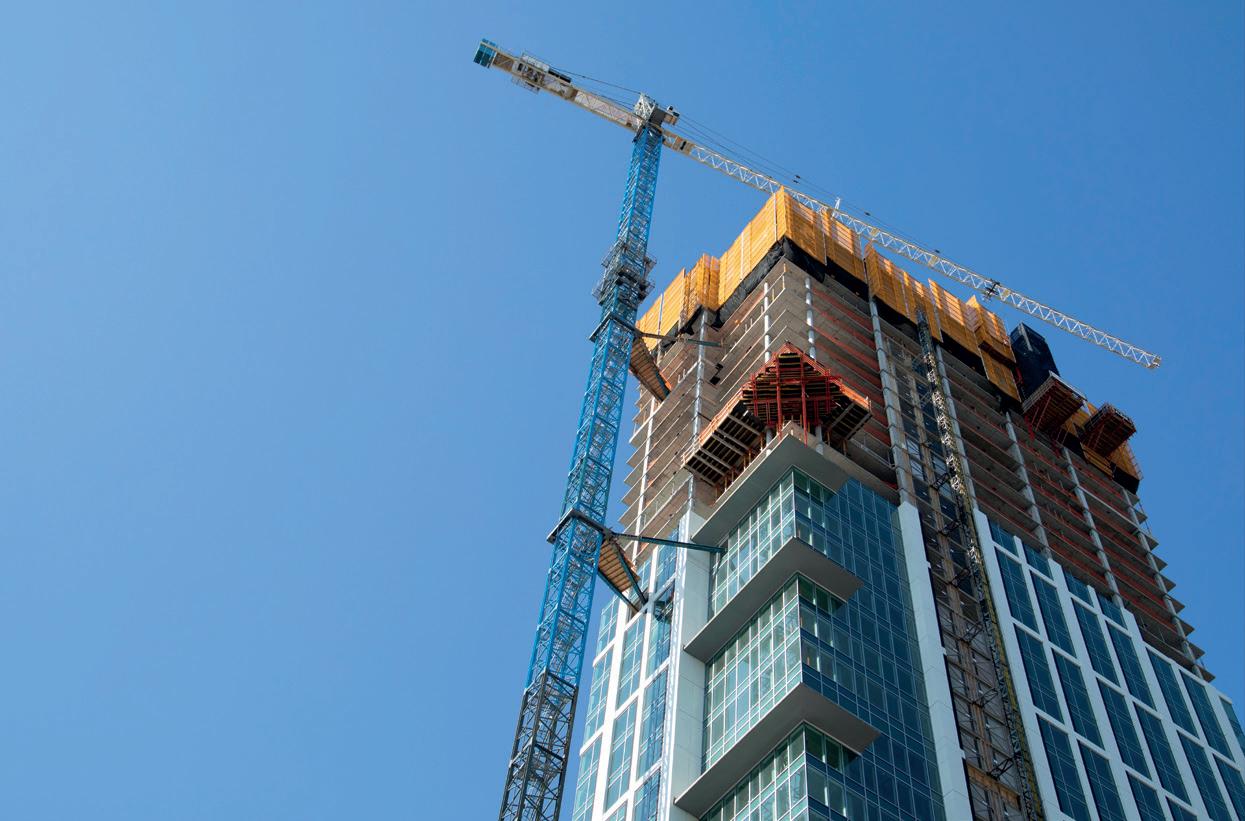
4 minute read
MMC
MMC WHY MODERN METHODS OF CONSTRUCTION AND DIGITAL TOOLS GO HAND IN HAND
It’s no secret that the events of the last two years have accelerated the rise of digitalisation like never before, with businesses pushed to discover new efficiencies and ways of working. As a result, many are realising the growing importance and potential of the digital world in keeping us all connected and running businesses more efficiently.
Advertisement
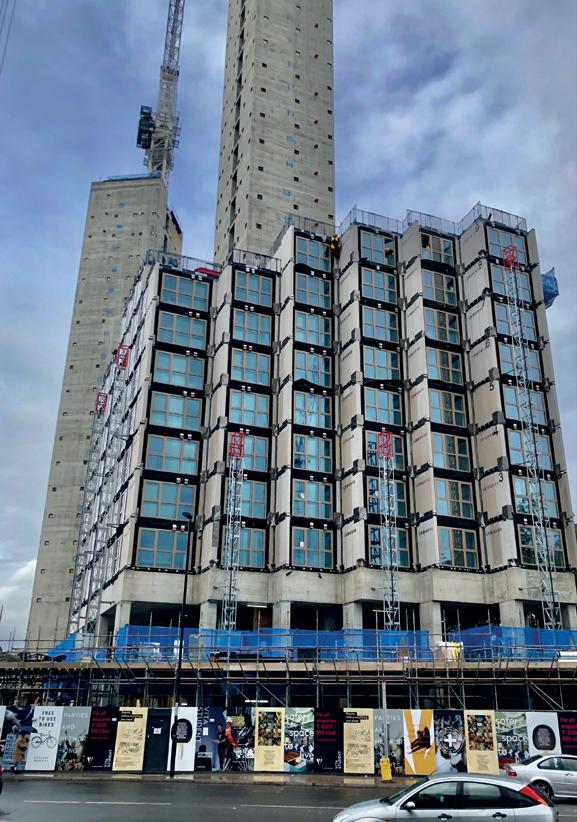
©Hamish Champ T he construction sector is one that is increasingly turning to technological innovation and digital tools to tackle the challenges the industry faces such as the drive to improve standards around quality, safety and performance, and the need to reduce carbon emissions in both construction and operation.
There are two main routes to achieving this, which both rely on the adoption of technology: adapting traditional practices or developing and testing new approaches. Modern methods of construction (MMC) and offsite construction fall into the latter, with a focus on the use of manufacturing techniques and standardisation to achieve better project outcomes. It is here where digital tools can make a big impact.
The digital side to MMC
The adoption of MMC will significantly transform the industry, offering the potential for more efficient, safer and sustainable alternatives to traditional methods. With problems around skills shortages and the rising cost of materials, we could see a very different construction industry, with a more diverse workforce and an increase in product innovation.
Offsite manufacturing techniques need digital practices at their core. This can cover a range of needs, from efficient ways to design and collaborate, improved quality assurance during production, and ongoing management of assets.
Get this right, and the industry will be able to meet the rising demand in sectors, such as housing, healthcare and education at scale, and improve the way we build, delivering greater value for communities and the taxpayer.
An offsite approach is already endorsed by the Government, with the Construction Playbook calling for greater collaboration, carbon reduction and digitalisation via this route. The current consultation on the Product Platform Rulebook, via the Construction Innovation Hub, also shows that this is the future direction of travel.
A perfect match
An area where MMC goes hand in hand with software solutions is that designs can be tested digitally and optimised in virtual and pre-production environments before going to site. The repeatability and standardisation of a manufacturing-led approach makes it perfect for this approach.
If data is accurately collected and collated during this process, it allows for greater measurement and validation when it comes to performance too, increasing our understanding of how built assets operate when comparing design and reality.
This means that we should see more effective and precise resource planning to avoid material wastage, reducing both the need and cost for labour and equipment. This, in turn, reduces the carbon footprint of the construction process in tandem with the offset that can be achieved from an efficient offsite manufacturing process.

Bringing people together
By utilising MMC in combination with software solutions, such as Bluebeam, project teams can communicate and collaborate in real-time across multiple locations and preserve important project data throughout the process from initial design through to the occupation and management of the final building.
This boosts transparency, encourages shared learning and provides an audit trail for every step of the project, helping from a compliance perspective. This makes it much more likely that potential risks and issues are identified and mitigated early on, avoiding costly delays or mistakes and resulting in better value and higher quality projects.
It also helps organisations to achieve a long-lasting ‘golden thread’ of information through fullytraceable digital records. This enables record keeping of what products and material specifications were used on projects, helping with ongoing maintenance, building a deeper understanding of performance, and allowing for greater risk management should any problems occur with products or if guidance or legislation changes.
It shows just how vital digital tools are when it comes to safeguarding the future of the built environment and its occupants, allowing construction professionals to meet the requirement for improved levels of asset information, as per the recent Building Safety Act.
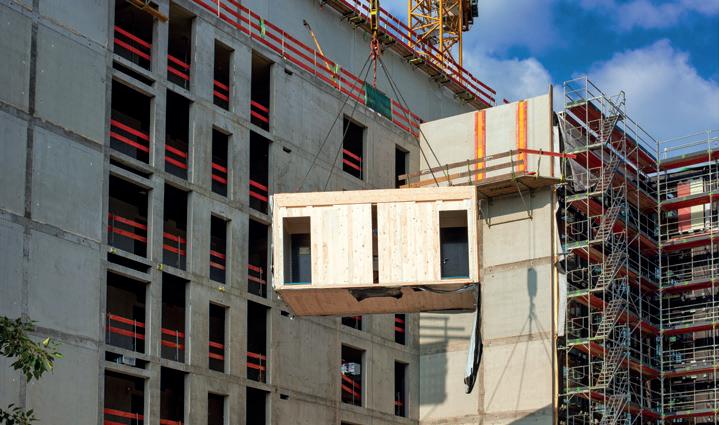
A model for the future
The construction sector needs to change the way it procures to support investment in MMC and digitalisation if it wants to tackle rising costs and supply chain disruption whilst increasing collaboration, value and sustainability.
By fully utilising and embedding the range of digital technologies in combination with MMC approaches, it is possible to standardise the industry’s approach to generating and classifying data, data security and data exchange.
Whilst technology doesn’t have all the answers, it is crucial that momentum continues to build on the uptake and investment of digital technology, strategies and skills to deliver rapid, high-quality, lowcarbon buildings that will stand the test of time. www.bluebeam.com/uk