
4 minute read
Labeline ensures compliant labelling
STICKER ALBUM
LABELLING • HAZARD LABELS AND PLACARDS MAY BE THE CHEAPEST ELEMENT OF A SHIPMENT BUT CAN ALSO BE THE MOST COSTLY, WARNS LABELINE INTERNATIONAL’S RICHARD SHREEVE
HAZARD LABELS, PLACARDS and handling marks are designed to minimise the risk posed by dangerous goods. They give information about the products to those who are handling and transporting them and, should an incident occur, help emergency responders to rapidly determine the best corrective action to take.
It is logical, therefore, that there are standard parameters for the specification, quality and properties of labels and marks included in the dangerous goods regulations for each mode of transport, namely ADR (road), RID (rail), IATA DGR/ICAO TI (air) and the IMDG Code (sea).
For example, both ADR and RID state at 5.2.2.1.7: “All labels shall be able to withstand open weather exposure without a substantial reduction in effectiveness”. Similar text applies in ADR, RID and IATA DGR for identifications marks, such as OVERPACK, SALVAGE, address labels, UN number, Proper Shipping Name and so on.
In 5.3.2.2.1, ADR and RID also specify the required properties of vehicle placards: “The material used shall be weather-resistant and ensure durable marking.” The International Air Transport Association’s (IATA) Dangerous Goods Regulations (DGR) state in 7.2.2.1: “The material of every label, the printing and any adhesive thereon, must be sufficiently durable to withstand normal transport conditions including open weather exposure without a substantial reduction in effectiveness.”
Perhaps understandably, the International Maritime Dangerous Goods (IMDG) Code is even more demanding, stating in 5.2.2.1.7: “The method of affixing the label(s) or applying stencil(s) of label(s) on packages containing dangerous goods shall be such that the label(s) or stencil(s) will still be identifiable on packages surviving at least 3 months’ immersion in the sea. In considering suitable labelling methods, account shall be taken of the durability of the packaging materials used and the surface of the package.”
This requirement to withstand three months in the sea is repeated in the IMDG Code to cover marks on packaged goods (5.2.1.2.2) as well as placards and marks on cargo transport units (5.3.1.1.1.2 and elsewhere).
BUY THE BEST One way in which users can ensure that their labels and marks are likely to comply with the above requirements is to make sure that they are certified to BS5609. This is a globally recognised specification to test printed pressure-sensitive, adhesive-coated labels for their adhesive properties and resistance to abrasion and sunlight. Labels are tested offshore, normally by applying them to aluminium plates that are then submerged and left to the elements for three months. Of course, to get the maximum adhesion, it is important that labels are applied to a clean, dry and suitable substrate.
Labeline’s new purpose-built offices overlook the banks of the Tor-Torridge estuary and its location gives the company’s founder and managing director, Keith Kingham, the opportunity to test labels on a variety of substrates in challenging conditions. The articles are hung into the estuary where they are dragged through the sand by strong tidal salt-water currents and exposed to all weathers.
AVOIDING SNAGS Damaged or incorrect labelling is a common and frequent cause for snagging consignments of dangerous goods. Usually, the biggest impact of a consignment being held is the delay to the customer and the consequential commercial implications. There is also the additional cost and inconvenience of having to rectify the problem. Some forwarders will replace incorrect or damaged labels on behalf of
their clients but they will usually charge a significant price for this service.
It is apparent that some generic label suppliers are offering hazard labels that are not compliant - even when the supplier has claimed BS5609, so it’s worth users doing their own tests.
A quick trawl through the dangerous goods enforcement pages that are publicly available on the UK Health & Safety Executive’s (HSE) website will show that Prohibition Notices are often issued for incorrect, illegible (dirty) or missing placards on vehicles carrying dangerous goods. Furthermore, a non-compliant label is good reason for enforcement officers to take a closer look at all aspects of a shipment or the vehicle carrying it.
Fines and penalties can be quite severe and vary from country to country. Here are some examples of the baseline fines that enforcement officers use for guidance in the US: - Using an incorrect hazard class/ identification number: up to $6,000 - Failure to mark a package containing
liquid hazardous materials with required orientation marking: $2,500 - Failure to label a package (or if the label has come off): $5,000 - Failure to place a required subsidiary label on a package: $500-$2,500 - Placing a label on a different surface of the package than, or away from, the proper shipping name: $800 - Placing an improper size label on a package: $800 - Placing a label on a package that does not meet colour specification requirements (depending on the variance): $600-$2,500 - Failure to provide and appropriate class or division number on a label: $2,500. It is essential that consignors of dangerous goods use compliant labelling that can withstand the rigours of distribution, storage, handling and product usage. After all, the person signing a Dangerous Goods Note is declaring that the contents of a consignment are “…marked and labelled/ placarded and are in all respects in proper condition for transport according to the applicable regulations”.
Purchasing from a label supplier that is up to date with the regulations gives the reassurance that this requirement is met. Good quality labels also reflect well on the consignor. www.labeline.com
BELOW: AFTER SEVEN MONTHS IN THE ESTUARY
OUTSIDE LABELINE’S OFFICE, ITS LABELS REMAIN
ADHERED AND LEGIBLE
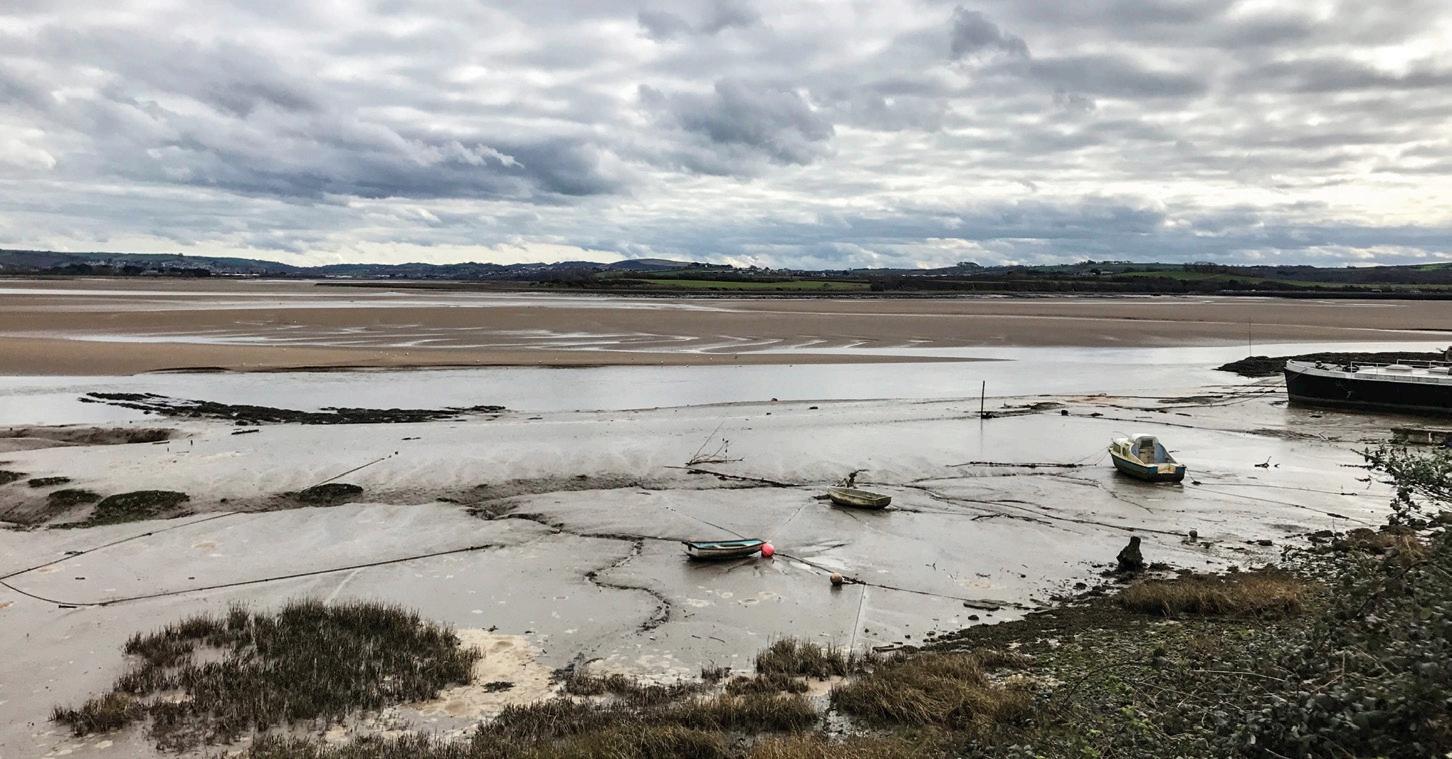
