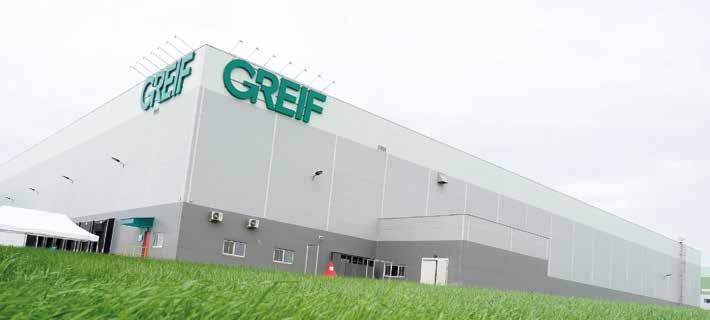
2 minute read
Greif expands in Russia
NEW AND IMPROVED
MANUFACTURING • THE OPENING OF GREIF’S NEW MANUFACTURING FACILITY NEAR MOSCOW WILL UNDERPIN GROWTH IN LOCAL DEMAND AND PLUG A GAP IN GREIF’S GLOBAL IBC AND DRUM NETWORK
GREIF, A GLOBAL leader in industrial packaging, recently welcomed more than 200 guests to the official opening of its new Russian steel drum production plant in Vorsino Industrial Park, Kaluga. The new facility (above), Greif’s ninth plant in Russia, is situated 80 km south-west of Moscow and has already begun production of the company’s state-ofthe-art drums, with a new intermediate bulk container (IBC) line due to be launched in 2019.
Speaking at the opening ceremony, Pete Watson, CEO of Greif, highlighted the expertise of the Greif team in Russia and the results that they have achieved over the past 25 years. Also In attendance were Dmitry Orlov, CEO of Gazprom Neft-Bitumen Materials, and Nikita Mikhin, deputy director of Obninskorgsintez, who represent longstanding partners advocating Greif’s product quality and customer service excellence.
The new 6,000-m² facility will employ a team of 50 and features an automated steel drum line with an annual capacity of two million units. The facility is also in close proximity to several of Greif’s key customers.
“We are delighted to officially open this latest Greif facility to better serve our local customer base,” says Konstantine Savinov, general manager of Greif Russia. “Delivering greater flexibility, reduced lead times and lower transportation costs is central to our ongoing improvement plans. The Kaluga plant will enable us to achieve all of this with existing partners and further build on our market leading position by introducing new customers.”
ON BRAND In addition to its new facility, Greif has introduced some improvements to its range of GCUBE IBCs. IBCs are stackable, reusable containers with an integrated pallet base mount that allows them to be easily manoeuvred with a forklift. IBCs have a volume range that sits between standard shipping drums and intermodal tank containers and can be made from metal, plastic or composite material.
Demand within the global market for IBCs has grown steadily in recent years with the rising need to transport liquids such as food, fuels, chemicals and hazardous materials. Some of the major growth drivers in the IBC market are the provision of cost-effective transport and storage, uncomplicated maintenance, and their reusability. The new innovations see Greif replace the generic aluminium foil seal with a GCUBE-branded one, designed specifically to remove the risk of product counterfeiting while also offering customers the reassurance of improved product protection.
“We continue to invest in our GCUBE IBC solutions and this new branded butterfly valve seal is yet another significant market development,” says Luca Bettoni, EMEA IBC and plastic product manager at Greif. “We are the first company to introduce a branded aluminium foil seal to its IBC valves giving customers total confidence in the integrity of the seal and most importantly the contents of the container at its end destination.”
Both the branded foil seal and the safety screw can be removed by hand. Additionally, the technology that Greif implement means that no foil residue will be left on the valve outlet, eliminating the risk of contamination.