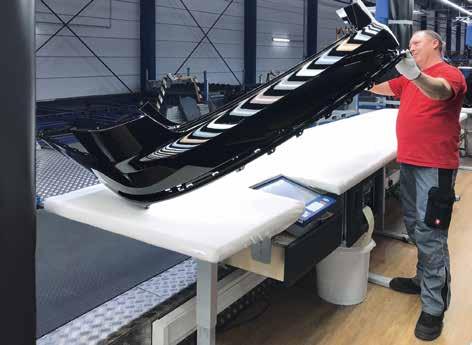
5 minute read
Schütz keeps contents clean
DECONTAMINATION ZONE
COATINGS • CLOSE ATTENTION TO DETAIL IS NEEDED IF AUTOMOTIVE COATINGS ARE TO REACH THE USER WITHOUT CONTAMINATION, SOMETHING THAT SCHÜTZ IBCS ARE DESIGNED TO PROVIDE
THE AUTOMOTIVE INDUSTRY frequently relies on layers of coatings that are a tenth of a millimetre thick; any contamination in these coatings can drastically compromise their protective function. This is particularly true with surfactant substances, such as silicone oils and fats. Any irregularities and issues with these substances can lead to wetting defects affecting both the appearance and protective function of the product. Rectifying compromised products can lead to considerable additional costs, so minimising the risk of contamination throughout the supply chain is absolutely essential.
The risk is even greater when viscous coatings are involved. These require stirring before use, but the introduction of a stirrer into the container can add to the potential for contamination. Even opening or closing the packaging can introduce forms of contamination.
Intermediate bulk containers (IBCs) are frequently used to transport and store coatings and IBC producers have been looking at how they can work together with fillers and users to mitigate the risks of contamination.
For instance, Schütz has been supplying Karl Wörwag Lack- und Farbenfabrik with IBCs for nearly two decades and also works closely with Samvardhana Motherson Peguform (SMP Automotive), a major customer of Wörwag. Wörwag is a specialist in the production of high-quality paints for a wide range of industrial applications, and SMP is a specialist in plastic-based components for major automobile manufacturers.
Wörwag and SMP had been seeking a solution to minimise the risk of contamination during filling and subsequent processing of clear coatings and primers. Schütz offered its Cleancert line of IBCs, configured to support the process with an Impeller and an S56x4 bung. Thanks to the integrated Impeller, the container is able to remain closed throughout the entire supply chain – from filling to emptying. Concurrently, the contents can be easily and effectively stirred. Conventional stirrers are no longer required, drastically reducing the risk of contamination.
MORE FOR YOUR MONEY Furthermore, Schütz’s IBCs are able to use the available space more efficiently than alternative solutions. Whereas only two steel containers can be stacked atop each other, up to four IBCs can be stacked together, substantially improving the use of storage space. The need to store empty containers is also significantly reduced through the use of the Schütz Ticket Service. This collection service ensures that emptied IBCs remain at the plant for no longer than seven days – it is not unknown for empty steel containers to remain in the plant for up to a month, which has historically caused bottlenecks in warehouses.
“These advantages absolutely convinced us, and that is why we use Schütz’s Cleancert IBC for clear coatings and primers as these products are particularly sensitive to surface defects,” says Benno Beuter, application engineer at Wörwag.
Over the course of several weeks, SMP conducted a series of tests to accurately document the benefits of the Cleancert IBC and Impeller closed packaging system in practice. Clear coats, primers and base coats are continuously stirred in an air-conditioned paint mixing room during processing, ensuring a homogeneous consistency. »
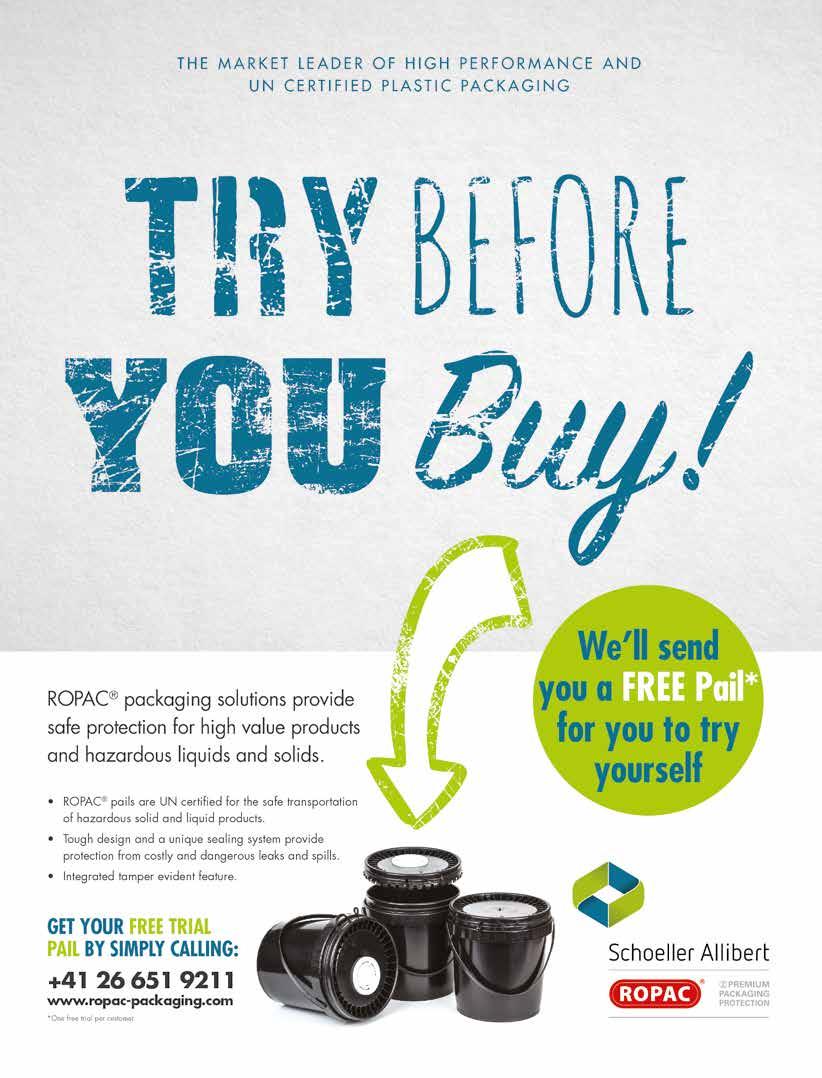
When testing with external steel stirrers, 140 to 200 revolutions per minute were required to maintain homogenisation. This high speed led to increased air intake into the product, which culminated in an amplification of microfoam formation. However, when stirring with the Schütz Impeller, only 80 to 110 revolutions per minute were sufficient. The lower speed ensured gentle stirring processes with optimum results. Anton Krojer, the SMP application engineer in charge of the test series, was highly satisfied with the positive test results, saying: “Thanks to the efficient stirring processes, we no longer need preparatory homogenisation measures prior to a container change.”
“The use of the Impeller as a disposable system completely rules out the risk of contamination due to residual product adhering to the stirrer. This greatly increases process reliability,” says Manfred Guttmann, head of the paint shop at SMP. “This eliminates the complex and time-consuming cleaning process for the agitator, as well as other risks. Employees no longer have to handle solvent-based cleaning agents, which greatly improves work safety.”
Through these tests, SMP was able to dramatically reduce the amount of work spent on corrections. Additionally, the tests highlighted the benefits possible and revealed business management advantages. This cross-party cooperation shows how important it is to involve all companies along the supply chain to achieve higher levels of compliance and efficiency.
HYGIENE AND TRACEABILITY According to Schütz, the initial idea for the development of the Cleancert IBC was prompted by the food industry, where production sites are certified according to the Food Safety System Certification (FSSC) 22000 standard, combined with the implementation of numerous specifications within the framework of the hazard analysis and critical control points (HACCP) and failure mode and effects analysis (FMEA) standards.
Hygiene is clearly vital in the food industry, with detailed regulations covering the cleanliness of personnel, their closing, the workplace and its equipment. Measures also include the prevention of dust, contamination, and glass and blade management procedures. There are maintenance regulations and checks on machinery, systematic pest control across the facilities, controlled use of all working materials – particularly when dealing with greases and lubricants – and a secure goods receipt.
Using a just-in-time model, Schütz works on the basis of specific customer orders. Immediately after the blowing process, IBC inner bottles are transferred to the final assembly stage and installed. Each production step and each component can be clearly assigned to the corresponding packaging. Identification via a barcode system enables complete traceability. There is also the ability to assign individual identification numbers for articles or packaging materials.
Once finished, the IBCs are loaded indoors and shipped directly, avoiding intermediate storage. Pre-produced components, such as screw caps, outlet valves or bung plugs, are hygienically packed and stored separately. Specialised closed rooms are available for shipments that are due to be dispatched at a later date. Optional plastic covers can be introduced to offer an additional layer of protection.
Ultimately, once combined, all of these precautions and detailed steps provide a huge amount of assistance to maintaining the quality of subsequent products across the supply chain. HCB www.schuetz.net
SCHÜTZ IBCS MINIMISE THE CHANCE OF CONTAMINATION
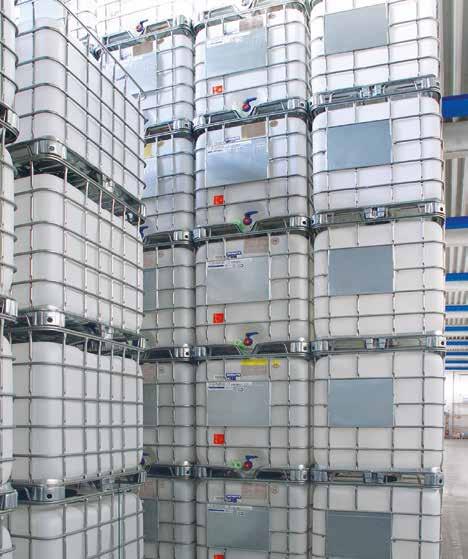