Comparison of Structural Foam Molding With Traditional Molding

When it comes to the manufacturing of plastic parts, there are two main molding methods, i.e. traditional molding and structural foam molding. However, since both the methods have their own advantages and disadvantages, it’s important to understand the differences between them so that you can choose the right method for your project. Ahead in this post, we’ll compare these two methods and discuss their pros and cons, as well as their costs.
Traditional Molding: It is an injection molding process, in which molten plastic is injected into a mold under high pressure. When the plastic cools and solidifies, the mold is opened to release the part. Traditional molding is widely used to produce small and simple to large and complex plastic parts for different industries.
Structural Foam Molding: On the other hand, it is also an injection molding process, in which a foaming agent is also added to the melted polymer when injecting it into a mold under low pressure. As a result, final parts have a cellular core and a solid skin, which makes it stronger and more lightweight than solid plastic parts. This method is primarily used to produce large and complex parts, such as automotive components, furniture and industrial equipment.
Differences Between Structural Foam Molding and Traditional Molding
There are four main differences between structural foam molding and traditional molding are:

A foaming agent or a chemical blowing agent is used in structural foam molding and hence, plastic parts built through this method have a cellular core and thick outer layers, while traditional molding produces entirely solid parts.
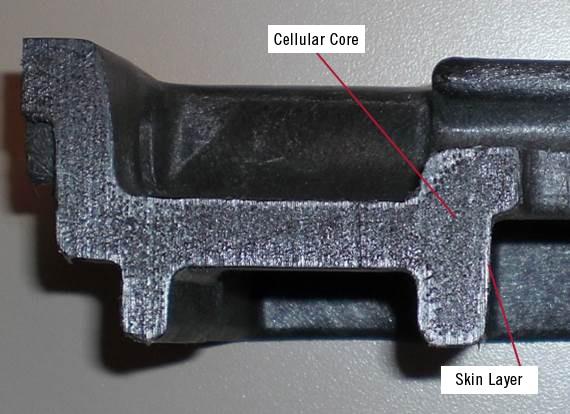
Low pressure is used in structural foam molding, while traditional molding is performed using high pressure.

The cycle time is longer in structural foam molding compared to traditional molding due to the foaming process.
Structural foam molding is more suitable for large and complex parts, while traditional molding can be used for a large variety of products.
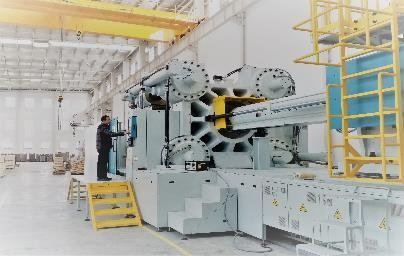
The advantages of structural foam molding are:

Lower material costs, as the foaming agent reduces the amount of plastic needed.
Stronger and more lightweight parts due to foam-like core and solid outer layers.
Reduced sink marks and warpage because low-pressure is used for the injection process.
Better impact resistance due to the cellular core.
Reduced part weight, which leads to lower shipping and handling costs.
Traditional Molding Advantages
The advantages of traditional molding are:
The high pressure allows faster cooling and solidification of the plastic parts, which eventually provides faster cycles.
More precise and detailed parts can be built because of the high pressure and precise control of the injection process.
Suitable for small and simple parts, as structural foam molding is less cost-effective for such parts.
You must choose between structural foam molding and traditional molding only after considering the following factors:

Part Size and Complexity
Structural foam molding is suitable for large and complex parts, while traditional molding can be used for a wider range of sizes and complexities.
Material and Performance Requirements
If strength and weight are important, structural foam molding may be the better choice, while traditional molding is more suitable for producing more precise and detailed parts.
Cost Considerations
Although structural foam molding requires less material, it comes with a longer cycle time, which can affect the overall production cost.
How to Choose a Manufacturer for Your Molding Needs!
If you are looking for a reliable agency for your Structural Foam Molding or Traditional Molding needs, iMold USA, LLC will be the right choice. However, before making the final, it is advised to consider their experience, capabilities and quality standards.

So basically, you should opt for a manufacturer with the following qualities:
1. Experience with the specific molding method and industry requirements.
2. They must hold a range of capabilities, such as tooling, design and secondary operations.
3. A strong quality management system, such as ISO 9001 certification.
4. Competitive pricing and lead times.
5. Good communication and customer service.
With these qualities in your partner molding agency, you can rest assured that you’ll achieve optimal results.
For more information Visit at: https://www.china-casting.biz/structural-foam.html
Contact Us: iMold USA LLC
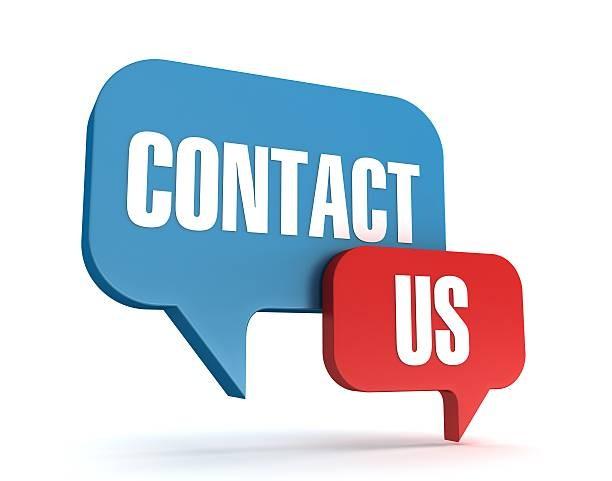

Address: 2220 Hillcrest Street Orlando, FL 32803
Phone: +1-407-9822797
Email: sales@china-casting.biz