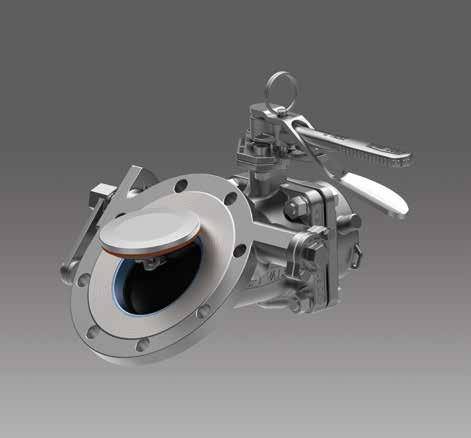
2 minute read
Fort Vale protects against corrosion
THE ACID TEST
CORROSION • FORT VALE IS TAKING A PROACTIVE STANCE ON THE THREAT OF CORROSION IN TANK CONTAINER EQUIPMENT, ADDING GREATER PROTECTION AGAINST AGGRESSIVE LADINGS
TANK CONTAINERS ARE built to last; their shells are almost always made of stainless steel, as are their main appurtenances, including their valves. That makes them impervious to attack by almost all commonly carried chemicals, even those that are highly corrosive.
But they are not totally immune to corrosion. The industry is becoming increasingly aware of issues of pitting corrosion, sometimes resulting from
FORT VALE WILL BE OFFERING EXTRA CORROSION improper classification or mis-declaration of the product being shipped.
During its members’ meeting in Antwerp in September 2018, the International Tank Container Organisation (ITCO) heard a presentation by specialists from Brookes Bell, a technical consultancy with experience in corrosion problems in stainless steel. They explained how the chromium that is added to steel to make it ‘stainless’ forms a passive layer on the steel, protecting it from attack. That passive layer can be damaged, notably by exposure to aggressive halide ions. Once the passive layer is damaged, the underlying steel can suffer pitting corrosion.
The ability of stainless steels to withstand pitting corrosion is indicated by its Pitting Resistance Equivalent Number (PREN), calculated according to the proportions of chromium, molybdenum and nitrogen within the steel. For instance, 304L-grade stainless steel has a PREN of 18, and 316L-grade a PREN of around 25. Stainless steels that are constantly exposed to seawater require a PREN of at least 40 to be fully protected.
PROTECT YOUR VALVES Fort Vale Engineering, one of the leading suppliers of footvalves, manlids, couplings and other fittings for tank containers, is taking the issue seriously. It has traditionally used 316-grade stainless steel but for the past two years has been looking at ways to improve corrosion protection for its equipment.
This has led to the development of a new welded coating for its Superseat tank container valves. Fort Vale had looked at using Hastelloy C276, a ‘super-alloy’ with high levels of nickel and the addition of tungsten, which achieves a PREN of 45, but this is very expensive.
Instead, Fort Vale has opted to apply a weld overlay of Inconel 625, a nickel-based super-alloy that has long been valued for its high strength, excellent performance in elevated temperature applications, and good corrosion resistance in highly acidic environments. It has a PREN of 41, offering protection against products such as hydrochloric acid and hydrofluoric acid that can attack the passive layer of more common grades of stainless steel.
Graham Blanchard, recently appointed as European sales director at Fort Vale, explains that this Inconel overlay is being rolled out across the company’s range of tank container bottom discharge footvalves and Cleanflow valves and will be supplied as standard, without additional cost to users.
Fort Vale will be explaining the advantages of its new corrosion protection approach at a number of major trade shows during the course of 2019; these include Transport Logistic in Munich in June, Intermodal Europe in Hamburg in November, and the Tank-ex show in the UK at the end of May. HCB www.fortvale.com