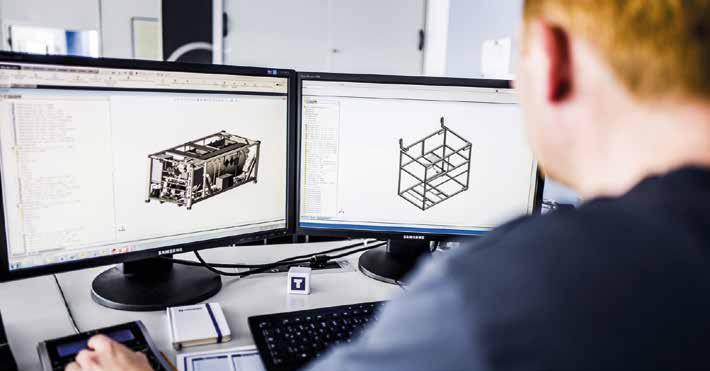
5 minute read
Thielmann designs your tank
DIFFERENT AND COMPLICATED
MANUFACTURING • THIELMANN’S EXPERIENCE IN DEALING WITH UNUSUAL APPLICATIONS AND AN OPEN-MINDED ATTITUDE HELP IT DEVELOP THE RIGHT TANK FOR THE JOB
WITH 2019 NOW well underway, THIELMANN is working on new and innovative ways to serve its customers. The company will be taking part in the Transport Logistic exhibition in Munich from 4 to 7 June and looks forward to seeing what trends operators across a range of sectors are most interested in and how latest THIELMANN technology developments can help them overcome their biggest challenges.
“Logistics is an increasingly important driver in changing global markets, which is why exhibitions such as Transport Logistic are such important events for us to get out to and talk to our customers about the developments and innovations we are working on,” Sebastian Bojarski, THIELMANN product line director, says. “For many, effective logistics are the cornerstone of their business models - with the ability to efficiently transport, store and distribute goods dictating where our customers can operate and how they can reach their customers.
“Our role is to make these processes as simple as possible, and provide end-to-end solutions that deliver not just efficiency, but have a direct impact on the bottom line – our ultimate goal is to help our customers achieve their business goals and we are working on innovative ways to do that.”
The company will be focusing on a number of new technologies at the event, and in particular will be highlighting a new solution currently in development for the chemical market. CHALLENGING CONDITIONS THIELMANN has a unique understanding of the constraints under which customers in the chemical sector are operating. In 2018 the company delivered fuel tanks to the Norwegian Polar Institute (NPI) for use in a fuel tank farm near NPI’s Troll Station, the Norwegian research station in Antarctica. The tank systems were designed to meet the harsh operational realities of operations in an environment where there is very little in the way of second chances. Certified to store and transport jet fuel, diesel and petroleum via road, rail and sea, the tanks were filled with diesel fuel for transport to Troll Station. As with the majority of THIELMANN’s fuel tanks, the systems could be deployed with minimal site preparation and were ready to begin discharging fuel immediately after their arrival on site.
“This was an immensely demanding project that needed an industry-leading expert to design, manufacture and deliver tanks capable of withstanding the challenging operational conditions at Troll Station, where temperatures can get as low as -40°C,” Bojarski says. “The tanks needed to be built to withstand those conditions without requiring heavy maintenance throughout their service life. »
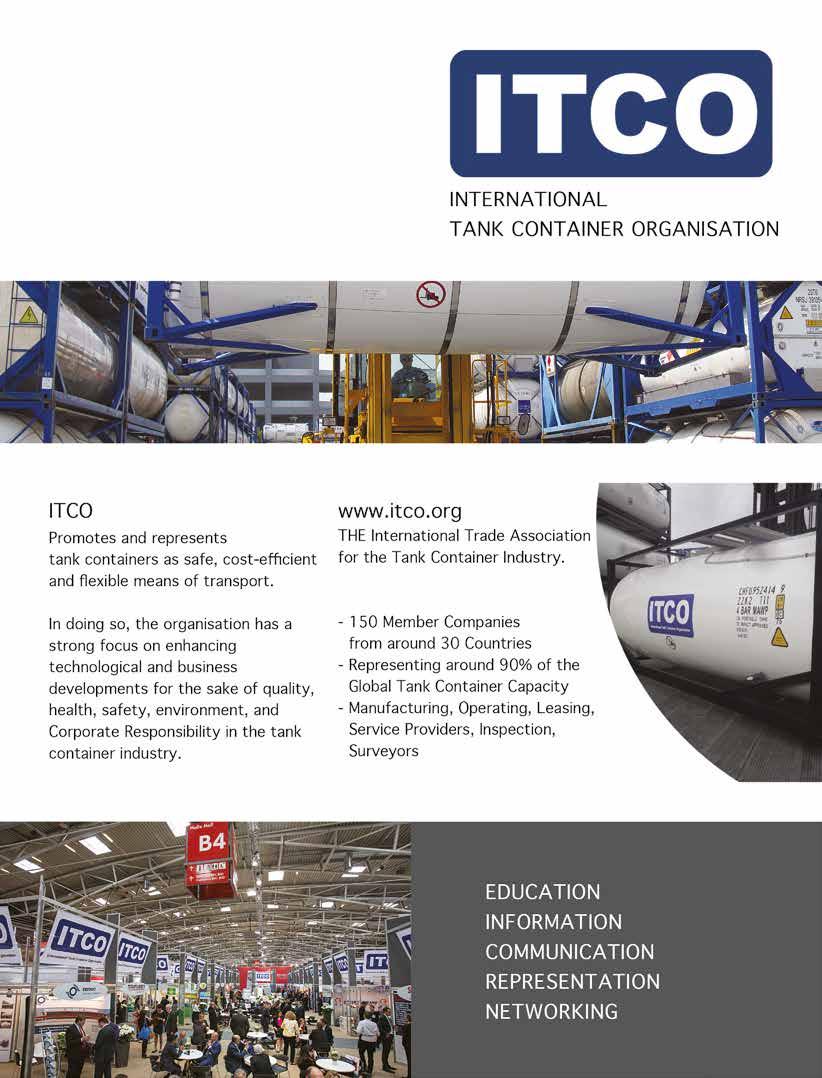
“Luckily THIELMANN stainless steel solutions can deliver on these requirements, and we were able to deliver these tanks on schedule. We are confident they will continue providing fuel for the next 30 years or more.”
THIELMANN ON SHOW THIELMANN is currently putting this experience to good use and a system that based on a similar design approach will form the focus of the company’s presence at the Transport Logistic exhibition.
The double-shell container system has been designed to meet the needs of the chemical industry. Fitted within a 20’ x 8’ x 8.6” frame with welded headbeam design, the tank has a nominal capacity of 7,500 liters (7,125 litres at 95 per cent filling). It is equipped for top discharge and approved for storage and transport on road, rail and sea of products in accordance with UN T20 approval, including methyl dichlorosilane, trichlorosilane and chlorosilane.
The tank has a working pressure of 6.66 bar, a maximum gross weight of 36,000 kg and a stacking weight of 192,000 kg. It is certified for handling according to ISO 3874 where applicable. Additionally, it can be fitted with access equipment including walkways (longitudinal and transverse), ladders (with foldable sections at top and bottom) and handrails.
The tank is manufactured from 1.4404 stainless steel. Accessories are manufactured in 1.4301 stainless steel and aluminium. Top surfaces are covered with anti-slip material for operator safety, and spillboxes with drainage tubes prevent pooling and direct overspill away from walkable areas.
The tank is also able to be fitted a 3-mm thick heating system. These heating channels can keep the tank heated in order to ensure the stability of the substance it contains, and further insulation is also a possible option. INNOVATION BY DESIGN As with all THIELMANN designs, the tank can be tailored to meet specific requirements and adjusted to meet the demands of all operations, no matter how niche. For example, heating and cooling systems in various designs can be used – from thermal oil, water and steam, and electric heating systems, to heating and cooling systems – with documentation recorders for materials which may only be transported in specified temperature ranges. Tank insulation is calculated according to the temperature range and use of the unit, and cladding can be installed using matt or high gloss stainless steel, aluminium or fiberglass. For substances that require inner lining – such as some acids or alkalis - a number of options are possible, including Chemline, Proco-EMAIL, or Säkaphen; plastic coatings (PFA/FEP/Teflon), special interior lacquers, lead linings and glassenamel coatings are also available.
“This design is testament to the extraordinary capabilities of our design engineering team, as they continue to push the limits of what is possible for our customers operating in demanding sectors,” Bojarski says. “Our long experience working with our clients in the chemical, oil and gas, nuclear, emergency services and government sectors have given us deep insight into the challenges these users face and how our solutions can overcome them.
“We specialise in the different and the complicated – our ability to take on these difficult projects and serve our customers with innovation is what sets us apart from our competitors. Whether the project requires multimodal transport, ancillary equipment such as pumps, specialist linings, filtration, telemetry as well as heating and cooling systems, our tanks are designed and approved for the transport and storage of some of the most dangerous and toxic chemicals on earth.” HCB www.thielmann.com
THIELMANN HAS USED ITS EXPERIENCE IN DEVELOPING
A SPECIALISED TANK FOR USE IN THE ANTARCTIC TO
COME UP WITH AN INNOVATIVE DESIGN FOR SPECIFIC
