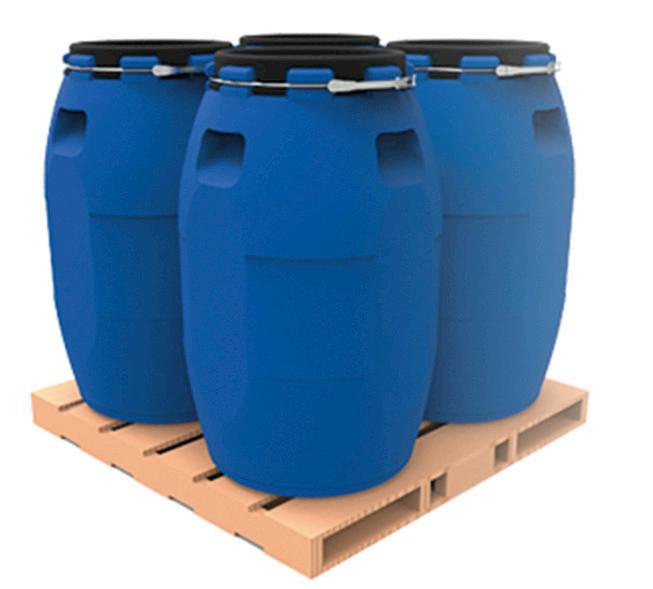
2 minute read
Greif introduces new concepts
BRIGHT IDEAS
PRODUCT DEVELOPMENT • AS BEFITS ITS POSITION AS ONE OF THE LEADING INDUSTRIAL PACKAGING MANUFACTURERS, GREIF HAS RECENTLY COME UP WITH SOME INTERESTING NEW IDEAS
WITH ITS 254 production sites in 41 countries and a workforce of some 16,000 employees, Greif is without doubt a major force in industrial packaging. But that does not divert its attention from the need to look after its customers and a number of recent product innovations have come in response to that need.
In Latin America, an existing customer came to Greif with a specific requirement for a large open-head drum with a reduced weight but the same performance and quality. The Greif LATAM team modified an existing drum mould to deliver those requirements and, along the way, came up with a unique geometric design that weighs 14 per cent less than a standard drum
Part of the design (below) was to include four exterior moulded handles, recessed into the body of the drum, for easier handling, and a faceted shape that optimises pallet utilisation.
Another project, designed to improve the sustainability of steel drums in remote locations, involves the provision of semi-
GREIF MUST CONSTANTLY UPDATE ITS DESIGNS finished drum parts that can be shipped from production facilities and assembled locally with minimum equipment. These ‘Knock Down Drums’ (KDD) (below right) can thus be transported more efficiently, with a single 20-foot container able to accommodate up to 1,176 of the 210-litre drums, either tight- or open-head, as opposed to 80 fully finished drums.
The drums come in three parts, ready welded, painted and nested. The user only needs to assemble the drum and test the seams with basic machines. Greif is currently manufacturing KDD units in Costa Rica, Portugal and South Africa.
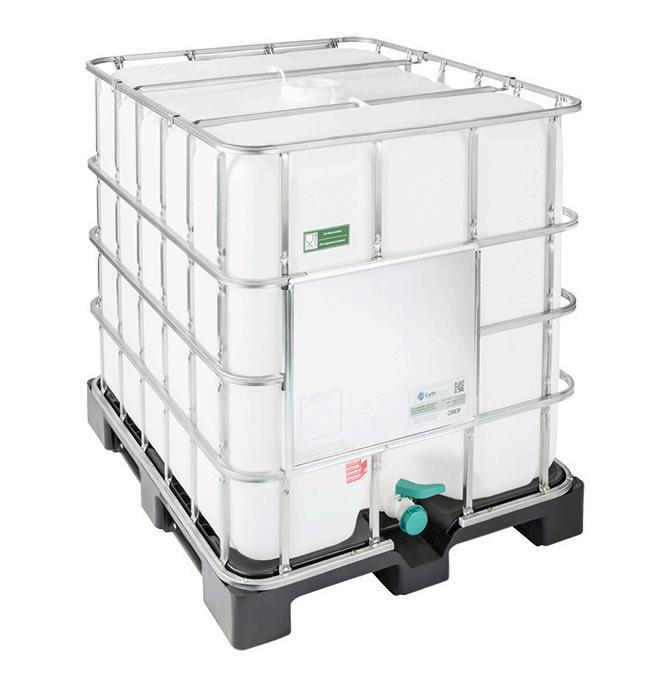
THE IBC FOR FOOD Further product development has come in the intermediate bulk container (IBC) segment, where Greif is expanding production of its GCUBE Food IBC (above). It is currently adding a third manufacturing site in the US, at Baytown, Texas, which, like the existing plants in Alsip, Illinois and Lavonia, Georgia will be certified according to the Global Food Safety Initiative (GFSI), giving strong assurance of operational integrity to Greif’s customers in the food industry.
At its IBC accessories site in Bottanuco, Italy, Greif has invested in a high-care production department, featuring a blue resin floor that clearly shows the cleanliness of operations. Wooden pallets have been eliminated from the operational areas, removing the risk of potential contamination.
Greif has also improved the IBC accessories used with the GCUBE Food unit, including an over-coated HDPE disc and an aluminium foil seal for the butterfly valve. These remove the risk of product counterfeiting and offer improve product protection.
“All of these recent developments and investments demonstrate Greif’s commitment to delivering the highest level of cleanliness and food safety standards to its customers,” says Kevin Kling, North America IBC and plastic product manager for Greif. “Customers can be assured that the supply chain for the full GCUBE Food portfolio is produced in highly controlled, safe facilities using the latest technologies and fully automated production and assembly lines.”
Luca Bettoni, Kling’s EMEA counterpart, adds: “Importantly, investment in food safety at Greif is not limited to IBC production alone. We have proactively worked closely with our customers in the food industry to ensure that we take appropriate measures to prevent product contamination throughout the entire supply chain.” www.greif.com
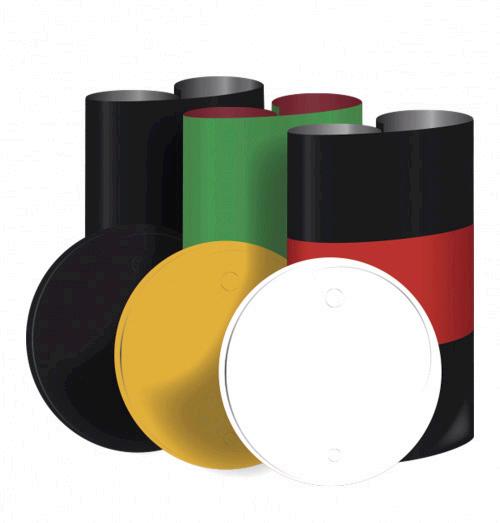