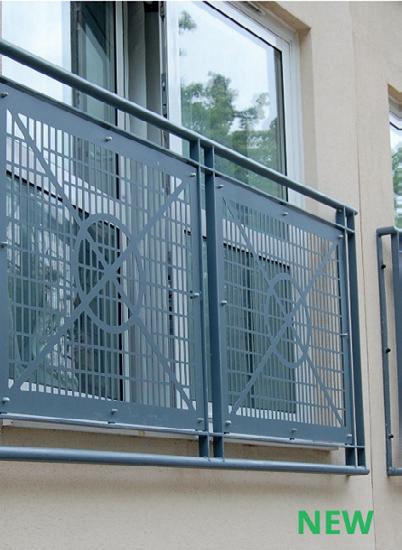
2 minute read
START WITH THE FINISH IN MIND
Richard Besant, Director at Powdertech (Corby), explains why considering the metal finishing process at the start of a design project will yield the best result in terms of coating appearance and integrity.
The outward appearance of a building influences its visitors, passers by and occupants in a variety of ways, both consciously and subconsciously, as it expresses the character and values of the owner and/or occupants of that building. First impressions count, influencing whether the viewer will want to use or work with that company, or live in that building.
Advertisement
Is it creative, sophisticated, traditional or radical? Importantly, is the building smart and well maintained? This last point will be greatly affected by the condition of the external materials and whether there is discolouration, flaking, chipping or rust staining.
Given the importance of final finish appearance, we are always surprised that this is rarely given due attention at the project start. Will the metal be powder coated, wet-painted or anodised? Even if this is clear, do the designers know how to ensure a finish that will look good and stay looking good for many years? Achieving an optimum, durable surface treatment on architectural metal elements, such as facade, soffit and cills, requires the application of simple design elements that should be carried out before the material arrives at the metal finisher. Not only will this result in the best possible surface finish but it will avoid time delays in addressing potential problems.
Although somewhat going against the grain of the creative freedom necessary for design, there are a few well-tested rules that need to be observed. These are not onerous and some are obvious but can easily be overlooked in the excitement of the creative process.
These rules include:
Metal design should eliminate water traps and allow runoff
Sharp edges should be rounded off to prevent the coating fracturing or thinning in these areas

Deep recesses in a metal fabrication should be avoided as the ‘Faraday cage effect’ can prevent the electrostaticallycharged powder from coating that area. Ideally, a recess should not be deeper than it is wide.
Suitable jigging points need to be incorporated into the design in order for the piece of metal to be suspended during powder coating
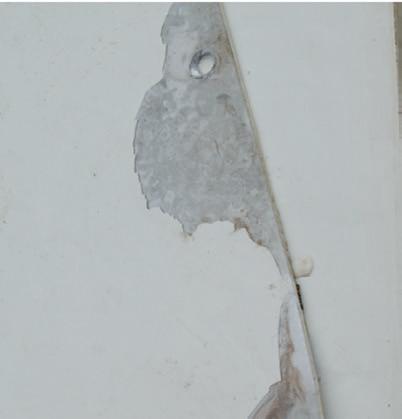
And, if galvanizing is required, then ventilation and drainage holes need to be included in the design.
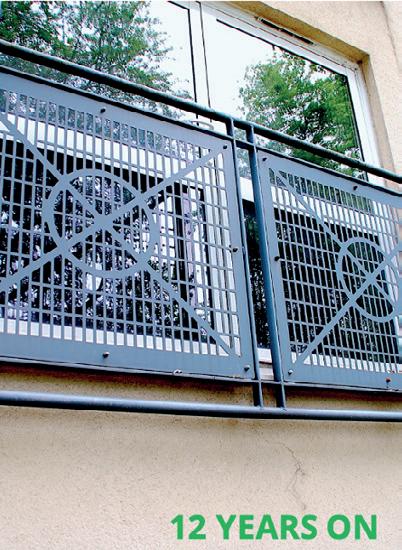
I recently had a conversation with a steel fabricator that neatly summarises the design, cost and performance triangle. The conversation went something like this. Fabricator: “I have made the balustrade to the architect’s drawing and need a 25-year guarantee.” A pause from me before I asked: “Are the edges of the steel chamfered to allow complete galvanizing, avoid coating fracture and make the finish much smoother?” www.powdertechcorby.co.uk
The reply was: “Do I need to?” “Yes,” I answered. “Can’t do that as it will cost too much,” they replied. “Can I still have a guarantee?” I will leave it to you to fill in the blank.
Our website carries details of design considerations, and designing for powder coating is also covered in the Powdertech RIBA-accredited CPD course found here https://www. ribacpd.com/powdertech-corbyltd/17632/overview.
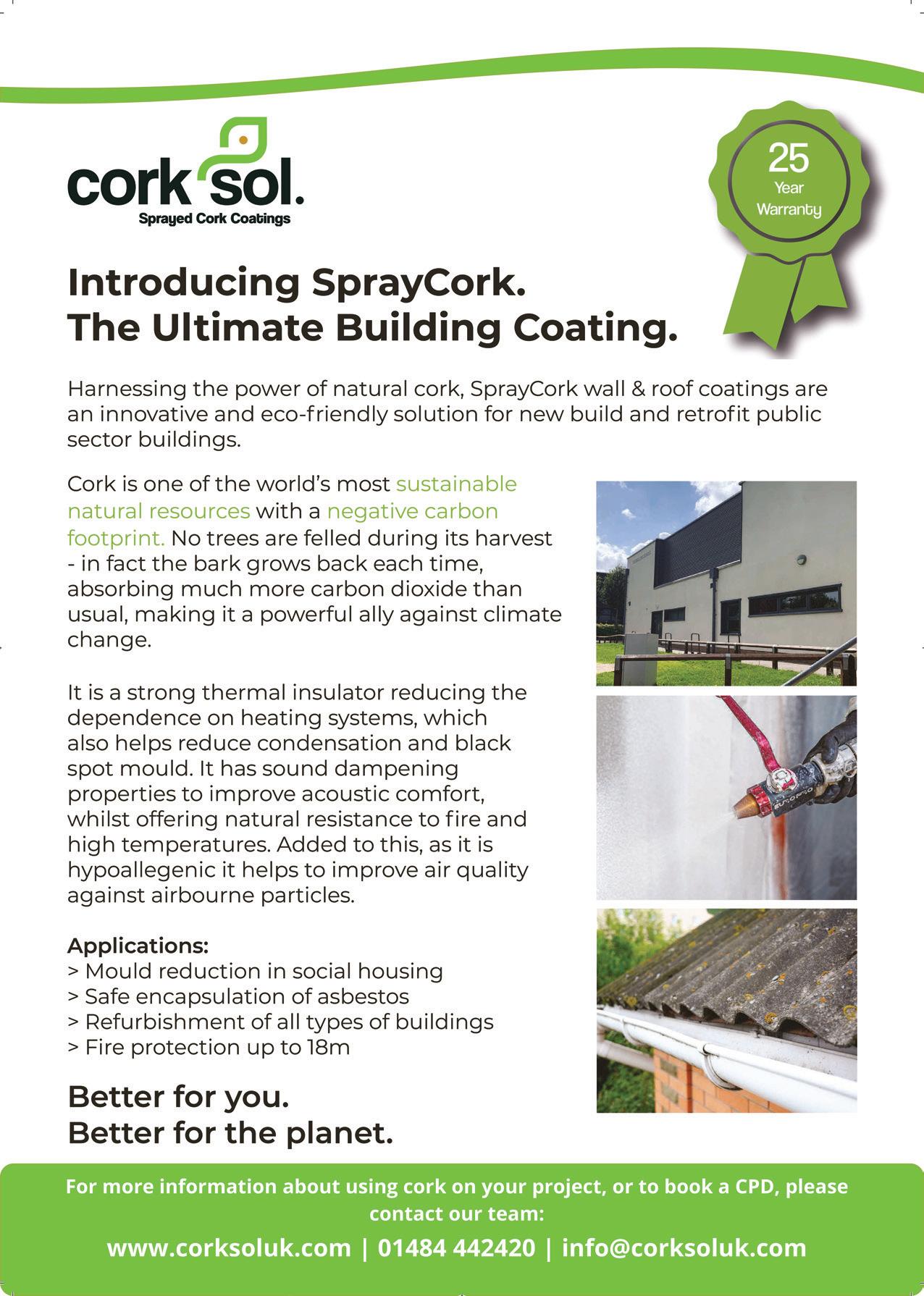