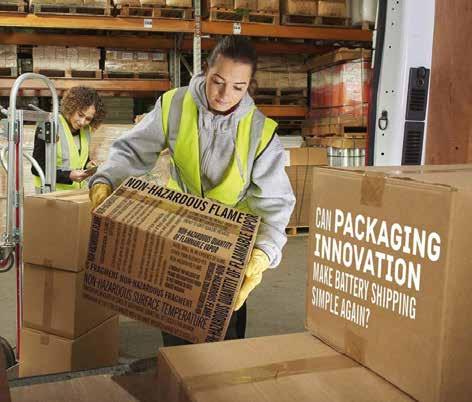
6 minute read
Labelmaster on battery packaging
ASK THE EXPERT…
LITHIUM BATTERY PACKAGING Brian Beetz, manager of regulatory affairs and corporate responsibility at Labelmaster, discusses the various ways to ensure the maximum level of safety during the transport of lithium batteries. It is, he says, “not a one-size fits all” solution.
LITHIUM BATTERIES HAVE become the talk of the industry the past few years, from the fire hazards they pose to the shipping challenges they present. And as the lithium battery market continues to evolve and grow in complexity, the spotlight looks to remain on this dangerous goods category.
Just how complex is the lithium battery landscape? Dangerous goods professionals must contend with shipping an array of battery sizes and chemistries (including lithium-cobalt oxide, lithium titanate, lithium iron-phosphate, lithium-nickel manganese cobalt oxide and lithium manganese oxide) across a wide range of product and device categories that include consumer electronics - cell phones, laptops, digital cameras, handheld devices; and personal transportation devices – hoverboards, e-scooters, Segways, e-bikes and even modern-day electric cars.
This, in turn, has spurred the development of strident restrictions around lithium battery shipments. One recent example is the interim final rule issued in the US this year with new safety provisions for transport, which further prohibit the transport of lithium ion cells or batteries on aircraft and impose additional marking and labeling requirements for shipments by road, rail and air. Another example is last year’s amendment to the UN battery testing regulation, which tests a battery or device’s ability to cope with extreme temperatures, high altitudes, and other system jolts to determine if their safe transport is possible.
Ever-increasing regulations combined with a burgeoning lithium battery marketplace make for a stressful transportation reality. But while dangerous goods professionals responsible for an organisation’s compliance cannot control legislation or product development, they can take control of how batteries are packaged for transport by looking to safer, modern advances that reduce shipping risk and offer the flexibility to accommodate multiple sizes and types of lithium batteries and devices.
RETHINK THE BOX Just as the lithium battery market has evolved, so too must industry’s approach to shipping and storing these goods. Not all sizes and types of batteries can be handled in the same manner. For dangerous goods professionals, understanding the context of their specific shipments can go a long way towards finding the right solution. But first, shippers must narrow down their packaging options.
Traditional cardboard box packaging, while used for decades, was not designed to handle the dangers and challenges inherent in modern lithium battery transport. Traditional cardboard is highly flammable and can easily ignite. One battery blaze can quickly engulf a warehouse, truck, plane, store or home. Dangerous goods pros cannot afford to skimp on proactive protection when it comes to shipping lithium battery-related cargo.
Enter today’s advanced packaging options, with packaging materials engineered to specifically provide a thermal barrier for the transportation and storage of such products and, in essence, contain a thermal event rather than fuel it. With improved flame retardance/arrestment, thermal management, pressure management, blast containment, and gas and smoke filtration, this new generation of modern cardboard boxes are ideally suited to handle lithium battery shipping and, at the same time, simplify the process via cost-effective elimination of gel packs, beads, liners, pellets and fillers.
Not only are there numerous edicts around the shipping and lithium batteries, the regulations and packaging requirements themselves vary depending on the purpose
of the shipment, the company involved in the shipment, the exact batteries or devices involved and the mode of transportation. So while it is important to invest in the latest, safest, most advanced packaging options, it is just as important to make sure the solution that is selected matches your unique situation and purpose.
For instance, ask yourself these questions: • Am I shipping a type of battery that can be transported in a standard corrugated box, or is a more complex UN-certified specification packaging solution required to meet regulatory and safety needs? • Am I transporting this battery as part of a recall, making it crucial to prevent incidents, accidents and exposures as the defective product or battery makes the return journey? • Given my organisation’s specific operations and environment, is simply adhering to the stated regulation enough or must I take additional precautions? • Am I shipping a single device or battery (and what size), or a large quantity of devices/ batteries, and via what shipping method?
To fully determine packaging needs, there’s one more important question to ask: what type of company am I a part of and what will our involvement with lithium-related batteries and products be? Here’s why this matters: • If you’re a device shipper or returner – whether you’re a manufacturer, retailer or other supply chain member, what it comes down to is that you’re responsible for transporting and storing intact lithium battery devices (both pre- and post-sale).
And on the other end, you’re responsible for transporting and storing damaged, defective or recalled (DDR) batteries and devices. • If you’re a recycler – you’re responsible for transporting what are typically old and end-of-life batteries or devices. And given that the number of lithium batteries entering recycling streams is on the rise, this makes the journey to and from recycling facilities (and within facility walls) that much riskier in terms of danger and potential fire hazards. • If you’re a firefighter – you’re tasked to safely handle a thermal runaway incident.
Water can put out a lithium-ion battery
fire, but it takes significantly more water to extinguish it, and even when the fire is put out, the batteries can reignite hours or days later, making proper containment and disposal a safety necessity. In addition, if the battery is lithium metal, water should never be used to extinguish the fire, because lithium metal reacts violently with water. • If you’re an air mover – you’re tasked with transporting lithium-based batteries or devices as cargo on aircraft. Given the potential fatalities that could occur as the result of a battery-caused fire on board, due diligence must be paid toward ensuring the safest transport packaging possible.
KNOW YOUR OPTIONS Once you have a grasp on how your organisation fits into the lithium battery shipment world and what considerations are most important to fulfil your obligations, you’ll want to select a transport packaging provider who can help you achieve your shipping safety goal – one that offers flexible options in terms of size and configuration of packaging. So before making an investment, ask yourself these final questions: • Is the solution easy enough for employees to use correctly? • Has the solution been comprehensively tested and thoroughly vetted to prove it will perform as advertised? • Does the solution adhere to the most recent hazmat shipping requirements and compliance mandates? • Does the solution help save time and resources via the option to have packaging arrive preassembled? Technology advancements will continue to push the boundaries of what lithium batteries can accomplish. As more lithium battery-powered inventions hit the market, the hazards of shipping battery-based products will only increase. Dangerous goods professionals must meet this challenge head on by proactively seeking safer alternatives to traditional transport packaging. This can best be accomplished by thoroughly understanding the industry and an organisation’s role in it. Only then can the best shipping and storage containers be chosen to meet the needs of an evolving lithium battery landscape. HCB
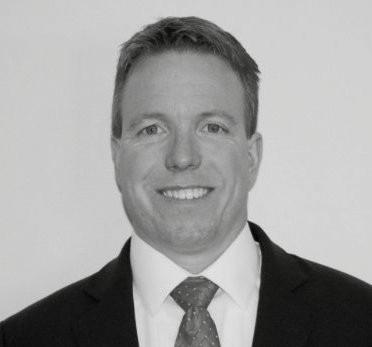
Labelmaster provides a range of services and products for the dangerous goods transport sector, including Obexion packaging for lithium batteries; more information can be found at www.labelmaster.com/obexion.
LABELMASTER’S BRIAN BEETZ (ABOVE) EXPLAINS THE
ROLE OF PACKAGING IN CONTAINING THE HAZARDS
PRESENTED BY LITHIUM BATTERIES IN TRANSPORT
