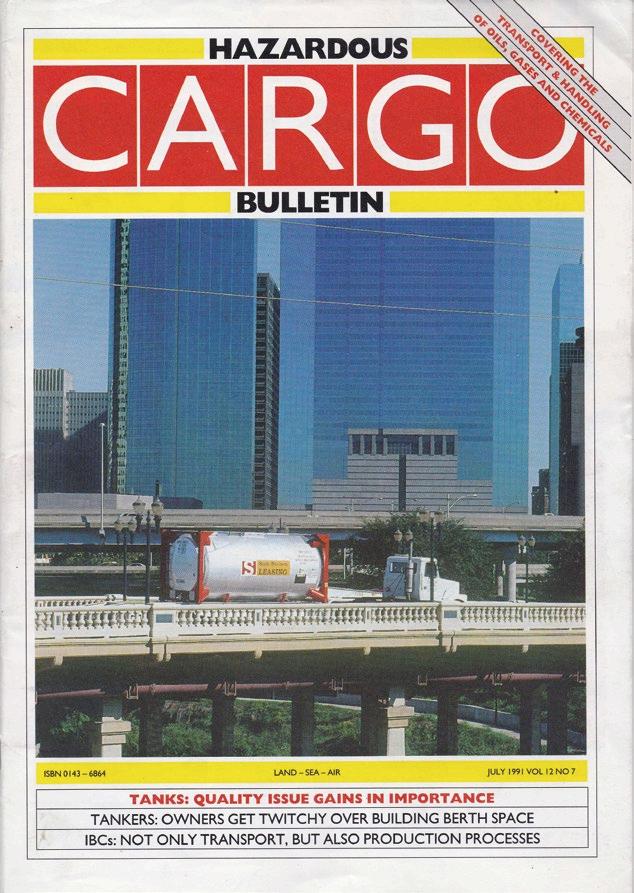
5 minute read
30 Years Ago
A LOOK BACK AT JULY 1991
The July 1991 issue of HCB had a big focus on tank containers and in particular on the inchoate market for this comparatively young concept in the US. Editor Mike Corkhill pointed out that, whereas in Europe, where the “lay of the land (and water)” offers an appealing market for intermodal tanks, the entrenched forces of the US railroads and truckers had conspired to delay the development of a domestic tank container (that is, ‘ISO tank’) sector in North America.
While some efforts had been made to expand the use of tank containers, notably by Union Pacific with its BulkTainer service, part of the problem was encouraging drayage companies to use suitable chassis, as well as the lack of dedicated regulation. However, the publication of HM-181 in December 1990, designed to bring the US Hazardous Materials Regulations closer into line with international provisions, was expected to help in that direction, while both Stolt and Hoyer had recently announced their commitment to the use of tank containers for US domestic transport(ation) and Stolt had formed an intermodal partnership with Chemical Leaman Tank Lines.
Those figures were borne out by HCB’s annual fleet review of tank container operators, with Hoyer (4,640 tanks) and Stolt (4,350) being far and away the largest in the business; only Transport Coulier, GCA Trans, Rinnen, VTG and Wim Vos – all European – having more than 1,000 tanks under their control. For the sake of comparison, in ITCO’s annual fleet survey this year, Stolt’s number was put at 40,330 and Hoyer – having been overtaken in the ranks by the now Chinese-owned NewPort Tank Container – at 35,500.
Meanwhile, concerns were growing about safety standards in US petrochemical manufacturing facilities after a series of fatal incidents, the latest – in June 1991 at the Albright & Wilson Americas plant in Charleston, South Carolina – having killed six workers and injured several more. Indeed, the New York Times reported that 79 people had died and nearly 1,000 been injured in the 12 worst chemical and refining incidents in the previous four years, prompting investigations to determine if there were any common causes.
At the time, investigation work was carried out by several different agencies, often with the results of those investigations being kept confidential over legal concerns. In 1990, the new Chemical Safety and Hazard Investigation Board (CSB) had been established following amendments to the Clean Air Act but a year later Congress had still not appointed any members of the Board nor approved any funding.
The petrochemical industry was taking its own steps, with the US Chemical Manufacturers Association (CMA) having formed a Carrier Assessment Council to develop a third-party assessment system to periodically evaluate carriers for safety fitness and regulatory compliance. This was intended to be a cost-effective means of implementing the Distribution Code under CMA’s Responsible Care programme, rather than to address the hazards so apparent in the chemical processing sector.
The move followed on from similar initiatives in Europe, where the European Council of Chemical Industry Federations (Cefic) and the European Petrochemical Association (EPCA) had recently been instrumental in setting up the International Chemical Environment (ICE) programme, which these days is in effect through the Safety and Quality Assessment for Sustainability (SQAS) and Chemical Distribution Institute (CDI) audit programmes.
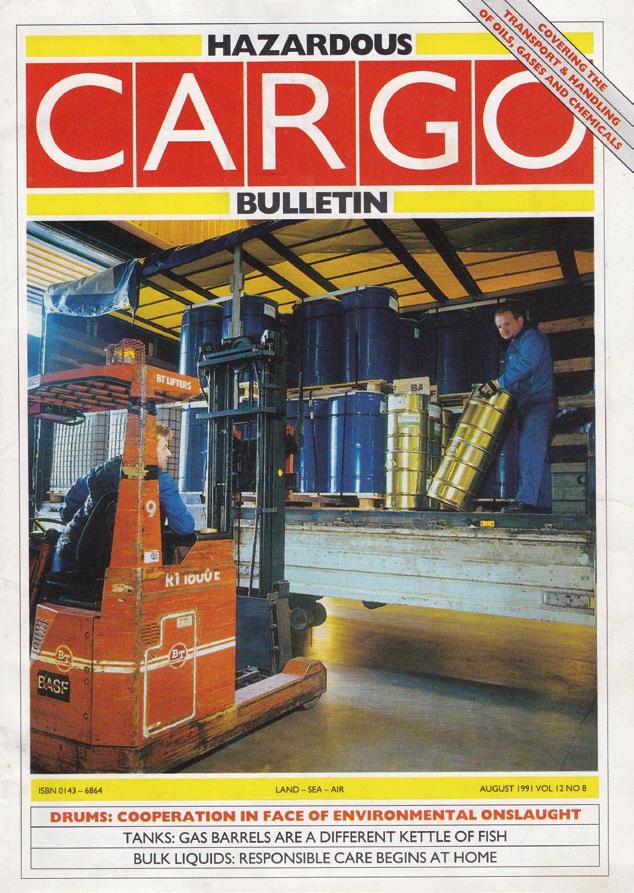
30 YEARS AGO
A LOOK BACK AT AUGUST 1991
HCB’s August 1991 issue majored on industrial packaging, prompted in no small part by the adoption of the HM-181 rulemaking in the US. This represented a massive shift in the approval of packagings used to transport hazardous materials, with a move away from the longestablished US domestic system towards the UN model of performanceoriented packagings.
But it was not to be a swift or smooth changeover. Our issue helpfully provided a digest of the important dates along the way, from publication of the final rule on 21 December 1990 to the effective date for HM-181 of 1 October 1991 and on through various deadlines to the end of the transition period five years later.
And that was far from the end of it. In our report from the eighth International Conference on Steel Drums, which had taken place in Toronto in June 1991, we reported on the decline in the market share of steel drums in the US, in the face of increasing environmental pressures (and the consequent higher cost of compliance for informal recyclers), the difficulty in disposing of contaminated steel, and the generally bad image of the steel drum, often associated in the public mind with a broader toxic waste problem.
Elsewhere in the August 1991 issue, John Pullen of Blagden Packaging looked at the new delayed drop test requirement for openhead drums used to transport viscous liquids – typically paint and related materials. In this test, drums are filled with water and held for some time before the test; this can result in the head gasket swelling with absorbed water. In the UK, such drums were expected to be able to pass the test after standing for up to three weeks, while in the Netherlands the period was only 24 hours. While John supported the UK position – Blagden’s open-head drums having successfully passed the test – he urged an international level playing field to avoid UK manufacturers losing market share to what could be deemed inferior drums imported from territories with a less stringent test.
Another issue on a similar topic was provided by Martin Castle of Pira, the body that at the time was responsible for packaging approvals in the UK. The UN package testing and marking system was still relatively new and, although it had been adopted in all the modal regulations, there were some variations in how the requirements were presented. Martin also highlighted that, while each approval shows that the particular design has passed the relevant tests, that does not absolve the user of responsibilities. Furthermore, any change to the design will invalidate the approval.
Martin discussed whether there was a need to follow the implementation of inspection schemes that had been introduced in a few countries, to ensure ongoing compliance. He felt it was not needed, unless there was an increase in the rate of packaging failures, although some formal quality control systems would be useful, especially for IBCs.
All these changes pointed towards a more structured, even ‘professional’ approach to the business of packaging and transporting dangerous goods. The European Commission was following suit, proposing that all firms involved in the business should appoint a suitably qualified risk prevention officer. That dream eventually became reality in the shape of the Dangerous Goods Safety Officer.