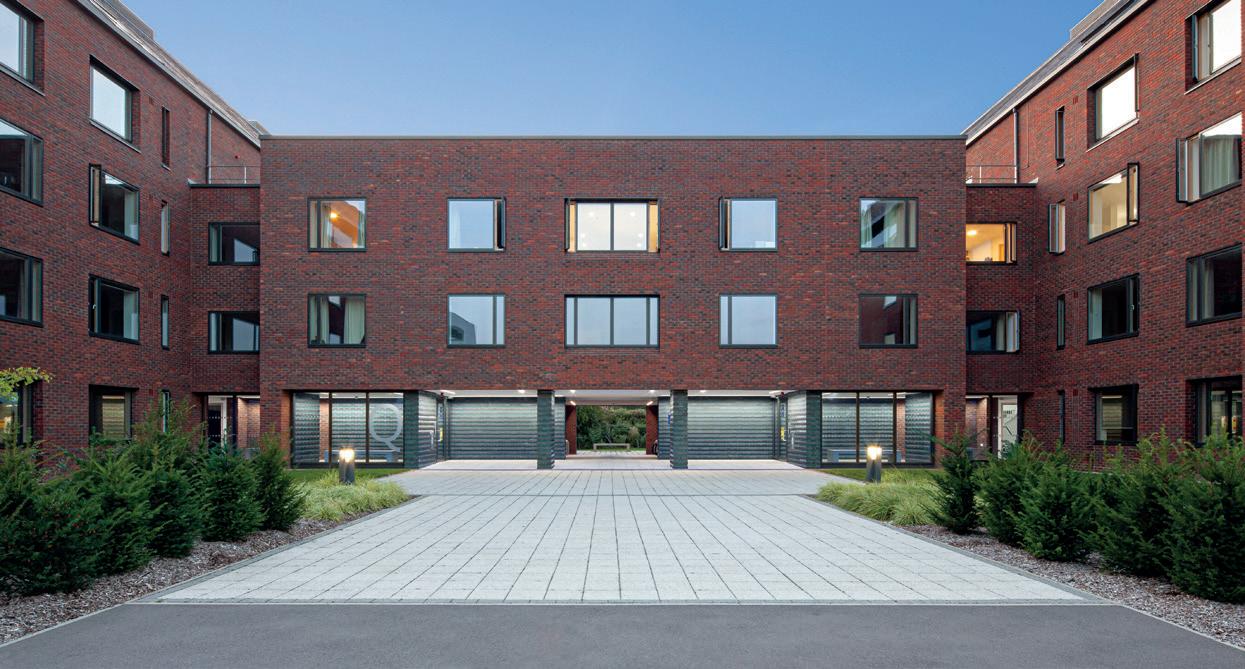
5 minute read
Bricks & Blocks
CHOOSING AND PROCURING CLAY BRICKS
Steve Wharton, Technical Manager of the Brick Development Association, talks about the issues of material shortages in the construction sector and how to reduce or avoid them when choosing clay bricks.
Advertisement
At the moment, we seem to hear almost daily about more and more material shortages as the UK continues to recover and open up after over a year of lockdowns and other restrictions. The additional problems of a shortage of experienced site labour and lorry drivers is also exacerbating the issue.
With construction activity levels at a seven-year high, what can we all do to ensure that the materials you need are there when you need them?
Common sense prevails and hence, planning and communication are essential to implementing best practice and will help to ensure that the supply of clay bricks for your project does not impact your construction programme. It will also help minimise confusion and make for a more streamlined procurement process.
The concept design stage is likely the first point in the project lifecycle, when the project team will consider the specification of the external materials. It may seem early in the process to engage with a clay brick manufacturer or supplier but making key decisions at this stage can help smooth the design and procurement process. Remember that clay bricks are available in thousands of different combinations of colours and textures.
There are two main routes of engagement with regards to the initial specification of bricks, either direct to the clay brick manufacturer or through a supplier such as a brick factor or builder’s merchant.
Both options have their positive and negative considerations. The clay brick manufacturers will have a better understanding of their product whereas suppliers will usually be able to provide a range of bricks from multiple manufacturers.
Whichever route you decide to follow, a good starting point for procurement is often through local clay brick manufacturers. It is likely that they will have a history of supplying the local area and will be able to provide great knowledge and guidance on a suitable clay brick specification. Key things to consider are:
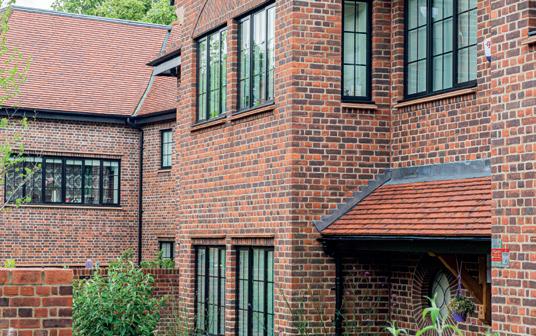
Preferred colour, size and texture of the clay brick. Ask for samples, if required.
The type and colour of mortar to be used and its profile
The brick bonding to be specified such as stretcher, header, Flemish, English, honeycomb or textured
Consider whether specialshaped clay bricks and sizes will be required early in the design process. Most clay brick manufacturers produce the full range of special shapes which will complement the facing bricks and provide attractive features. Some of the more commonly-used standard specials are usually stocked but others will frequently be made to order. It is essential that early engagement with the manufacturer takes place to discuss purpose-made nonstandard specials. Due to the different manufacturing process, some specials can have subtle differences from the standard brick. A ‘cut-and-bonded’ specialshaped brick or contrasting colour may be a quicker option.
Clearly establish the ‘Exposure Zone’ for the brickwork to determine an appropriate specification to ensure suitability for the application Obtain preliminary cost information to source the clay brick options at an appropriate range of values Draft an initial ‘Construction Strategy’ including planning and preliminary start dates
Agree on the likely volumes of clay bricks (including a wastage factor) to be used. Ensure that material delivery schedules are supplied and updated as required.
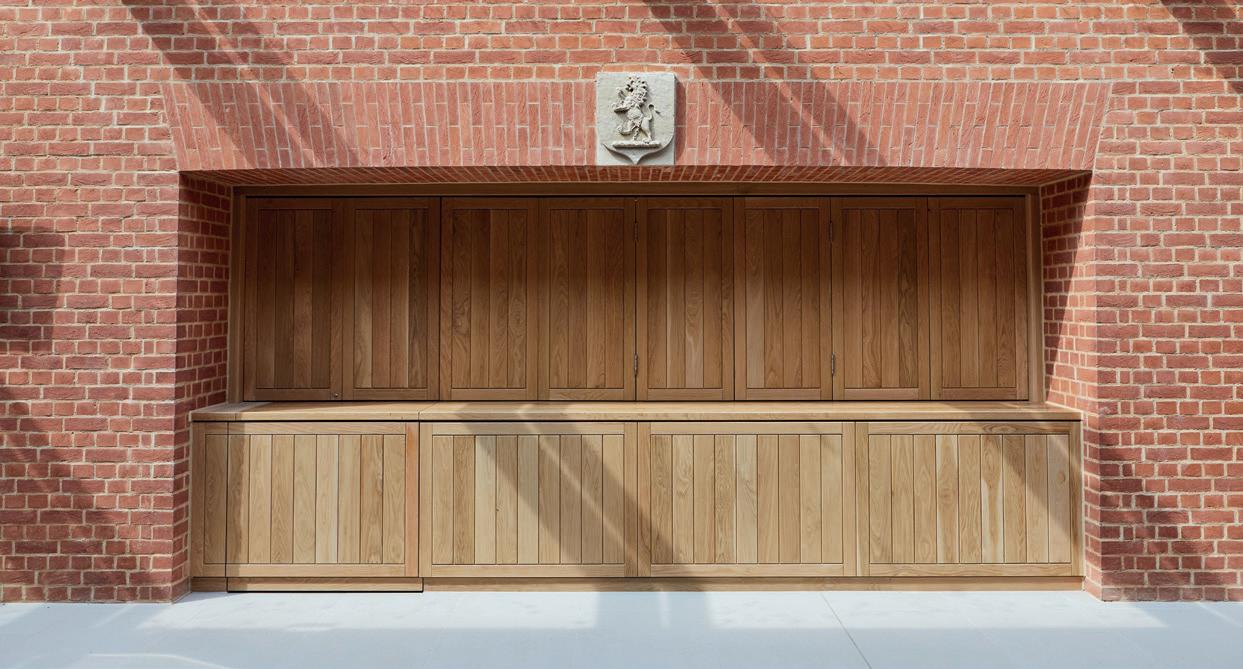
A clay brick specification should ideally be narrowed down to a couple of options, which satisfy all of the necessary specification, budget, buildability and logistical requirements.
Physical samples of the chosen clay brick options should be supplied and a sample reference panel will possibly be constructed on the proposed site. Sample reference panels provide an essential benchmark should any issues arise during the brickwork programme. Panels should be built in a location to be maintained for the length of the project and will provide an agreed level of material characteristics and workmanship.
The clay bricks for the reference panel should be reasonably representative of the average quality of the whole order to be delivered.
The panel should be a minimum of 1m2 and ideally built by the successful brickwork contractor. The panel should include any particular details or features and should be reviewed at a distance of 3m.
Review the design to consider any potential buildability or logistics issues which could affect the procurement. For example, a lack of storage space on the site, which may necessitate ‘just-in-time’ deliveries. Always ensure that delivery schedules and a site storage plan have been agreed. If required, ensure good liaison with the suppliers of the ancillary components to ensure specification compatibility including wall ties, tension straps, hangers, brackets and bed joint reinforcement.
Determine whether any elements of the design would benefit from being pre-fabricated, such as areas of complex geometry, arches, lintels and chimney details.
Also consider how the clay bricks will be supported and whether the structural solution will affect the procurement. For example, a brick support angle may require a rebated stretcher (Pistol Brick).
Your preferred clay brick manufacturer will be able to confirm lead times for your preferred brick. This information should be incorporated into the procurement programme to determine a date for order placement which will ensure that the bricks are delivered when needed on the site.
Discuss potential phasing of the development with your preferred manufacturer/supplier. It may be that it is preferable to place a single order for the full quantity of bricks to complete a development. This will help ensure that the bricks are procured from a single batch to minimise the potential for variation.
The ‘Bill of Quantities’ should identify the quantity of brickwork required including wastage and preliminaries. A brick calculator can be found on the BDA website to assist with determining quantities. Generally, a square metre rate is given for standard brickwork areas – linear metre rates and quantities are also used for special elements. www.brick.org.uk
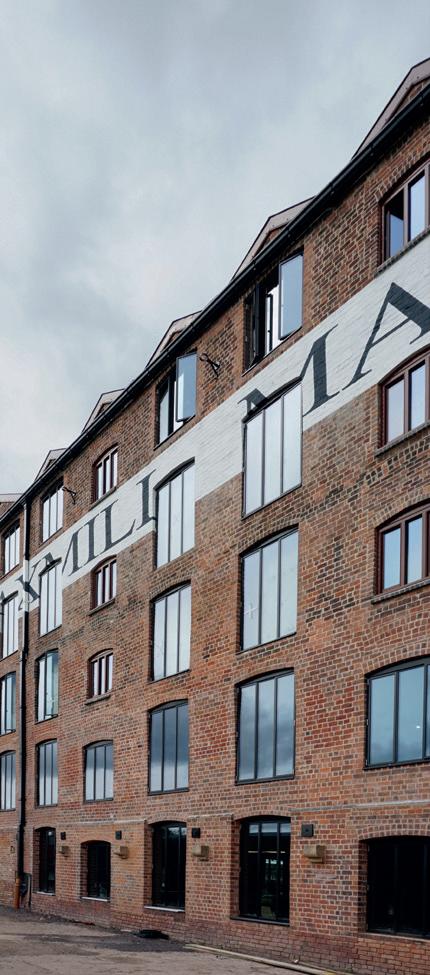