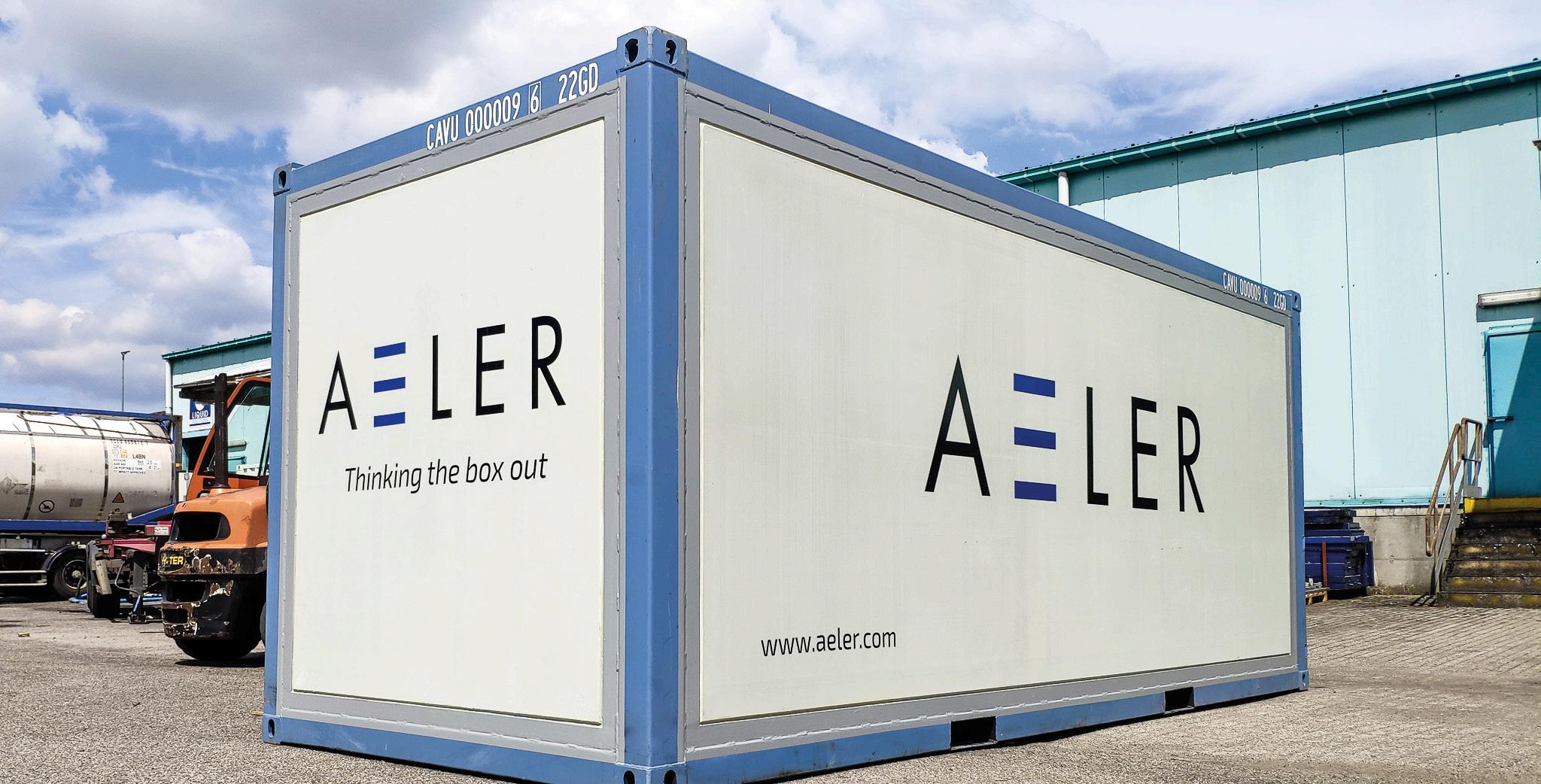
3 minute read
Aeler offers new container concept
OUTSIDE THE BOX
CONTAINERS • SPECIALISED PRODUCTS DEMAND SPECIALISED TRANSPORT SOLUTIONS. AELER HAS DEVELOPED AN INNOVATIVE CONCEPT FOR INSULATED, SMART CONTAINERS
BUILD A BETTER mouse trap and the world will beat a path to your door, or so it’s said. There is nothing in this world that cannot be improved and aim is now being taken on the metal freight container, a concept that is some 60 years old. Switzerland-based Aeler, a technology-driven company designing hardware and software to meet fundamental logistics needs, is creating a smart and lighter container that, it says, promises to transform global logistics operations.
To find out more about this revolutionary concept, HCB spoke to Naïk Londono, Aeler’s co-founder and CEO. HCB: Tell us more about Aeler. When was it founded? Who was involved? What skills and expertise does the company bring to the market?
NL: Aeler is a Swiss technology company developing hardware and software to solve what we see as the most important logistics challenges: efficiency, visibility and sustainability. We founded the company in 2018 but the technologies used in our solutions are the result of decades of research and development. We bring three types of technologies to the market: - The use of composite materials to build better containers - Advanced embedded electronics to make containers as intelligent as they should be in the 21st century - Data analytics and machine learning to enable our customers to reach supply chain excellence using the new wealth of data that is available about their supply chain. Our lighthouse solution is a new-generation 20-foot shipping container that enables efficient and safe transportation. There are two segments that highly benefit from our innovations: - Flexitank transport, where we can enable higher payloads without any container bulging, prevent leakages outside of the container and provide insulation to protect cargo - Sensitive goods transport, where our high-grade insulation maintains cargo quality and, coupled with our 24/7 cargo monitoring, ensures cargo safety and the identification of any deviation harming cargo quality.
HCB: Do you see chemical shippers and their logistics partners becoming more accepting of digitised solutions? Is there confidence in cloud-based platforms?
NL: We see digitisation playing an important role for chemical shippers in order to keep up with an increasingly challenging array of demands and expectations from customers.
AELER’S LIGHTWEIGHT CONTAINER DESIGN WILL
With new solutions offering simplified integrations and adapting themselves conveniently to legacy system, making the move to newer technologies is easier than ever and many have benefitted from becoming early adopters.
What we feel is still lacking is a good quantification of the potential benefits from visibility and digitised operations, therefore reducing interest and good measures of success.
HCB: Has the Coronavirus pandemic accelerated the pace of take-up of your services?
NL: At our current state, the Covid situation has not had such a great impact on the adoption of and interest in Aeler’s solutions. What has happened is that customers are more aware than before of the importance of good supply chain visibility and, interestingly enough, the Covid situation has brought sustainability more to the forefront.
HCB: What developments do you have in the planning stage to take things forward?
NL: Beyond our current 20-foot container, we are planning a 40-foot HQ version to meet the demand we’re receiving for affordable premium services in regards to insulation, security and visibility.
We will also extend our network to incorporate more depots around the world to facilitate our one-way container usage service and add capacity to satisfy the service needs of even our most demanding customers.
HCB: Can you illustrate this with a case study?
NL: A shipper moving FMCG precursors through flexitanks that need to be heated before unloading. The use case here is not only to load 28 tonnes of cargo versus their usual 24-tonne loads, but to ensure the cargo temperature does not fall too much after loading during the winter, effectively reducing heating time significantly before unloading.
Not only does this shipper gain efficiency in payload, but reduces by days the necessary heating time, therefore reducing his costs and receiving his cargo earlier than using a traditional box.
Throughout the entire process, the shipper can measure the actual temperature of the cargo, further improving the efficiency of his unloading operations and gaining a new insight on cargo quality throughout transportation.
As with this case, insulation and monitoring are proving to be important added values for cargo that needs to remain within certain temperature ranges for quality reasons. www.aeler.com
