
12 minute read
SCPC reinvented for the modern world
REFRESHING THE COMMITTEE
EPCA’S SUPPLY CHAIN PROGRAMME COMMITTEE IS DEVELOPING TO MEET THE CHANGING NEEDS OF EUROPE’S PETROCHEMICAL INDUSTRY AND ITS LOGISTICS PARTNERS
EPCA is fortunate to have among its membership ranks a weight of industry expertise and knowledge. It draws on that pool of expertise in its committees, not least the Supply Chain Programme Committee (SCPC), which includes among its members senior representatives from both the petrochemical industry and from its logistics service partners.
Indeed, as the virtual EPCA Annual Meeting nears, those members of SCPC have been gathering online and continuing their discussion of the themes that will be addressed via the EPCA Community app and in webinars over the three days in early October. They have brought with them insights and experience that will help industry navigate the uncertain times ahead as the world – hopefully – moves into a postpandemic phase, albeit a world that will still need to face the pre-existing issues of volatility and economic difficulties, as well as the need to move forward into a greener way of operating.
Ahead of the EPCA Annual Meeting, HCB spoke to three members of SCPC to gauge how they and their companies are bringing their experience to bear on the issues of digitisation, sustainability and business resilience. None of these can be taken in isolation, though – there is a common theme running through them, not least the need for greater visibility along the supply chain and for a greater willingness to cooperate and share information, for the good of the industry as a whole and of the planet on which it depends.
Of course, the other issue that all have had to face up to is carrying on with business during the disruption generated by the Covid-19 pandemic and the lockdowns, social distancing measures and slump in demand that accompanied it. Has that interrupted the journey towards sustainability, or accelerated the adoption of technologies that will be able to help?
Jan Arnet, CEO of Bertschi Group, agrees that the disruption was major and sudden. As the pandemic gripped Europe, supply chains had to be quickly reorganised on a day-to-day basis – and without physical communication. “Operations had to be transferred online within a few days,” he says.
As an intermodal transport service provider, Bertschi also had some challenges to face early in the pandemic, not least ensuring the health and well-being of its drivers out on the road.
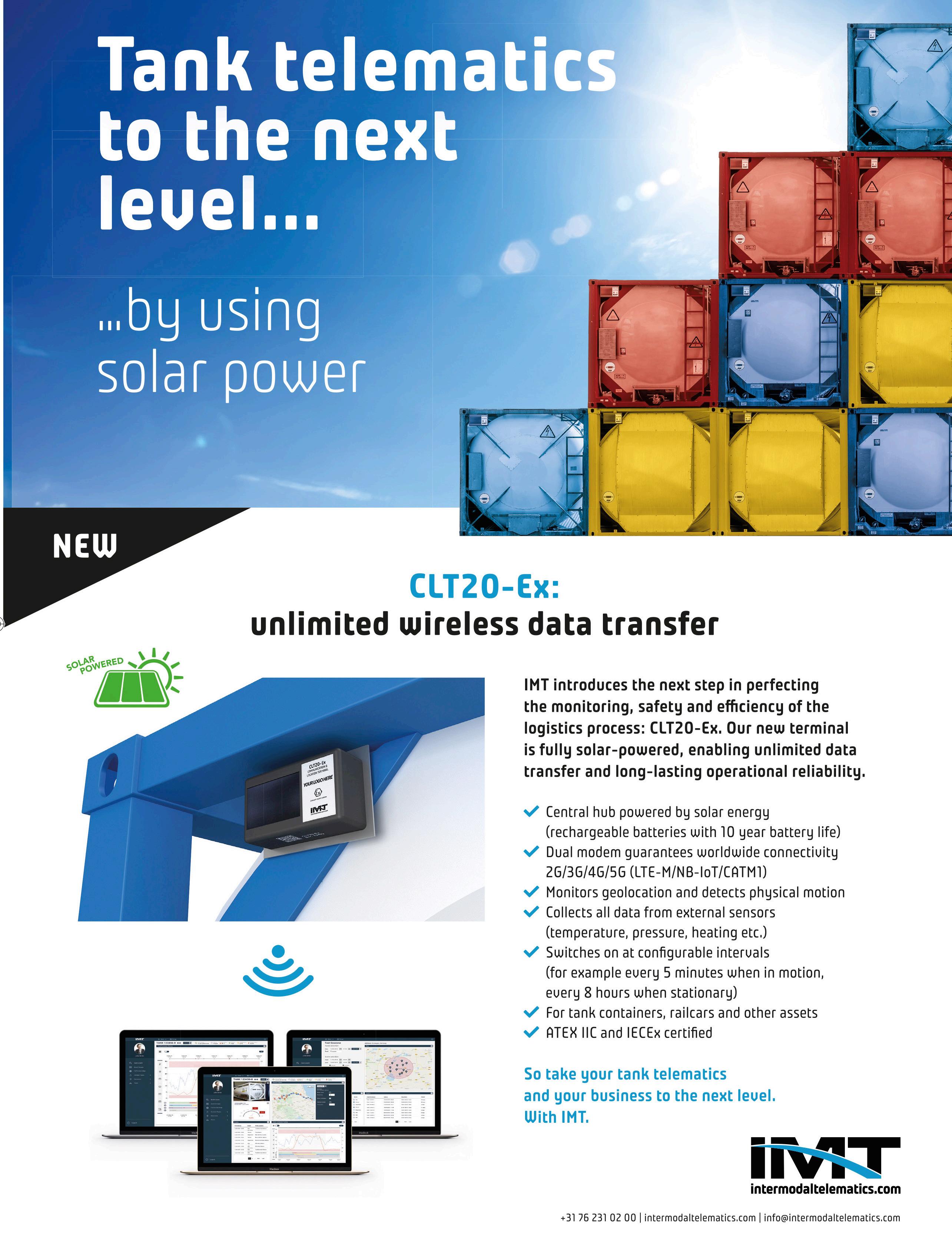


With counties imposing rapid and unexpected border closures, road transport became difficult but it was unclear at first how this would affect rail transport. Would rail terminals stay open? In response, Bertschi established emergency teams to organise operations and scaled up its Truck Tracer app; it also brought its planning online, which meant standardising processes and the elimination of manual input.
In effect, Arnet says, “the pandemic accelerated the process of digitisation. Changes that usually take years had to be made immediately.” Bertschi was already advanced on the digitisation journey but the pandemic removed any hesitancy among its own personnel and its customers. After all, those customers were also working from home and needed more visibility and appreciated receiving milestones and ETA in real time through their electronic connections. As a result, the new online processes have reduced the number of queries from customers and delivered productivity gains.
“We saved two years in the process of digitisation,” Arnet says. “It was a real eye-opener. External influences drove people to adopt new technology.” Interestingly,
Above left: Jan Arnet, Bertschi Group CEO Arnet reports, there was little resistance to the change, with older employees proving especially enthusiastic. This is not necessarily what we have been led to believe; yes, training was needed but Bertschi saw the opportunity and to use digitisation as a way of achieving business resilience.
Bulk liquids storage terminals may not be such a labour-intensive business as intermodal transport but Guy Bessant, president of Stolthaven Terminals, reports similar changes, saying: “Covid-19 showed that a good IT system and digitisation made us better able to respond to rapidly changing conditions.” It has also provided justification to continue to invest in digitisation.
But again, on a practical level, the pandemic moved people out of the office and the company had to take care of them. As a business, Bessant says, Stolthaven had to keep running, not least as it operates critical infrastructure, but it could not expose its people to risk.
How can a company manage those risks? “The business is involved in handling products that need to be carefully managed and handled with risk mitigation a key focus to ensure we can operate safely,” Bessant explains. “Covid-19 is just another risk to be mitigated.” Physical barriers were put in place to ensure social distancing but that was not something that Stolthaven had planned for.
Bessant says that, as a business leader, the pandemic has brought him closer to the business; he has had to reach out to his people in different ways and this has not been all negative. Now the focus is on getting people safely back into the office as, he says, “physical interaction is critical”. Overall, though, the lockdown has changed attitudes, especially to working from home, and technology has proven itself. He adds that the need for visibility – especially real-time information – during the pandemic has led to a realisation on the part of some companies that digitisation is sufficiently important to warrant continued investment, even at a time when they are looking to conserve cash.
Bessant says the world “is not a happy place” right now – but it is not as bad as it could have been. But, he notes, businesses have partially shifted their focus away from a number of sustainability and digitisation initiatives: “it’s all about saving cash at the moment”.
On the other hand, as has been well documented, the recession that has travelled with the pandemic has not affected the overall chemical industry as badly as some sectors; although there has been a sharp drop in demand for chemicals for use in the automotive and construction industries, other areas have helped compensate, not least in the field of hygiene and pharmaceuticals.
Those companies that are seriously looking to improve their sustainability efforts are certainly relying on technology and innovation to help them achieve their aims but it is not clear how much will actually get done, especially during the current crisis and the likely recession to follow. The EU is supporting green projects as part of its support for the industry, but questions remain as to how this will be financed. The Emissions Trading Scheme will likely be revised and may well involve a carbon tax on shipping; this could raise costs for the chemical industry and have other impacts.
Stolthaven has taken its own approach to innovation in its search for better sustainability in its terminal operations. Bessant notes that such innovation is usually found at the coal face: it is those who work directly with assets that often have the best ideas on how to do things more efficiently, a truth he observed first-hand at sister company Stolt Sea Farm. He also raises the point that sustainability is a broader topic than just the environment and has to include people – social injustice around the world is a coming issue and companies will have to take that on board.
Stolthaven Terminals has recently adopted the edison365 ideation and innovation platform to offer a way for its employees to put forward new ideas and to open up discussion across the company. Bessant says this is already generating information about issues that need addressing and a lot of little ideas are coming forward. The company will be able to use this for continuous improvement in its operations.
More radical innovation will be needed to address the coming energy transition and Bessant is challenging the entire organisation to come up with ideas. But beneath it all lies the power of digitised systems to crowd-source ideas and better communication tools, such as the recently installed Yammer.
That ability is also crucial at a time when many people are working at home. Jan Arnet is insistent that innovation shall not suffer but needs people to be working together actively and closely, whether working from home or on site.
But, Arnet believes, many of the processes that were changed to support Bertschi in handling business during the pandemic will not go away. “Having processes online is here to stay,” he says. “We are able to respond to changes even faster than before and it enables visibility and reliability in the supply chain.” That move online has redefined some work roles too, and Bertschi found that it had to assign tasks to those who had the best skills. Greater digitisation means, for instance, that the role of transport planners has changed as there is no longer any need to follow goods in transit – it is all done digitally and provided to customers in real time. But there is still a need to manage exceptions manually; this can make planners’ jobs more interesting and gets them closer to the customers, Arnet reports.
With 80 per cent of its people working from home, the dynamics of communication have changed completely. This worked well during the crisis but will it also work in the long term? This is something that has to be managed and, for a company with a global reach, it is something that Bertschi has already experienced; it needs to be a part of the corporate culture.
Digitisation is certainly playing a major part in that culture and helped Bertschi cope with the drastic changes in the market in the early days of the Covid-19 lockdown. Shifting product trades meant that transport assets had to be in the right place very quickly and its digitised systems helped with forward planning and with customer service. There is a lot of information in its own and in customers’ ERP systems and all players in the chain still need to learn how to use all that data. That is likely to become crucial in a post-pandemic world as shippers seek to reduce their working capital while still bolstering their resilience to sudden shocks, for example by supply chain diversification rather than single-sourcing. Visibility is now needed more than ever, Arnet says.
Ultimately, whether it is business resilience, greater sustainability and the need to reduce carbon emissions, or just for more efficient operations, digitisation will underpin developments moving forward. Anyone who has doubted EPCA’s focus on new technology in recent years must now see the logic.
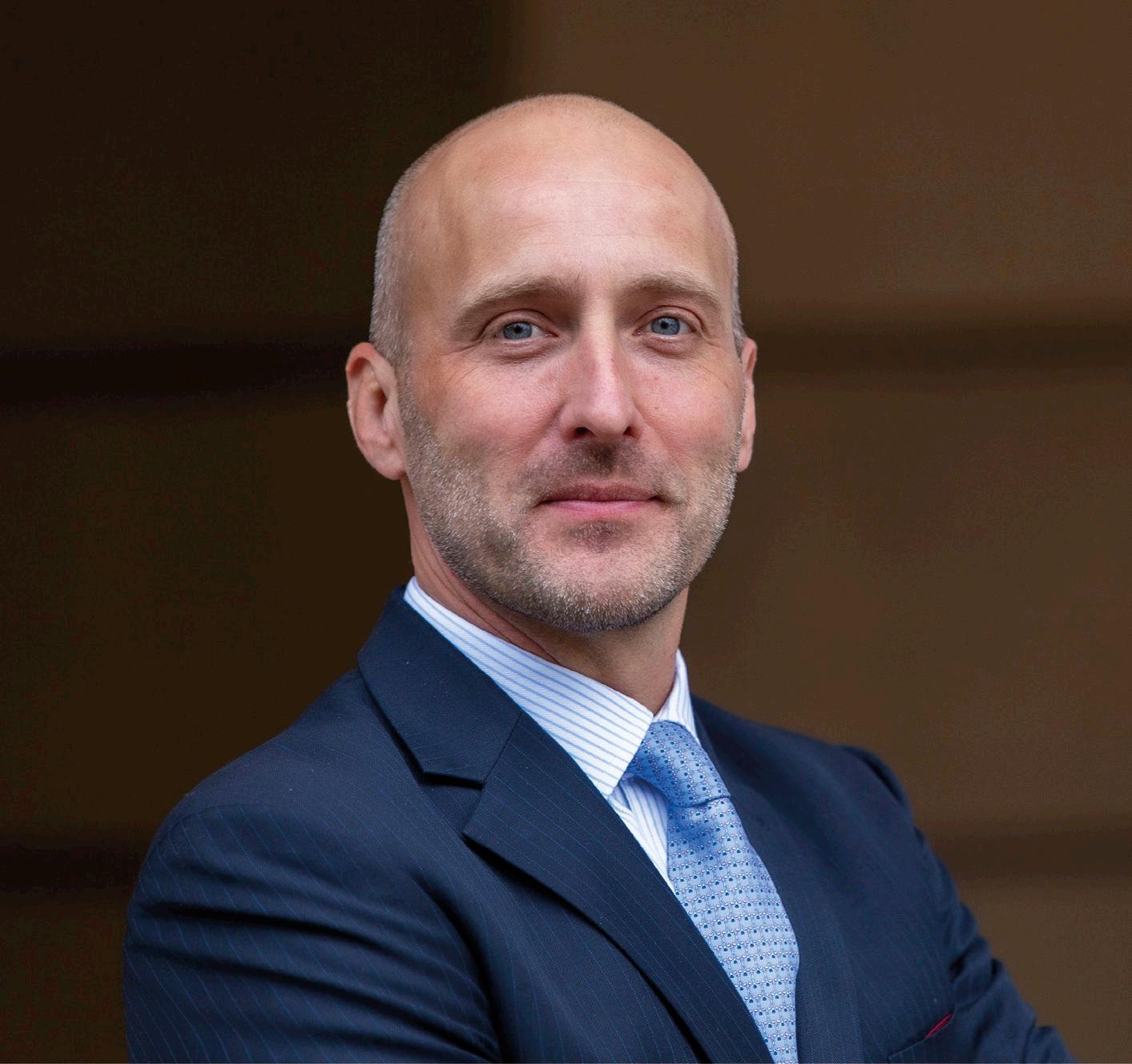
FACE OF THE FUTURE
This year, SCPC has been opened up further with the inclusion of Frederick Ronse, founder and CEO of Ovinto, in the group as it seeks to delve deeper into the possibilities that digital technologies can offer to help the petrochemical industry meet its aims and obligations to reduce its carbon footprint and move towards a sustainable and circular economy.
Ronse is unequivocal about the importance of digitisation: “How can you talk about supply chain efficiencies if you don’t know where your shipment is?” Not being connected causes inefficiencies and this is why digitisation is so important to the whole discussion of sustainability, climate change and the circular economy. Greater efficiencies in the supply chain mean more product is moved with less effort and with less impact on the environment. It’s good for the bottom line and good for the planet. Bessant agrees with that: “Sustainability and innovation are interlinked,” he says, but thinks the focus on innovation – and the willingness to spend money – has been weakened by the pandemic.
It is clear that digitisation represents a trend whose time has well and truly come, whether it is to contribute to business resilience during a time of unprecedented and rapid change or to help industry meet the growing need for sustainability in all its operations. There are a lot of new technologies out there that have already been used in other industrial sectors and, although there has been a lot of talk at previous EPCA events, there is also a need for some clarity and organisation if the petrochemical industry and its logistics partners are to benefit.
That is one reason behind the arrival of Frederick Ronse in SCPC and he has plenty of ideas about how to take the conversation forward. After a three-year digital journey within the petrochemical supply chain, which saw the active participation of the EPCA community in dedicated research and workshops, it is now time to get a broader view on digital trends and new technologies by bringing together experts from academia, from venture capital and from other industries, as well as trendwatchers and futurologists, in the Digital Advisory Body. “Let’s put those people together,” Ronse says. “Let’s scan the market for interesting new technologies that can help the petrochemical industry.”
Ronse sees it as vital to be open to different viewpoints, and not solely from Europe. He hopes SCPC will be able to invite every single company with interesting technology to present it through a showcase to the EPCA community. He explains: “I hope I can find a mechanism to optimise the search for new technology that will be of use to the European petrochemical industry.”
“There will be all sorts of things,” Ronse adds. “The broader we look the more we will find.” And he is not just talking about new technology but also new applications for old technology. Through that search, he says, “we can start to give answers to all EPCA members according to their needs and their place on the digital journey”. That will be particularly useful for smaller companies that perhaps lack the capability to develop their own roadmap to digitisation or to address sustainability and the circular economy.
Ronse concludes with a plea to the EPCA community: “Think of new technology that can help, bring it to EPCA – don’t wait to be told!”
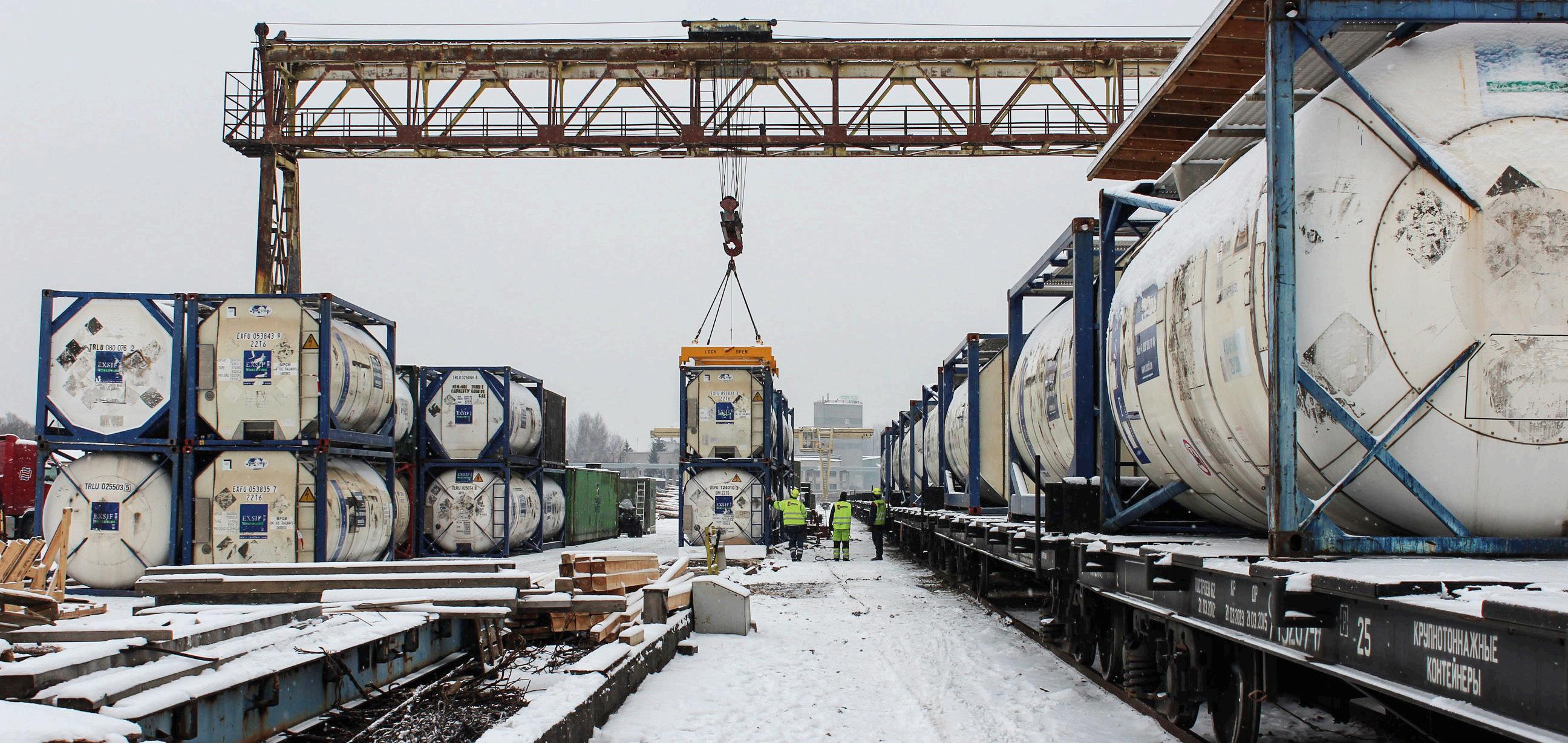
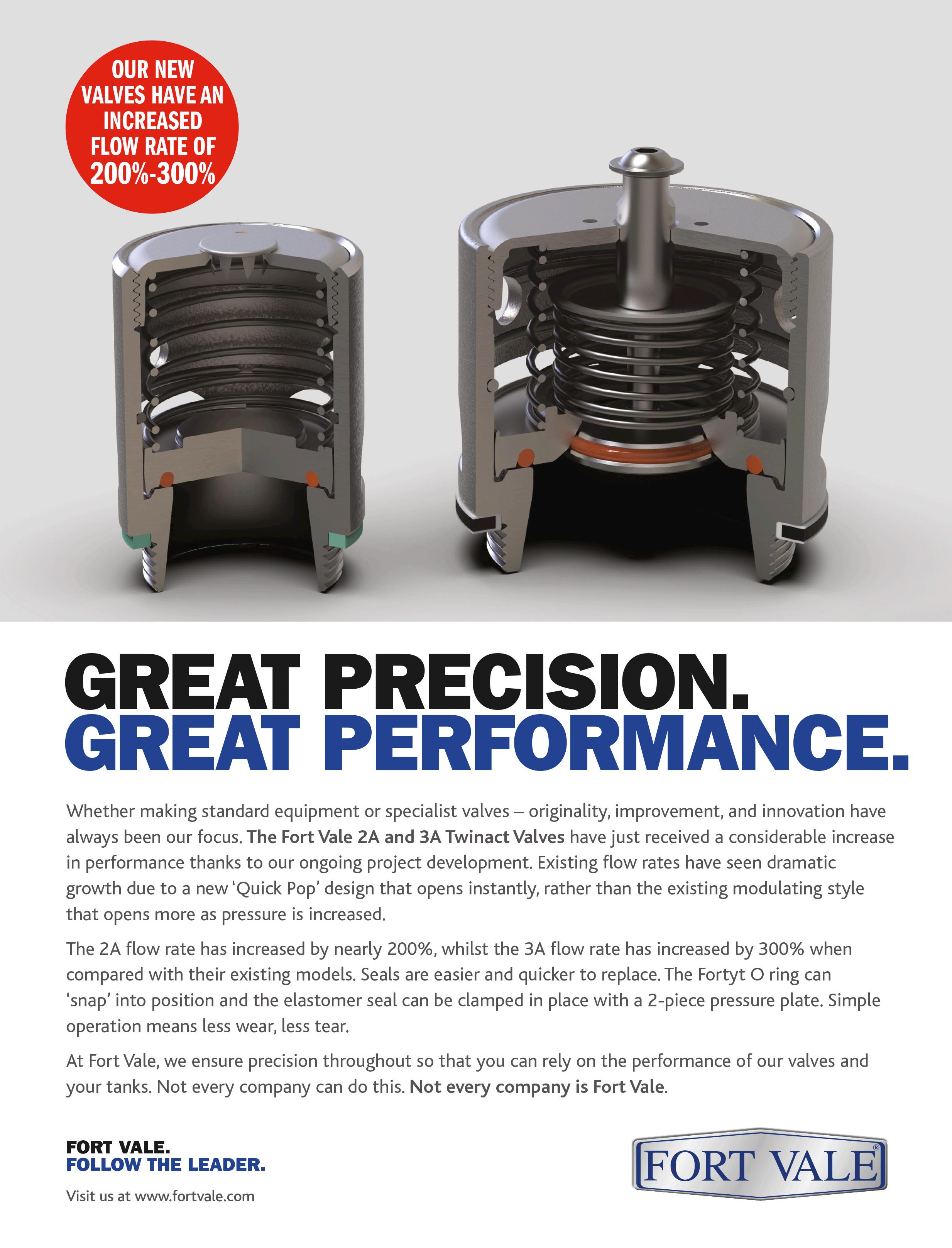
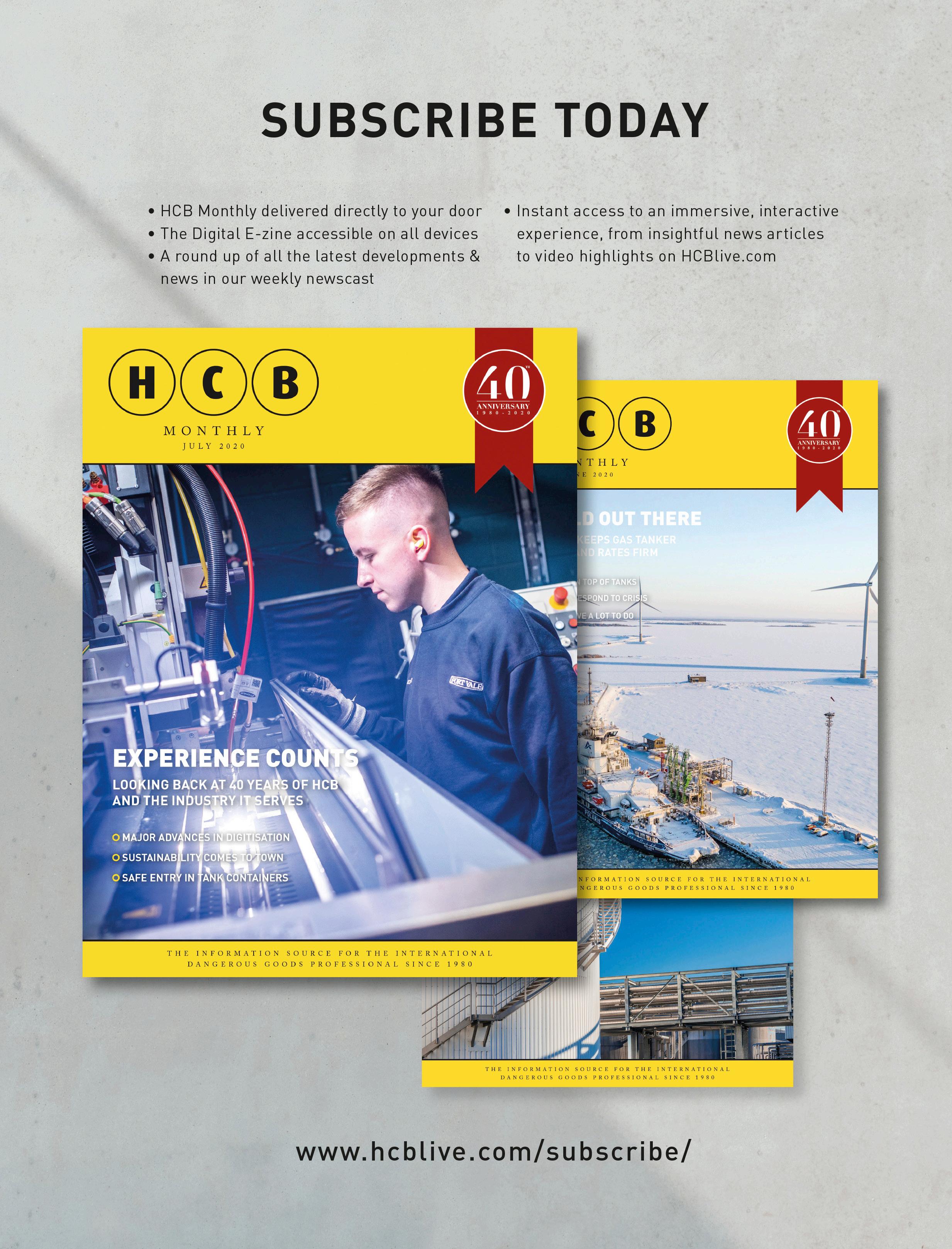