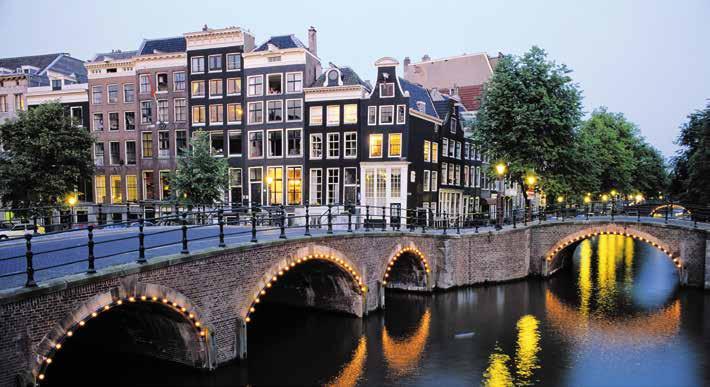
12 minute read
LogiChem leads on digitisation
ELECTRIC IDEAS
CONFERENCE REPORT • THIS YEAR’S LOGICHEM CONFERENCE MAJORED ON DIGITISATION BUT THERE IS MORE TO INNOVATION IN THE CHEMICAL SUPPLY CHAIN THAN JUST THAT
SINCE MOVING TO Amsterdam a few years ago, the annual LogiChem conference has been rejuvenated. It has found an important role particularly in disseminating information and experience about the process of digitising the chemical supply chain, this year attracting some 1,300 delegates to hear from industry leaders about how they are adopting innovations and enhancing efficiency in the logistics sector.
The three-day event opened at the Grand Hotel Krasnapolsky in the heart of Amsterdam on 19 February. Early morning starts and a packed agenda left heads spinning with the volume of information provided, of which this article can give merely an impression – particularly as many of the conference sessions split out into different strands to concentrate on particular themes.
As the chair for the first day, Peter Devos, joint managing director of the European Chemical Transport Association (ECTA), said, “Digitisation is a topic close to all our hearts” – not least his, as he has played a leading role in the development of a digitised version of the European Cleaning Document, the eECD and knows very well the hurdles that have had to be overcome to make that initiative a reality.
Introducing the conference, Devos said he hoped that discussions would inspire the audience and offer a “bridge to the future” and open up the possibility of collaborative ecosystems in the supply chain (which, he said, some find “a bridge too far”).
ONE YEAR ON The pace of development was ably illustrated by Sybille Mutschler, head of digital at Clariant, who reprised her presentation from the 2018 event, reminding the audience of the need to get used to new business models, larger ecosystems, evolving technology and an absence of standards.
There is still time to get onboard but, Mutschler said, the spread is widening. There are still some companies, particularly small and medium-sized enterprises (SMEs), that are not yet on the digital journey, and many of those that are on that path are still in the experimental stage. Furthermore, there is as yet no evidence that digitisation is having an impact on the balance sheet. What it comes down to is, she said, “a race to get to an end-to-end view of supply chains”. Some companies are well advanced but they started years ago. What they have learned is that it is “a journey, not a project”.
Experience with the digital process so far shows that ‘internal kingdoms’ and corporate silos are an obstacle; most successful companies have redefined the areas of needs and skills. Mutschler was critical of system vendors, saying there is a tendency to over-sell their solutions; companies need to solve problems, not to represent a ‘use case’. Experience has also shown that ‘big bang’ thinking is a barrier: the best results have »
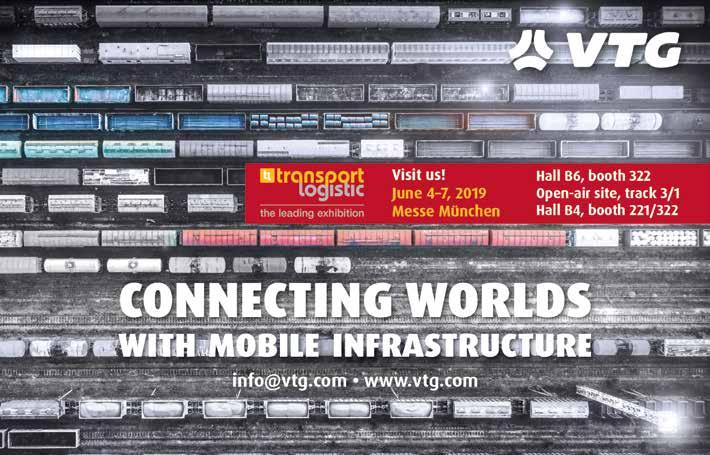
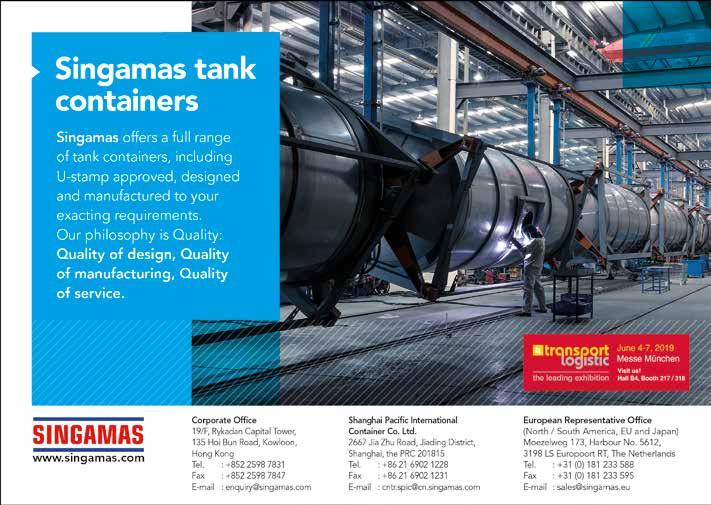
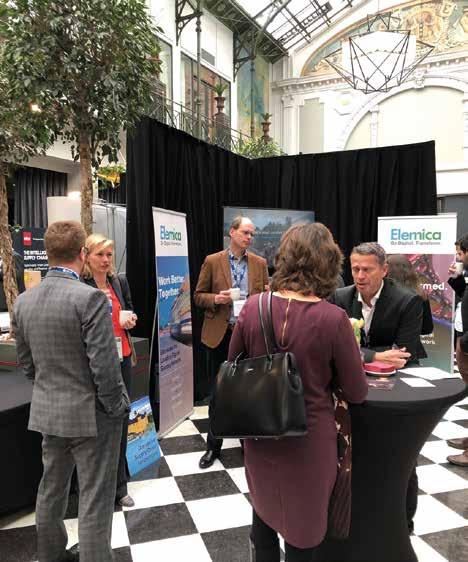
come from learning through implementation and taking a gradual approach.
Developments are also being prompted by customers; a lot of companies have started to digitise the interface with their clients, either because of acceleration in the supply chain or because customers are demanding it. In addition, Mutschler said, there appears to be a pattern of the provision of additional services to customers, especially in the realm of big data analytics.
Platform economics has become a hot topic; there are a lot of startups – Mutschler mentioned Knowde as a notable example – but some incumbent players such as Amazon and Alibaba are moving into the chemicals space. Other chemical producers and distributors are also coming in. But in the end, it is not useful to ask: “Who will win?” It’s not about platforms, it’s about networks, she said. The chemical industry has to get together and collaborate, “but that could get messy”.
GET WITH THE CHAIN Mutschler also mentioned the ‘B-word’ – Blockchain. A year ago this was still seen as an enabling technology that was in the future but there were plenty of examples over the course of the LogiChem conference that it is already being shown to be a way forward. Some companies are experimenting with Blockchain as a way to reduce costs and inventories but, she said, it’s most immediate applicability is in supply chains that require traceability.
Mutschler finished her presentation by saying that her summary this year was very similar to last years – only faster. And the need for collaboration cannot be ignored.
Paul Brody, global Blockchain leader at EY, had more to say on Blockchain, with the experience of implementing more than 300 client projects. “Blockchains will do for networks of enterprises and business ecosystems what enterprise resource planning (ERP) did for the single company,” he said. But he had some warnings to offer: if the system is not broken, companies will not make any money fixing it; and in particular, private Blockchains are a dead end – there can only be one.
Heinz Günther Lux, sensor digital analyst at Evonik, gave his experience of the digital journey, citing five trends: • The growing use of automation and robotics in production • Applying artificial intelligence (AI) to use unstructured information intelligently • Allowing big data to work for the company • Growing use of ‘e-money’ – or the
‘functionalised euro’ – in automated invoicing and payment • Use of Blockchain to change how systems interact. Digitisation can take over the routine work, “leaving people to do the interesting stuff,” Lux said. That means there is a need for different skills in the workplace; people will need to understand the whole process, not just their particular role.
Lux also addressed the issue of legacy systems, which many see as a barrier. But, he said, big investment is not necessarily the answer, just the right ideas. Simple processes are already available to link legacy ERP systems between business processes, which points to the use of Blockchain technology. However, a company cannot simply ‘buy’ Blockchain and force it on its partners: all participants in the supply chain, including customers, need to sit down and define their needs.
WHAT THE BIG BOYS THINK Two speakers from BASF gave their insights on how the company has experienced the digital journey. Jan Brüning, cluster head of smart supply chain, reminded the audience that BASF had set out to define a digital road map in 2015 and quickly identified the need to break down the silo mentality and “build some
logic into processes”. The vision was to create visibility on the end-to-end flow of material via a central platform and, through horizontal integration and collaboration, to generate end-to-end planning in real time.
BASF found that initiating the digitisation journey requires a ‘sandbox’ with a mandate from the CEO. “We have to challenge existing ways of thinking, we have to be agile and imaginative, with out-of-the-box ideas,” Brüning said. “We have to be able to isolate this before developing the pilot. Be careful how this is funded.”
Brüning’s second finding from the process was that buy-in from users and clear leadership are prerequisites for successful scaling of pilots to the organisation level. The benefits need to be clear and need to fit with business KPIs. Leadership is crucial.
By the end of the ‘BASF 4.0’ project in 2018, the company had identified the need for a centralised data core but with decentralised accountability, Brüning explained. The digital transformation is built on the co-existence of a central push and a decentralised pull. “Build a common backbone with basic tools, without bloated bureaucracy,” he advised.
BASF is still not where it would like to be, but it is getting there, Brüning said. It has already cut inventory levels at customer locations and is getting more feedback. Digitisation is now seen as a core and integral part of the BASF business.
Holger Ruckdäschel, head of digital innovation, looked at some of the specific initiatives BASF has implemented, such as multi-load smart assets. For instance, it partnered with a startup, AHRMA, to develop smart pallets, which are equipped with a transponder that sends information on location, acceleration, temperature, humidity and weight to existing ERP systems. Putting in a system such as this opens up the possibility for users to think beyond the immediate application and about how the solution could be applied elsewhere.
BASF is well placed to do this sort of work, Ruckdäschel said. Its huge internal ecosystem allows space for experimentation and to mimic the external ecosystem before rolling out new ideas. “Start small but scale fast,” he said, and be prepared to fail fast.
NEWS FROM THE REAL WORLD There was plenty more on digitisation during the first day’s presentations, but the second day moved towards “the real ugly world out there”, as Maarten Cornelissen, head of supply chain at Teijin and chair for the day, put it. Lars Koppelmann, vice-president of supply chain management and logistics procurement, EMEA at Ineos Styrolution, was a little more measured, describing it as “an increasingly dynamic, volatile world” where the US president can start trade wars or shift stock markets with a Tweet, where children »
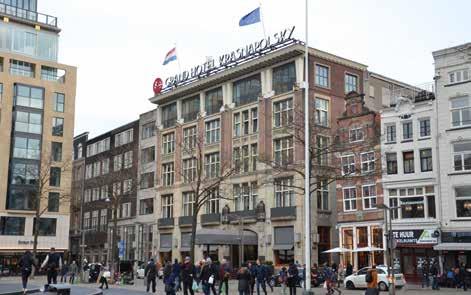
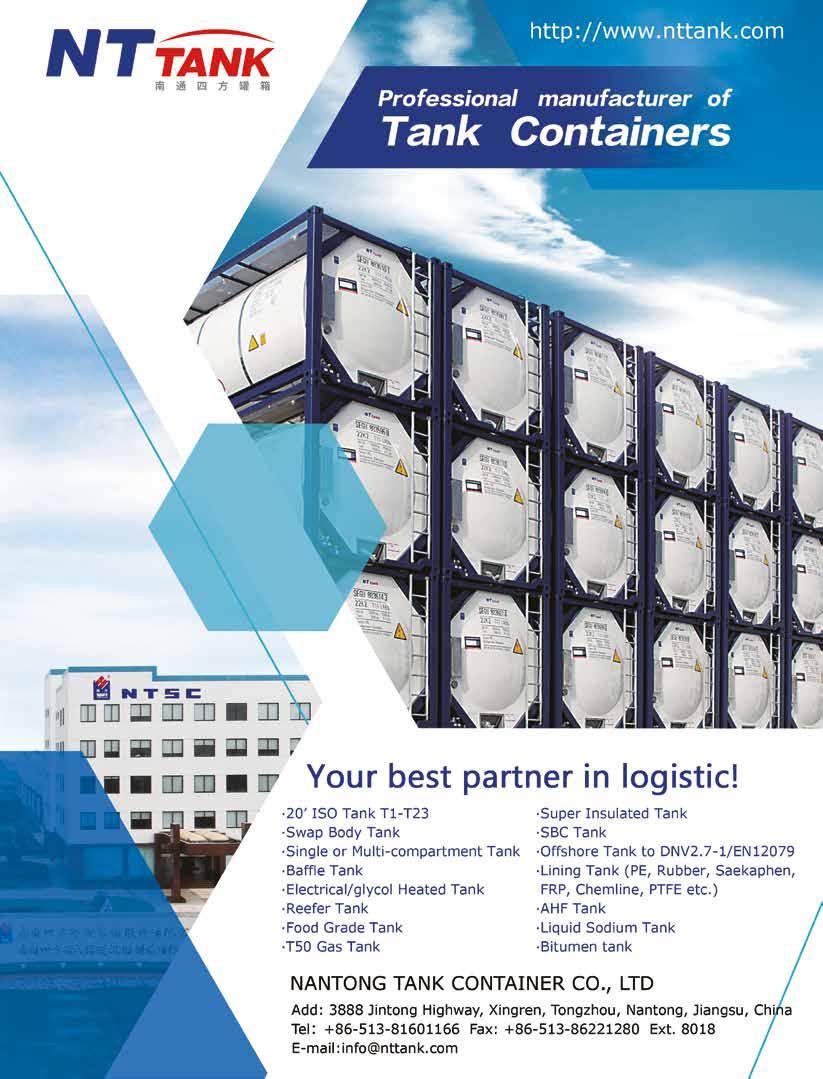
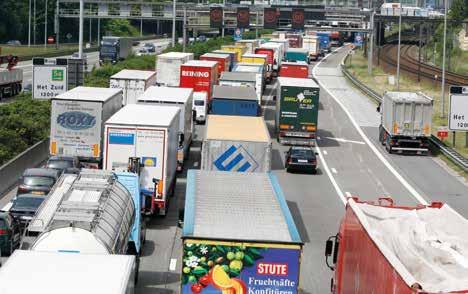
are protesting in the streets – and don’t get him started on Brexit.
This is all summed up in a handy new abbreviation – VUCA (volatility, uncertainty, complexity, ambiguity). Europe has failed to address ageing and limited road and rail infrastructure, Koppelmann said; in contrast, many Asian countries have invested heavily and quickly on hinterland connectivity. The European focus on stricter regulation, especially on environmental issues, is not addressing capacity problems.
All this VUCA generates big changes in product flows and the logistics function now has to be a differentiator in business. Ineos wants to use more rail transport in Europe but the capacity is not there; it is not flexible and not reliable. Similarly, barge transport has been subject to disruption from low or high water levels on the Rhine.
Digitisation can provide real value and collaboration is vital, Koppelmann said, not just between companies but between industry and government.
In a panel session, Cornelissen said that recent product shortages meant that Teijin turned from an exporter to an importer; finding the product was no problem but transport capacity was – the company had to buy product at a location where transport was available. That led into a discussion of the relationship between shippers and their logistics service providers (LSPs), with Jan Roed, head of global logistics at Borealis, saying that price is becoming less and less important. Sustainability demands point to greater use of rail and barge, even if those modes are costlier and less reliable. “Customers are not willing to pay for short lead times,” he said, “they are more interested in reliability.”
BE LUCKY The topic of sustainability was picked up on by Steven Beddegenoodts, lead of the petrochemical supply chain at Sabic, who said that sustainability is “more real than money”. How do you measure it? He advised to look at where the carbon is coming from – and in the logistics sector that is mainly in truck exhausts. For chemical companies, logistics operations account for only 4 to 7 per cent of their total greenhouse gas (GHG) emissions – but they are more visible to the public.
The new Global Reporting Index programme includes limits on emissions from transport operations, which will be mandatory from 2022. For any shipper, the only way to reduce overall emissions is to shift modes, Beddegenoodts said. He noted that recent improvements in ship design have shown that fuel savings of up to 32 per cent are possible. “Think if that happened on trucks!” he said.
But sustainability is more than just about the carbon footprint. “What you do should matter,” Beddegenoodts continued. “Transport will never be totally sustainable – there is a need for fuel to move things from A to B.” But companies can look at issues such as human development, Corporate Social Responsibility, better SHEQ »
standards, plastics pollution, and so on. Also, as he concluded, “If it’s not safe, it’s only sustainable until your luck runs out.”
There was an interesting panel discussion on the thorny issue of driver waiting times, involving Jan Roed, Peter Devos and Pablo Nosti of DuPont. Drivers are in short supply in many markets and it seems ridiculous that they spend so much of their time hanging around rather than driving, which may also deter new entrants to the business.
As Devos put it: “Look at it from the driver’s point of view. He’s filling your order, his profession is driving, not hanging around. Even if the driver is compensated for waiting time, it’s still a frustration. It’s now becoming a liability – drivers are leaving to more rewarding roles.”
KEEP THE DRIVER HAPPY Nosti observed that driver waiting times can highlight inefficiencies in producers’ own processes. “We don’t work on it enough,” he admitted. Devos reminded the panel that a working group looking at driver shortages recommended the use of time slots. That was in 2007 and traffic congestion has worsened since then (“especially in Antwerp”), he said. And it’s not just at the shipper’s plant; the driver may have to wait to unload, to clean the tank and then again at the next load point.
“We need to start collecting data,” Nosti said, “and to start working on allowing outof-hours loading.” DuPont is trying to bring the conversation into the contract renewal process and give its LSPs the opportunity to reveal the extent of the problem.
Devos agreed that opening up the dialogue is a good thing and will help identify inefficiencies. It will also allow parties to look at the end-to-end transport chain; for instance, at present, if a truck is parked up outside the plant waiting for entry, it does not count as ‘waiting time’. It also appears that LSPs are beginning to avoid serving those facilities that are known to have long waiting times.
ECTA has been working with the European Chemical Industry Council (Cefic) and the International Road Transport Union (IRU) on the problem; a report is expected later this year. It may point towards the use of preloading, with loaded trailers parked outside the plant so that drivers can just pick them up, and towards greater use of multimodal transport. Essentially, though, “Drivers need to be treated with respects at both ends of the trip,” Devos stresses.
Technology is now available to automate the entrance procedure and loading/unloading operations, and some pilot projects are underway, Devos noted. This is fine for regular operations but there is no standardisation between companies, or even between one company’s various locations. However, it looks like a solution for the future. HCB
Speaking of the future, next year LogiChem will up sticks again and will take place at De Doelen ICC, Rotterdam on 17 to 19 March. Full information is available at https://logichem.wbresearch.com.
