
18 minute read
ACCENTUATING THE POSITIVES OF REGULATORY COMPLIANCE
from FC&A July 2023
The UK construction industry is in the process of adapting to a new regulatory environment, one which promises to deliver safer, more sustainable and higher quality buildings. Arising from the Building Safety Act (BSA) 2022, a raft of recently-introduced codes and standards are having a transformative effect, particularly in the residential property sector, says Maria Hudson, CMO at Zutec.
Ho wever, achieving compliance with these new requirements is another matter entirely and, with so much to consider, can become a complex and nebulous undertaking for housebuilders, developers and property owners alike.
Advertisement
I mportant deadlines are approaching, including the enforcement of the Higher Risk Buildings (Key Building Information) (England) (1st October 2023), a subset regulation of the Building Safety Act and the introduction of Gateways 2 and 3 (also October 2023). It’s imperative for players operating in this vertical to ensure their digital assets are complete, correct and compliant.
U nfortunately, a degree of apprehension about the regulations persists, and this might be due, in part, to a lack of clarity within official guidance combined with persistent knowledge gaps.
Fortunately, technology is providing the answer to some of these longstanding and ongoing problems, offering the tools needed to compile the necessary building information and understand where gaps to be rectified exist at an affordable price.
A n evolving narrative
The winds of change are gathering momentum, and neither asset owners nor developers can afford to stand by as they get stronger.
M ichael Gove has made it clear that those who don’t comply will receive harsh fines or have to find another market. These are strong words, but they’ve also become part of the problem towards encouraging investment in regulatory compliance.
T he ‘Golden Thread’, once a good analogy, is now perceived by some as a daunting prospect when it needn’t be. Especially if we take a step-by-step approach to bring building information assets into line across the building lifecycle, whether that be for new builds or in-use buildings.
For example, when we start a conversation with a new client, we aim to develop an achievable, phased approach to bring together building information, and locating and storing their data correctly. It’s all about practical, deliverable outcomes that get the information they need for the compliance they require in one place to put them on the right side of the law.
The complete package
S o many organisations in this sector have been operating with their data and information spread across different systems, locations and formats. It’s little wonder so many have been left trying to establish if they have the right documentation as this first wave of regulations has landed.
H owever, the proliferation of data management tools and Common Data Environments (CDE) over the past few years is having a significant and efficacious effect, improving the administration of information and simplifying the compliance process. These systems are offering developers, contractors, asset owners and operators real peace of mind from a risk management perspective.
Effectively, it’s providing an accessible, transparent place to manage all data in place with a traceable audit trail to show how building information has been brought together, updated or edited, and evidence work done on a building. This increased efficiency means the right documentation, whether a building manual or fire safety certificate, can be quickly identified and drawn off on request and updated if a renewal is required. Furthermore, missing documents and data gaps can be isolated and updated, fulfilling the twin aims of quality and compliance.
I t might sound complex, but it’s better to think of it as a simple yet sophisticated live data bank, drawing all your information into one place.
From this first step, these types of solutions can be enhanced, ensuring that across each stage of the construction journey, particularly Gateways 1, 2 and 3. There are also templates in place to meet the BSA requirements as they are introduced.
The safety-first culture
A s you can see, the road to regulatory compliance is not as complex as it might first appear, especially with the right digital software and solutions in place.
We need to move the conversation on. Rather than just focusing on the consequences of non compliance, we need to balance the conversation with the real, commercial benefits, from better quality building data to safer housing.
I t will start by promoting a safety-first culture within the sector, celebrating and rewarding those who behave responsibly. It’s also about making building information universally accessible so decisions can be made that mitigate risk.
Access for all
U ltimately, the data-gathering process is not just about having information in one place but the ability to access it to make it accessible to those that need to see it, whether a regulator or tenant, and drive decisions that achieve more control over assets. Sharing the information with inspectors, regulators and tenants to ensure their homes are safe. Understanding correct procedure has been followed will also establish a reputation for best practice.
T his will undoubtedly lead to better reputations, increased resident and consumer trust and higher margins. All this from better management of information and a more positive spin on regulatory requirements.
Although just one part of a wider process, technology can support this aim, delivering ROI above and beyond the sheer ability to practice with the UK residential market, keeping residents safer now and in the future.
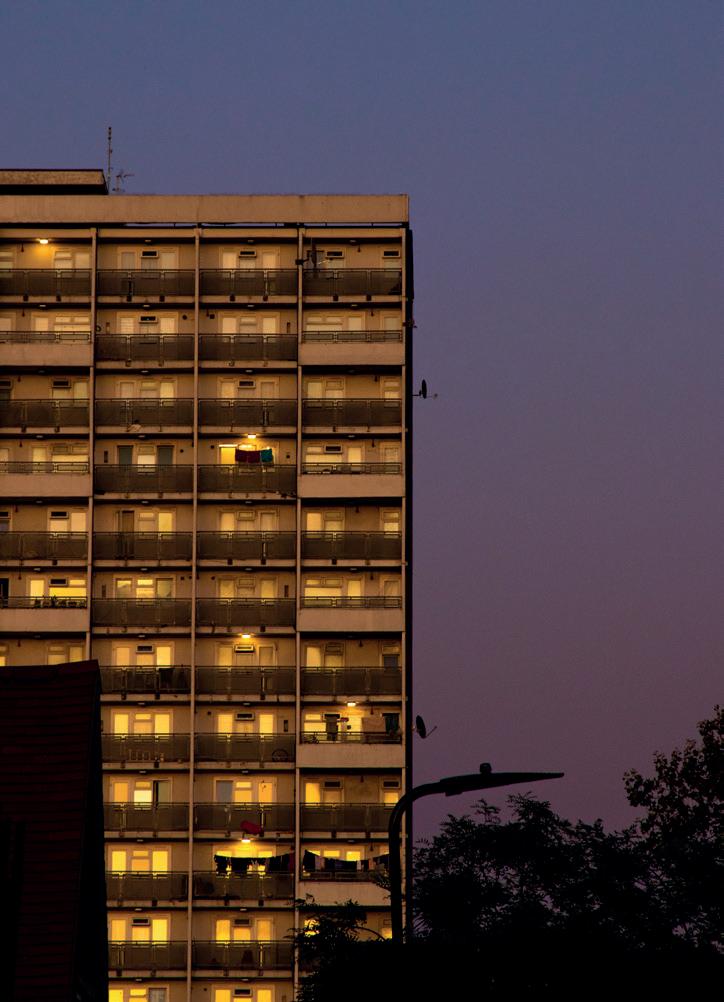
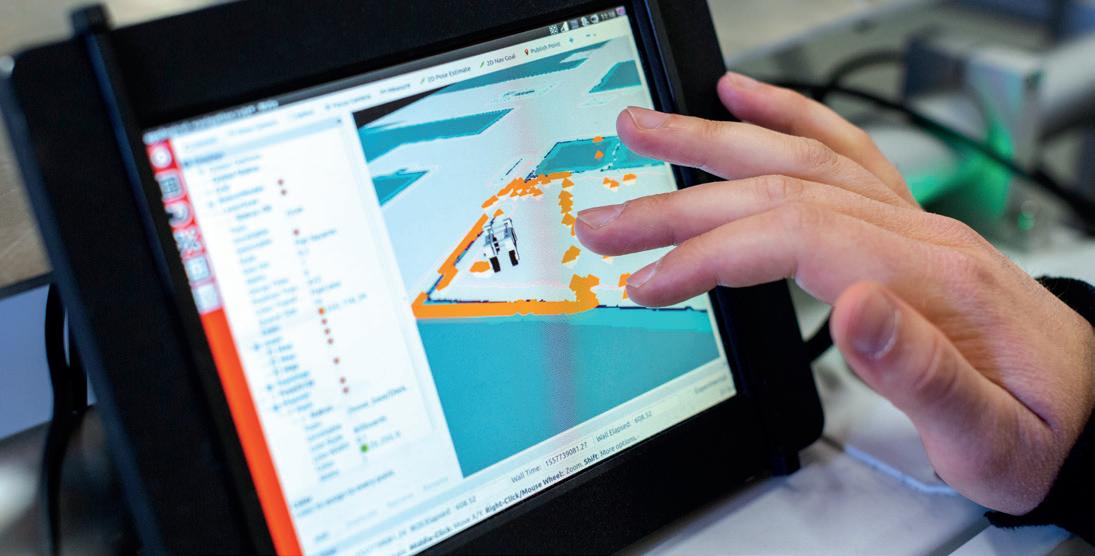
Shining A Light On Part L And Rooflight Specification
Rooflights can help flood a space with daylight. However, specifying the right product to comply with Building Regulations is far from straightforward, as Ross Finnie, Sales Director at SIG Design & Technology (D&T), explains.

Ro oflights are an increasingly popular means of allowing daylight into a flat-roofed building. In deepplan commercial buildings, overhead glazing enables daylight to penetrate into the core to create a better, more dynamic indoor environment. In homes, meanwhile, the addition of a rooflight will brighten up even the most mundane of extensions, making the space appear bigger and brighter.
T here are a huge number of rooflight products available for flat-roof applications in both the domestic and commercial sectors. These are suitable for both newbuild and replacement applications.
B ut be aware, specifying a rooflight solution that will comply with Part L of the Building Regulations – the section of the regulations that deals with energy efficiency of buildings – is often far from straightforward.
Understanding the regulations
A pproved Document L provides guidance on how to meet the energy requirements set out in Building Regulations. It is published in two parts: Volume 1 deals with dwellings; mixeduse buildings and buildings other than dwellings are dealt with in Volume 2. This article references the 2021 edition of the Approved Document L (ADL), which came into effect on 15th June 2022 (Note: ADL was amended in 2023, but these amendments do not impact the section of the document that deals with rooflights).
A good starting point in the selection of a rooflight is to define its required thermal performance, or the rate of heat transfer through that element, from inside to outside. This is known as the rooflight’s U-value, measured in W/m 2 .K. In words, this is the amount of heat transmitted in Watts for every square metre of the surface area of that element per degree of temperature difference between inside and outside.
In short, the lower the U-value, the more slowly heat will pass through it and the more thermally efficient it is.
New buildings
A new building must be built to minimum energy standards and requires an energy assessment to demonstrate compliance. ADL also gives a limiting U-value for the fabric elements of a building’s envelope, which includes rooflights.
In other words, this is the worst thermal performance allowed for that element. This is to provide designers with some flexibility in how they meet the total energy performance requirements by using thermally-efficient fabric elements.
T he first point where confusion can occur is in the definition of a rooflight. This is because Part L distinguishes between a roof window and a rooflight. If you think these are different names for the same thing, think again.
A DL gives a limiting U-value figure for rooflights of 2.2W/m 2.K, whereas for roof windows, the limiting U-value is 1.6W/m2.K for both new and existing buildings.
SIG DESIGN & TECHNOLOGY (D&T)
A DL references the BRE document BR443 Conventions for U-value calculations, which makes a distinction between the two. It defines a roof window as being installed in the same plane as the surrounding roof, with a minimum pitch of 15 ° (such as a centre pivot window in a tiled roof). Instead, a rooflight is installed on an upstand and so is not in the same plane as the surrounding roof (such as a flat glass rooflight on a flat roof).
T he difference in limiting U-values is because the U-values for roof windows are calculated based on them being vertical, whereas the U-value for a rooflight is calculated based on it being horizontal. If a supplier gives the U-value for an element in the wrong plane, it must be adjusted according to the data in BR443.
A nother aspect to be aware of is that the U-value is based on the rooflight and its frame. The U-value can also include the kerb assembly when the kerb is supplied as part of the rooflight assembly. Where an upstand to support a rooflight is constructed on site, the upstand should have a maximum U-value of 0.35W/m 2 .K.
S pecifiers need to be aware that this requirement can result in the surface area of the rooflight being greater than the area of the roof opening, which will impact the building’s heat loss calculations.
I n addition to the thermal performance, other considerations include the type of glazing. All overhead glass must be safety glass, which is usually annealed laminated glass or polycarbonate.
Loadings are also important because in addition to being able to withstand wind and snow loads, some rooflights may also need to withstand being walked upon, and so may need to be able to withstand the weight of a person.
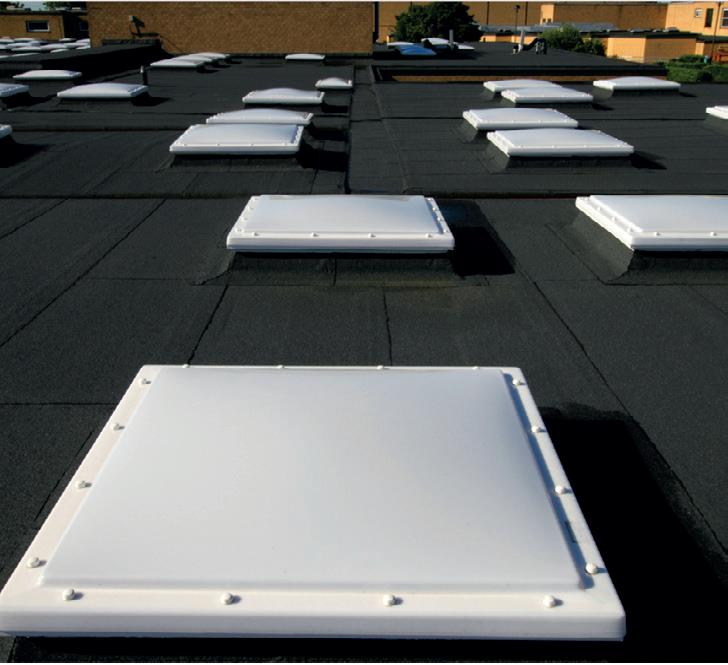
E xisting buildings
Replacement rooflights and rooflight and kerb assemblies must also have a U-value no greater than 2.2W/m 2.K. The exception to this is if only the glazing is being replaced as a remedial. In this instance, the glazing does not have to meet the energy-efficiency requirements, but its thermal performance cannot be any worse than the thermal performance of the glazing it is replacing.
Where a dwelling is being extended, the total area of rooflights, roof windows, windows and doors should not exceed:
1 25% of the extension’s floor area
2 . The total area of any windows and doors that no longer exist or are exposed due to the extension.
B y contrast, where a building other than a dwelling is being extended, the area of rooflights typically cannot be greater than 20% of the area of the roof.
C learly, there is a lot to consider when specifying a rooflight. Where a bespoke rooflight is needed, SIG D&T can provide advice on suitable options for a particular application. SIG D&T is also able to draw on the expertise of the SIG360 team when it comes to advice on specific compliance issues.

W here a more cost-effective modular rooflight is required, selection is easy using the SIG D&T online Rooflight Configurator. Using the simple interface, designers and contractors can choose which type of rooflight suits their needs and then pick the specification required, including size, kerb, tints, opening options, ventilation requirements, accessories and more. They can make an enquiry about that specific product or download the appropriate brochure. www.sigdandt.co.uk
Taking You To The Next Level
Staircases, lifts, balconies and balustrades are some of the strongest transition elements in architecture; they are designed to connect two spaces, whether interior to exterior or different internal levels. Positioning these elements in a multi-level building will always be vital, but now it is just as essential to create a design visual and consider them as main features, says Jonathan Reed, Managing Director at Amron Architectural.
De signers are always looking at more inspirational approaches to the interiors of a space. The demand for creating more inviting spaces and the inclusion of a variety of different applications can completely transform the character of a room. Amongst these approaches, we are seeing an increase in the use of metal meshes both from the point of view that they are generally made from recycled material in the case of aluminium and steel – but also because the style and look of them have that upcycled feel that we are all trying to be more conscious of.
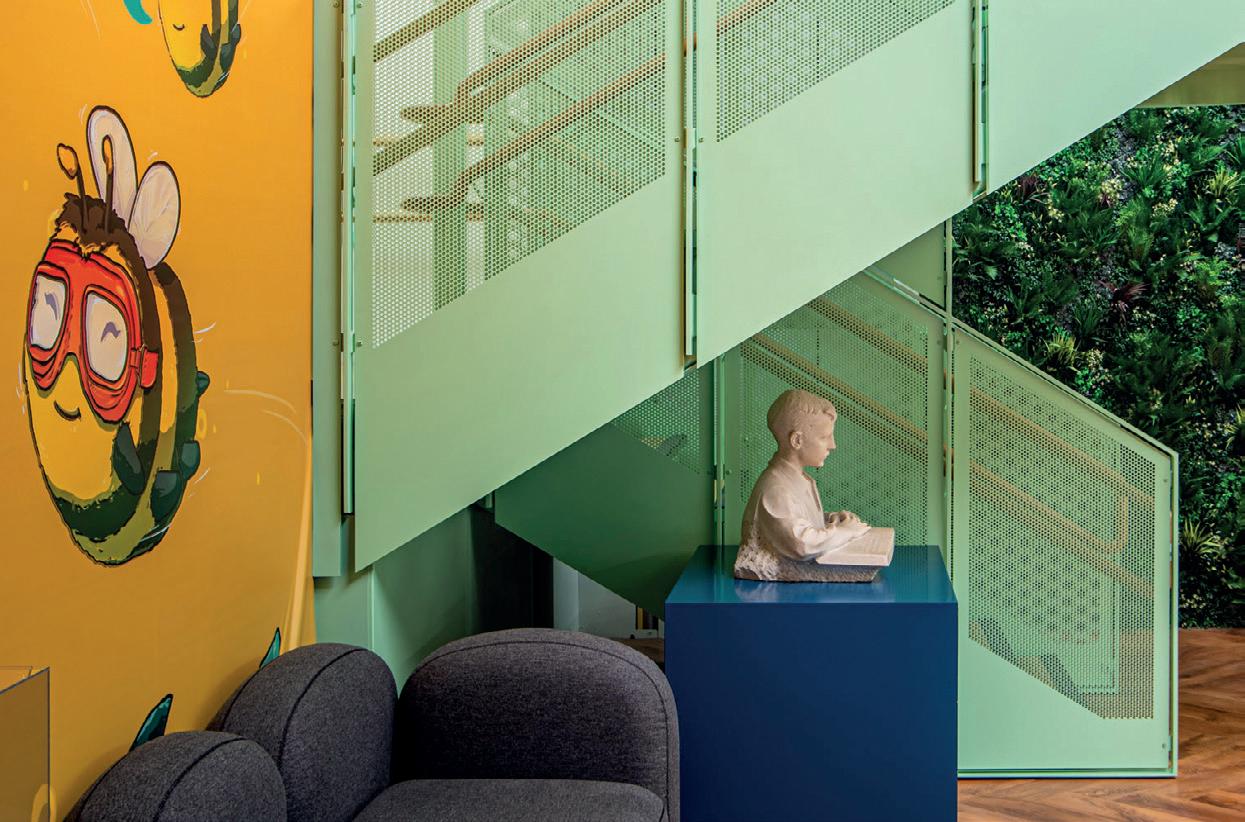
Metal mesh has a long tradition of outdoor use spanning hundreds of years. Over time, metal mesh has earned a reputation as a practical, durable, yet surprisingly versatile product thanks in part to its uncanny ability to meet a wide range of specifications. It is an extremely versatile product and has functionality like no other. It is being increasingly considered for decorative purposes like ceilings, wall coverings and partitions and is a great solution for smaller applications like cabinets, bars and shop displays. It’s being seen as an alternative to replace bulky, opaque materials in functional areas of restaurants, lobbies and office spaces without making the space look smaller. It is also specified as a safety element, including balustrade infill panels, which is a great option for safety and pushes the design boundaries.
A s interior and architectural trends evolve, so do the materials and components. The popularity of metal mesh has seen it be used in almost every sector of construction from the hardest industrial environments, such as oil rigs where the mesh needs to be durable, non-slip and anticorrosive, to the most delicate of installations in luxury hotels where aesthetic is everything. So, it is not surprising that architects and designers are developing new ways to use metal mesh to add character.
Bespoke colour
C olour is one of the main attractions when it comes to the finishing of metal mesh and, in particular, how the mesh is coloured without it corroding. Having researched a number of finish processes that work well with the commonly-used architectural meshes (woven, expanded and perforated), powder coating is the most cost-effective way to apply an almost unlimited range of RAL colours. Powder coating uses an electrostatic charge to attract a fluidised powder evenly across all surfaces of the mesh. The electrostatic charge holds the pigmented powder until it passes through an oven, where it melts and adheres permanently to the mesh. After curing, the mesh has a colourful and durable coating that adds to the desired aesthetic of the project.
Product in practice
T he Royal Society for Blind Children has opened a new centre in Tower Bridge, London. The charity, which was first founded by Thomas Lucas in 1938, supports blind and partially-sighted children, young people and their families. Initially, the charity was set up with the intention of teaching blind children how to read, but it has since expanded to help those who are visually impaired gain employment. The RSBC also provides homeworker schemes and workshops to assist in the development of confidence and skills through activities and education.
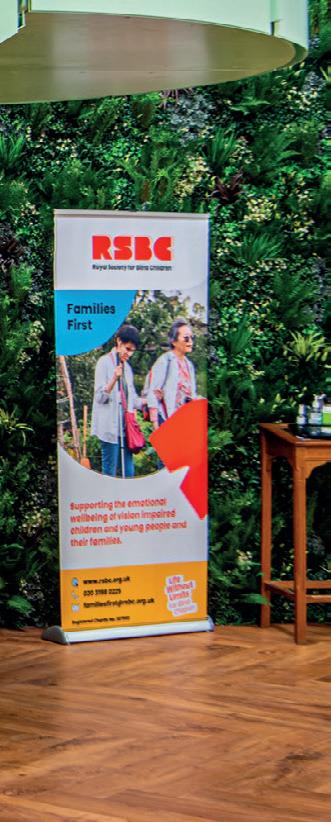
Moving into the new Richard Desmond Life Without Limits Centre in the heart of London, the RSBC is known for vibrant colours and playful interiors to create an uplifting environment for staff and visitors. The new centre does just that, transforming an old car park into an engaging activity hub for users while also providing a modern and flexible workspace for volunteers and visitors to meet, play and learn.
Working alongside Tsunami Axis and Force Five Engineering, we were asked to supply perforated metal sheets in raw mild steel for the balustrading surrounding the staircase.
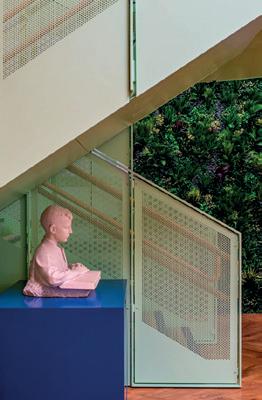
T he metal sheets were then powder coated and given a pastel green finish. Alongside the flower-printed walls and bright, earthy colours, the pastel green perforated sheets gave an optimistic, calm and fresh feel to the hub. www.amronarchitectural.co.uk
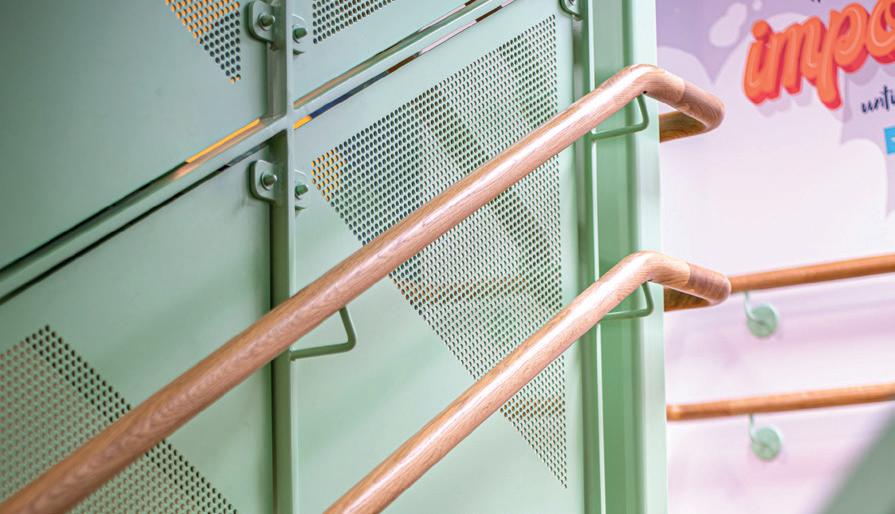
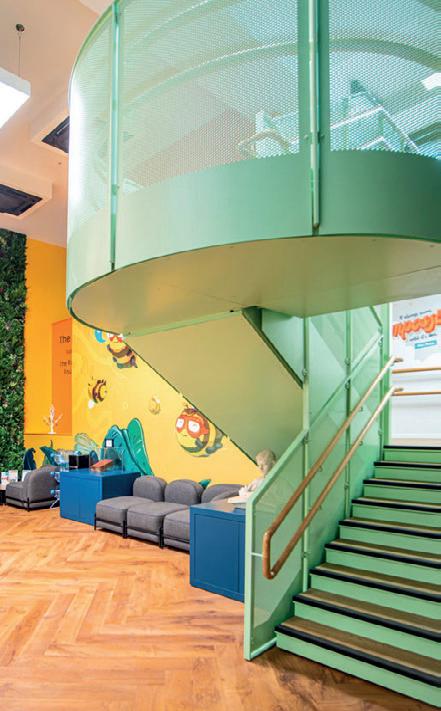

W hether you choose to use metal mesh for its functional or decorative virtues, the material comes in a variety of thicknesses, patterns and shapes to inspire you for your interior design.
BIGGER, BOLDER AND BRIGHTER
Architectural surfacing, or rather the decors market as a whole, is one of the fastest-growing building product categories in the UK, and this increasing appetite is driving a wider choice of materials and innovation. Here, we delve deeper into the subject with John Martyn, an expert in architectural surfaces.
Wi th new solid surfaces, melamines, veneers, laminate and the like coming online each week, it can be hard to keep up with the latest trends and tastes influencing purchasing decisions. These range from evolving visual preferences to deeper-held sentiments and requirements, including sustainability and circularity.
Let’s take a closer look:
H yper-realistic design
V isual and textural mimicry is currently the height of fashion, especially against the backdrop of material shortages and rising costs of categories such as natural stones, pure metals and glass.
I t’s encouraging specifiers to seek alternatives and manufacturers of surfaces to up the ante in their R&D departments to not only deliver the look of those hard-to-access materials but also the feel, at a competitive price point.
Looking at some of the myriad options coming onto the UK market, Dekodur’s incredible ‘Real Metal’ HPL collection and Swiss Krono’s ‘One World’ melamine range are pushing the boundaries about what can be achieved visually on these types of surfaces.

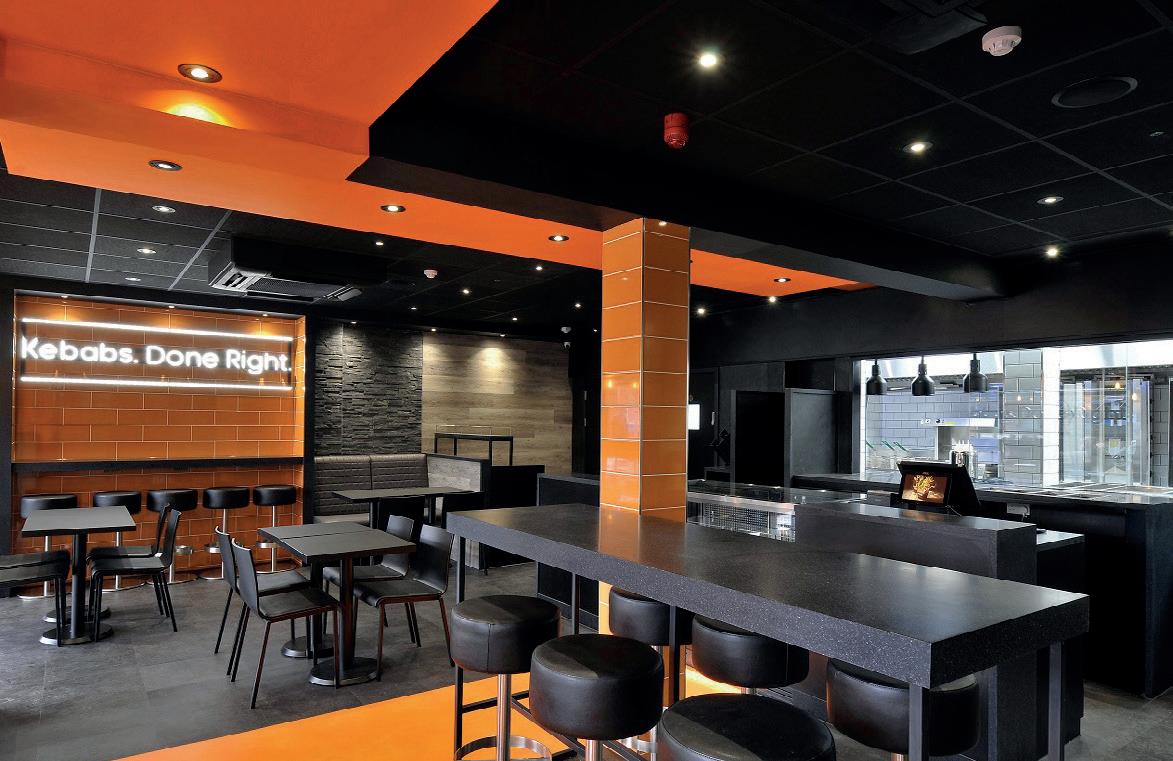
D elivering an authentic-to-the-touch texture has long been a challenge, but these brands have invested in the latest technology to create tactile surfaces true to the materials they represent.
In fact, Dekodur’s collection actually has a layer of real metal on its surface, a landmark achievement in this market and something that will immediately appeal to those designers in the high-end commercial sector.
S urface manufacturer Transformad has taken this even further, creating Tmatt, a range of melaminefaced boards, super soft and sensuous to the touch, yet moisture resistant and anti-fingerprint too.
B end and shape
Curves are in, and it’s shaping the decisions of specifiers when looking for finishing materials within either commercial or residential spaces, whether robust boards or ultra-thin wraparound veneers.
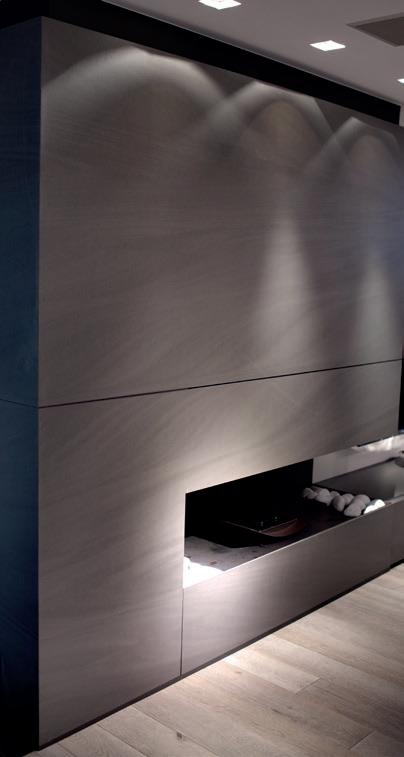
I t’s definitely encouraged a spurt of innovation in the marketplace, with LG Hausys’ HIMACS leading the way when it comes to creating smooth bends with seamless joints. This has been recently seen on a large-scale UK project, which has seen the material, provided by distributor James Latham, used extensively by the rapidly-growing fast food chain, German Doner Kebab, across many of its sites in this country.
W hat made it instantly appeal to the vendor, aside from its vivid colourways, is its tensile strength, which can deliver a robust structure even when formed into bends. It can even be twisted, adding another interesting visual dimension. All this whilst still achieving a hardwearing, hygienic surface that is essential for any retail or hospitality application.
F ibre of the future
W ith sustainability becoming an increasingly compulsory requirement of the design brief, decor manufacturers are responding to specifiers’ calls for the lowest carbon, most eco-friendly products possible.

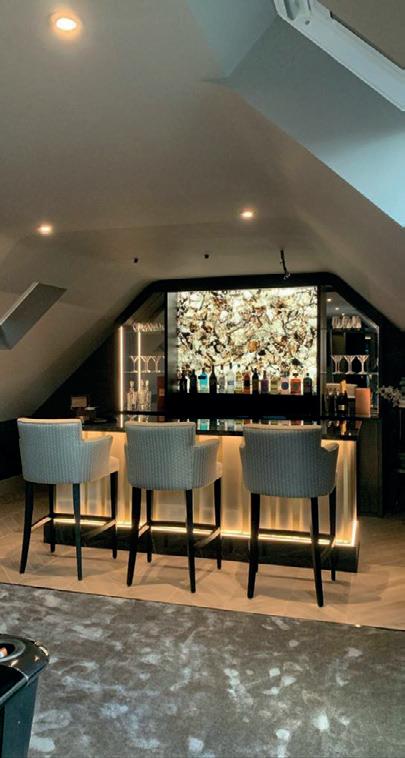
T his starts from the materials used to make up the surface, and one particular category in which we’re seeing particular innovation is fibreboards.
O ne that springs to mind is Honext, an innovative panel from Barcelona, composed of the cellulose slurry left behind by the paper-making industry. Reimagined as a lightweight substrate, its low-carbon production is also helping to reduce CO 2 levels, especially in commercial interiors.
G oing further into this category, brands like Valchromat are also committed to finding ways to reuse waste byproducts, with all of its full-colour MDF boards being FSC certified and sourced from forest waste, residue from timber mills and recycled pine with organic dyes.
R ecently, the full potential of the material’s surfacing ability was demonstrated at leading UK furniture college, Rycotewood, where a number of the students were able to achieve an ultra-smooth finish on the material.
G reen is the word
Taking a deeper dive into sustainable decors gaining popularity on the market are recycled plastics, which can be made into HDPE (polyethylene) sheets for super-resistant worktops. One that comes to mind is Durat, which has actually been on the market since 1990, using industrial waste plastics to create vibrantly-coloured, durable terrazzoinspired hard surfaces, perfect for countertop applications.
M anufacturing processes are just as important as the composition of materials. Sintered stone brands, such as Neolith, Dekton and Lapitec, are leading the way in sustainable hard surface products. Whilst organic materials are a must, it extends to the way they’re produced from using 100% green energy in production to guaranteeing circularity within the product’s lifecycle.
Circularity is something that many surfacing brands take very seriously, and as much as it’s still of value to be recyclable, being reusable is fast becoming the preferred outcome at the end of life. From take-back schemes to being repurposed for other useful applications, manufacturers are exploring innovative ways in which their materials can be reimagined at the end of their initial life.
A vibrant market
We’ve only scratched the surface of what’s currently going on within this exciting and ever-evolving category. What is clear is that, as much as change is being driven by fashion, it’s also arising from necessity as net zero gets closer and virgin resources become scarcer.
H owever, with so many different manufacturers investing in their raw materials and production processes, specifiers have plenty of choices when looking for materials which visually, structurally and sustainably meet requirements.
Delivering The Largest Prefabricated Electrical Installation In Europe
Here, we find out how RMS partnered with LMOB electrical contractors to meet strict time deadlines for what they claim to be the largest offsite-manufactured electrical and building services solution in Europe.
4
0 Leadenhall is an £885m 900,000ft 2 office development with some retail and leisure facilities in the City of London. It consists of several stepped blocks that include two towers, one of which is 34 storeys tall and the other 14 storeys high.
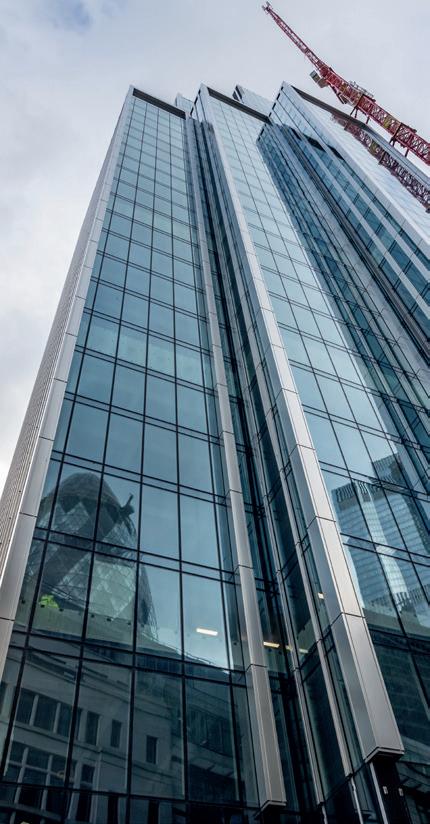
T he challenge for the electrical and building services was to find a solution that contractors could install incrementally one floor at a time while sticking to a strict timetable to keep the project on track.
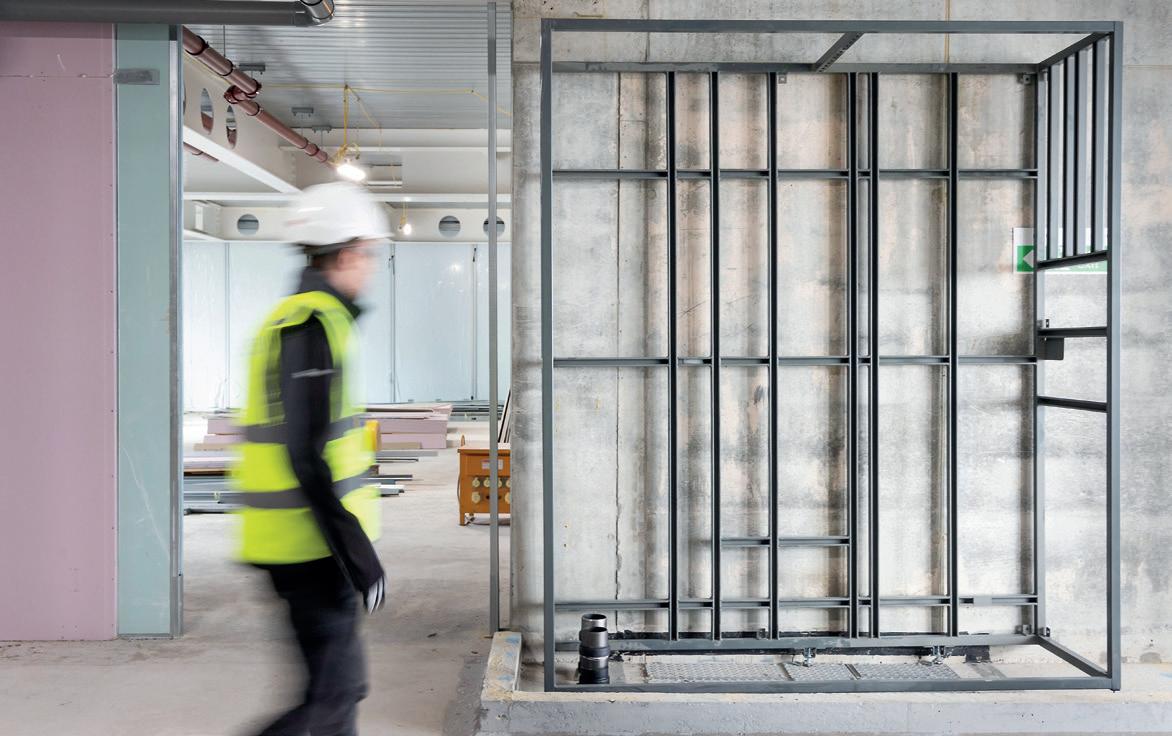
D ue to the scale of the project, the electrical contractor, LMOB, needed to install seven main risers, three in one tower and four in the other. They also needed a cable management solution to run the cabling to services on each floor.
L MOB contacted RMS with a proposed design for the main risers. These would be modular units that interconnect between each floor and need to accommodate a huge amount of services, equipment and cabling. Due to the complexity of constructing such units on site, RMS and LMOB decided that an offsite solution delivered to the site incrementally to meet the build schedule was the best option.
R MS decided to prototype a riser module for testing and inspection to prove that the concept would work in practice before committing to manufacturing. Produced in just two days, the team made some minor alterations to this test module before it was signed off.
S ays Pete Willshire, Managing Director of RMS: “It is one thing to have a design drawing for a solution, but for large, complex projects such as this, it really pays to prove that the concept will work in practice. It is better to test a concept than having to alter it on a busy construction site.”
For the main installation, RMS manufactured 460 modular riser units that the contractors installed one unit at a time. Many of these risers had services, such as electrical distribution boards, installed within them. To achieve this, contractors from LMOB worked on site at the RMS factory in partnership with the company. This ensured that each prefabricated riser module with preinstalled services was quality checked before delivery.
RMS scheduled deliveries with LMOB so that the riser unit modules for each floor, plus standard cable tray, trunking and other cable management products, all arrived one week in advance as a complete package.
E ach riser module connects to the module on the floor above and below it using a flexible link also designed and manufactured by RMS. These all had different heights since the concrete floors between levels have different thicknesses depending on how high each floor is in the building, with lower storeys having thicker floors.
Time-saving solution
Says Richard Pendleton, Operations Director at LMOB: “We managed to cut the electrical installation time for each floor down from an expected two to three weeks to just three days. When you are working on large projects like this and need to coordinate different trades, any time savings are a major factor in keeping projects on track.”
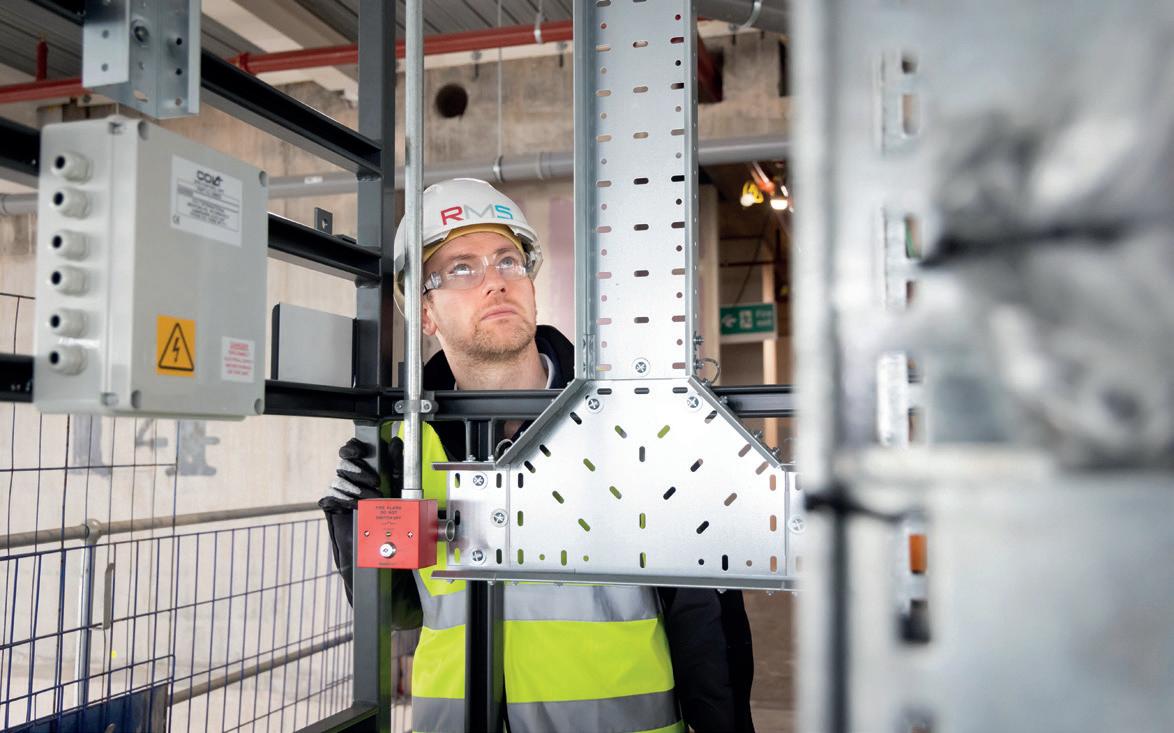
Working closely with LMOB, it was also a major logistical exercise for RMS to ensure that the right modules and standard products were all delivered to a central London site on schedule.
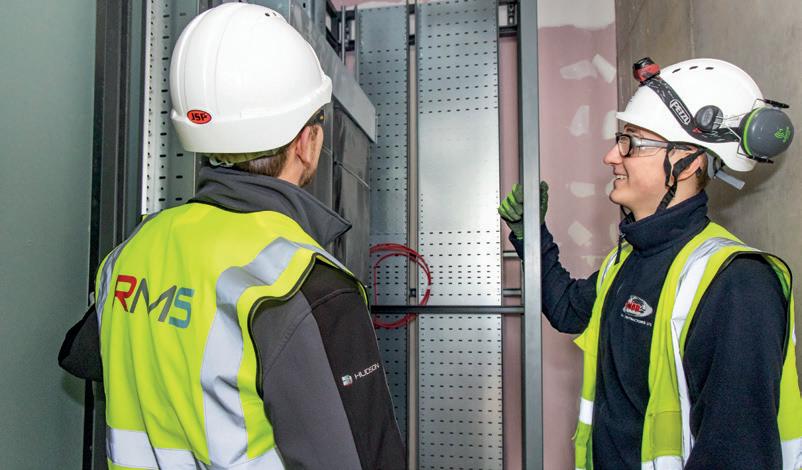
Continues Wilshire from RMS: “When people talk about offsite construction, they often think of complete rooms or pods that are connected together. Often, however, a manufactured solution removes complexity from the construction site to help save time and ensure a high-quality, consistent build for a complex system.
“At RMS, we are often involved in projects that combine bespoke design with offsite manufacturing at our factory with standardised cable management systems from our sister company Armorduct. It is far from a one-size-fitsall solution. Modern projects demand flexibility to meet the challenges of a construction site and being able to flex to meet different needs is an important requirement from manufacturers.
“ Over the years, we have learnt that the best results happen when a specifier engages with us at the beginning of a process. In this case, LMOB understood what they needed, and we provided the design and manufacturing expertise to help them achieve this.” www.rmscablemanagement.com
40 Leadenhall is due for completion towards the end of this year. A major part of keeping the electrical and building services installation on track was due to offsite manufacturing, removing complexity from the construction site to cut time on site. With the shortages of skilled labour available, it is vital to maximise the resource that you have on site, so the role of offsite manufacturing is set to grow.