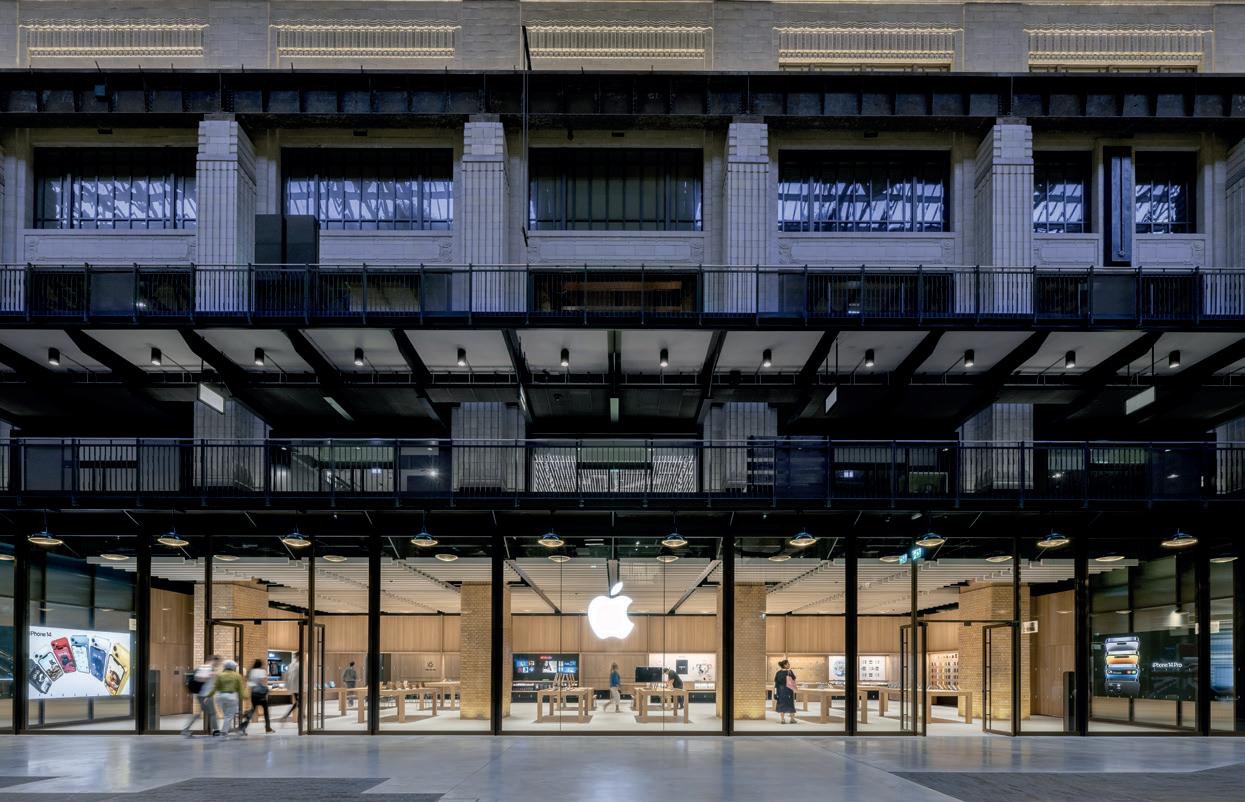
10 minute read
NEW MODULAR DESIGN APPROACH FOR APPLE BATTERSEA
Apple’s latest store, at the heart of Battersea Power Station’s Turbine Hall, has opened to the public. It is the first Apple store in Europe to integrate a new modular design approach that builds on Apple and Foster + Partners’ previous collaborative ventures and features inclusive, innovative and sustainable design enhancements.
Th e store opening ties in with the completion of Apple’s new London offices within Battersea Power Station. Foster + Partners’ design literally breathes new life into the heart of the erstwhile coalfired power station, transforming it into a 21st-century workspace that stimulates all of the senses.
Advertisement
Stefan Behling, Head of Studio at Foster + Partners, said: “This is a new design approach for more accessible neighbourhood stores, which serve the local community. Inherently flexible, easy to install, dismantle and reuse, the sustainable new system can be replicated in any location around the world. It is a great privilege to open the first European store of its kind in the iconic Battersea Power Station, a stone’s throw from our London studio.”
P refabricated solid timber avenues are an integral part of the new system. These modular spaces have been designed to accommodate themed avenue bays and counter-based services within a universal framework. The design includes an Apple Pickup station and re-introduces the Genius Bar, with a reimagined counter for face-to-face conversations during hands-on technical and hardware support. It also features a brandnew customer experience area, where visitors can try out devices or customise them to suit their needs. The system adopts an energyefficient displacement air strategy, which delivers conditioned air through the base of the avenues, creating a comfortable environment for staff and visitors. www.fosterandpartners.com
To extend the life of the store –without significant interventions –and reduce its carbon footprint, the new system can be easily modified, repaired and re-assembled to adapt to future needs. The system also makes reductions in petrochemical and carbon-intensive materials.

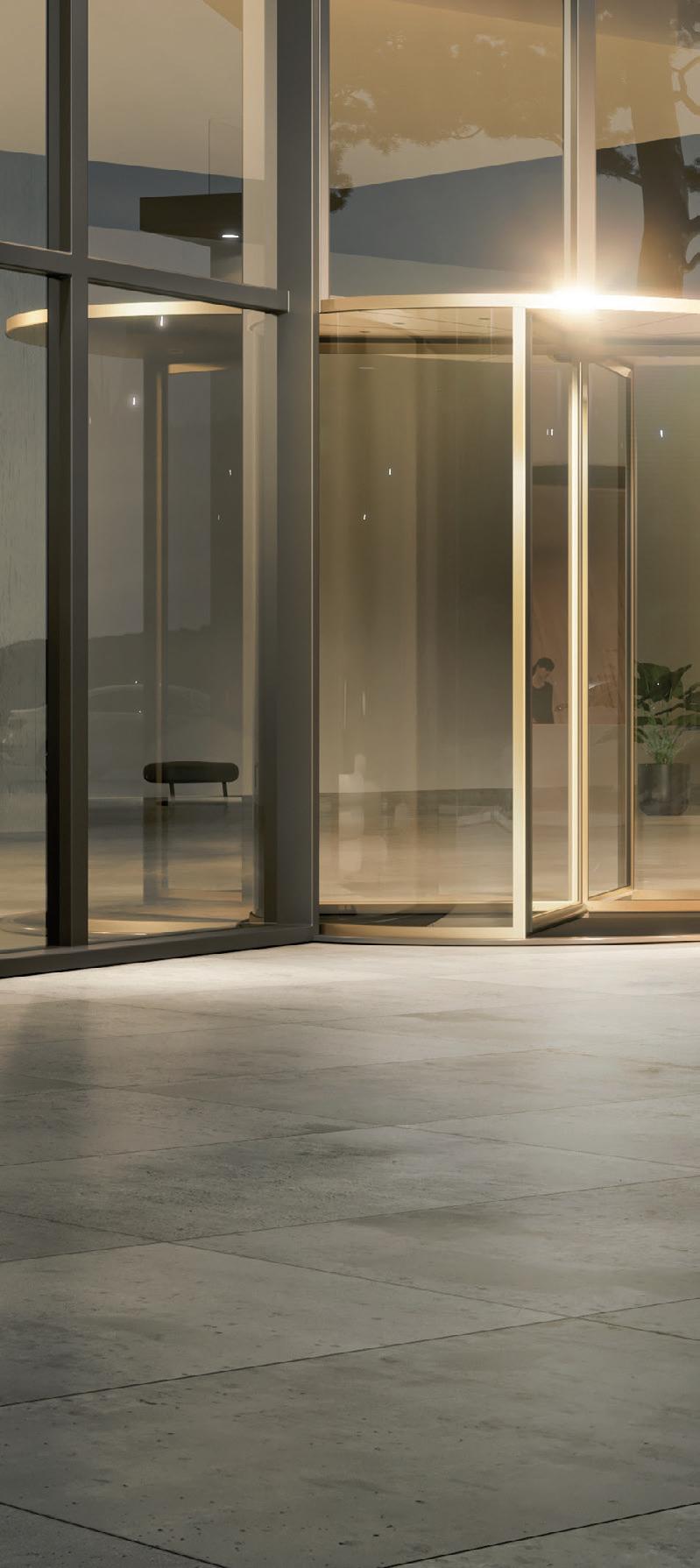
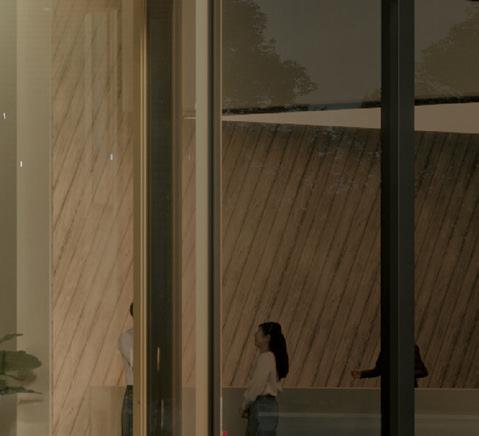
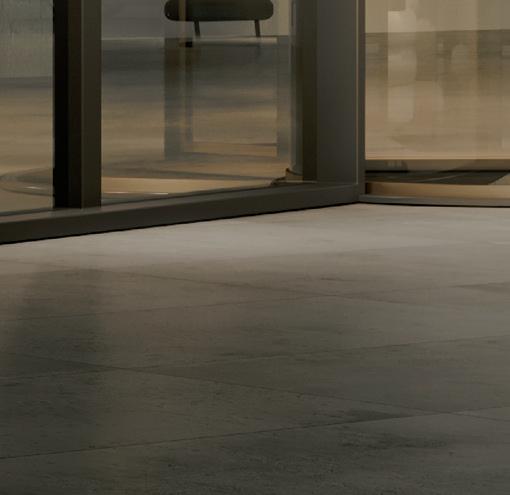
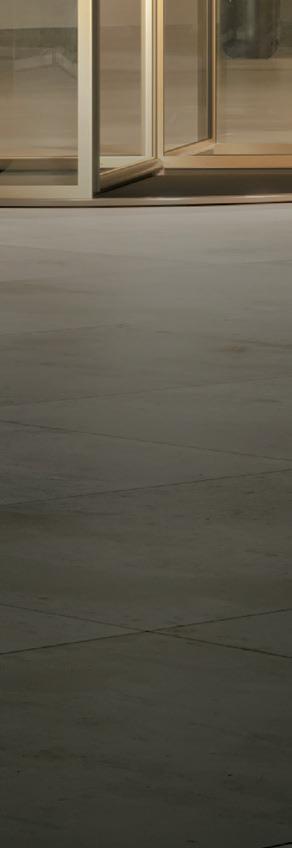
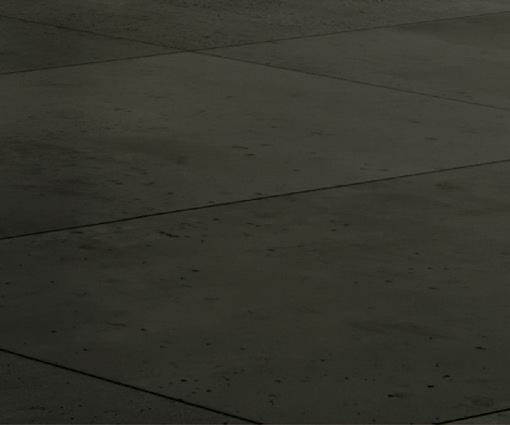
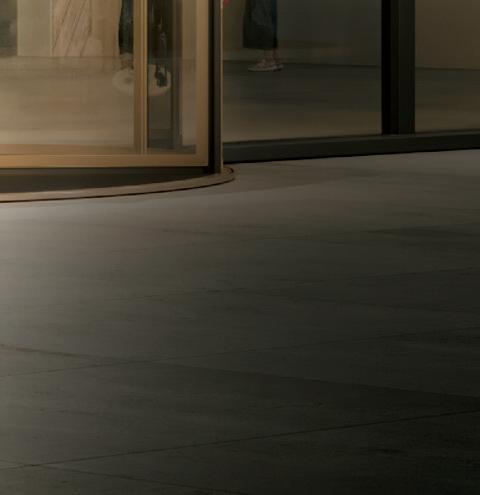
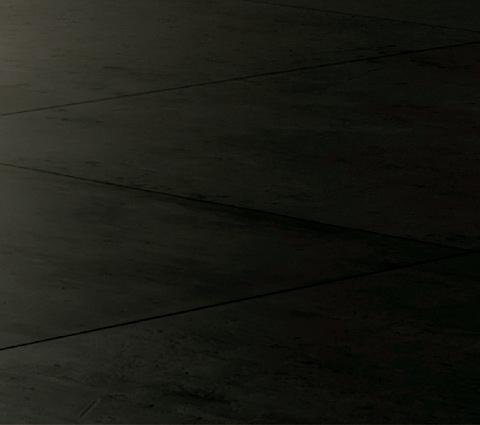
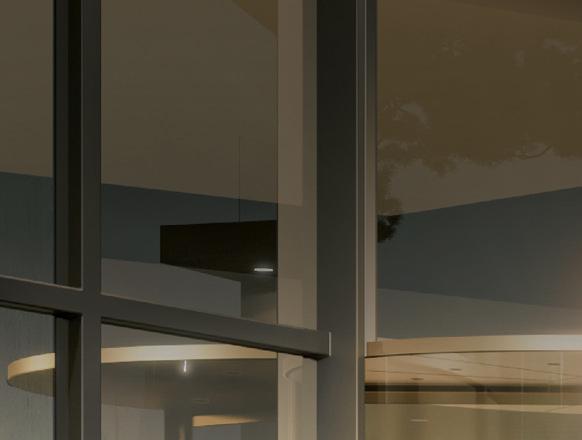
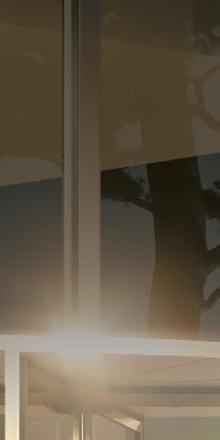

The uniquely-designed ceiling is made of biogenic acoustic baffles, minimising the dependency on metals, while the bio-resin terrazzo flooring is created with biopolymers, reducing the need for chemical resins. These measures reduce both the store’s operational energy consumption and the embodied energy of construction. Apple Battersea runs on 100% renewable energy and is carbon neutral, like all Apple retail locations.
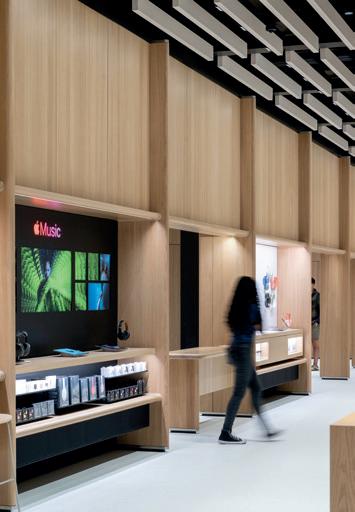
T he system is centred on universal design principles, creating an inviting space where everyone is welcome. It offers varied table and seating heights, as well as access routes that give wheelchair users more space to navigate. For hearing aid users, the store offers a portable hearing loop that can be used anywhere and an additional in-ground version at the Today at Apple table, removing the need for the user to self-identify.
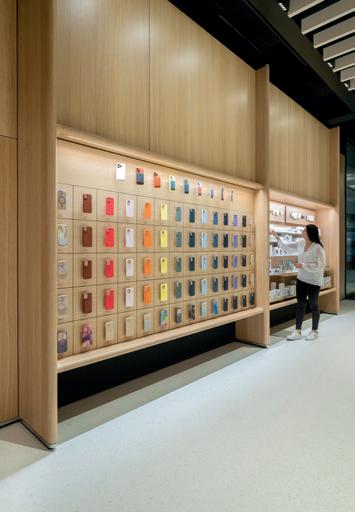
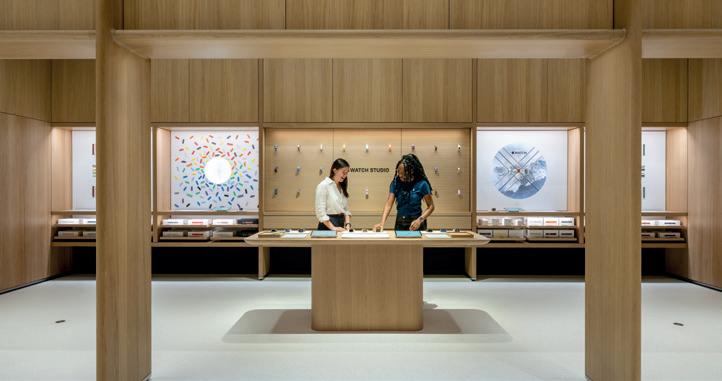
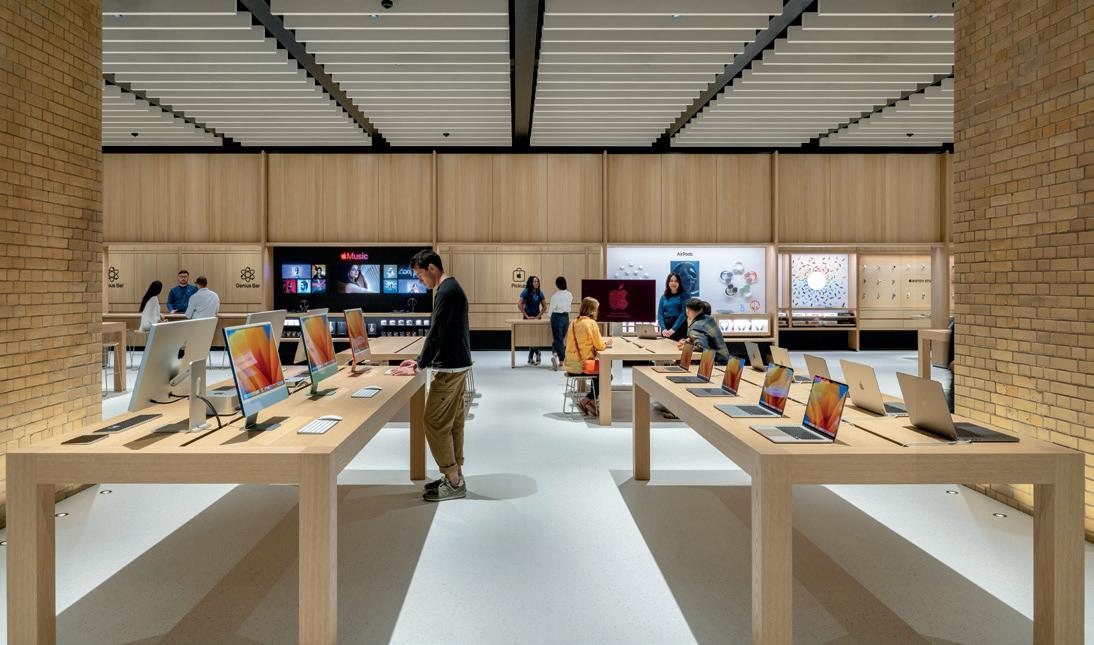
T he new store in Battersea Power Station is quintessentially Apple while respecting the historic Grade II*-Listed landmark. Four central brick columns have been retained to enhance the character of the space. The system’s material palette of timber, terrazzo and exposed metal works in harmony with the heritage-driven approach to the major redevelopment project. A glazed storefront with bronze framing is in keeping with the adjacent retail units in the Turbine Hall.
T he design carefully balances historical and contemporary elements – creating a space that celebrates the building’s industrial past while embracing technological innovations of the future.
A Symphony Of Architectural Melody
The award-winning architecture practice, Hollaway Studio, has designed a remarkable new music school and concert hall with acoustics fit for an international philharmonic concert hall.
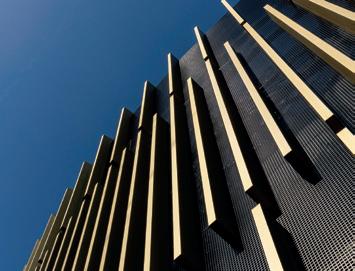
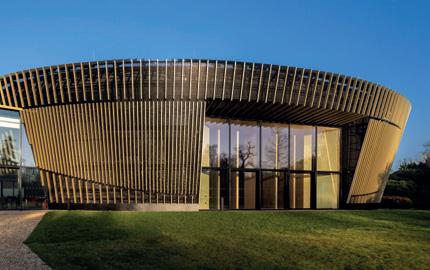

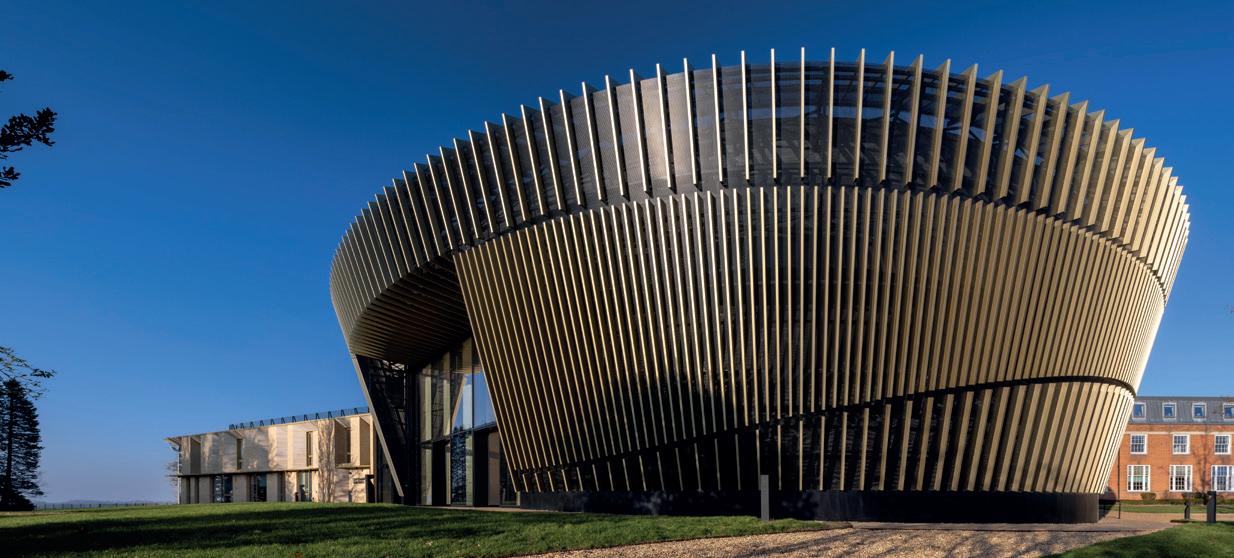
‘Acoustic perfection’ fit for a ‘mini Glyndebourne’
S ituated at Benenden School, Kent, and conceived as a musical instrument in its own right, every part of the design of the Centenary Buildings – from the materials used, the detailing as well as employing a world-leading acoustician – all contribute to an environment that embodies ‘acoustic perfection’ Hollaway Studio has created a building made to give life to music – and so to the cultural education of both Benenden’s pupils and the local community beyond.
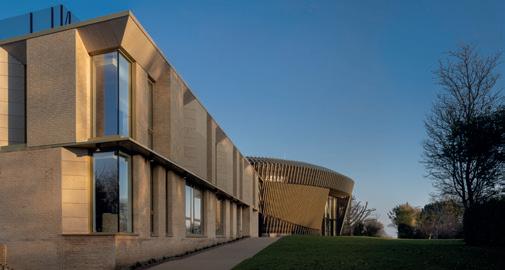
I n a school that dedicates itself to the whole-person education of its students, music is absolutely central to the curriculum. As much a teaching and practice space as it is dedicated to performance, Centenary Buildings includes a 750-seat, uniquely-shaped, timber-framed concert hall known as the Centenary Hall; t he Sir David K. P. Li Music School, comprising the 150-seat Bonnie Yeung-Tsang Recital Hall, which opens out onto the courtyard by the use of side glazing; digital media suites with stateof-the-art recording and performance facilities , including the Metherell Song Room and extensive landscaping allowing for external performances.
D esigned as a concert hall first, the building also works as a school hall, although Hollaway Studio considered it a ‘mini Glyndebourne’ during the design process. Fittingly, the Philharmonia Orchestra performed at the opening ceremony of the building.
C onnecting a new music department to the performance space in order to work together, the Sir David K. P. Li Music School houses more than 20 light-filled practice, rehearsal, percussion and song rooms, the latter for choral and solo practice. Each room is designed to respond to its anticipated use. Benefitting hugely from framed views, the Music School is linked to the Centenary Hall by the Beethoven Bridge through the stunning new double-height atrium space, which also links to the west wing, chapel and main school and flows into the new seniors’ courtyard outside, creating a tranquil and beautiful space in which pupils can relax and gather with friends. The Centenary Buildings are situated at the end of the ‘academic corridor’, which sets up a line through Benenden, picking up sciences, art and library spaces and now connecting to music.
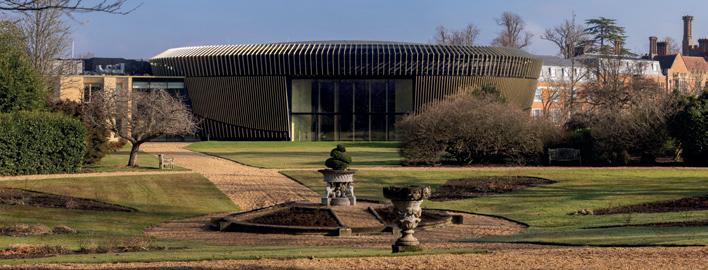
G uy Hollaway, Principal Partner at Hollaway Studio, says: “Centenary Hall is like a musical instrument in its own right. To create a mini Glyndebourne in this setting is an incredible feat of design and acoustic engineering and truly shows how important music is as part of education. We wanted to create something that could be used in so many different ways to benefit the school and its surrounding community for now and generations to come, and I think this building really does that.”
C rucial to the structure is the Centenary Hall’s giant doors that function not just as an entrance but also as sonic reflectors. When open, the doors let the light of the natural world in – the Centenary Hall’s oval external perimeter echoes the shape of the rose garden in which it sits and has been restored as part of the project. When closed, they stand guard over the acoustics so that nothing can detract from it. Added to this, the fins of the timber facade, created with Colorminium, emulate the strings of an instrument and fold around the air ducts concealing them from view. The striking diagrid roof is designed as both a structure and acoustic device in one. Its addition allows sound to bounce around the bays, encouraging the volume to feel larger, devoid of echoes.
World-leading Acoustician Matthew Harrison, a Partner at engineering consultant Buro Happold, was brought in to advise on achieving unrivalled acoustics in the hall. His ambition was to achieve exceptional musical acoustics in spaces that would also be used in the daily life of the school.
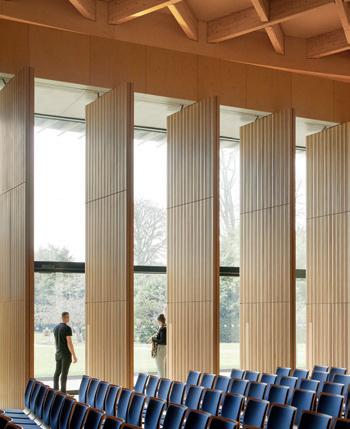
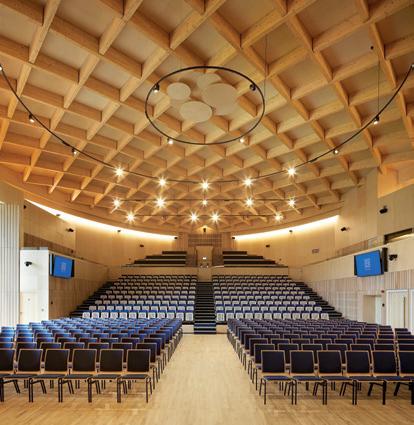
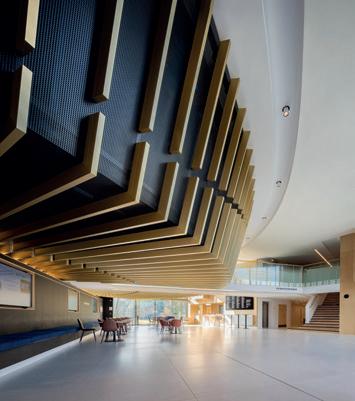
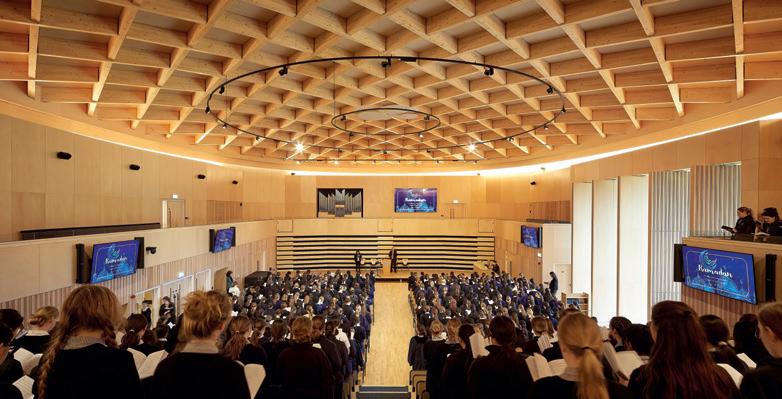

As he explains: “The Centenary Hall has been designed so that a person can address the entire 750-seat audience at once without using a microphone even though the hall has sufficient acoustic responsiveness to support live orchestral work. The final acoustics are warm and well-balanced with good clarity, evident when the organ is played. The Bonnie Yeung-Tsang Recital Hall has been designed to emulate the acoustics of the Centenary Hall to give students confidence as they develop their playing and to give an intimate atmosphere for an audience. The Metherell Song Room in the Sir David K. P. Li Music School also reproduces the same acoustic characteristics giving Benenden School a distinctive sound of its own.”
The heart of the school community for future generations
S et within 250 acres of parkland, Benenden’s original School Hall was built in 1939 when there were just over 200 pupils, meaning that with the current intake of 550, it was significantly outdated. Now, Hollaway Studio has designed something fit for both today’s school and for future generations while retaining the building’s place at the heart of the school community. Flexible seating configurations allow a space appropriate for prayer, performance, events or celebrations. The Centenary Hall also makes the most of its position in one of the most beautiful parts of the school site, while the new design retains some tiered seating which had been a treasured part of the old hall for generations of Benenden girls.
H ollaway Studio’s design – the most ambitious in the school’s history –provides an exceptional performance space for both the school and visiting orchestras, while the attached Sir David K. P. Li Music School will support and promote the arts to the student body and wider community. The addition of the latest technology, lighting and sound management systems has resulted in a world-class centre of music, performance and worship that reflects Benenden School’s ambition and continues to build upon the strong legacy of high-quality architecture that is already found across the campus.
Demand For Offsite Construction Continues To Rise
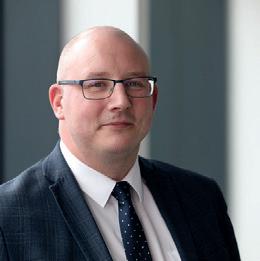
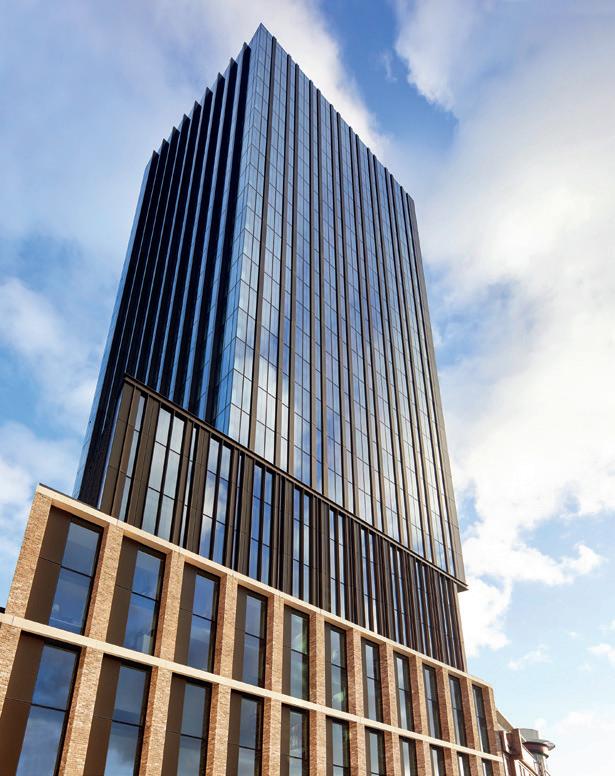
The practice of offsite manufacturing has been around for hundreds of years; the first example being recorded in 1895 by Sears Roebuck and Company in the US, who began selling new home-building kits. Over the past few years, offsite manufacturing has become a preferred method of construction for many specifiers and contractors. Prior to 2022, offsite construction accounted for around 2% of the total construction market. While latest figures estimate this is set to grow by around 6% by 2029. Here, Dan Gleeson, Head of Commercial Sales for Reynaers Aluminium UK, discusses the advantages of offsite manufacturing and benefits specifically for unitised, panelised and modular construction.
Of fsite manufacturing is a relatively modern approach, which involves sections of an external wall being constructed off site; this can be panelised, unitised or full sections of the building. Panelised facade systems are like unitised ones, but the prefabricated modules are generally much larger to incorporate different materials and components (such as windows). This process significantly expedites the construction and installation processes, making it more efficient, saving both time and money, requires less skilled labour on site and generates fewer carbon emissions.
W ith ambitious net-zero targets on the horizon, using modern methods of construction (MMC), such as offsite manufacturing, is an effective way to decarbonise some of the production processes. For example, delivering building elements in a controlled environment enables contractors to ‘get it right the first time’. This means using fewer materials, emitting less carbon and driving efficiencies.
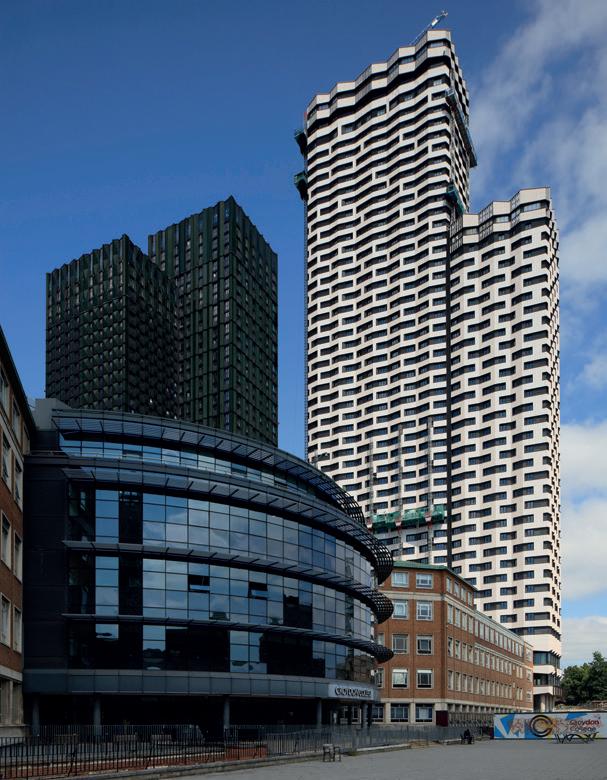
More efficient – less labour
M uch of the construction that would traditionally take place on site, occurs in the factory. The prefabrication of components in a controlled environment increases the quality of the product and reduces some of the workmanship issues on site. The speed of installation on site is also much quicker with both panelised, unitised and modular or volumetric construction, which saves both time and money. While unitised facades are tested to withstand the most onerous conditions, panelised and modular or volumetric may require some onsite water testing, especially if some of the joints are sealed prior to transit.
The unitised approach to glazing and facades
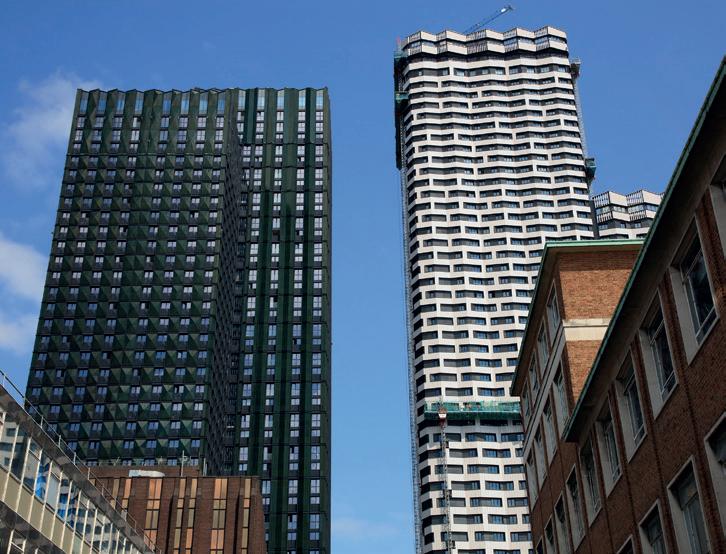
I mplementing a unitised approach to glazing and facades can yield significant benefits. Unitised systems consist of prefabricated units that are fully glazed and sealed off site. The complete units are then moved to site for swift and easy installation onto the steel or concrete frames with integrated location and carrying devices locking the panels in the correct relationship to one another.
O ffsite manufacturing offers greater control over the process and ensures the quality and consistency of all systems and components. This is particularly crucial for the unitised facade elements, which must be fully compliant with the latest Building Regulations and be robust enough to withstand the UK weather. Manufacturing off site means each unit can be monitored and checked for compliance and performance before leaving the factory. This not only reduces the risk of defects but also prevents issues on site, which can be more difficult, time consuming and costly to rectify. Prefabrication in a factory environment also minimises the risk of damage and so reduces the chance of waste.
Panelised
W ith panelised construction, we typically see windows glazed into openings formed from precast concrete panels. The windows are installed off site and glazed; in some instances, they are then fully sealed with EPDM perimeter seals and internal air seals. The panelised component is then sent to site and craned onto the building. Typically, there will be a water test regime in place, either spray bar testing of opening elements or hose testing of fixed joints while on site.
Modular or volumetric
M odular or volumetric construction is slightly different in that the modules provide the internal walls of the building as well as either a primary or secondary structure. When the structure gets to a certain height, it needs to be connected back to the building’s core to ensure that excessive building movement does not occur. The steel modules then form external walls with steel frame system infill or, in instances, containers have been used. The external wall build up is then mounted to the relative face of the module, with more conventional external wall build ups, such as rainscreen, then stick curtain wall, unitised curtain wall, windows or doors can be installed in the apertures created. As with panelised construction, water testing will likely be required to ensure that all seals are in place and correctly connected.
Less time – fewer delays
O ffsite fabrication also significantly reduces the amount of time required on site. The delivery of the facade units to site can be scheduled for exactly when they are needed and installed quickly, preventing clashes with other contractors and trades and minimising delays to the overall build. The progress of a project is also less reliant on the weather conditions, something that is becoming more important as the UK’s weather becomes more extreme and less predictable.
O ffsite construction also has the potential to improve the way we design and construct buildings, driving improvements in quality, safety and cost. However, it does require closer collaboration between members of the supply chain throughout the project, so early engagement is required. The companies required to deliver largescale unitised projects must have the correct technical and commercial infrastructure to be considered for these projects, and while time is saved on site, the design period is protracted and adequate time in the programme needs to be allowed for. It’s vital, therefore, that the industry continues to embrace a more integrated way of working across the value chain to ensure it continues to take advantage of the benefits offsite construction methods provide.
R eynaers UK is a leading expert in the design and installation of unitised, panelised and modular window systems and facades for the commercial sector. To find out more about its expertise and projects, visit the below website.
www.reynaers.co.uk/are-you-architect
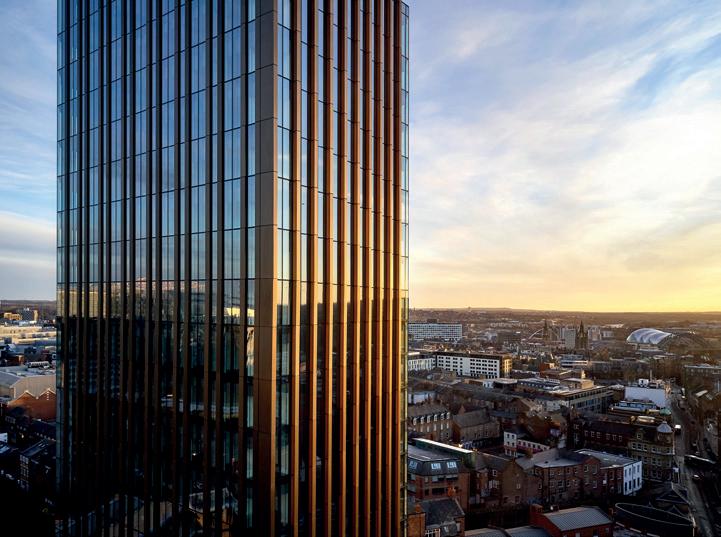