
5 minute read
Matlack looks at pre-loading
BE PREPARED
DRIVERS • TACKLING THE WIDESPREAD DRIVER SHORTAGE IS NO EASY TASK BUT, AS MATLACK LEASING SAYS, THERE ARE SEVERAL THINGS OPERATORS AND SHIPPERS CAN DO TO HELP
THAT THERE IS a shortage of heavy goods vehicle drivers in the mature markets of North America and Europe is not news: the problem has been around for several years now, but that situation is becoming more acute, if not critical. An ageing pool of existing drivers, a profession that does not appear to appeal to the young, and competition from locally based home delivery services have all contributed to a position where the demand for freight transportation is beginning to outstrip the availability of drivers to satisfy it.
In the face of a lack of effective action by governments, haulage companies have been taking the initiative, offering steadily increasing wage rates and investing in cleaner and more comfortable cabs for their drivers. But still the number of active drivers declines. At Matlack Leasing puts it: “Regulatory requirements, safety concerns, lifestyle choices including time away from family, compensation and other factors make recruitment of drivers difficult.”
Matlack also notes that the driver shortage is particularly severe in the tank truck sector, especially in the transport of chemicals, where there are more stringent requirements for driver experience and safety. “The impacts associated with a shortage of drivers will increase as the country re-opens and industrial production and the economy rebound,” the company says.
While new technologies are in development and some regulatory action is likely, in the near term there is an immediate need to increase the time drivers spend on the road. That will be fine for drivers: they want to drive, not hang around waiting. IDLE TIME Under the Federal Motor Carriers Safety Administration (FMCSA) Hours of Service (HOS) regulations, commercial drivers are permitted to work for 11 hours per day; however, Matlack notes, research by MIT Freight Lab published in May 2020 indicates that they spend on average only seven hours a day on the move. “Clearly there is room for improving efficiency and miles travelled,” Matlack says. “The time drivers spend loading and unloading in depots, terminals and manufacturing facilities, as well as time spent on breakdowns and equipment repairs contribute to delivery delays and increase the cost of goods.”
During times of shortage, whatever the asset being considered, it makes sense to get more out of the available assets – and that includes drivers. Reducing gate-in to gate-out times is an obvious target but, at present, there are many barriers to improving driver efficiency as they are dependent on a range of external parties, not least when operating as part of port logistics. While some factors affecting efficiency are not within the control of the operator or the port – inclement weather, road construction activity and, to an extent, traffic congestion – others can be
addressed. Congestion within the port area itself, delays to cargo arrivals, maintenance and product sampling can all be eased, if only by providing better and more timely information to the carrier.
“Truck turnaround times may be improved by investing in pre-loading, automation, timely maintenance and technology,” Matlack says. These strategies can add value in the supply chain by increasing the time drivers spend driving.
GET READY One area that has been considered in Europe, without much success as yet, is the idea of pre-loading trailers. This can have a significant impact on truck turnaround times, with benefits for cargo owners, logistics companies and the terminal facilities themselves. At some facilities, pre-loading is already in place: the tank trailer, tank container or other container is loaded before the driver arrives on site so that the driver merely has to attach the trailer or chassis to the tractor unit and can depart promptly. Matlack notes that this will require the shipper or – more likely – carrier to invest in enough complementary equipment so that one trailer can be being loaded while another is on the road.
Pre-loading can expedite the driver’s departure from the terminal, reducing time on site and improving their driving time. There are also benefits for the terminal, such as greater flexibility in terms of scheduling, something that often reduces overtime costs. It also means that truck drivers can adapt their schedules to avoid peak traffic times and get on the road faster, while shippers can offer earlier delivery time windows.
Matlack believes that pre-loading is one tool to improve driver utilisation but there are also other changes that can be made. For instance, blown tyres, mechanical breakdowns and loads that are overweight or not properly secured can all lead to delays and reduce drivers’ mileage. Companies that use younger equipment, implement timely routine maintenance and use the proper equipment for their freight experience fewer such disruptions and emergencies on the road, improving driver efficiency and driver satisfaction.
LET’S GET DIGITAL Technology also has the potential to improve driver efficiency. GPS systems aid in route planning and can guide drivers on how to avoid traffic jams. Barcodes, scanners and hand-held tablets more accurately monitor freight and streamline formerly paper transactions during cargo drop-off and loading. Routine tasks such as vehicle inspections and trip logs are completed faster with improved accuracy and consistency.
Advances in automotive technology also assist with the maintenance issues described above. Signals will alert drivers to shifting loads, low or flat tyres, and other safety concerns that could delay the driver from reaching their destination. Employing technology results in a more productive work environment, Matlack says.
Ultimately, driver efficiency and satisfaction are significant and growing concerns for chemical manufacturers, chemical distributors and other liquid bulk freight haulers. Driver compensation is based on miles travelled and it has been proven that higher levels of driver satisfaction are linked to higher compensation. That can only help in the drive to attract and retain new talent to the North American tank truck driving pool.
PRE-LOADING OFFERS AN IMMEDIATE BENEFIT TO
ALL PLAYERS IN THE LOGISTICS CHAIN BUT THERE
ARE ALSO OTHER WAYS OF GETTING BETTER USE OF This article is an edited version of a column written by Matlack Leasing’s April Uhlenburg and published this past April; Matlack Leasing, based in Bala Clwyd, Pennsylvania, is a major provider of tank trailers, tank chassis and tank containers. For more information, visit www. matlackleasing.com.
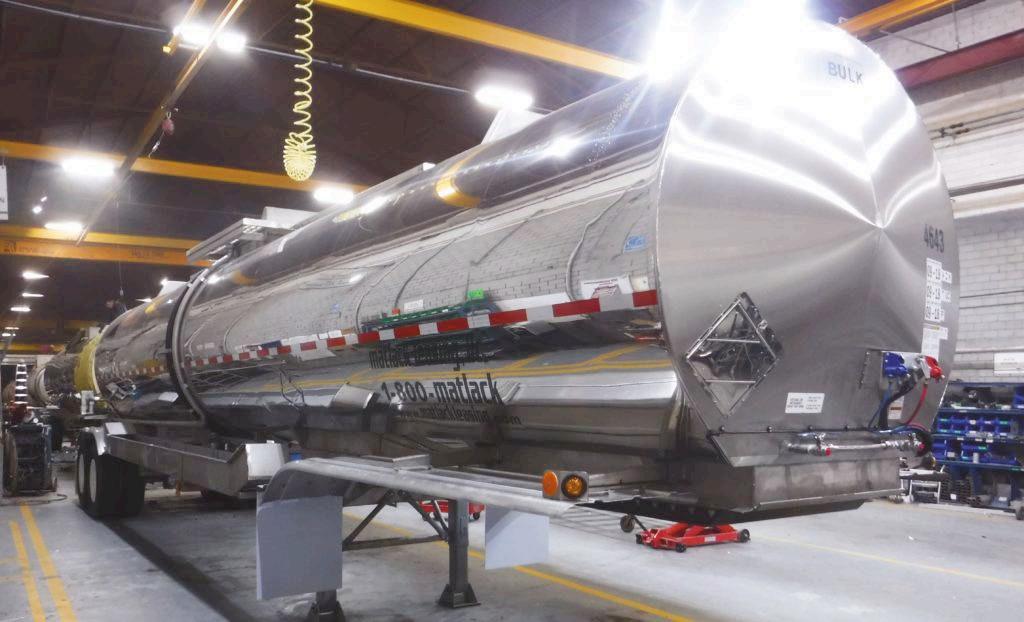
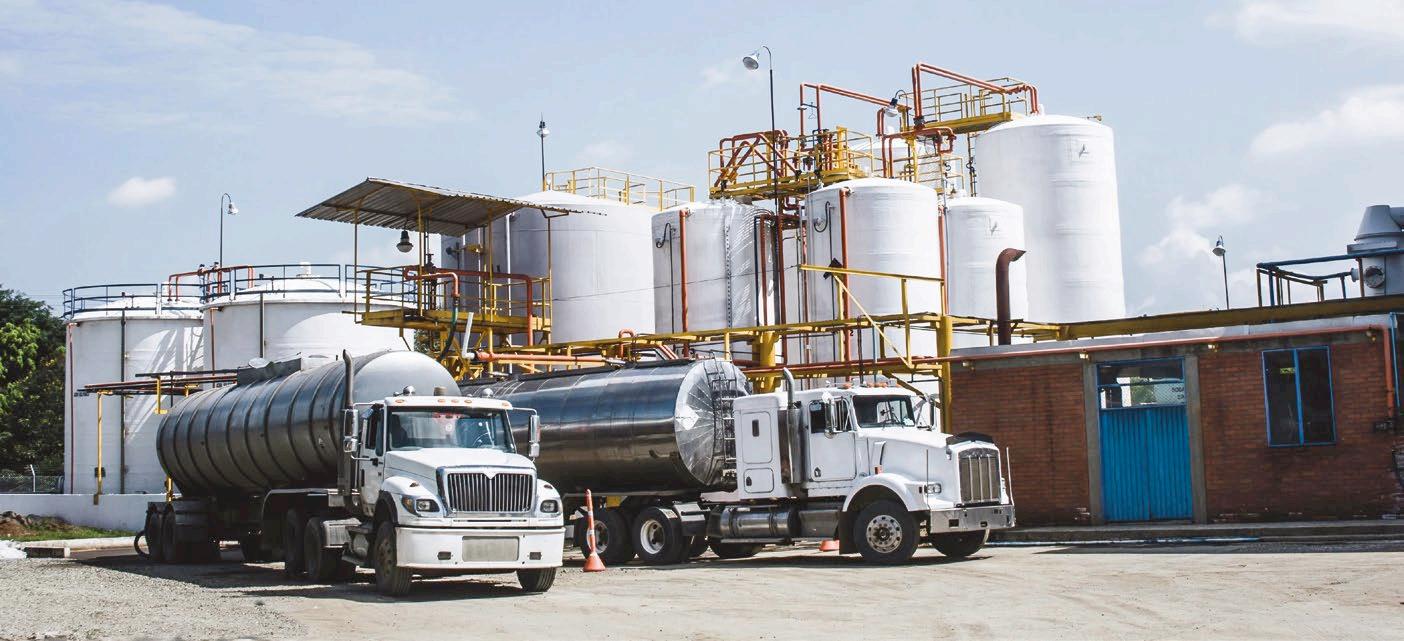