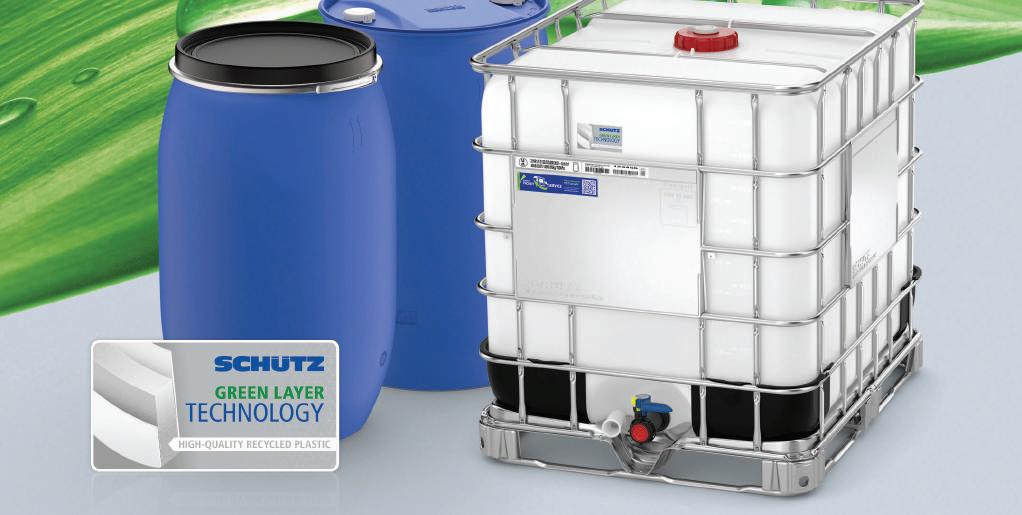
5 minute read
Schütz expands Green Layer line
from HCB-September 2022
LET’S GO ROUND AGAIN
IBC MANUFACTURING • SCHÜTZ HAS PLENTY OF EXPERTISE IN THE CIRCULAR ECONOMY BUT IS NOW AGGRESSIVELY EXPANDING ITS COLLECTION, RECONDITIONING AND RECYCLING CAPACITY
REDUCING CARBON DIOXIDE emissions is becoming an increasingly important consideration for the packaging industry. Through the European Green Deal and the Action Plan for the Circular Economy, the EU has defined the future framework conditions for resource-saving economic growth. One central measure is the use of plastic recyclate in packaging.
This is nothing new for manufacturers of industrial packaging. Indeed, Schütz – one of the pioneers in the field – is constantly increasing the recycled content of its packaging by using state-of-the-art, multilayer extrusion and continually developing its recycling processes.
The Green Layer series is the latest development in Schütz’s Green Lifecycle Management. With this programme, the packaging specialist supports customers in meeting their sustainability goals and further reducing the overall CO2 footprint of their packaging. The aim is to ensure the broadest possible and most cost-effective supply of eco-friendly packaging.
This can only be done if all partners along the supply chain collaborate in ensuring the return of used packagings so that Schütz has access to the volume of recyclate it needs. Schütz is not alone in having set up such a return system some years ago but this is a fine example of the packaging industry having led the way in what we now know as a ‘circular economy’. The Schütz Ticket Service allows the company to collect emptied industrial packagings anywhere in the world, reconditioning what it can and using the rest to as a source of recyclate, both according to the highest environmental and safety standards.
RIGHT FROM THE START The ability to re-use and recycle used packagings relies on smart design in the first place. Schütz says it has always focused on achieving maximum environmental friendliness in the entire lifecycle of its packaging, through smart product design, advanced production processes, long-lasting product quality and closed material cycles. Schütz has worked hard to reduce the weight of its packaging in recent years and continuously invests in state-of-theart production technology as well as in research and development.
For instance, Schütz Japan has recently opened a new production plant in Ako, to the west of Osaka in Hyogo prefecture, its second in the country. The new plant, covering some 30,000 m2, has a multi-layer extrusion blow-moulding line for the production of inner bottles for intermediate bulk containers (IBCs) and a highly automated assembly line. The site has space for expansion, with a reconditioning line already planned.
“The new production plant enables us to optimise the supply chains of our many customers in the region,” the company says. “Being geographically close to customers means shorter transport routes for the delivery of new IBCs and the collection of used containers through the Schütz Ticket System. By opening the new plant in Ako we are in an even better position to meet the needs and requirements of our customers.”
MAKING THE MOST The recycling process has also undergone development, allowing Schütz to now use even heavily contaminated material. It can recycle different grades of high-density polyethylene (HDPE) depending on the desired applications – both for packaging or components. In its factories in Europe, Schütz uses three- or six-layer extrusion blow moulding for the production of IBC inner bottles; this allows it to use recycled material for the middle layer, with virgin HDPE for the inner and outer layers, meaning that the filling product does not come into contact with recycled material. This makes for a 30 per cent reduction in the consumption of virgin HDPE, helping to meet the EU targets for CO2 emissions reduction.
This ‘Green Layer’ concept is used on both IBCs and plastics drums and, Schütz says, packagings produced in this way are identical in quality to its other product ranges. Most of the Green Layer containers, especially plastics drums, have UN approvals for use with dangerous goods.
Schütz is continually expanding its collection reconditioning network and recently added adding a state-of-the-art reconditioning facility at the Schütz Container Systems (SCS) production site in Fontana, California, making it the regional hub for IBC collection services on the west coast of the US.
The new equipment installed at the Fontana plant is in line with Schütz’s globally standardised specifications, based on the highest environmental, safety and quality management standards. Old inner bottles are removed and recycled for use in packaging components, while the cages are reconditioned and fitted with new inner bottles. Schütz says the resulting Recobulk IBCs are identical in terms of safety and quality to new Ecobulk units.
This year SCS is also investing in enlarging its Canadian plant at Belleville, Ontario, adding a high-tech reconditioning plant to further expand the North American collection network. The Belleville site was opened last year to meet demand from the growing industrial base in the area for IBCs and plastics drums. SCS also expanded its site in Perrysburgh, Ohio last year, with four new blow-moulders and a six-layer line for the production of IBCs with an EVOH permeation barrier.
OUT ON THE ROAD The Green Layer series will be on show later this month at the FackPack exhibition in Nuremberg, Germany and at the Scanpack show in Gothenburg in early October. Alongside those products, Schütz will also present the Ecobulk MX 560, an IBC specially designed for smaller filling volumes. It has a nominal volume of 560 litres and was developed on the basis of the globally successful 1,200 x 1,000 mm pallet. The compact dimensions of the container mean that storage and transport space can be optimally utilised. The Ecobulk MX 560 is the ideal solution for mixed loads, as the IBC is fully compatible with all other MX IBC variants from Schütz thanks to its pallet size. Its low tare weight makes it easy to handle in daily use. If required, the Ecobulk MX 560 can also be equipped with an EVOH permeation barrier, which protects the filling product from changes and the environment from pollution. SCS expanded its plant at St Joseph, Missouri last year specifically to produce MX 560 units.
Also on display at FachPack will be the Exobulk SX-D, developed specifically for use with flammable or highly combustible liquids and other demanding products. The IBC has already received the quality seal of the FM Global Group, underscoring its performance as safe packaging for sensitive goods.
Thanks to its special design and features, the Ecobulk SX-D meets the highest safety standards. For example, it has a closed, fire-resistant hull in addition to the classic steel grid. This hull is welded to the integrated bottom plate, forming a separate sealed containment basin around the inner bottle of the container. The double-wall construction provides effective additional protection against leakage and stops sensitive liquids from escaping, even in extreme situations, for example in the event of a fire with very high temperatures. www.schuetz.net
WHILE MAINTAINING ITS FOCUS ON SUSTAINABILITY, SCHÜTZ CONTINUES TO DEVELOP ITS IBC PORTFOLIO
WITH PRODUCTS DESIGNED TO MEET THE PARTICULAR
NEEDS OF INDUSTRIAL USERS
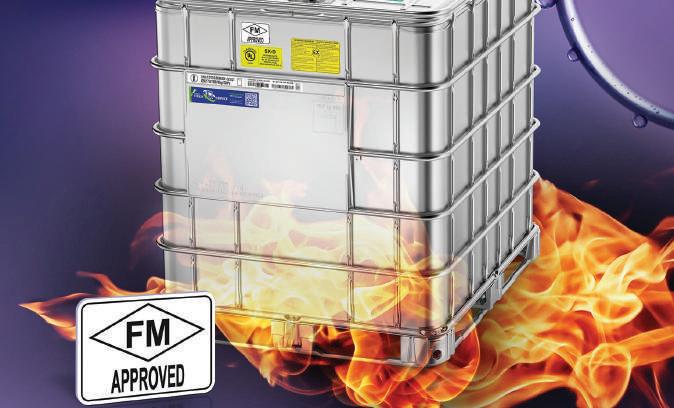