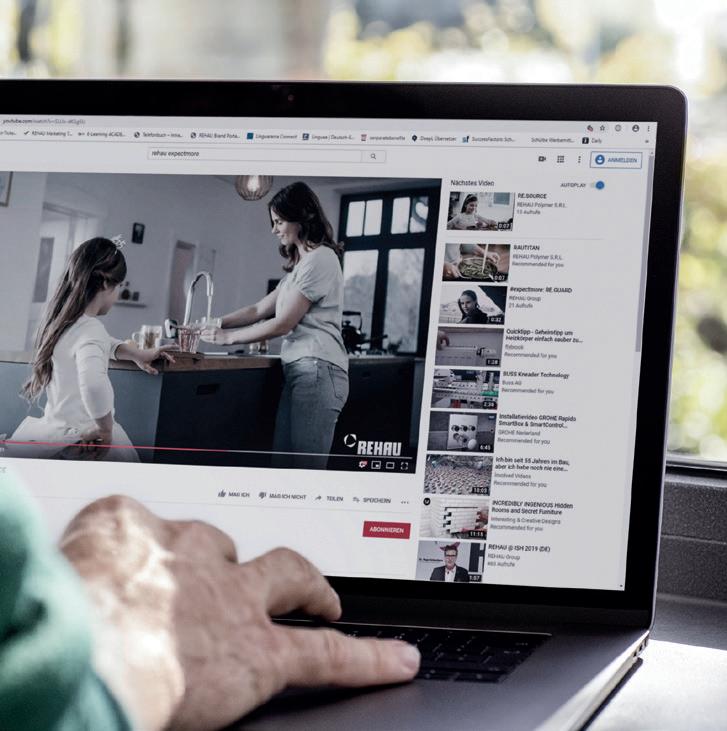
6 minute read
Doors, Windows & Balustrades
FUTURE HOMES STANDARD: NAVIGATING THE CHANGES
Energy efficiency and ventilation regulations in construction have come under the spotlight at local authorities since uplifts to Building Regulations under the Future Homes Standard. Implementing sustainability-minded changes is a pressing challenge for council specifiers, architects and contractors working on public sector projects. With this in mind, Steve Tonkiss, Head of Sales at REHAU, explores the legislation’s ramifications, and the role of doors and windows in ensuring compliance with the new, more stringent requirements.
Advertisement
The long-awaited Future Homes Standard (FHS) came into force earlier this year, causing significant upheaval for local authority construction. Specifically, clear ramifications are expected on the design and product selection of new-build local authority projects and the refurbishment of existing properties, to ensure new standards of ventilation and energy efficiency.
Though the standard’s launch date was advertised well in advance as part of the Government’s 2019 Spring Statement, this push for clarity has had the opposite effect. Namely, years of debate on the topic has led to conflicting information and advice. It is, therefore, understandable that specifiers at local authorities may not know where to start when looking for marginal gains in areas, such as windows, that will be required to hit the standard’s thermal performance targets.
Yet, in order to achieve the FHS’ requirements, local authority specifiers must first cut through the noise and understand what they entail, and why they have been implemented. The UK’s goal of achieving net zero by 2050 is the overarching reason behind the updated rules, with new homes built from 2022 needing to produce 31% less carbon emissions, and further drops of 75 to 80% expected by 2025.
Specifier steps
Consequently, architects, surveyors and specifiers working with local authorities are under pressure to consider new, sustainability-minded factors when choosing products for new-build or refurbishment projects. While all building components have a part to play in decarbonising structures, windows provide an especially effective avenue through which important gains can be made.
This can be seen in findings published by the Energy Saving Trust in March 2022, which demonstrated that installing high-performance double glazing to a semi-detached gas-heated property could result in annual savings of up to £175 and 410kg of carbon dioxide. Applied across larger local authority properties, these benefits have the potential to be further scaled up.
The key aspects of the FHS relating to windows are uplifts to Part L and F of the Building Regulations, pertaining to energy-efficiency and ventilation requirements respectively. Changes to Part L have involved optimising window U-values. Specifically, under the updated requirements, the target U-value for windows has been set at 1.2W/m2K, restricting the lowest specification allowable – the limiting U-value for SAP calculation – to 1.6W/m2K.
When it comes to doors in new builds, those with a glazed area greater than 60% must similarly achieve a target U-value of 1.2W/m2K, alongside doors below the 60% benchmark at 1.0W/m2K. Furthermore, replacement windows within existing dwellings must attain a Window Energy Rating (WER) of B or higher, with a maximum U-value of 1.4W/ m2K. Replacement doors with a glazed area larger than 60% must achieve a WER C, or B for those less than that figure.
Futureproofing
Importantly, these uplifts are part of a longer process – further technical consultation is expected on FHS requirements in spring 2023, and targets could be adjusted again. As such, it is vital to select frames and materials that offer best possible futureproofing. Of the options available, polymer has become an increasingly attractive choice, especially as the material eliminates the thermal bridging that can be a major issue in new-build properties insofar as heat loss is concerned.
Additionally, advances in frame foil technologies mean that project stakeholders can enjoy the performance benefits of polymer while convincingly imitating the aesthetic appeal of other materials, including aluminium and wood. Alongside this, it is important to note that polymer solutions already exist that meet and exceed FHS requirements, such as REHAU’s TOTAL70 window and door system, with the company’s GENEO solution able to meet Passivhaus requirements.
Appropriate ventilation
The significant upheaval in energyefficiency requirements under the FHS is mirrored in Part F of the Building Regulations, covering ventilation for both new projects and refurbishment works. Specifically, old windows with trickle vents must be replaced by windows that
have trickle vents that are at least the same size or larger and be controlled automatically or by the dwelling’s occupants.
Ventilation standards are contained in Part F of the FHS. As with windows’ energy efficiency covered in Part L, ventilation applies to both new housing and refurbishment projects. The ventilation standard states that old windows with trickle vents must be replaced by windows that have trickle vents that are at least the same size or larger and be controlled automatically or by the dwelling’s occupants.
If the frames being replaced do not have trickle vents, then the new windows must meet minimum Equivalent Air Area requirements (EQA) – the metric specifying the minimum amount of air passing through new vents. For existing buildings, approved under test conditions, a minimum EQA of 8000mm2 is specified for habitable rooms and kitchens in multi-floor dwellings, with 10,000mm2 required for single-floor dwellings. For bathrooms without a toilet or habitable rooms with continuous mechanical extract ventilation, excluding wetrooms, the EQA standard is 4000mm2 .
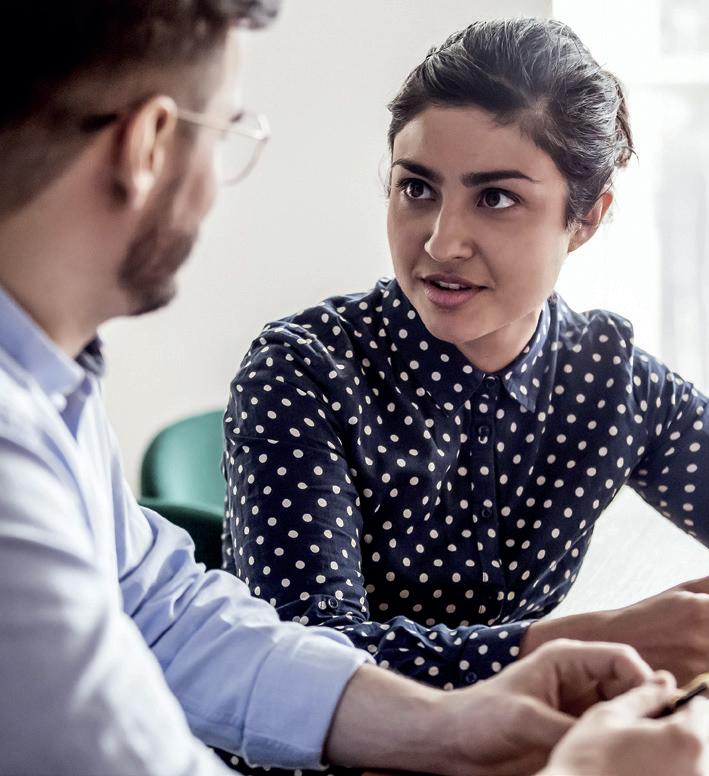
System types
Three types of ventilation systems are required for new builds – System 1, System 2 and System 3. System 1 is known as ‘natural ventilation,’ in which trickle vents are used in dwellings defined as ‘less airtight’ during design stage calculations – showing an air permeability higher than 5m3/hm2 at 50Pa. If airtightness tests are carried out after the build, air permeability must be higher than 3m3/hm2 at 50Pa.
System 2 uses continuous mechanical extraction, meaning trickle vents with a minimum EQA of 4000mm2 can be used in each habitable room. The amount of vents used on a property depends on the number of bedrooms – two more of the former are required than the latter (three for a one-bed project, four for a two-bed dwelling, etc.).
System 3 requires a mechanical ventilation system with heat recovery and no provision for background ventilators. Once the system type has been chosen, minimum EQAs can be implemented. For habitable rooms and kitchens in multiple floor housing, the EQA is 8000mm2. For single-floor (bungalow) counterparts, 10,000mm2 is required. An EQA of 4000mm2 is shared across bathrooms in either type of property, with no requirements for utility rooms or sanitary accommodation.
Additional assistance
The technical specifications with the updated FHS standards is causing disruption in public sector construction, with project stakeholders needing to keep track of upheaval across multiple building components. With this in mind, it is incumbent on solution suppliers to provide as much technical support as possible to architects, surveyors and specifiers working with local authorities if they are to remain compliant.
REHAU, for example, are offering free CPD courses to ensure specification teams are compliant and understand the new requirements for windows and doors. Alongside this, the organisation have developed a series of four fact sheets aimed at those working with architects, specifiers and surveyors, which aim to provide a brief introduction to the changes, projected timeline and targets. www.rehau.com
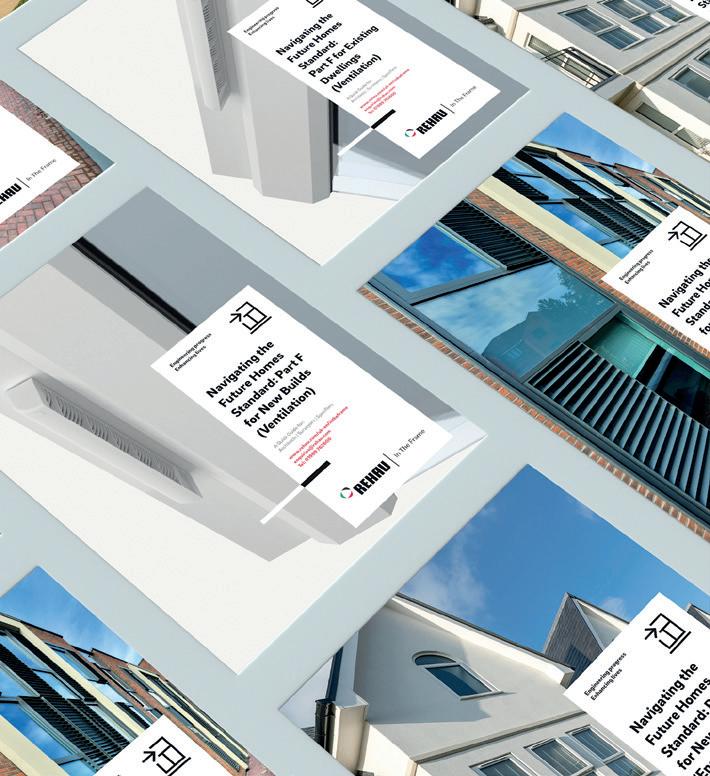