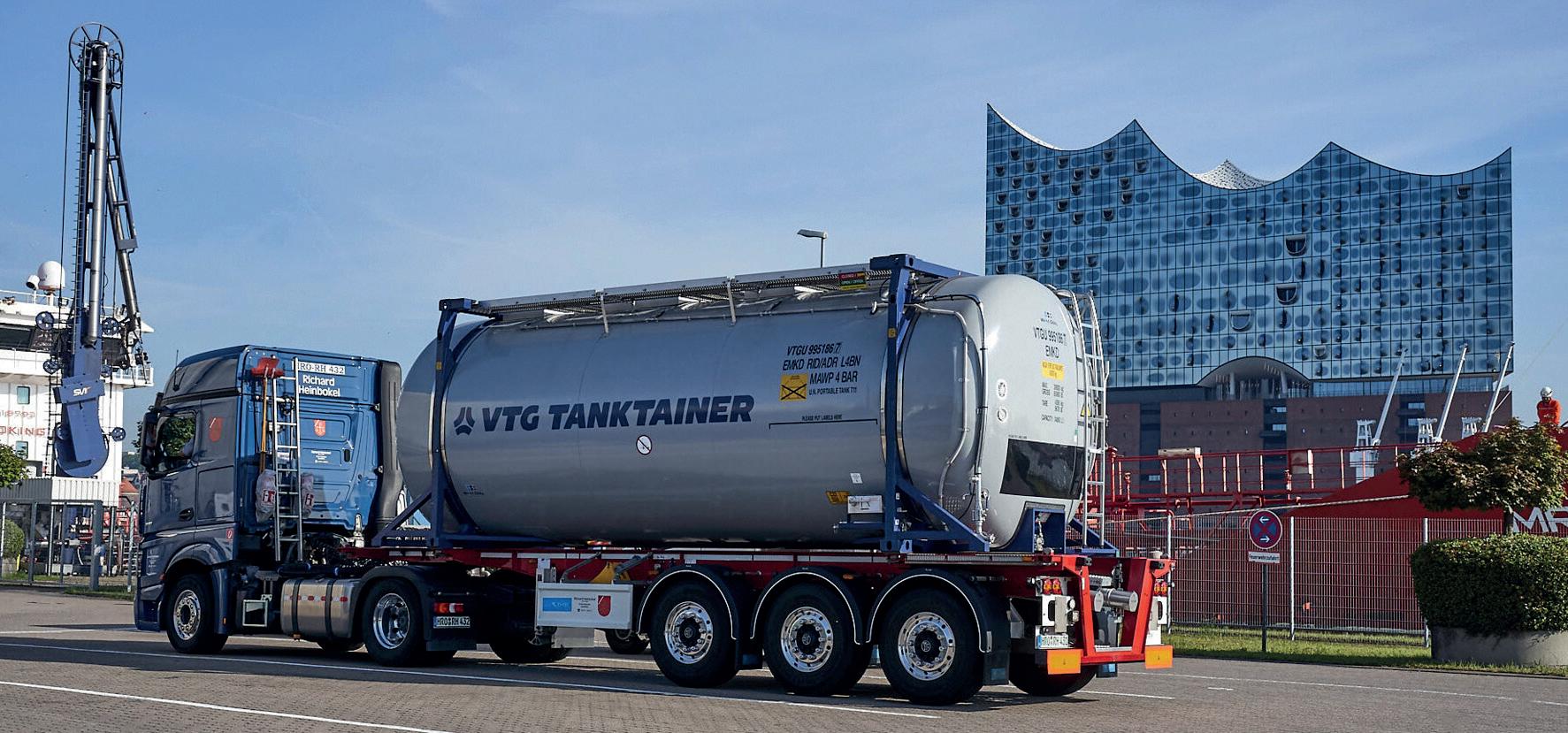
9 minute read
Nexxiot promotes standardisation
SHARING IS CARING
TRANSPARENCY • STANDARDISATION IN THE DIGITAL SUPPLY CHAIN IS ONE OF THE MOST PRESSING MATTERS, ACCORDING TO NEXXIOT. EFFORTS ARE NOW UNDER WAY TO FIND A SOLUTION
Nexxiot, a specialist in the digitisation of supply chains, became a full member of the International Tank Container Organisation (ITCO) in October 2019 and is aiming to help instigate industry-wide standardisation for digitised solutions.
Since joining ITCO, Nexxiot has launched working groups aimed at collaborating closely with tank container operators to radically improve the industry. Furthermore, Nexxiot announced it will be responsible for the digitisation of roughly 9,000 tank containers in long-time collaborator VTG’s tank fleet.
“It was our idea to start such a working group,” says Tim Thiemann, segment head tank containers at Nexxiot. “It happened during the recent ITCO event [in Amsterdam in October 2019] and we asked the other participants who would be interested in joining this work group to create these standards. We were previously a member of this kind of group in the rail sector where it also started to develop a focus on standardisation. We made good results in this work group and agreed on different standards that we believed would not only be important for the rail sector, but also for the tank container sector.”
JOIN THE CLUB There is no doubt that the rapid progress being made with digital solutions has been incredible. It has flooded the industry and has become the driving force of future developments, yet selecting the correct product can often be technical and confusing, which is why Nexxiot aims to work with ITCO members to home in on what users desire and require.
“ITCO is the most important group for the tank container business and we are very specialised in this segment,” says Thiemann. “We think that we could both benefit through cooperation, which is why we asked for membership. I see our role as a support for the tank container industry - to support them with the opportunities available with different kinds of digitisation and what kind of possibilities are available with the data being generated.”
Thiemann continues: “Digitisation is not only industry’s current buzz-word, but it will also be the basis for business in the future. For this, we have launched a working group inside ITCO for standardisation. When we spoke to our customers, it was clear there was confusion surrounding what device or what kind of system would be the best for them. We often got requests concerning different devices, sensors and platforms and, since we believe that an open system could be a big benefit for all and we want to avoid developing an ‘Apple’ world [where one system is incompatible with the others], we launched this work group together with other companies, operators and lessors in ITCO – to go forward with standardisation in this special topic.” SEEING CLEARLY Thiemann believes that the biggest change in recent years – thanks to the growth of digitisation and inter-operator communication – has been transparency between businesses. This has opened the doors to a seismic shift in the way business is conducted and has changed how potential collaborators view working with each other.
“Regarding transparency, in the last couple of years the data sharing methods between different companies have changed. Everyone wanted to keep their data secret, but there has been a change of mind across the whole industry to fulfil the goals of sustainability. Better cooperation has to be the target for the next few years and transparency is very important to this. It won’t be 100 per cent transparent, but it will be much more than what has been available the last few years.”
However, there are some issues that need addressing. Most notable is the problem of agreeing on standardisation between different digital solution providers. It is great to have the ability to monitor a dozen different factors of a shipment through the use of sensors and predictive technologies, but if the different solutions are not able to communicate with each other through a common language and practical platform, it will not be utilised by potential users.
Thiemann explains: “I think the biggest hurdle will be to find a common ground in standardisation, not only within members of ITCO, but with other digitisation companies also.”
In-depth discussions with Container Owners Association (COA), where Nexxiot is also working on standardisation, to form a universal system of standards for hazardous and non-hazardous goods are currently underway and the results of the working group are due to be released in the next few weeks. www.nexxiot.com

NEXXIOT’S TIM THIEMANN SAYS INCREASED
TRANSPARENCY BETWEEN BUSINESSES IS
CHANGING HOW THEY WORK TOGETHER
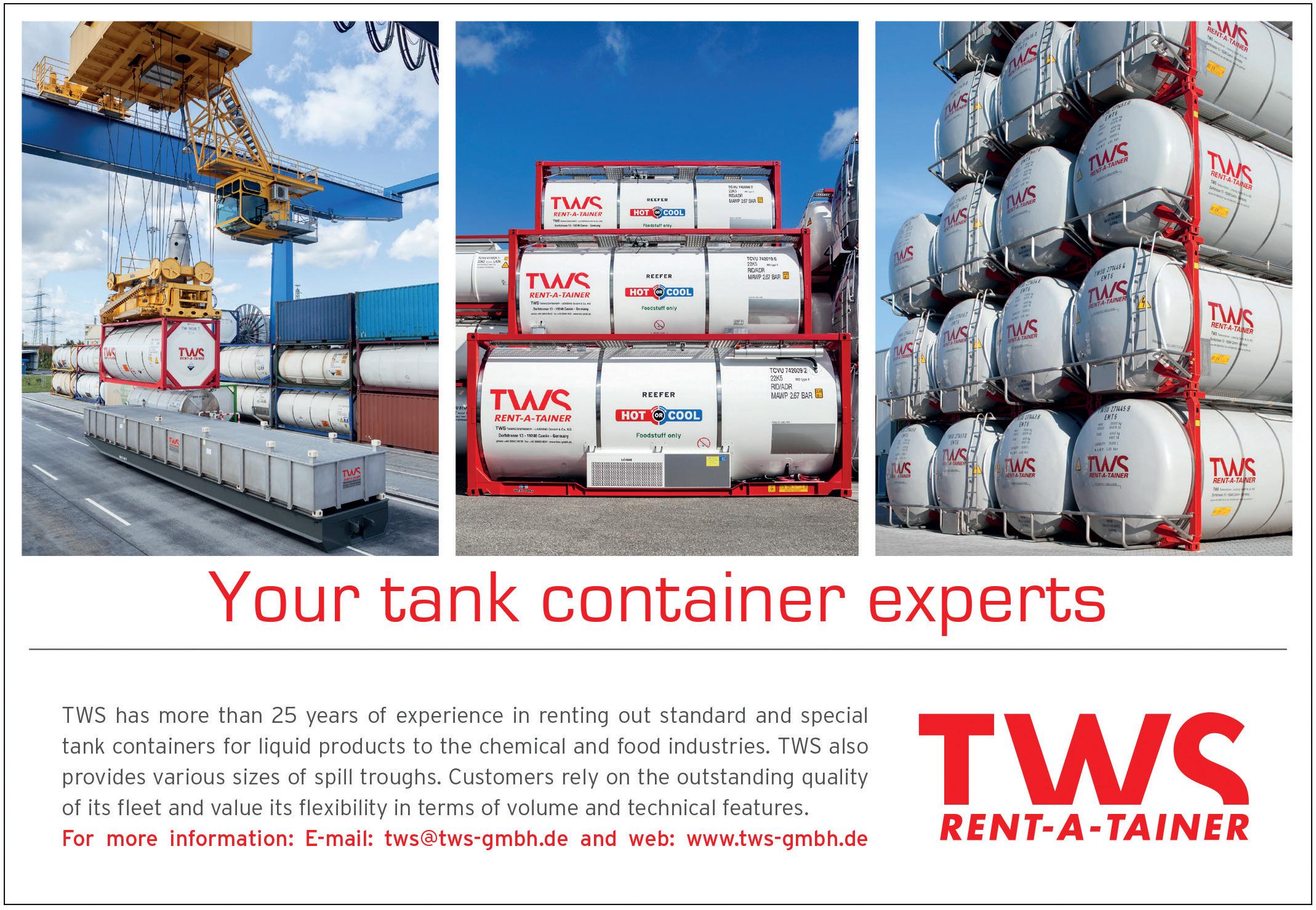
PRODUCING SOLUTIONS
TRACKING • MONITORING SHIPMENTS AND COLLECTING DATA WILL BECOME EVEN EASIER AS INNOVATOR PACKWISE TEAMS WITH DIEHL FOR PRODUCTION ON A LARGE SCALE
IN NOVEMBER 2019 digital start-up Packwise signed a contract with Diehl Connectivity Solutions (DCS) to put the Packwise Smart Cap into series production. Readers of HCB may remember the introduction to Packwise’s plug-and-play Internet of Things (IoT) device, Smart Cap, last year (HCB October 2019, page 97) and how the pilot testing of the new device is already showing good results. From April 2020, the first set of Smart Caps will be coming off the production line and being shipped to businesses.
Being able to accurately keep track of thousands of intermediate bulk containers (IBCs) and other packagings is essential if operators are to reduce waste, improve efficiency and provide the highest level of service to customers. Applying the Smart Cap technology, containers can be easily connected to a network that follows every movement and can keep track of the level of product inside each container. The open software solution visualises and automates processes for various applications in the supply chain. It warns of deviations from parameters and provides recommendations for action should the situation arise.
“We know the industry and want to use our innovations to solve current problems and create new opportunities for our customers,” says Packwise managing director Gesche Weger. As Smart Cap leaves the prototype stage and enters full production, the results of various trials have shown highly accurate measurements across all mediums, and success in accurate filling level measurements in silo tanks up to 8 m; new software features have been developed and amended accordingly and, perhaps most importantly, product market fit has been confirmed.
MAKING FRIENDS The innovative creation and far-reaching benefits of the Smart Cap technology were noticed quickly by DCS, which offered to take the product from prototype to reality. DCS is a system integrator for the Industrial IoT and belongs to the Diehl Group, headquartered in Nürnberg, Germany. As a partner for digital business models, DCS industrialises an integrated IoT infrastructure from sensor to cloud for its customers on an international scale.
“Together with Packwise, we are developing a pioneering digital business model in logistics that combines ecological management with tangible cost advantages,” says Horst Leonberger, managing director of DCS.
Joining with DCS provided Packwise with a great portfolio of expertise to consult, leading to further developments with the Smart Cap. The main feature to have been added since its inception is the ability to accurately monitor filling levels through a range of containers, including double-walled containers. This means pay-per-use or payment according to actual consumption is now possible.
“We are pleased to now have DCS as a partner on our side at eye level for the industrialisation of the Packwise Smart Cap,” says Gesche. “This is readily scalable. We can easily produce several hundred thousand units per year if necessary,” adds Felix Weger, product development at Packwise.
TRIED AND TESTED There have been a number of pilot studies in recent months involving the Smart Cap by several different members of the chemical industry that are using different types of container and seeking to achieve different goals. •Company A, a user of combination IBCs, wanted to increase its level of customer service. Using the Smart Cap led to improvements in restock times, created a new touchpoint with the customer and provided a higher level of data for the customer •Company B, a user of a range of full plastic IBCs, aimed to improve turnaround time and utilisation but also experienced improvements preventing theft and loss of the IBCs •Company C, a user of steel IBCs, improved risk management with the Smart Cap by tracking shelf lives and temperatures, as well as being able to monitor unauthorised refilling and contamination.
“We haven’t found any product we can’t measure – from liquid PVC, acids, mineral oils and more,” says Felix Weger. “We can track everything we have encountered and have tested across many sectors of the industry with large chemical distributors.”
There have been many other examples of businesses using Smart Cap to enhance a wide set of factors in the supply chain, from locating containers across borders to ensuring empty container pickups are arranged as efficiently as possible.
One of the concerns with digital sensors is longevity. Based on a daily transmission interval, Packwise is able to guarantee a battery life of five years for the Smart Cap. Additionally, should the container being monitored become damaged or need to be taken out of service, the Smart Cap can be easily removed and attached to a new container allowing for multiple reuse.
CONTINUED DEVELOPMENT Looking forward to the rest of 2020 and beyond the initial production of the Smart Cap, Felix Weger explains: “We are aiming to find as many uses [for Smart Cap] as possible and become as visual and loud as possible to show people our solution. Now, it’s about ‘how deep can we integrate into the ERP systems of our customers?’ Our data are very interesting, but standalone they are not as valuable as they could be when enriched with the data stored in an ERP system. We can use the Smart Cap as a catalyst for existing data to create more insights.”
Packwise has designed its software to be as useful as possible for any form of existing software that may be installed by a diverse range of businesses. In the Packwise web application, Packwise Flow, customers can visualise container data, analyse KPIs via a customised dashboard and create calls for action.
DCS is a trusted partner for Packwise for secure data transmission with end-to-end encryption. “We are service providers and bring data securely, standardised and wirelessly into the IT systems of customers like Packwise, where they are analysed and evaluated in the customer’s jurisdiction.” adds Nikolaus Haas, director sales and customer solutions at DCS.
For readers wanting to experience the Smart Cap first hand and receive a more in-depth understanding of the range of possibilities available, Packwise will be presenting the concept at this year’s LogiMat show in Stuttgart, Germany on 10 to 12 March; visitors can find them in Hall 7, Stand C16. packwise.de
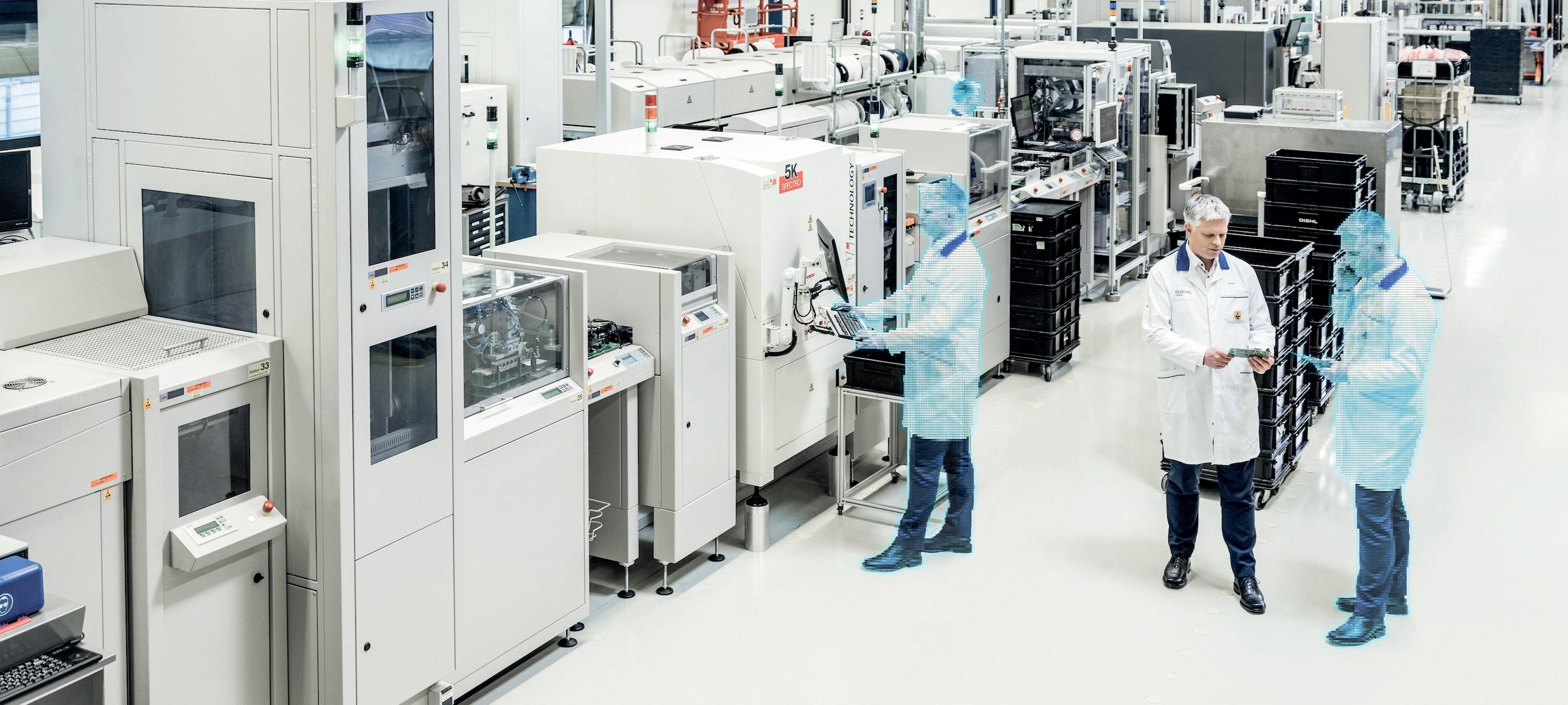
BRINGING TOGETHER THE EXPERTISE OF TWO
COMPANIES WILL HELP ACCELERATE DEVELOPMENT
AND PRODUCTION OF THE SMART CAP AND ITS
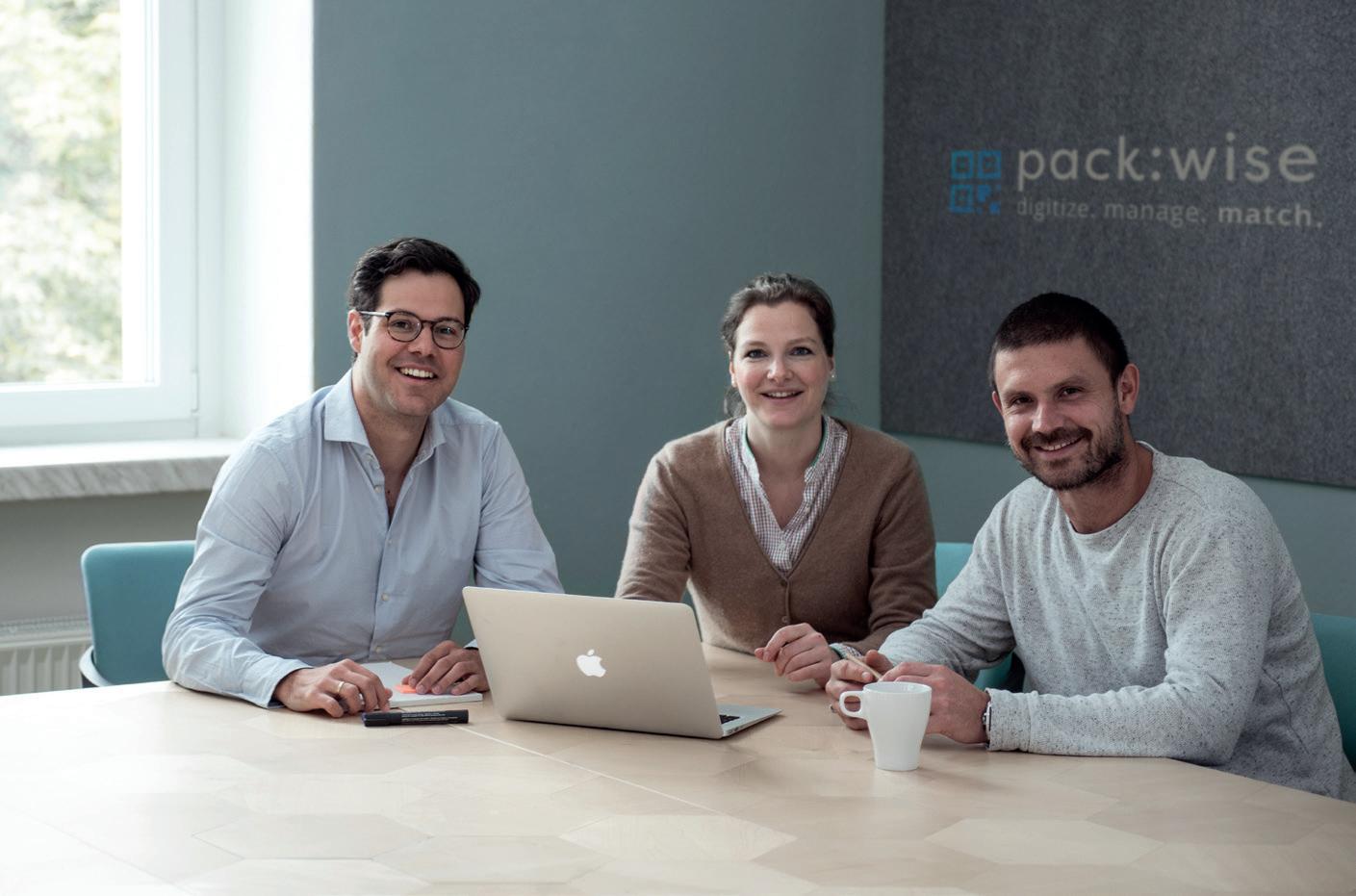