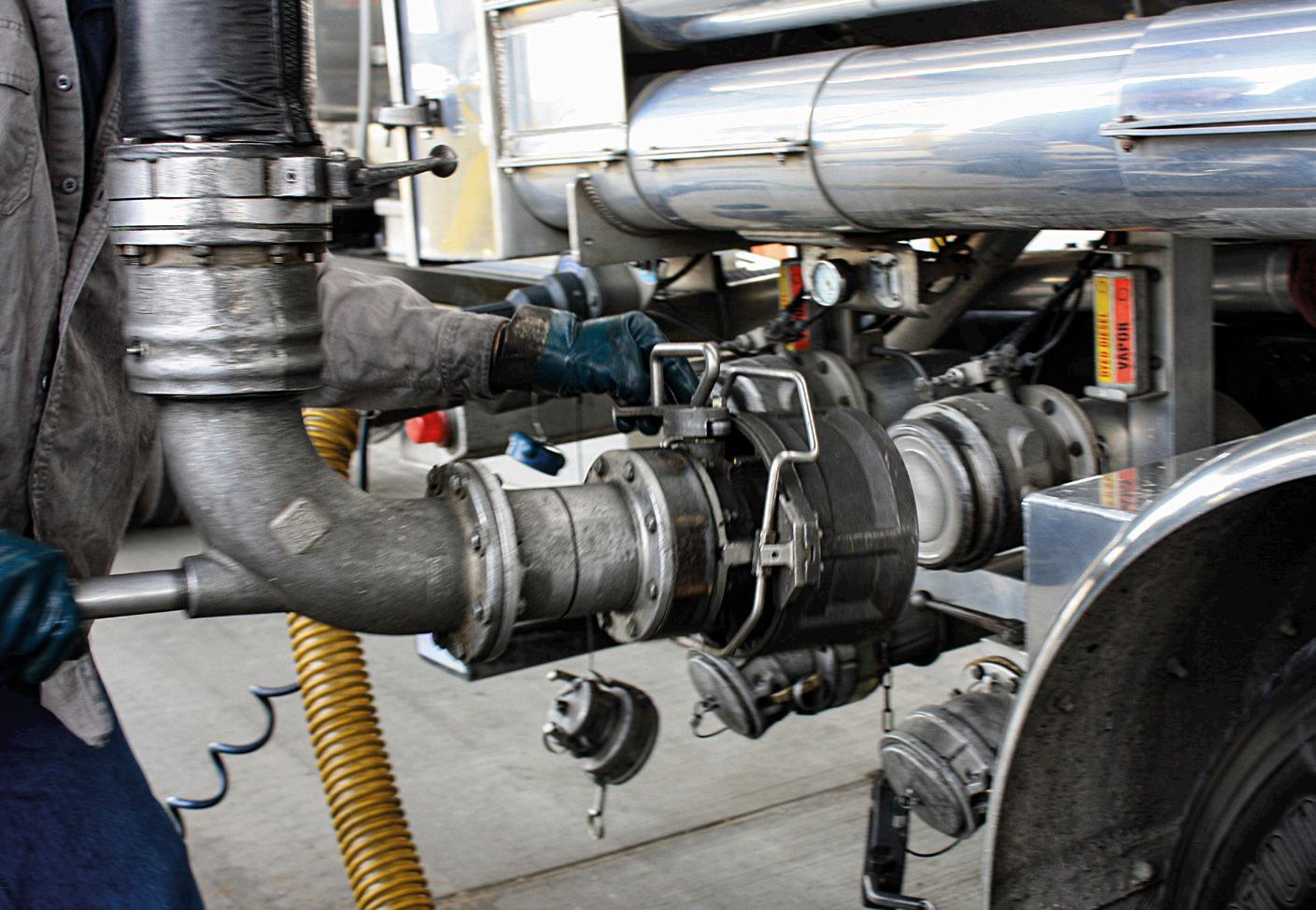
2 minute read
The importance of API couplers
MISSED CONNECTIONS
COUPLERS • FAILURE TO ENSURE API COUPLERS ARE MAINTAINED CORRECTLY CAN LEAD TO DIMINISHED EFFICIENCY AND HEALTH HAZARDS IN DAILY TERMINAL OPERATIONS, OPW SAYS
THERE ARE FEW things more disconcerting than discovering a leak when working in a terminal. Leaks lead to heightened safety problems and can cost a small fortune through lost product and downtime required for repairs, so reducing the chances of them occurring in the first place is priceless.
Fortunately, OPW Engineered Systems, a manufacturer of loading arms, swivel joints, process products and quick- and dry-disconnect fittings, has compiled a selection of key questions to answer that can help determine the cause of leaks.
API COUPLERS FACE A LOT OF HARD WORK AND NEED
TO BE INSPECTED REGULARLY TO AVOID LEAKS Additionally, should a more detailed approach be required to discover the cause of a leak, informative videos can be found through OPW’s website.
EXAMINING EVIDENCE API couplers are used more frequently than most pieces of hardware in terminals, meaning coupler care is pivotal to ensuring optimised terminal operations. It is common for couplers to have more than 50 ‘head-on’ collisions and connections with truck adaptors every single day. This eventually adds up and can equate to damaged equipment or safety failures. Even with modern load heads and improved pieces of kit, there are some key questions that need to be asked to provide the smoothest operations.
Firstly, is the coupler leaking? If so, this is a key scenario that requires monitoring. If it’s the case that the coupler leaks while connected to a truck, it could indicate seal wear – specifically related to the nose seal – to the primary seal between the truck and coupler. Loading arm adjustment could also contribute to a minor leak. Ideally, loading arms should be balanced at the truck adaptor height. A major leak might indicate a weak or broken wave spring. Wave springs provide seal compression when connected to the truck adaptor. If this is the case, operators would have to take the coupler out of service for inspection or completely replacing the wave spring.
Is the coupler leaking when parked? Minor leaking while parked could also be due to seal wear, but it may signify greater problems. Thermal expansion is known to affect API couplers if thermal reliefs are not in place and functioning fully. This then pushes the couplers to much higher pressures than their optimal operating ratings. It is possible that couplers could experience more than 34 bar during extreme thermal expansion. This can cause significant seal damage and potentially catastrophic failure. Even small issues, such as difficult to open and close handles, can be a sign of thermal damage.
Temperature, specifically cold weather, can be the culprit behind many leaks. Regardless of temperature, any terminal must keep flowing. Even though modern seals are reliable in temperatures down to -18°C, operators may need additional protection. Special cold-weather seals designed for extreme cold can keep couplers in operation well below zero. If couplers are leaking in cold weather, verify the seal material and consider a lower temperature option.
Finally, are there troubles connecting to the truck adaptor? If so, thoroughly check the latches and cams of the couplers in question. These areas are very prone to dirt and debris build-up, frequently causing cams to face difficulties, especially in winter months.
It cannot be overstated just how important regular inspections of couplers and connections in terminals are in being able to provide the most efficient, safe and effective facility. www.opw-es.com