
10 minute read
What went wrong with Stolt Groenland
HEAT TREATMENT
INCIDENT REPORT • MAIB’S INVESTIGATION OF THE STOLT GROENLAND EXPLOSION HIGHLIGHTS THE NEED TO PROPERLY MONITOR INHIBITED CARGOES CARRIED IN BULK
A FAILURE TO appreciate the extent of heat transfer between cargo tanks, together with a lack of temperature monitoring in cargo tanks with styrene monomer, were the main causes of the catastrophic loss of containment on the chemical tanker Stolt Groenland in the port of Ulsan, South Korea on 28 September 2019, according to the report of the investigation carried out by the UK Marine Accident Investigation Branch (MAIB).
The immediate cause of the incident was not hard to establish: a runaway polymerisation in a cargo tank with styrene led to an overpressurisation of that tank, causing a rupture that allowed vapour to escape; this vapour found an ignition source, causing a fireball that reached the road bridge above the jetty. Two crew suffered minor injuries and 15 emergency responders were injured during firefighting efforts that lasted for more than six hours.
MAIB determined that the polymerisation was initiated by elevated temperatures in the tank, caused by heat transfer from other chemical cargoes, reducing the effectiveness of the inhibitor added to the styrene. “Athough the styrene monomer had not been stowed directly adjacent to heated cargo, the potential for heat transfer through intermediate tanks was not fully appreciated or assessed,” MAIB’s report says. “Critical temperature limits had been reached before the vessel berthed under the road bridge in Ulsan. The tanker’s crew did not monitor the temperature of the styrene monomer during the voyage, and therefore were not aware of the increasingly dangerous situation.”
AS IT UNFOLDED At the time of the incident, while Stolt Groenland (43,500 dwt, built 2009) was moored at the jetty to unload cargo, the smaller chemical tanker Bow Dalian (9,150 dwt, 2012) was moored outboard to receive cargo by ship-to-ship transfer and was already receiving nitrogen from shoreside vehicles for purging its tanks. Stolt Groenland had loaded 20 different chemical cargoes from terminals in Texas, including four tanks of hexamethylenediamene (HMD) and two of diglyceryl ether of bisphenol-A, both of which required heating during the passage to Asia. Four tanks had been discharged to barges while the tanker was anchored off Kobe; it then proceeded to Ulsan where it discharged six tanks of adiponitrile at the Odfjell terminal before moving to the Yeompo Quay. There two tanks with Voranol were discharged to Stolt Voyager by ship-to-ship transfer.
The first sign of a problem arrived with a release of vapour from the pressure/vacuum
relief valve on a cargo tank with styrene; two minutes later the tank’s high-level alarm sounded, which was noticed by the crew. While the crew were investigating, the high-high-level alarm sounded, indicating that the level of the tank had increased to 98 per cent. Within minutes, two explosions occurred in rapid succession in way of the vessel’s cargo manifold; the second of these ignited the styrene vapour released from the tank, causing the fireball. One crewman was blown over the guardrails.
The chief officer of Stolt Groenland activated the deck foam monitor system and directed the port monitor towards the cargo manifold; the master ordered all crew to the lifeboat station where they abandoned the tanker using the freefall lifeboat. Meanwhile, the chief oficer of Bow Dalian activated the deck foam fire extinguishing system, directing the monitors towards Stolt Groenland’s main deck and cargo manifolds. The crew abandoned ship by rope ladder onto Korea Coast Guard vessels that had arrived to assist.
MAIB investigators later found that there was a large hole in the main deck in way of the cargo tank that ruptured, and in its common bulkhead with the centre tank. There was fire damage in the manifold area and the midships deckhouse was burned out. There was also extensive internal fire damage in the accommodation block; heat and smoke had also got onto the bridge, damaging much of its equipment.
PRIOR EXPERIENCE MAIB was interested to note that another Stolt Tankers vessel, Stolt Focus (37,500 dwt, 2001) had experienced a similar polymerisation incident two weeks earlier, though without the dramatic outcome experienced by Stolt Groenland. Both ships had loaded the styrene, produced by Ineos Styrolutions, from the same tank at the LBC terminal in Houston; in both cases sufficient 4-tert-butylcatechol (TBC) inhibitor had been added to provide effective protection against polymerisation for between 60 and 90 days.
Stolt Focus had noted some increased temperature readings in its styrene tanks on arrival in Kobe; actions were taken to cool the cargo and contain the situation. Later, after further steady rises in temperature, it was decided to introduce sea water into the tanks to stop the reaction, although this increased viscosity, making the cargo unpumpable. It then proposed to dilute the cargo with benzine in international waters, also adding a shortstop inhibitor, phenothiazine, to stabilise the material and allow its discharge for incineration ashore.
MAIB asked Stolt Tankers for further information but, MAIB says, Stolt refused to provide it, as it did not consider the polymerisation aboard Stolt Focus as a marine accident or incident. MAIB was informed of another incident involving styrene monomer loaded in Houston, which was rejected on arrival in China as the cargo had a high concentration of polymer. During passage that cargo had also shown elevated temperatures but it had been cooled by running water on the deck. MAIB suspects that this reaction had been caused by the inadvertent introduction of nitrogen into the tank. MAIB also notes a number of runaway polymerisation incidents involving styrene in land-based accidents, saying that, while the causes varied, insufficient temperature monitoring was a common contributing factor.
HOTTER THAN IT SHOULD BE MAIB focused on the temperature of the styrene cargo, noting that the loading of the material had been performed correctly and that the application of the inhibitor, the cleanliness of the cargo tank, sampling and stowage location (away from heated tanks) were all in order. Nevertheless, the styrene monomer carried in the tank that ruptured had been heated to levels well above ambient temperatures during the voyage, at times exceeding 37˚C.
The styrene had been maintained at 13˚C in the shore tank in Houston; by the end of the loading process its temperature had risen to some 17˚C. At the time, the ambient temperature was about 30˚C, so cargoes loaded into tanks adjacent to the styrene would have been at or above that temperature and, MAIB says, it is likely that the temperature of the styrene would soon have reached a similar level, likely exceeding the 29.4˚C maximum specified on the certificate of inhibitor by the time the vessel departed Houston. Although this is unlikely to have been the single cause of the runaway polymerisation, the elevated temperature would have significantly increased the rate of TBC depletion and, therefore, the risk of polymerisation.
MAIB notes that the HMD cargoes were loaded at a temperature of 61˚C and maintained between 45˚C and 55˚C (despite a stated maximum carriage temperature of 50˚C). Heat transfer to adjacent tanks raised their temperatures to between 40˚C and 44˚C. It also says that the relatively low specific heat capacity of adiponitrile and styrene would have allowed the transfer of heat from the HMD cargo in the 9P cargo tank into the adiponitrile in 9C and thence to the styrene in 9S, the tank
THE FIRE BURNED FOR SIX HOURS, BADLY AFFECTING
THE DECK AND MIDSHIPS DECKHOUSE. HAD IT
HAPPENED AT SEA, THE CONSEQUENCES FOR THE CREW
that ruptured in Ulsan.
Any rise in temperature has a measurable effect on the inhibitor, which was added at loading at 17 ppm. According to indicative depletion rates provided by Plastics Europe, that TBC concentration would have dropped to its lower recommended limit of 10 ppm after 77 days at a temperature of 25˚C; at 30˚C it would take only 49 days, which was less than the planned voyage of 56 days. At 40˚C it would take only 10.5 days to reach the limit. MAIB tested samples from other styrene tanks on Stolt Groenland and found their TBC concentration to be between 7 and 8 ppm; it assumes that, as the temperature in 9S was at least 5˚C higher, its TBC concentration would have been substantially lower.
CONCLUSIONS AND RECOMMENDATIONS MAIB concludes that the explosion and fire, caused by a runaway polymerisation of the styrene monomer cargo in cargo tank 9S was initiated by the cargo’s elevated temperature for much of the voyage, resulting from the transfer of heat from the HMD cargo in tank 9P. It says that the precaution of not stowing the styrene cargo next to the heated HMD cargo was not sufficient to meet the segregation requirements in the International Code for the Construction and Equipment of Ships Carrying Dangerous Chemicals in Bulk (IBC Code) and the probability of this heat transfer was not fully considered during the planning and approval of the cargo stowage. Calculations to predict heat transfer were not conducted because they were complex and outside the capabilities of the ship operator and the vessel’s crew and also outside the scope of the cargo stowage software. While there were instructions on the stowage of inhibited cargoes, these did not cover in detail the possibility of heat transfer through adjacent or intermediate cargo tanks.
Further, despite it being a requirement in the ship’s Safety Management System (SMS), the temperature of the styrene cargo was not monitored and temperature alarms, although available, were not set. MAIB says the crew either did not notice or did not recognise the significance of elevated cargoes discharged prior to the event. The absence of temperature monitoring appeared to derive from the crew’s view that styrene is benign when inhibited, and that no previous problems had been experienced.
Although it did not contribute to the incident, the certificate of inhibitor contained actions to be taken in the event of a rise in temperature that were not viable. The crew had no means of testing for TBC concentration or the presence of polymers and no additional TBC was carried onboard. MAIB also remarks that the operator missed an opportunity to alert its tanker masters to the similar incident aboard Stolt Focus two weeks before.
Since the incident, Stolt Tankers has embarked on efforts to raise awareness of the hazards posed by inhibited cargoes and amended its procedures and requirements to address some of the issues raised by the investigation. It has also begun work with manufacturers and industry bodies to ensure that cargo handling instructions and protocols for inhibited cargoes are practical and achievable. It looked at the use of polymer testing equipment for use onboard its ships but determined that this is not viable with current technology.
Responding to the MAIB report, Stolt Tankers says: “Stolt Tankers has used the learnings from this regrettable accident to improve its procedures for handling inhibited cargoes. During 2020, we made several improvements in our stowage planning processes afloat and ashore, and in our practices relating to inhibitors, managing cargo alarms and reporting of cargo temperatures to shore staff. Our seafarers also receive additional training to increase their understanding and awareness of the importance of these changes. The MAIB report acknowledges that these actions have already been taken.”
MAIB has meanwhile issued a series of recommendations to the International Maritime Organisation (IMO), the Chemical Distribution Institute (CDI) and Plastics Europe to amend their relevant codes and guidance to reflect the lessons learned from the incident.
Meanwhile, Stolt Groenland remains afloat in Tongyeong, South Korea, with all cargo residues removed. The company is planning for repairs as it awaits approval from local authorities to tow the ship to China.
The MAIB incident report can be downloaded in full at www.gov.uk/maibreports/cargo-tank-explosion-and-fire-onchemical-tanker-stolt-groenland.
THE EXPLOSION THREATENED NEARBY TRAFFIC
AND INDUSTRIAL ACTIVITY
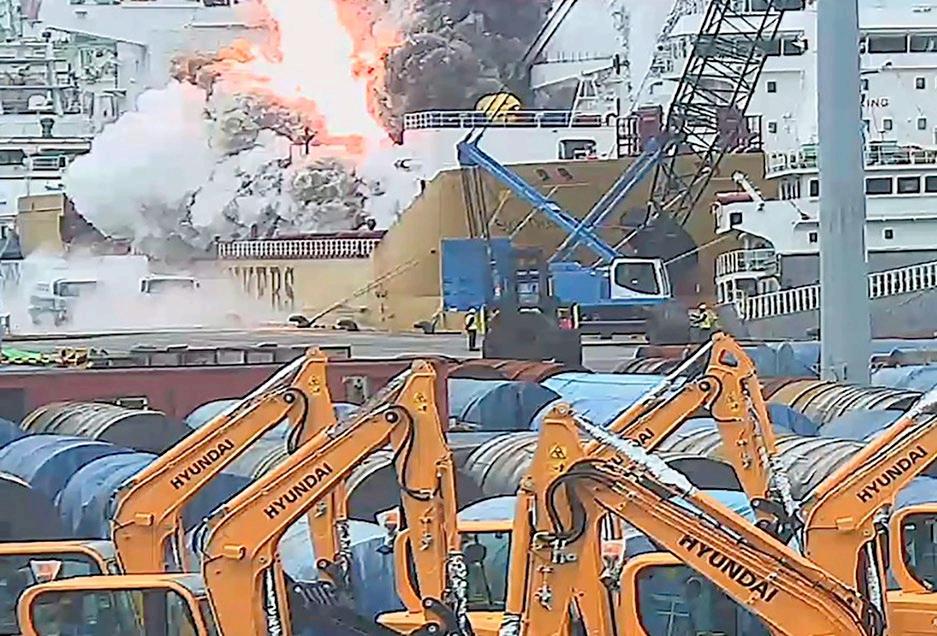