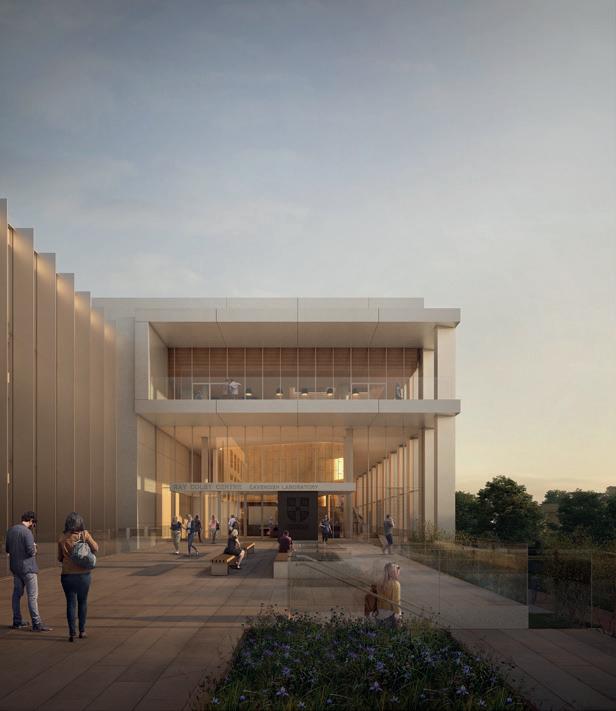
5 minute read
Floors, Walls & Ceilings

NORWOOD’S MODULAR EXPERTISE PROVIDES A SOUND SOLUTION FOR THE RAY DOLBY CENTRE
Advertisement
A key aim for both higher education providers and the corporate world is to create opportunities for academia and research to work collaboratively with businesses. There are advantages for both sides of the equation. For universities, it means opportunities for students and researchers to work on real-world projects and connect with potential future employers; while for companies, it offers a chance to shape future skills and benefit from knowledgeable specialists.
The challenge to delivering this aim is in creating an infrastructure that supports such collaboration. For many universities, developing a physical space for research and study that also provides an environment for private sector engagement has become a priority. At Cambridge University, a £250m development – the Ray Dolby Centre – has become the benchmark for such collaboration between education and business. Designed in Revit by nbbj and delivered in BIM by Bouygues UK, with specialist modular partitioning designed, manufactured and installed by Norwood, the new centre for research and collaboration will form part of Cambridge University’s physics department.
The development has been named after Ray Dolby, a PhD alumnus of Cambridge University, a former fellow of Pembroke College, an inventor and the founder of Dolby; the A/V company synonymous with sound recording. It has been co-funded by Dolby and seeks to continue his legacy of innovation by providing a world-leading facility for research projects that furthers learning and underpins commercial product development.
Safety and transparency
A noticeable trend in the design and construction of research environments is the move to make research as visible as possible and connect projects with the outside world. This is a key principle of the Ray Dolby development, which has been designed to showcase the innovation that takes place within the building to visitors and inspire students from across the university. The facility is high tech, with cleanrooms and controlled environments where research activities and experiments can take place, but the atrium provides a viewing gallery with a 2.85m-high, fire-rated glazed wall providing both segregation and safety.
The fire-rated glazed wall was part of Norwood’s £1.9m package on the Ray Dolby Centre project, which also included a 2500m2 walk-on ceiling, and design, manufacture and installation of a cleanroom partitioning system totalling 4080m2. To provide the safety protection required for the R&D areas, the glazed wall called upon the cleanroom partition specialist’s design expertise and UK manufacturing capabilities.
Alongside the goals of transparency and exemplary health and safety, the facility has also been designed to address any commercial sensitivities for the corporate projects under development in the labs and research areas. To this end, the glazing has been fitted with blackout blinds to enable any commercially-sensitive research projects to be protected.
Glazed partition
The fire-rated glazed wall was designed by the Norwood team and is the largest fire-rated glazed partition the company has ever created. The specification requirement was for 60-minute fire integrity and insulation to protect the atrium from fire and heat from any incidents within the cleanroom or lab areas, and to protect the research facilities from any fire and heat due to an incident in the publicly-accessible areas.
“The design process for the glazed wall not only needed to consider the safety performance criteria for the installation, but also aesthetics and buildability,” explains Josh Banister, Managing Director of Norwood. “The aesthetics are important because this is a showpiece development that will attract both students and commercial partners for the university. Buildability was essential across a wide range of considerations, including structural loading, safety on site during the construction phase and the logistics of getting such a huge glazed wall into and out of the building.
“Our expertise in designing modular systems, and our joined-up service across design, manufacture and installation, enabled us to overcome the buildability challenges of this aspect of the specification with a modular solution, while answering safety and aesthetic requirements.”
The 70m span of the glazed wall was manufactured in 2.85m-high panels and was independently tested by UKASaccredited fire safety services specialist, Warringtonfire, prior to installation by the Norwood team. With each glazed panel weighing 200kg, installation of the fire-rated glazed wall was meticulously orchestrated by Norwood.

Flexible solution
The 2500m2 walk-on ceiling designed and installed by Norwood as part of the project has a 100kg/1200mm2 load capacity to enable ease of maintenance for the complex building services required by the labs and cleanrooms below. The ceiling has been installed at two levels, 3.2 and 3.5m, to accommodate the varying services and fit-out specifications across the building.
Norwood was also responsible for design, manufacture and installation of a cleanroom partitioning system totalling 4080m2. Flexibility was a key element of the specification for the facility to allow research spaces to be reconfigured for different projects over time, so Norwood’s Mediline fully-demountable modular cleanroom partitioning system was an ideal solution. The company tailored its standard 1000mm modular cleanroom partitioning system to meet the required 1200mm specification and provide the required acoustic and firesafety requirements. Part of the design requirement for the project was the ability to reconfigure the internal space around the changing needs of the university and different research and commercial projects. To this end, the Norwood team also developed a bespoke T-bolt system to enable easier reconfiguration of the cleanroom layouts during the lifecycle of the building. The system enables shelves to be mounted quickly and easily above or below the vision panel aligned to research teams’ requirements.
Jordan Taylor, Project Manager at Bouygues UK, commented: “Norwood has worked collaboratively with our team to design a bespoke solution for the exacting specification of this unique building. The solution the team has developed brings together the company’s tried-and-tested expertise in modular acoustic panelling systems for cleanroom and advanced engineering environments, with an agile approach to customised design and a focus on the purpose of the finished building.
“The fire-rated glazed walls are a showpiece element of the project and Norwood was able to offer a turnkey solution from concept to installation. With the walk-on ceiling now also complete and the cleanroom partitions well underway, Norwood is helping us to make good progress on the build and is contributing to the versatility of this innovative research facility.” www.norwood.co.uk
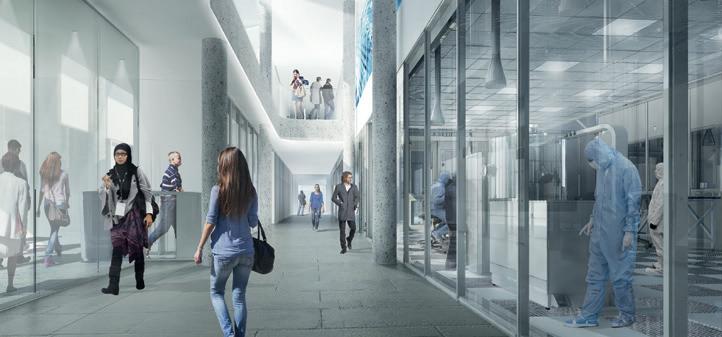