension to that 10-day period can be requested but only in exceptional circumstances – financial issues or transport organisation issues are not sufficient reasons. “A container terminal is not a temporary storage location for dangerous goods,” Wauters said.
Pre-declaration of dangerous goods arriving in the port gives the Harbour Master’s Department time to check that the declaration is correct and complete and that the container can be properly segregated within the terminal in accordance with the IMDG Code. The information will be shared with national and international authorities and will also be used if an incident occurs.
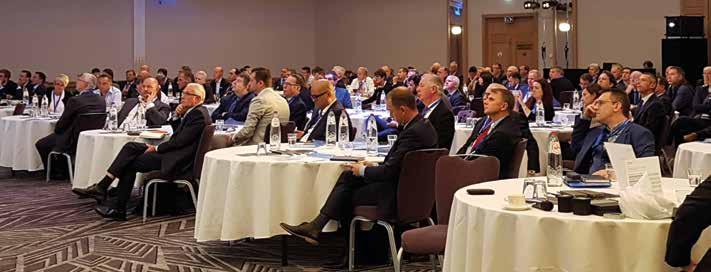
TWO CODES TO ONE Looking specifically at tank containers, Wauters spoke about the confusion that can arise due to the different specifications for tanks between the ADR/RID/ADN system and the UN T-code system for portable tanks. It is impossible to tell just by looking at a tank which specification it was built to, but there are different construction and equipment requirements.
For instance, UN 1230 methanol requires either an L4BH tank under ADR or a T7 tank under the UN system. Both tanks have three bottom openings and a calculation or minimum test pressure of 4 bar. However, the ADR tank must be hermetically closed, while the T7 tank has normal pressure relief requirements. Wauters showed a picture of a tank carrying methanol from Antwerp to Hamburg, which had two codes marked – L4BN and T11. According to the T-code, such transport is allowed but not according to the ADR tank code.
Wauters explained the position thus: a tank is either a tank container or a UN portable tank, not both. The UN system is designed both for sea and land transport, while an ADR tank code is good only for land transport. Tanks showing both codes can cause confusion for the consignor, loader and port authorities and result in delays in loading, refusal for loading, fines or a frustrated shipment. Wauters advised tank operators in the audience to remove the ADR tank code from their UN portable tanks.
CORROSION CONFUSION The final presentation came from Drs Penelope Cooke and Ken Kirby of Brookes Bell, who analysed the potential risks to tanks from improper cargo classification and the problems of corrosion. They were particularly interested in some parts of the IMDG Code, notably that which says, “Unless provided otherwise by this Code, the following are forbidden from transport…”. It then lists “any substance or article which, as presented for transport, is liable to explode, dangerously produce a flame or dangerous evolution of heat, or dangerous emission of toxic, corrosive or flammable gases or vapours under normal conditions of transport”. That seems to cover six of the nine classes of dangerous goods.
However, there are various ways by which ‘normal conditions of transport’ are altered, including the means of packaging, stowage and segregation and, more specifically, refrigeration, heating, the use of pressure tanks, consignment in small quantities, or the use of diluents.
For a consignor, the proper classification for transport is the starting point. Having identified the correct UN entry, proper shipping name and packing group (using the safety data sheet), the IMDG Code will explain what type of portable tank (if any) can be used and what portable tank special provisions apply.
What the speakers wanted to highlight was the issue of corrosive substances. In the IMDG Code, ‘corrosivity’ covers a wide range of products, which may be corrosive to some or all metals and to skin, or only to some of those. They listed a number of substances that are not authorised for carriage in portable tanks due to their corrosivity or other properties, while other substances that are corrosive to most metals – such as UN 3298 iodine monochloride – are authorised.
The speakers reminded the audience of what makes stainless steel ‘stainless’ but also that it can corrode in certain circumstances. Stainless steel is generally corrosion-resistant, even to sulphuric and nitric acids; chromium in the steel forms an oxide layer a few atoms thick, termed the ‘passive’ layer – but this can be compromised. Damage can be caused by aggressive halide ions, contamination, physical damage, low-oxygen environments or under-deposit corrosion. Any breach in the passive layer allows the formation of a corrosion cell that can then prompt further corrosion, although in the right conditions the passive layer can repair itself.
The speakers pointed to the new standard, ISO 10855:2018, which covers the design, manufacture, periodic inspection, examination and testing of UN portable tanks. It includes a number of scientific methods to be used during intermediate and full periodic inspections to check the structural integrity of a tank and to detect any faults that might render the tank unusable. HCB
ABOVE: REG LEE HAS ANOTHER TWO YEARS TO The next major event for ITCO will be the Tank Container Village during the Transport Logistic show in Munich from 4 to 7 June. More details on that and all other ITCO activities can be found at www.international-tank-container.org
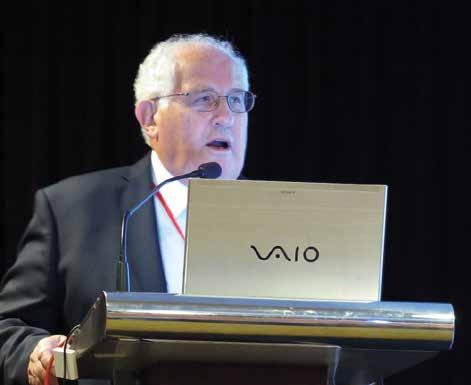