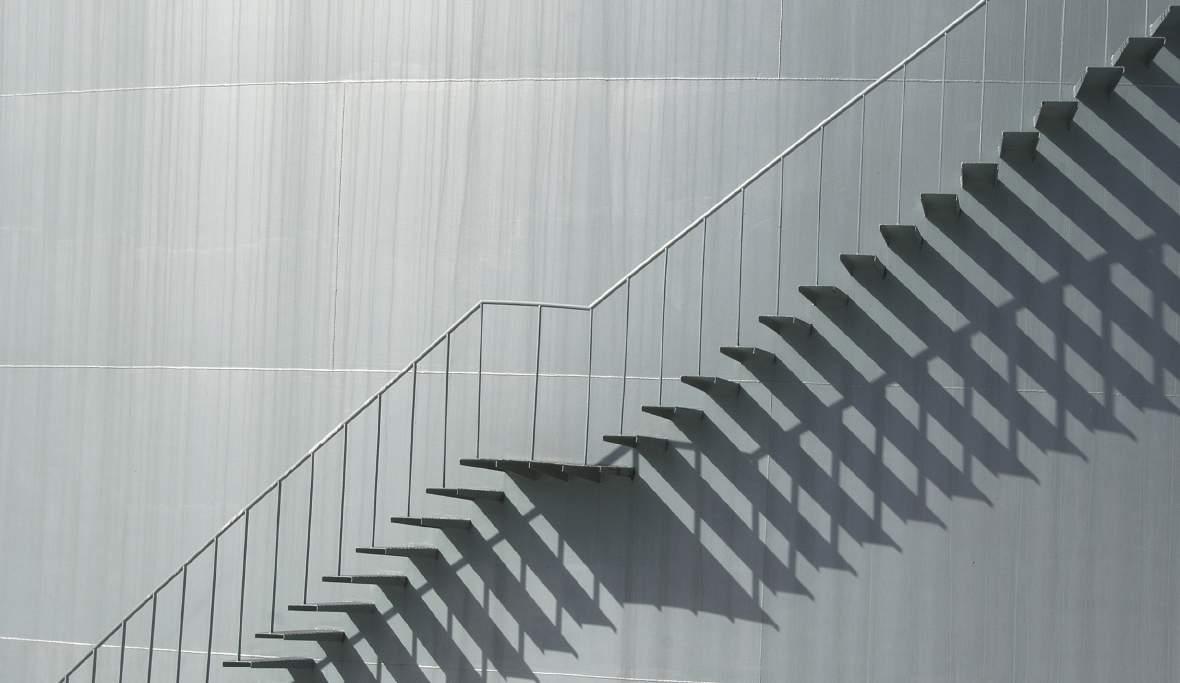
120 minute read
Years Ago 04 Learning by Training 05
Ita sundit adit accabo. Nequas et, te laut vent, voluptas dellatibusa volo qui abo. Caeptam fugit, que volorecabo. Ut verum in reicae nim qui consequ assunt.
Volupta exerate verovit lita sequas re etument pliti berrore iciati quiaeperiae volupta tatate nonem. Ro issi consequis parum aut liamusam exerae cuptum, untis dem re quidem eaquuntota sum nos acias dit aut eatem earum quatemporem aped quatquaes dunt eumquibus, as et que nonsequis dit venia vid qui sererorro blametur? Ehenisquasim veni doloreroremo blatur?
Obist, architatur? Qui re deritas volore necum imporisqui doluptate porem exeris endi dolenihilia de et fugiaspient.
Epudae doleste cullit liae lati tem fugia dellame niendic tem inum voluptam et optatur rempos nimet et officit, totatem quaepudist utas conse nost qui accus dolupis rehentis res aut inimet acest, qui nemporpos adipidus ea volupta quaecti optam fugitae quaesto tatquid endelia acia volor re, sanisit hicia aut rem quiandae vent quae eum quaspere plam qui omniet a net aut et rem. Tem asperov itatioreptam essundesti dolorum re dereicate doluptatibus int de nos volenis volo mo blaboribus dolorumque dus excearuptio. Maximpero vel moluptatusa dolupta eperrum qui volupta simusciis archica boribus maio. Et asimi, corepelis porerum etur, volorunt ipsanda epeles iundis que debitiam eum quoditatus eveniationse nim fugitis di rest ut ommoluptat odis arum nossit velendus etur? Harcita epersperion corunt.
Online meetings and webinars
The following meetings will take place online: • 6 December 2022: TSA Energy
Transition Committee • 8 December 2022: TSA Council • 15 December 2022: TSA SHE
Committee For more information on TSA’s meetings, write to info@tankstorage. org.uk The Tank Storage Association has launched a new Instagram account. Stay up-to-date with all our latest news by connecting with us @uk_tsa.
TSA’s annual review of the UK’s bulk liquid storage sector is available at www. tankstorage.org.uk/ publications
Autumn Statement & 2023 Rating Revaluation
Business Rates bills are all based on the product of a Rateable Value and a Multiplier. On 17th November 2022 in his Autumn Statement, Chancellor Jeremy Hunt confirmed that the 2023 Rating Revaluation in England and Wales would proceed, with a valuation date of 1st April 2021. This is the first Revaluation since 2017, which had a valuation date of 1st April 2015. This six-year gap is very unfortunate. The proposed 2022 Revaluation was changed to be from 2021 which was then cancelled altogether due to the Covid pandemic. The Devolved Administrations in Scotland and Northern Ireland are now expected to confirm their own 2023 Revaluations.
New Rating Assessments come into force from 1st April 2023, but there are important differences in the valuation dates. In England and Wales, the valuation date is 1st April 2021, a date chosen by the Government to allow the impact of the Covid pandemic to be considered. This followed a law change ruling out any Rating Appeals citing Covid as a “Material Change in Circumstances”. In Scotland, the valuation date is 1st April 2022. In Northern Ireland, the 2023 valuation date is 1st October 2021, with their last Revaluation having taken place in 2020, with a valuation date of 1st April 2018.
“It is an important principle that (rates) bills should accurately reflect market values” said Mr Hunt in his Autumn Statement. This is widely agreed. A Rateable Value is an estimated annual rental value. For most properties such as shops, offices, and warehouses, there is rental evidence available to set Rating Assessments. The big winners from 2023 are the Retail and Hospitality sectors, where Rateable Values have come down, reflecting the drop in retail rental values, and where there are also further support measures. The good news in England, for all ratepayers including TSA members, is that the 2023/24 mulitiplier is frozen at the 2022/23 level, a reduction of over 10% in Rate Liability. The Industrial and Logistics sectors have seen rental value increases, resulting in higher draft 2023 Rating Assessments. The industrial theme applies also to the Bulk Liquid Storage sector. There is no rental evidence, so Rating Assessments for Bulk Storage terminals are set using a Depreciated Replacement Cost approach, combined with a Decapitalisation Rate which is set by each Devolved Administration.
Replacement costs for Rateable plant and Machinery, and commercial property values, increased from 1st April 2015 to 1st April 2021. The Welsh Assembly invited representations regarding the setting of the Decapitalisation Rate for the 2023 Revaluation, which included a submission from this practice. The Welsh Assembly correctly decided to reduce the Decapitalisation Rate, by 11%. A quick study of TSA member terminals in Wales indicates 2023 Rateable Values rising by no more than 20%. In England, no consultation took place about the Decapitalisation Rate, with the same figure retained from the 2017 Revaluation. This is incorrect and too high. Representations are now needed to seek to correct this for the many industrial businesses affected, including TSA members. For England, draft 2023 Rateable Values are typically 30% up on the 2017 Rateable Values. The good news is that next year’s rates bills are limited to a cap of 30% above this year’s bill, and with no 10% inflation factor. No significant changes are expected next year in Northern Ireland, with the 2023 Revaluation following on soon after the 2020 Revaluation. Final thoughts though are on Scotland which has a valuation date of 1st April 2022, so there are seven years of cost and land value increases to consider! At the time of writing, 18th November, no further details for Scotland, Wales, or Northern Ireland are known.
Author
David McCausland is Head of Rating at Farebrother Chartered Surveyors. He is a known specialist in the bulk liquid storage sector, a member of the UKPIA Rating Panel, and a guest lecturer for the RICS Rating Diploma course (Plant & Machinery Module).
REDUCING OIL STORAGE TERMINAL EMISSIONS THROUGH DIGITALISATION
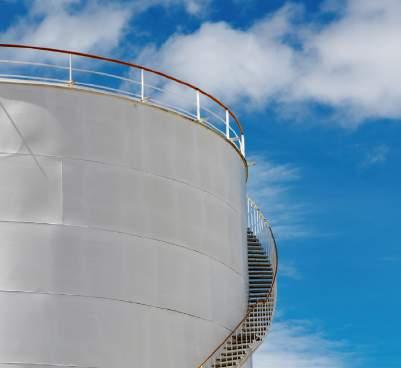
he European Union has ambitious emissions reduction goals. The European Climate Law seals the EU’s commitment to reduce greenhouse gas emissions by at least 55% from 1990 levels by 2030 and become carbon neutral by 2050. Additionally, the United Kingdom has its own goal to reduce emissions by 78% compared to 1990 by 2035 and reach net zero by 2050. Naturally, these goals affect all industries, the oil terminal industry included. Efforts to reliably reduce energy consumption and emissions will require clear visibility into operations — not guesswork — powered by innovation and new monitoring technologies.
Digitalisation and the data-driven decision-making it empowers are not new to the European tank storage sector. By integrating connected technologies throughout terminals, businesses have received many advantages, including lower costs, greater reliability and lesser risk. One of the elements in the terminal to recently receive greater digital capability is the thief hatch. Almost half of all emissions in major oil basins are from storage tanks, and a primary way that emissions escape is through open thief hatches. Storage tanks are typically located on remote sites that can cover many kilometers. They may go days without a site visit and physical inspection. If thief hatches are accidentally left unlatched, they may go undetected — and release fugitive emissions — for a long time. Remote thief hatch monitoring helps terminals identify any unsealed hatches quickly, which can significantly reduce emissions.
Thief hatches have several important functions. They serve as a tank’s maintenance access hatch and the primary level of pressure protection for venting and vacuuming. Thief hatches have historically allowed producers to check tank levels and media properties required to complete custody transfer; however, because of fugitive emissions and worker safety, this is a practice the industry is trying to move away from.
During site visits, thief hatches are frequently accessed by a variety of personnel measuring the contents of storage tanks, transferring fluids to and from the tank or testing the thief hatch seals. Unintentionally, hatches may be left fully open or, more frequently, closed without being securely latched. Without reliable monitoring, days or weeks
may pass before personnel notice an open or unsealed hatch and close it. As chemicals evaporate, the vapors escape through the open hatch and enter the atmosphere.
As a sealing element, thief hatches are inherently subject to leakage. While manufacturers and producers have long collaborated to develop better, tighter sealing thief hatches, no seal can account for a failed closure. A newly built, closed and properly sealed thief hatch can limit emissions, but a hatch left open or not fully sealed allows emissions to continuously vent out into the atmosphere. Not only is this an environmental concern, it can also result in lost product.
Monitoring solutions help terminal operators to confidently know that a hatch is sealed. The latest technology can provide precise data that includes how long each hatch at a terminal is open and confirmation that it’s closed and securely sealed after access, which can allow for measurement of total site emissions.
Improving monitoring accuracy and device installation
While thief hatch monitoring solutions have been available in the past, these early designs had a consistent issue — false signaling. The first monitoring systems sometimes made no distinction between a latched and unlatched thief hatch switch, which resulted in a false trip. A false trip can have substantial consequences. Since the thief hatch may display
Remotely located oil storage terminals often receive infrequent personnel visits, which means that open thief hatches may not be detected for long stretches of time. (Image courtesy of Emerson)

Emerson’s thief hatch monitoring solutions offer simple installation on both new and existing thief hatch models and can reliably sense that thief hatches are properly latched. (Image courtesy of Emerson)
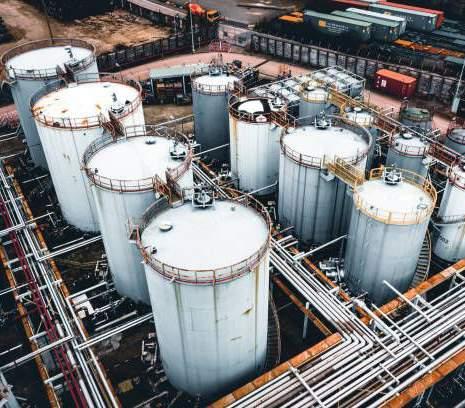
as open when it is, in reality, closed and latched, operators may invest unnecessary time manually checking thief hatches.
Another challenge is the sheer range of thief hatch designs in the field. There can be thousands upon thousands of thief hatches in terminals, from brand new to decades old. It’s essential that a monitoring solution easily installs on and fits multiple models and designs. Mounting patterns, latch positions and angles differ from product to product.
There are now advanced solutions that address the biggest challenges in thief hatch monitoring. The latest monitoring technologies reliably sense a thief hatch is properly latched
Emerson’s AVENTICSTM Series AF2 Sensor continuously monitors air consumption in pneumatic systems and provides insights that can help terminal operators quickly detect and address leaks. (Image courtesy of Emerson) and easily install in the field on both new and existing thief hatch models. Producers can receive these solutions in modular mounting kits that allow them to retrofit their thief hatches in the field using only simple tools.
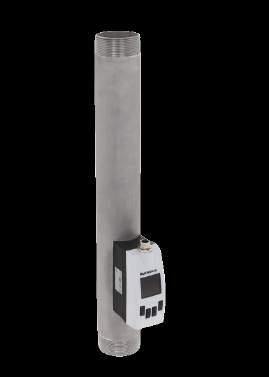
The kits include an ultra-reliable, sophisticated proximity sensor and easy-to-install wireless transmitter that precisely and continuously monitor hatch position in real time, allowing operators to confidently ensure that hatches are fully sealed when not being accessed.
The precision position sensor is specifically designed to signal only when a lid is fully latched. Proven in mission-critical, process applications, it features a robust bracket design that guarantees no false signaling will occur. The sensor is designed to reliably operate in high- and lowtemperature extremes and highpressure and potentially explosive environments.
Like a proximity switch, the sensor has no moving parts and uses magnets to detect a ferrous metal or magnetic target. Like a limit switch, it provides highly precise readings. By combining these features, the sensor requires far less maintenance than traditional limit switches and performs within harsh environments that often prohibit the use of other technologies, such as inductive or capacitive sensors.
The sensor can connect to the wireless transmitter, which offers control system access to discrete points that are otherwise not connected due to wiring costs and lack of input/output. The transmitter automatically keeps a time-stamped record of each time the thief hatches are open and closed. Operators can access a 24-hour automatic log of thief hatch status, which reduces the need for visual tank inspections. Since the connected sensor doesn’t draw power, optimising the battery life of the wireless transmitter, both devices are certified for global explosionproof applications.
The simplicity and sophistication of the design allow producers to easily install the system on both old and new thief hatches and remotely monitor their status without false trips. This helps ensure that emissions readings are accurate and reduces personnel trips to the field.
Identifying opportunities to reduce energy use
In addition to thief hatches, there are many other opportunities in oil terminals to reduce emissions. If left unchecked, pneumatic systems can use more energy than they need, resulting in excess consumption and higher carbon emissions. By optimising the energy consumption that pneumatic systems use, terminals can reduce emissions levels.
One way to optimise the energy use of pneumatic systems is by detecting
and addressing compressed air leaks. Compressed air production can be responsible for a considerable percentage of a terminal’s energy use. If there are leaks in the line, more air than necessary must be produced to compensate for what’s lost. Advanced air flow sensors can continuously monitor air consumption in pneumatic systems, and the visibility can help terminals reduce energy use as well as unplanned downtime. These stand-alone sensors are more than flow meters — they provide diagnostic data and insights that help operators quickly detect and address leaks and perform predictive maintenance that can prevent leak formation. Sensors can also interface with digital control and other systems and be retrofit on an existing pipeline up to 50 millimeters.
Another way to reduce energy consumption and, in turn, emissions is to replace solenoid operating valves (SOVs) with lower-wattage models. There are now Ex d directacting valves available that use less than 2 watts. This can save more than 10 watts per SOV compared to standard models, which translates to a savings of 87.4 kilowatt hours. This may not sound like much, but terminals can have hundreds of SOVs that can usually last 10 years before replacement. Plant-wide energy savings and emission reduction can be significant.
Some terminals may use smaller valves commonly controlled by a rack-and-pinion actuator. These are usually NAMUR-interfaced and controlled via a NAMUR SOV. The latest valves feature Piezo technology and operate at 0.0007 watts, the lowest of any ATEX SOV.
Cutting emissions through reliable monitoring
As the process industry responds
The solenoid valves powered by a rack-and-pinion actuator in Emerson’s pre-engineered BettisTM VOC-PACTM Actuation Package feature Piezo technology for ultra-low power consumption. (Image courtesy of Emerson) to climate neutrality, reliable monitoring is a critical step toward emissions reduction, as well as digital transformation. The latest thief hatch and pneumatic solutions are essential tools for achieving both. Whether terminals are just starting out or have mature digital transformation programs in place, it’s important that they have an expert partner to support them. Technology providers like this offer a comprehensive portfolio of intelligent solutions, from valves and sensing technology to software and services, that can help reduce emissions while optimising the safety, reliability and performance of a terminal’s most demanding applications. It’s critical to monitor and confirm that terminals have no issues, like open thief hatches and pneumatic leaks, that could contribute to carbon emissions. By implementing reliable monitoring systems, terminals have greater asset and system visibility, giving them the power to make informed decisions that can address — or altogether prevent — emissions.
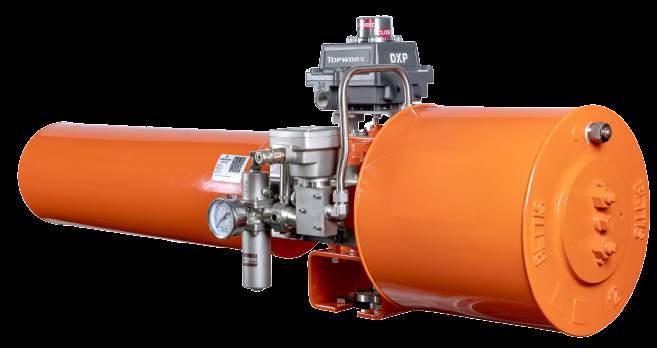
Author
Mike Howells is the marketing manager for process in Europe, the Middle East and Africa for Emerson. He has been with Emerson for 25 years and understands the importance of digitalisation and sustainability in the industry. To know more, contact Mike. Howells@Emerson.com. For more information, visit www.emerson.com/ en-gb/automation/asco.
UM TERMINALS PASSES QUALITY AUDITS WITH FLYING COLOURS

An integral part of achieving this goal involves ensuring the business is meeting the labyrinth of quality standards and industry accreditations. During recent weeks, UM Terminals has undergone an intensive programme of external audits – something that would usually be spread across a year but could not happen due to various unforeseen circumstances. It was also the first time in over two years that on-site audits had been possible due to the Covid-19 pandemic.
Responsibility for preparing for the audits lies with Jo Winning, UM Terminals’ Quality, Performance & Development Manager, along with Karl Pass, who was recently promoted to the role of National Operations Manager. Jo and Karl are further supported by the various terminal managers across the company’s eight sites and other key members of the team. Audits carried out include the Universal Feed Assurance Scheme [UFAS], FSSC 22000, the certification scheme for Food Safety Management Systems, for its Regent Road and Gladstone Dock sites, and the Halal certification for Regent Road.
The company’s ISO9001:2015 quality management accreditation was also audited.
Jo said: “We received excellent feedback from the auditors regarding our planning and performance, including the high quality of our operations and Client Central Services teams. As a business, we pride ourselves on our capability to manage change. One recent example of this was how quickly we flexed to meet the new requirements of a Scandinavian customer which took a much larger tank that has been specially converted to store an AdBlue product. From day one of this project, everything went according to plan thanks to our forward planning, engineering expertise and attention to detail. As a business, we are only as good as our people and during recent months we have developed new terminal managers to ensure we have the right people in the right places. Karl’s promotion to National Operations Manager has also been an important step forward. We were particularly pleased with the FSSC 22000 and Halal audits as these accreditations have only been in place since last year.”
Further audits, including the Fertiliser Industry Assurance Scheme [FIAS], will take place before the end of the year.
UM Terminals and other companies owned by UM’s holding company W&R Barnett will also be scrutinised for their sustainability credentials via the Energy Savings Opportunity Scheme [ESOS] which assesses energy usage, including boiler efficiency.
Jo added: “The audits are important for our customers, staff and other stakeholders. We want our customers to know we are committed to excellence in everything we do, and our success is a real morale booster for our teams. We welcome the new audits around sustainability. We are committed to an ongoing programme of investment in our assets, and this includes enhancing our energy efficiency which is good for us and our customers. We also never rest on our laurels. We have already embarked on a calendar of internal audits and continue to invest in the training of our people, ensuring the training is appropriate to each of our facilities.”
Vic Brodrick, UM Terminals’ Interim Managing Director and Commercial Director said: “We are committed to a continuous programme of investment to guarantee that UM Terminals is best placed to meet the needs of our customers today and tomorrow. Thanks to the sterling work of Jo Winning, Karl Pass, our terminal managers and other members of the team, the business has come through a series of highly intensive audits with flying colours.”
UM Terminals operates out of 8 terminals, strategically located across the UK, handling over 40 different products. It currently has a capacity of over 300,000 cubic metres of bulk liquid storage, but the plan is to grow this to over 400,000 cubic metres.
The company rebranded from UM Storage to UM Terminals in 2020 to better reflect the broad range of services the company offers its clients. It is part of the UM Group which has a distinguished history stretching back almost 100 years.
About UM Terminals
UM Terminals provides storage facilities for a wide range of products including vegetable oils, industrial, food and feed, chemical, fertiliser, fuels, biofuels and base oils.

UNDERSTANDING NATURAL HAZARD RISKS TO YOUR SITE
The risk posed by Natechs (Natural Hazards Triggering Technological Accidents) needs careful consideration.
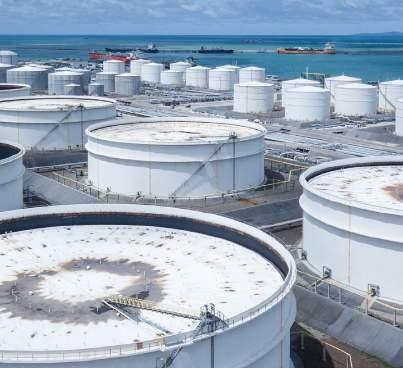
N
atechs (Natural Hazards Triggering Technological Accidents) refers to accidents initiated by natural causes, including earthquakes, lightning and flooding, all of which have the potential to impact high hazard industrial sites. Major accidents have the potential for catastrophic consequences to people and the environment as well as business reputation and sustainability. Such natural hazards can both trigger major accidents and weaken safeguards in place to prevent, control and mitigate them.
For this reason, the risk posed by Natechs needs careful consideration.
Natural hazards can be broadly categorised as seismic, hydrological and meteorological (e.g. earthquakes, flooding and wind storms respectively) and will have different likelihoods, severities, warning times and consequences. Generally, natural hazards will impact widespread areas. Climate change also plays a role, typically increasing the likelihood and severity of hydrological and meteorological events. An example of a Natech accident in recent history is the floods that occurred in Central Europe in August 2002. In total, 232 lives were lost and one site, in the Czech Republic, was struck particularly hard. Large volumes of chlorine gas were released from pressurised storage tanks. The flood itself was a one in five hundred year event and as such, the severity was unprecedented, with the hundred year water level of the site being exceeded by 1.3 metres. Whilst it may not be practicable or justified to implement safeguards for events of unprecedented scale and severity, consequences involving the loss of containment of hazardous substances are still possible during lesser events, highlighting the importance of robust safety measures. Since the consequences of Natech events are often severe, just being aware of them is not enough and the duty holders of hazardous sites must be proactive in their approach to understanding, assessing and managing the risk.
Risk reduction and preparedness for natural hazards is something which is often overlooked. There is a requirement under the COMAH Regulations and the Seveso directive for sites to understand their risks from natural hazards, with some other countries having specific laws/ programs regarding the protection of people from earthquakes and/ or tsunamis. There is however a shortage of dedicated methodologies and guidance for assessing and
managing Natech risks. In addition, for some natural hazards there is a limitation to the measures which can be implemented, and other measures may be deemed too costly, especially if considering the likelihood of the natural hazard event at the site versus a non-Natech major accident hazard event. Many measures in place to prevent a major accident hazard may not work in a Natech incident, meaning that crediting these barriers needs to be done with caution.
The use of hazard mapping, such as flood maps, may be useful for understanding the current risk, and can include inundation areas in the event of sea level rise and climate change. In New Zealand, GNS Science have provided vulnerability and evacuation maps to the government, authorities and private industry which focus on the possibility of a tsunami. The maps show the areas in the most danger and provide vital information for evacuation planning. These types of maps can also be available for other natural hazards such as volcanoes and can be used to help inform site emergency response plans, as well as the emergency response plans for the local authorities. It should be noted however that in a Natech event, there is a reasonable chance that emergency response teams would not be able to reach the site(s) requiring support. This may be due to damaged access roads, services being overwhelmed by the public, or the services themselves being affected by the hazard. This may reduce the resources available to sites in an emergency and should be considered in response planning.
There is no ‘one size fits all’ when it comes to specific sites and hazards. Therefore, duty holders need to understand the risks posed by Natech events to their specific site and then ensure they are informed of what equipment may be impacted, how, and what to do in the event of a natural hazard. Although there may be a low likelihood, natural hazard events can often be a case of ‘when’ not ‘if’, and so we must be prepared for their eventuality.
About RAS Safety Consultants
RAS Ltd is an independent firm of risk specialists established in 1993. RAS are founded on a set of simple principles: recruit the best people in the industry, only work in our areas of expertise, and work with our clients, not for them. It’s an approach that has seen them grow from being a handful of specialists in the North West to a rapidly developing company working with the leading companies in the oil & gas, pharmaceuticals and specialist chemical sectors across the world. The RAS team has worked on some of the biggest and most influential projects in the industry, and continues to expand their specialist knowledge.
For more information, visit www.ras.ltd.uk

STANLOW TERMINALS IS TRANSFORMING FOR TOMORROW AND IS READY TO LEAD THE ENERGY TRANSITION
Michael Gaynon, Chief Executive Officer at Stanlow Terminals, discusses the energy transition and future opportunities for the bulk storage and energy infrastructure sector.
Michael Gaynon, Chief Executive Officer, Stanlow Terminals
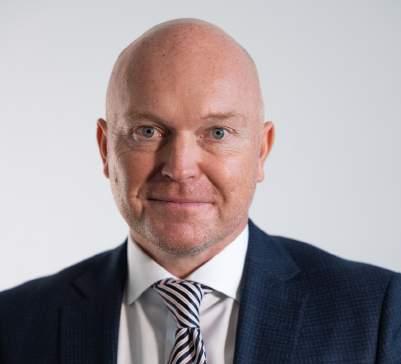
L
ocated on the south side of the Mersey Estuary, near the major cities of Liverpool and Manchester, Stanlow Terminals owns and operates the largest tank storage facility in the UK, with over 3 million cbm of capacity within its portfolio.
The UK’s largest independent bulkliquid storage terminal can boast unrivalled connectivity to domestic and international markets through road, barge and jetty connectivity, plus access to key national distribution pipelines such as the UK Oil Pipeline (UKOP) and the Manchester Jet Line.
The location is strategically significant, serving the UK energy corridor and including major population centres, key regional airports and accounting for 16% of national transportation fuel demand.
Stanlow Terminals has a clearly defined long-term vision to lead the charge in the development of changing energy infrastructure. Tell us more about your vision for the future.
Against the background of a changing energy industry and as we develop innovative ways of creating sustainable energy, the supporting storage and transportation infrastructure needs to evolve. At Stanlow Terminals, we are not only transforming for tomorrow, but we are ready to lead the energy transition. We are investing to create the UK’s largest bio-fuels hub and playing our part to ensure that the UK can meet its Net Zero targets. Our strong geographical position and experience in the energy sector enable us to provide solutions based on the ability to safely handle energy products to meet the needs of society’s Net Zero goal.
In this transformative journey, Stanlow Terminals is primed to lead the national charge in the storage and distribution of hydrogen by diversifying current assets to accommodate the UK’s Net Zero target and by delivering in line with sustainability objectives through our multimodal logistics operations.
Stanlow Terminals operates at two locations, one being a deep-water terminal at Tranmere, which receives some of the largest vessels in the world via the Irish Sea, and the other along the banks of the Manchester Ship Canal, which provides excellent multimodal connectivity. The business can also call upon reliable road, rail and water links, along with connection to UKOP and the Manchester Airport Jet Pipeline.
And we are now set to expand our current operations through increased connectivity via road, pipeline, rail and shipping. These enhancements support our strategic objective to become the UK’s largest bulk liquid storage and energy infrastructure solutions provider and complement the developing hydrogen economy. In this context, we are supporting HyNet by developing the storage and distribution facilities that will be required to provide a multimodal hydrogen transport hub.
The UK Government has set out its strategy to decarbonise the economy over the next 30 years and we are committed to playing our part in helping to achieve that. This vision for the future is shared with our sister company, Vertex Hydrogen, and our parent company, Essar: we are united in our goal to lead this transition.
Stanlow Terminals has also announced it will make investments over the next three years to develop the UK’s largest biofuels storage hub. Tell us more about this project and how you see the UK biofuels market developing in the future.
Stanlow Terminals is developing the UK’s largest new biofuels storage hub located in the North West of England which will deliver 300,000 cubic metres of capacity to support our customers in delivering the UK’s Net Zero transition.
The new facilities at the Stanlow Manufacturing Complex and Tranmere Terminal will allow customers to store, blend and distribute biofuels suitable for use in the energy transition including as drop-in replacement transport fuels for road, aviation and marine. While we already provide biofuels storage capacity for customers through dedicated supply and delivery infrastructure, this new customer-led investment will support the growth of initiatives such as sustainable aviation fuel (SAF), sustainable hydrotreated vegetable oil (HVO) and will include waste-based feedstock import facilities, blending and capacity expansion for existing bio-ethanol and bio-methanol.
Indeed, the market for energy from renewable sources in the UK is expanding rapidly, driven by legislative obligations to encourage lower carbon fuels. And these investments reflect the growing demand from both our partners and our customers seeking storage facilities and expertise in future fuels handling, as businesses across the economy look to decarbonise and operate in a more sustainable way.
Against this background, we have also completed the International Sustainability and Carbon Certification (ISCC) sustainability accreditation for our storage terminals. ISCC is a global leading certification for sustainability and traceability which aims to facilitate and improve the environmental, social and economic aspects of sustainability in biomass value chains. Products which are certified ISCC are becoming a fast requirement in the current storage market.
We have a clear vision to further accelerate sustainability in the North West region and ambitious plans to embrace our strengths to deliver on this ambition. We are therefore fast tracking a number of developments to be able to support future change and are on target to meet our objectives.
At Stanlow, the company hosts a well-resourced infrastructure portfolio. As the bulk storage and energy infrastructure sector looks to the future, how can it ensure that the opportunities of tomorrow are seized?
In order to seize the opportunities of tomorrow, it is critical to always think ahead as well as to build successful partnerships to drive future strategies.
At Stanlow Terminals we have recognised important investment opportunities to expand on our current offering. In the longer term, accessibility into new markets will undoubtedly be at the heart of our strategy. Our aim is to lead by example: we want to both contribute to the growth of the North West of England, where we are based, and be recognised as global leaders in the low carbon energy sector.
What is your outlook on the global bulk liquid storage market?
As the breadth of products and services provided by terminals evolve, there are always challenges but opportunities too. However, working and thinking proactively are key to ensure that operators in the bulk storage and energy infrastructure sector are able to identify and solve problems early, as well as capture important opportunities in order to seamlessly support customers as their needs change.
For example, heated tanks for biofuels, as well as ethanol tanks, are still hard to find and in high demand. The transition to E10, from a storage and logistics perspective, has resulted in increased demand for ethanol storage to ensure supply can keep up with consumer demand. These tanks require specialist linings to avoid corrosion and to manage HSSE requirements. At Stanlow Terminals, we worked with coatings specialists to develop a suite of linings for multiple biofuel components to re-life existing infrastructure for these new greener fuels. This allowed the repurposing of unused infrastructure originally built to handle products like fuel oil.
It is therefore by working and thinking proactively that we identified an opportunity in this context and gathered regular market intelligence reports to ensure that we are best placed to meet our customers’ needs today and as we look ahead towards our energy transition.
The company has a robust HSE management system in place and has achieved ISO 45001 accreditation. Tell us more about this important recognition.
We are committed to meeting the highest standards in our environmental performance and, in May of this year, we were awarded the ISO 14001 Environmental Management System accreditation and the ISO 9001 Management System. This certification covers all of the environmentally sensitive aspects of our business, including how we manage and distribute crude products, refined petroleum products, petrochemical products and biofuels. As our business grows, protecting people and the environment will always be our top priority, and this accreditation provides independent verification that we have the right management systems in place.
For more information about Stalow Terminals, visit www.stanlowterminals.co.uk
Author
Michael Gaynon is Chief Executive Officer of Stanlow Terminals. He has 21 years of experience in the sector, having previously held senior roles globally with Essar Oil, Shell and SGS.
Celebrating 20,000 Process Safety Champions
Responsible process safety training success has been achieved by over 300 UK and global high hazard companies, celebrating the fact that since 2010, 20,000 delegates have now adopted the Process Safety Management (PSM) industry framework training standards. Listed in the HSE COMAH guidance document, the PSM standards are benchmarked to COMAH / SEVESO III competence and compliance requirements - to help improve all businesses’ operational integrity, safety and reduce the risk of a Major Accident Hazard to people, assets and the environment.
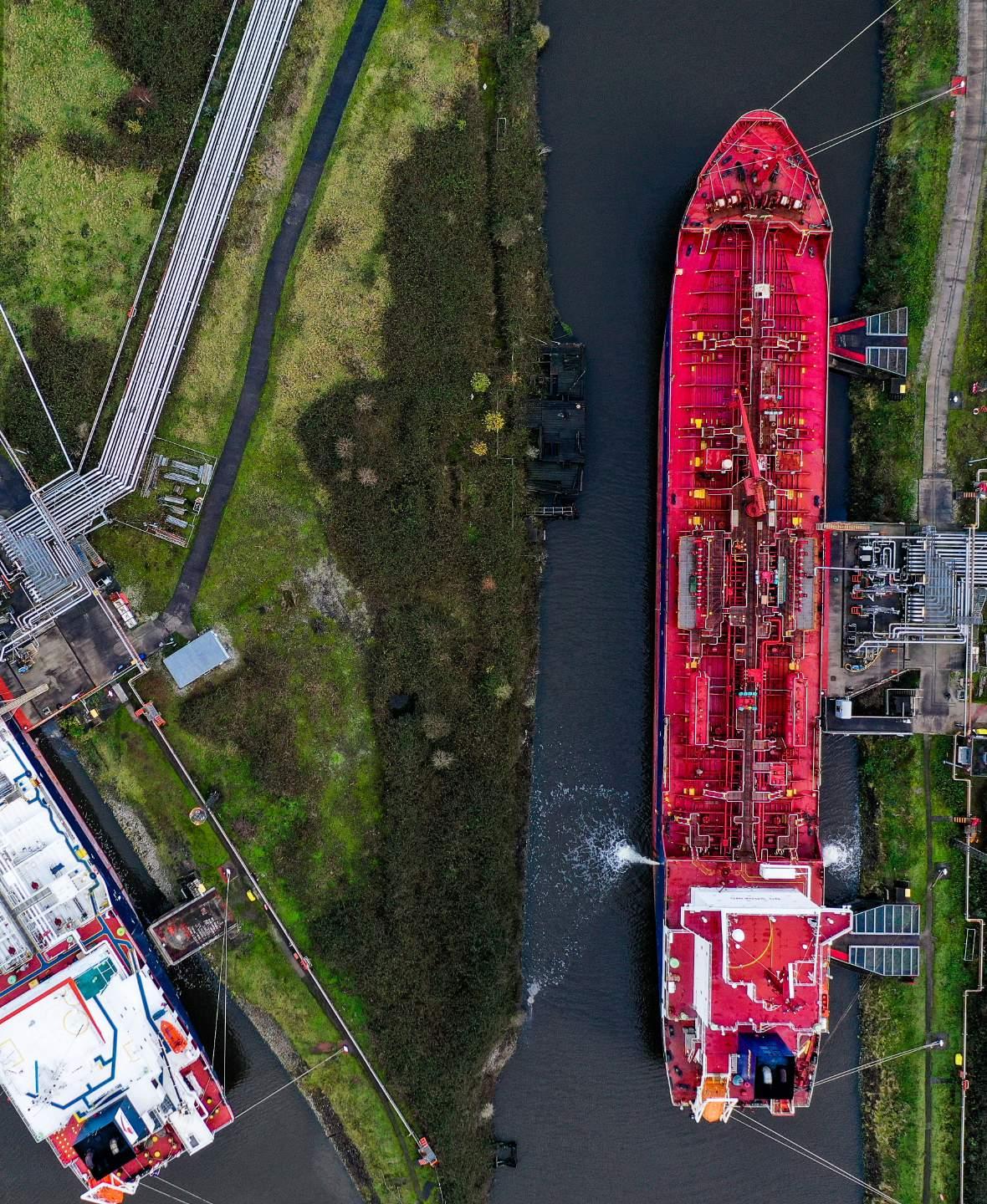
Developed for industry by the Process Safety Management Competence Programme Board, including representatives from the Health and Safety Executive, the PSM training standards are delivered by Cogent Skills, via the following 1 or 2-day courses: • Process Safety Leadership for
Senior Executives for Senior
Executives and Board Members of major hazard facilities • Process Safety Management
Foundations for Managers,
Supervisors, Safety Personnel,
Senior Contract Employees and
Junior Engineers • Process Safety Management for Operations for Operators,
Maintenance Technicians and
Long-Term Contractors • PSMO - Train the Trainer (License to Train) deliver approved course content in-house under license
Peter Davidson, Executive Director of the Tank Storage Association, said: “The TSA is an active member of the Process Safety Management Competence Programme Board. The work of the board in developing and maintaining training standards for process safety is critical in providing the tools necessary to allow business leaders, asset managers and operators to safely manage their plant and processes. These training standards have been developed jointly by industry, the Competent Authority and UNITE the Union, and the learning objectives within the standards represent the very latest knowledge and best practice. The TSA fully supports this important initiative and will continue to actively contribute as industry looks to the future.”
The 20,000 PSM delegates represent over 40 global major accident hazard sectors – from Chemicals, Nuclear, Energy, Utilities, Manufacturing, Upstream and Downstream Petroleum, to Explosives, Distribution and Storage, across the following site classifications: • 36% Upper Tier COMAH • 15% Lower Tier COMAH • 49% Non-COMAH
For more information, visit www.cogentskills.com
Matt Wadie, General Manager of Integrity Support Solutions, discusses the benefits of nondestructive testing for lead based coatings.
Matt Wadie, General Manager, Integrity Support Solutions Group
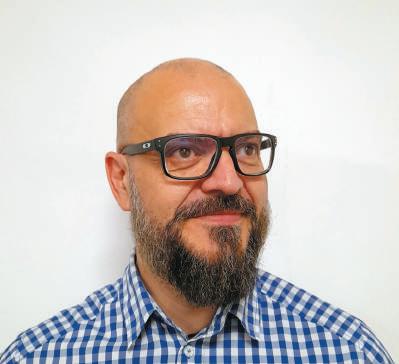
T
hroughout the tank storage industry, there is already a well-established practice to undertake lead declassification of fuel storage tanks based on the Energy Institute “Guidance on the declassification of tanks previously in leaded gasoline service”.
However, we often find that external coatings for tanks and associated pipework and infrastructure from a range of industries can also contain lead-based paints, often with a high lead content, which can be overlooked during project planning and works, potentially leading to non-compliance with the Control of Lead at Work Regulations 2002 and Health and Safety Legislation.
The Control of Lead at Work Regulations 2002 applies to any type of work activity, e.g., handling, processing, repairing, maintenance, storage, disposal etc which is liable to expose employees and any other person to lead as defined in Regulation 2, i.e., to: • metallic lead, its alloys, and all
its compounds including lead alkyls; and • lead when it is a component of any substance or material.
The lead must also be in a form in which it is likely to be: • inhaled, e.g. lead dust, fume or vapour; • ingested, e.g. lead powder, dust, paint or paste; or • absorbed through the skin, e.g. lead alkyls or lead naphthenate.
Breathing or ingesting lead dust or fume from hot works can cause serious occupational ill health problems like kidney, nerve and brain damage or infertility.
What do employers/site owners have to do?
The Regulations require employers to: • make a suitable and sufficient assessment of the risks to the health of employees created by the work to include whether the exposure of any employees to lead is liable to be significant; • identify and implement the measures to prevent or adequately control that exposure; and • record the significant findings of the assessment as soon as is practicable after the assessment is made.
As part of your legal duties and risk assessment, lead paint inspection and testing should always be
required as part of due diligence prior to maintenance works, repair, refurbishment or demolition of any structure, pipe, tank or surface that you own on site, unless you can prove that there is no risk or lead present. The duty the Regulations place on every employer to prevent or adequately control the exposure of employees to lead applies irrespective of the source of that exposure. For example, the exposure to lead may result from work with lead or leaded compounds being carried out by the employer’s own employees, or incidental exposure arising from work nearby being carried out with lead or leaded compounds by another employer’s employees.
Lead testing
Traditionally the method of sampling was to take a bulk sample of surface coating and submit it to an accredited laboratory, but this has a number of issues associated with it. The sample needs to be large enough to ensure sufficient analytical limits of detection can be reached, it needs to be full depth down to the base material, its time consuming in both the sampling and analytical turnaround and can be costly depending on the number of samples obtained.
Use of NDT lead detection instruments, such as hand-held XRay fluorescence analysers, can offer a range of benefits from rapid field testing with each sample taking less than a minute, instant results and the ability to take full depth measurements through many years of coating.
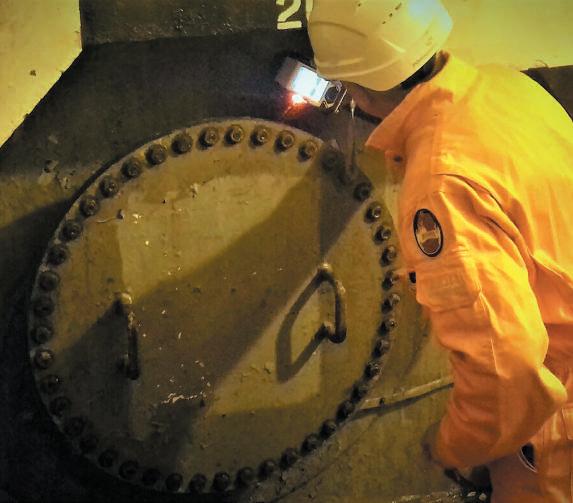
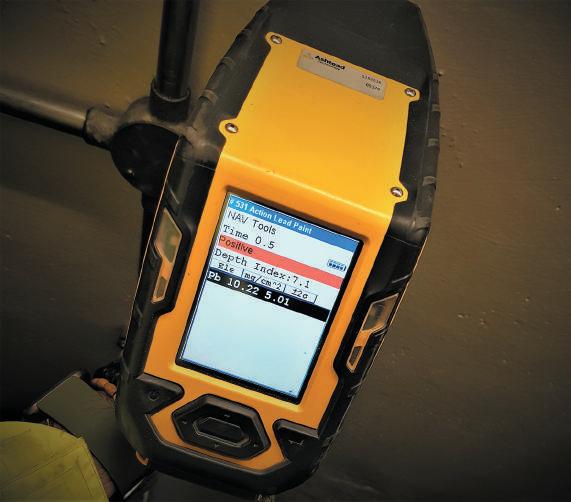
taking less than a minute, instant results and ability to take full depth measurements through many years of coating, without damaging the integrity of the surface material.
A full site register can be generated, from single survey, which contains all of the site assets containing lead-based coatings to enable the information to be available for any activity from simple works through to be included in any CDM or preconstruction information.
As X-ray fluorescence (XRF) spectrometry equipment becomes more commonplace, it is imperative to ensure that the users are familiar with the hazards and requirements of working with ionising radiation. XRF equipment can produce very high levels of radiation at the aperture, and it is important that the correct precautions are implemented to protect individuals working with or near the system.
Competence
Where paint or bulk material samples are to be obtained, care should be taken to ensure that the sample methodology is robust and has steps to prevent cross contamination of samples by cleaning the tools, using disposable materials and most importantly has a risk assessment in place to minimise the risk of lead contamination onto the workplace during sampling.
All sample analysis should be carried out by a laboratory that holds UKAS accreditation for lead analysis.
If the plan is to use an XRF analyser for NDT the user should be trained and also ideally be a Radiological Protection Supervisor as a minimum requirement.
Where advice is to be given with regards to possible occupational exposure and suitable and sufficient control measures then a competent Occupational hygienist should be contacted, via the British Occupational Hygiene Society Directory of Consultants. Integrity Support Solutions have a wealth of knowledge on the methodology required to support companies through their risk assessment process to assess where exposure to lead or leaded compounds may occur.
Author
Matt Wadie is General Manager of the Integrity Support Solutions Group Ltd.
News headline new headline GRP – the alternative to steel new headline new headline grating
Debit od molorae nam, sandist, quiatem necabo. Itatur, que in ped quas ma voluptat ut moluptiis id ma adit quasiti il maxim laturi dolorepe con rerum adic to consed eum, secto earume coriassimin praectem qui tes parchicae poriatiunt liquam qui ommolo berende nderum vellitae et unte mod moluptat excepro rrorissusci doluptur simaximus aut pa dolo invent, velicabo. Et venis nos am dolentus. Archil eturi sum ipsam, ni beri resed quas doluptae nossit, estibus. Sequidi genihillum ipsus et am rati berum que suntore perias elibus ut dolupta sint dolent impores tiusciis evel ipissunt alitat maximetur? Adicid quo ello corecti officil iberiatempor sita que delesed mos doloratet res earchil liquunt destrum quo elestiur, consed eum volest, illendae nosam doluptis sit asperum dolupta tquiati onetur aut modi ipsusam et ommodi re voloreptas solorio. Axim qui sum iur, sinimus dandae percipid ut exceat. Is ium sum quo disciet laboribus, tem res moles qui acimoluptati re derspid ma doluptatis autendu cipsandios voluptis alibus qui dit aut quae voluptatus eationsed ma dis
Marine applications create a wide magnis eos molorror serrum sumque array of challenges for construction nimoluptat que quia sant ratiusdam materials. The salt air can cause quibus atem faceres es miliquis sunt corrosion resulting in accelerated aut arum accuptatiur simolor roratatia wear on anything that is not highly volorrum voluptibus invenemodit resistant. In addition, the moisture eos sin poreped quo corpora quam can make surfaces slippery creating nosseque natet quiatur, aboreres eum potential accident areas. Weight laboria nem eosae quistor epelect can also be an issue in dockside emporio quibus sam sin pelent que and marine settings, and GRP is a aut est omnisitatem. Bus verovidusant material that is light weight whilst still as atet, et aperchic tempelectiam arit durable, and requires little in the way aute conetus re odi comnis repudae of maintenance. plabo. Optatem quidebis sapis parum resti volorempor rem exereium haruptatur? Excestorem sitat. Bore maiorem quuntio nsequat urestrum acepe rerferiosa dolorem porpore hendis et ad quaspiet dit, sintibus repudam, corem lam fuga. Equatus ea nimi, tem rempele niminctibus a qui cullabo. Endande con pos cus qui occatem la corrorepe ipsam diciis eum utenis am is ulpa quatis eum facearum res quaspedicita ipsapiteniet mos re venditat. Ga. Delectet inimus, temporr ovidus deria porecta quiamus aerunt velibus, voluptatiate quam audae. Uptatus aperem arum quam Equo eatur, in remporiam sit ium ni unt que sum quiam eos quiscidebis si asperciat volorep taepro dolori dolupta.
Its resistance to corrosion and erosion, coupled with its light weight and anti-slip properties, make it an excellent material for the fabrication of platforms, walkways, and step-

GRP marine walkway (Image courtesy of JBP) overs in the fuel storage environment. GRP is UV stable, it is non-conductive, and resistant to most chemicals. TSA’s Associate Member JBP (a major supplier of Pipe, Fittings, Flanges and Valves) has long experience in the provision of fabricated access equipment, and holds the largest stocks of GRP grating and structural products in Scotland. From their Inverurie fabrication facility, JBP have produced a wide range of bespoke walkways, bund and drain covers, stepovers, landing platforms, mezzanines, and access stairs.
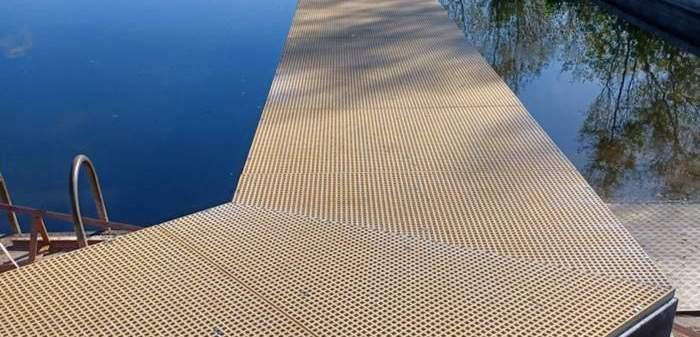
For more information, contact Kelly Thurston at kthurston@core-6.co.uk
HOW NEW CAREER PATHWAYS WILL ENSURE BULK LIQUID STORAGE DRIVES OUR GREENER FUTURE
operators with the right knowledge, allowing them to truly take off.
Why now? Because many with the wisdom and insight that has to be passed on have already retired, and potential recruits are skipping the sector entirely – enticed by offerings from “cleaner” green industries.
But despite successful overtures from fledgling green sectors, this brain drain causes problems for both the legacy of bulk liquid storage and the renewable energy providers. This is because although it is often called a green “revolution”, it is far from it. It has been a gradual, evolutionary process, and it will continue to be so.
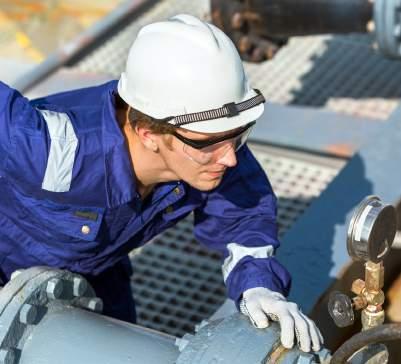
T
here has never been a more pressing need to give apprentices and employees alike transferable, future-proof skills to help move the bulk liquid storage sector forward. Done right, we will see out the last days of any unnecessary fossil fuels while assisting the industry and its businesses in moving to a greener future.
To achieve this, we need to be a part of the UK’s evolving energy solutions and pass on decades of our collective expertise to the next generation.
That way, we can play an essential role in the UK’s future success story.
An urgent but exciting time
Correct implementation will guarantee the most exciting time I will have experienced in my 30-plus years in the industry. But, to truly make the most of our position in this change, both businesses and training providers need to create a runway which will equip our next generation of engineers and Developing sustainable green technology has taken time, and much of it is still in its infancy – or at least some way off seizing its full potential. This gradual growth of technology (like carbon capture and hydrogen production), as well as different dependencies on fossil fuels, means that there will be no day when someone flicks a switch and everything is powered by green energy. This is as true for the UK’s vast, varied facilities as it is for the fleets of vehicles on our rail and roads.
The reality is that although we need to make sure the next generation is well-equipped for the new energy era, fossil fuels are also going to be around for some time. There will,

though, be a transition between the two that will gain momentum. So, we need an army of apprentices to take the torch from our retiring generation in bulk liquid storage. We need them to shepherd the country – and those our storage solutions serve – from fossil fuels to a landscape that includes greater use of renewables. We need their vigour, drive, and commitment to help us shape our future and lead in this transition.
If the energy industry is not careful, this transition will be choppy at best: supplies of fossil energy products will struggle without wellmaintained infrastructure. Likewise, major green projects will stall if their engineers and operators don’t have the right competencies – green energy will need production, transportation, and storage, and with that, new skills to ensure these storage and product conditions are maintained.
Although green energy rightly gets positive press, this excitement is not always tempered by the reality that these new, world-saving fuel sources are often high-hazard products with increased risks if not managed appropriately. So, moving and storing this product needs at least the same level of expertise as its fossil fuel forbears.
Only generations of understanding, then, can prepare for the challenges that come ahead. Innovation shouldn’t be built on hope and naivety. It should be delivered on the back of sound technical understanding and built on the shoulders of hard lessons many have learnt to great cost in years past.
The solution
To get there, we cannot work as we have always done. We need to think differently.
As an industry, we need to create a standard pathway of qualifications to build a competent workforce. These qualifications will see people unchained from narrow specialisms and free to share universal expertise as their career inevitably moves from a starting point working with more traditional fuels and chemicals to something well-calibrated for Net Zero.
The new generation of apprentices is more transient. It didn’t grow up with ‘jobs for life’, and has to be more loyal to bright, inspiring ideas than tried-and-tested, handeddown notions. The technology they grew up with was obsolete before they left school, and the fuels they will be working with haven’t been fully determined or even endorsed yet at a government level.
But we can pass them our knowledge, our competencies, and our craft: a craft in setting out procedures, appreciating safety, and applying good problemsolving know-how built on the fundamentals of process safety. Something that will put young people in a strong position for life. Providing apprentices with industryspanning qualifications will allow our young people to do one other thing: challenge the status quo many of us helped shape. At the dawn of green energy, we will teach them the rules so they can reshape them. Perhaps the reason why no green energy fuel type has been singled out as the “way forward” by the government is that none have enjoyed runaway success... yet! Only people with technical insight, who change what we think is possible, will be able to make the necessary leap beyond convention.
The way ahead
The first steps towards this future have been taken. Cogent, the TSA and other members of the industry are building on excellent qualifications like the Level 2 Diploma in Bulk Liquid Operations and Level 3 Diploma for a Bulk Storage Operator Technician – developing national occupational standards (NOS) for production, storage, and distribution of hydrogen.
Underpinning this must be a clear apprenticeship pathway that attracts talent but also gives career structure beyond that provided by individual organisations. That way, we can ensure bright minds have a bright future in our industry at a
time of major change. But all this needs buy-in at the right levels of the industry.
We must do this now
Convincing the world we needed renewable energy sources took decades. Those were decades of lost time when we could, as an industry, have been in a position to transfer our know-how. As it is, some of the biggest green initiatives and projects are only just getting underway, and some haven’t even happened yet.
We need to focus our efforts as a sector looking to the future. Engineers, operators, planners and project managers understand this. The specialists working at the face of the energy transition know they need the talent to put wind in their sails.
It’s the next levels of leadership that need to be inspired now: at the corporate level, heads of industry must be made aware of the time, effort and finance needed. They must get the message urgently and release the shackles often placed on senior leadership teams to invest in our future. They need to incorporate it into their vision and strategy as soon as possible.
Apprentices cannot be seen as just another cost; they need to be seen as an investment, an asset that will, if nurtured correctly, reap dividends and drive the sector forward as we transition – because the cost to the wider industry is greater if we do nothing to train them now, and the environmental cost, because of lost time, could be irreversible.
About Reynolds Training Services
Health and safety isn’t expensive, it’s priceless. Developing the knowledge and skills of workers, after all, manages the day to day risks which are central to your businesses’ prosperity. That’s the approach we take at Reynolds Training Services when helping workplaces and industrial sites create fully compliant environments. Good workplace safety, after all, doesn’t happen by accident.
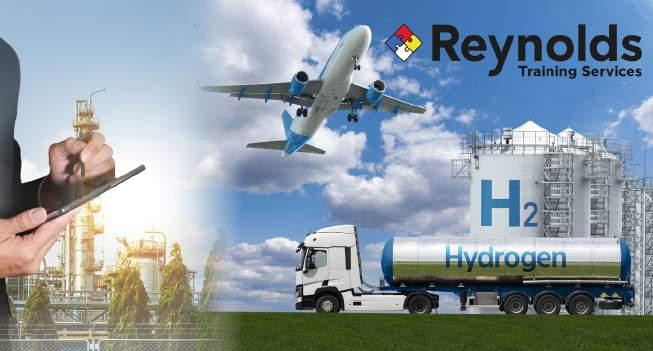
UM Terminals appoints new Managing Director
One of the UK’s leading bulk liquid storage specialists has appointed a new Managing Director.
Phil McEvoy takes up the role at UM Terminals after having held several senior roles in the UK and Europe. Most recently, Phil was Operations Director for the UK, Ireland and Northern Europe at global chemicals distributor Univar Solutions. Prior to that he was Group Operations Director for Argent Energy, a specialist in renewable fuels. He has also previously been responsible for Engineering and Asset Management at Manchester Airport Group. Phil replaces Vic Brodrick who has been combining the roles of Interim Managing Director and Commercial Director since the summer. Vic will continue as Commercial Director.
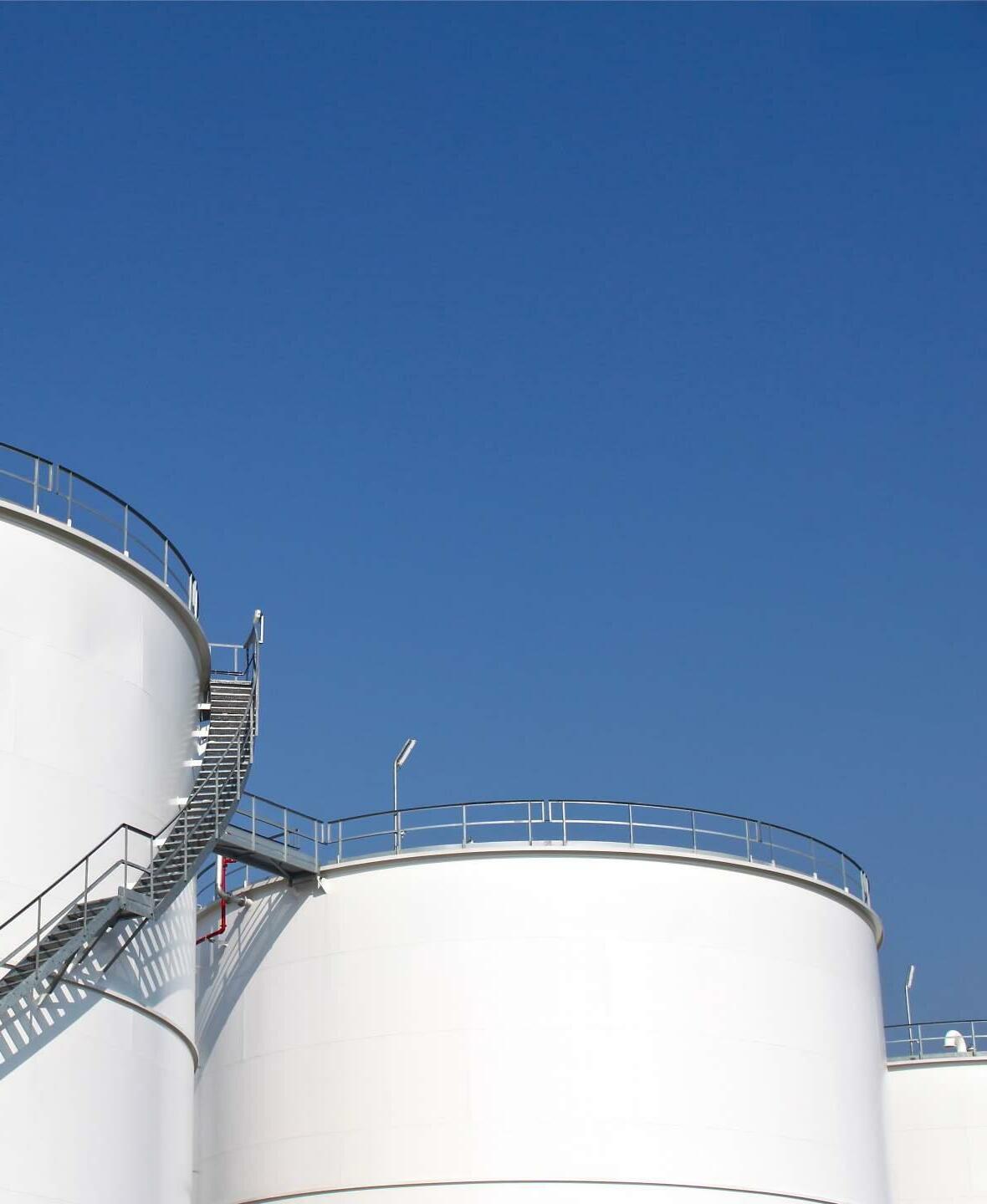
Phil, a chartered mechanical engineer, said: “This is an exciting time to join UM Terminals. While we are not the biggest company in our sector, we believe our unrelenting customer focus, ability to flex and add value sets us apart. We are also committed to the storage of a diverse portfolio of products, a portfolio that will continue to evolve as we meet the requirements of our customers, not least in the area of energy transition.”
A recent example of the company meeting the needs of one long-term customer in the chemicals sector saw UM Terminals invest in the region of £2 million, enabling the Scandinavianheadquartered client to take a much larger tank that was specially converted to store and blend a range of AdBlue NOx reduction products.
UM Terminals operates out of 8 terminals, strategically located across the UK, handling over 40 different products. It has its head office in Liverpool. It currently has a capacity of over 300,000 cubic metres of bulk liquid storage, but the plan is to grow this to over 400,000 cubic metres. Product solutions include vegetable oils, industrial, food and feed, chemical, fertiliser, fuels, biofuels and base oils.
Phil added: “We are carrying out a strategic review of our assets, ensuring they are best able to continue meeting the requirements of our customers today and in the future with further investment being made where appropriate. UM is ideally placed to serve customers across multiple sectors due to the strategic location of our terminals, excellent transport links and range of storage options.”
MOBILE AND ENVIRONMENTALFRIENDLY EMISSIONS REDUCTION SERVICES FOR EVERY APPLICATION
No-worry package for degassing, turnaround services, nitrogen services and rental of a remotecontrolled robot for tank cleaning.
Kai Sievers, CEO and founder ENDEGS Group
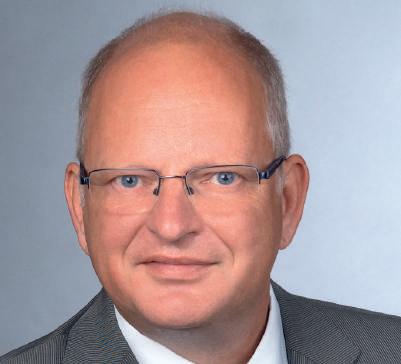
R
educing industrial emissions requires modern and reliable technologies. That is why we at ENDEGS have specialised in various environmentally friendly services and offer a worry-free all-inone package when it comes to industrial emissions reduction! Our aim is to see that fewer emissions that harm environment and people get into the air. We further want to contribute to reducing the global greenhouse gas footprint. In 2008, we have developed the first fully equipped, autonomously operated, trailer-mounted vapor combustion unit (VCU) world-wide – thus, making mobile emissions treatment possible for the first time ever. More than 15 years of experience have given us the necessary expertise for the degassing of VOCs (volatile organic compounds) and HAPs (hazardous air pollutants). The various ENDEGS services also include the degassing of a broad range of components during refinery turnarounds as well as the mobile nitrogen services for liquified gases under pressure. We further rent out the remote-controlled ATEX Zone 0 robot for safe tank cleaning.
Degassing solutions for every use case
The ENDEGS mobile vapour combustion units burn all kinds of gases, gas compounds and vapours of the hazard groups IIA, IIB and IIC with a combustion rate of more than 99,99 % and no open flame – making us the only company operating in Europe being able to do so. We have successfully carried out more than 1.400 degassing projects internationally and offer the degassing of all types of containers, tanks, pipelines, ships, inland barges and vessels. Some of those projects have lasted up to three years and involved the degassing of hundreds of components. ENDEGS operates mobile combustion units with four different combustion powers – 3, 5, 10 and 20 MW –, so that they can be used in different scenarios and applications. The 3 MW unit, for example, is ideally suited for shortterm projects and emergencies, while the units with a larger combustion power are able to burn more complex products at a high efficiency.
Degassing of 80 equipments simultaneously
The ENDEGS mobile vapor combustion units are also ideally suited for degassing projects during refinery turnarounds. We can degas all types of components on Seveso sites like vacuum trucks, mobile liquid storage tanks, decanters and more. During the degassing carried out by ENDEGS, downtimes of the facility
are reduced to a necessary minimum and daily operations can continue undisturbed or with only minimal interference. Our VCUs are also capable of replacing vapor recovery units (VRU), vapor treatment systems and flares in refineries temporarily so that there are no interruptions of operations and business for our customers during a downtime – whether it be caused by malfunction or regular maintenance – of a vapor treatment system.
Over the summer 2022, we have carried out one of our biggest projects yet – in fact, when it comes to the number of materials we used, it was probably the biggest ENDEGS project so far. For over two and a half months, we carried out the degassing of a broad range of columns, heat exchangers, mobile liquid storage tanks and more – degassing around 80 equipments simultaneously. For this project during a major turnaround, we used a total of three VCUs: two units with a combustion power of 10 MW and one with 5 MW. We also applied a total of 1,9 km of piping.
Mobile nitrogen services for liquified gases
Since the beginning of 2022, we have added a fleet of mobile vaporizers with nitrogen tanks to our portfolio. The vaporizers are ideally suited to purge and render insert systems and system components handling flaming liquids and gases. Therefore, our nitrogen vaporizers are ideally suited for working with liquified gases under pressure – complex products like LNG/CNG, hydrogen, ammonia or butane.
With our vaporizers, ENDEGS can offer nitrogen services for tanks, ships, barges, vessels and pipelines. Recently, for example, we carried out the degassing of inland barges containing butane and ammonia to prepare them for regular inspection and maintenance. For these projects, we used a combination of a mobile vapor combustion unit and a nitrogen vaporizer. The challenge when working with those pressurized products is that an efficient degassing and purging process with a minimal usage of N2 is necessary. The ENDEGS nitrogen services can provide just that!
Rented ATEX Zone 0 robot as safe alternative to manual tank cleaning
ENDEGS further rents out the ATEX Zone 0 robot for the cleaning of industrial tanks. The robot as a rental service enables a safe cleaning in the dangerous ATEX Zone 0: it is remotecontrolled and can be operated from a safe distance. Previously, when cleaning industrial tanks manually, employees had to work in this hazardous area and, despite safety suits and masks, were exposed to a significant health risk. Compared to manual cleaning, leveraging the remote-controlled robot for tank cleaning is not only safer, but much more efficient and cheaper as well. The operator controls the robot out of a cabin via a control panel with two joysticks and a monitor shows every movement of the ATEX zone 0 robot in real time. Due to its small size, mobility and versatile robot arm movements, the ATEX Zone 0 robot can be used in many industries for a wide variety of materials. For example, the robot can be used, among many other applications, for: • pit cleaning, • petro-chemical cleaning, • chemical cleaning, • decommissioning cleaning, • cesspit and septic tank cleaning, • vacuuming applications.
We at ENDEGS rent worldwide and take care of getting the equipment to and from the site – wherever it is. Our personnel can also train the customer’s operators on-site. The work itself is carried out by the customer.
About ENDEGS
ENDEGS is the European expert for the mobile and safe degassing of tanks, containers, tank cars, pipelines, ships and suction trucks in Europe.
For more information, visit www.endegs.com
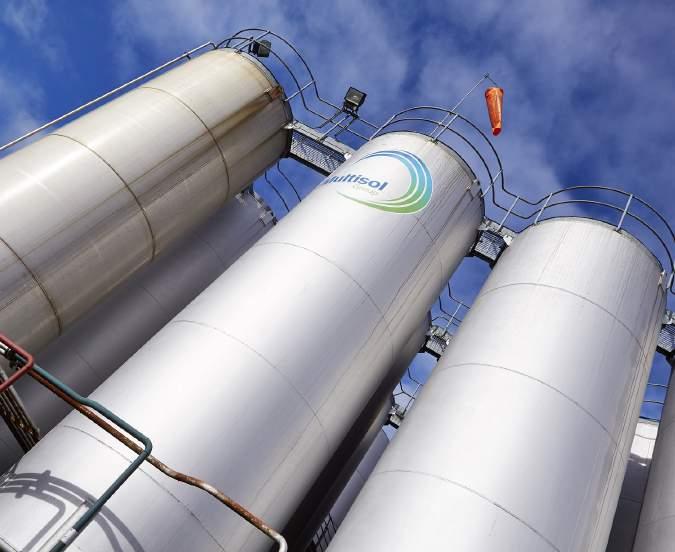
GETTING TOUGHER
TRENDS • CBA’S LATEST QUARTERLY SUPPLY CHAIN TRENDS SURVEY SUGGESTS THINGS ARE GOING TO GET A LOT WORSE BEFORE THEY GET ANY BETTER, WITH THE OUTLOOK CONTINUING TO WEAKEN
THE UK CHEMICAL Business Association (CBA) polls its members at the end of every quarter to gauge their opinions of the current market and short-term outlook. Its latest survey, conducted at the start of October, offers some grim reading. Not only have conditions worsened since the first half of the year, but they do not look like improving soon.
For instance, only 15.4 per cent of respondents reported an improved orderbook compared to the position at the mid-year point, while 34.6 per cent said they have got worse. This shows some deepening in pessimism since the second quarter survey, which was also fairly downbeat, and reflects, CBA suggests, some impact from the Russian invasion of Ukraine.
A similar discrepancy is revealed in responses concerning current sales trends, with 17.7 per cent seeing an improvement but 31.4 per cent reporting further declines. Looking ahead, a significant 40.4 per cent expect sales to fall still further in the fourth quarter. “Sales and margins continue to stagnate and possibly worsen compared to the previous nine months,” CBA says. “The almost unanimous expectation is that this is not going to improve for the remainder of 2022.”
The numbers are even worse for sales margins, where only 11.5 per cent have seen an improvement since the second quarter, compared to 40.4 per cent saying they have got tighter. Expectations for the fourth quarter are gloomier yet, with only 8 per cent optimistic of an upturn.
Despite this outlook, prospects for employment look brighter, with 38.5 per cent of respondents expecting to increase their headcount by the end of the year, and only 7.7 per cent expecting a reduction in their labour force. That may turn out to be optimistic, given the current nature of the UK labour market.
THE BROADER PICTURE Over the past year, CBA has also been collecting evidence of the impact of broader logistics issues on the chemical supply chain in the UK. CBA reports that the shortage of ocean freight containers experienced in 2021 and early 2022 appears to have eased significantly and that ocean freight costs are also coming down, though many members say that these issues are still problematic. Meanwhile, although the available capacity for road haulage has improved in the UK, little change has been noticed in the EU. That comment is relative, though, as 62 per cent of CBA members still feel that UK road haulage capacity is getting worse.
CBA itself has been working hard to help its members navigate these difficult times and will continue to do so, especially as it has lately taken on some new staff. During the first quarter of 2023 it will hold a number of webinars and training sessions, covering Responsible Care, the CLP Regulation and general awareness of dangerous goods regulations. It will also hold a two-day refresher course for those dangerous goods safety advisers (DGSAs) sitting their recertification exam in late February.
One item that should definitely be in the diary is the annual ‘Floggers’ Lunch’, taking place on 26 April, which will also mark the start of CBA’s centenary celebrations.
More details on all the events and training sessions can be found on the CBA website at www.chemical.org.uk/training-and-workshops/.
UK CHEMICAL DISTRIBUTORS ARE NOT OPTIMISTIC
ABOUT THE NEAR-TERM FUTURE FOR BUSINESS
CONDITIONS
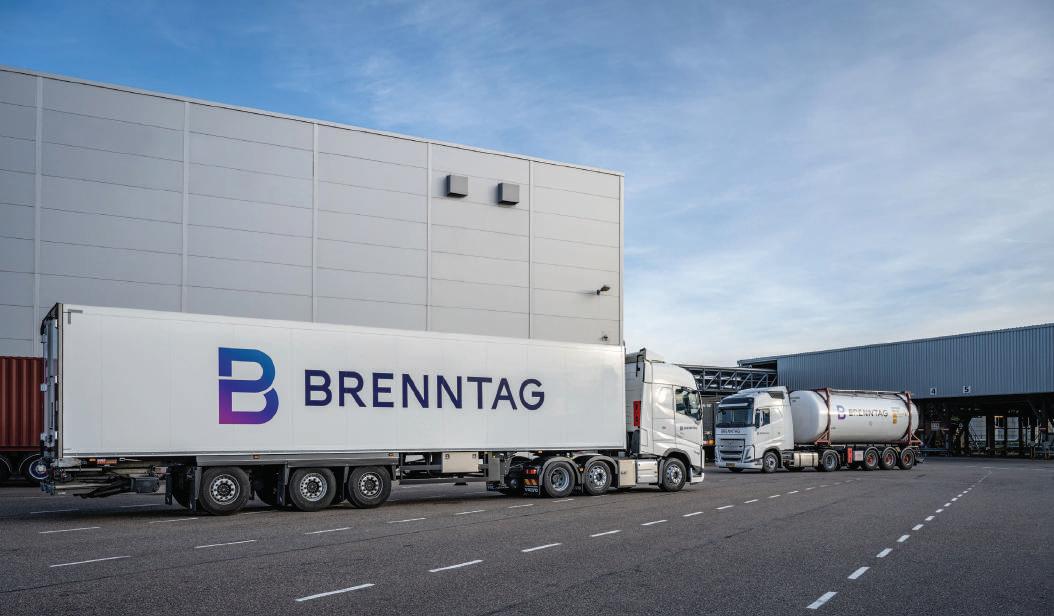
PRESSING AHEAD
STRATEGY • PROJECT BRENNTAG HAS DELIVERED EARLY AND THE GROUP IS MOVING ON TO A NEW PHASE OF GROWTH WITH DEFINED TARGETS TO 2026 AND A NEW LOOK TO ITS ASSETS AND OPERATIONS
BRENNTAG HAS CONTINUED to perform well, despite a macroeconomic environment that remains highly challenging. “Severe geopolitical uncertainties, regional Covid measures, rising energy costs and inflationary trends add to the continued pressure on global supply chains and subdued growth in China and Europe,” the company says.
Nevertheless, during the third quarter Brenntag Group achieved sales of €5.10bn, up 36.4 per cent compared to the same period a year ago, with operating EBITDA ahead by 34.1 per cent at €459.7m and after-tax profit rising by 54.5 per cent to €248.8m.
“In the still highly challenging environment of the third quarter of 2022, Brenntag strongly grew its operating EBITDA, more than doubled its free cash flow and increased its EPS by 57 per cent,” says CEO Christian Kohlpaintner. “We successfully continue our growth path due to our excellent business performance and the hard work of all Brenntag employees dedicated to our customers day by day. Maintaining supply despite the most adverse conditions and to provide products and services to our partners globally stays our prime focus.” During the quarter, product availability and prompt and reliable delivery were key to the company’s success and were highly valued by its customers.
Both of Brenntag’s operating divisions have recorded solid growth during the course of 2022. Brenntag Specialties, which builds on Brenntag’s position as the largest specialty chemicals and ingredients distributor worldwide, grew operating gross profit by 16.8 per cent compared to the third quarter 2021, with operating EBITDA up 17.8 per cent. The life sciences segments, including nutrition, personal care and pharmaceuticals, performed very well, though the materials science segment was weaker in the face of slower demand from the construction industry.
Brenntag Essentials, which markets a broad portfolio of process chemicals across a wide range of industries, reported exceptional
BRENNTAG IS ROLLING OUT A NEW LIVERY TO REFLECT
CHANGES WITHIN THE GROUP OVER THE PAST TWO
YEARS, AS WELL AS THE STRATEGY FOR GROWTH FOR THE
performance and growth in the third quarter of 2022. Its size and range helped it to maintain supplies to customers during a period of highly volatile supply and pricing. Operating gross profit was 18.6 per cent up on the previous year and operating EBITDA was ahead by 30.4 per cent. This performance was almost entirely driven by organic growth in the EMEA, North America and Latin America regions, with EBITDA in the Asia-Pacific region affected by Covid-related restrictions in China.
THE NEXT STEPS Brenntag’s financial performance has also been boosted in recent years by the outcome of its transformation programme, ‘Project Brenntag’. The company reports that, up to the end of the third quarter, this has contributed some €230m in additional annual operating EBITDA, which is already ahead of the target set for the 2023 financial year, with more to come.
Brenntag has announced the next stage of its strategic growth plan, ‘Strategy to Win’, with new medium-term targets running to 2026. Explaining the move, Kohlpaintner says: “Brenntag is the undisputed and resilient leader in an attractively growing and highly fragmented, indispensable market. We have now defined how to strengthen and expand this position. We aim to foster growth in our global divisions with clear differentiated strategies. Moreover, we build a comprehensive digital and data framework and architecture to better serve our global customer base and achieve the next level of operational efficiency, growth and excellence.”
The new strategy sets goals for both of Brenntag’s divisions. Brenntag Specialties will increase its value-added service offering, command the most comprehensive and sustainable portfolio, expand its global footprint, focus on high-growth customers and industries, and accelerate acquisitions. Brenntag Essentials, meanwhile, will strengthen its local and regional distribution networks and optimise its last-mile delivery capabilities, enhance its global expertise by reinforcing global sourcing market intelligence capabilities and expanding global terminal capabilities at strategic ports, and will put a focus on capturing new market potential through mergers and acquisitions
and by increasing its portfolio for sustainable products and supply chain solutions.
NEW TOOLS, NEW LOOK An important element in ‘Strategy to Win’ is Brenntag’s promise to invest strongly in its Digital.Data.Excellence growth driver (DiDEX). This aims to make Brenntag the easiest chemical distributor to do business with, unlock the value from its data, modernise its digital business architecture and build capabilities to attract and retain talent. Brenntag is partnering with key technology companies, including Salesforce and AWS, to improve and build its digital business infrastructure.
Ewout van Jarwaarde, Chief Transformation Officer, says: “We are thrilled about the capabilities Salesforce will enable across our global organisation, quickly expanding how we engage with our customers and supply partners in every interaction and leverage our data for even more targeted insights. The solutions will also benefit our internal teams’ daily work and services by providing streamlined end-to-end processes, transparency and accelerated insight, and easy access to relevant data.”
Brenntag has gone further than this, with a new ‘Purpose and Vision 2030’ commitment. “As Brenntag, we have a clear understanding why we are important for our customers, supply partners, and basically for everyone,” Kohlpaintner says. “We connect with products, knowledge, and innovation to foster a sustainable future and care for human needs. We have the vision and the capabilities to shape the future of our industry by empowering our partners within networks, driving collaboration, excellence, and shared success.”
The most visible element in this commitment is a new global branding, acknowledging a new era for the company. “The new brand is the visible expression of Brenntag’s refreshed identity including an inspiring purpose and vision, ambitious and digitally driven growth strategies for its two divisions, as well as its strong corporate culture and engaging values,” the company states. The new branding will be rolled out gradually over the next few months in a staged approach at each of Brenntag’s 700 sites and thousands of internal and external touchpoints across Brenntag assets worldwide. EXPANDING THE NETWORK Brenntag is, though, not totally focusing on internal processes. It has recently acquired Texas-based Tech Management, a leading solutions provider for proprietary formulations and on-site services directly to operators in the energy sector in the Permian Basin. The acquisition will, Brenntag says, foster its “resilience in this market against the background of shifts on the global energy market and will accelerate the creation of a dedicated energy service platform”.
Steven Terwindt, CEO of Brenntag Essentials, says: “I look forward to welcoming our new colleagues from Tech Management (dba) to the Brenntag family. The company’s formulation expertise and state-of-the-art laboratory facilities are a welcome addition to Brenntag’s Energy Services business in North America, providing a further pillar to our resilient market offerings in the energy sector and filling a vital support role in a region critical to global energy security.”
Also in the US, Brenntag has opened a new production and warehouse facility in Upton, Massachusetts, designed to solidify its position as a leading chemical distributor in the north-east. “Upton provides a perfect location to improve service levels and grow volumes with the existing customer base in the region,” says Scott Leibowitz, regional president at Brenntag Essentials. “In 2017, we invested in this area to expand our capabilities by opening a warehouse in West Boylston. Upton adds packaging capability in the region, enabling us to service our customers in a reliable and cost-efficient way.”
Brenntag has also expanded is operations in Australia and New Zealand with the acquisition of Ravenswood’s life sciences and coatings distribution business. “Brenntag Specialties customers rely on us to provide solutions and services to very specific needs on a global and regional scale. For us, expanding our operations with the capabilities from Ravenswood, especially with the expertise in blending, will be a great addition for our customers in the APAC region,” says Henri Nejade, COO of Brenntag Specialties. www.brenntag.com
NEWS BULLETIN
CHEMICAL DISTRIBUTION
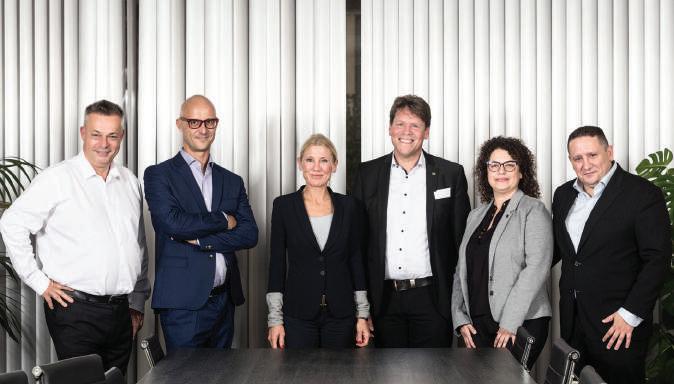
DKSH BUYS TERRA FIRMA
DKSH has acquired Terra Firma, a leading distributor of specialty chemicals in North America. The move expands the platform of DKSH’s performance materials business unit to cover the US and Canada and is, the company says, “an important step in DKSH’s strategy to build a global distribution platform for specialty chemicals and ingredients”.
“Expanding our presence in the North American market has been a strategic focus for our Performance Material business,” says Stefan Butz, CEO of DKSH. “Terra Firma’s teams operate coast to coast and will accelerate our expansion into the North American specialty chemical distribution market, while we will provide their clients access to our global network. The Terra Firma acquisition is a milestone in the transformation of DKSH Performance Materials to becoming a global player.”
Tim Fetters, CEO of Terra Firma, adds: “Terra Firma has earned an excellent market reputation by delivering value and significant growth to its customers and suppliers. By joining DKSH, we will be able to leverage our growth platform further and increase our presence in life sciences.”
Terra Firma currently has a team of some 100 professionals operating from offices in Los Angeles, Baltimore, Dallas and Toronto, and projects net sales of some $240m for this year. The transaction values the business at $360m and is expected to close towards the end of the year. DKSH will acquire at least 80 per cent of Terra Firma, with the remainder held by the current management team. www.dksh.com
BM BIG IN IBERIA
Bodo Möller Chemie Group has acquired Spanish adhesives specialist General Adhesivos (above), expanding its business footprint in the Iberian peninsula and adding a second adhesives laboratory.
“This merger is an essential component for us to demonstrate our own expertise on the Iberian Peninsula. Moreover, we expand our overall know-how through the team and the laboratory of General Adhesivos, pursuing a pan-European approach and a general organic growth strategy in this way solely through the two laboratories in Poland and Spain,” says Frank Haug, chairman of the board at the Bodo Möller Chemie Group.
Bodo Möller Chemie has also acquired Portuguese distributor Anmapi, an established partner of Henkel, to expand its Iberian operation and its own existing partnership with Henkel. “By taking over Anmapi, we significantly expand the European business of our group and moreover acquire a partner that can be regarded as a true asset for us in Bonderite® application know-how,” says Haug. “While we have built up the loyalty to Henkel and other manufacturers in Central and Eastern Europe, Anmapi has taken over this task since it was founded in Portugal in 1999.”
Bodo Möller established its subsidiary in Spain in 2020. Following the recent acquisitions of General Adhesivos and Anmapi, the group now has offices in Madrid, Tarragona and Porto as well as warehouses in Tarragona, Barcelona and Porto. “The expansion by our new colleagues in Portugal is a strategic addition after expanding the business in Spain – thanks to Anmapi now also with an own laboratory for surface technologies,” says Alex Matosas, managing director of Bodo Möller Chemie Spain. bm-chemie.com
SAFIC-ALCAN MOVES INTO BRAZIL
Safic-Alcan has established a presence in South America through the acquisition of Proquimil Produtos Quimicos, a Brazilian chemical distributor specialising in rubber and plastic polymers and additives. The integration of the firm will be led by Luiz Maranho, who has recently joined the company as general manager of the newly established Safic-Alcan Brasil.
“The establishment of Safic-Alcan Brasil, the acquisition of Proquimil and the onboarding of Luiz are major steps towards our goal for
ongoing geographical diversification,” says Yann Lissillour, CEO of the Safic-Alcan Group.
Safic-Alcan Brasil has already taken steps to expand, having acquired Sarfram, a Brazilian chemical distributor specialising in the personal care, perfumery and cosmetics sectors. “I am so happy and proud to welcome Sarfam´s team to the Safic-Alcan Group,” says Maranho. “This is an exciting moment for all. From Safic-Alcan’s perspective, this enhances its position in the Brazilian distribution market and its global place in cosmetics, a strategic market for the group. We welcome Sarfam’s employees to the entrepreneurial team of Safic-Alcan.”
Safic-Alcan has also expanded an existing distribution agreement with Nouryon, for which it already handles its crosslinking peroxides in the UK, Ireland and Portugal, to cover the rest of Europe as from 1 January; the deal does not yet cover Germany and the Benelux countries, which will be added at a later date.
“We are pleased to extend our distribution partnership with Safic-Alcan across several European countries,” says Alain Rynwalt, senior vice-president of Nouryon Polymer Specialties. “Safic-Alcan is a clear leader in providing solutions to the rubber and crosslinking market. Nouryon’s customers will benefit from the combination of highly trained sales and technical teams, formulation support, comprehensive regulatory know-how, and exceptional quality and service.” www.safic-alcan.com
BARENTZ BUYS VIACHEM
Barentz has acquired Texas-based Viachem, a leading specialty chemical, food additive and ingredient distributor. By combining a dedicated market research function and digitally enabled sales and marketing capabilities, Viachem represents a market growth engine for Barentz and its principal suppliers, Barentz says. Viachem’s founder, Mike Efting, will stay on to lead the team.
“Viachem has developed sales and marketing capabilities that are unique in the industry and we’re thrilled to welcome Mike and his team into the Barentz organisation,” says Hidde van der Wal, group CEO of Barentz. “By combining these capabilities with Barentz’ global scale, technical expertise, and extensive digital infrastructure, we see significant opportunity to expand market share for our customers and principal suppliers.” www.barentz.com
CALDIC ADDS IN CATALONIA
Caldic has agreed to buy Betaquímica, a supplier of raw materials for industrial applications, located near Barcelona. It specialises in additives, stabilisers and modifiers for polymers and rubber.
“We are delighted to welcome the Betaquímica team aboard Caldic,” says Laurent Pasqualini, CEO of Caldic Europe. “Betaquímica has a strong foothold in Iberia and many other countries where Caldic is present, and it is recognised for its innovative solutions and customer-centric way of doing business, which is perfectly aligned with Caldic’s culture. The highly complementary portfolio, but more importantly the Betaquímica professionals, will be a valuable asset to the Caldic organisation. Their expertise will enhance our ability to inspire value-add solutions across various applications and support further growth in the industrial formulation markets.” www.caldic.com
IMCD GROWS IN SHANGHAI
IMCD has agreed to acquire Shanghai Sanrise Industries & Development (below), one of the leading distributors in the personal care market in China. IMCD will take 70 per cent of the company now and the remaining 30 per cent in 2025; in between, Sanrise’s founders will continue to lead the company.
“The acquisition will provide IMCD with a comprehensive portfolio from leading global suppliers and elevate our technical expertise with the addition of a fully equipped technical centre, putting us in a strong position in the Chinese market,” says Andreas Igerl, president of IMCD Asia. “This is a significant milestone to accelerate our growth momentum by complementing our existing life science portfolio and business.”
The transaction is subject to customary closing conditions and regulatory approval; it is expected to close in the first quarter of 2023. www.imcdgroup.com
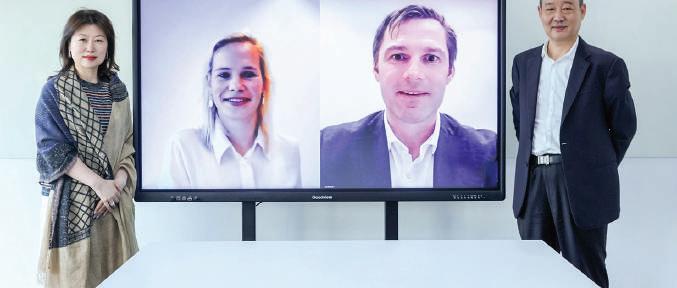
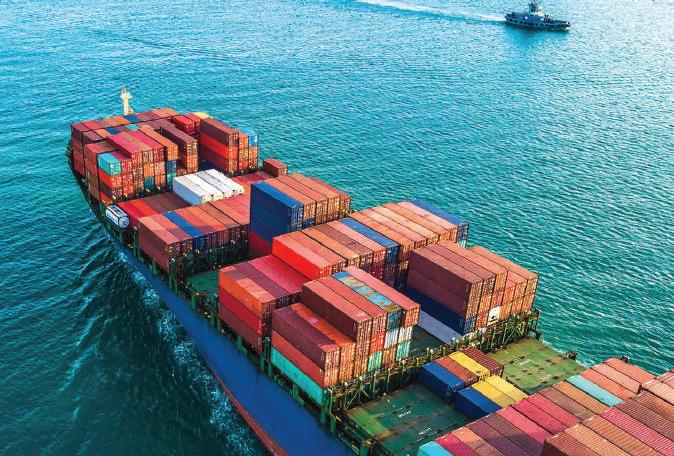
WORK THAT DATA
INSURANCE • THERE IS PLENTY OF DATA OUT THERE ABOUT BADLY SHIPPED DANGEROUS GOODS BUT MAKING SENSE OF IT IS NOT SO EASY. MUNICH RE IS OFFERING ITS HELP TO NCB AND USCG
THERE HAVE, ACCORDING to the International Union of Marine Insurance (IUMI), been an unprecedented number of cargo fires aboard ships over the past five years. In addition to loss of life and serious injuries, damage to property and the vessels themselves has fallen on underwriters. That is not to forget environmental damage and probably uninsured reputational losses arising from subsequent supply chain disruption. IUMI also says that the single largest cause of these fires is improperly shipped dangerous goods in containers, whether due to improper packaging, placarding and stowage aboard the vessel or to unintentional or fraudulent mis-declaration.
National Cargo Bureau (NCB) and the US Coast Guard (USCG) conduct more container inspections than any other country and, as a result, both have captured significant amounts of data and information. Both organisations are looking to leverage this information to allow potentially problematic shipments to be identified more easily and targeted for inspection.
NCB and USCG have been looking for partners with predictive analytical capabilities to analyse their data. They have now found a partner in Munich Re, which is offering them value-added data analysis and modelling to better inform their strategy and decision making in terms of cargo and vessel inspection at ports, allowing them to expand the data fields they are both viewing. Munich Re can also identify certain trends and make recommendations for meaningful data capture.
UNDERSTAND THE DATA Janet Wesner, head of analytics at Munich Re US, explains more: “Analytics starts with data and understanding the data. We worked with both the USCG and NCB to define risk scores based on deficiency types and severities that could serve as proxies for how dangerous the results of an inspection are. From there, by questioning the data and having a dialogue with experts who knew which conclusions were real insights versus artifacts of the data collection process, we were able to provide recommendations into areas to explore further and ways to enhance future data capture.”
“Our global marine expertise and reputation for innovation and investments in data analytics will greatly benefit those in the in the marine community,” adds Sean Dalton, Munich Re’s head of marine underwriting in North America. “It is impossible to inspect all containers, as it would cause massive delays. Any improvements that target ‘higher interest’ shipments hold a huge potential. Our collective, ultimate goal is to prevent improperly shipped dangerous goods from being loaded aboard a vessel.”
That goal will come closer once data from NCB-owned Exis Technologies, which has been specialising in this field for 35 years, is integrated with the inspection data.
“We are delighted to be working alongside USCG and Munich Re to better understand the important data we are generating from our container inspection activities,” says Ian Lennard, president of NCB. “To promote our not-for-profit mission of Safety of Life and Cargo at Sea, we feel it is critical that predictive analytics is incorporated into our work, not only to enhance safety but to ensure that safety becomes more efficient. Through the application of analytics, we allow for a more economical use of industry resources in the prevention of high-risk containers loading onto vessels.”
“Our collaboration with NCB and Munich Re in this specific initiative to deep dive into containerised shipping data alongside cargo and predictive analytic professionals has been extremely influential toward our best efforts of promoting a more widespread safety culture in the world of containerised hazardous material cargo shipping that will ultimately benefit the entire supply chain,” adds John Hillin, USCG’s New York Safety and Security Division chief. natcargo.org
KEEP IT OPEN
SALVAGE • USE OF THE LLOYD’S OPEN FORM CONTRACT FOR SALVAGE HAS BEEN IN DECLINE BUT, AS UNDERWRITERS ARE BECOMING AWARE, ITS USE OFFERS BENEFITS IN THE EVENT OF A CASUALTY
THE WORK THAT salvors do is not only dangerous to life and limb – and the environment – but also financially perilous. Salvage companies need to invest in assets that may be used only intermittently, but those assets need to be available – and at short notice – in the event of a casualty at sea. There are still plenty of casualties, usually in bad weather, and response needs to be fast, with little time to be arguing over the details of a salvage contract.
As such, salvage companies have long relied on the Lloyd’s Open Form (LOF) approach but, in recent years, it has been used less regularly, much to the concern of salvors themselves. But it has come to the point now where underwriters are becoming worried; in July this year, the International Group of P&I Clubs (IG) published the results of an independent review carried out by Hugh Shaw, the former UK Secretary of State’s Representative for Salvage and Maritime Intervention, into the potential for delays in the contracting and engagement of salvage services.
That report found that delays are occurring, with more than 80 per cent of stakeholders feeling that avoidable delays in the engagement of salvage services can open up a casualty to escalation to a point where significant damage, loss and/or danger to life might occur.
“Any delays in decision making may not only have a detrimental effect on the safety of life of those onboard but may ultimately determine the fate of the vessel and its cargo, with the potential for consequential damage to the environment,” the IG report notes. “The consequences of delays in requesting or agreeing salvage services can be disastrous, especially if there is damage, or the potential of damage, to the marine environment.”
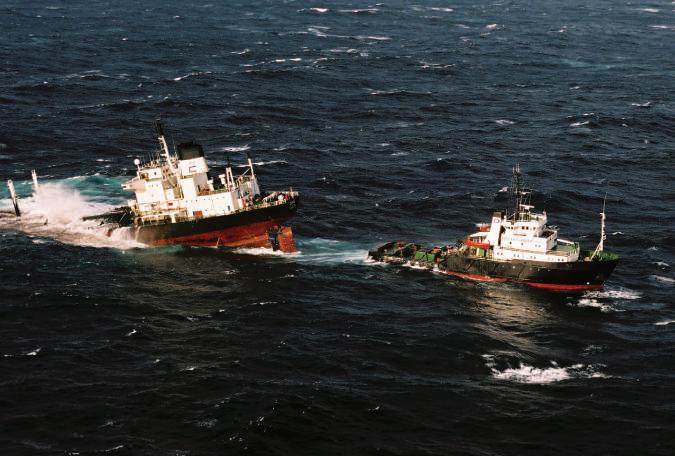
LET’S TALK ABOUT IT Hugh Shaw made a number of recommendations in his report, particularly about the role of LOF in minimising delays in contracting. His comments arrived at an opportune moment since Lloyd’s had been considering closing its salvage arbitration branch. The International Salvage Union (ISU), which represents the majority of the major salvage companies, reports that momentum is now building to reinvigorate LOF and that Lloyd’s has now initiated a programme of work, along with key stakeholders, to encourage greater use of LOF.
The work has been grouped into three streams: linking LOF to the Environmental, Social and Governance (ESG) agenda that is of increasing importance to business, including the shipping and insurance sectors; promoting greater use of LOF contracts in Asia and the Far East; and looking at the awards and costs associated with using the form. Central to all the work streams is consideration of the importance of spreading awareness and understanding of LOF.
The three work groups are made up of a wide range of interested parties, including ISU members. Initial sessions have taken place, with the Lloyd’s salvage group expected to consider their outputs before the end of the year and take into account the independent review report published by IG.
ISU is clear about the benefits of LOF, saying: “Few casualties improve with age and delay can lead to worsening of the situation with the potential for increased risk of loss of property – sometimes even total loss – and damage to the environment. Rapid intervention and full cooperation in the interests of the owner is always the best approach.” www.marine-salvage.com www.igpandi.org
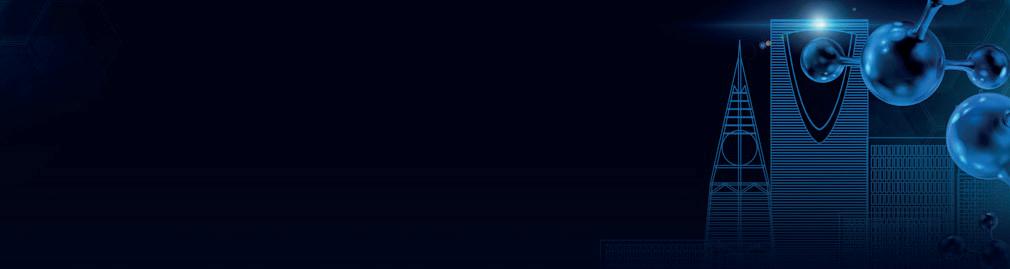
GPCA
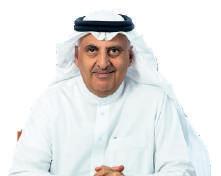
CONFERENCE DIARY
DECEMBER
NISTM DECEMBER 6-7, THE WOODLANDS 15th Annual National Aboveground Storage Tank Conference & Trade Show www.nistm.org
GPCA Forum DECEMBER 6-8, RIYADH 16th annual meeting of the Gulf Petrochemicals & Chemicals Association www.gpcaforum.com
JANUARY
CDG General Awareness Workshop JANUARY 17, CREWE/ONLINE Workshop to update dutyholders on regulatory changes www.chemical.org.uk/training-and-workshops/ cdg-general-awareness-workshop-2/
COHMED JANUARY 23-27, SAN ANTONIO Annual conference of the Cooperative Hazardous Materials Enforcement Development (COHMED) programme cvsa.org/eventpage/events/cohmed-conference/
FEBRUARY
Argus Clean Ammonia Middle East FEBRUARY 14-16, ABU DHABI Conference for pioneers in the new energy sector www.argusmedia.com/en/conferences-eventslisting/clean-ammonia-middle-east
Internationale Gefahrgut-Tage Hamburg 2023 FEBRUARY 27-28, HAMBURG 38th annual conference on dangerous goods transport (German language) www.ecomed-storck.de/Veranstaltungen/ Internationale-Gefahrgut-Tage-HamburgVeranstaltung-Hamburg-27-28-02-2023.html International Energy Week FEBRUARY 28-MARCH 2, VIRTUAL/LONDON Annual week of meetings, conferences and seminars (formerly ‘IP Week’) www.ieweek.co.uk
Intermodal South America FEBRUARY 28-MARCH 2, SÃO PAULO 27th annual international exhibition on intermodal logistics, cargo transport and international trade www.intermodal.com.br/en
MARCH
Battery Recycling Europe MARCH 1-2, LONDON Conference for the battery recycling and manufacturing sectors www.wplgroup.com/aci/event/battery-recyclingeurope/
Hazardex 2023 MARCH 1-2, HARROGATE Conference and exhibition on hazardous area operations and personal protective technology www.hazardex-event.co.uk/
PPC Spring Meeting MARCH 5-7, SAVANNAH Bi-annual meeting and tradeshow of the Petroleum Packaging Council www.ppcouncil.org/upcoming-meetings.php
Hydrogen & Fuel Cells Energy Summit MARCH 8-9, LISBON 6th annual conference to discuss innovations in hydrogen and fuel cell technology, production and transport www.wplgroup.com/aci/event/hydrogen-fuel-cellsenergy-summit/
BADGP MARCH 9, COVENTRY Annual AGM and seminar of the British Association of Dangerous Goods Professionals www.badgp.org/ ChemCon The Americas 2023 MARCH 13-17, SAN FRANCISCO Global conference on chemical regulation https://chemcon.net
LogiChem MARCH 14-16, ROTTERDAM Chemical supply chain and logistics conference http://logichem.wbresearch.com/
FETSA Annual Conference MARCH 14-16, ROTTERDAM Annual conference and AGM of the Federation of European Tank Storage Associations https://fetsa.eu/annual-conference/
StocExpo 2023 MARCH 14-16, ROTTERDAM The main annual exhibition and conference for the European tank terminal industry www.stocexpo.com/en/
LNG Congress Russia MARCH 15-16, MOSCOW Ninth annual congress and exhibition on developments in Russian and Arctic LNG www.lngrussiacongress.com/en
World Petrochemical Conference MARCH 20-24, HOUSTON WPC 2023 provides an outlook on petrochemical supply chain, feedstocks, sustainability and more wpc.ihsmarkit.com/index.html
International Transport & Logistics Week (SITL) MARCH 28-30, PARIS Annual transport event, including hybrid and in-person conferences and workshops www.sitl.eu/en-gb.html
NISTM APRIL 12-14, ORLANDO National Institute for Storage Tank Management’s 25th annual international aboveground storage tank conference and trade show www.nistm.org
INCIDENT LOG
ROAD/RAIL/AIR INCIDENTS
Date Location Vehicle Type Substance Details Source
1/10/22 Sitapur, UP, India road tanker ethanol Road tanker with ethanol from Biswa sugar mill collided with tractor-trolley near Muratpur; tanker overturned, Hindustan igniting spilling ethanol; tractor-trolley driver killed in fire, five other people injured Times
2/10/22 Pietermaritzburg, road tanker oil KZN, South Africa
3/10/22 Jaipur, Rajasthan, India road tanker LPG Road tanker with unspecified oil cargo overturned on N3 highway near Peter Brown Interchange; tanker Sowetan caught fire, driver died; Durban-bound lanes closed during response and cleanup, causing heavy congestion Live
Truck crashed into LPG tanker making u-turn on Ajmer-Jaipur Highway; crash damaged tank valve, leaking Times of LPG but did not ignite; cab, tyres of tanker were on fire; highway closed while LPG was transferred India
6/10/22 Bilhaur, UP, India road tanker carbon Gas tanker overturned after swiping truck on GT Road, causing CO2 to start leaking from tank; police closed Times of dioxide road while fire crews plugged leak, removed vehicles; both drivers suffered minor injuries India
6/10/22 Ilo Awela, road tanker gasoline Road tanker overturned while ascending slope on Abeokuta-Lagos expressway, possibly due to mechanical Vanguard Ogun, Nigeria defect; leaking fuel caught fire, which spread to several other vehicles; two people killed, three injured
6/10/22 Wax, Kentucky, US road tanker fuel Key Oil Co rigid tanker exploded while delivering unspecified fuel to convenience store; blast blew off rear WAVE part of tank; thought that only one compartment contained fuel at the time but cause of blast not known
7/10/22 Palghar, Maharashtra, India road tanker chemicals Road tanker carrying chemicals used in dyes overturned on Boisar Chillar road in Warangade village, cause Times of unknown; no leak reported and no injuries but road had to be closed for two hours while wreck was removed India
7/10/22 Sandusky, freight train paraffin Ten cars of 101-car Norfolk Southern train derailed on bridge over Columbus Avenue; some cars leaked WTVG Ohio, US wax paraffin wax, which solidified, posing no danger; engineers found bridge sound but road work needed
15/10/22 Aligarh, UP, India road tanker gasoline Thief took road tanker and sped off, chased by driver and assistant on motorcycle; tanker overturned, spilling TNN gasoline into ditch; thief fled; locals ran to collect fuel; one minor injury but no fire
20/10/22 Aguascalientes City, road tanker fuel Mexico Road tanker crashed into overpass by rail line, probably due to excessive speed, caught fire; up to 1,000 locals Reuters evacuated; driver arrested; only one minor injury; initial reports said truck had hit a train, though not the case
20/10/22 Sagamu, road tanker gasoline Road tanker overturned after being hit by speeding truck on Lagos-Ibadan expressway; spilling gasoline Premium Ogun, Nigeria caught fire, tanker exploded; at least ten people killed, five vehicles destroyed in blaze Times
21/10/22 Bhopal, MP, India
23/10/22 Lufkin, Texas, US road tanker gasoline Seven people injured by blast during filling of road tanker at Bharat Petroleum depot in Bakania district; News 18 six of those hurt were HPCL drivers; police suspect explosion was caused by a short-circuit
road tanker baryte Fire broke out in engine of cab hauling tanker (?) carrying baryte (barium sulphate), used in oil drilling fluids; Lufkin driver suspected hose had come loose, splashing oil onto engine; trailer with baryte not badly damaged Daily N’s
23/10/22 New Smyrna Beach,road tanker gasoline Vacuum tanker caught fire while pumping gasoline from underground tank at filling station; three people Daytona Florida, US injured in fire; likely that generator running nearby ignited vapours; fire department investigating Beach N-J
25/10/22 Delray Beach, road tanker fuel Florida, US
26/10/22 Khargone, road tanker fuel MP, India Tank truck with unspecified fuel overturned after being hit by car on I-95, exploding in fireball; five people WPTV injured; car driver cited; widespread damage to road, barriers; locals reiterated safety concerns over highway
Road tanker with unspecified fuel overturned, caught fire; tanker exploded while locals were collecting fuel Times of spilling from tanker; one person killed on the spot, nine more died later in hospital India
MARINE/INLAND WATERWAY INCIDENTS
Date Location Vessel Substance Details Source
5/10/22 Red Sea TSS Pearl containers Major fire broke out in containers aboard containership heading from Jeddah to Aden; thick black smoke FleetMon engulfed superstructure; all crew rescued; vessel later sank, with several reports of containers drifting
8/10/22 Georgetown, Tradewind fuel Guyana Passion Product tanker (7,740 dwt, 2008), heading up Demerara River to Guyoil pier, struck floating bridge that closed FleetMon before all of convoy had passed through; bridge seriously damaged, some damage to tanker
8/10/22 Bangkok, Smooth Sea 18 fuel Thailand Product tanker (7,450 dwt, 2014), in load with unspecified fuel and heading upstream to terminal, lost control FleetMon after passing tug and barges, dropped anchor; brought to a stop close to riverside restaurant, scaring off diners
15/10/22 off Wuqui Island, Kelsey 2 oil, Product tanker (8,420 dwt, 2002), with cargo of oils, chemicals from Hong Kong to Gunsan, sank in Taiwan FleetMon
Taiwan chemicals Strait after reporting water ingress in aft section; one crew died, all others were rescued
MISCELLANEOUS INCIDENTS
Date Location Plant type Substance Details Source
2/10/22 Clayton, N Carolina, US oil depot kerosene Some 2,000 gal (7,500 litres) spilled to creek behind high school; though that winds from Hurricane Ian had WRAL caused damage at TR Lee Oil & Gas facility; hay bales deployed to soak up spill
4/10/22 Kazanlak, weapons fireworks One killed, one seriously injured, two missing after explosion at Arsenal weapons plant in unit preparing Novinite SZ, Bulgaria factory material for fireworks; workshop destroyed in blast; prosecutor filed charges for failure to follow safety rules
4/10/22 Chirchik, chemical fertiliser Fire broke out in synthesis shop at Maksam-Chirchik plant, leading to explosion that injured two employees; Urdu Uzbekistan plant no off-site impact; other units at site were not damaged and continued work; investigation underway Point
15/10/22 Westlake, chemical chemicals Fire broke out in Ziegler alcohol synthesis unit at Sasol’s Lake Charles chemical complex; brief shelter- KPLC Louisiana, US plant in-place order but no off-site impact recorded; no injuries; Sasol investigating cause
20/10/22 Morena, MP, India house fireworks Four killed, six injured by explosion that demolished house being used to store firecrackers at Banmor Naga; NDTV officials investigating whether the explosion was initiated by gunpowder or by a gas cylinder
22/10/22 Malik, Syrdaria, military ammunition 16 people were injured by an explosion in a Ministry of Defence warehouse, presumably due to initiation of kun.uz Kazakhstan warehouse stored ammunition; nearby homes, shops suffered damage; military experts investigating incident
23/10/22 Vijayawada, shops AP, India fireworks Fire broke out in cluster of shops set up to sell firecrackers for Deepavali festival; two people killed in fire, PTI said to be workers sleeping in the shops; locals worried that shops were allowed to set up opposite fuel station
27/10/22 Pengerang, oil refinery oil Johor, Malaysia Fire broke out in pipework at Petronas refinery in Pengerang Integrated Complex, followed by explosion; NST Petronas fire crews responded, dealt with blaze; no casualties reported
27/10/22 Kaohsiung, oil refinery gas Taiwan Explosion, fire in CPC’s Dalin refinery was seen from several kilometres away; fire started in hydrotreater SCMP in desulphurisation unit during maintenance, possibly due to gas leak; no injuries reported
3/11/22 Sta Maria, Bulacan, fireworks fireworks Ten people, eight of them employees, were injured by explosion in fireworks factory in residential area of Sun Star Philippines factory Sitio Manggahan; police said that factory lacked the necessary permits to operate
TRAINING COURSES
Build your skills and confidence as a regulatory professional
Get the training you need to stay informed, develop your product safety and compliance strategies.
Attend our training courses around the world led by accredited trainers who are experts in their field. Key training course topics include:
• Biocides
• Toxicology • Chemistry • TSCA
• REACH
• Food contact regulations
Discover the right training course for you and start your professional development journey: events.chemicalwatch.com/training-courses
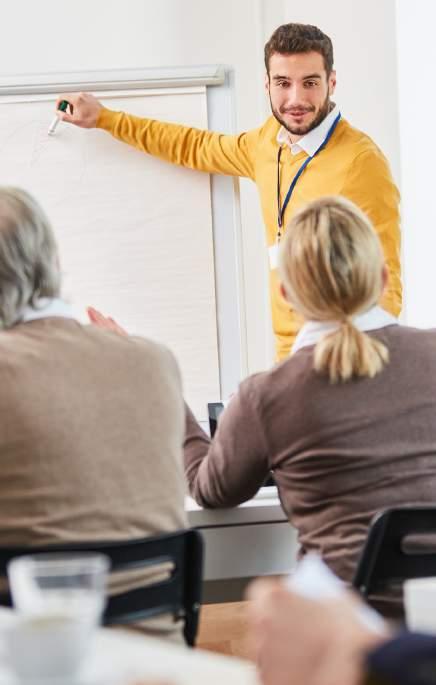
SPLASH AND BURN
LITHIUM BATTERIES • SEVERAL RECENT FIRES HAVE CONCENTRATED THE MINDS OF MARINE UNDERWRITERS REGARDING THE SAFE TRANSPORT OF LITHIUM BATTERIES
THE HAZARDS POSED by lithium batteries during transport were first identified in the aviation sector; protecting aircraft and those in them from those hazards has been a major driver in the developing regulation of lithium batteries. However, after a number of shipboard fires during the course of this year, the maritime sector is also waking up to the threats posed by lithium batteries in containerised goods, whether they are properly declared or not.
To raise awareness of the hazards that such batteries present, Thomas Miller’s two mutual insurance businesses, TT Club and UK P&I Club, have worked with scientific consultant Brookes Bell on a white paper that outlines many of the numerous challenges facing the shipping industry and the potentially catastrophic situation that can be caused by battery failure. The three parties hope that this will help in correcting the widely held perception in the maritime community that risks in the supply chain of such products are relatively small.
“Recently, serious and sometimes catastrophic incidents involving lithium-ion batteries have become more commonplace, with fires reported in all modes of transport – ocean, air and land - as well as in warehouses and where such consignments are at rest,” notes Peregrine Storrs-Fox, risk management director at TT Club.
The topics covered in the white paper include details of the science behind lithium-ion batteries, the dangers they can pose during transport and the reasons for those hazards, such as insufficient testing and incorrect declaration. The paper also provides a review of current regulatory provisions, focusing on the International Maritime Dangerous Goods (IMDG) Code, with recommendations for change or further work. The final section of the paper discusses the current state of the firefighting provision and changes that could be implemented.
“The consequences of battery failure and the resultant thermal runaway must be clearly understood and the correct procedures for handling them adhered to throughout their lifespan,” comments Stuart Edmonston, loss prevention director at UK P&I Club. “The dangers can exist no matter the status of the battery; charged, semi-charged, used, second-hand or scrap, and whether present in devices and vehicles or packaged separately.”
KEEP UP AT THE BACK The white paper does not limit itself to the cause of lithium battery thermal runaway but also offers advice on extinguishing fires and puts forward suggestions and guidelines for helping to pre-empt dangerous goods incidents through correct classification and declaration. Safe and effective packaging, mandatory markings and labelling, uniformity of regulations regarding testing and suitable storage environments while batteries are awaiting transport can all play a part in reducing risk and should be encouraged.
The white paper also calls for action in various areas, some of which are already being addressed by the relevant regulatory authorities, such as the provision of the lithium battery test summary to parties along the supply chain and the classification and marking of electric vehicles during their transport. The authors suggest more guidance would be valuable on how to prevent short circuits and that the 30 per cent state of charge limit imposed for air transport should be picked up by the other modes.
With ongoing technical development and massive growth in the volume of batteries being transported as the world seeks ways to move away from carbon-heavy energy sources, the risk during transport is also growing. Dr Karwei So, managing scientist at Brookes Bell, says: “While increased industry awareness is crucial and technology to monitor and restrict fires is advancing, the increased capacities of batteries and the expected rise in trade volumes means regulations are potentially not fit for purpose, having been slow to catch up.”
The joint white paper can be downloaded free of charge from the TT Club website at www.ttclub.com/news-and-resources/ publications/lithium-batteries-whitepaper.
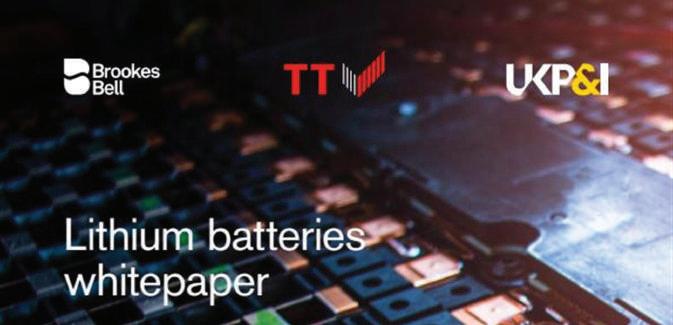
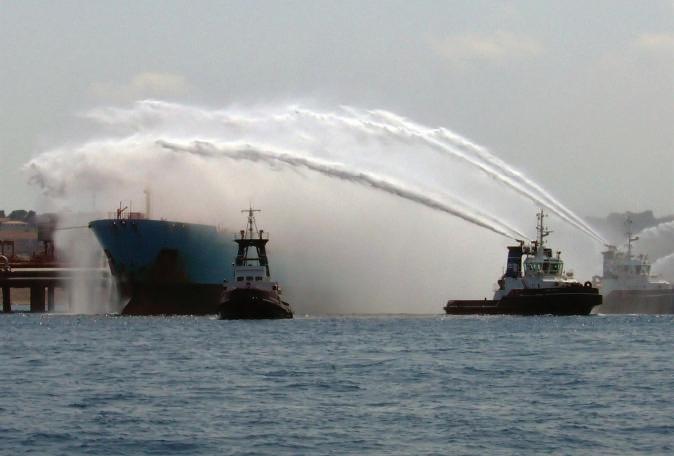
USE IT OR LOSE IT
CONTAINER FIRES • CONTINUED VIGILANCE IS NEEDED IF THE SHIPPING INDUSTRY IS TO BE ABLE TO LIMIT THE NUMBER OF CONTAINERSHIP FIRES. TT CLUB HAS PLENTY OF TOOLS TO HELP ENVIRONMENTAL IMPACTS
THE FREIGHT TRANSPORT and logistics insurance specialist insurer TT Club is continuing its battle to convince cargo interests, supply chain professionals and enforcement agencies that the responsibility for mitigating containership fires is shared by numerous entities across the entire global supply chain. The estimated 60-day average occurrence of serious fires was been maintained recently by the Zim Charleston fire in August and the TSS Pearl in the Red Sea in early October. TT Club is once more urging a more comprehensive approach to arresting the trend.
“There were significant lessons coming from the sad incident on the MSC Flaminia, which cost the lives of three seafarers, particularly from the subsequent legal proceedings that adjudged the shipper and NVOC responsible for root cause errors,” says TT Club’s Peregrine Storrs-Fox. “Despite the biennial updates to the IMDG Code, including multiple arising from this particular incident, the judge’s assessment that the regulations merely set the ‘baseline’ for good practice remains utterly true today.”
Ensuring compliance with the latest mandatorily applicable version of the International Maritime Dangerous Goods (IMDG) Code is essential as a minimum standard for all those shipping dangerous goods by sea. But the liability judgment in the MSC Flaminia case made it clear that regulations merely set the baseline. “This is an important statement to which any entity inclined to rely solely on the letter of the law when consigning dangerous goods, would do very well to pay heed,” comments Storrs-Fox. HELP IS OUT THERE TT Club advocates a comprehensive approach, striving to bring an understanding of all the factors contributing to these fires to all those involved in the movement of cargo in containers and underlining their responsibilities for safety. Errors, misunderstandings, mis-declarations and inadequate packing and securing lie at the heart of many significant incidents, both at sea and in storage facilities. Attention to accurate classification and declaration are critical to improve certainty of outcome from end to end. This requires truth as much as awareness of regulations and sound safety practices.
TT Club, along with its sister insurer the UK P&I Club, has worked hard to disseminate awareness and knowledge; most recently, they have updated the guideline publication Book it Right, Pack it Tight, which provides key insights for all those involved in the shipment of dangerous goods by sea. Closely related but with a broader applicability, and as part of the industry-wide Cargo Integrity Group, TT Club has contributed to the ‘quick guide’ to the IMO/ ILO/UNECE Code of Practice for Packing of Cargo Transport Units (CTU Code). While this Code is non-mandatory, it is referenced in the IMDG Code and, as the MSC Flaminia case showed, industry standards are just as important as regulation when it comes to assigning liability.
TT Club’s campaign to influence industry will continue with a series of webinars in early 2023 on the subject of containership fires and the ongoing efforts to prevent them. The intent is to attract awareness and debate, particularly around innovations that could materially improve the risk profile. These online forums will contribute further to the valuable weight of knowledge and expertise in the arena.
“The complexities of the global container trades increase rather than diminish,” concludes Storrs-Fox. “No one entity can surmount the dangers of these horrific fires, as a consequence it is essential that the entirety of the risk faced should be embraced by all involved through the supply chain if they are to be successfully reduced.”
HCB will alert readers to the upcoming webinars; meanwhile, they will also be announced on the TT Club website, www.ttclub.com.
TT CLUB IS LEADING EFFORTS TO ERADICATE THE
SCOURGE OF FIRES ABOARD CONTAINER CARRIERS

A CLEAN SLATE
MULTIMODAL • NOW THAT THE 2023 REGULATIONS ARE AGREED AND PRINTED, ATTENTION IS TURNING TO THE NEXT ROUND OF REGULATORY AMENDMENTS DUE TO ENTER INTO FORCE IN 2025
THE AUTUMN SESSION of the Joint Meeting of the RID Committee of Experts and the Working Party on the Transport of Dangerous Goods (WP15) of the UN Economic Commission for Europe was held in Geneva from 12 to 16 September 2022, with Claude Pfauvadel (France) in the chair and Silvia Garcia Wolfrum (Spain) as as vice-chair.
The purpose of the Joint Meeting is to maintain, insofar as is possible and desirable, harmonisation between the modal regulations covering the transport of dangerous goods by rail (RID), road (ADR) and inland waterway (ADN) in Europe, and with the international regulations for transport by sea and air. The September session arrived after the finalisation of the amendments to those regulations that will enter into force in January 2023 but before the final meeting of the biennium of the UN Sub-committee of Experts on the transport of dangerous goods; the parent Committee was only due to adopt the latest set of amendments to the UN Model Regulations this month so it was premature of the Joint Meeting to take those into account.
It was, as a result, a relatively short agenda that faced the delegates who met in Geneva or attended the meeting online. The UN office in Geneva is aiming to return to ‘business as usual’ from 2023, with the next sessions expected to be in-person only. For this meeting, 23 countries were represented as full members, along with the European Commission, EU Agency for Railways (ERA) and 19 non-governmental organisations represented in a consultative capacity.
TANKS MATTERS The International Union of Wagon Keepers (UIP) rehearsed earlier discussions – going back as far as 2014 – about the use of digital inspection reports and tank records, which had not delivered a provision to accept such electronic documents. It is now the case that digital versions, including a ‘simple electronic signature’, are the only copies provided by accreditation bodies; UIP returned to its 2014 proposal to add a note to recognise this alternative.
As time has gone by, it would appear that the experts had become more comfortable with the idea, although some concerns were raised about the ambiguity of the words ‘suitable’ and ‘secure’ in UIP’s proposal. In the end, on a majority vote, a slightly amended version was adopted as a Note to 4.3.2.1.7:
The tank record may alternatively be maintained in electronic form.
The UK followed up on discussions at the previous Joint Meeting on the use of level gauges and, in particular, whether sight glass gauges meet the requirements of 6.8.2.2.11. At that time, the general feeling was that such gauges should not be allowed for tanks subject to Chapter 6.8 but are suitable for those of Chapter 6.10 (vacuum-operated waste tanks).
The experts agreed the need to clarify the provisions in 6.8.2.2.11 but could not reach an agreement and, taking note of the diverse
technologies available for tank level gauges, it was decided to defer discussion to the next session. The Working Group on Tanks was invited to consider the subject in detail.
The UK also followed up on the proposal at the previous session to develop a standard for relief valves on tank vehicles carrying dangerous goods other than petroleum products and LPG. At present, the requirements for such relief valves are found in several paragraphs in ADR and, as a result, some manufacturers have developed their own testing procedures or used inappropriate standards. The UK has put a proposal to the relevant technical committee of the European Committee for Standardisation (CEN), which was due to meet in November.
The Joint Meeting welcomed the UK’s input and felt it would be best to be able to include a reference to an existing standard in Chapter 6.8; it encouraged CEN to develop such a standard. It may be that other development work by CEN and/or the International Standardisation Organisation (ISO) will be relevant (see below).
The remaining papers on topics relating to transport in tanks were remitted to the Working Group on Tanks, which met concurrently with the plenary session under the chairmanship of Arne Bale (UK). Its deliberations resulted in two specific proposals.
Firstly, Russia proposed a clarification for calculating the shell thickness of P22DH tanks for the transport of chlorine (UN 1017) and phosgene (UN 1076), as the existing text makes no reference to the calculation pressure for Class 2 gases. It offered three options for amendments, of which the Joint Meeting chose the addition of “or in the table of 4.3.3.1.1” at the end of the definition for ‘Pc’ in 6.8.2.1.17.
Secondly, the UK returned to the issue of the accreditation of inspection bodies for the authorisation and surveillance of in-house inspection services; it had been decided at the March 2022 session that this should be addressed during the next biennium, for which the September session was the first meeting. The purpose of the work would be to improve the precision of the wording relating to such matters and to take into account the relevant clauses in EN ISO/ IEC 17021-1:2015 and the work of the European Cooperation for Accreditation (EA), particularly the EA Document on Accreditation for Notification Purposes.
Following discussion of the UK’s paper by the Working Group on Tanks, the UK offered to Who do you contact for the latest DG compliant labels?
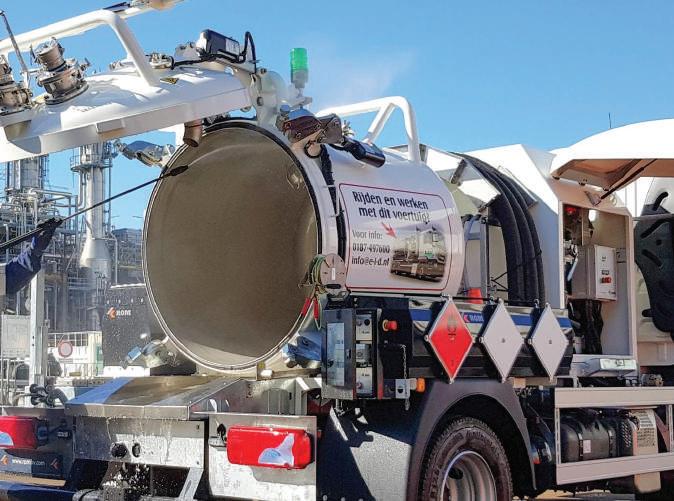
Free DG Label ID poster with every order
Tel: +44 (0)870 850 50 51 Email: sales@labeline.com
www.labeline.com
develop a short proposal to better set out what is expected of an inspection body when assessing the competence of an in-house inspection service in relation to the requirements of 1.8.7.7.2(a) of RID/ADR.
WORKING GROUP ON STANDARDS CEN provided the Working Group on Standards with an update of its work on those standards of relevance to the transport of dangerous goods, including some new work items and reports on the progress of others already in the pipeline. The Secretariat also noted that revised versions of EN 14025 and EN 13799, which had already been adopted by the Joint Meeting, had not been published in time to be notified for inclusion in the 2023 texts of RID/ADR. It proposed therefore that they should be added to the list of amendments for the 2025 texts.
As a result of those reports, the Joint Meeting adopted several changes. Firstly, in Table 4.1.6.15.1, reference to EN ISO 11114-2:2013 is updated to the 2021 edition.
In the table ‘for design and construction of closures’ in 6.2.4.1, a new row is added at the end for EN 13799:[2022] LPG equipment and accessories – Contents gauges for Liquefied Petroleum Gas (LPG) pressure vessels.
In the table in 6.8.2.6.1, under ‘For design and construction of tanks’, the existing row for EN 14025:2018 + AC:2020 will now expire on 31 December 2026 and a new row is added for EN 14025:[2023].
In the same table, under ‘For equipment’, the existing row for EN 14432:2014 will now expire on 31 December 2016 and a new row is added for EN 14432:[2023]. The same change is made for EN 14433:2014. A new row is added at the end for EN 13799:[2022].
Finally, in 6.8.4(d), TT11 in the paragraph after the table, ‘EN 14025:2018’ is replaced by ‘EN 14025:[2023].
The RID Committee of Experts’ standing working group had considered including a reference to EN 14841 in the 2023 text of RID but felt that this would be premature, as it is not expected to be published until well into 2023. Moreover, even though its use would be voluntary, the standing working group felt that there were problems in its contents and the nature of its development.
CEN reported back on an issue raised by France a year earlier concerning the difficulties experienced when applying EN ISO 11118:2015, as referenced in 6.2.4. Those issues had been forwarded to the relevant ISO Technical Committee, which in October 2021 agreed to establish a Task Force of experts to review the points that had been raised. That Task Force acknowledged that some improvements and clarifications could be made without affecting the scope or content of the standard. The matter was to be discussed by the relevant Technical Committee in October 2022 and it is to be hoped that a revised version will be made available during 2023.
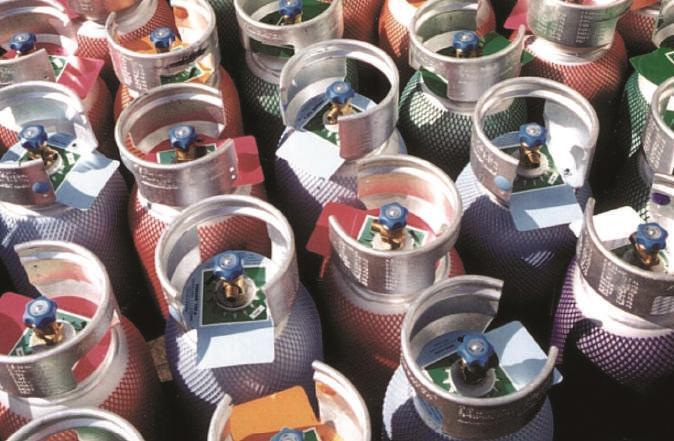
PROPOSALS FOR AMENDMENT Germany came back as promised with a formal proposal to add a new special provision for damaged or defective lithium batteries. At the previous session, it had noted that special provision 376, which was brought into RID/ ADR from the UN Model Regulations, with some amendment, differentiates between batteries that are liable to react dangerously under normal conditions of carriage and those that are not prone to such a reaction. However, SP 376 does not provide full information on the transport category, which is crucial in RID/ADR for the application of the small load relief in 1.1.3.6.
Recalling that the Joint Meeting had already agreed to the need for change, the experts opted to add a new special provision 677:
Cells and batteries which, in accordance with special provision 376, are identified as damaged or defective and liable to rapidly disassemble, dangerously react, produce a flame or a dangerous evolution of heat or a dangerous emission of toxic, corrosive or flammable gases or vapours under normal conditions of carriage, shall be assigned to transport category 0. In the transport document, the words “Carriage in accordance with special provision 376” shall be supplemented by the words “Transport category 0”.
This new special provision 677 is assigned to UN Nos 3090, 3091, 3480 and 3481 in column (6) of the Dangerous Goods List in Table A of Chapter 3.2.
In addition, the last sentence of SP 376, which reads “In both cases the cells and batteries are assigned to transport category 0.”, is deleted. Delegations were invited to submit proposals for any further amendment they deemed necessary.
Germany had also been doing some research into the assignment of packing instruction R001 to the two entries under UN 1308 for zirconium suspended in a flammable liquid, PG II. This is inconsistent with the
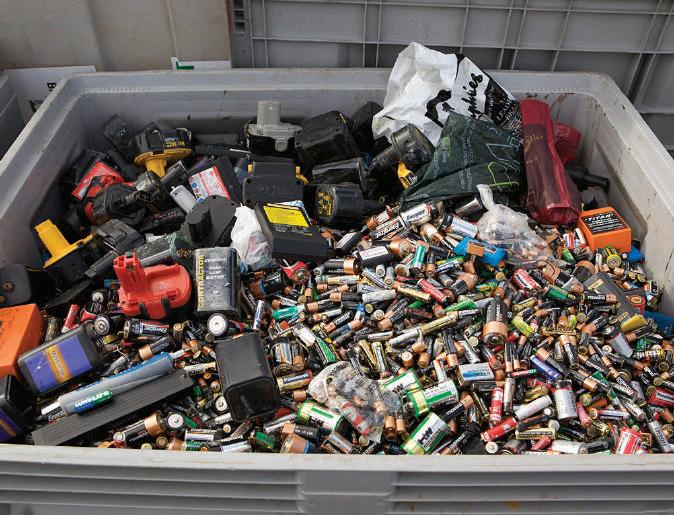
assignment of special packaging provision PP 33, which allows only combination packagings, while R001 refers to light-gauge metal packagings, which are single packagings In addition, the first entry for UN 1308 has a vapour pressure more than 11 kPa at 50°C, which is not allowed in packagings conforming to R001.
The European Chemical Industry Council (Cefic) volunteered to look into the background of packing instruction R001 to the second entry for UN 1308 and, while the Joint Meeting agreed on the rationale for its removal from the first entry, it was decided to resume consideration of the subject at the next session.
The Council on Safe Transportation of Hazardous Articles (COSTHA) came back to its two queries on home deliveries, which had been raised at the previous session and also at the summer meeting of the UN Subcommittee of Experts. The first of these looked at the challenges posed by direct-tocustomer delivery services, which may involve the transport of dangerous goods such as aerosols, corrosive cleaning products, organic peroxides, flammable liquids and lithium batteries. When consumers buy these goods at the store and take them home, they are in retail packaging and also exempted from the provisions of ADR; if they are delivered by the retailer’s own vehicles, do the provisions apply? If not, should this not be made clear? COSTHA offered an additional paragraph for 1.1.3.1, based on existing UK and Canadian exemptions.
There was some support for COSTHA’s proposal but some delegations felt the proposed amendments were too broad in scope and they wanted time to carefully consider potential loopholes. There were also questions about some of the terminology used in the proposal and, indeed, some felt that the issue was best dealt with at the national level. Nevertheless, the Joint Meeting agreed to resume consideration of the subject at its next session, possibly on the basis of a revised proposal from COSTHA.
COSTHA also raised the issue of the use of handling devices by parcel delivery and postal services to assist in the organisation of parcels within a delivery vehicle. These bags could be regarded as overpacks, as they may well contain dangerous goods, most likely in limited quantities. However, their contents do not remain constant throughout the delivery route and it would be difficult to ensure that
Free DG Label ID poster with every order
Tel: +44 (0)870 850 50 51
Email: sales@labeline.com www.labeline.com 2023 IATA DGR
Free worldwide shipping from IATA’s leading international distributor Do you consign Dangerous Goods?
For a local, professional consultant DGSA, contact Labeline The ‘Biennial’ returns!
Tel: +44 (0)870 850 50 51 Email: sales@labeline.com
www.labeline.com
the bag is correctly marked at all times.
COSTHA had also noticed that the definition of overpack in RID/ADR/ADN differs from that in the UN Model Regulations, whereas the international air and sea regulations and domestic regulations in the US and Canada are in alignment with the UN. It offered some options to harmonise the different provisions.
Once again, there was no agreement on the proposal, with some delegates observing that the definition of overpack in RID/ADR/ADN had been deliberately chosen to allow for differing practices. There were also those who felt that the change would be too broad and may have unintended consequences. The proposal also kicked off a discussion as to whether two- and three-wheeled vehicles are covered by ADR. The Joint Meeting will, though, pick up on the subject again at its next session, once more potentially on the basis of a revised proposal from COSTHA.
The impending expiry of the transitional period in 1.6.1.44 that relieves consignors of the duty to appoint a safety adviser (DGSA) has concentrated the minds of many in the industry. The UK also observed that the existing exemption in 1.8.3.2(b), which applies to undertakings for which their main or secondary activity does not include the carriage or handling of dangerous goods, applies to carriers, packers, fillers, loaders and unloaders, but not to consignors. In an informal document it asked whether this should not be rectified.
The Joint Meeting had no hesitation in agreeing to the change and, having renumbered the relevant paragraph as 1.8.3.2(c) in ADR and ADN to mirror that in RID, decided in all cases to insert “consignment,” before “carriage”, twice.
Cefic raised a similarly urgent issue, which is the expiry of the transitional period under 1.6.1.46 on 31 December 2022; after then, the exemption in 1.1.3.1(b) for dangerous goods in machinery and apparatus will disappear. While some new provisions relating to the carriage of articles (in particular UN 3363 and UN 3537 to 3548) include an appropriate alternative, industry is concerned that they do not address all current operations, especially those involving the transport of articles, machinery and apparatus for repair or maintenance.
Some delegates agreed on the urgent need to review the relevant provisions; while a new special provision might offer a solution, in the meantime a multilateral agreement could be initiated to resolve the urgency of the matter.
Liquid Gas Europe alerted the Joint Meeting to the need to discuss revising the definition of LPG in light of the introduction of ‘bioLPG’ and other renewable fuels such as renewable dimethyl ether. It sought to open a discussion prior to putting forward a formal proposal at the next session. Liquid Gas Europe, in collaboration with the World LPG Association, was also planning to submit a similar paper to the November/December session of the UN Sub-committee of Experts.
Most delegates who took the floor supported the initiative in principle and were keen to learn more in future about the percentage of blends with dimethyl ether. The Joint Meeting underlined the need to coordinate any amendments with the UN Model Regulations, while Germany offered the suggestion that a new special provision might be a more elegant solution. Liquid Gas Europe said it would consider that option and will also return with an official document at the next session, bearing in mind the outcome of discussions by the UN Sub-committee.
The European Federation of Waste Management and Environmental Services (FEAD) sought a revision of 4.1.1.22 to include reference to liquid waste classified under 2.1.3.5.5, for which the testing for chemical compatibility with plastics packagings is, from a practical point of view, difficult or impossible.
The Joint Meeting was not opposed to the suggestion, though it was felt an amendment of 4.1.1.21 might be preferable. FEAD invited interested delegates to send written comments so that it can prepare a new document for the next session.
FEAD had a similar query about the transport of packaged waste in combined packaging. When original products are so
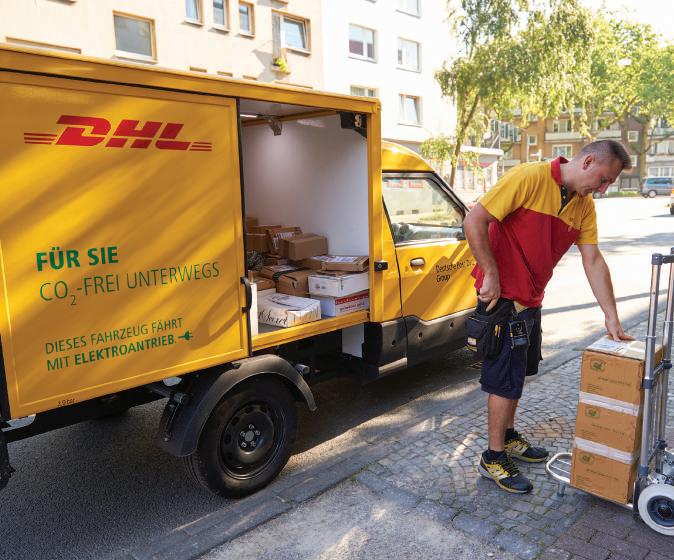

Free worldwide shipping from IATA’s leading international distributor Do you consign Dangerous Goods?
packaged, the inner and outer packagings are specifically tested for that purpose; however, when waste is collected, it is most common for only the inner packaging to be available. Nevertheless, the waste must be sorted according to its hazardous properties and be packaged in compliance with the regulatory requirements. There is currently no simple way to do this and, in the absence of such rules, some countries have developed their own national derogations, although this does not help if an international movement is required.
FEAD offered an amendment in the form of a new 4.1.1.5.3, though the UK in particular raised concerns about the proposals. Delegates were again invited to send written comments to FEAD, which will prepare a new document for the next session.
FEAD also raised the question of the disposal of household waste, such as empty aerosols or packagings for corrosive products, in the general waste stream. It felt that new text could be added to 1.1.3.1(a) to clarify the exemption of such waste. Again, it was felt that more work was needed on the proposal and FEAD will take another look.
France had a query about the applicability of
the training requirements in Chapter 1.3, specifically about the training of ‘consignees’ when those are persons at private homes or small businesses where heating oil, LPG or similar products are being delivered. Are such individuals considered ‘consignees’ according to Chapter 1.4? Opinion was divided; some said that anyone Free DG Label ID poster with every order taking delivery of dangerous goods should be considered as a consignee, others that those at a private home should be differentiated from businesses, whether small or large. It was, though, acknowledged that some consignees would not be able to meet the training requirements. France offered to prepare a more detailed document for the next session. WORKING GROUP REPORTS Germany provided a resume of the discussions of the informal working group on the carriage of molten aluminium (UN 3257). This product is carried in bulk in accordance
Tel: +44 (0)870 850 50 51 with special provision VC3, which provides for Tel: +44 (0)870 850 50 51
Email: sales@labeline.com the competent authority of the country of Email: sales@labeline.com www.labeline.com origin to specify conditions of carriage. The www.labeline.com result of the work involved a proposal for a new alphanumeric code AP 11 in 7.3.3.2.7,
All UK consignors must have an appointed DGSA by 1st January 2023 For a local, professional consultant DGSA, contact Labeline The ‘Biennial’ returns! THE multimodal regulatory update webinar 18th October 2022
You need Labeline.com
Labeline is the leading worldwide “One Stop Dangerous Goods Service” for Air, Sea, Road, and Rail
We serve Freight Forwarders, Shippers, Airlines, DCA’s, Port Authorities, Petrochemical industry and the Pharmaceutical industry.
Labeline is one of the world’s leading regulatory services and product provider; we hold comprehensive stocks with a fast worldwide delivery service.
We are one of the very few authorised Multi-mode providers worldwide and described by industry as a pro-active organisation, our name is recommended by many leading authorities and a world class service providers.
When it’s time to order your DG products and services, Labeline will be your “One Stop Service”
Compliant with IATA, ICAO, ADR, IMDG, RID, DoT
Dangerous Goods Labels Regulations Documentation Packaging Software Training GHS Chem Regs
Tel: +44 (0)870 850 50 51 Email: sales@labeline.com
www.labeline.com
setting out uniform minimum requirements for carriage.
The Joint Meeting welcomed the report and there was support for the proposed provisions. After discussion, Germany invited written comments and said it would aim to submit an updated proposal for the next session.
A report on the first meeting of the informal working group on e-learning was provided by Germany and the International Road Transport Union (IRU). The meeting had received several presentations and comments about existing e-learning and online training courses, while noting that the legal standing of such courses differs significantly between countries. It was widely agreed that e-learning is suitable for refresher training (though not for practical elements) but there were mixed opinions about initial training. Some felt that the decision should be left to national competent authorities, though others noted that, were e-learning to be accepted as an alternative to in-person training, then appropriate provisions should be included in Chapter 8.2 of ADR.
The informal working group was due to meet again in October and expected to hear from other training institutes. The Joint Meeting invited the group to develop any necessary amendments to ADR/ADN for consideration at its next session.
FEAD presented the minutes from the fifth meeting of the informal working group on the transport of hazardous waste, which had taken place in June 2022. The Joint Meeting welcomed the group’s conclusions and noted its intention to meet again to finalise a draft proposal for the transport of asbestos in bulk for consideration by the Joint Meeting at its next session.
ERA provided a progress report on the informal working group on the improvement of the Transport of Dangerous Goods occurrence report, ahead of the anticipated adoption of the Common Safety Methods on the Assessment of Safety Level and Performance of Railway Operators (CSM ASLP) by the European Commission later this year or early in 2023. As a result, it would be beneficial to align the accident reporting requirements in 1.8.5 of RID with those in the CSM ASLP, which are somewhat more streamlined. There are several other points on which the two systems diverge and ERA is continuing to coordinate work ahead of a planned proposal of amendment to RID/ADR/ ADN for consideration at the next session.
OTHER BUSINESS Four informal documents were presented on the topic of the use of electronic freight transport information (eFTI) and the work of the Digital Transport Logistics Forum (DTLF). The current data model, developed in the context of the EU Regulation 2020/1056, do not take account of the specifics of dangerous goods transport and an informal working group on telematics has been investigating the differences in architecture principles. It was stressed that eFTI and dangerous goods experts need to work together to ensure close cooperation and resolve any potential issues.
The EU stressed that the DTLF work was still ongoing, in particular on the datasets, data models and architecture models for the transport of dangerous goods, and that input from the Joint Meeting would be valuable.
In terms of the UN’s Sustainable Development Goals, the Secretariat advised the Joint Meeting that the terms of reference of the Inland Transport Committee (ITC) have been revised and that it will be looking for the Joint Meeting to report back on aspects of its work related to the circular economy. Delegates were invited to contribute to the discussion. The Joint Meeting agreed that this topic should form a new agenda item to ensure regular discussion.
Claude Pfauvadel and Silvia García Wolfrum were re-elected to serve as chair and vice-chair, respectively, for the meetings scheduled in 2023. The chair announced that he is planning to retire shortly and will not be available to serve the Joint Meeting from 2024. The next session of the Joint Meeting is scheduled to take place in Bern from 20 to 24 March 2023.

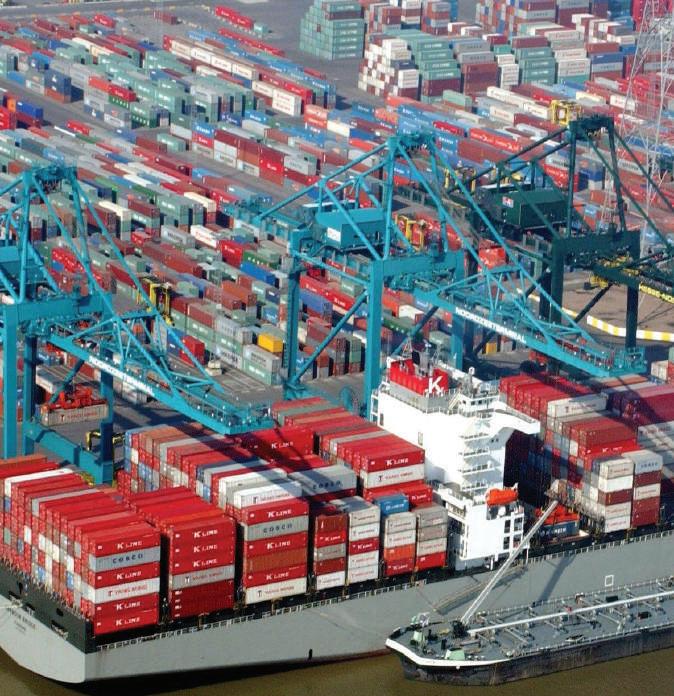
SMALL CHANGE
MARITIME • IMDG CODE AMENDMENT 41-22 IS AVAILABLE FOR USE FROM 1 JANUARY. ALTHOUGH THERE ARE FEW MAJOR CHANGES THIS YEAR, USERS NEED TO BE AWARE OF THE DETAILED UPDATES
THE LATEST UPDATE to the International Maritime Dangerous Goods (IMDG) Code, Amendment 41-22, was adopted by the International Maritime Organisation (IMO) earlier this year and will take effect on 1 January 2023. As usual, there is a one-year transitional period to the end of 2023, during which time the current version, Amendment 40-20, may still be used.
Amendment 41-22 takes account of the changes that appear in the 22nd revised edition of the UN Model Regulations but includes also some mode-specific changes, particularly in terms of stowage and segregation. The regulators, both at the UN and IMO, have been affected by the Covid pandemic just as much as anyone else, and the number of changes included in Amendment 41-22 are fewer in number than is often the case; there are also no major changes for dutyholders to deal with. Nevertheless, they do need to pay close attention to the details of the Amendment if they are to remain compliant.
Exis Technologies has once more published a detailed summary of the changes that appear in Amendment 41-22, which can be downloaded free of charge from its website at https://existec.com/hazcheck/imdg-codefree-summary-of-changes-41-22/. HCB is grateful to Exis for doing the work and for allowing us to provide the following precis.
GENERAL OBSERVATIONS The UN experts picked up on a number of changes introduced by the International Atomic Energy Agency (IAEA) in its SSR-6 document for transport safety; these have been transposed into the IMDG Code as appropriate, notably in 2.7, 5.1 and 6.4.
There are also a number of new and amended definitions in 1.2, particularly affecting inner vessels, pressure receptacle shells and service equipment. In addition, some changes have been made to the security provisions in 1.4.3.2.3 specific to highconsequence dangerous goods (HCDG) to clarify their applicability.
As usual, there are many new and amended self-reactive substances and organic peroxides; a change has also been made to avoid confusion in the selection of control and emergency temperatures for these substances, clarifying the applicability of packing instruction IBC520 and tank code T23.
Also important are various changes in Part 6 concerning the design, construction and testing of packagings and tanks. In most cases these clarify the meaning of the requirements and the terminology used, though they also have consequential amendments. IMO has also adopted the new 6.10 dealing with portable tanks with shells manufactured of fibre-reinforced plastics (FRP) materials, which has led to some changes in 6.7.
In Part 2, the introductory notes to 2.6 now include UN 3462, covering solid toxins from plant, animal or bacterial sources, or toxins contained in substances that are not themselves infectious substances; liquids under UN 3172 are also considered for classification.
There are updates to 2.8.3 on the classification of corrosives, relating to the assignment of packing groups to substances and mixtures. A note is added to 2.9.3.4.3(a) and 2.9.4.7 to extend the exception to the lithium battery test summary requirements to cover button cells installed in equipment.
DG LIST AND SPECIAL PROVISIONS There is only one new entry in the Dangerous Goods List: UN 3550 Cobalt dihydroxide powder, containing not less than 10 per cent respirable particles. The two entries under UN 1169 are deleted and consolidated into UN 1197, renamed Extracts, liquid, for flavour or aroma.
The entry for UN 1439 Ammonium dichromate is amended, with the word “strong” deleted and the properties and observations column now reads merely “acids”; SG75, which applies to strong acids, has been replaced by SG35 in column 16b. Similar changes have been made to a number of other entries. Similarly, all entries assigned SGG1a now have SGG1 instead.
The entry for UN 1891 Ethyl bromide has been changed, so that it is now Class 3 with a Division 6.1 subsidiary hazard; the LQ, EQ and EmS values have been amended and the flashpoint is added to the properties and observations column.
The UN experts corrected one mistake applicable to UN 3208 and 3209 Metallic substance, water-reactive; in UN 3208 PGII, E0 is replaced by E2 and in UN 3209 PGII, E2 is replaced by E0. For polyester resin kits (UN 3527), PGII and III, ‘E0’ is replace by ‘See SP340’, which provides more guidance.
The relatively new entry UN 3538 Articles containing non-flammable, non-toxic gas, nos is assigned a new special provision 396, which specifies the conditions under which ‘large and robust articles’ may be transported with connected gas cylinders and open valves.
There are two more new special provisions. SP397 is assigned to UN 1002 and makes it clear that this entry can apply to mixtures containing not more than 23.5 per cent oxygen by volume when no other oxidising gases are present. SP398 applies to UN 1012 and clarifies its applicability to certain isomers of butylene.
There are amendments to SP188, to remove the elapsed marking provisions, and SP225, which has a new note clarifying that it applies equally to portable fire extinguishers shipped without the necessary components required for them to function.
PACKING AND TANK PROVISIONS There are some important changes in Part 4, including a new sentence added at the end of 4.1.3.3 relating to packagings that do not need to meet the design type test as per 4.1.1.3 and that are authorised in various packing instructions and special provisions. This clarifies that these packagings are not subject to the mass or volume limits of Chapter 6.1, unless otherwise indicated in the packing instruction. Therefore, authorised packagings may exceed 400 kg. Notes to that effect have been added to a number of packing instructions and special packing provisions.
There are a number of other amendments to the packing instructions, especially P200, where special packing provisions ‘d’ and ‘z’ have been revised and the LC50 values for UN 1008, 2196, 2198 and 1052 have also changed. More packaging options are now available for UN 2196 and 2198. P621 also now has more packing options for drums and jerricans. An additional requirement (i) is added in P911 to address consignments of multiple batteries and multiple items of equipment containing batteries, with similar amendments in LP906.
In the intermediate bulk container (IBC) packing instructions, special packing provision B15 in IBC02 has been amended; the new special packing provision B40 is added to IBC07 to provide for the use of flexible IBCs (13H3 and 13H4) with the new UN 3550 entry.
Elsewhere in Part 4, there is a new note to 4.1.1.15 to clarify that the period of use for composite IBCs refers to the date of manufacture of the inner packaging. The maximum size of salvage pressure receptacles in 4.1.1.9.2 has been increased from 1,000 litres to 3,000 litres. In 4.1.6 there are several small amendments to the special packing provisions for Class 2 gases and reference to tanks and IBCs is removed from 4.1.9.1.4.
Chapter 4.2 has several changes that reflect the inclusion of provisions for FRP tanks in the new 6.10. A new sentence is
THE LITHIUM BATTERY MARK WILL NO LONGER NEED TO
SHOW A PHONE NUMBER, AS NONE OF THE REGULATORS
COULD RECALL WHY IT WAS THERE OR WHAT
INFORMATION SHOULD BE PROVIDED BY THE SHIPPER
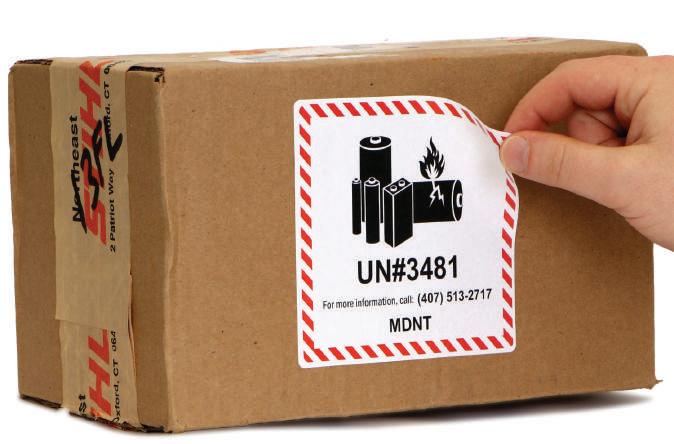
added at the end of the portable tank instruction table for T1 to T22 to clarify that the instructions for FRP tanks apply to substances of Classes 1, 3, 5.1, 6.1, 6.2, 8 and 9. TP32 has been updated to include a reference to FRP material.
LABELLING AND DOCUMENTATION IMO followed the UN’s lead in removing the requirement for an emergency phone number on the lithium battery mark, as no one could remember why it was there in the first place and it is not clear what information should or could be provided.
There are several changes in Chapter 5.4, notably relating to the use of the words ‘molten’, ‘stabilised’ and ‘temperature controlled’, as appropriate, as part of the proper shipping name in documentation. In addition, 5.4.1.5.3 is replaced with new text to clarify that the documentation requirements for approved salvage packagings and receptacles also applies to any other appropriate packagings used. Significantly, 5.4.1.5.17 is no longer specific to ‘Engines’ but has been broadened to apply to all instances where a special provision requires additional information to be included in the transport document.
CONSTRUCTION AND TESTING There are quite a lot of changes in Part 6, especially in Chapter 6.2 (and not just the usual amendments to references to updated and new standards), largely for clarification; and the new 6.10 is added to deal with FRP portable tanks. Those in Chapter 6.2 cover a wide range of containments, including pressure receptacles (as well as specific changes for acetylene cylinders), service equipment, closed cryogenic receptacles, bundles of cylinders and aerosol dispensers.
There are some minor edits in 6.3.2 on the provisions for packagings for infectious substances of Division 6.2, Category A.
Chapter 6.5 has been revised to reflect ongoing product development in the IBC market, with changes to 6.5.1.1.2, and the increasing use of recycled plastics material in the manufacture of IBCs (in 6.5.2.1.2 and 6.5.5).
TRANSPORT OPERATIONS IMO has removed the distinction between ‘acids’ and ‘strong acids’, so the segregation provision SGG1a is deleted from 7.2.5.2; SG75 is also deleted from 7.2.8, as it refers to stowing ‘separated from’ strong acids.
In 7.3.7.2.3.1, the word ‘Stabilised’ is replaced by ‘Temperature controlled’. And in 7.9.3, which gives contact information for the main national competent authorities, reference is now made to using IMO’s Global Integrated Shipping Information System (GISIS) to access up-to-date information.
SCHEDULES AND ANNEXES In the Emergency Schedules (EmS), for UN 1891 Ethyl bromide, ‘F-A, S-A’ is replaced by ‘F-E, S-D’. This follows on from the reclassification of this substance. The new UN 3550 entry for cobalt dihydroxide powder is given ‘F-A, S-A’ schedules.
In the Annex, there are several changes to the Recommendations on the safe use of pesticides in ships applicable to the fumigation of cargo transport units.
CHANGES TO STOWAGE AND SEGREGATION PROVISIONS
WILL IMPACT CARRIERS, WHO WILL HAVE TO UPDATE
THEIR SYSTEMS TO ENSURE THAT THE REVISED
REQUIREMENTS ARE REFLECTED IN THEIR OPERATIONS
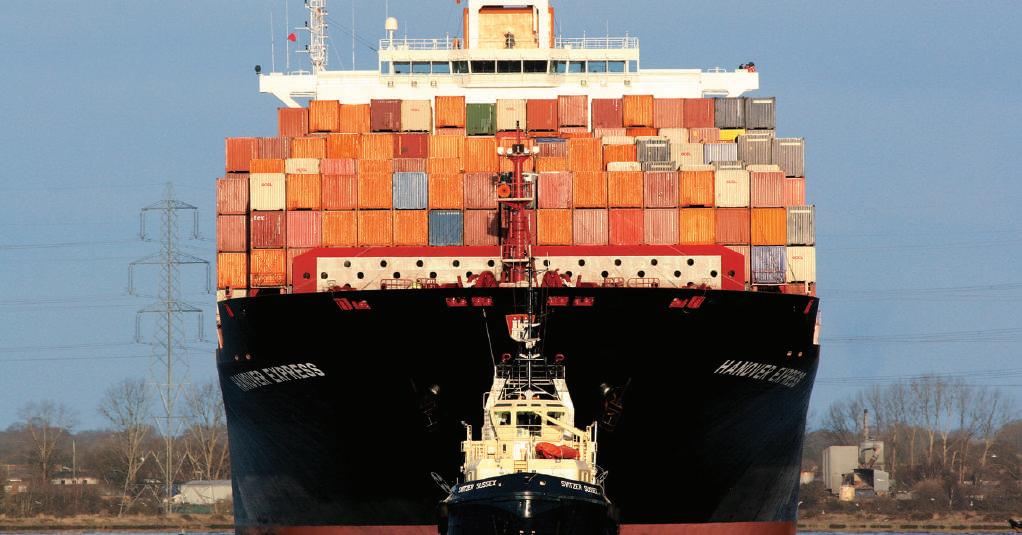
Intelligence to transform Intelligence to transform product safety product safety Our new membership gives you and your colleagues unlimited use of our new class-leading platform, featuring:
Timely, in-depth, impartial and easy to News and insight understand global coverage from our award-winning team of industry journalists Timely, in-depth, impartial and easy to to inform your product safety strategy. understand global coverage from our award-winning team of industry journalists Leveraging our unique network of contacts, to inform your product safety strategy. we dig deeper into the issues, developments, challenges, and drivers to give you a Leveraging our unique network of contacts, thorough overview of the topics important we dig deeper into the issues, developments, to you and your business. challenges, and drivers to give you a thorough overview of the topics important to you and your business. Tools and directories Regularly updated, practical directories and Tools and directories databases so you have the data you need on-hand, plus the latest job opportunities, Regularly updated, practical directories and industry events and company news to databases so you have the data you need promote you and your team’s development. on-hand, plus the latest job opportunities, industry events and company news to promote you and your team’s development.
Custom insight
Bespoke materials and insights for you Custom insight and your organisation from our dedicated analyst team, as and when you need it, Bespoke materials and insights for you so you can make throughly informed and your organisation from our dedicated decisions in your product safety strategy. analyst team, as and when you need it, so you can make throughly informed decisions in your product safety strategy.
Resources
An extensive range of resources saving time Resources and arming your team with the intelligence you need, including: An extensive range of resources saving time and arming your team with the intelligence • Comprehensive reference library of you need, including:legislation, guidance, and translations • • Comprehensive reference library of Strategic global compliance tools • legislation, guidance, and translations Practical compliance resources • • Strategic global compliance tools Expert analysis, horizon-scanning • Practical compliance resources and interpretation • Expert analysis, horizon-scanning and interpretation Networking and development
Networking and Meet our influential network of industry development experts at our regular conferences, workshops and webinars, and maintain Meet our influential network of industry your professional skills through our experts at our regular conferences, training and eLearning courses. workshops and webinars, and maintain your professional skills through our training and eLearning courses. Class-leading platform Navigate content by regions, topics, sectors Class-leading platform and substance groups, save personalised content views, and create collaborative Navigate content by regions, topics, sectors groups – quick and easy access to the and substance groups, save personalised information and resources you need. content views, and create collaborative groups – quick and easy access to the information and resources you need.
Empower your business and create safer products with the new Chemical Watch Empower your business and create safer products with the new Chemical Watch Visit our new website to find out more: chemicalwatch.com Visit our new website to find out more:
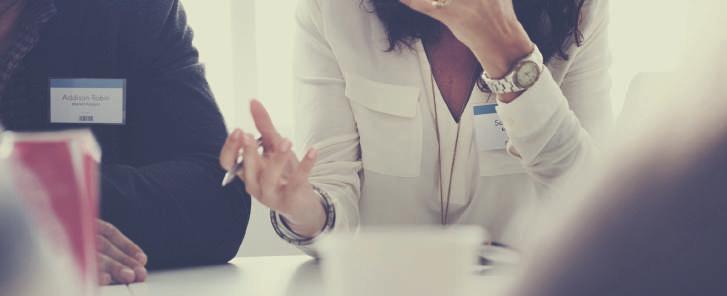