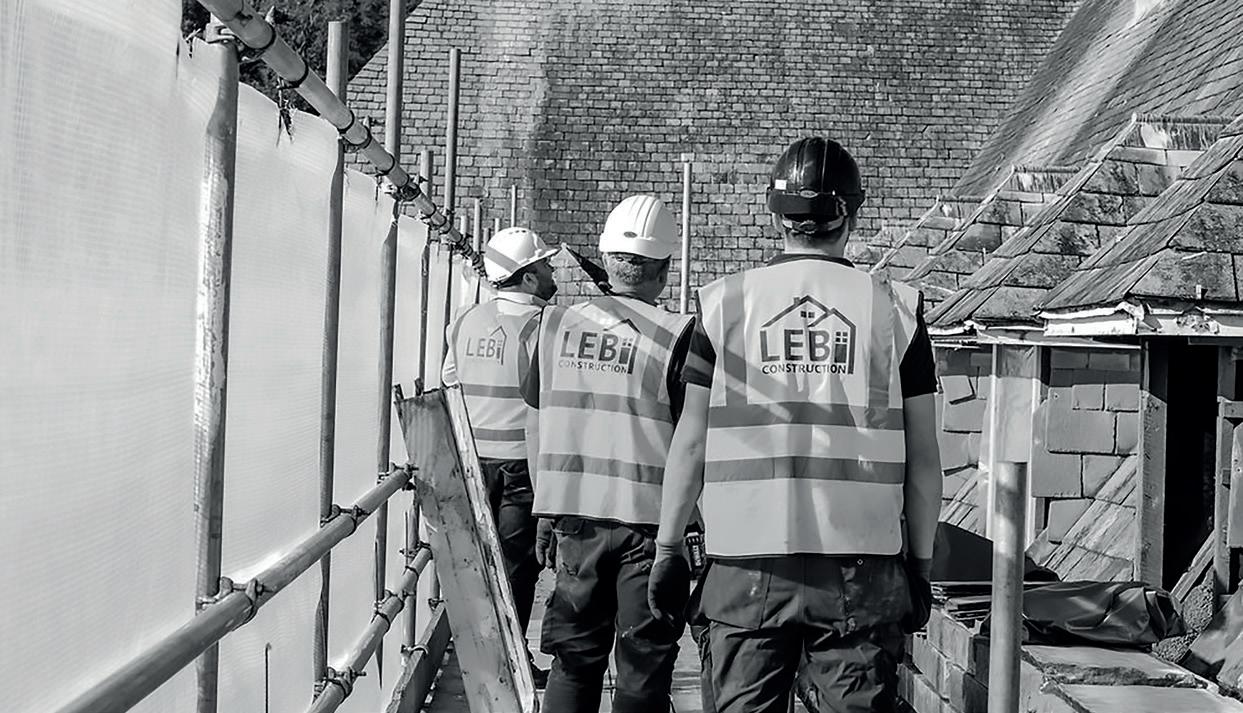
3 minute read
Legal & Business
from PSBJ July 21
SAFETY ACROSS THE SUPPLY CHAIN ON PUBLIC SECTOR SITES
Luke Baker, Managing Director of LEB Construction, discusses the need for all elements of the delivery chain to implement best practice health and safety protocols on public sector sites.
Advertisement
Health and safety should always be a top priority for all organisations involved in any aspect of construction. Over the past 18 months, that responsibility has been more urgent and complex than ever, with the need to keep both site personnel and the public safe from COVID-19, while continuing to manage the hazards and risks inherent in the programme. As a main contractor, LEB Construction is often also the designated principal contractor, which involves responsibility for all aspects of site safety. That includes ensuring risk assessments and method statements are thorough, as well as implementing measurable health and safety policies and practices. It also includes adjusting health and safety protocols in response to any changes – such as adverse weather conditions, for example, or revisions to the scope of works.
Since the onset of the pandemic, the need to respond in real time to changing health and safety considerations has never been greater. Not only have we needed to modify site set-up to enable social distancing, sanitisation and one-way systems, there has also been a need for health screening, avoiding bottlenecks in restroom facilities and preventing unnecessary visitors coming to site. Even more challenging than these requirements, perhaps, has been adjusting to unknowns. Changing lockdown restrictions and the potential for workers to be absent from site due to infection or trackand-trace self-isolation requests has created the potential for teams to be short-handed, which can create gaps in safe supervision or unsafe site behaviours in order to avoid falling behind schedule.
It is across all these scenarios that the role of the principal contractor is not simply to impose health and safety best practice but to actively collaborate and communicate with all supply chain partners. Only then can a genuine safety culture be delivered consistently throughout the site.
Where necessary, that must include flagging any challenges with the client and building additional time into the programme to enable both quality assurance and safety best practice. Even when the project in question is the refurbishment of an occupied building or requires handover within a missioncritical deadline, accountability for health and safety at every level is essential and should be integral to a best value delivery model.
With a problem-solving approach, an experienced team and effective collaboration, it should be possible to avoid the cost and disruption of overruns by identifying issues early and putting measures in place
Luke Baker
is Managing Director of LEB Construction, which he set up in 2009 after training as a Carpenter at Coleg Ceredigion, apprenticed to a wellrespected local builder.
to maintain progress, quality and safety. A main contractor that nurtures the trust and confidence of all supply chain partners, keeps the client up to speed and calls on the expertise of all involved to find solutions to safety challenges can avoid both risk and delays. At LEB Construction, we have been very fortunate to work in a region of Wales that has avoided the spikes in COVID-19 cases that have affected some areas of the UK, but effective health and safety management is not just about responding quickly; it’s also about anticipating risk. A collaborative culture is fundamental to risk management, both during the pandemic and beyond, so, for clients, principal contractors and supply chain partners, it should always be a priority.
www.lebconstruction.co.uk
