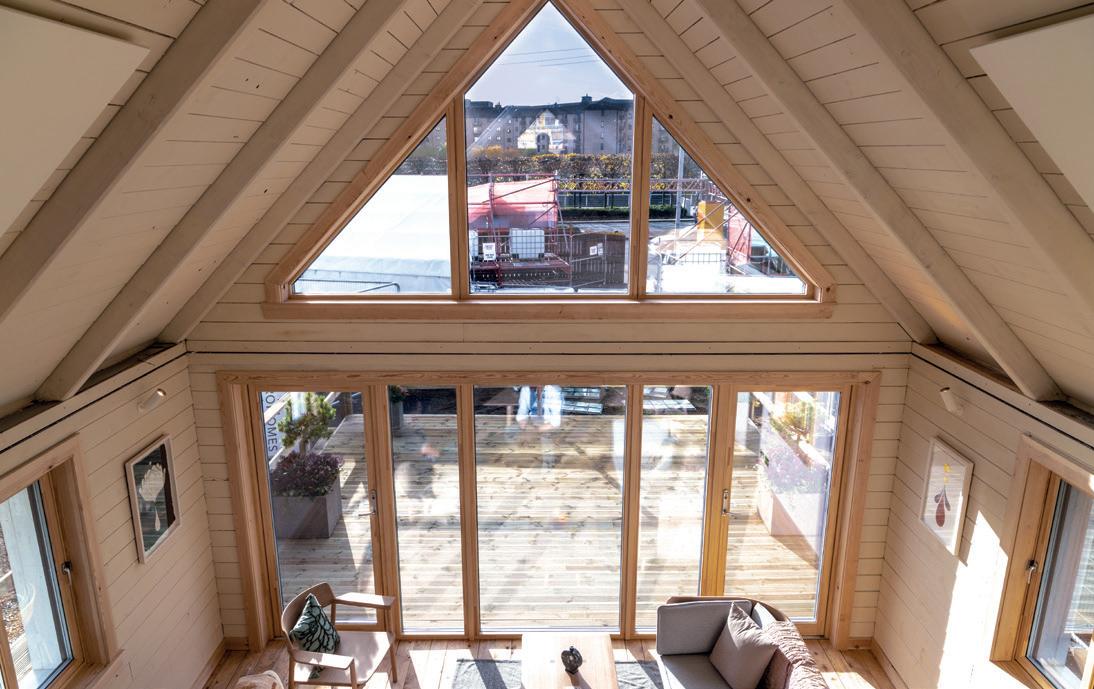
4 minute read
Timber
from PSBJ April 2022
HOW CAN WE TACKLE EMBODIED CARBON?
North Norfolk MP Duncan Baker recently proposed a parliamentary bill that will make it mandatory to calculate and reduce the embodied carbon footprint of new buildings. Here, Mike Stevenson, Senior Manager of Strategic Markets at windows and doors manufacturer NorDan UK, shares how developers can measure and reduce the amount of embodied carbon in new-build and retrofit projects by choosing low-carbon, high-quality building products.
Advertisement
When it has come to reducing building carbon reduction, UK legislation to date has focused more on the reduction of operational – or in-use – carbon. As a result, social landlords have sought to increase the energy and heat efficiency of new homes – and make retrospective improvements to existing properties.
Embodied carbon, the emissions from the building materials, products and the construction process itself, has seen no such legislation, and has, therefore, been a much lesser priority.
According to the World Green Building Council, construction and buildings are currently responsible for 39% of global energy-related carbon emissions: 28% from operational emissions and the remaining 11% from embodied carbon.
With increased levels of construction, and ever-improving operational efficiency, it’s projected that embodied carbon will be on a par with operational emissions by 2050.
The proposed Carbon Emissions (Buildings) Bill would require Building Regulations to be amended to limit the roughly 50 million tonnes of CO2 that are emitted from the materials and construction of buildings in the UK every year.
Even without the ‘stick’ of the proposed new legislation, most developers are beginning to realise that without tackling embodied carbon they will not meet the ambitious net-zero targets or those outlined in the Future Homes Standard.
But let’s be clear, we need to act: poor, short-termism specifying decisions around construction methods, products and materials curse buildings with a negative environmental impact from birth – an original carbon sin that cannot be retrieved or reduced.
Choose low-carbon materials
Embodied carbon content differs significantly between different building materials and products depending on how they are sourced and manufactured.
I’ve worked across numerous building materials over 30 years, including PVCu, aluminium and composite, and over that time I’ve built a picture of how various products deliver different types of embodied carbon – and the motivating factors behind good and bad decision making (usually money).
Of all the materials I’ve experienced, timber is without doubt the most sustainable. Timber is a natural carbon sink, meaning that it absorbs and stores more carbon than it emits during its growth time, which makes its embodied carbon figures amongst the lowest in the industry.
When sourced responsibly and processed appropriately, timber products can offer both industry-leading sustainability credentials, a long lifespan and minimal maintenance requirements.
A standard NorDan window frame is made with more than 90% timber, with a thin aluminium cladding. The result is a window with the sustainability credentials of a timber window, but with reduced maintenance requirements and extended lifecycle of 60-plus years.
This is why NorDan windows are so robust, and contain some of the lowest embodied carbon available on the market today; they are around twice as sustainable as standard composite windows and are five times more sustainable than aluminium windows.
Measuring embodied carbon in a building product also requires tracking materials through often complex supply chains, but manufacturers can assist housing developers by providing third-party verified certification of their products, such as Environmental Products Declarations (EPDs).
EPDs are a transparent, objective report that communicate what a product is made of and how it impacts the environment across its entire lifecycle. NorDan has invested heavily in providing EDPs for its entire product range and, to date, is the only fenestration company in the UK to have done so.
Refurb over rebuild
One of the big lessons we’ve learnt with regards to embodied carbon is the value of refurbishment over rebuild. The carbon expended in demolishing and replacing a building is enormous, and will take even the most energyefficient new build decades to retrieve.
A great example is Castle Court, a large social housing tower block in Sheffield managed by The Guinness Partnership.
In the late 1980s, Sheffield City Council took the decision to refurbish the then-dilapidated 1960s development to provide athlete accommodation for the 1991 World Student Games and, beyond that, social housing.
Using the games as a catalyst for investment, the decision was taken to retrofit Castle Court to a high specification, including the installation of NorDan’s Norwegian-designed StormGuard aluminium clad windows. 30 years on, neither the facade of the building nor any of NorDan’s windows have needed maintenance or replacing. The tilt-and-drop mechanism still operates perfectly, and homes are dry, airtight and warm.
PVCu windows may have been a cheaper refurbishment option and reduced capital cost, but would have needed to be replaced at least once by now – whereas NorDan’s windows still have a further 30-year lifespan, minimum.
Today, Castle Court remains one of the most sought-after social housing developments in Sheffield. Compare this to a neighbouring tower which was demolished around the same time that Castle Court was refurbished. Imagine the embodied carbon lost? It’s a fantastic case study made more relevant and valuable by its age, and one NorDan is happy to share in further detail.
Social, financial and environmental benefits
Embodied carbon legislation and regulation changes should drive what Castle Court perfectly demonstrates; the wider benefits of specifying high-quality building products and materials, because, given enough time, social, financial and environmental values are able to align.
Tenants have warmer, more comfortable homes to live in, landlords have reduced ongoing product maintenance and costs, and, of course, there’s lower embodied and operational carbon emissions. It just makes sense. www.nordan.co.uk
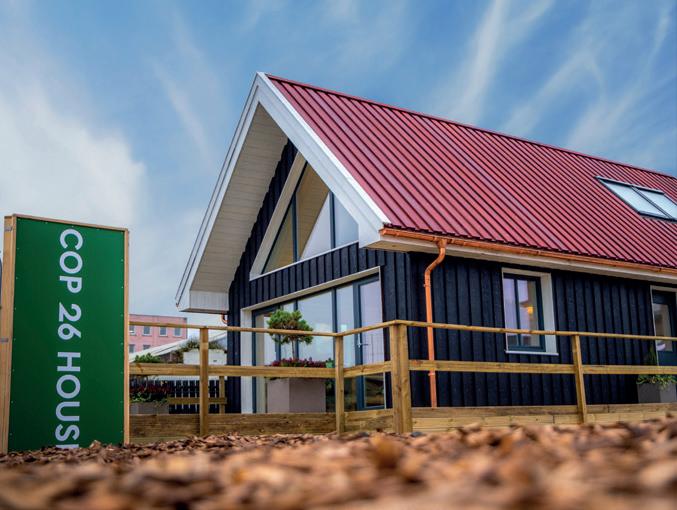

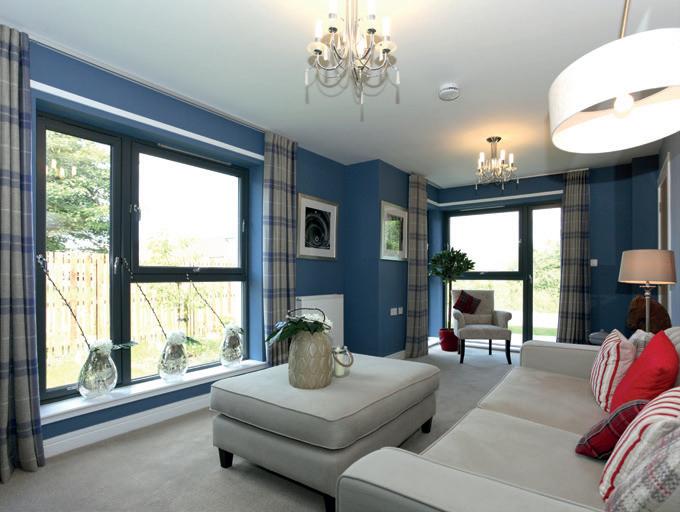