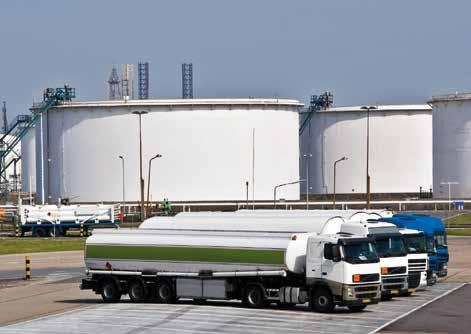
2 minute read
Understanding diesel runaway
CLOSE ENCOUNTERS
RUNAWAY • UNDERSTANDING THE MECHANISM BEHIND DIESEL ENGINE RUNAWAY IS THE FIRST STEP IN PREVENTING IT. AMOT EXPLAINS HOW ITS EXPERIENCE CAN HELP INDUSTRY AVERT DISASTERS
PETROLEUM PRODUCTS PLAY a vital role in our day-to-day life and confidence in the safety of the industry’s operations is paramount. Diesel engine runaway is an unexpected danger for bulk liquids storage operations at Control of Major Accident Hazards (COMAH) sites, and has led to fatal accidents for companies involved in storing crude oil, petroleum and refined products.
‘Runaway’ is a dangerous phenomenon where the running diesel engine draws extra energy from low concentrations of any hydrocarbons in the surrounding air. This causes uncontrolled overspeed beyond the safe design limits and an explosion or ignition of the external air/fuel mixture.
Drawing in the surrounding combustible mixture and using this energy as fuel is both unstable and uncontrollable. The engine’s control system attempts to limit the diesel injection to keep the engine under control but, as more vapours are ingested, the speed will increase beyond the normal limits This can cause the internal valves to bounce, exposing the combustion to the manifolds and the flames will pass out, meeting the flammable vapours being drawn in.
RAISING THE BAR Recent tests by the International Electrotechnical Commission (IEC) have shown that a diesel engine can start to run away within three to nine seconds of a gas being drawn in, at a concentration as low as 22 per cent Lower Explosive Limit (LEL). Once this begins, turning off the ignition key will not stop a diesel engine. There is very little margin for error if engine shutdown is dependent on human intervention. The only proven, reliable method to stop the engine running away beyond a safe limit is to install an emergency shutoff valve in the engine’s air intake system. Blocking the engine’s air intake effectively cuts off the external fuel source and air supply, so the engine quickly stops and the ignition source is removed.
Few industries are more hazardous or more safety-conscious than oil and gas and understanding the lessons learnt from the Texas City refinery and Buncefield fuel depot explosions is useful for addressing this safety issue. The key recommendation is to ensure that these risks are understood by all employees and that this message is reinforced. As regulations change and new standards and guidance are developed, consideration should be given to periodic updates to maintain operator awareness.
Areas designated for no ignition sources are places where diesel engines must have appropriate upgrades to mitigate their potential for ignition. All employees should be educated about the risks and a risk assessment should be performed. An inspection and maintenance schedule should be implemented to ensure the overspeed systems are functional and fit for purpose. An air shut-off valve is not a ‘fit and forget’ device and a visual inspection may not be sufficient to ensure valve function. The selected air shut-off valves must be engineered to withstand the harsh site conditions, extreme temperatures and high vibrations of the engine.
For more than 25 years, AMOT has been promoting safety by raising awareness of the explosive risks from runaway diesel engines and educating industry professionals of ways to better protect equipment and employees. AMOT offers on-site training, consultations and public presentations to operators and managers and safety specialists to educate on best practices adopted within the global oil and gas industry. HCB www.chalwyn.com
TERMINAL OPERATORS NEED TO BE AWARE OF