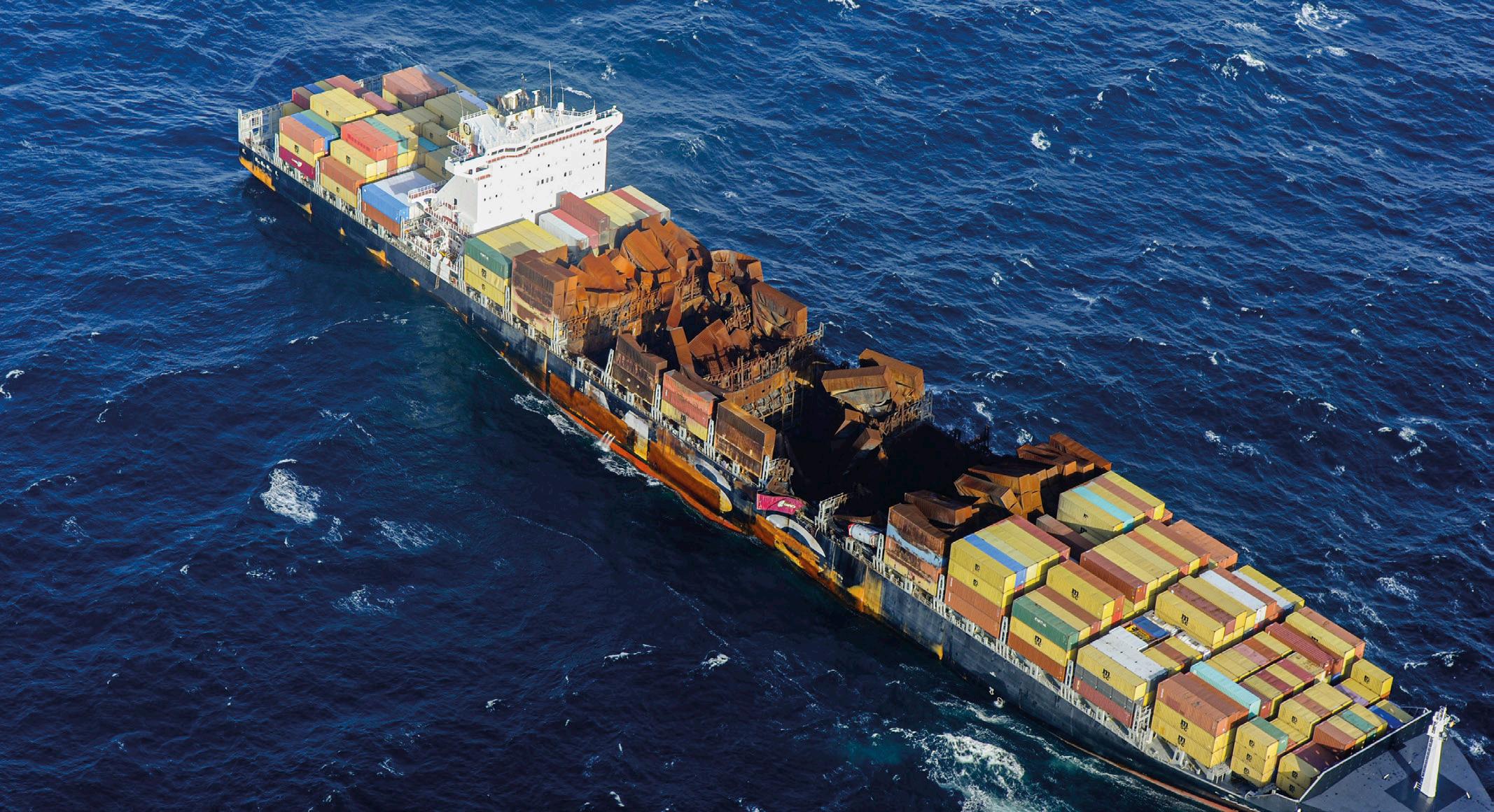
12 minute read
Report on ITCO’s Amsterdam meeting
TANK PEOPLE
REPORT • ITCO’S AMSTERDAM MEETING DREW A LARGE CROWD, KEEN TO HEAR HOW RECENT ACCIDENTS AND REGULATORY ACTIVITY WILL IMPACT THEM AND THEIR OPERATIONS
The disaster aboard the containership MSC Flaminia in July 2012 is still causing waves in industry. A court judgment in New York last year divided liability for the incident between Deltech, manufacturer of the cargo of divinyl benzene, which is thought to have almost certainly been the seat of the initial fire aboard the ship, and Stolt Tank Containers, in its role as an intermediary in the transport and operator of the tank containers that the product was stowed in.
The realisation of the potentially enormous liabilities that could land at the doors of tank container operators and their partners in the supply chain was perhaps one reason for the big turnout at the annual members’ meeting of the International Tank Container Organisation (ITCO), which took place in Amsterdam on 30 September and 1 October this year. Nearly 150 people attended the event, which in its open sessions featured a panel discussion moderated by HCB’s editor-in-chief Peter Mackay and a series of presentations on topics of crucial interest to the sector.
Delegates were welcomed by Reg Lee, ITCO president, and the format was explained by Patrick Hicks, general secretary of the Organisation.
THE FULL IMPLICATIONS OF THE MSC FLAMINIA
INCIDENT AND COURT JUDGMENT ARE ONLY NOW THE ROOT CAUSE While there was more to talk about than just the MSC Flaminia incident, the keynote session started with a presentation by Peregrine Storrs-Fox, risk management director of the TT Club, a mutual insurance group with a focus on dangerous goods in the international maritime supply chain, who recapped the events that led to the fire and explosion aboard the vessel, with the loss of three lives, and the attempts made to save the ship and to investigate the cause. He also gave some indication of the extraordinary length of the court case, the results of which are still subject to appeal.
It was, though, heartening to hear from Storrs-Fox that the MSC Flaminia case is one of the very few that has been directly linked to tank containers, which in general are an exceptionally safe way of moving dangerous products. That does, though, not prevent this incident having repercussions arising from the court case.
For a start, the judge who made the allocation of liability was very clear that the regulations governing the transport of dangerous goods merely set the baseline for compliance. Shippers and their intermediaries should of course comply with the regulatory requirements but in addition should make sure to provide all relevant information to other parties in the supply chain, whether or not it is required by regulation. Storrs-Fox »
posed a question: what is the implication of that statement?
What is more, how is all that relevant information to be transmitted? Should it be included in the safety data sheet (SDS)? Has the SDS now become a transport document? What is the role of IT in matching the SDS with the Dangerous Goods Declaration (DGD)? These are all difficult questions to answer. The SDS is not designed to be a transport document – it is supposed to provide information to the ‘supply and use’ sectors further downstream and lists the inherent chemical and physical properties of a substance; while there is some information relevant to transport, this ought to be limited to its classification under the transport regulations.
The underlying problem, Storrs-Fox posited, is that parties across the supply chain are finding it difficult to interpret the regulations. Why is that? Is it because the regulations are so complex? Or is there a lack of expertise? It is probably a mixture of both. DOING IT RIGHT ITCO had done well to get someone from Dow Chemical to come and speak to the audience about how the chemical major is addressing safety in the transport chain. Maayke van Noort, global senior ES&S mode leader for marine bulk and terminals at Dow, explained the company’s 2025 Transportation Stewardship programme, its version of product stewardship for the logistics sector. This fits in with Dow’s broader sustainability drive and focuses on ‘control management’ rather than ‘consequence management’.
Van Noort also explained Dow’s Transportation Safety and Security Outreach programme, which aims to share the lessons of incidents in the supply chain across its logistics service providers (LSPs). It does, perhaps, offer a model for others in the industry to follow, and van Noort was only too happy to share the information.
The stewardship programme includes specific additional risk assessments for high-hazard products, van Noort said, and this includes polymerisers – although she also noted that monomers do not make up a large proportion of Dow’s shipments. These risk assessments do, though, point to a need for particular measures to be taken during transport, including for instance the use of ‘smart tanks’ with temperature control. The main drawback to the use of such tanks is the limited connectivity available during a sea voyage.
Dow is also trying to limit the storage of loaded tank containers during shipment, either by getting them faster to the consignee or by transferring their contents into bulk storage.
Van Noort was not the first during the event – nor would she be the last – to stress the importance of communication between all parties in the supply chain, not least between the ‘shipper’ – the manufacturer or supplier – and the tank container operator; the MSC Flaminia case had highlighted the fact that under US law the tank container operator takes the role of the ‘person offering the tank’ and as such is in effect the shipper, with all the legal obligations that follow.
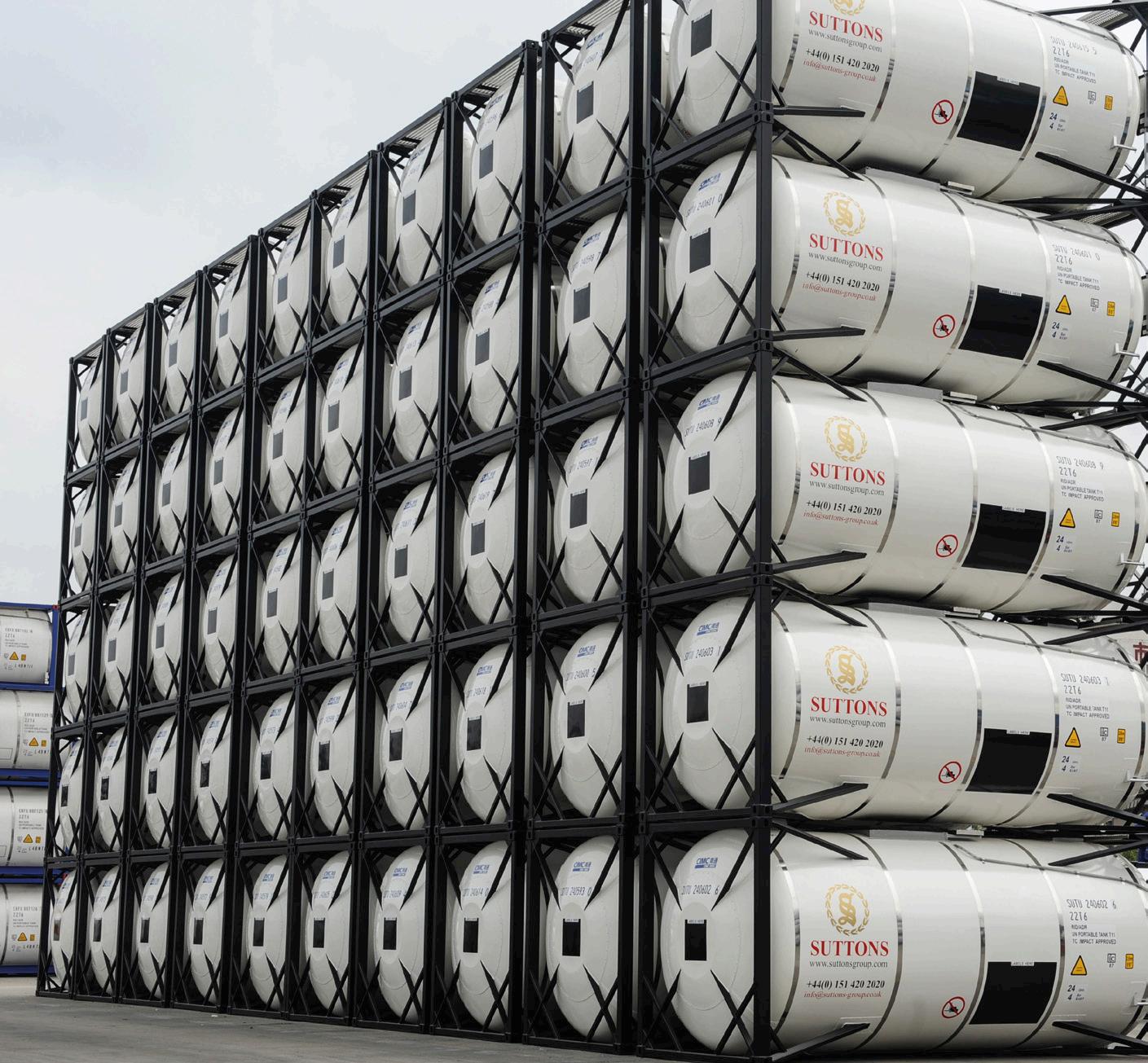
WHAT THE PANEL THINKS Van Noort then took her seat alongside Storrs-Fox and three other panellists: Martin Levitt, technical director of Den Hartogh Global Logistics; James Rawlinson, group technical services manager at M&S Logistics; and Colin Rubery, technical secretary of ITCO.
The panel began by discussing the particular obligations under special provision 386 in the International Maritime Dangerous Goods (IMDG) Code and the issues that it raises in terms of the transport of polymerising substances in tank containers. As should by now be clear, implementation of those obligations requires communication between all the parties, including the shipping line. More specifically for this audience, the tank container operator has an obvious duty of care that extends beyond the strict provisions of the IMDG Code.
In terms of the use of the SDS in the transport chain, the panel agreed that data relevant to logistics is limited; both the panel and contributors from the floor also agreed that the accuracy of classification information on the SDS is variable at best. There are also
frequent cases of – perhaps wilful – misdeclaration. The audience was urged to evaluate all SDSs they are provided with and to ask for missing data and query anything that looks wrong.
Given the importance of information sharing, the panel also discussed the growing position of fourth-party logistics providers (4PLs) in the chain and whether this was causing problems. Properly vetted and managed, like any partner in the chain, there should be no issue but the supply chain is already complex and the use of 4PLs does add yet more complexity. Electronic data transmission has the potential to make life easier for all concerned but it was also stressed that this is not a panacea - all parties still need to know what information is needed and have a duty of care to make sure it is shared.
It was relatively easy to get the panel to agree that safety in the transport of dangerous goods in tank containers requires a solid approach to quality management by all parties. The recruitment of suitable personnel is becoming a problem but all parties can help by ensuring those that they do hire are provided with full and effective training. But when it comes down to it, it’s all about effective communication.
The day ended with a very enjoyable networking reception at the meeting’s venue, the Hilton Apollolaan, with plenty of local beer and foreign wines, that kept attendees together for lengthy discussion of the afternoon’s events.
KNOW YOUR RISKS Suitably revivified, the meeting reconvened the following morning for a review of the panel discussions and a series of presentations. Anyone still feeling a little sleepy was roused by Peter Mackay, who spoke about the need to learn from the lessons of accidents in the past, especially as the older heads in the business reach retirement (or pass over into the world of consultancy). For instance, he reminded the audience of the Flixborough disaster in the UK, which led to the Control of Major Industrial Hazards regulations; this took place in 1974 and, on the basis of a show of hands, at least half the audience were not even born then.
Capt Howard Snaith, general manager of the Chemical Distribution Institute (CDI), explained the role of CDI in inspecting and auditing procedures to improve safety in the supply chain. CDI was initially established to provide a consistent auditing programme for chemical and gas tankers and soon developed a parallel system for storage terminals. More recently it embarked on an ambitious project to offer audits along the marine packed cargo supply chain, including tank container operators. Snaith offered this observation: the safe transport of your tank container is only as safe as the container it’s stowed next to. In other words, everyone in the supply chain is at risk from those who do not do things properly.
Snaith spoke more about ‘risk’: it is the chance of something happening but, he said, not all risks are immediately apparent, hence the need for effective oversight. Risk management is the implementation of processes or systems designed to reduce the risk of an incident in everyday operations; to be effective, risks need to be assessed. And to do that requires knowledgeable, experienced people who can define the protocols that establish risk; and properly trained people to collect the necessary information. Here again, the dangers posed by the loss of expertise were apparent.
The real threat to the global containerised supply chain, Snaith said, is that only about 3 per cent of all containers are actually inspected. Given that there are more than 200 containership casualties every year, peaking at 267 in 2016, according to Lloyds Casualty Reporting Service, there is a real risk that any shipment may get caught up in an incident. This is where CDI’s International Marine Packed Cargo Audit Scheme (IMPCAS) aims to make a difference, and Snaith urged those in the room to get involved. He ended with a brief advertisement for CDI’s latest publication, Packaged Chemicals by Sea: Risk Mitigation, clearly a must-read for this audience.
KEEP OFF THE TOP One often overlooked risk in the supply chain is presented by the need to work at height. Evert de Jong, joint managing director of the European Chemical Transport Association (ECTA), reviewed the European legislation »
ABOVE: IF PERSONNEL HAVE TO WORK AT HEIGHT, THEY
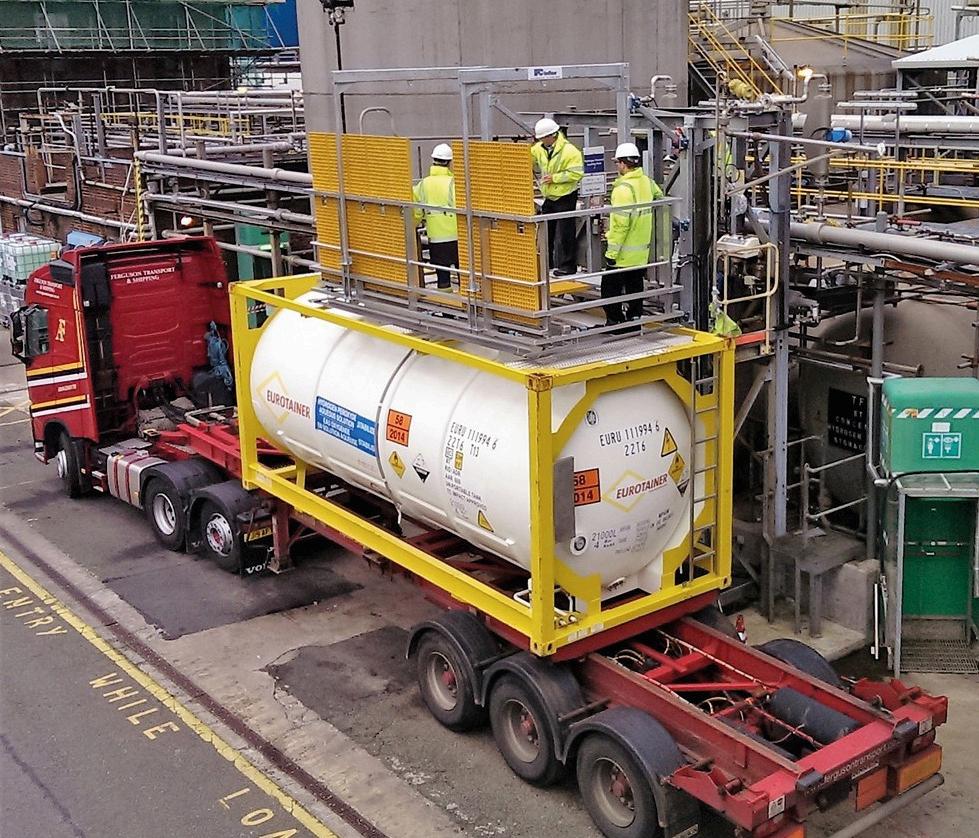
dealing with working at height as well as ITCO’s work in this area, which saw the publication in 2006 of a protocol developed in collaboration with the UK Health & Safety Executive (HSE), and ECTA’s own best practice guidelines, published in 2012, which were developed along with the European Chemical Industry Council (Cefic) and the European Association of Chemical Distributors (Fecc).
De Jong gave his own opinion on risk. “If you accept risk, you accept liability,” he said. He urged those in the audience to put 95 per cent of their risk reduction efforts into preventing incidents, and only 5 per cent into limiting liability. After all, if incidents are prevented there is no liability.
There is a hierarchy of control when it comes to working at height. Firstly: don’t do it! Systems and arrangements can be changed – think of the move towards bottom loading for road tankers, which means drivers and terminal personnel no longer have to access the tops of trailers. If personnel really have to access tank tops, make sure there is a fixed or mobile gantry with fencing on all sides so that there is no way for them to fall off.
The use of fall arrest systems, such as harnesses and cables, is a last resort, de Jong said. These can cause injuries when they come into play and are not a failsafe solution. If personnel are presented with a gantry with only a side rail, or with no protection at all, they should stop work, he stressed, and sites that offer limited or no protection are the real problem.
Some sites do not want to spend the money to provide proper protection, and some think they can avoid liability by moving operations outside the gate; some sites look to the LSP to solve their problem or fail to act on accidents and near-misses. But their customers can be just as culpable, perhaps fearing a loss of business if they make too much fuss.
De Jong urged attendees to be firm on working at height; they should report any unsafe practices and establish links with their local occupational health and safety inspectors. A manual and procedures should be in place so that their personnel do not feel they have to accede to requests for unsafe working when they are a site, and a whistleblower procedure should make them feel able to report such events.
The final presentation came from Graham Wood, director of Davlis ISO Containers, who addressed the issue of leaks from tank containers. This is sometimes due to over-filling or over-pressure in the tank, but most often results from leaks from valves (actually usually from valve flanges). This can be due to damaged seals or valve seats, damage to the valve or the use of poor quality valves; there is also a growing market for third-party gaskets, which may not be as good as those from reputable suppliers.
Wood urged the audience not to be taken in by the chance of saving a little on cheaper equipment, when a failure and leak can cost thousands. He advised providing depots with a list of approved valve manufacturers and gasket suppliers and said that unannounced visits to depots is the only way to ensure they are following these instructions.
The Amsterdam event also featured meetings of ITCO’s various divisions and technical reports; these sessions were not open to the press, although documents are available on the ITCO website, https://international-tank-container.org.
ITCO’s next regional meeting is scheduled to take place on 27 November in Shanghai. Full information can be found on the ITCO website.
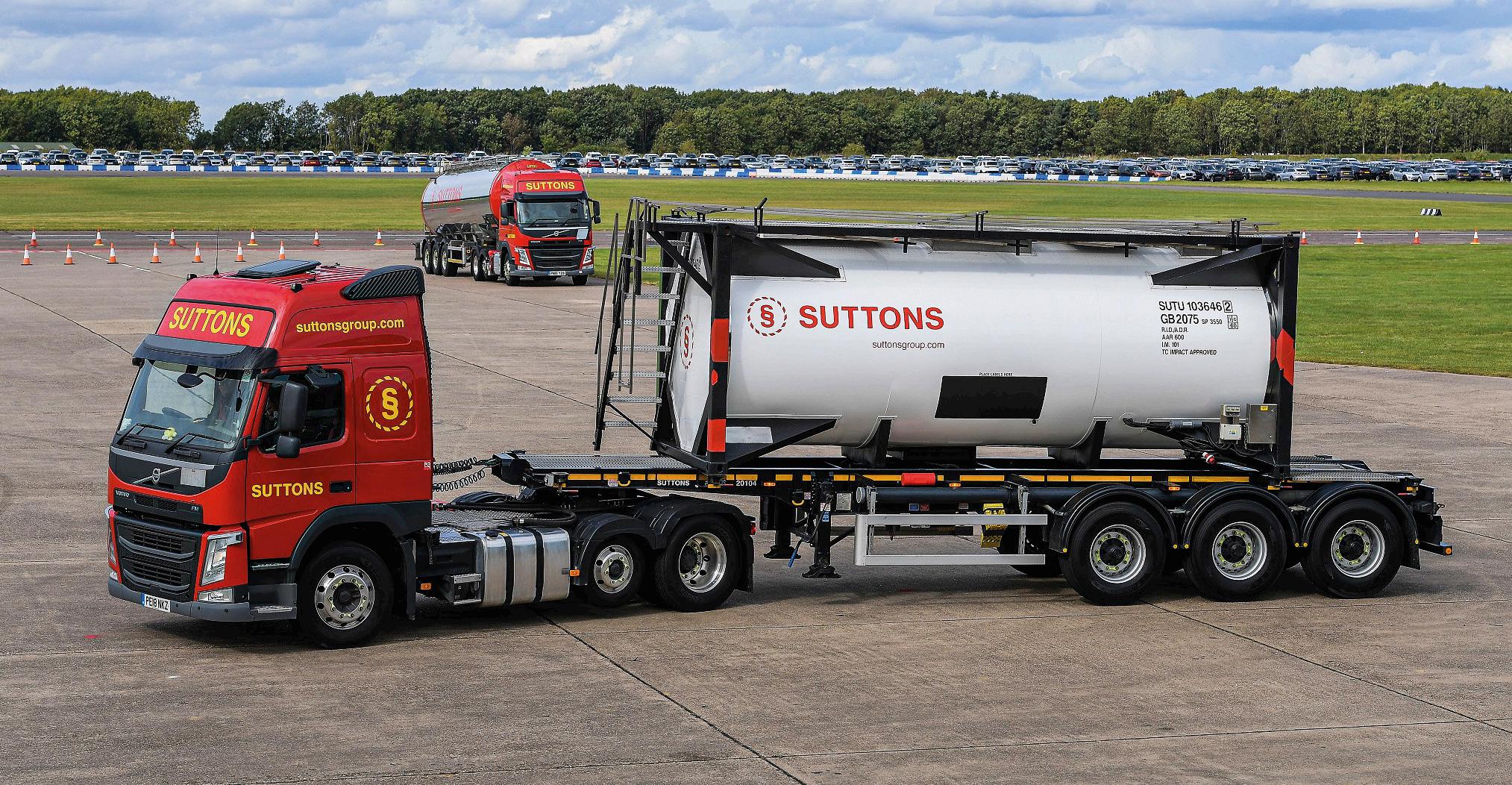