Gal Shachor
2021/22AssociationArchitectural14ExperimentalSEAWEEDCOMPOUNDINGDevelopingacarbon-negativebiodegradableseaweed-basedbuildingmaterial
BOOKTS
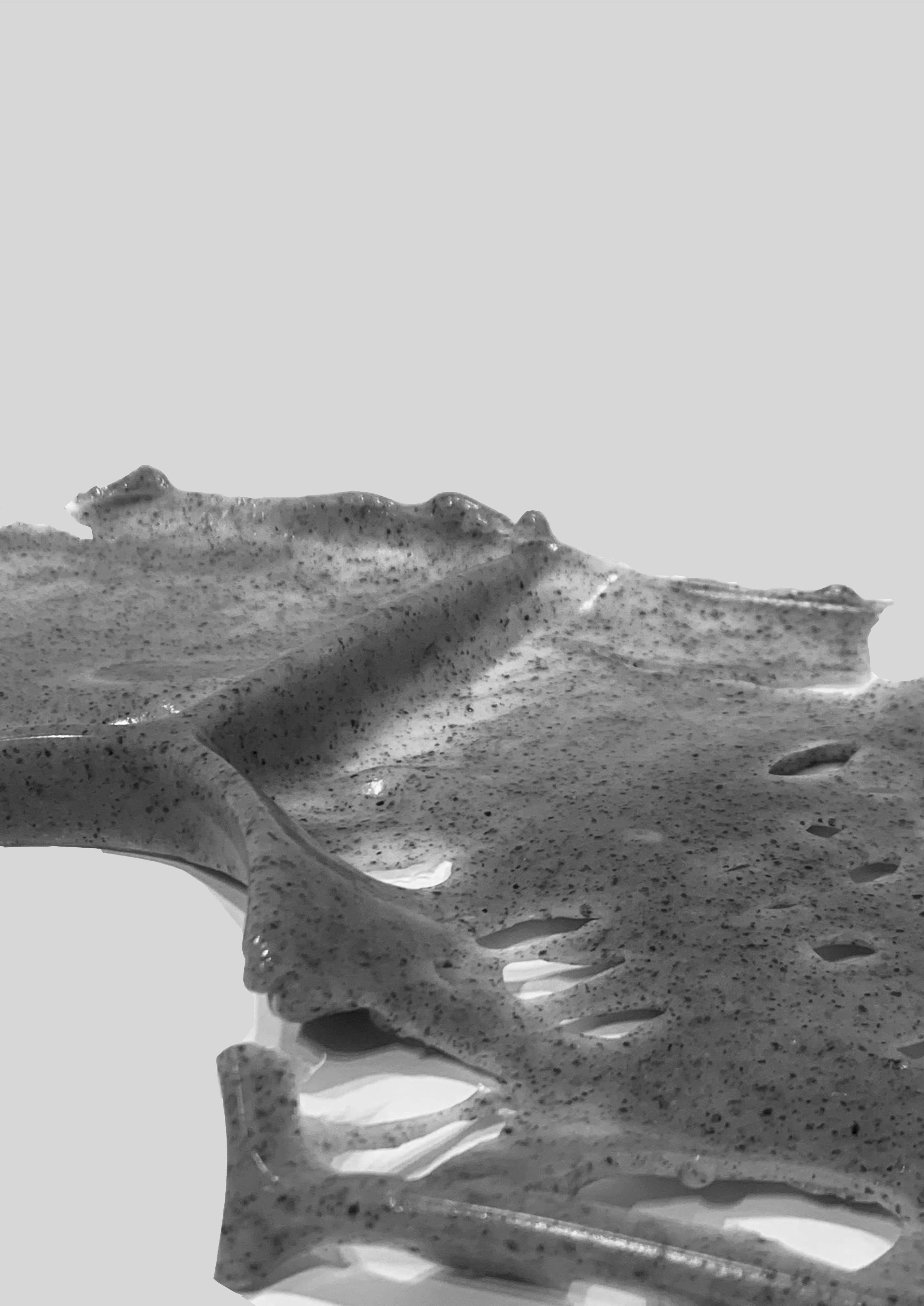
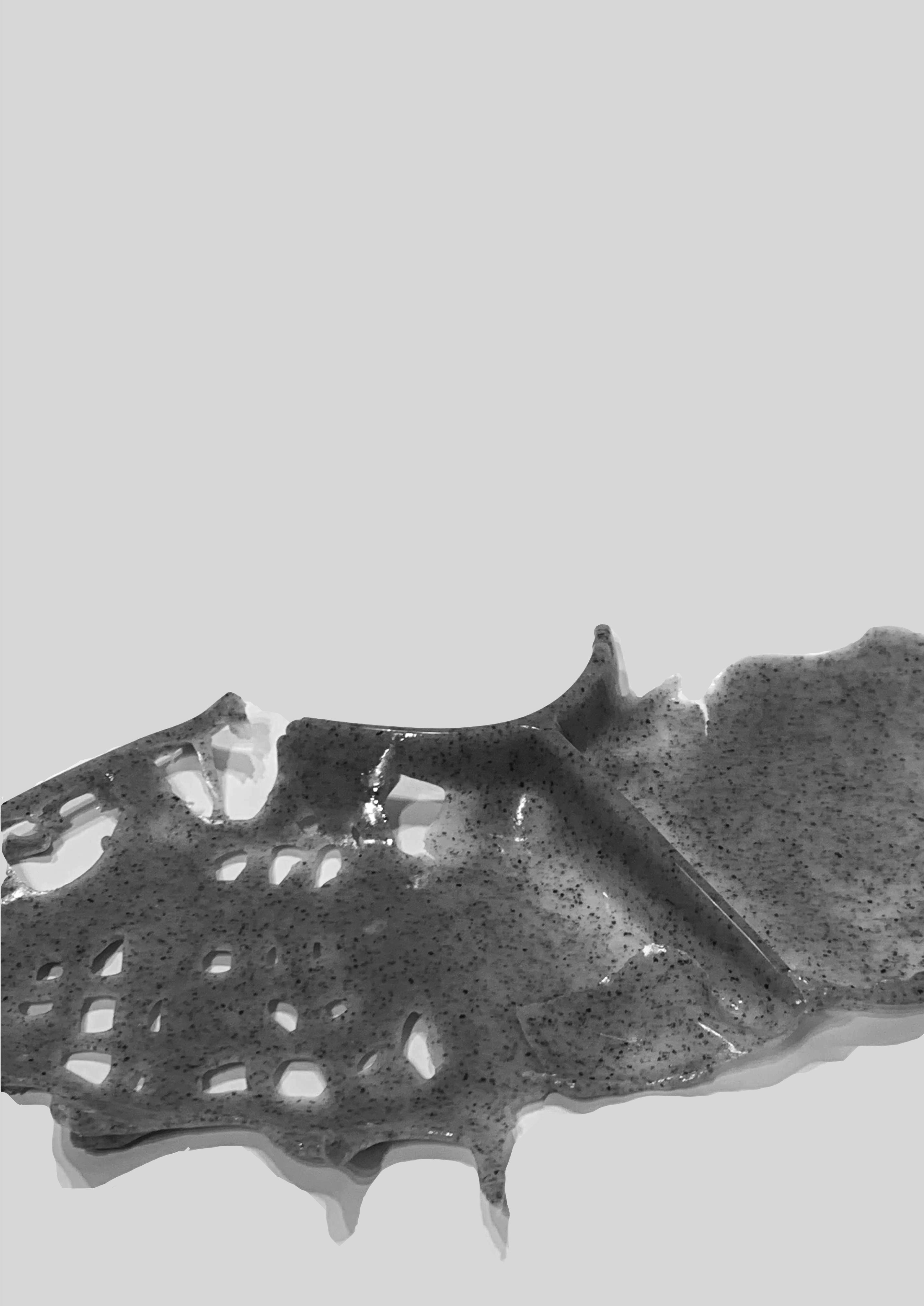
1.2 Seaweed industry in Scotland Scotland 40-4542-434544
2.2 Properties
Chapter 05
3.1 Ultimate tensile strength
Artefact - Testing the applicability of the material
8.1 Attaching the seaweed compound to other materials 8.2 Artefact - narrative and structure 8.3 Apply and assemble a system on site 80-8388-9186-8784-8578-7976-7774-91
7.3 Industrial Heritage of Edinburgh Corn exchange building and former Gas station 36-3932-3528-3126-2722-392425
CONTENTSOFTABLE 8-96-7
Ts Projectstatementessentials 14-1512-1310-15
9.1 Site damage report - Mapping opportunities for design 9.2 Interpretation of material experiments to interventions
Chapter Seaweed022.1
6.2 Potential uses catalogue Architectural application 104-107102-123108-111114-117112-113118-123
9.4 Maintenance as opportunity for design
Chapter 03 Material Experiments part I
Chapter 04
4.2 Algae Dress - Carbon neutral fabric 16-2118-192021
Morphology and anatomy
9.5 Details and application systems of the seaweed compound 98-10192-10194-9596-97
7.6 Seaweed factory - Reversible maintenance
2.3 Seaweed Benefits as a building material 70-7368-6966-73
9.3 Refurbishing the yard - new industry
3.3 Starch experiment - tensile and surface strength
Material Experiments part II
From slurry to composite material
5.2 Webbed structure - Elasticity
5.3 Casted joint, webbed structure - Elasticity Layering - Strength A study of joints 3D robotic printing - Strength
3.4 Creating new properties
3.5 Creating new material
5.4
5.5
5.6
5.1 Vessel prototype - Strength and translucency
House - responsive design
Chapter 011.1 Vernacular Architecture and Local Industries
7.2 Master plan - A cyclic holistic cleansing system 7.4 Existing Site 7.5 Preparing the building for the flooding
3.2 Seaweed, starch and surface tension
Case Studies4.1Shiver
Chapter 08
4.3 Earwig and the art of Origami - learning of mechanism
3.6 3D Robotic printing 64-6558-6356-5754-5552-5350-5148-4946-65
Chapter Maintenance09 as opportunity for design Between the controlled and the random
5.7 Adaptation and optimization of the robot
Chapter 07 Site: Leith,7.1EdinburghFlooding forecast of Leith
Chapter 066.1 Material data sheet
This seaweed-based compound can be 3d manufactured by 3d robotic printing and molding in different methods.
TS STATEMENT
Modifications of the robot have been done to get ideal conditions when printing. Examining the potential of this biodegradable material that has a short life span as a relevant solution to challenges of the 21st Examiningcentury.
An iterative process of robotic printings has been done to optimize and adapt the robot to this specific material’s needs and properties.
This TS is about developing a carbonnegative seaweed [Laminaria - Kelp] based material and implementing it into architectural Compoundingapplications. Seaweed [Laminaria - Kelp] with other bio-materials and polymers to produce a carbon-negative biodegradable Experimentingmaterial. with the compound’s properties [strength, elasticity, and transparency] to use it as a building material of the 21st century.
a design system that responds to environmental conditions – in this caseflooding due to increasing global temperature and rising sea levels. For the purpose of this TS, I will be working on a system that would respond to a flooding forecast in Leith - the port district of ThisEdinburgh.TSwill investigate the potential of such a system as a cyclic manufacturing process, with the seaweed compound as a main biodegradable building material.
PROJECT STATEMENTKEYWORDS
Time-specific structure

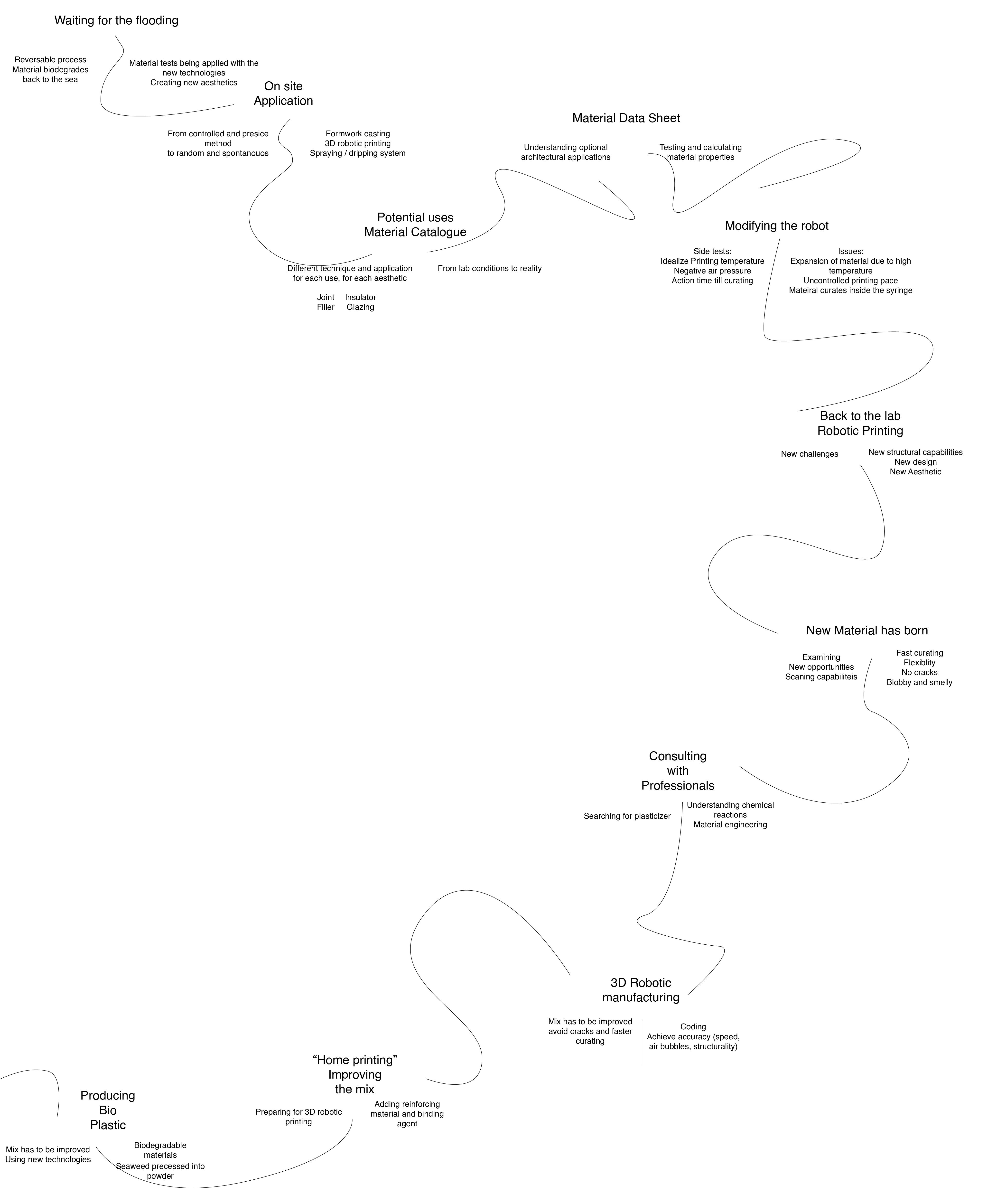
By 2030, much of Leith - the port district of Edinburgh - would be submerged by rising sea levels due to increasing global Thetemperatures.projectworks with the accepted predictions of the flooding forecast and would prepare the building for flooding, suggesting a cyclic system –starts and ends in the sea. In the years up to that deadline, parts of the existing building would be gradually replaced with a carbon-negative seaweed-based Formaterial.thatneed, a new 21st-century industry would be created. As the building slowly deteriorates over time, more and more parts would be replaced by seaweed-based Asmaterial.thematerial has a short life span, constant maintenance and renew would be needed – and constant production and process of the material. This way, the moments of the necessity of maintenance become opportunities for design. The properties of the material, together with new technologies, create new symbolizingaesthetics,thechallenges and the values of the 21st century.
QUESTIONSGUIDING
Do we need to have the intention to preserve a building as long as possible? What if we suggest a shorter life span of a building – by using biodegradable materials that may be site-specific, systemspecific, and time-specific?

BiodegradableLifePreservationBioplasticCarbon-negativeSeaweedspanmaterials
Responsive design
CHAPTER 01 SCOTLAND 1.1 Scotland Vernacular Architecture and Local Industries 1.2 Seaweed industry in Scotland
1.1
Getting familiar with local materials, building typologies, and industries was the main goal of the trip to Scotland. The seaweed industry was discovered not only as a rich history industry in the highlands of Scotland but also as one with a big potential to integrate and apply with other new industries such as the building industry. Seaweed is a fleshy, flexible, strong, and high-rate carbon sequestrating organism, and its potential uses are yet to discover.
SCOTLAND 13
Scotland A Journey following Local Industries, Materials, and Building Typologies
Arnish Point Industrial Estate, Hebridean Seaweed Company
New map for Scotland | Following the seaweed industry
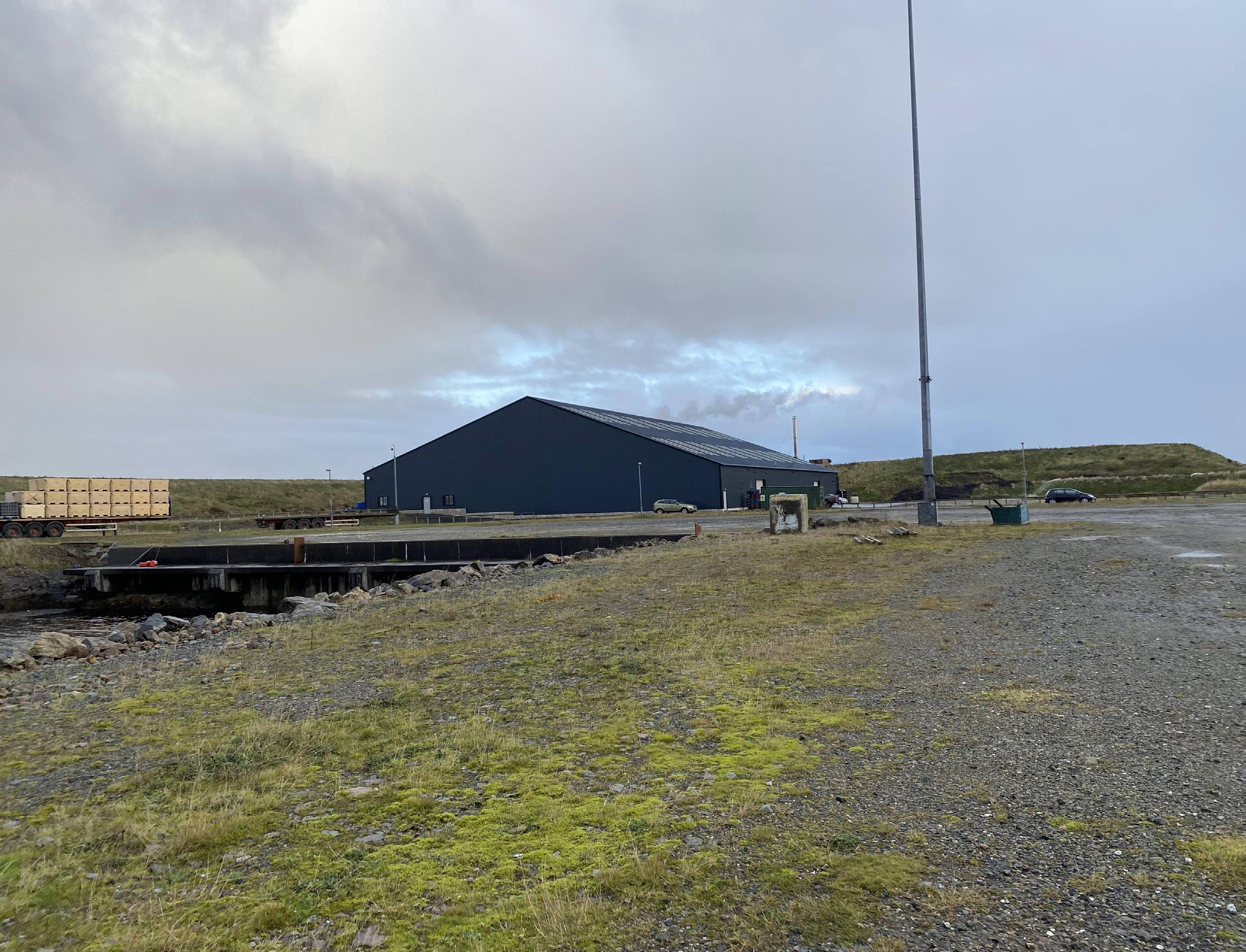
The highland clearances were a forced eviction of inhabitants of Scotland’s Highlands and western islands from the mid-tolate 18th century to the mid-19th Theycentury.were primarily conducted so that landowners could increase their income by repurposing the areas of the Highlands and western Scottish islands for sheep and cattle
We
SCOTLAND 15
Asfarming.aresult, the seaweed industry also started to flourish. of the 21stcentury industry? need to
Isle of Skye Aerial view | Scottish local industries and vernacular typologies
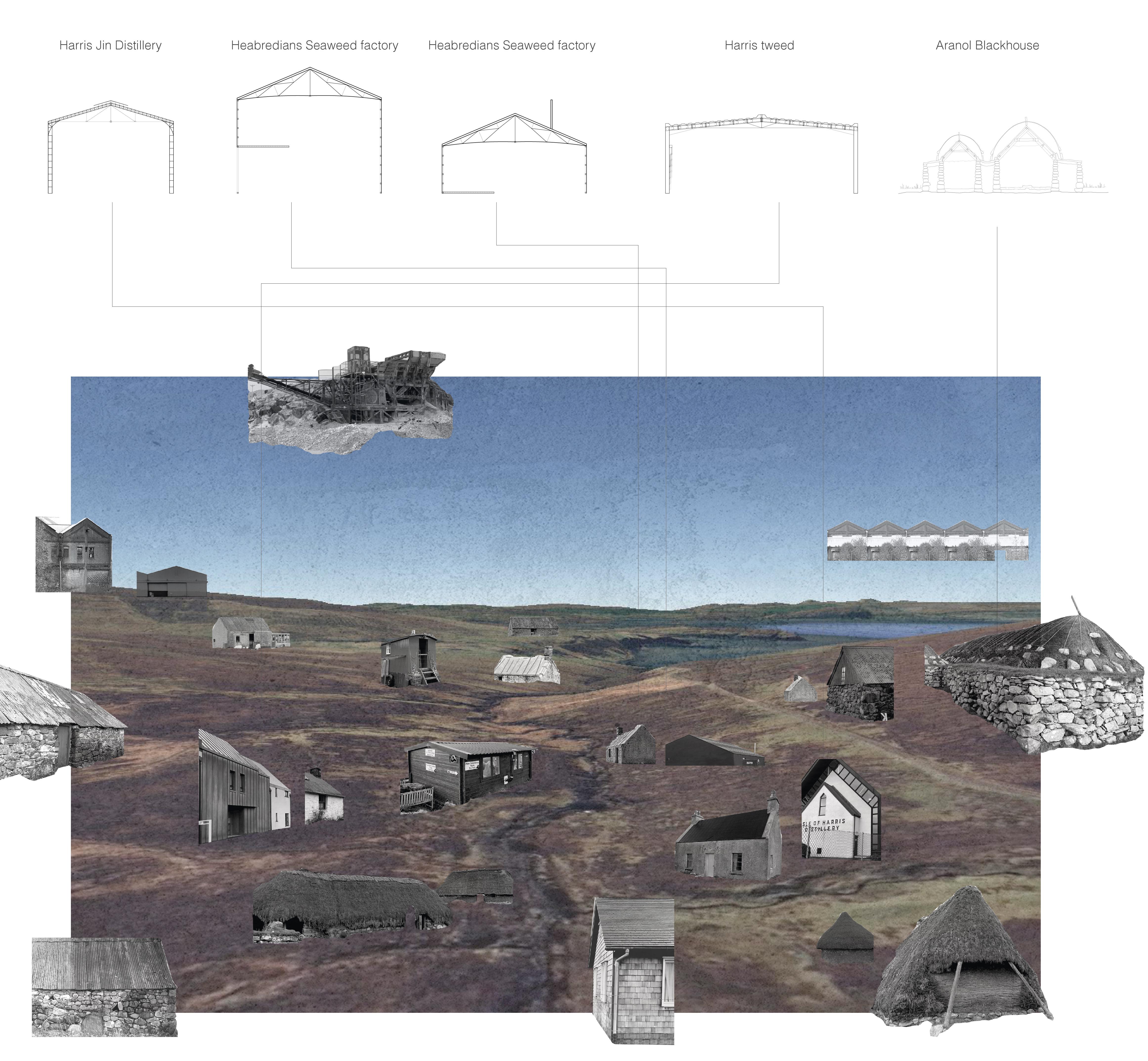
In the 18th century, the seaweed industry appeared in western and northern Scotland. By the 1760s, it was practiced from Kintyre to Orkney. Its importance was due to the growing demand for chemicals produced on an industrial scale and the loss of the main alternative source – Spanish barilla, the ash residue from the glasswort plant – during the Napoleonic Wars.
A Journey following Local Industries, Materials, and Building Typologies questionThisindustrialmaytypologiesandcommunities.oftypologiesTraditionalConclusion:industrialareanindicationvariouslocalcraftsandLearninginvestigatingtheseandtraditionsbethebasisofanewtypology;raisesanimportantWhat are characteristicsthe
conditions.andandcontemporaryconsiderchallengesadaptprinciplesvaluestothesenew 1.2
CHAPTER 02 SEAWEED 2.1 Seaweed morphology and anatomy 2.2 Seaweed properties 2.3 Seaweed benefits as a building material
18 19
Hapteron (holdfast) - attaches the seaweed firmly to the substratum
Laminalamina
Analysing the seaweed structure

Blade Midrib
Anatomy and Morphology
The Kelp is renowned for its nutritional value and ability to lock away vast quantities of carbon Seaweeddioxide.alsoimproves water quality by extracting harmful nutrients such as nitrogen from the sea.
Epidermis - photosynthetis cells closely packed together; several cell layers beneath the epidermis also carry out photosynthesis Fronds
Green seaweed morphology | Microscopic view
2.1
Receptaclephotosynthesis-swollen tip of fertile frond
Midrib medulla - contain longitudinal fillaments densely packed together
Air bladders -keep the blade buoyant and near the surface of the water for efficient
Cortex cells - loosely arranged with some mucilage
Seaweed [red, green, or brown] marine algae grow along seashores. Seaweed are generally anchored to the sea bottom or other solid structures by root-like “holdfast,” which perform the sole function of attachment and do not extract nutrients as do the roots of
Seaweed
Medulla - filamentous cells with large amounts of mucilage
Margin - Entire
higher plants. Brown algae commonly found as seaweeds include Kelps and Fucus. The kelps are among the largest algae, and certain species exceed 33 meters in length.They are widely distributed in colder zones and are absent from tropical waters.
Midrib -central vein; of
Arrangement of tissues in lamina
Conceptacles - contain reproductive structures
Stipe - tough and flexible; keeps frond elevated above the surface and witstand wave action
Lamina (blade) -tough and leathery to withstand wave action
Mucilage canal
Seaweed benefits as a building material 2.2 2.3

MeristodermEpidermis
Seaweed
protects the plant body from decay underwater Carbon-negative material 1 1 2 2 3 3 Growth Harvestingratemethods
Microscopic view - morphology of green seaweed
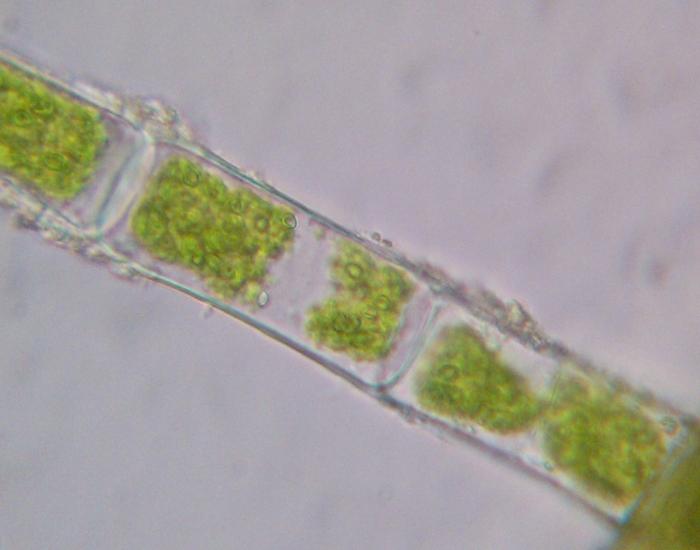
Structure of the stipe in brown seaweed
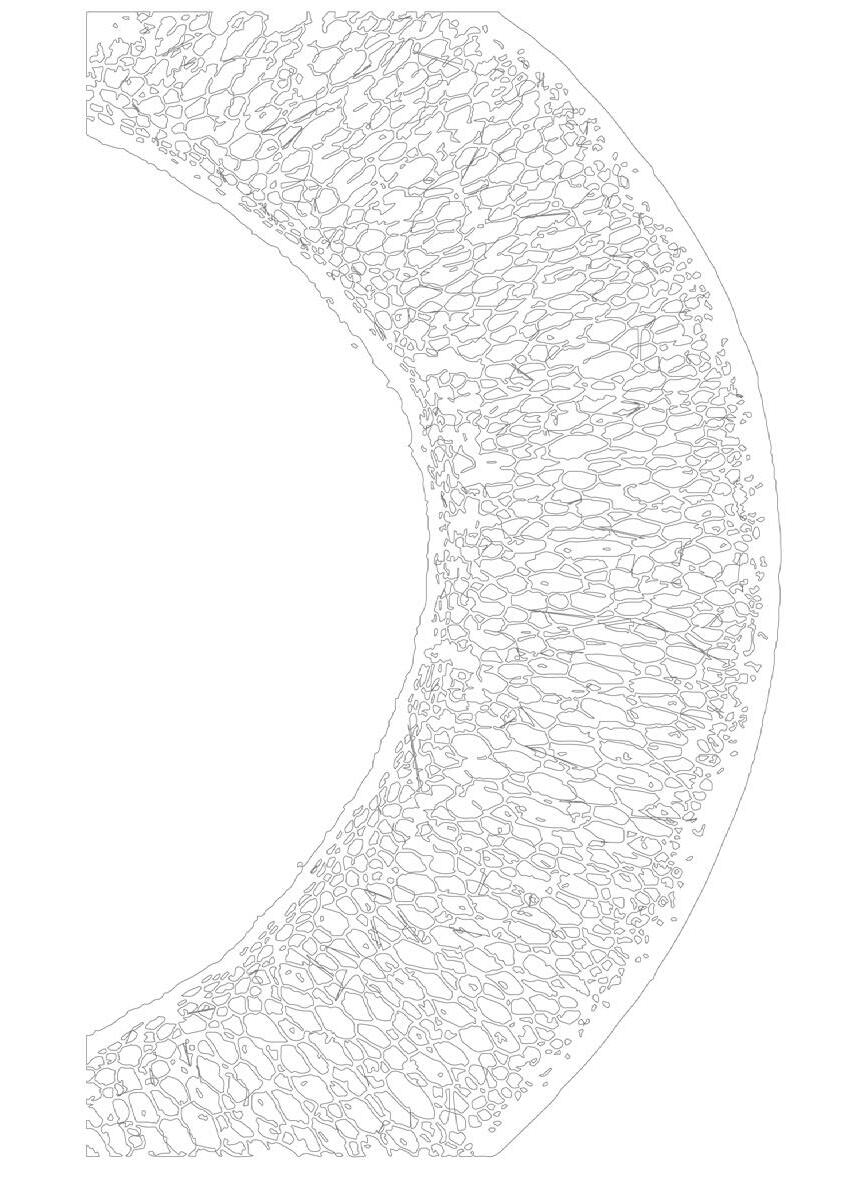
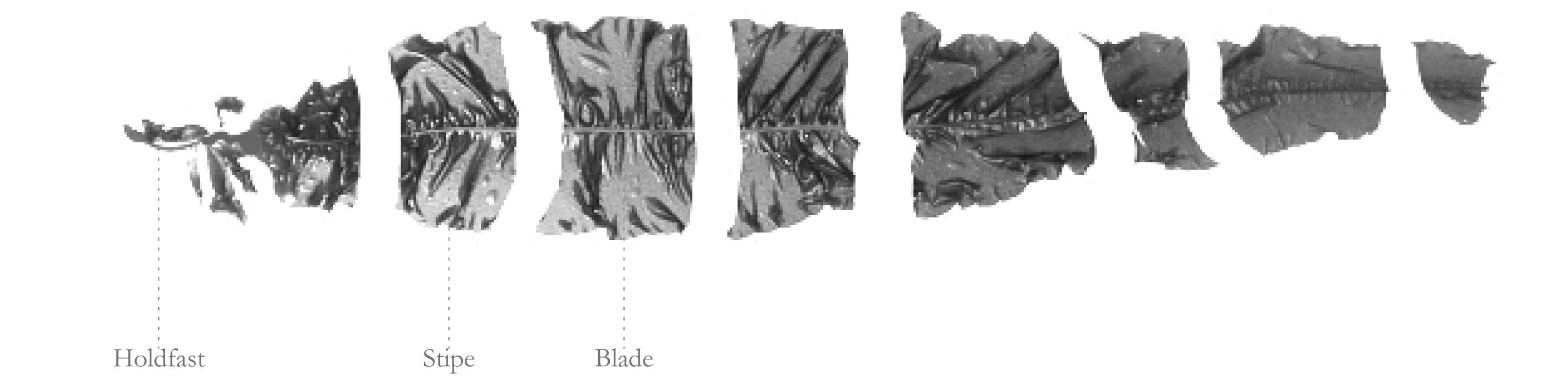
Outer
Seaweed, like land plants, makingprocessphotosynthesisacceleratingonlyafastgrowthThesequestration.knownThisseaweeddioxidetophotosynthesisuseturncarbon(CO2)intobiomass.processisascarbonseaweedrateisveryandcanreachfewmetersinafewdays,itsandit
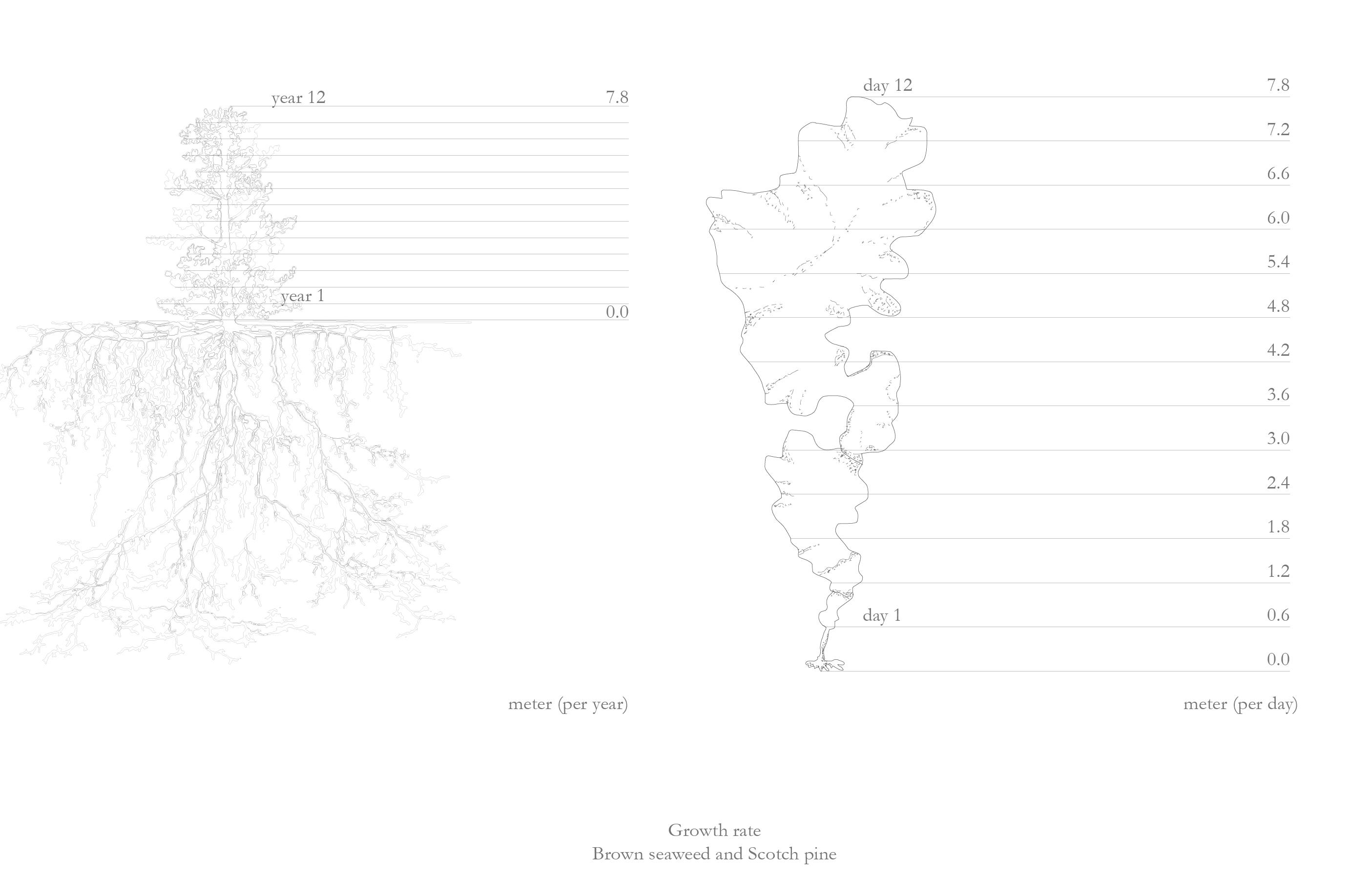
MedullaPerimedullacortexcortex
One acre of seaweed can remove up to 2.7 tons per day of CO2. Certain species have also been shown to efficiently remove CO2 at a 10–50 times higher rate than terrestrial plants.
Seaweed is very easy to cultivate, whether wild harvesting or farming. Thanks to its abundance, it is accessible and cheap.
highly efficient in its sequesteringcarbon- rate.
SEAWEED 21
Inner
CHAPTER 03
PART I
EXPERIMENTSMATERIAL
3.1 Ultimate tensile strength 3.2 Seaweed, starch and surface tension 3.3 Starch experiment - tensile and surface strength 3.4 Creating new properties 3.5 Creating new material 3.6 3D Robotic printing
Starch; a white, granular, organic chemical that is produced by all green plants.
In the first experiment - the vertical force - the seaweed tore at approximately 6.8 kg. The other two experiments were less accurate due to the slippery surface of the seaweed and the sticky liquid that covers it.
Surface Tension; The property of the surface of a liquid that allows it to resist an external force, due to the cohesive nature of its molecules.
32112 3
The UTS has been examined in three conditions: vertical force at one point, vertical force from two points, and horizontal force from two points.
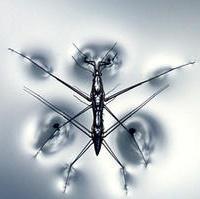
Vertical force at one point
24 25
To get better results, the surface of the seaweed must be rougher and less smooth. Also, the experiment must contain a comparison between groups to conclude.
Definition
Molecules at the surface form stronger bonds
The first experiment with the seaweed aimed to understand better its ultimate tensile strength.
Starch contributes to the stiffness and bonding within a sheet of paper. Cationic starch is added to improve internal bond, tensile strength, and as part of certain retention and drainage programs
Vertical force from two points
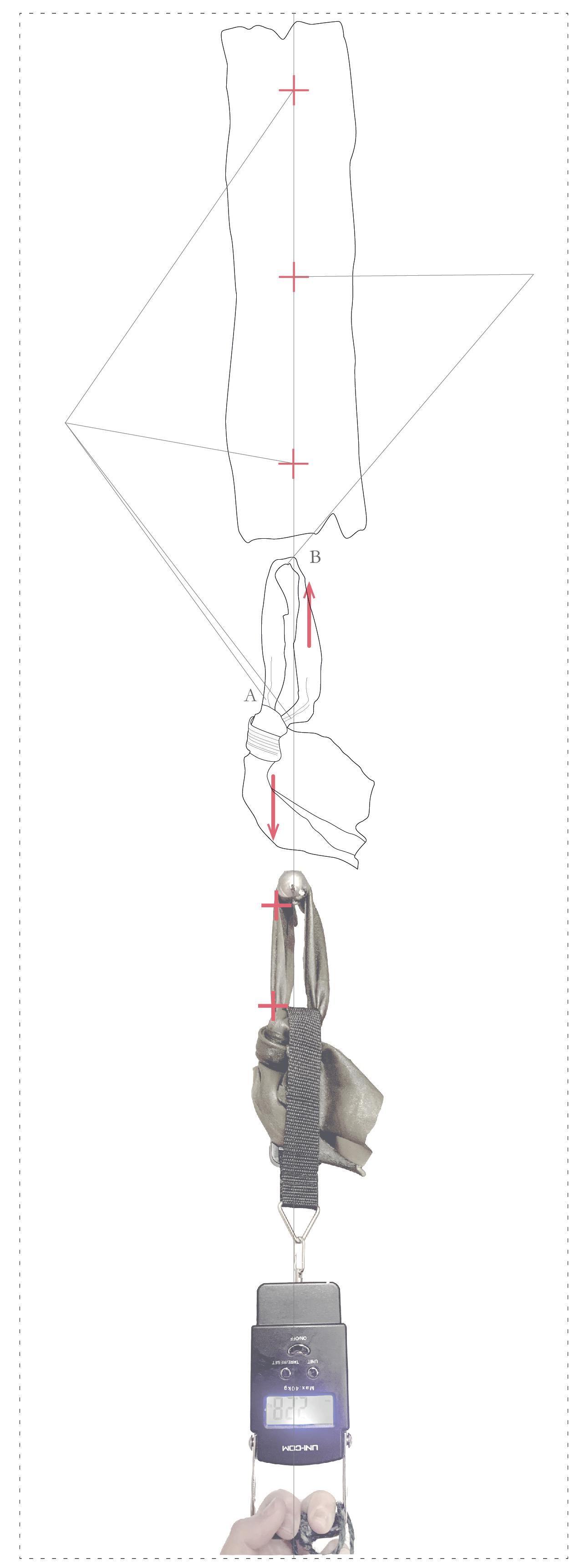
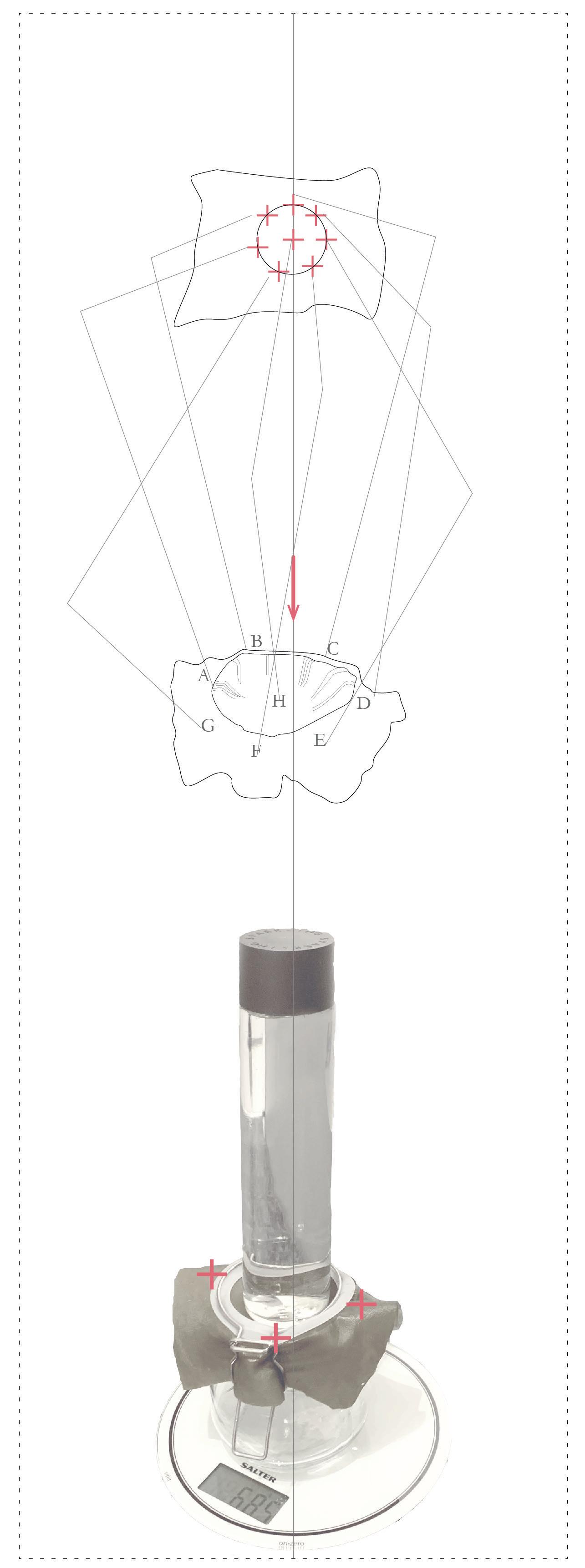
MATERIAL EXPERIMENTS PART I
DefinitionDefinition
ULTIMATE TENSILE STRENGTH
3.1 3.2
Experiment description
* The interaction between contacting surfaces of a liquid and a solid that distorts the liquid surface from a planar shape and causes the liquid to rise or fall in a narrow tube.
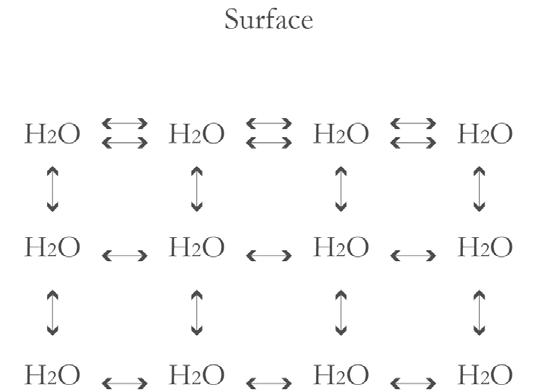
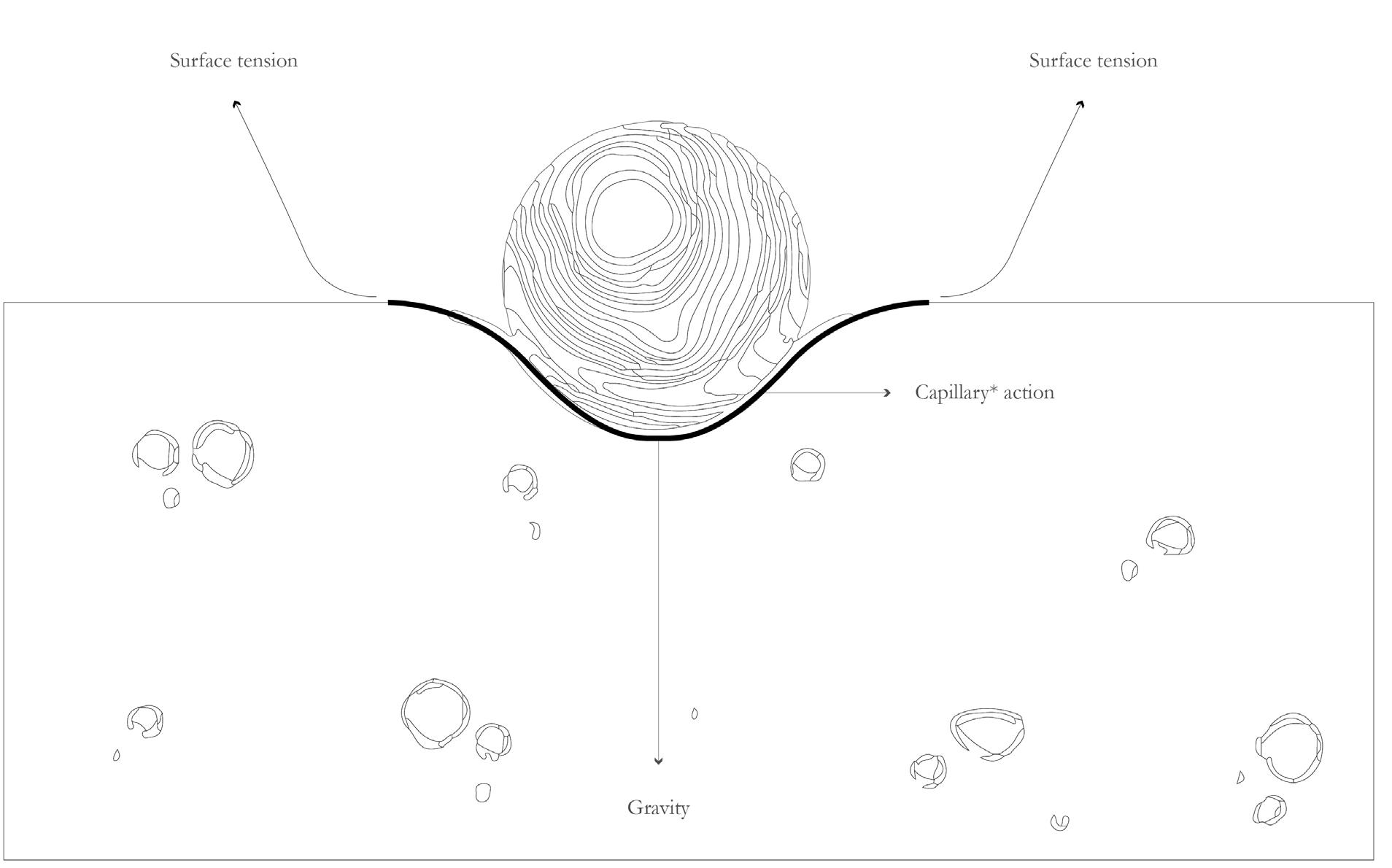

and water mixed acts both like a solid and a liquid. Starch and water is a suspension mixture with a solid dispersed into a liquid. When you press the mixture quickly, the starch molecules close together. This causes the water to get trapped between the starch chains and create a semi-rigid structure.
Horizontal force from two points
Experiment conclusion
[uts] is the maximum stress that a material can withstand while being stretched or pulled before breaking. Some materials break very sharply, without plastic deformation, in what is called a brittle failure. Others, which are more ductile, including most metals, experience some plastic deformation and possibly necking before fracture.

Why do starch and water Starchreact?
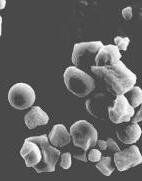
SEAWEED, STARCH AND SURFACE TENSION
uts of seaweed is ~50 MPa

Strength (load capacity, kg)
The failure points of the 5 groups of the seaweed with the starch were between 9.4 kg to 11.2 kg, whereas the point of failure of the group with the cacao was 6.2 kg.
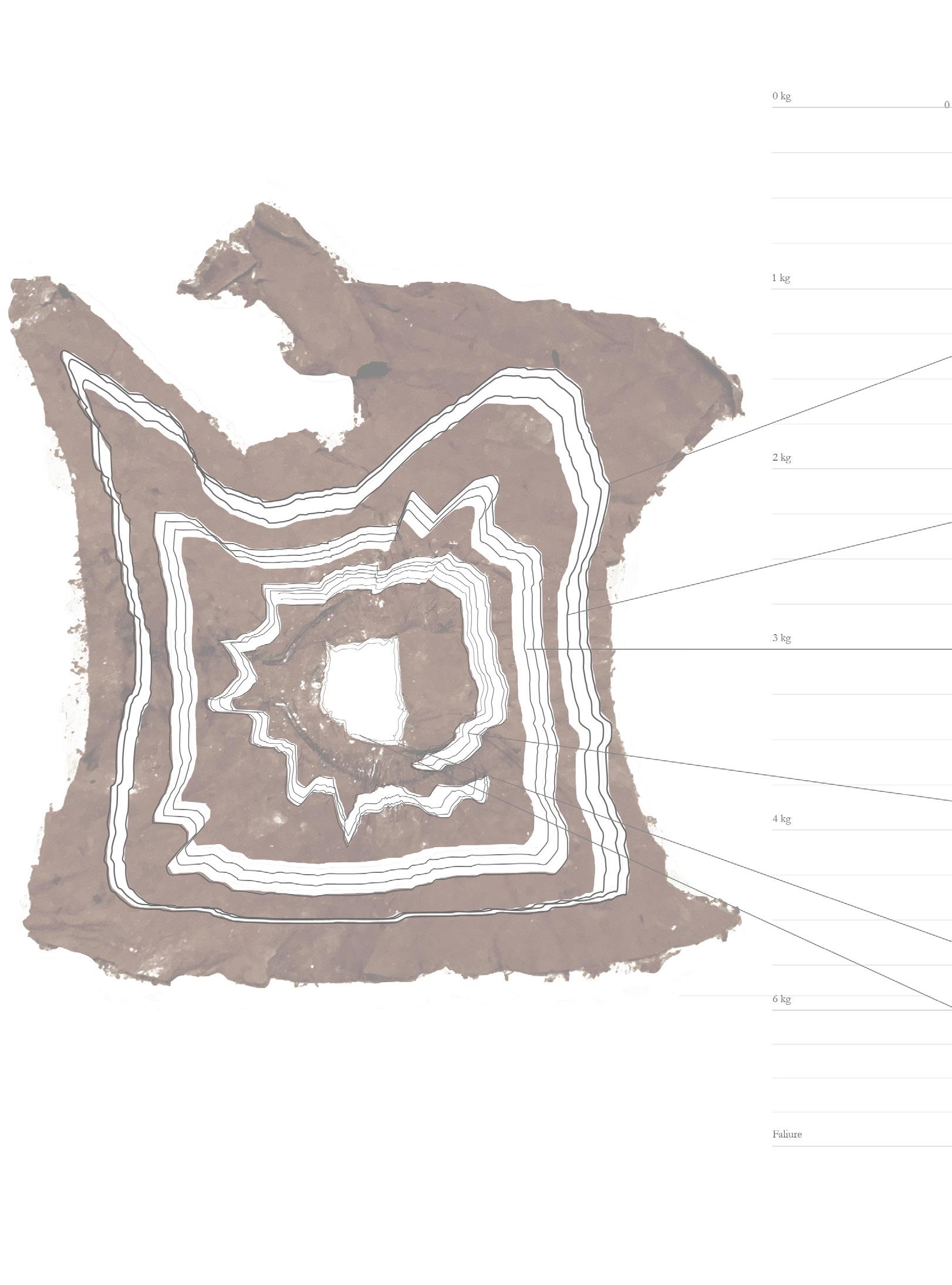
Seaweed initial size 30 X 17 cm
27MATERIAL EXPERIMENTS26
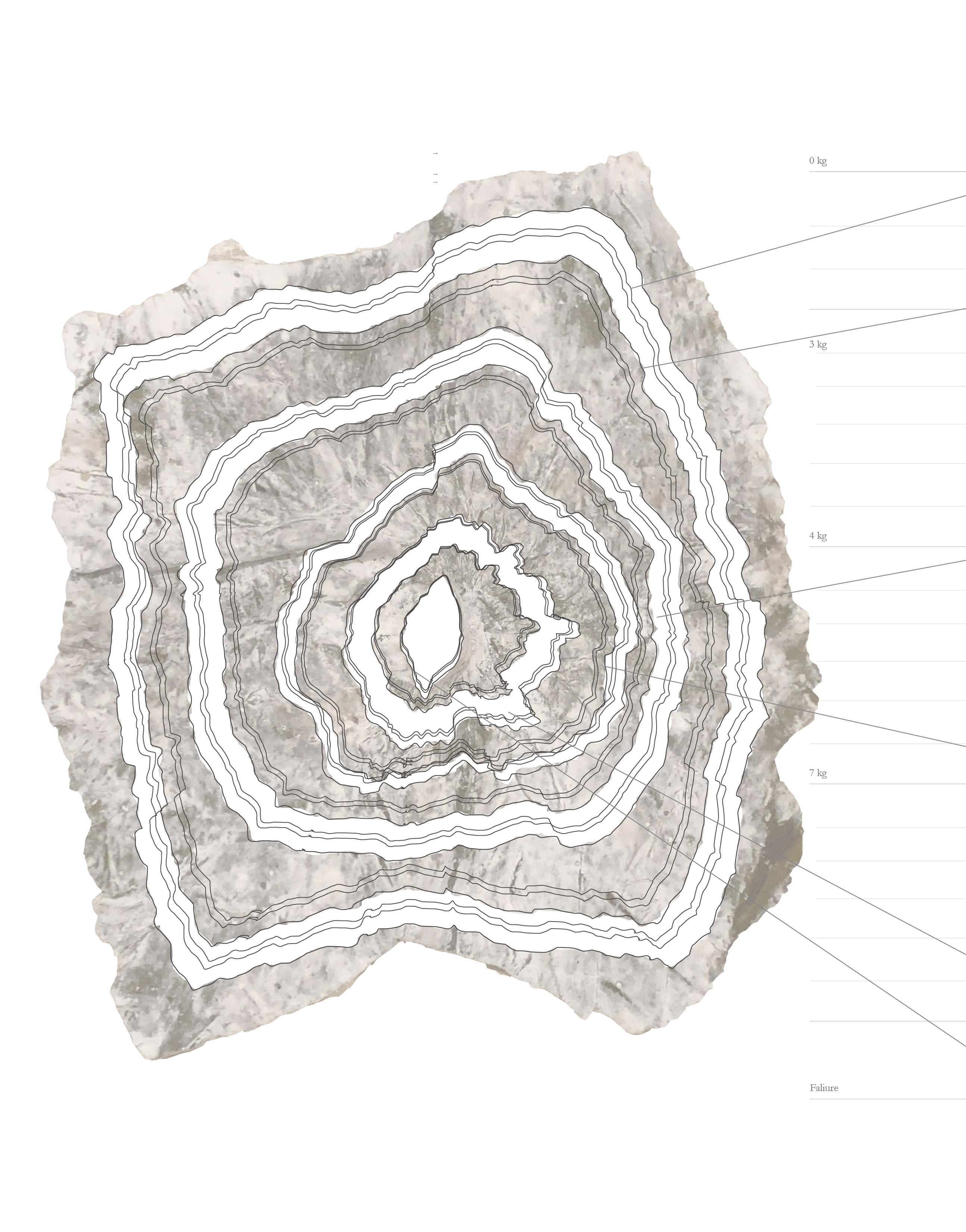
3.3
Seaweed end size 35 X 23 cm
Strength (load capacity, kg) 10.6239.720
Seaweed, sweet potato starch
Seaweed initial size 28.8 X 18 cm
To test strength, the experiment tests what is the point of failure of the surface – what weight makes to surface tear.
Time to failure (seconds)
Time to failure (seconds)
Seaweed initial size 32 X 28 cm
Time to failure (seconds)
Time to failure (seconds)
Experiment conclusion
Seaweed end size 35 X 31 cm
Seaweed end size 33.2 X 18 cm
Seaweed,
11.215623 Elasticity minmax Deformation Point Effort

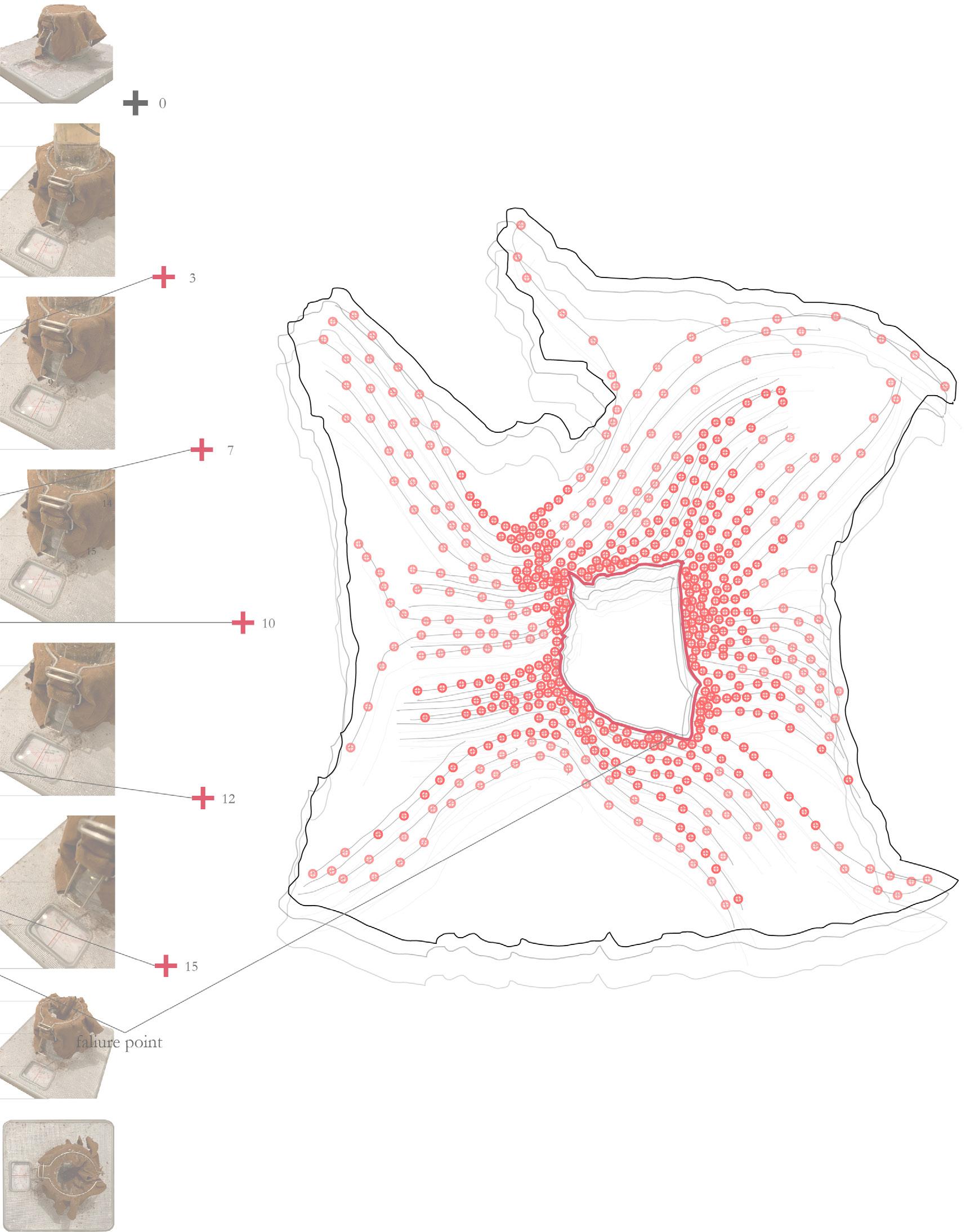
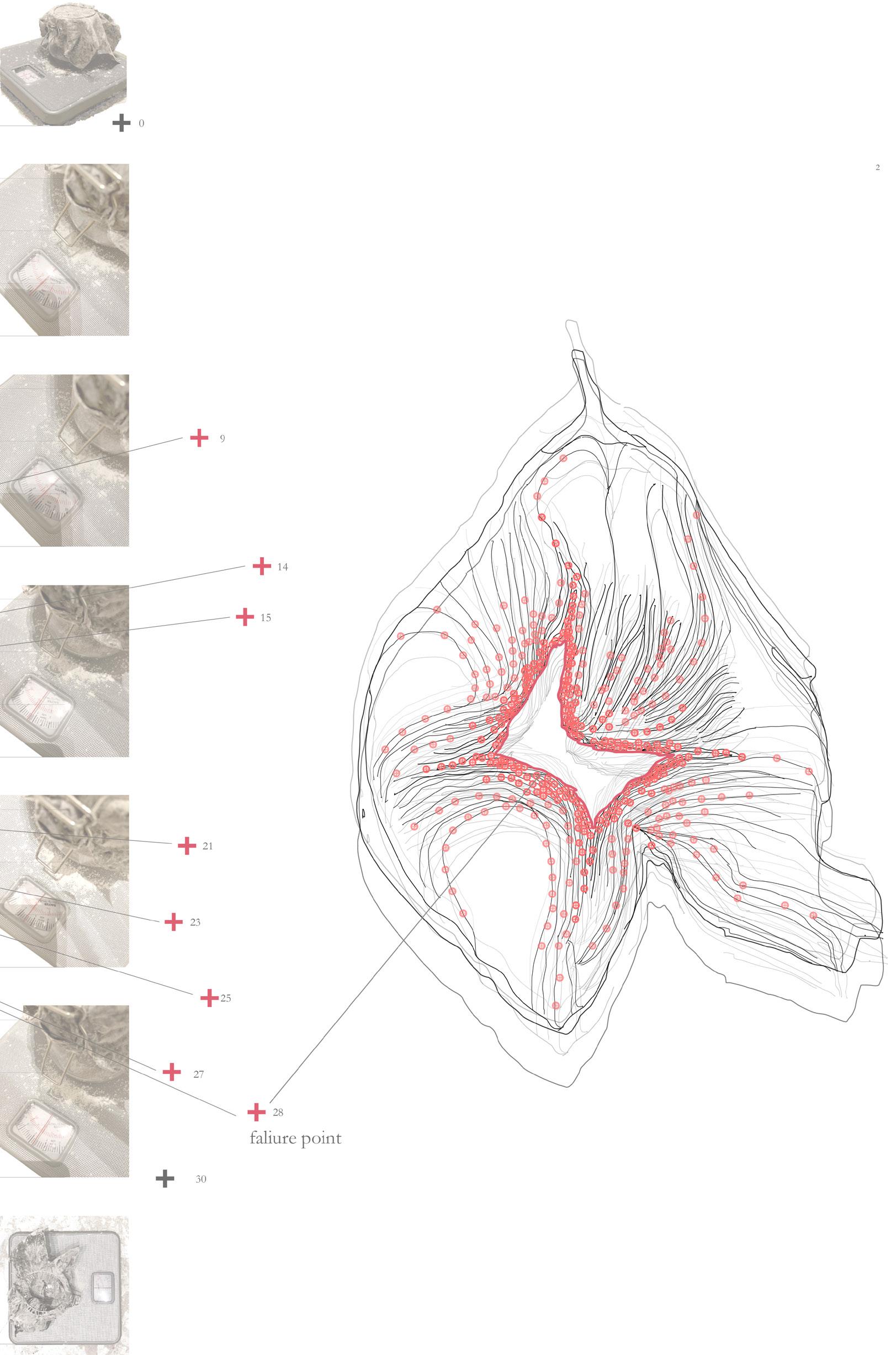
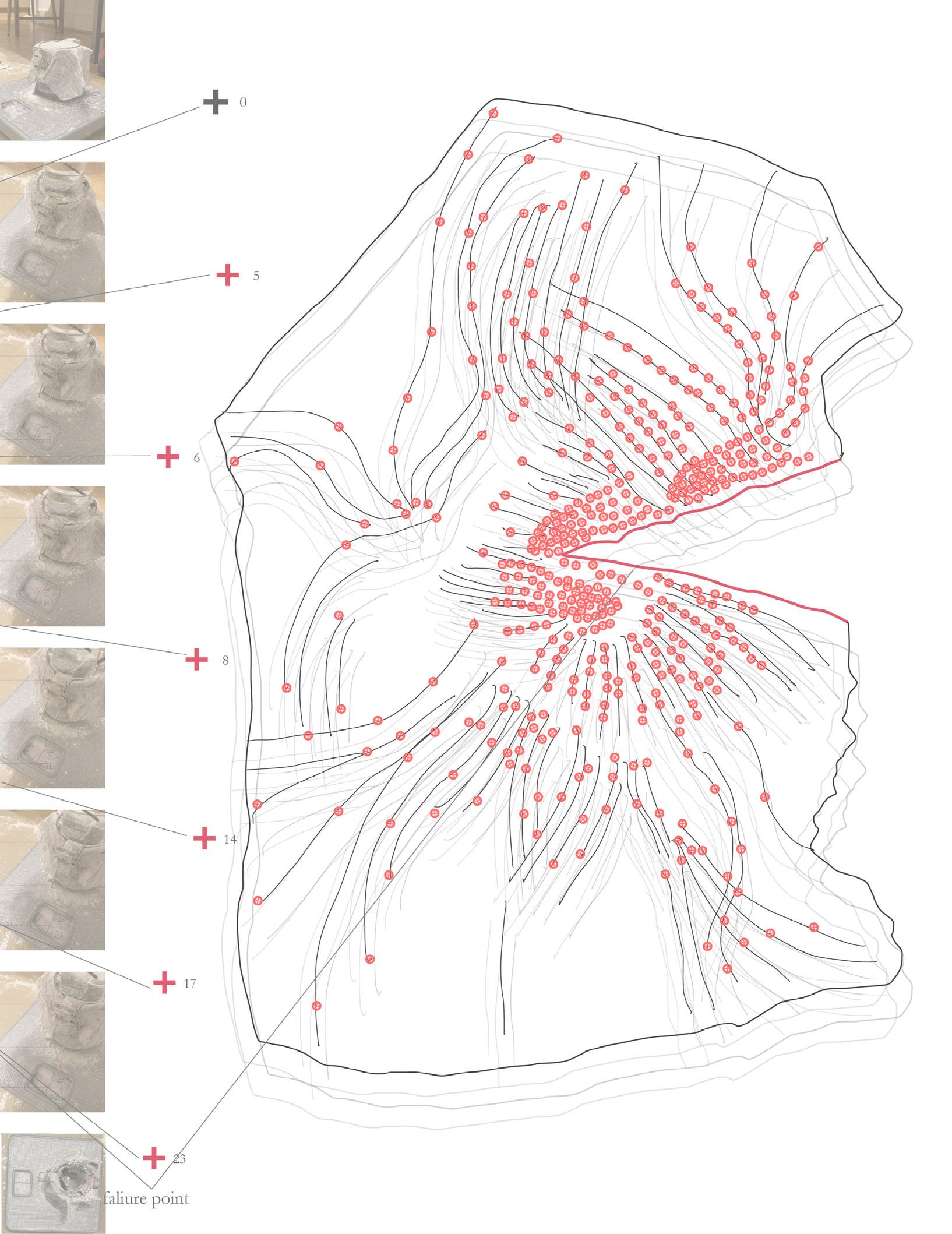
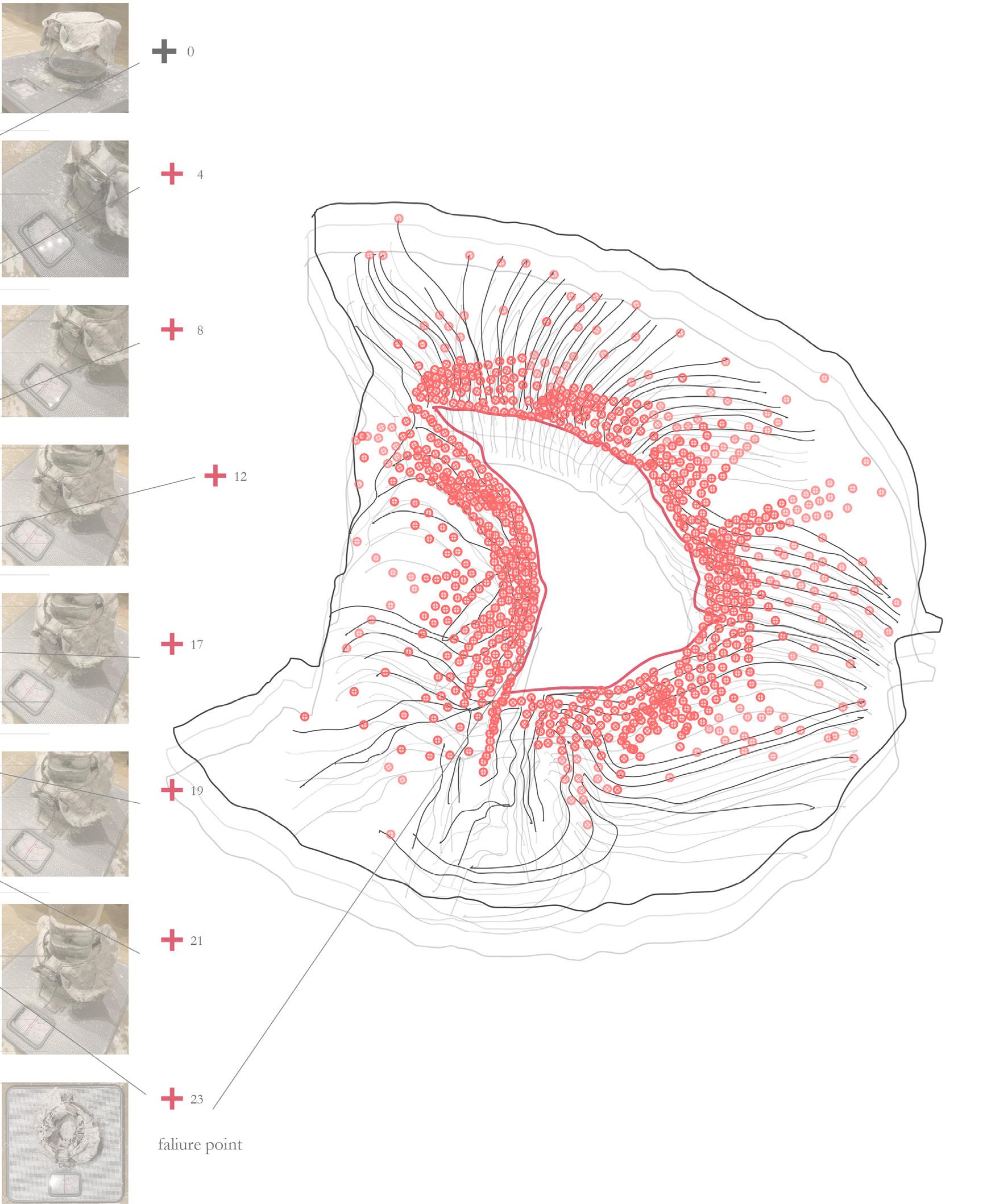
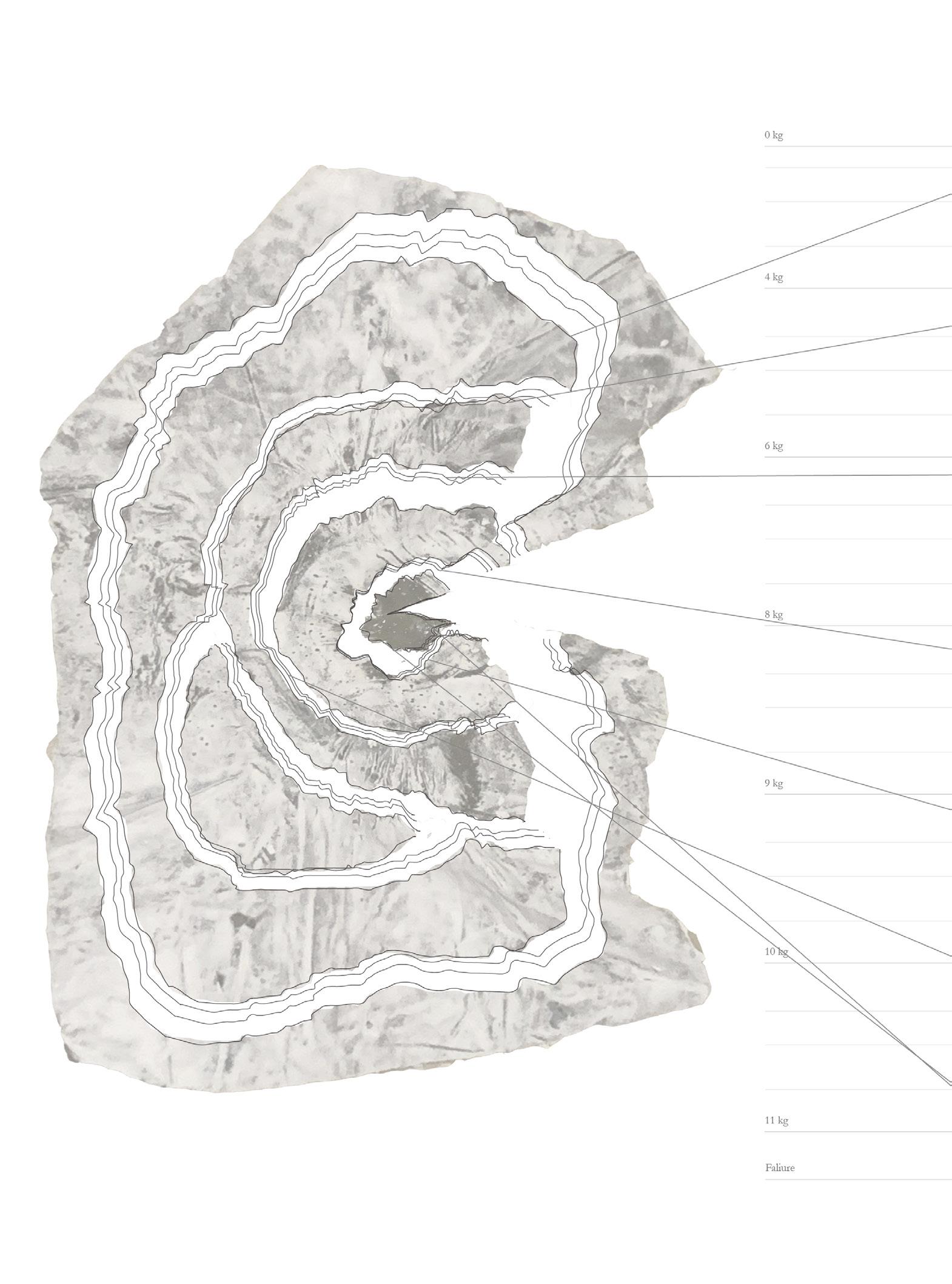

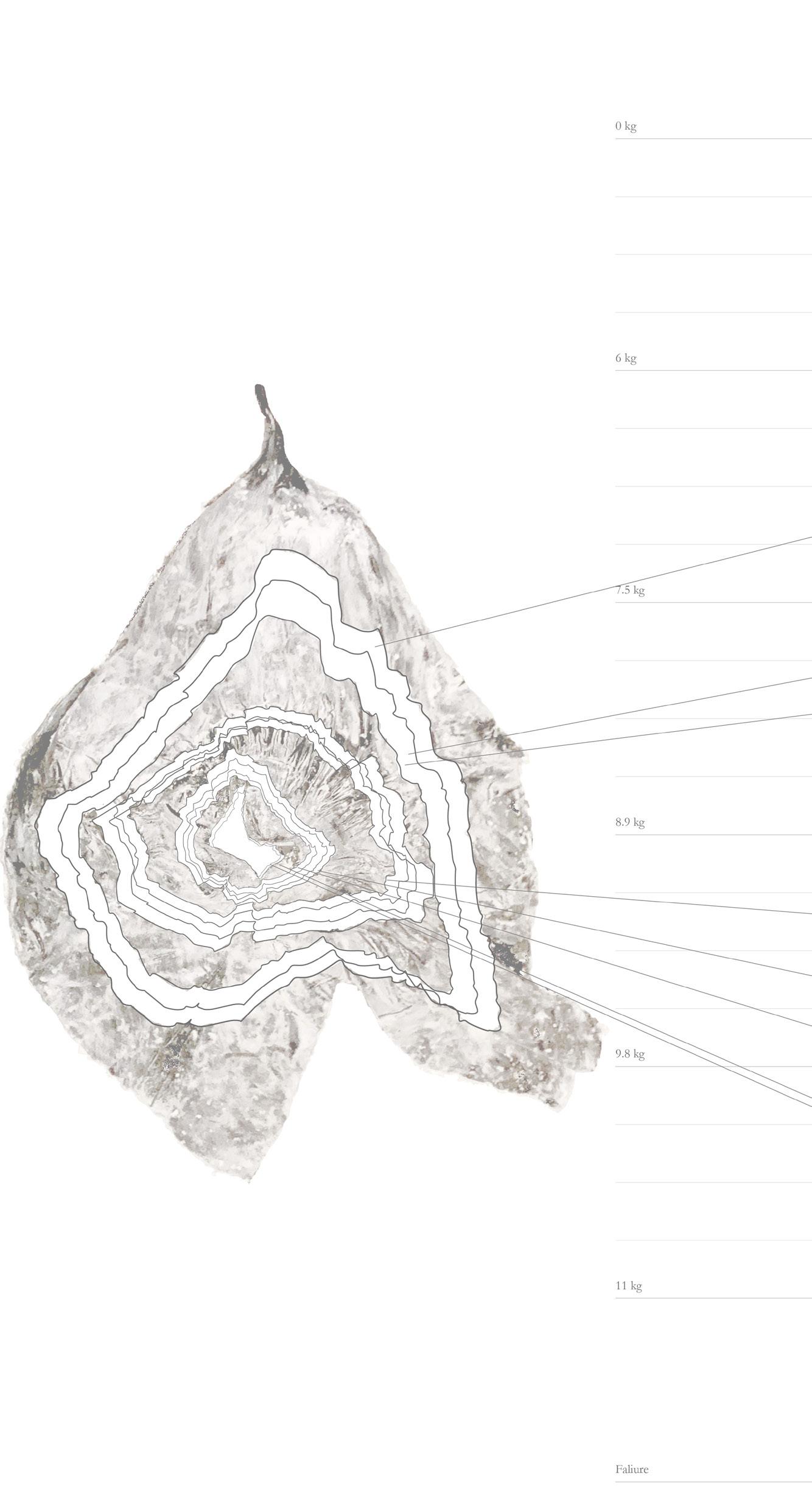
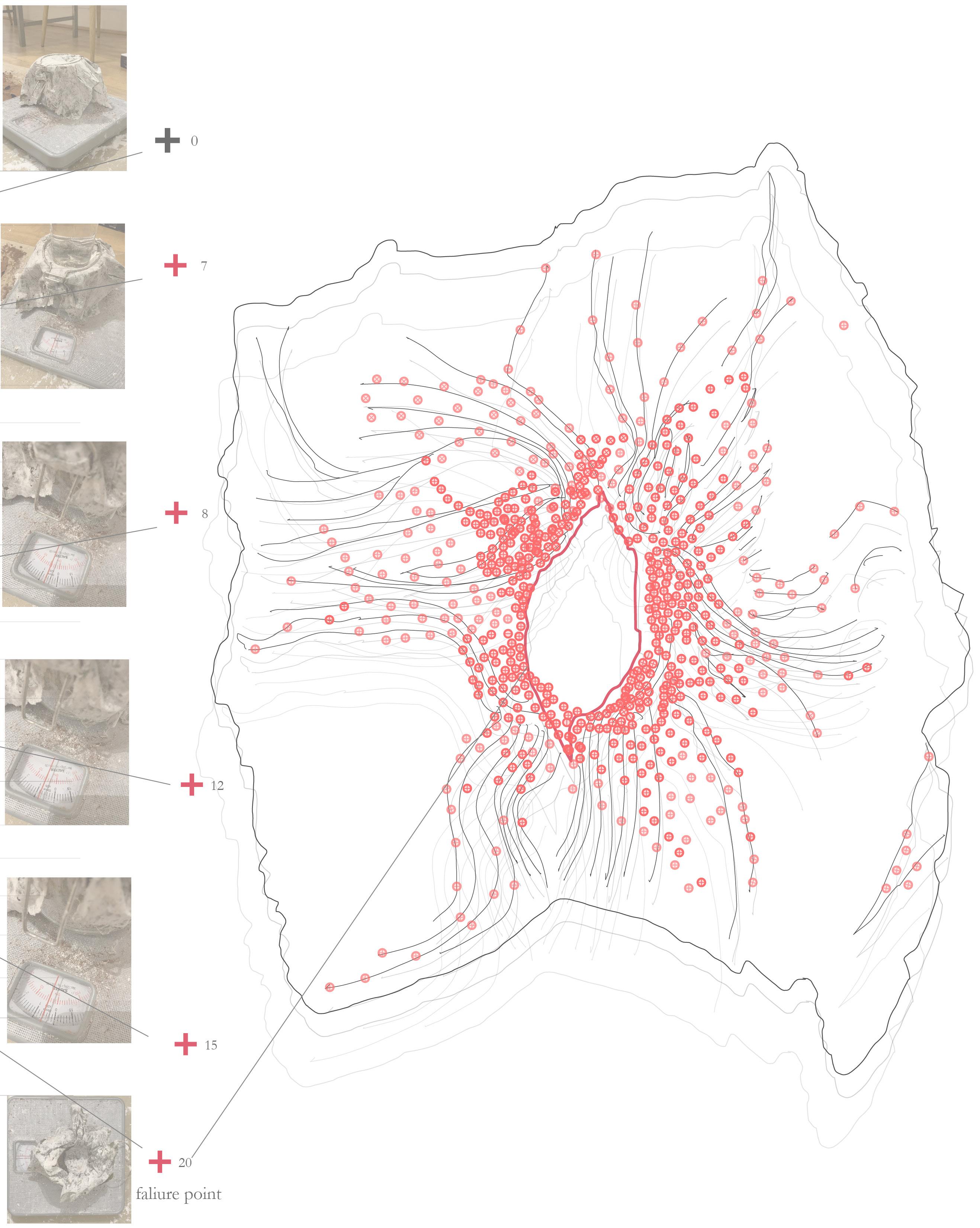
Seaweed end size 32 X 19 cm
Strength (load capacity, kg)
Starch experiment - tensile and surface strength
Seaweed, starch
Strength (load capacity, kg)
Seaweed initial size 34.5 X 15 cm
Seaweed, Cacao
As explained on the way starch react with water and liquid (see page 23), the assumption is that the starch molecules would bind and potentially reinforce the surface of the seaweed. Starch and water mixed acts both like a solid and liquid.
The weight that documented in the moment of failure will point out regarding the strength of the surface.
Strength (load capacity, kg)
wheat
Time to failure (seconds)
Load (kg)
Seaweed and Starch
(seconds)timelineonpointsDeformation

Seaweed end size 39.2 X 17 cm
10.210.22827
Experiment description
Seaweed initial size 32 X 15 cm
This experiment examines whether the starch gives strength to the seaweed surface. The experiment divided into 5 groups of starch and one critic group with cacao powder.
The starch indeed made the surface of the seaweed stronger.
There is a range of strength between the different groups of the starch (tapioca is the strongest 11.2 kg, and wheat is the weakest 9.4 kg), but still the wheat starch group (9.4 kg) is much stronger than Cacaothegroup (6.2 kg).
Time to failure (seconds)
Strength (load capacity, kg)
Seaweed end size 35 X 17 cm
Tapioca starch
Experiment results
Seaweed initial size 31 X 21 cm
Experiment assumption
Seaweed, cassava starch
Experiment no. 3
Seaweed, Corn starch
First, coating the seaweed with the powder. Second, stretching the seaweed on top of a device that keeps static. Third, putting the device with the seaweed on top of a weight. Last, putting force on the seaweed from top down till the surface tears.
Reinforcing the seaweed surface
29 ml AGAGAG 18.2%30.7%30.7%MaterialSWSWSW Composition Tools Mix 01 Structure I Mix 02 Structure II Mix 03 Base layer 10ml syringePastry bag 9%24.1%24.1% strengthstrengthstrength wetnesswetnesswetnesstransparencytransparencytransparency crackscrackscrackselasticityelasticityelasticity durabilitydurabilitydurabilityGLGLGL 54.6%10.2%5.3%STSTST 18.2%35%40% Dimensions 32 X 45 cm Extruder diameter (mm) 1,3
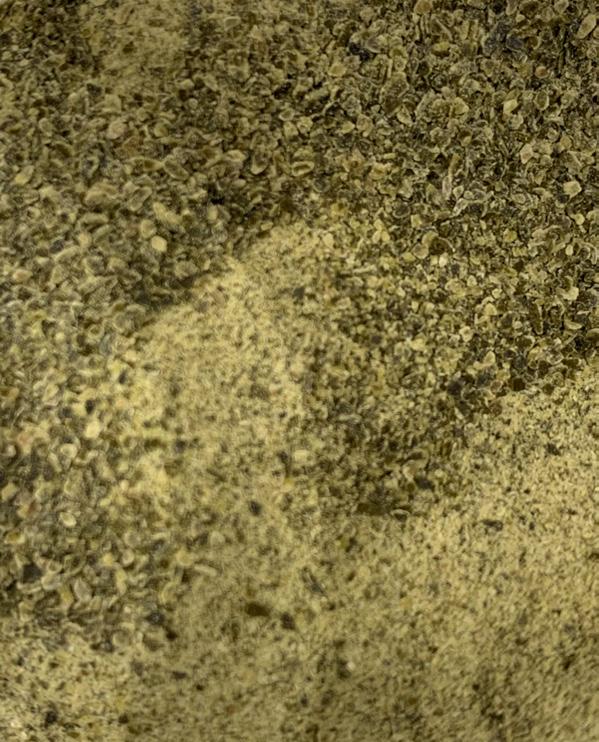

Mix 01 - base layer: Contains smallest amount of seaweed, starch and Agar, and biggest amount of Glycerine.
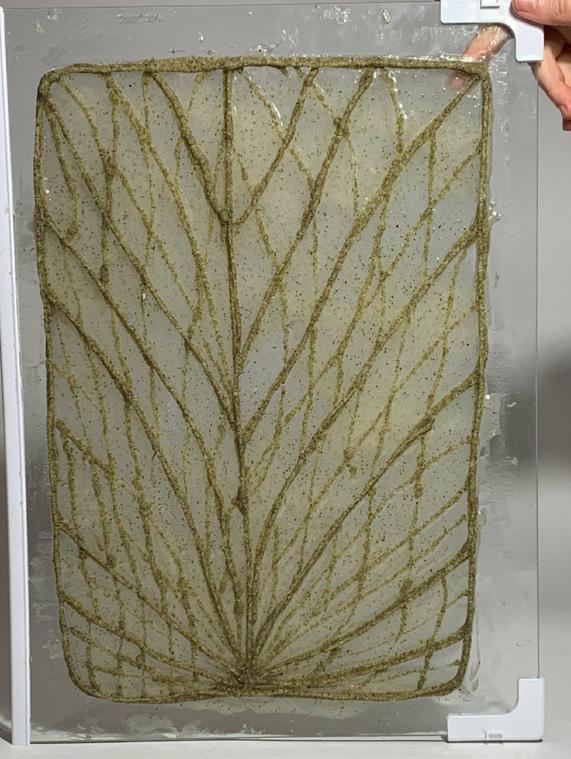
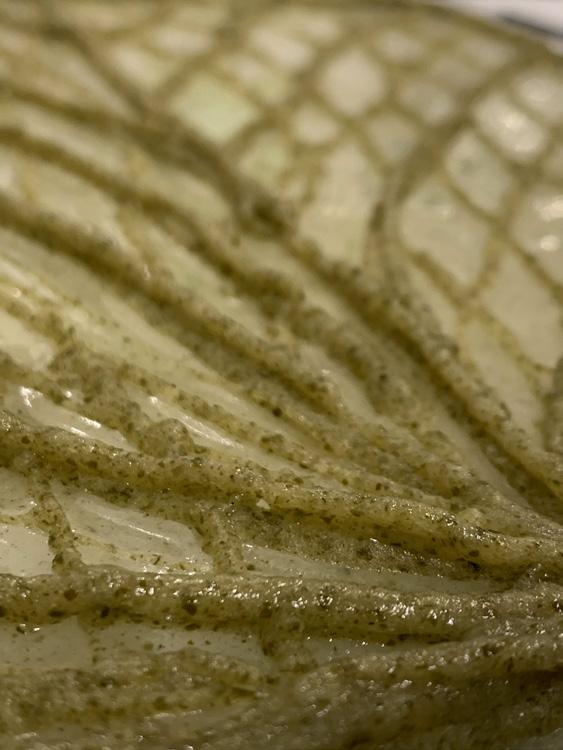
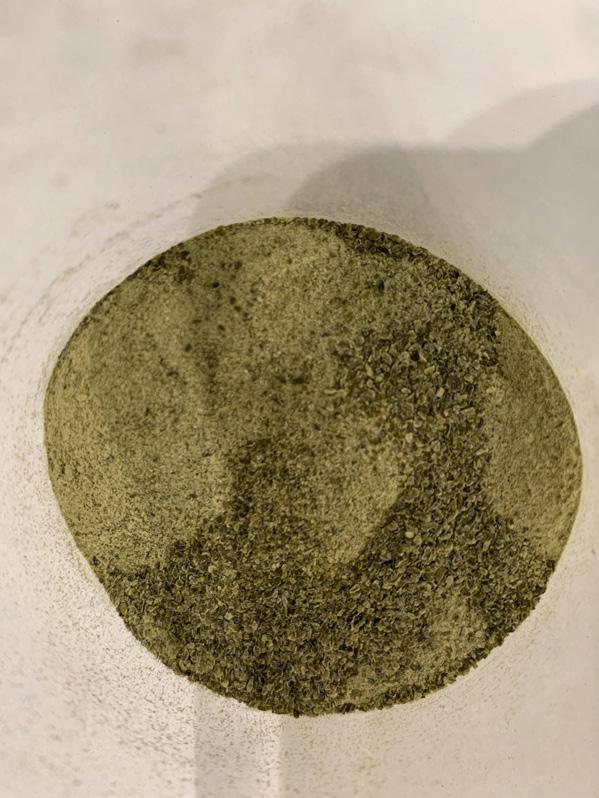
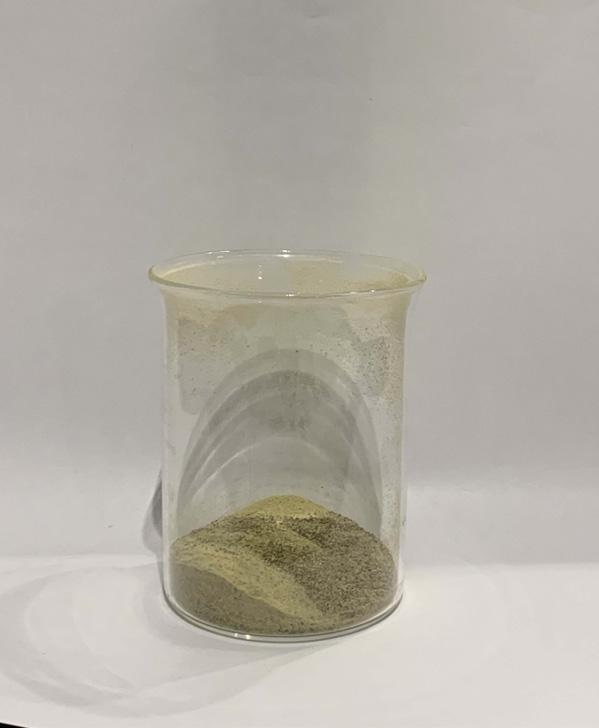
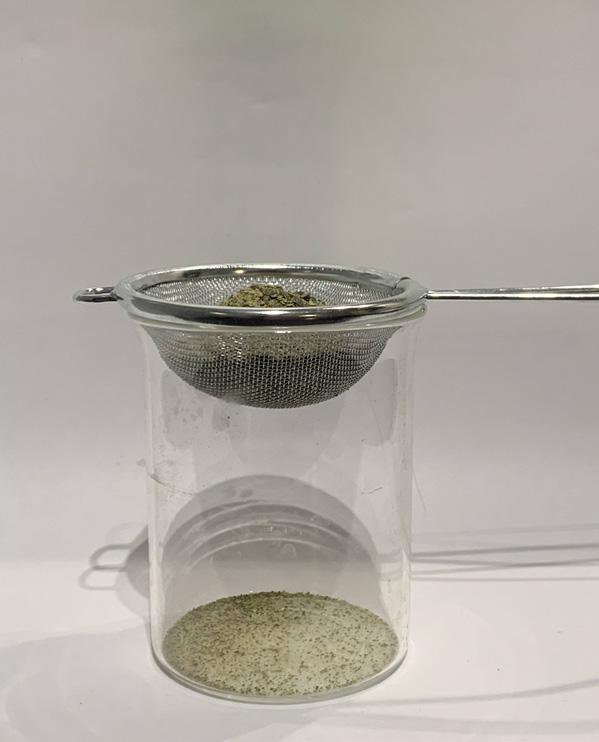

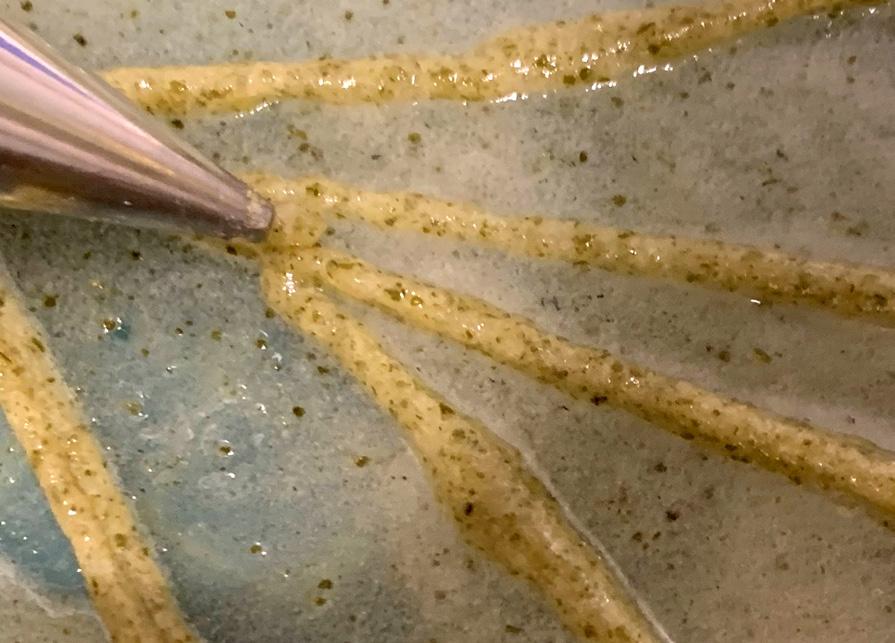
Mix 02 - Structure II: Contains more seaweed starch and Agar and less MixGlycerine.03-Structure I: Contains biggest amount of Seaweed Starch and Agar and smallest amount of Glycerine.
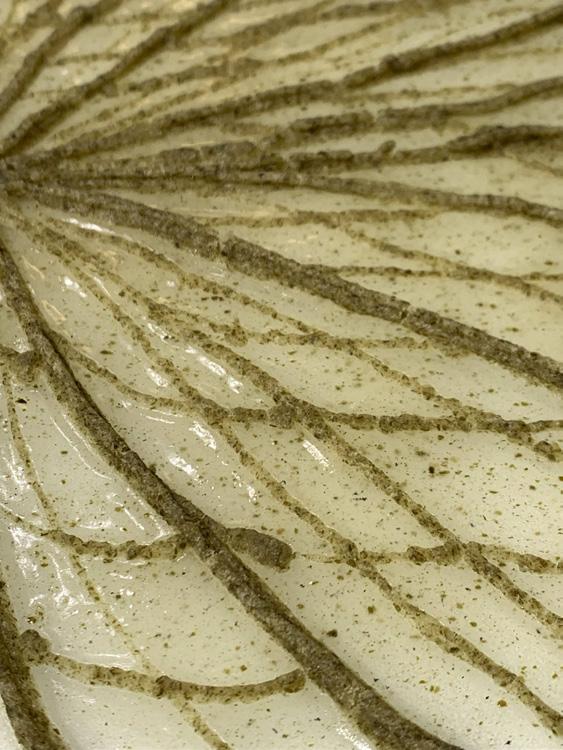
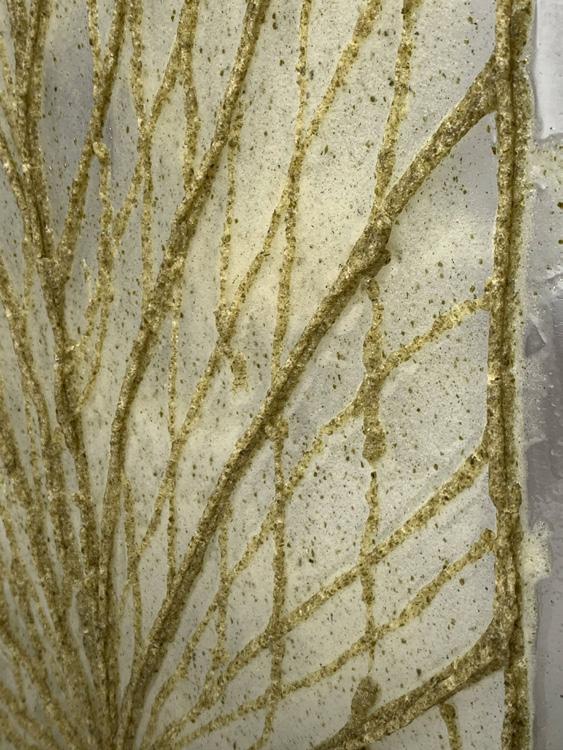
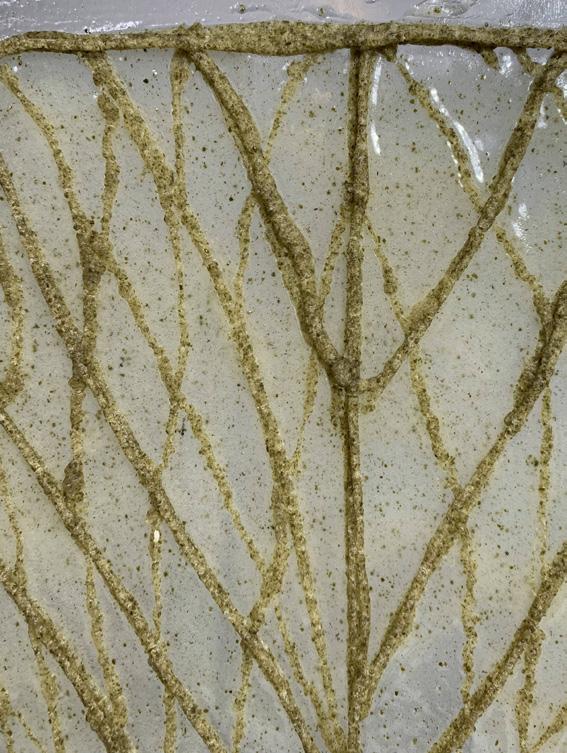
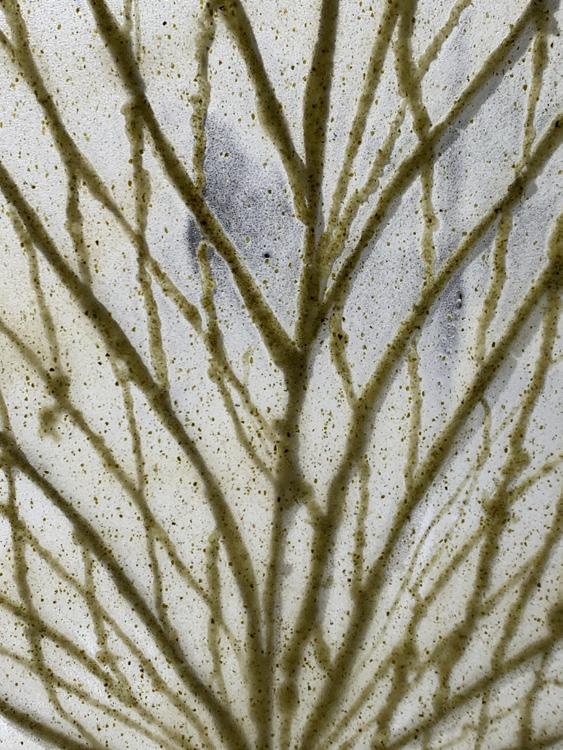
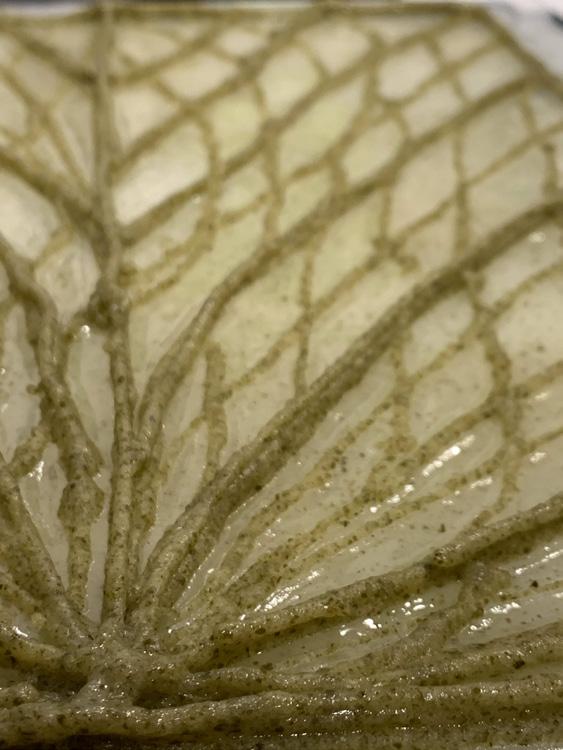


3 Layers; Different mix to each layer Translucency and Elasticity
Creating
new properties Experiment no. 5 3.4
In this experiment, three different compounds were produced - to be able to examine a range of properties. The compounds didn’t differ in the ingredients but their portions.

The model stayed wet and glossy, which are properties of the seaweed that be wanted to preserve.
Layer 02 minimum light penetration
30 31
Layer 03 penetration
Role of ingredients in the mix
Following the understanding that starch makes the seaweed surface strongertension - the following experiment tries to produce bio-plastic by mixing seaweed and starch with other Toadditives.produce bio-plastic - a compound - the seaweed had to change its form into powder.
ExperimentExperimentExperimentinaccuracies.parameterspurposeassumption
Layers of model Material(%)compound Seaweed C ST GL AG

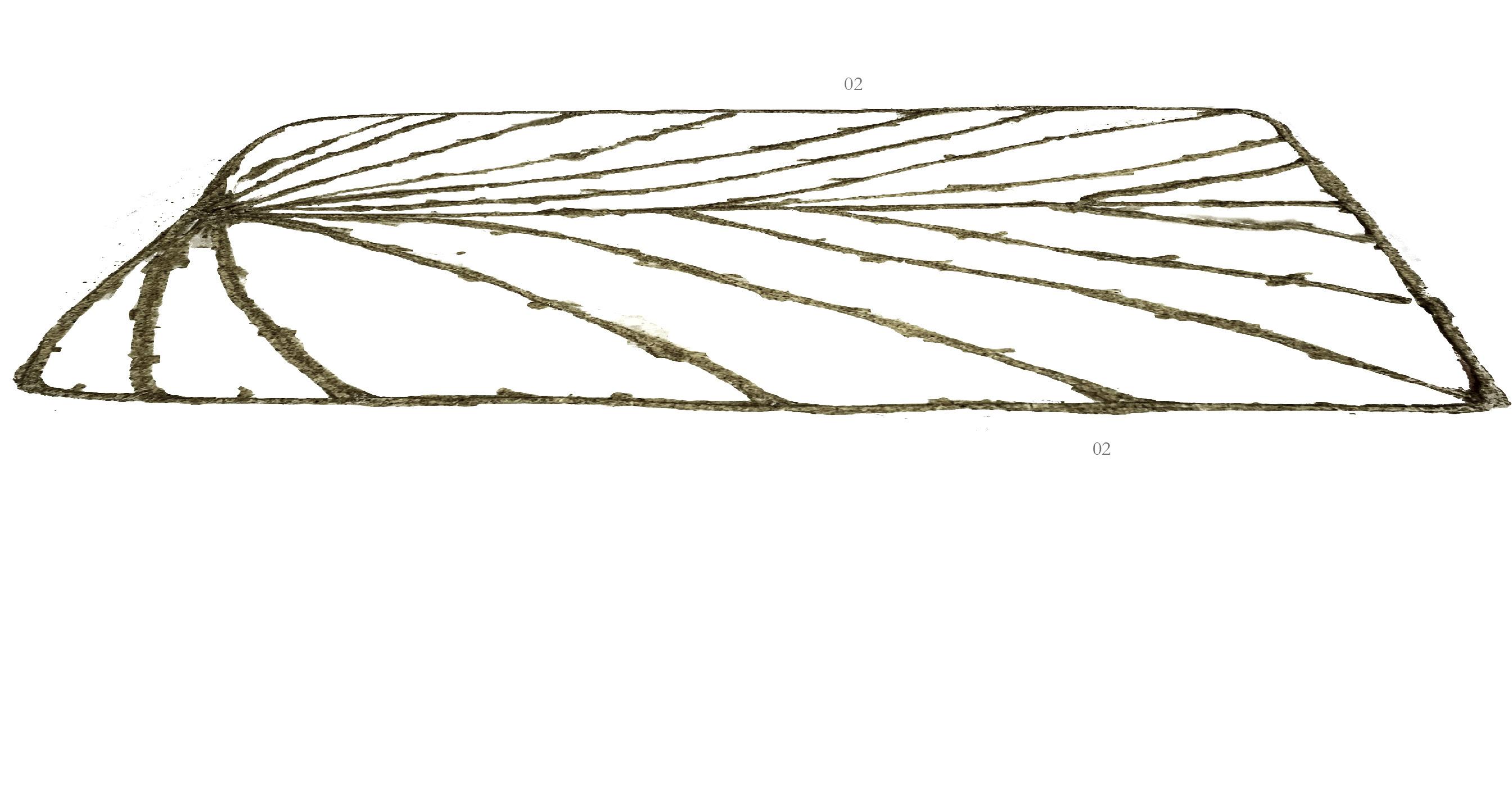
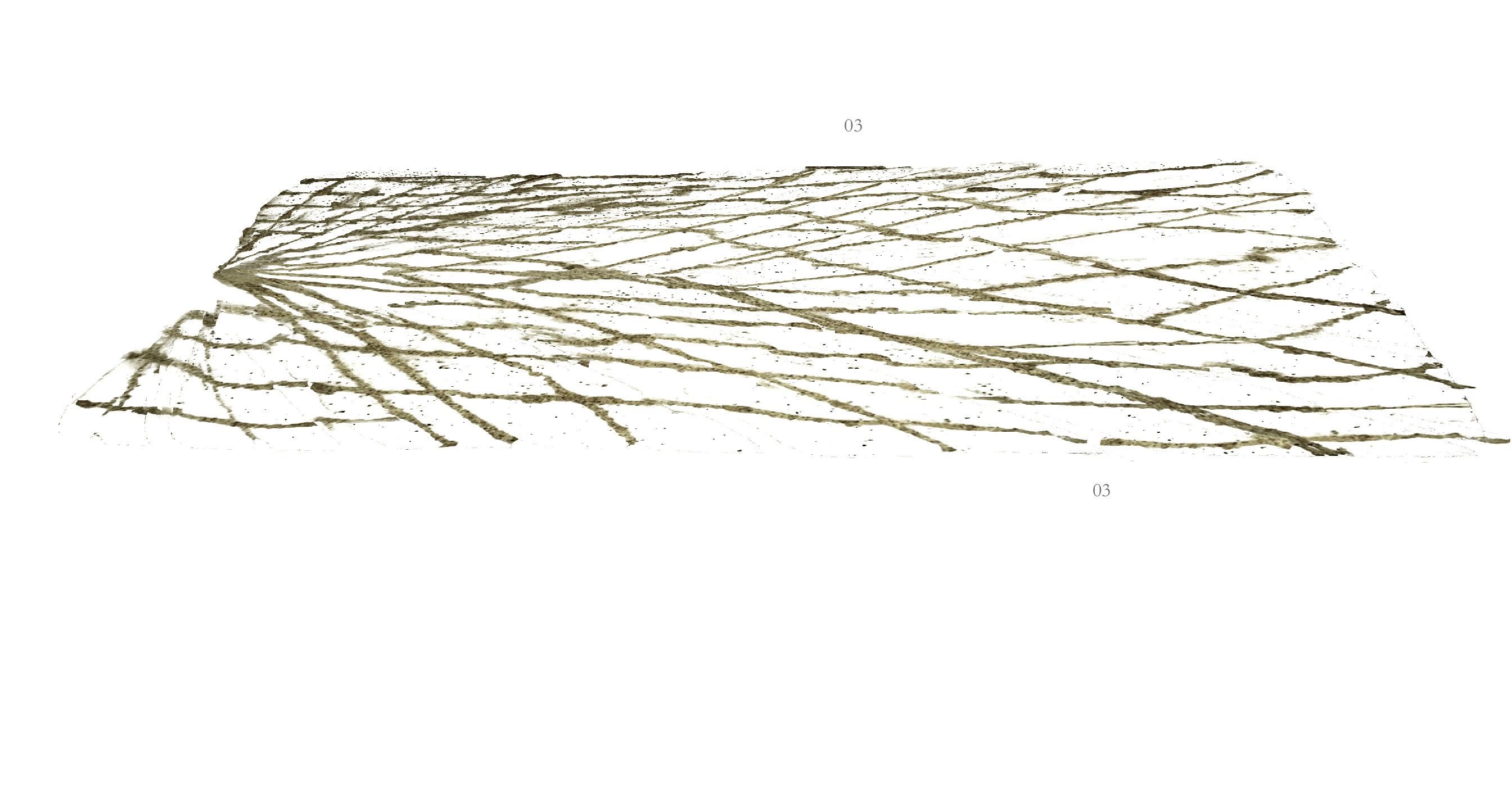
Transparency
Creating new properties
3.4
Properties that were tested in the experiment were transparency and
Agar: Glycerine:Starch:binderstrengthElasticity and softness
Smallerelasticity.amount of seaweed would allow the mix to be more transparent, Agar would make it more robust, and more Glycerine would enhance flexibility. minmax
Translucency and Elasticity
Layer 03 maximum light penetration
partial light
TheConclusionsmixwasn't strong as expected and couldn't detach from the glass surface. An array of transparencies did achieve. Also, some control in densities and stability between the different compounds.
Experiment no. 5
The next step would be improving the mix to achieve better control and 3d printing to avoid air bubbles and
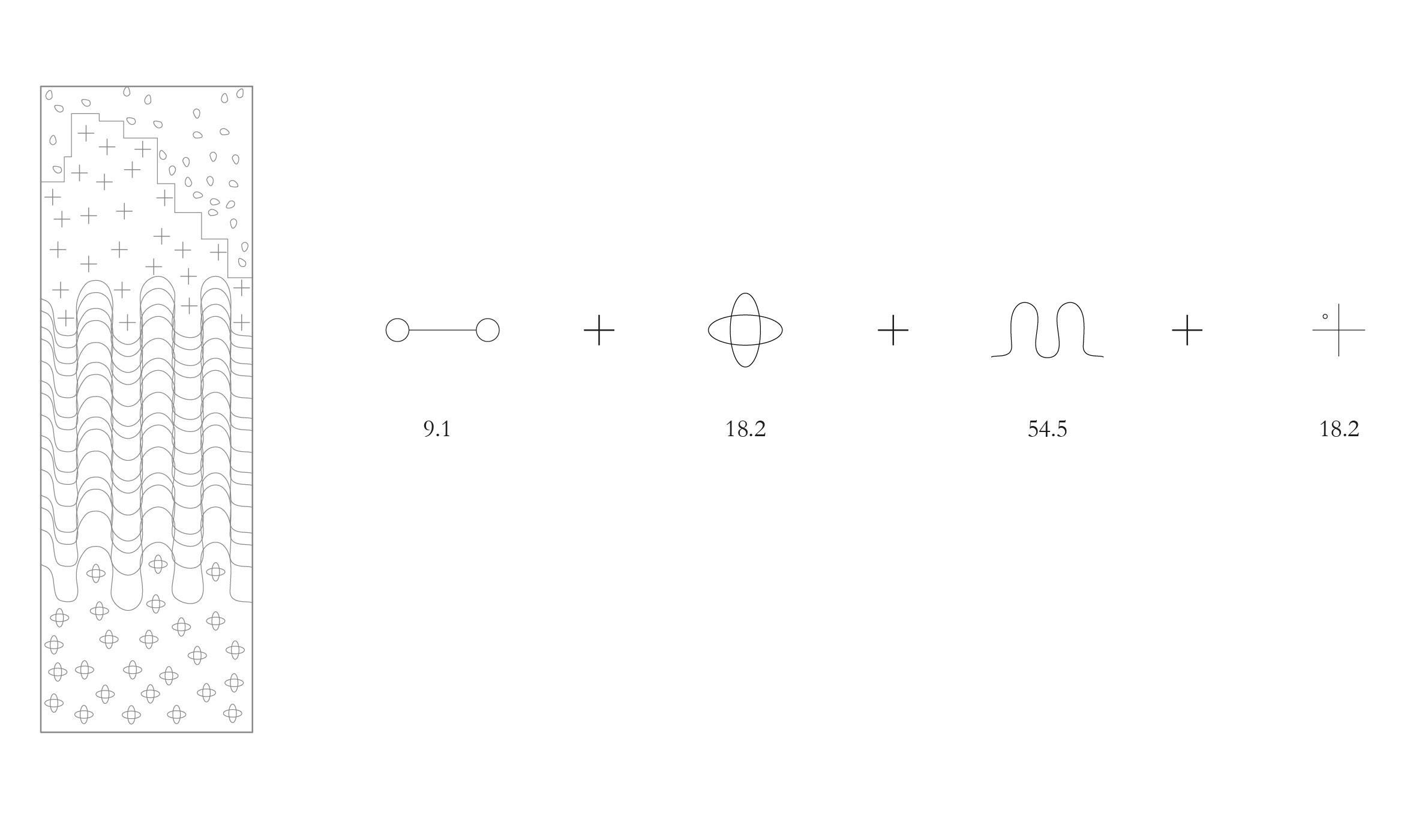
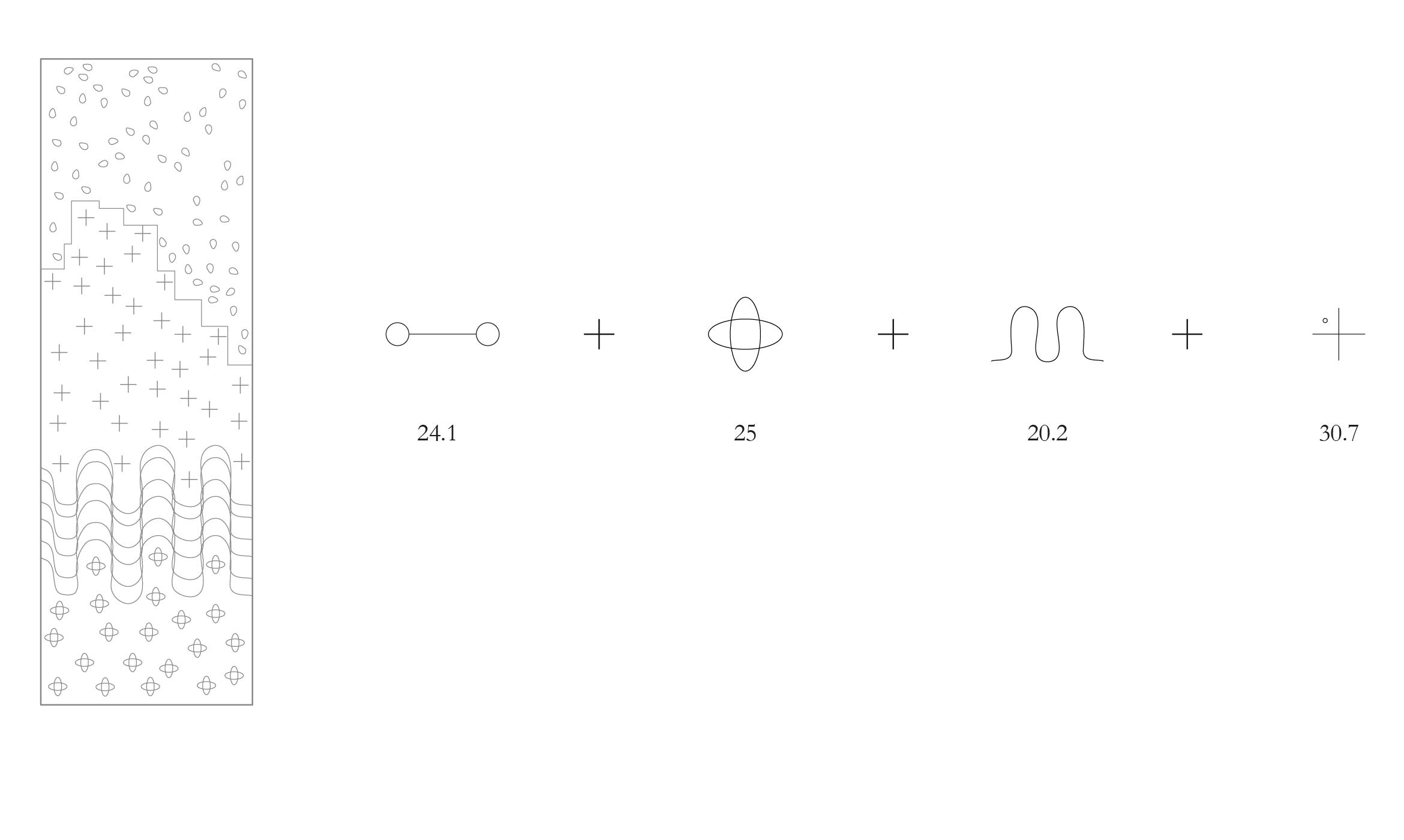
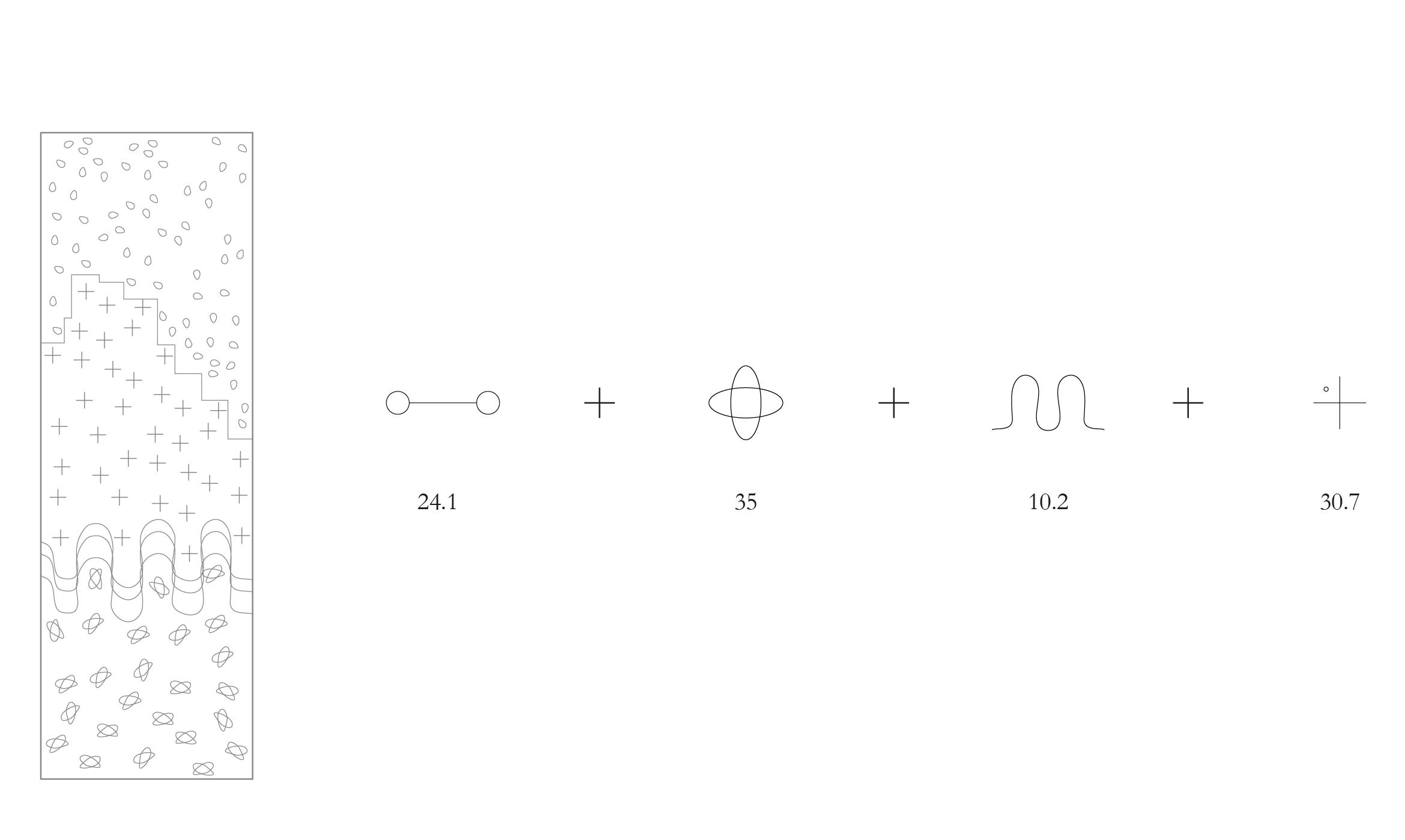

3.5
Experiment assumption
Experiment description
Experiment no. 23 AG 33.3% MaterialSW Composition25% strengthwetness Weak point transparencycracks elasticitydurability GL 16.7% ST 8.3%8.3%8.3%CACE ExtruderDimensionsDiameter 1 mm 3.5 10cm X 3.5cm ml 10ml syringe
Experiment conclusion
Layer Thickness 1.25-1.5 mm Number of Layers 2132
Volume π×52×31 = 775π = 2434.73 cm Area 517.5 cm
By choosing the 1 mm syringe – the model would probably be detailed but wouldn’t be able to hold itself to a very high structure.
Creating new material
Scale of the model doesn’t give sufficient information regarding strength and potential capabilities of the material. By scaling the nozzle and getting wider layers is it possible that the mix would hold itself better. Accuracy and continuous pace of material extrusion could also help.

experiment examines whether the mix of the seaweed with the other bio-polymers can hold itself (without any external reinforcements). It also examines the mix as a potential material for using in additive manufacturing technique using 3d printing.
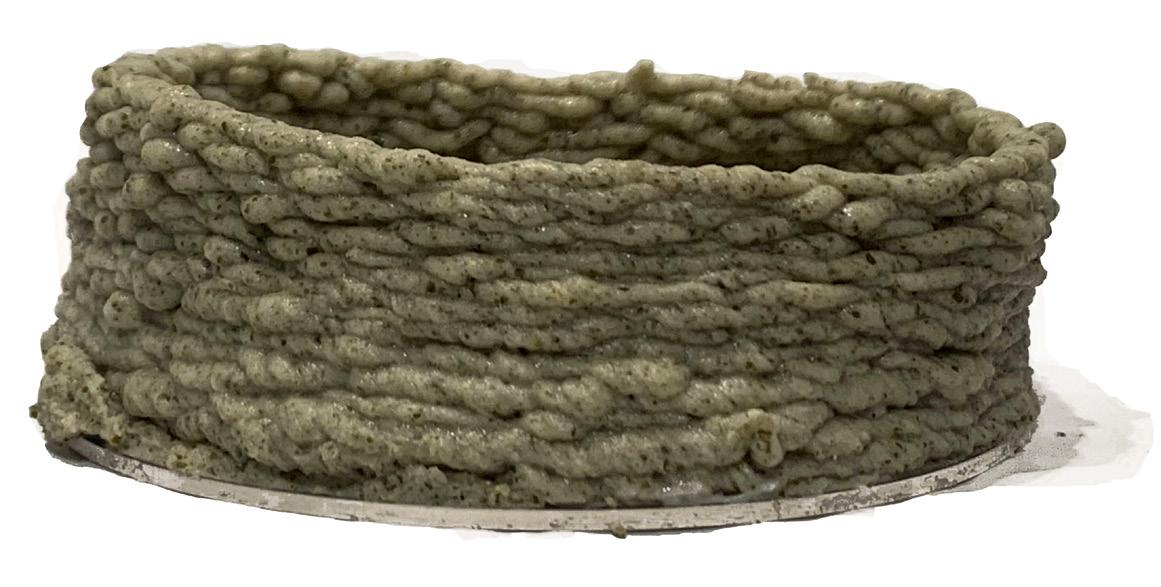
Creating a thin base layer of the mix that potentially would allow the upper layers hold themselves better and achieve more height. Then layering the mix one on top of each other using 1mm syringe. Pausing after every 4-5 layers to give the mix time for stabilize. Air bubbles within the syringe cause the mix suddenly to splash out.
After 23 layers (3.5 cm) the structure starts showing weakness. The model is very detailed thanks to the 1 mm nozzle of the syringe. However, bigger nozzle would probably allow achieving higher structure. The mix stronger than what was expected but takes time to dry and stabilize – this is also avoiding the model from achieving height.
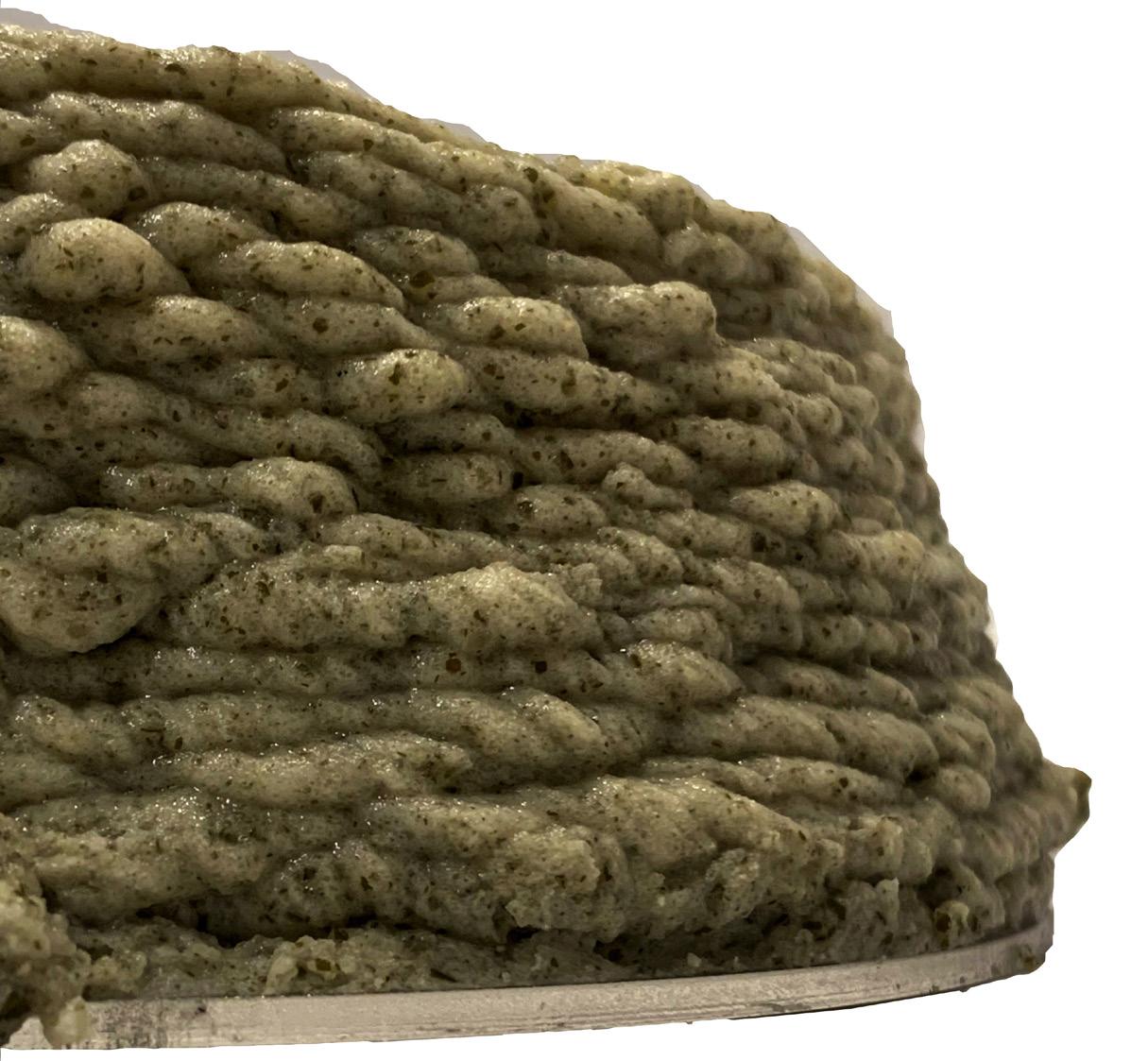
MATERIAL EXPERIMENTSThis32
Achieving Strength by Layering
Experiment results
new material Experiment no. 23 3.5
Experiment conclusions
Images 1-14 - Layering in different forms and structures 1 5 11109 141312876432 Achieving Strength by Layering
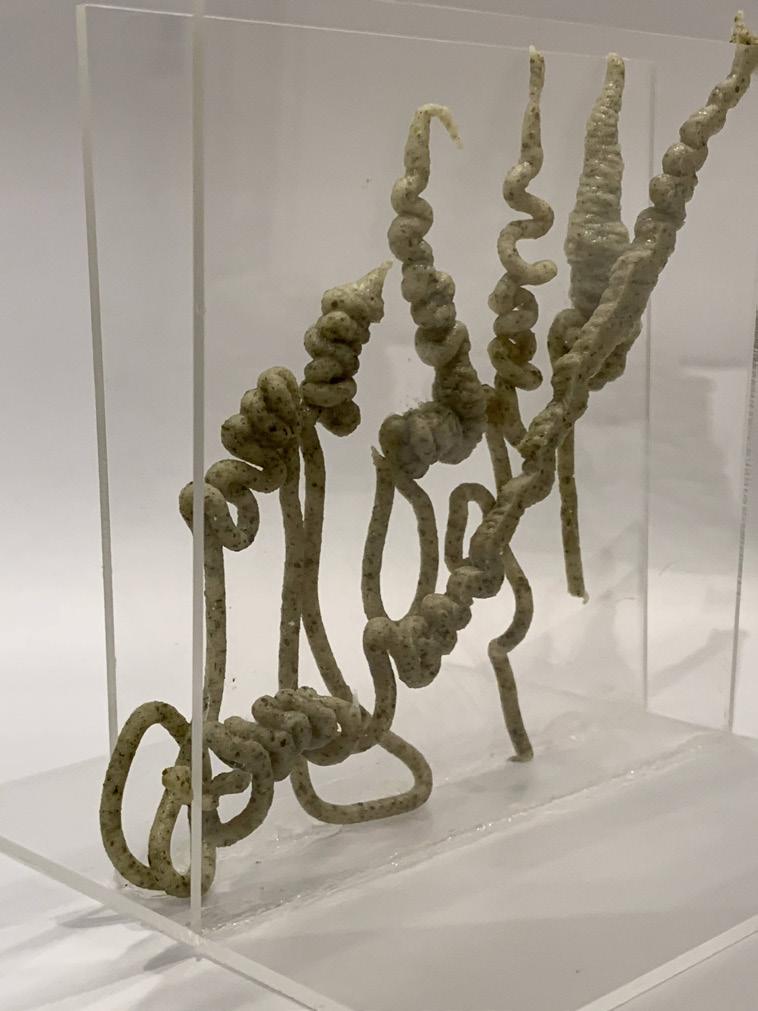
Scale of the model doesn’t give sufficient information regarding strength and potential capabilities of the material. By scaling the nozzle and getting wider layers is it possible that the mix would hold itself better. Accuracy and continuous pace of material extrusion could also help.
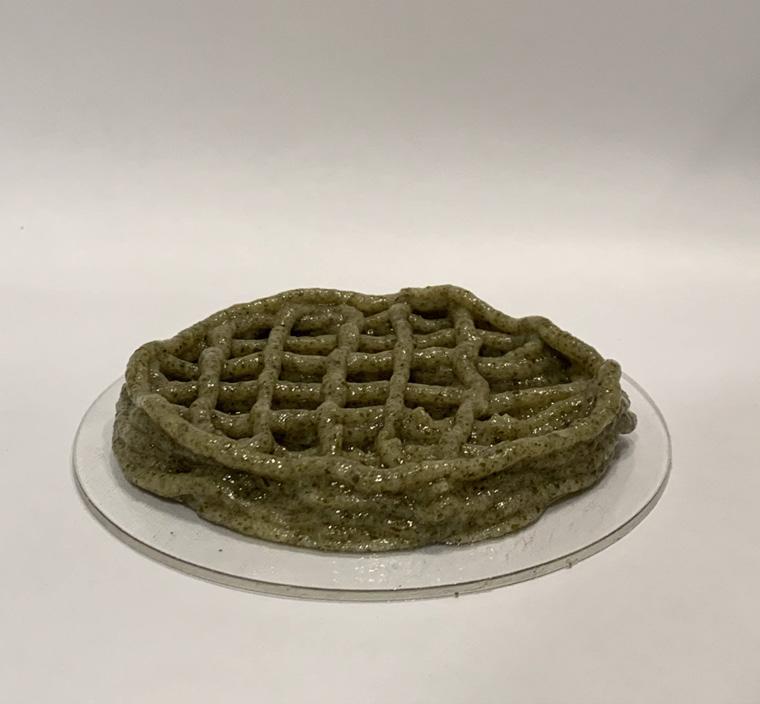

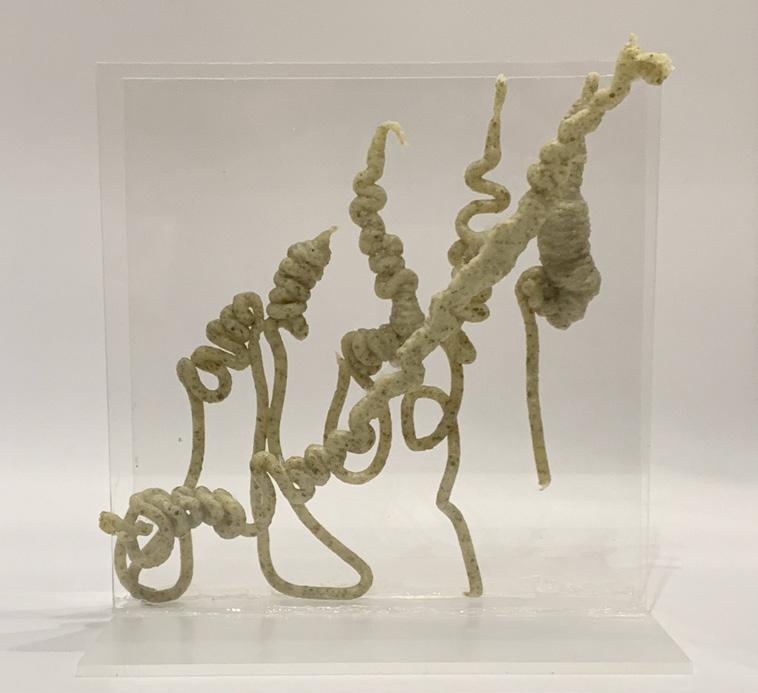
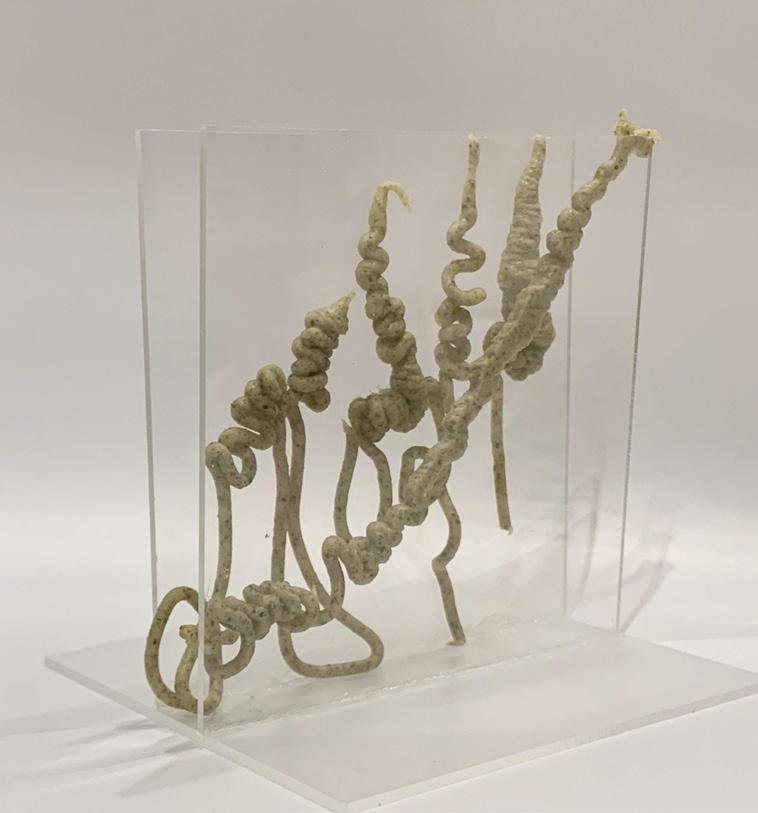
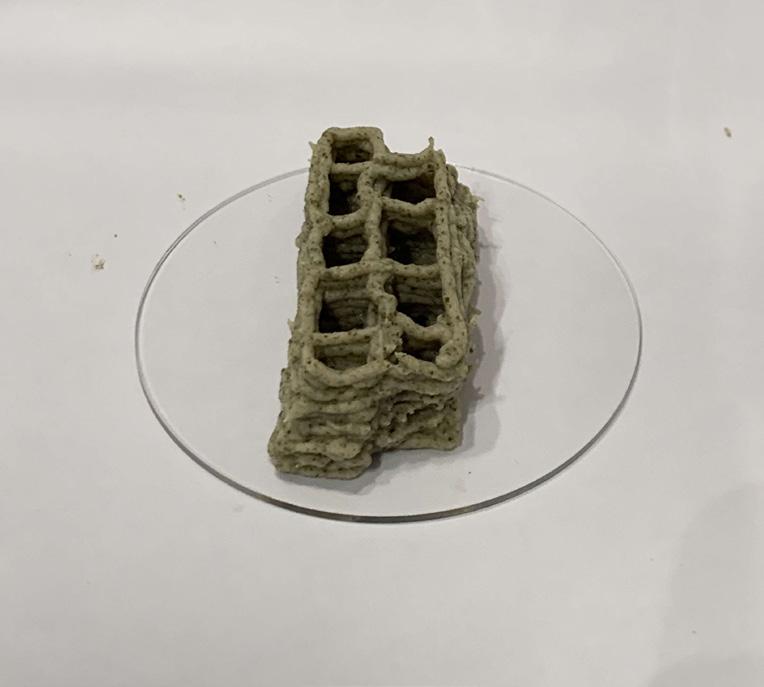
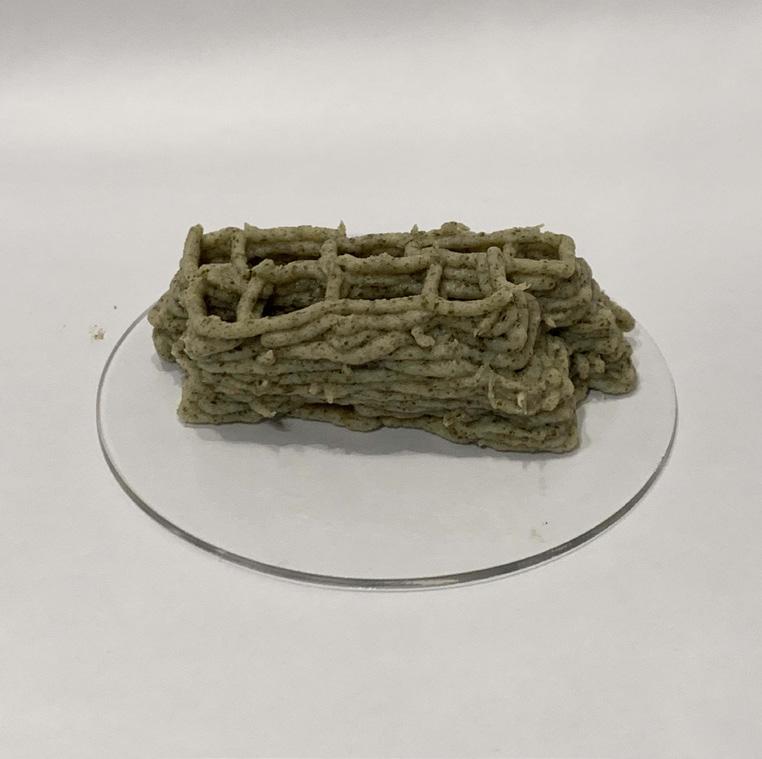
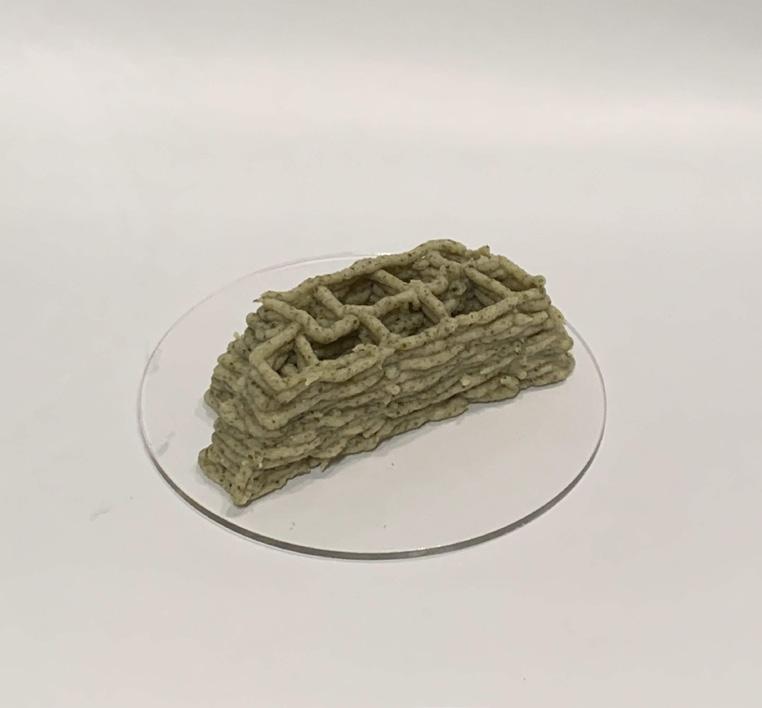
MATERIAL EXPERIMENTS34

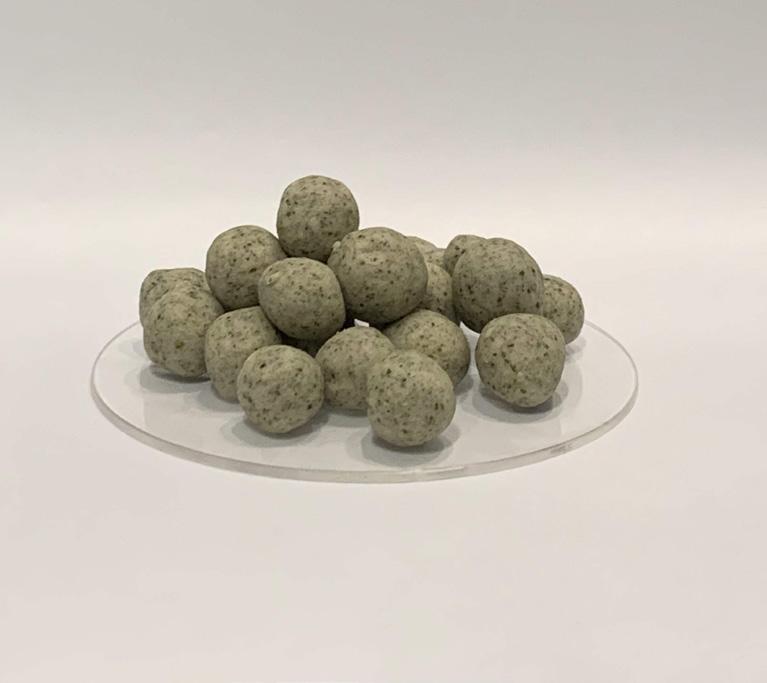
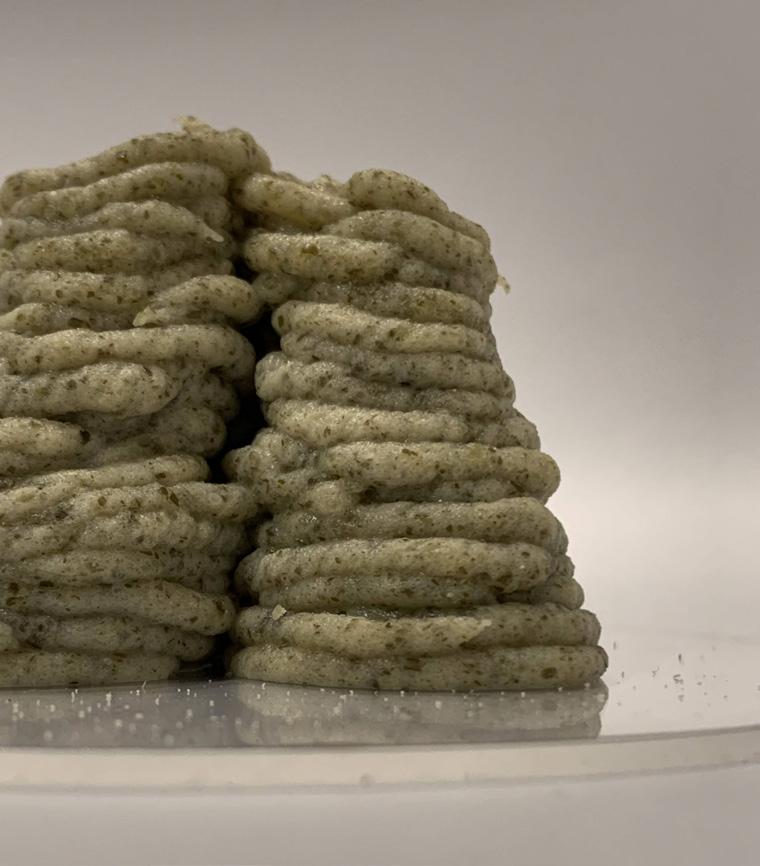
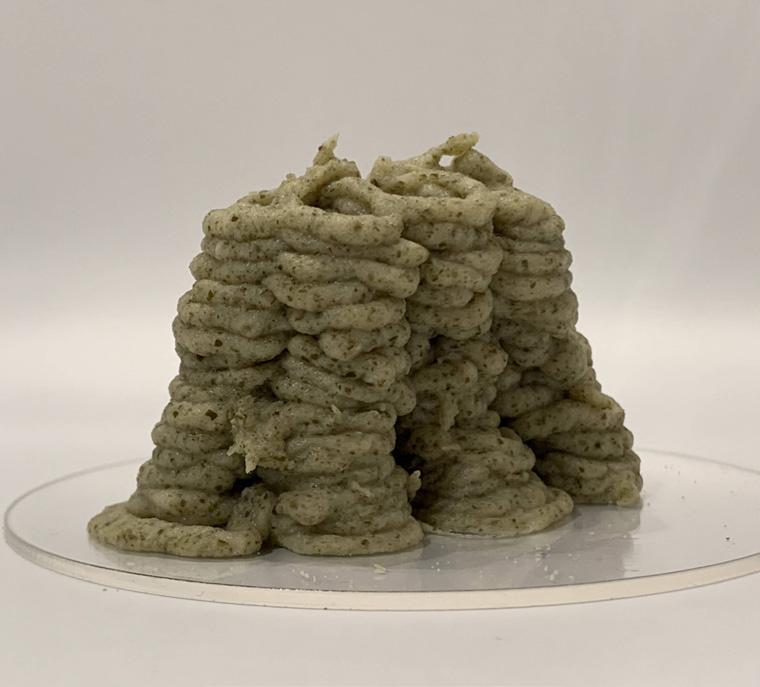
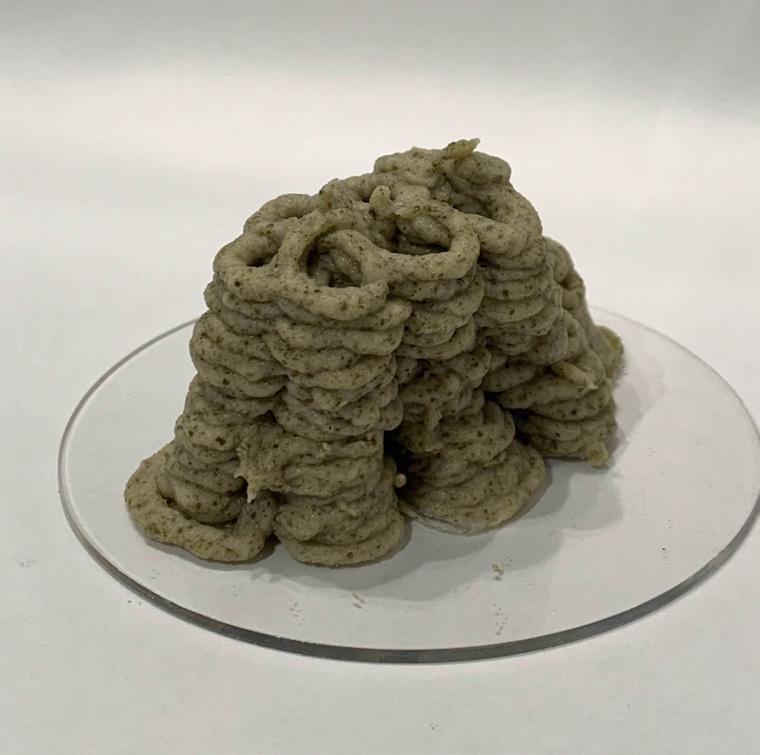
Creating
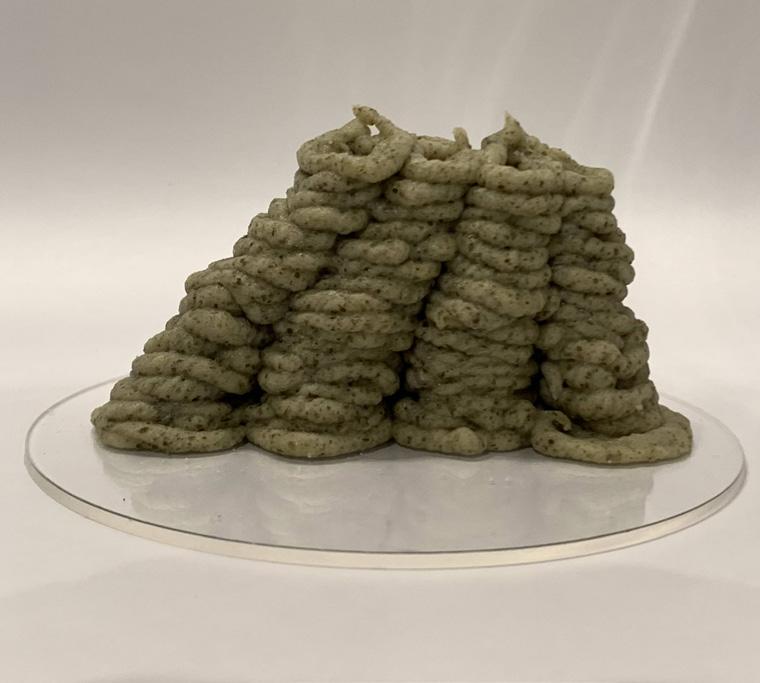
As it has been showed in the last experiment using syringe - the mix can be printed with air pressure. Since the shape and the proportions of the model are challenging to test the limits and the capabilities of the mix – it is assumed that the mix wouldn’t be able to hold itself. Height of layers of the model generated to be 3 cm, however taking under consideration material distortion - it is assumed that eventually each layer would be 2.5 cm Experimentheight. description

Layer Thickness 5 mm
Hight printed 7cm
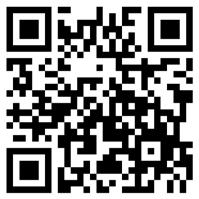
3.6
Layers in model 40 Printed Layers 23
The mix extruded easily and smoothly using a low air pressure. Adaptations had to be done during printing in real time. Speed of the robot has to change regarding the stronger parts and the weaker parts of the model (for example - accelerating the speed in weaker points to extrude less material). After about 18 layers (out of 30) the model started to crash in certain points.
Experiment result
The mix extruded smoothly, and the model reached 8 cm height (roughly 2.25 cm per layer). The model couldn’t hold itself because the mix was too wobbly. Furthermore, if the mix could dry or curate faster - it would enable the material to hold itself better by that build more layers. Few days later the mix starting to crack and shrink.
Max radius 6cm
This experiment examines a method of production process and scaling. Goals of using 3d printing were achieving accuracy, avoiding air bubbles and scaling the model to potentially architectural scale.
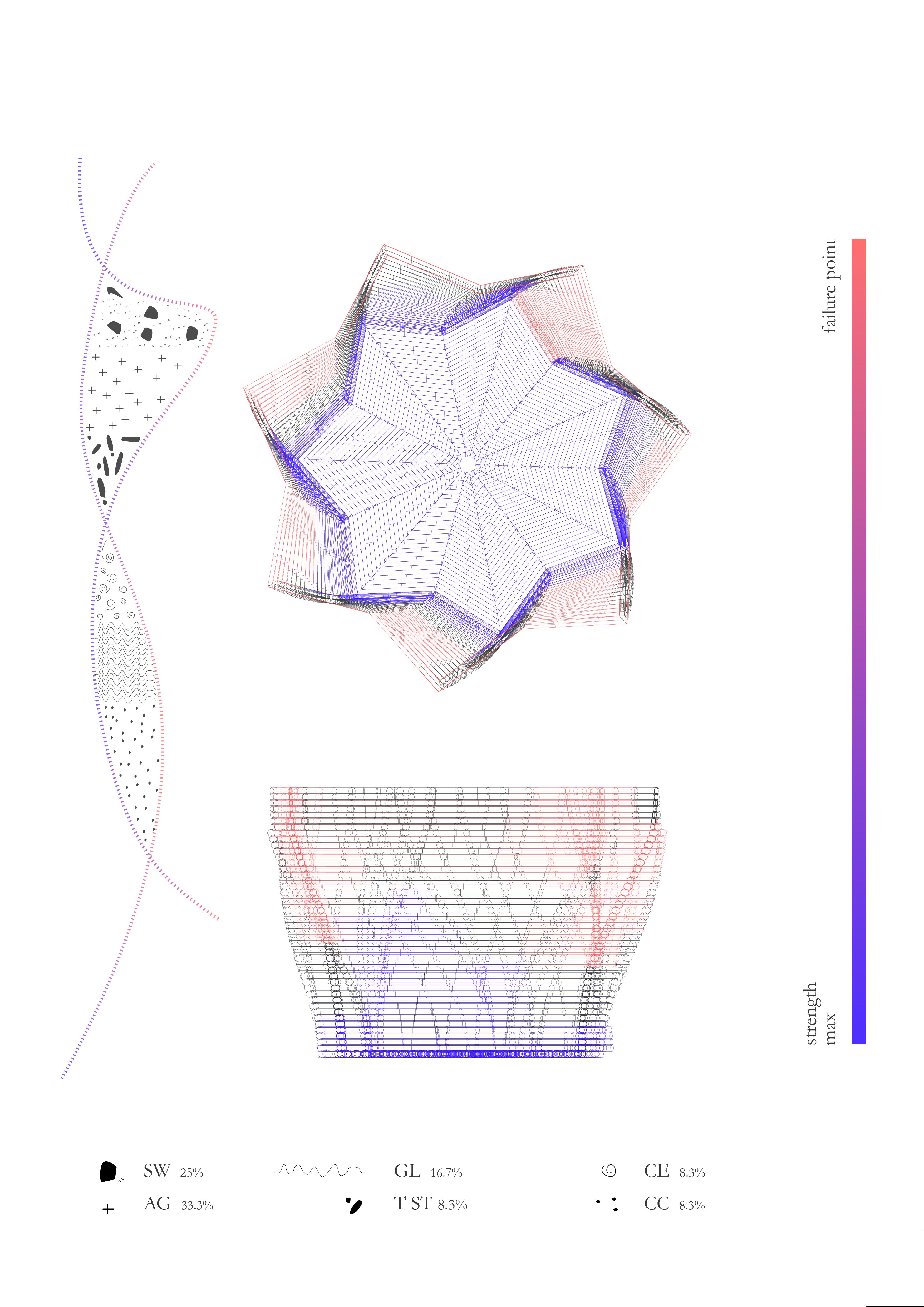
Experiment assumption
36 37 3D Robotic printing Experiment no. 25 Scaling up Tool KUKA KR-60 Extruder Diameter 5 mm AG 33.3% MaterialSW Composition25% strengthwetness transparencycracks elasticitydurability GL 16.7% ST 8.3%8.3%8.3%CACE
The mix must be improved. Faster curating time would bring better results. To avoid cracks the mix must be softer. Taking under consideration drying the mix in different ways (exposing to UV) and searching after another material (plasticizer) that would potentially bind the mix together.

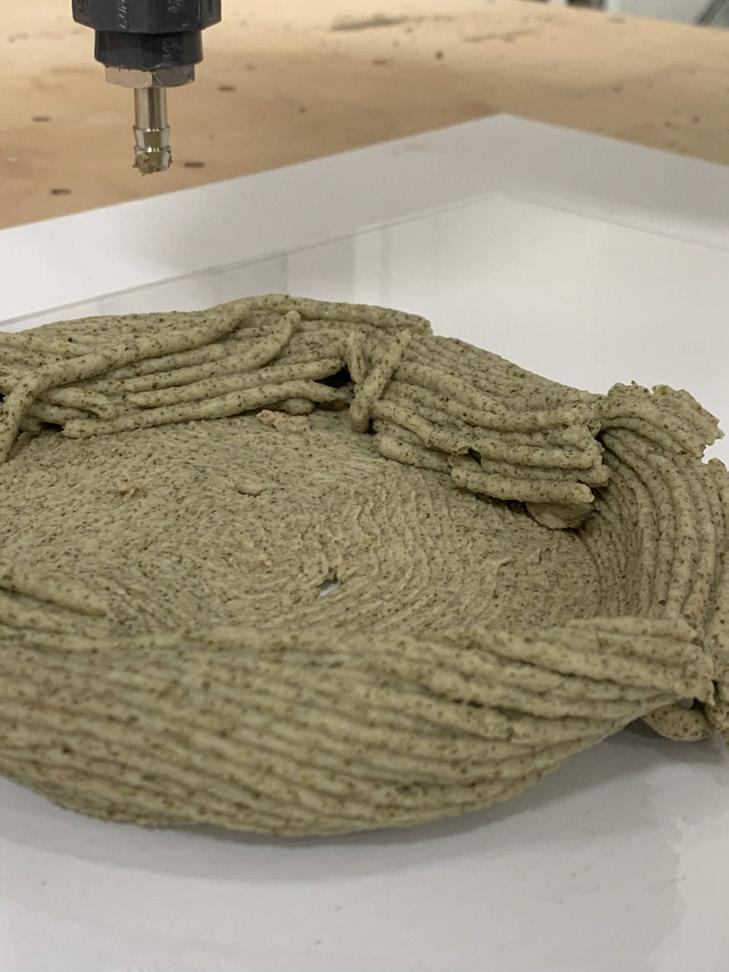
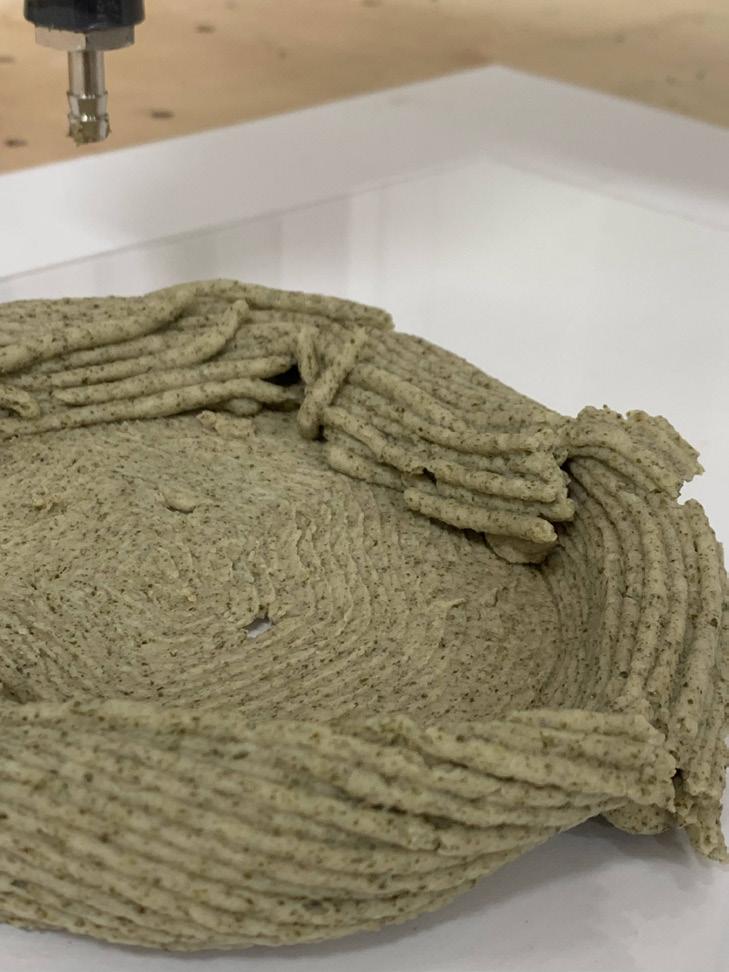
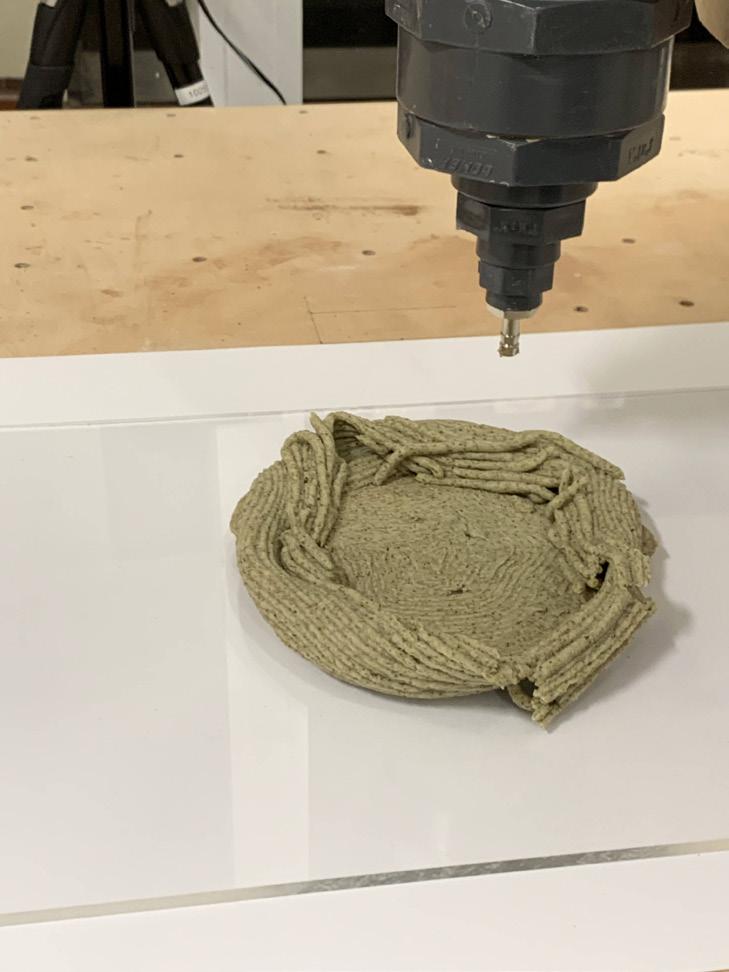
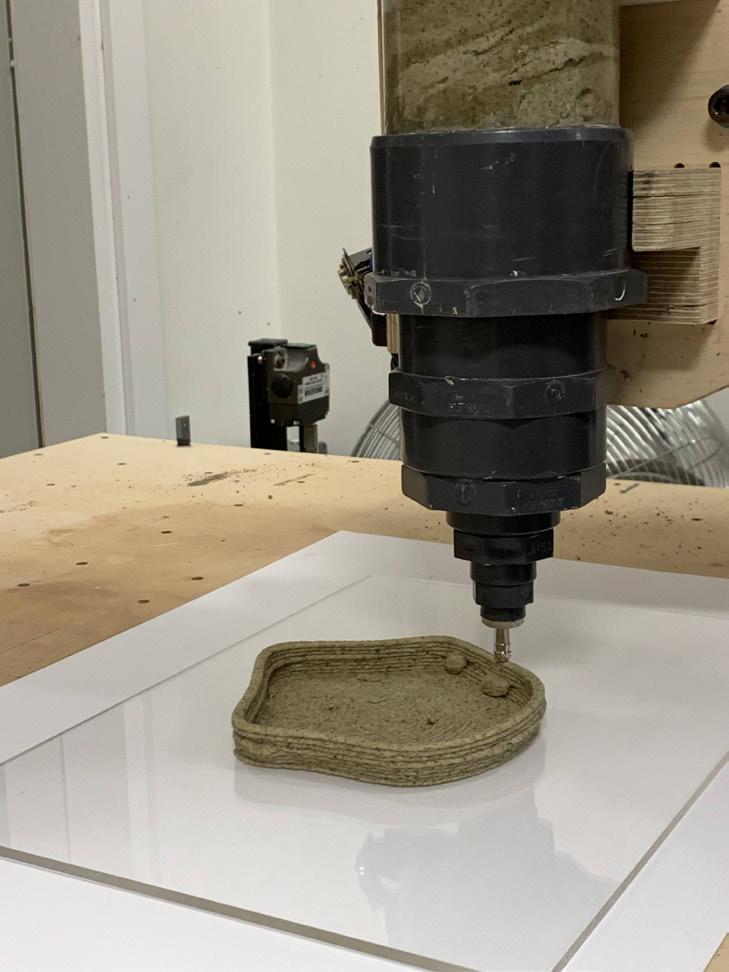
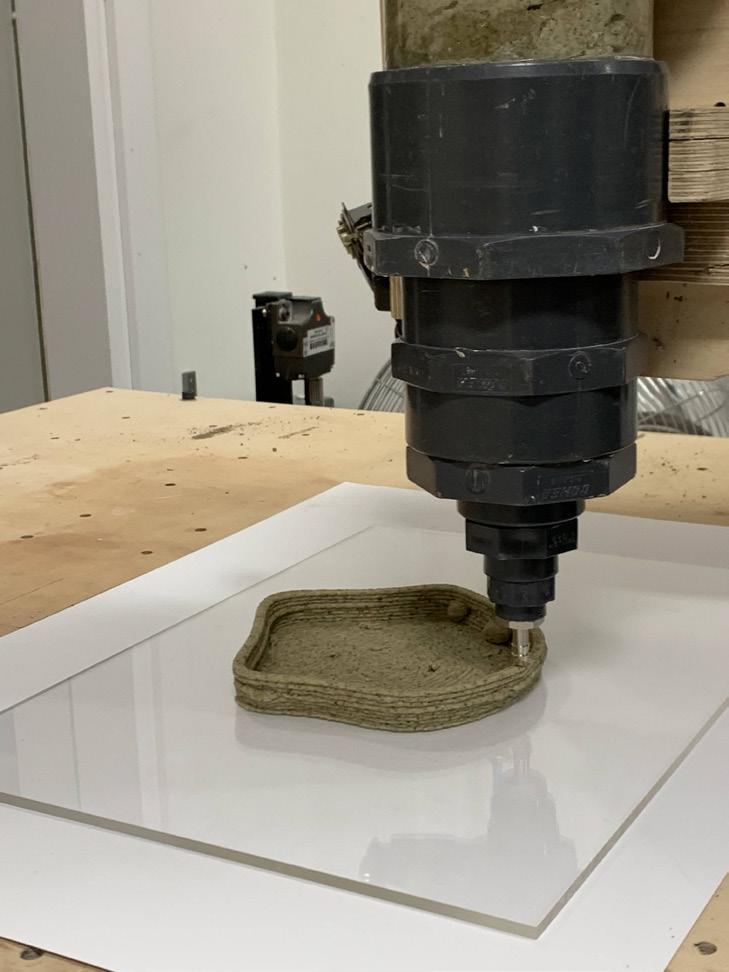
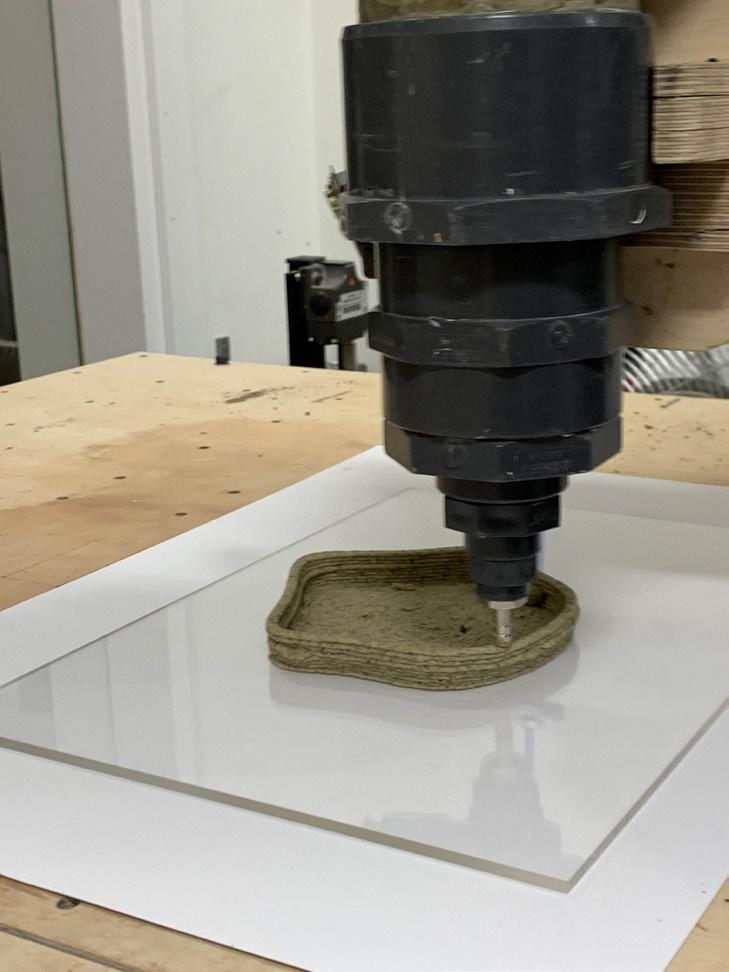
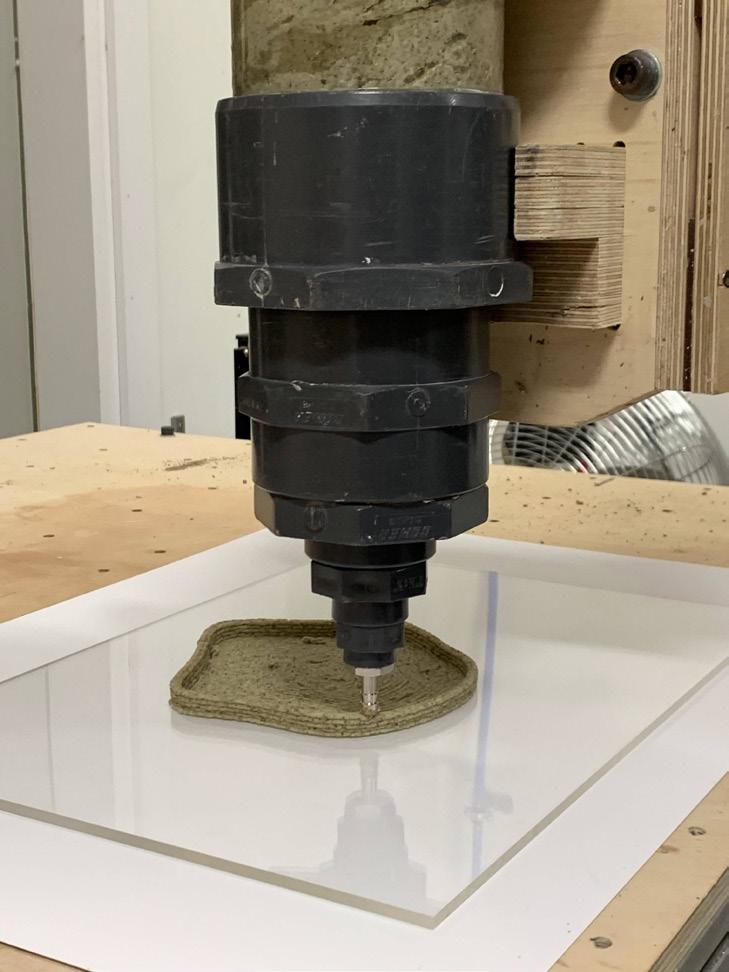

3D Robotic printing Experiment no. 25 Scaling up 3.6

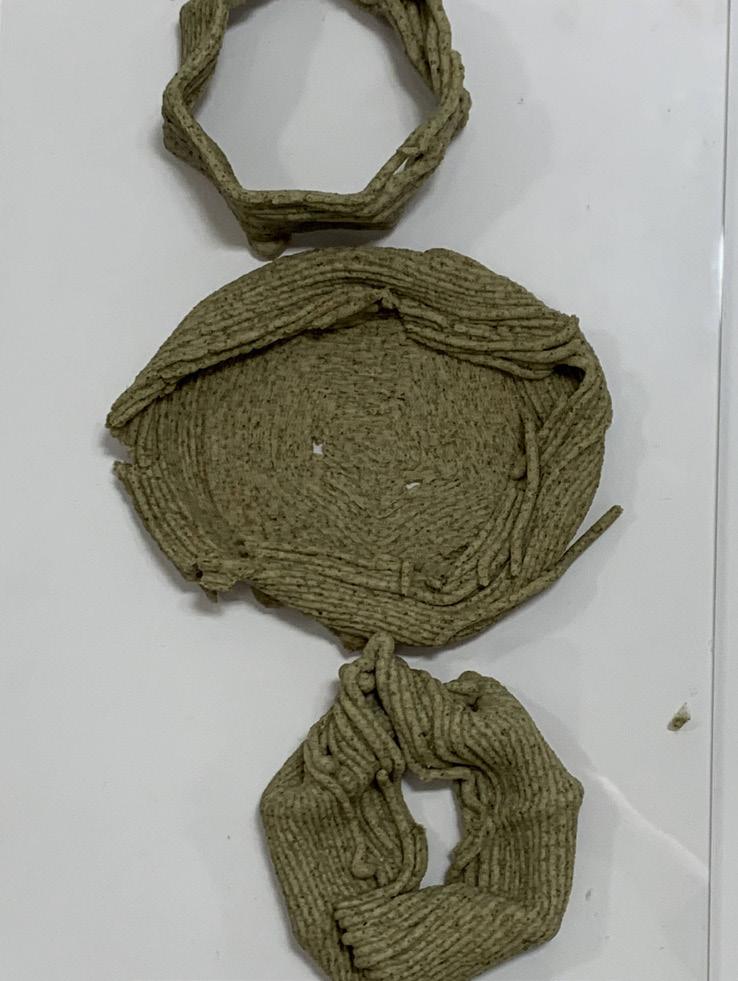
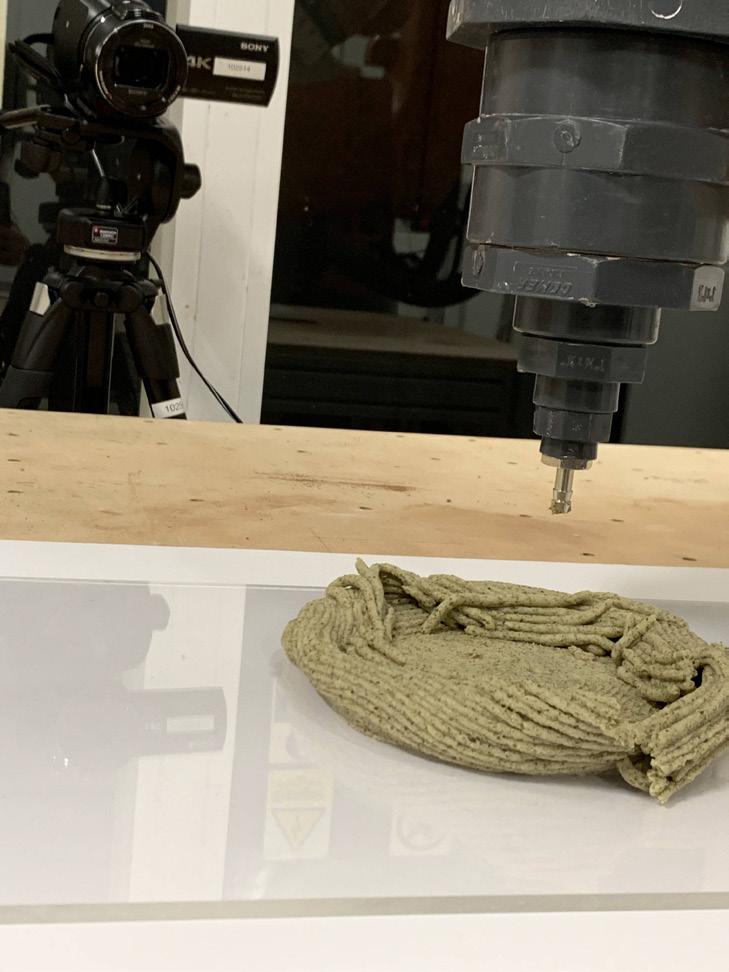
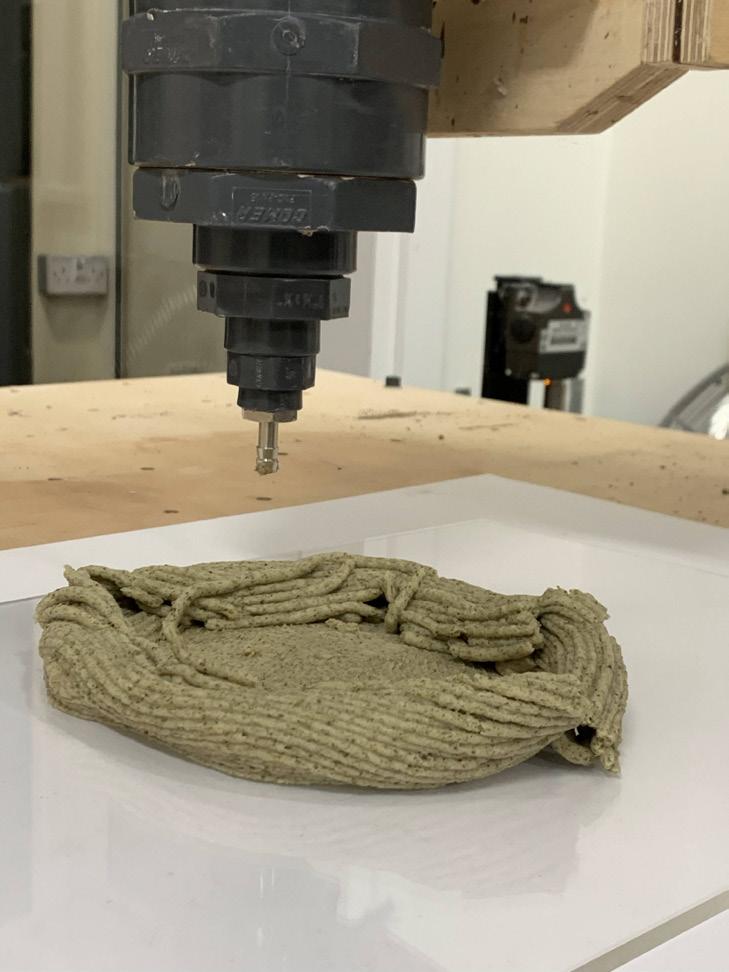
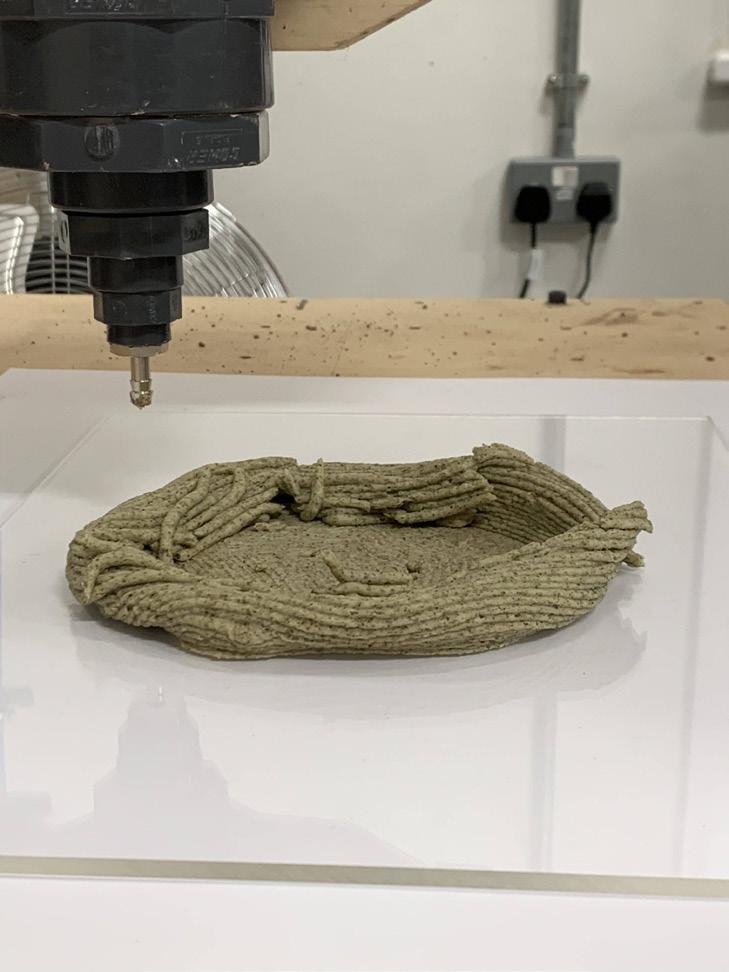
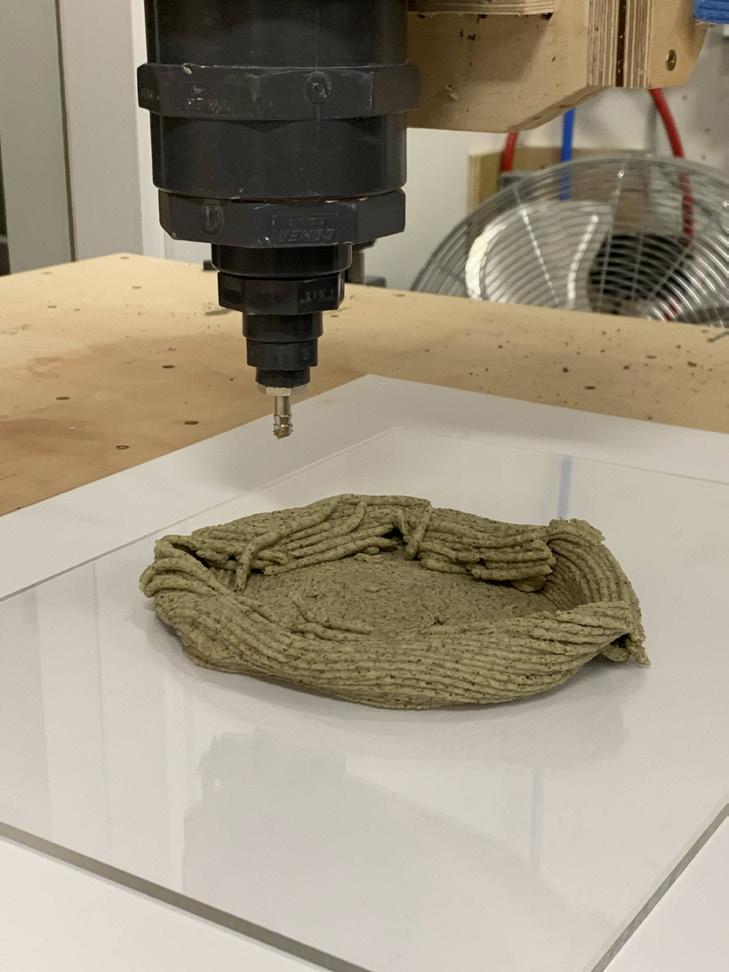
MATERIAL EXPERIMENTS38
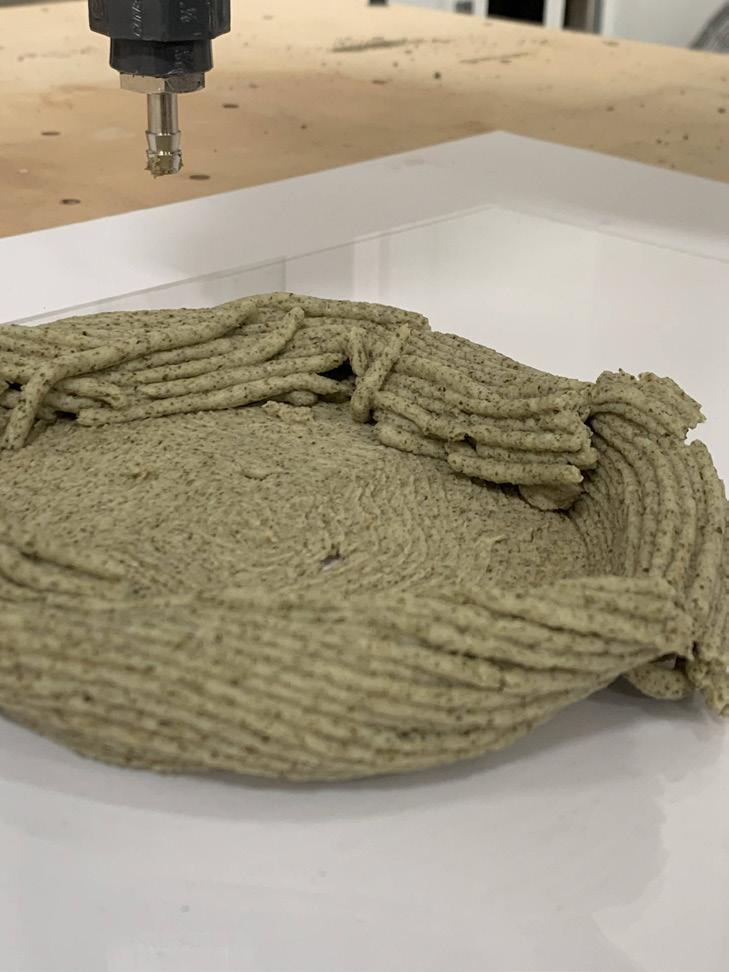
Experiment conclusions
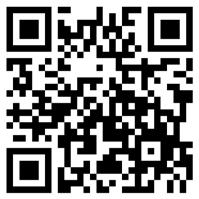
CHAPTER 04 CASE STUDIES 4.1 Shiver House 4.2 AlgaeDress - Carbon neutral fabric 4.3 Earwig and the Art of Origami
Each one of the case studies mentioned here has a key principle that I would like to apply in my project:
Rethink about the production process of textiles as it is one of the most pollutants releasing industries of the world - 20 percent of all freshwater pollution is made by textile treatment and dyeing - And turn it into a carbon-negative process.
Learning a sophisticated mechanism such as the elastic joints of the earwig's wing.
Developing and design a responsive system that reacts to site conditions.
The house employs the use of 600 kinetic counter-weighted shingles which respond to the changing weather conditions of the site. Wind, rain and snow cause the shingles to rotate into a closed position giving the structure the temporary appearance and function of a shelter. The Shiver House is constantly transforming between being a functional shelter and a poetic and experiential device. Users that sit within the structure can observe the ever changing environment as they watch the kinetic shingles modulate the internal light levels as well as views out to the surrounding landscape.
Materials & Construction
tensioned steel wire folded and cut Airplane, soaked in a protective oil stainless-steel nut and bolt
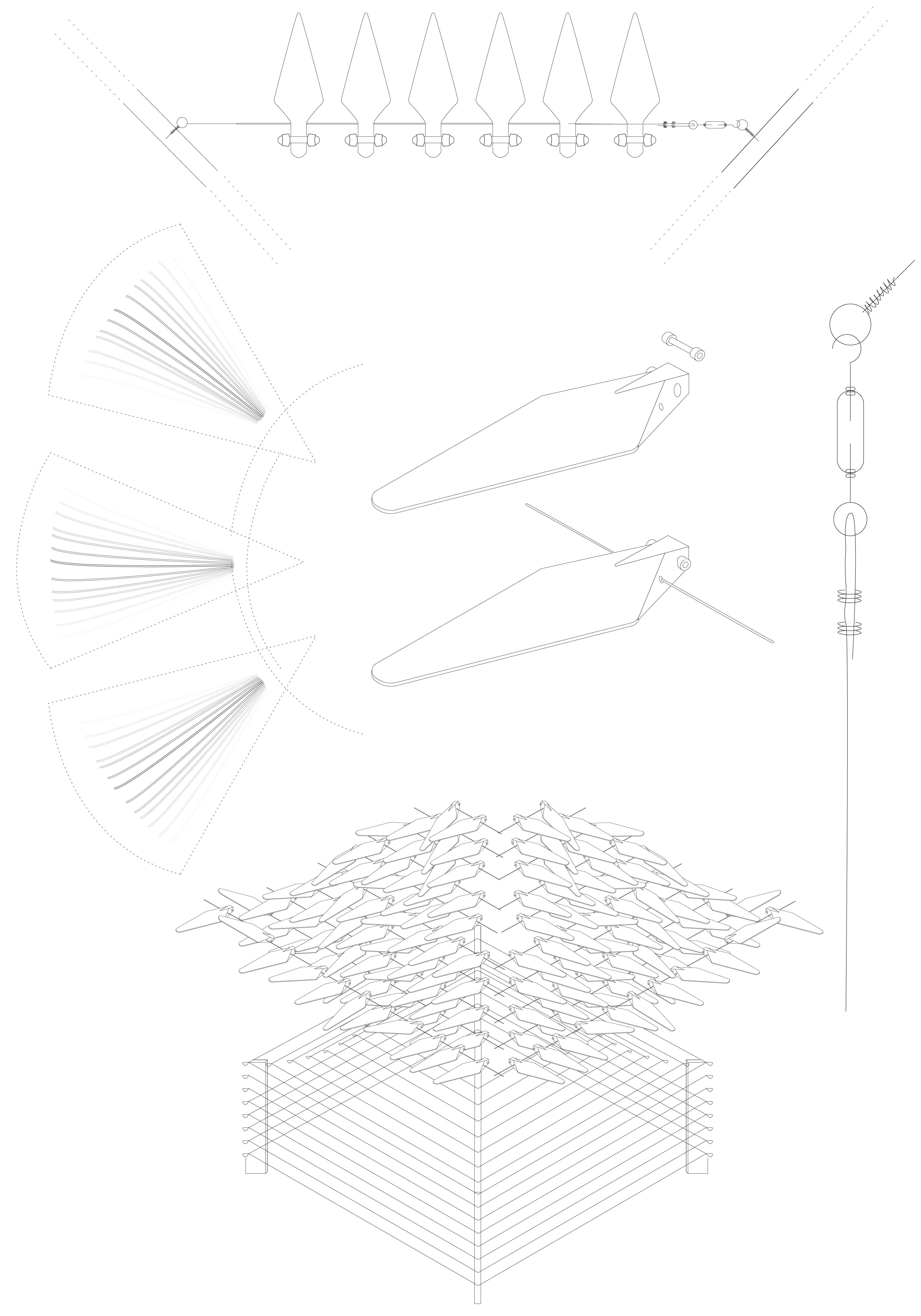
1 1 2 2 3 3 4 4 4 5 5 Shiver House Responsive systemNEON 4.1
timber structure
600 Kinetic Shingles
42 43
Shiver House is a radical reinvention of the common Finnish Hut (mökki). The project is a kinetic “animal like” structure which moves and adapts in response to surrounding natural .forces
The project is nutaconstructedcounterweightprotectivebeenPlyandusingconstructedshinglesshingles.counterweightedtoareaswireswire.ofnumberwhichtimberusingconstructedasimplestructuresupportsaofrowstensionedsteelThesesteelaretreatedbatonsanddesignedholdtheTheareafoldedcutAirplanewhichhassoakedinaoil.Theisusingstainless-steelandbolt.
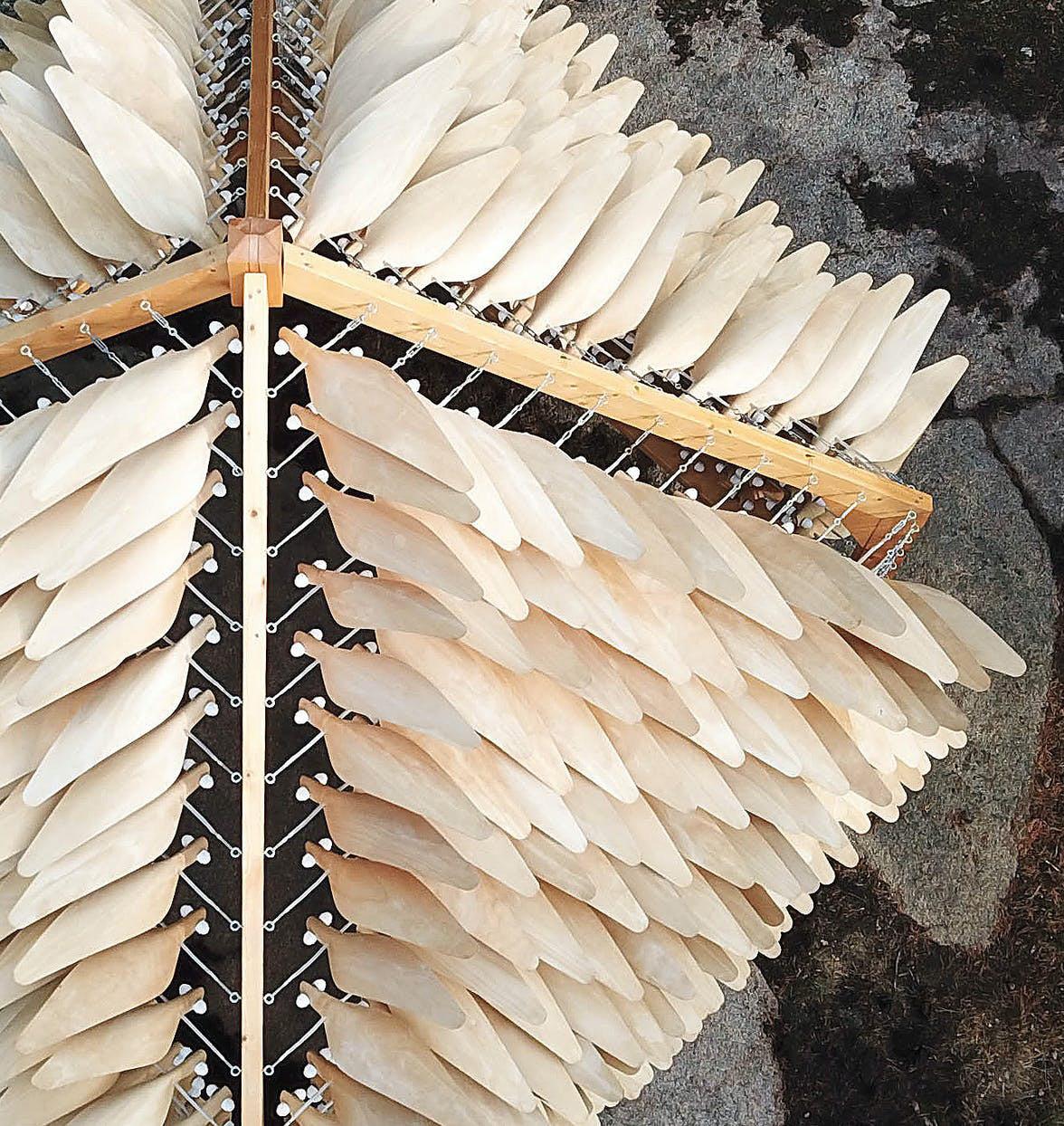
ETH PurdueZurichUniversity
The crucial factor in the design of the insect’s wing is its elastic folds, which can operate either as an extensional or rotational spring.
Fashion designer Phillip Lim and industrial designer Charlotte McCurdy created a petroleum-free dress covered in bioplastic sequins.
Algae bioplastic fronds are sewn onto a biodegradable base layer made of plant fibres. This makes the dress free of crude-oil derivatives such as synthetic fibres, dyes and plastic sequins, which have recently come under fire for the pollution they cause.
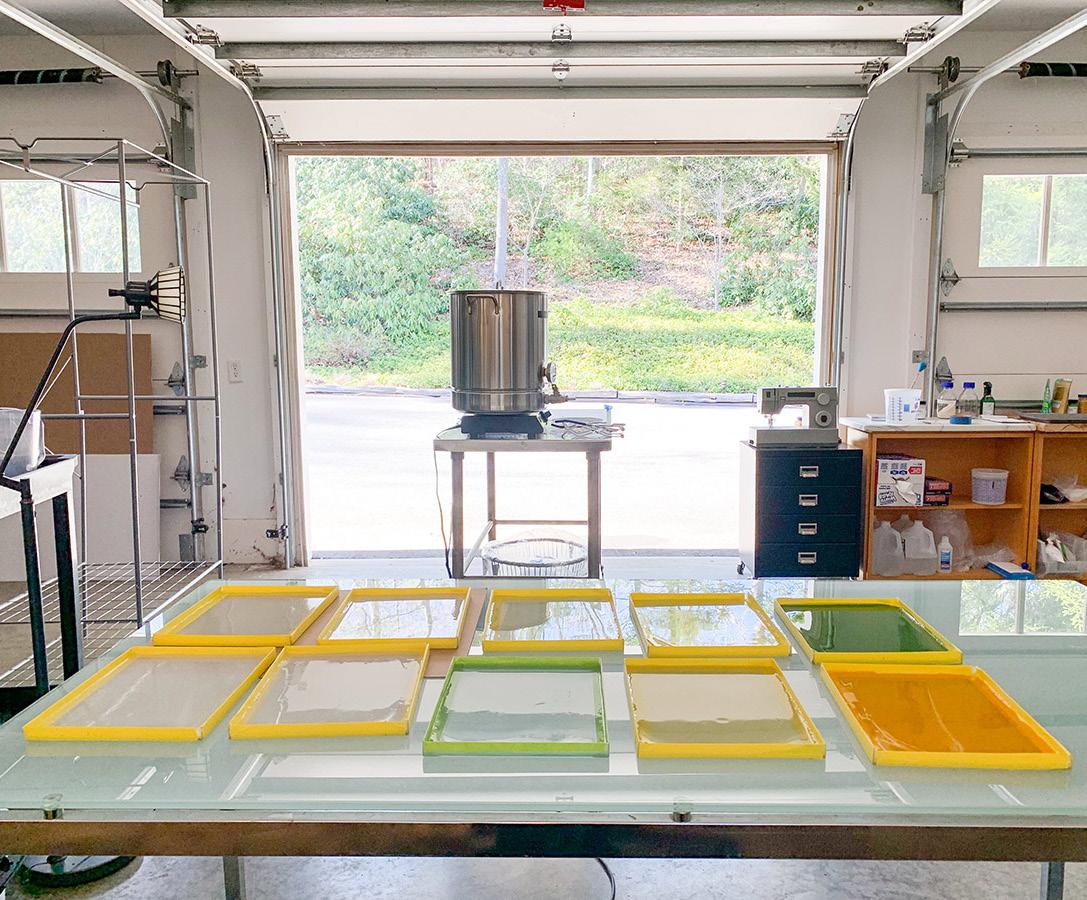
SEQUINS ARE SYNONYMOUS WITH PLASTIC WASTE.” PHILLIP LIM anpreviouslyhasdevelopedalgaebioplastic
Petroleum-Free Dress ONE X ONE PROJECT Phillip
film made entirely of marine macro-algae, which removes and sequesters carbon from the
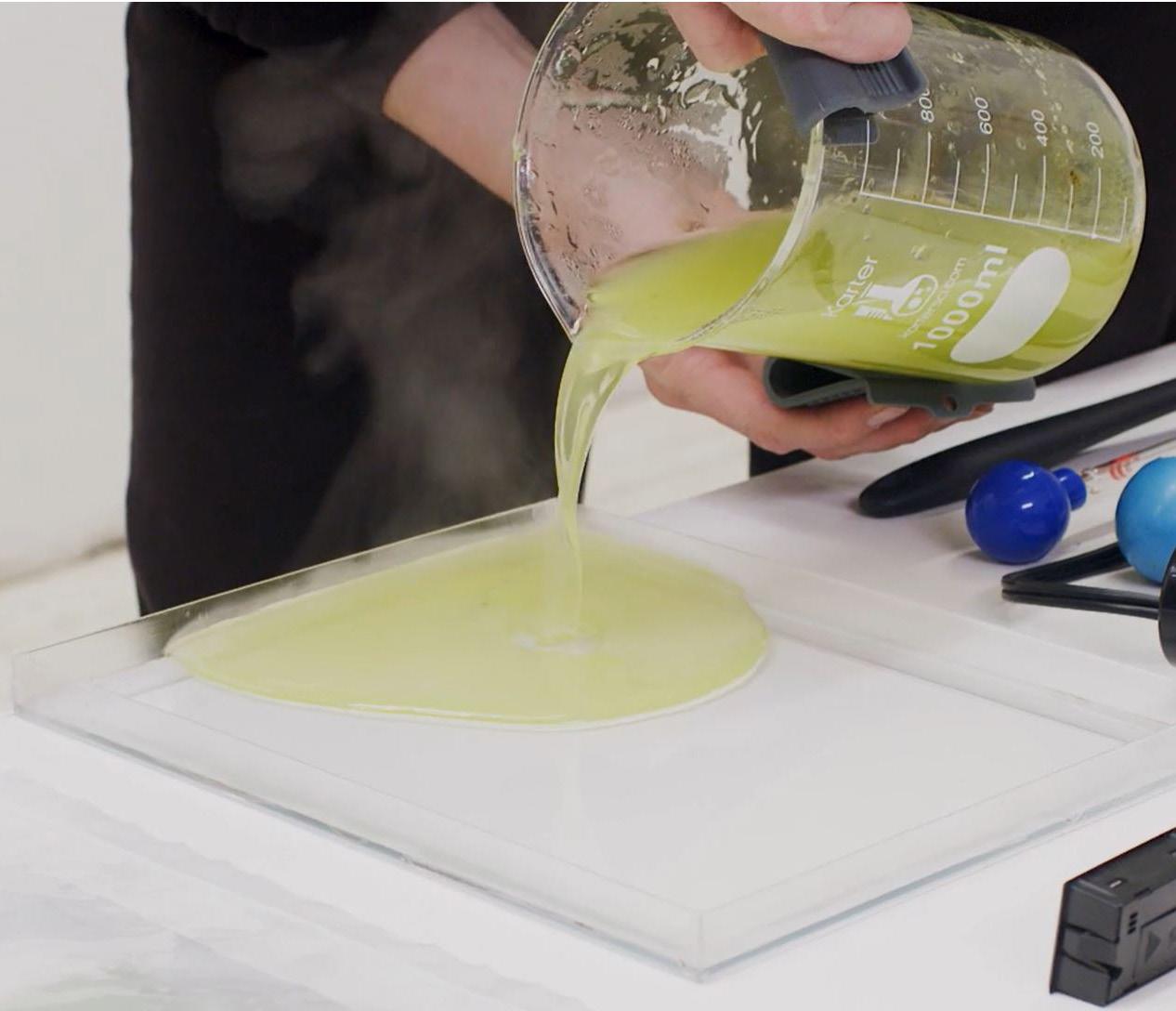
If the wing were to operate on the classical origami principle – using rig id, straight folds with an angular sum of 360 degrees at their intersections – the earwig would only be able to fold its wing down to a third of its size.
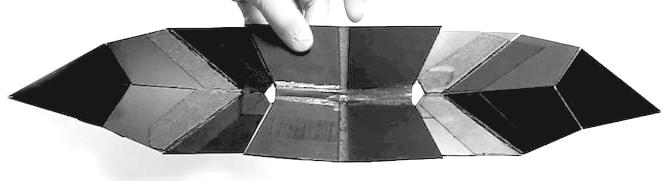

Resilin is an elastomeric protein found in many insects and other arthropods. It provides soft rubber-elasticity to mechanically active organs and tissue; for example, it enables insects of many species to jump or pivot their wings efficiently. Resilin is currently the most efficient elastic protein known
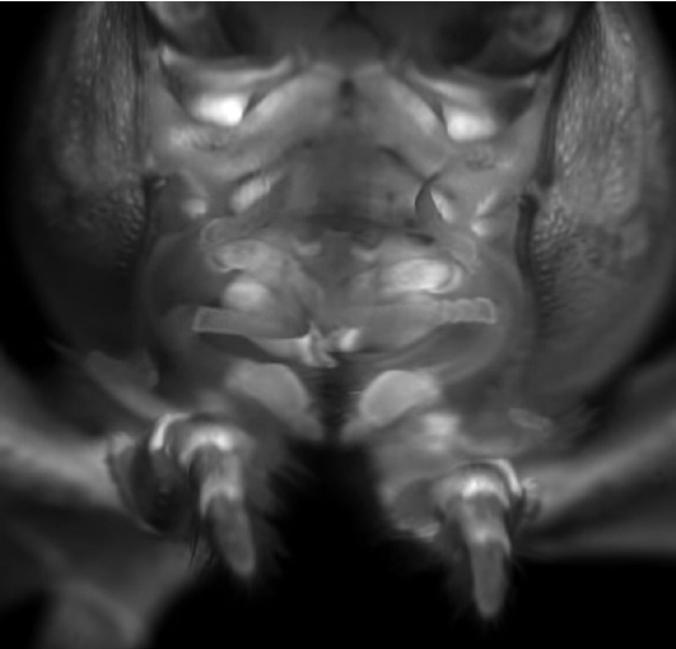

MAKING
McCurdy
OUT
negative.materialmakingthroughoutatmosphereitslifetheresultingcarbon Extracting frombio-polymerthetheseaweed Casting the material in a deeper mould made of glass that transfers its reflective finish onto the final Cuttingproduct.thefilms into squins 1 1 2 2 3 3 54 5 4 Exposing the algae mix to heat to bind together Mix poured into a custom-made mould Cure and solidify + + strenghtadditivesplant-basedheatingwater-thethemixthepolymerbondsstarttoopenupandrelink moldsmadecostum-mixpouringthentheintoglass + + + + in the temperarureright
SO WE
IS
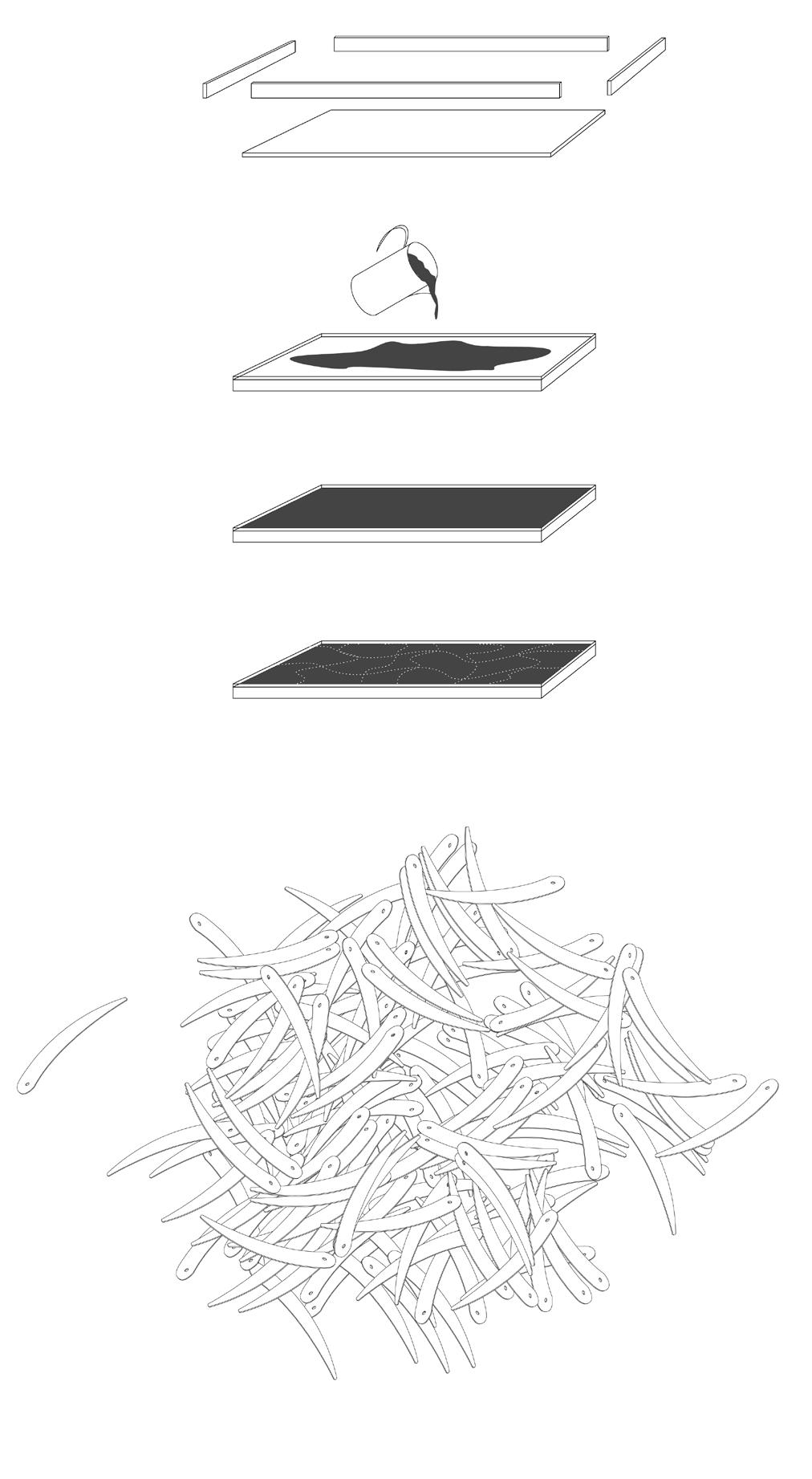
foldsElastic CharlotteLimMuccurdy ofandEarwigstheartOrigami
(Elvin et al., 2005). The elastic efficiency of the resilin has been reported to be 97% (only 3% of stored energy is lost as heat).
“THE KEY TO THIS EXPERIMENT TO TAKE IT OF A MUSEUM CONTEXT PUT IT IN REAL LIFE. THOUGHT ABOUT: PUSH IT INTO SEQUINS?
The crucial factor in the design of the insect’s wing is its elastic folds, which can operate either as an extensional or rotational spring.
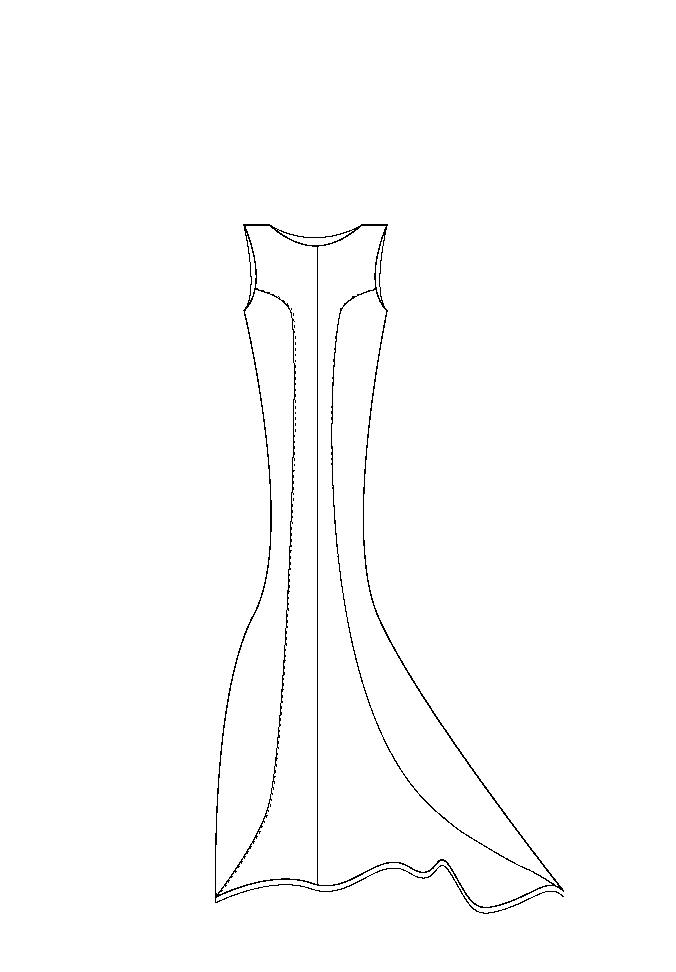
The wing joints are made from layers of a special elastic biopolymer, resilin, whose arrangement and thickness determines the spring type.
44 45 productionCarbon-negativeprocess
HOW DO WE
The large wing area allows the insect to fly, while the compact way the wings retracts enables the creature to tunnel underground without damaging its Thewings.wing design has another unique infeature;itsopen, locked state the wing remains stiff with no need for muscle power to provide stability.

With just one “click”, the wing folds into itself completely, without muscular actuation.

In some instances, both extensional and rotational functions are combined in the same joint.
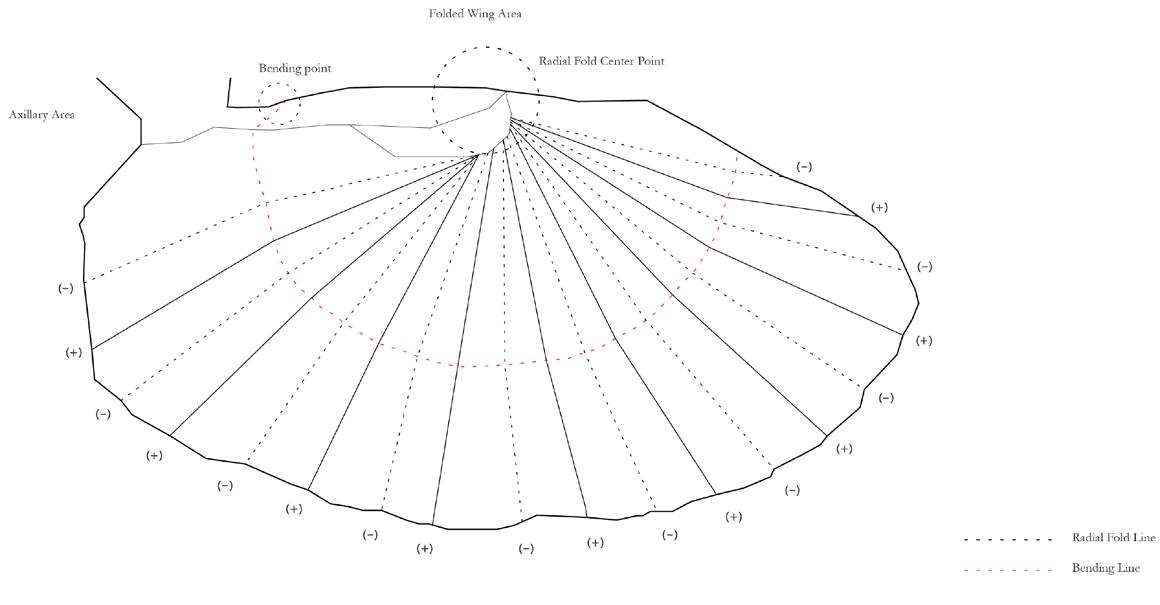
When open, the earwig wing expands ten times larger than when closed –one of the highest folding ratios in the animal kingdom.
Reaserchers at ETH zurich and Purdue University have been studying the secret of the earwig's origami-like wings and have created an artificial structure that functions using the same Theprinciples.project comprises four rigid plates connected to each other by a soft elastic joint. The object is stable when open, but folds together automatically when touched. The self-folding origami elements are currently only available as prototypes. Self-locking origami structures would save space, weight, and energy, as they do not require any actuators or additional stabilisers.
AND
4.2 4.3
MATERIALCOMPOSITETOSLURRYFROM
5.1
EXPERIMENTSMATERIAL PART II
CHAPTER 05
Vessel prototype - Strength and translucency 5.4 Layering - Strength 5.2 Webbed structure - Elasticity 5.5 A study of joints 5.3 Casted joint, webbed structure - Elasticity 5.6 3D robotic printing - Strength 5.7 Adaptation and optimization of the robot
AsREACTIONCHEMICALPRODUCINGmarkedinthe conclusions from the last printing experiment (page 37), faster curating time would be achieved by producing chemical reaction. This would potentially bind the components together. It might also help avoiding cracks in the mix after drying. Composite material; contains at least two components – soluble material, and polysaccharides.
48 49 15432 “Vessel” prototype Strength and translucency After getting transparenciesRangestrengthCompressionpotentialExperimentpressing.squidgy,“wet”inmodel:PropertiesbreakupandTheare“walls”translucentbasetransparenciescontainsTheExperimenttopthedrying,BeforetolayercastingthisThedescriptionExperimentcracks85cureThemadefewbetweenthecomponentspropertiesregardingunderstandingbetteroftheandpotentialbindsthem–changeshadinthemix.results-fastertime(aboutseconds),noafterdrying.techniqueinexperimentwasathinbasetogivestrengththestructure.baselayerstartlayeringmaterialoneonofanother.resultsmodelrangeof–layerismostandofthemodelalmostopaque.mixdriedfastcouldeasilyturnsidedownwithoutordistort.oftheFlexiblethinnerparts,look,glossy,strongwhenof 5.1

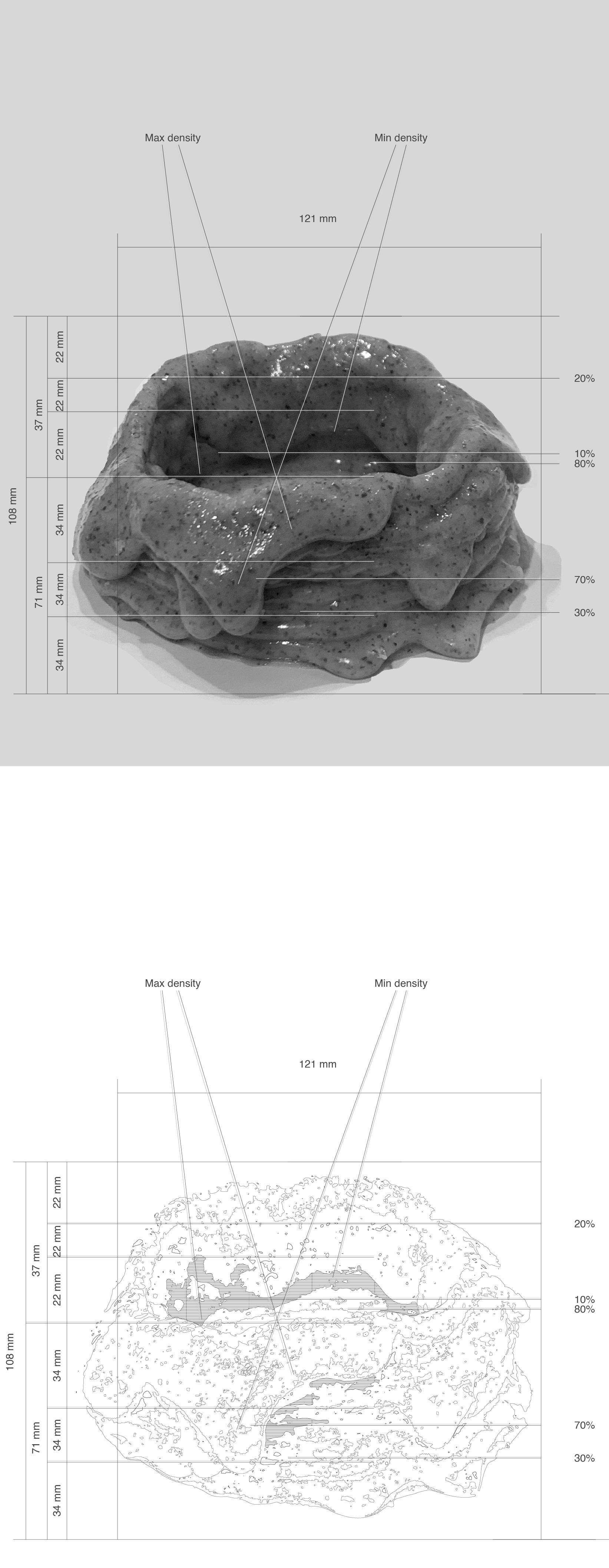
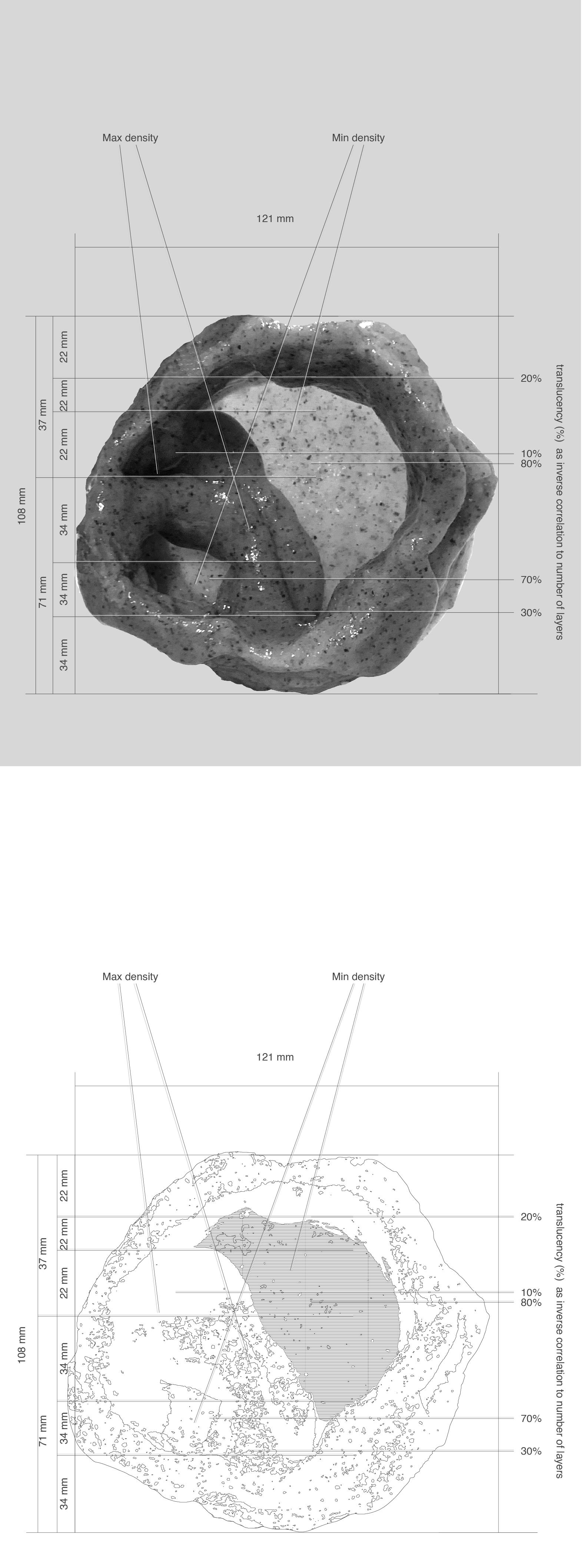
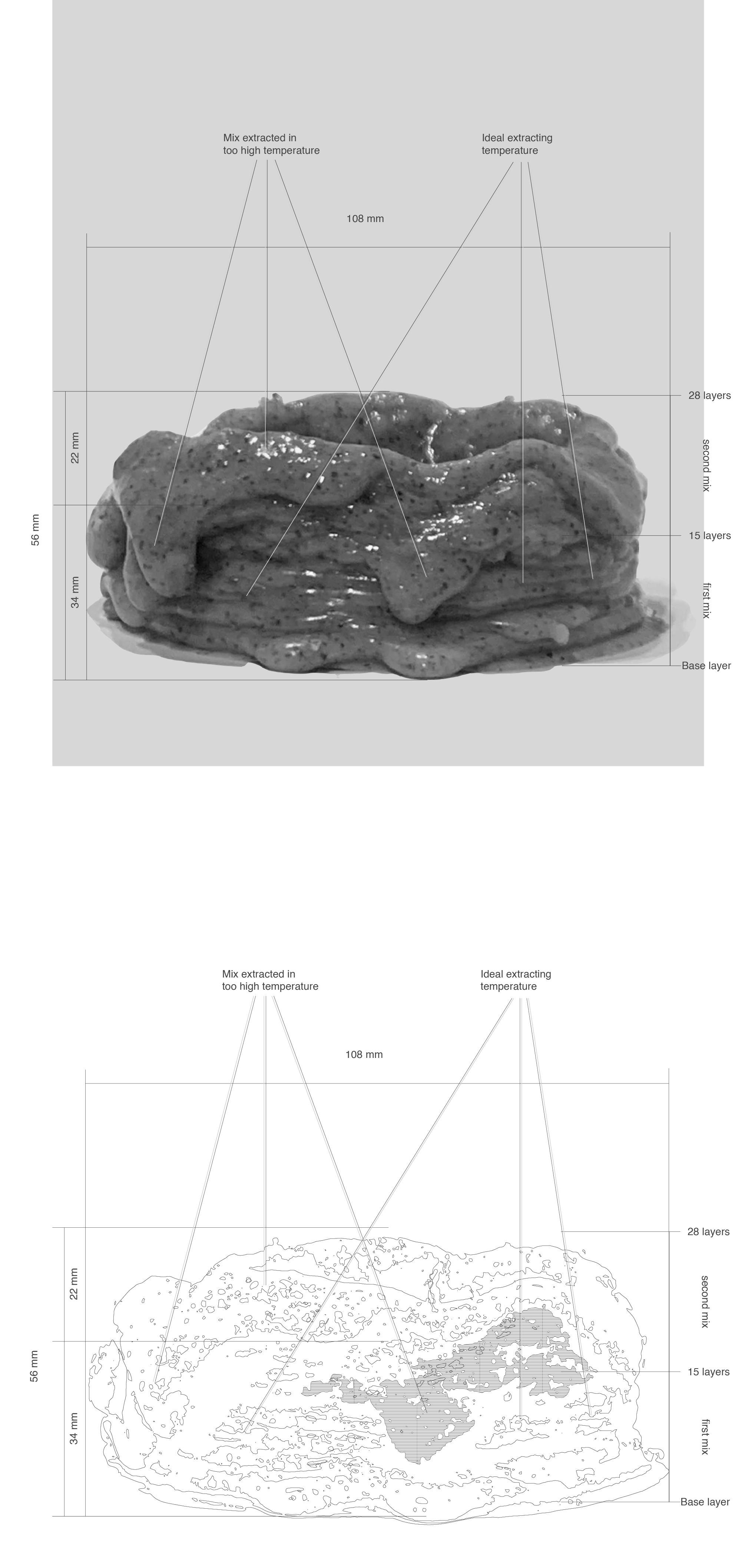

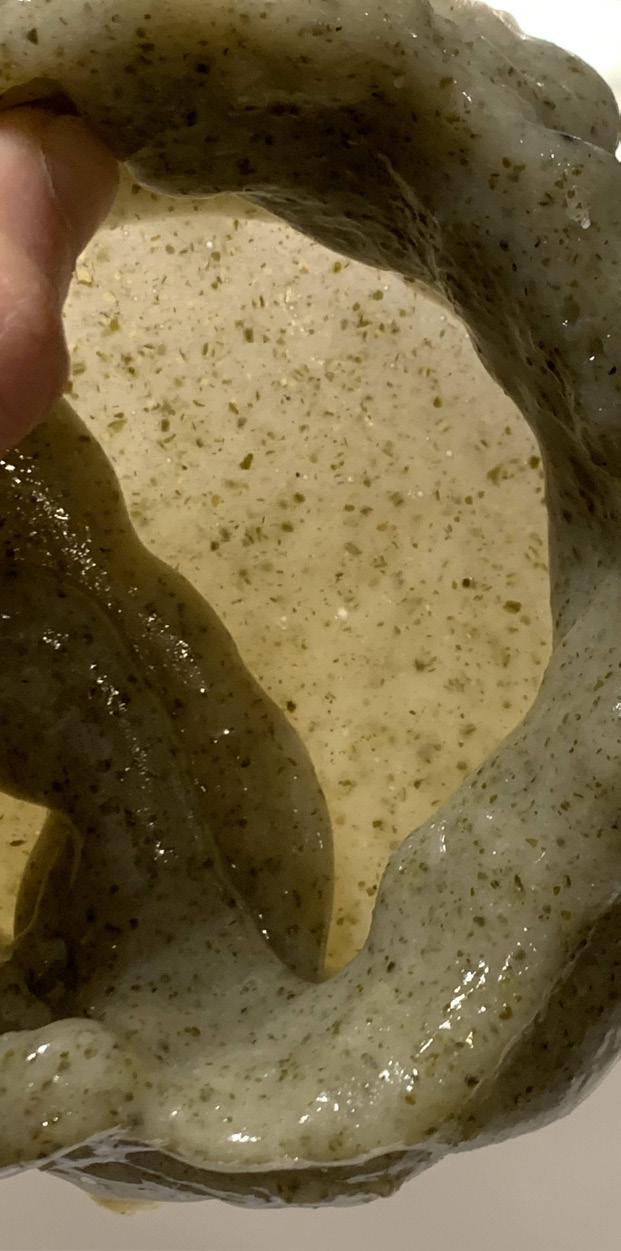

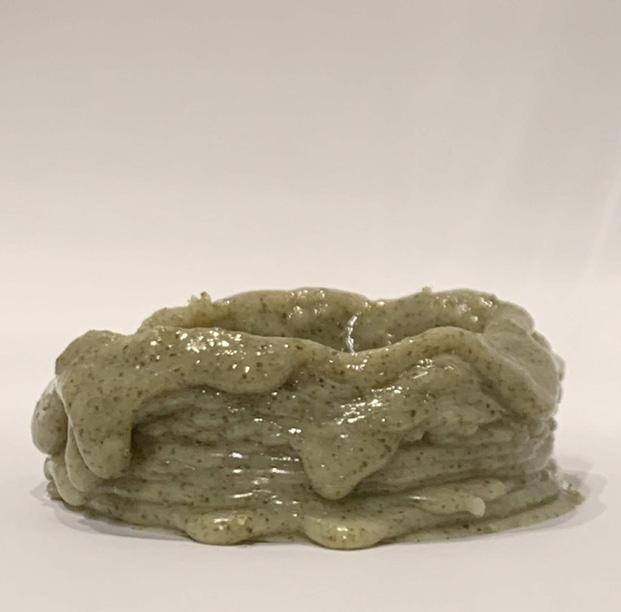
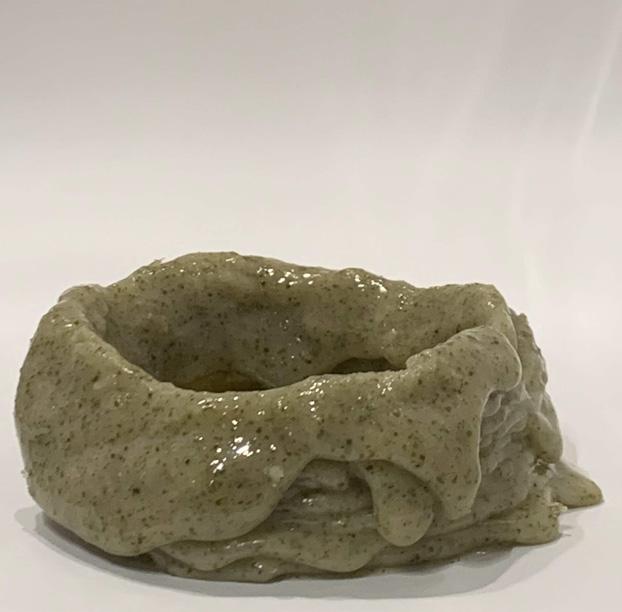
The experiment examines another form of the mix. The last experiment examine strength and translucency (pages 48-49), however, this experiment would examine whether the mix can function as net without break or crack.

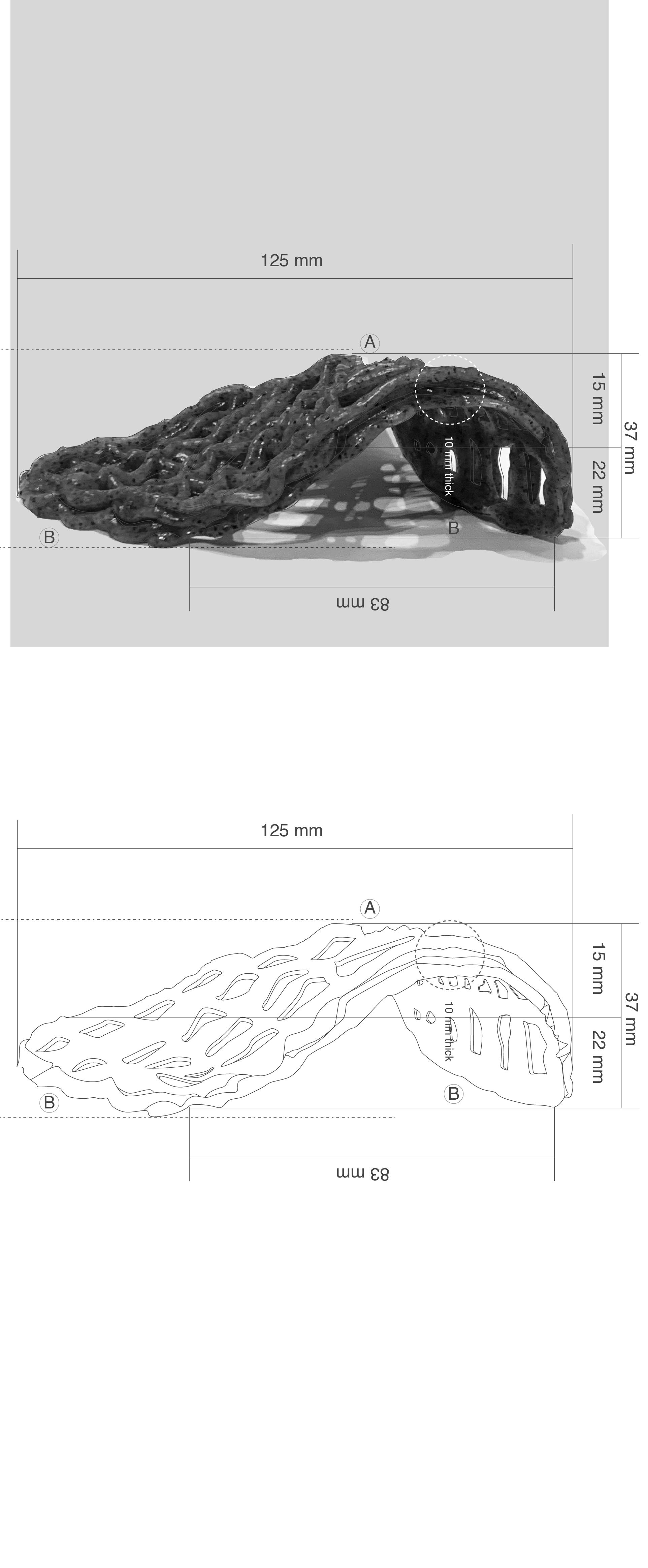
MATERIAL EXPERIMENTSImages50 1-4 Webbed structure experiment 4321
Using layers in crossing directions method, the model created as a grid or webbed structure that potentially reinforce itself and would cover the fact that the model doesn’t have a supporting base layer.
Experiment description
The model is very flexible and is capable of fold itself and also come back to its original shape automatically. The model doesn’t crack from being folded but it is not capable of being stretched so much without tear.

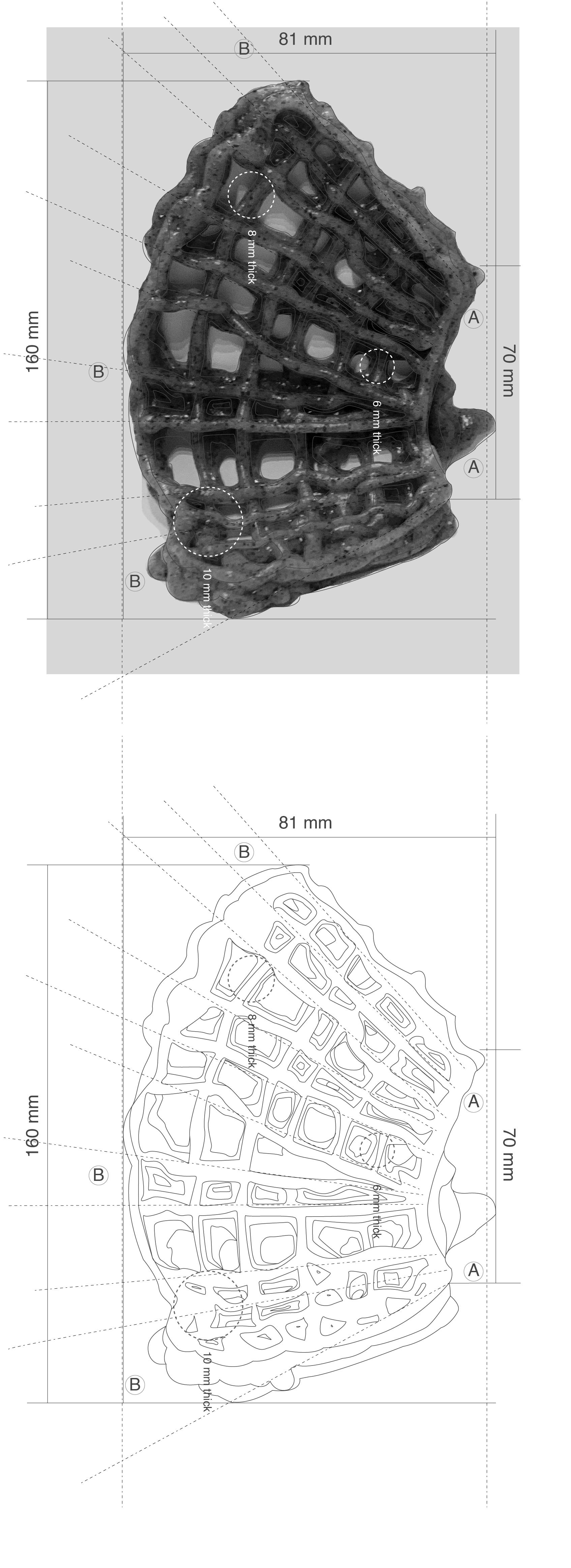
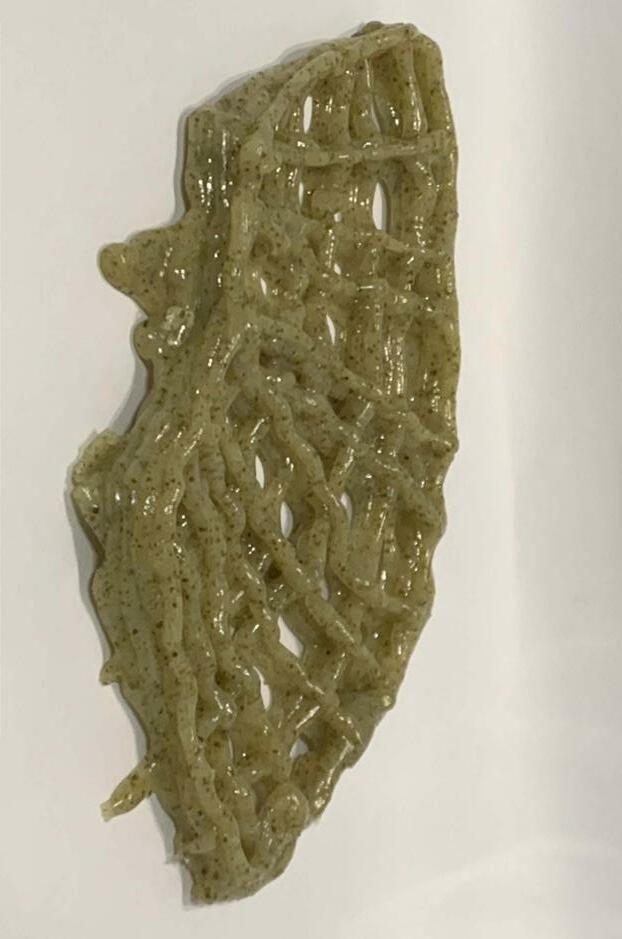
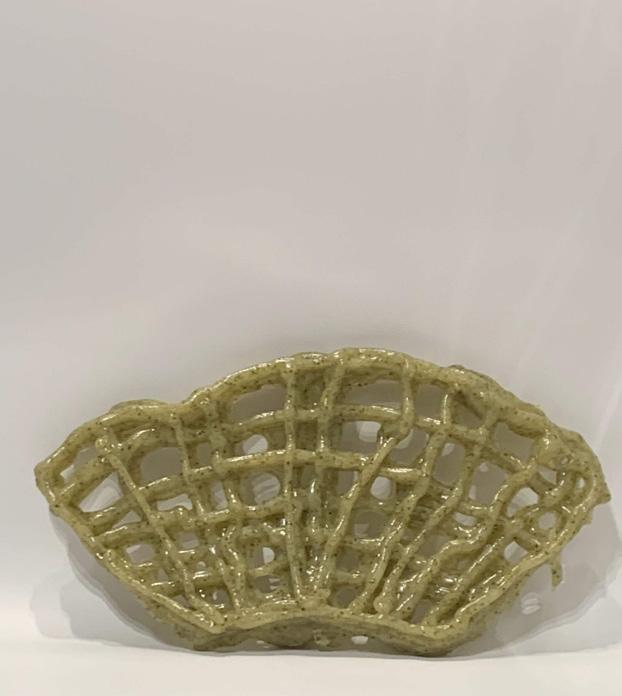
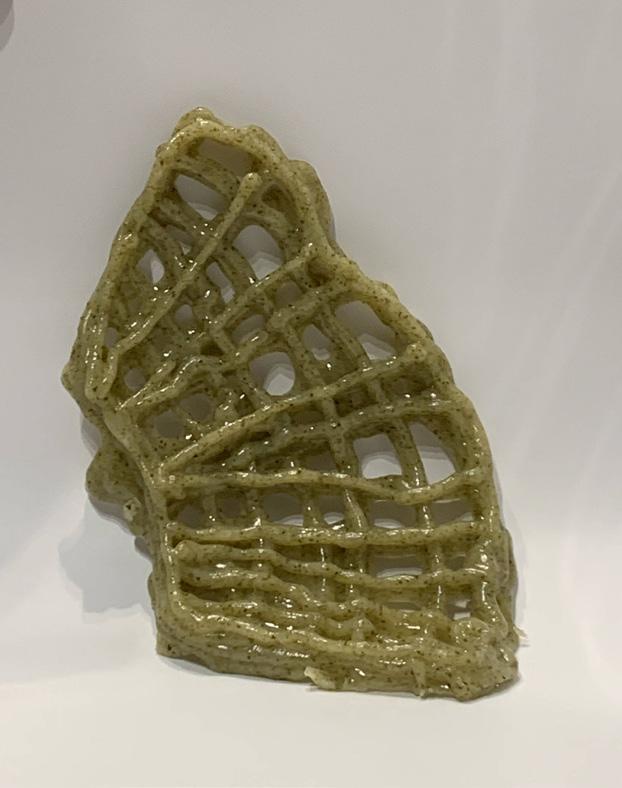
Webbed structure Elasticity 5.2
Experiment results
Elasticity 5.3
52 53 Images 1-5 Combination of two methods 54321 This UsingdescriptionExperimenttransparentveryalmostverythicknesses,densitiespartssyringe.ofandtogethertwocombinationexaminesexperimentaofmethods–castingextractionmaterialusingThecastevariedinandfromthickandsolidpartstothinandalmostparts.mouldand
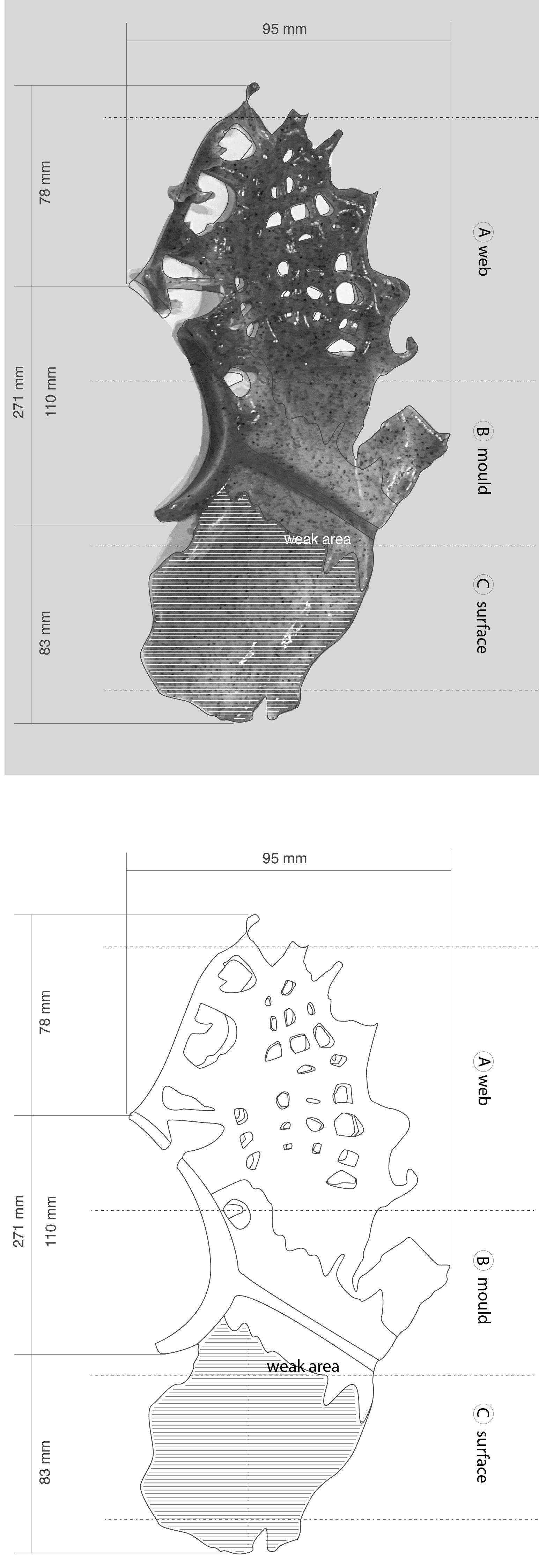

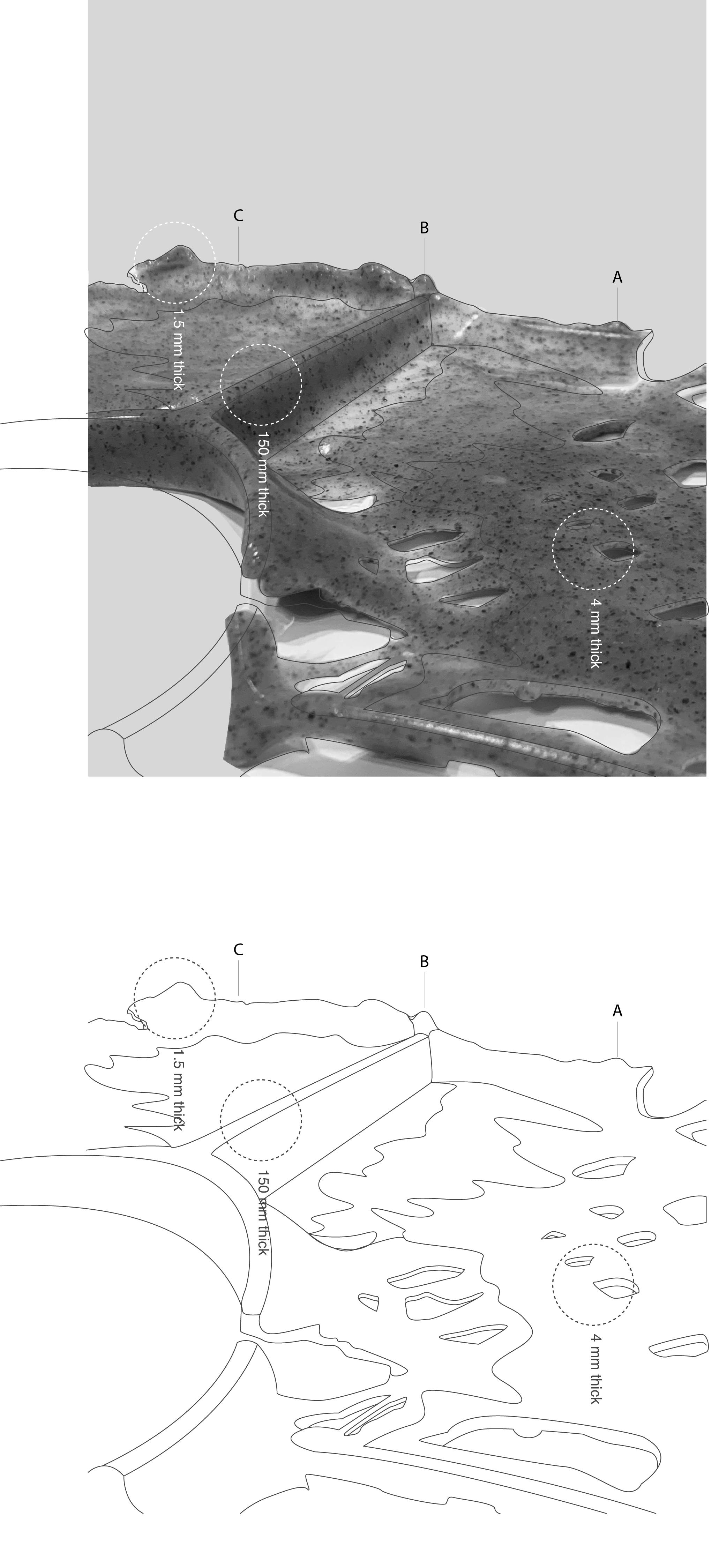
Casted joint, Webbed structure model
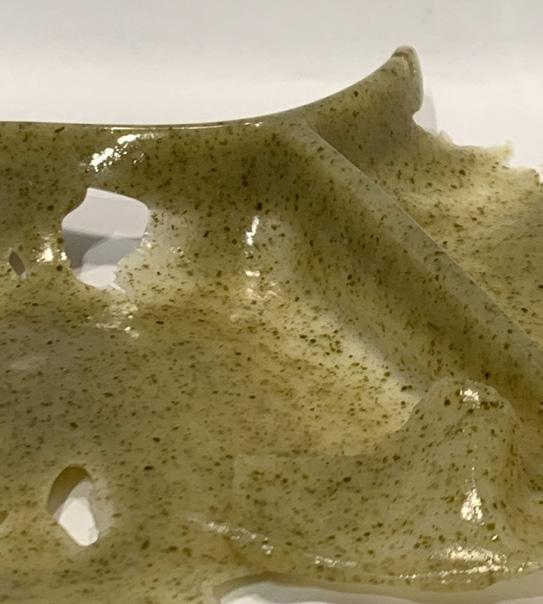
syringe – first, the mix poured into the mould then, before cures and when the mix is still hot, the webbed part has been samefewopportunitiesform,astheTheExperimentmodelled.resultstwopartsofmodeldriedonecontinuousopeningofusingtechniquesinthemodel.


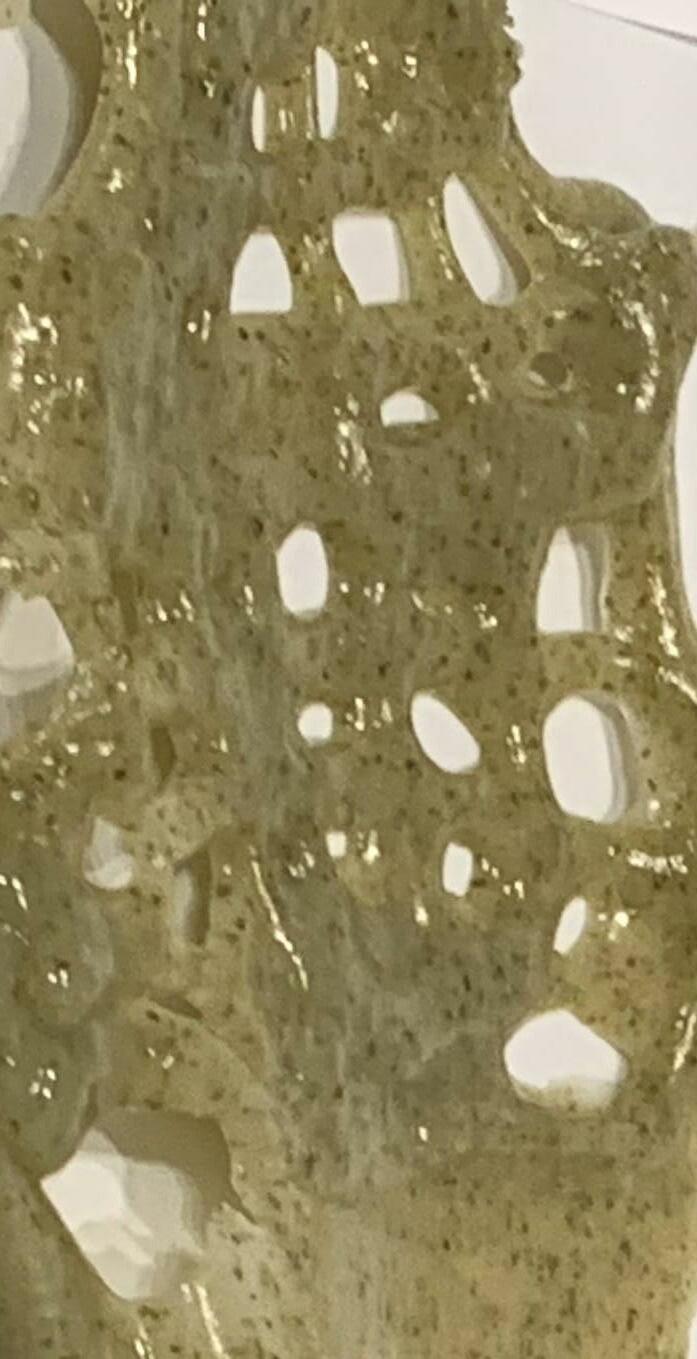
Skin-like

MATERIAL EXPERIMENTS54
As seen in images (1-5), the base layer eventually became a buffer between two parts of the model – like a partition that has openings. The model could carry its own weight also in a perpendicular direction and be strong also when pressed (see movie by scanning the QR code). However, when distorted it does not come back to it’s original shape.


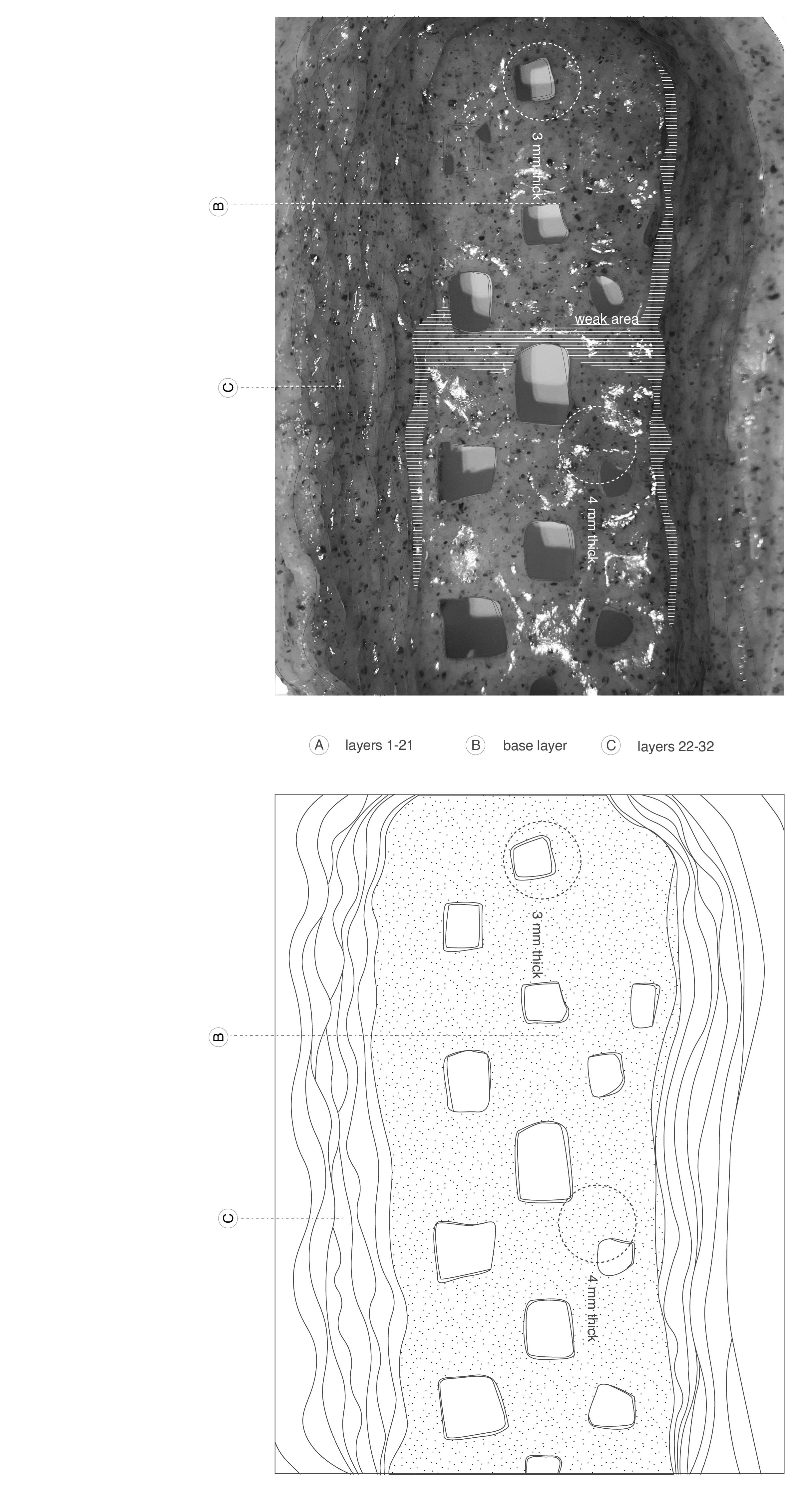
This experiment examines technique of layers in different way to achieve more height and strength.
Experimentside. results
First, base layer has been modelled using syringe, then –“walls” has modelled one on top of each other – as described in the experiment on pages 48-49. The innovation was flipping the model upside down when dries and continuing build on top of the base layer from the other

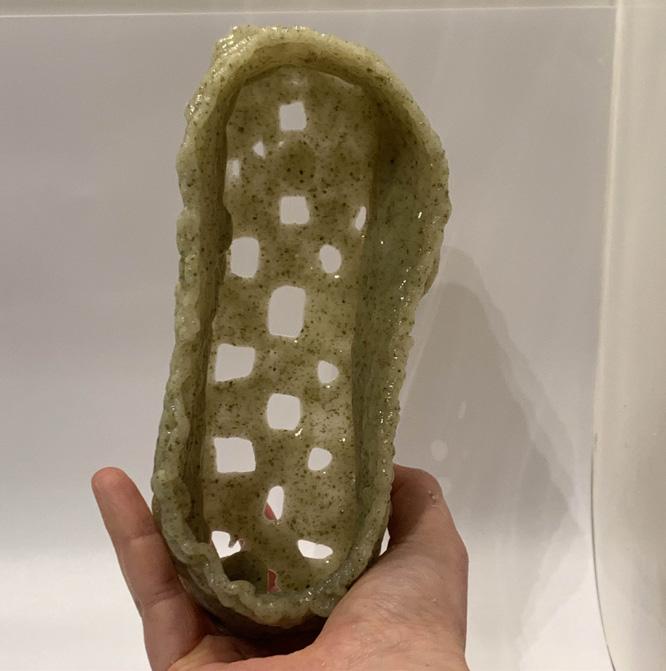

Experiment description
Layering
Achieving height by creating
“levels” 5.4
Images 1-5 Base layer forming the model
54321 Strength

Joints experiment - Seaweed compound and Metal components
This experiment tries to connect metal tubes using the shrinkage of the material.
“Bio joints” in nature: A closer observation on a webbed structure of the duck’s leg has shown one material that changes resolution correlating to function. There are no parts in this structure.
5.5
Bio Cartilagejointsin human body and webbed structure in duck’s legs
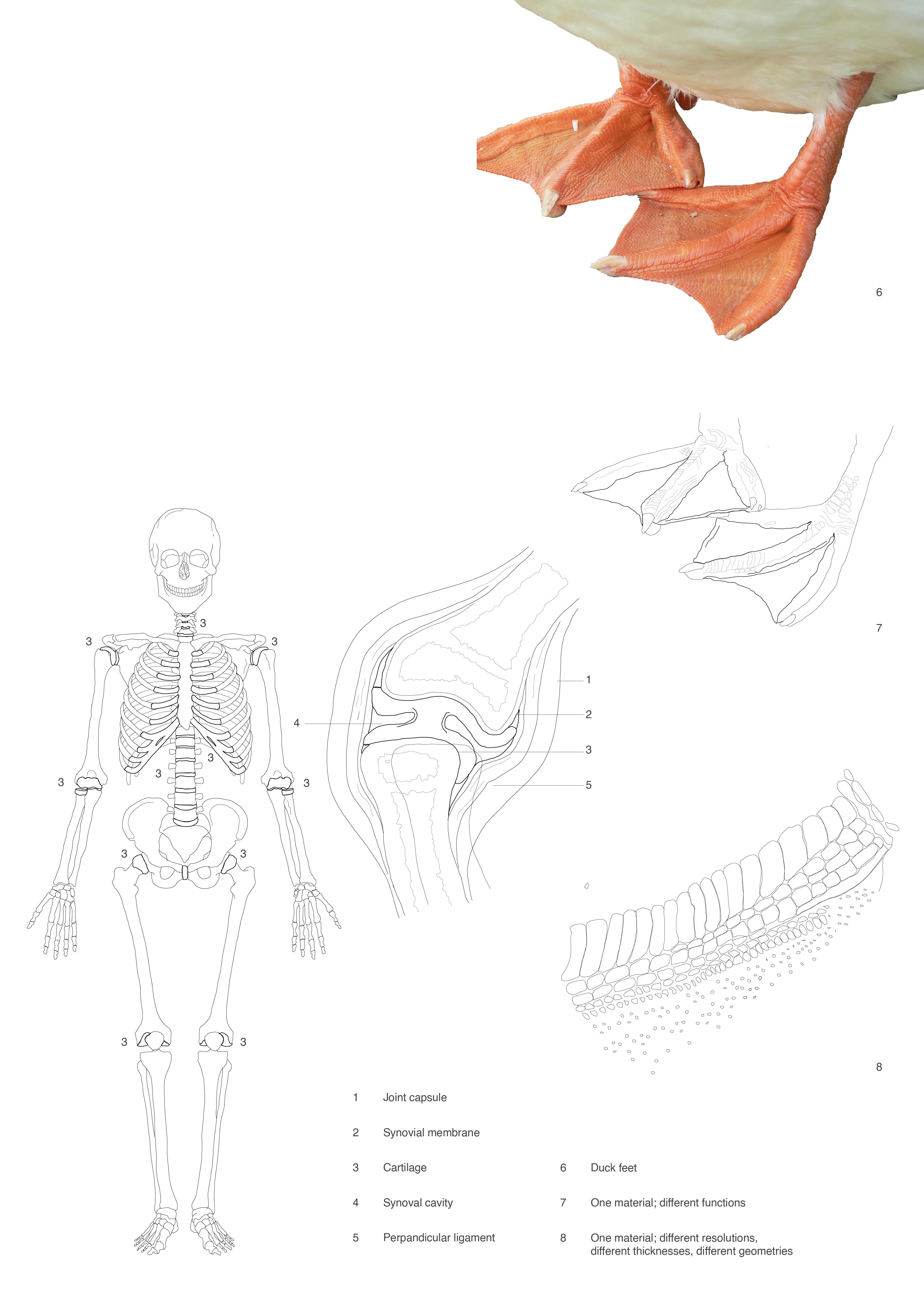
The seaweed material is flexible and is capable of absorbing Learningmovements.and researching new joint mechanisms to examine how to harness these properties to the design process.
Movements joints in concrete allow the building components to expand. Movements and changes in a building usually happen due to temperature changes and moisture variation. As the joint effectively shrinks, its role is to accommodate movement. They are intended to prevent potentially damaging forces accumulating within the concrete slab itself, or surrounding structures.
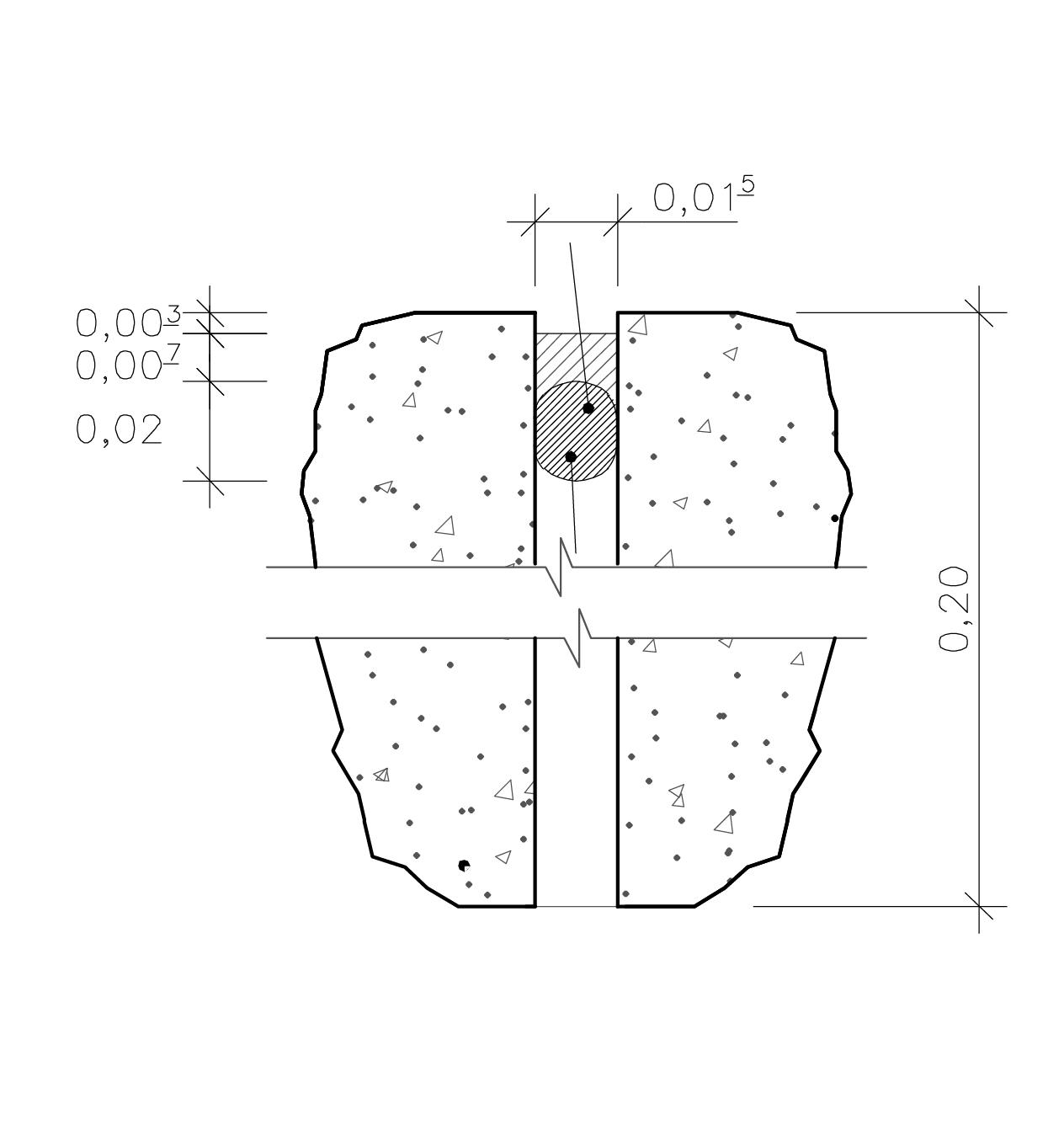


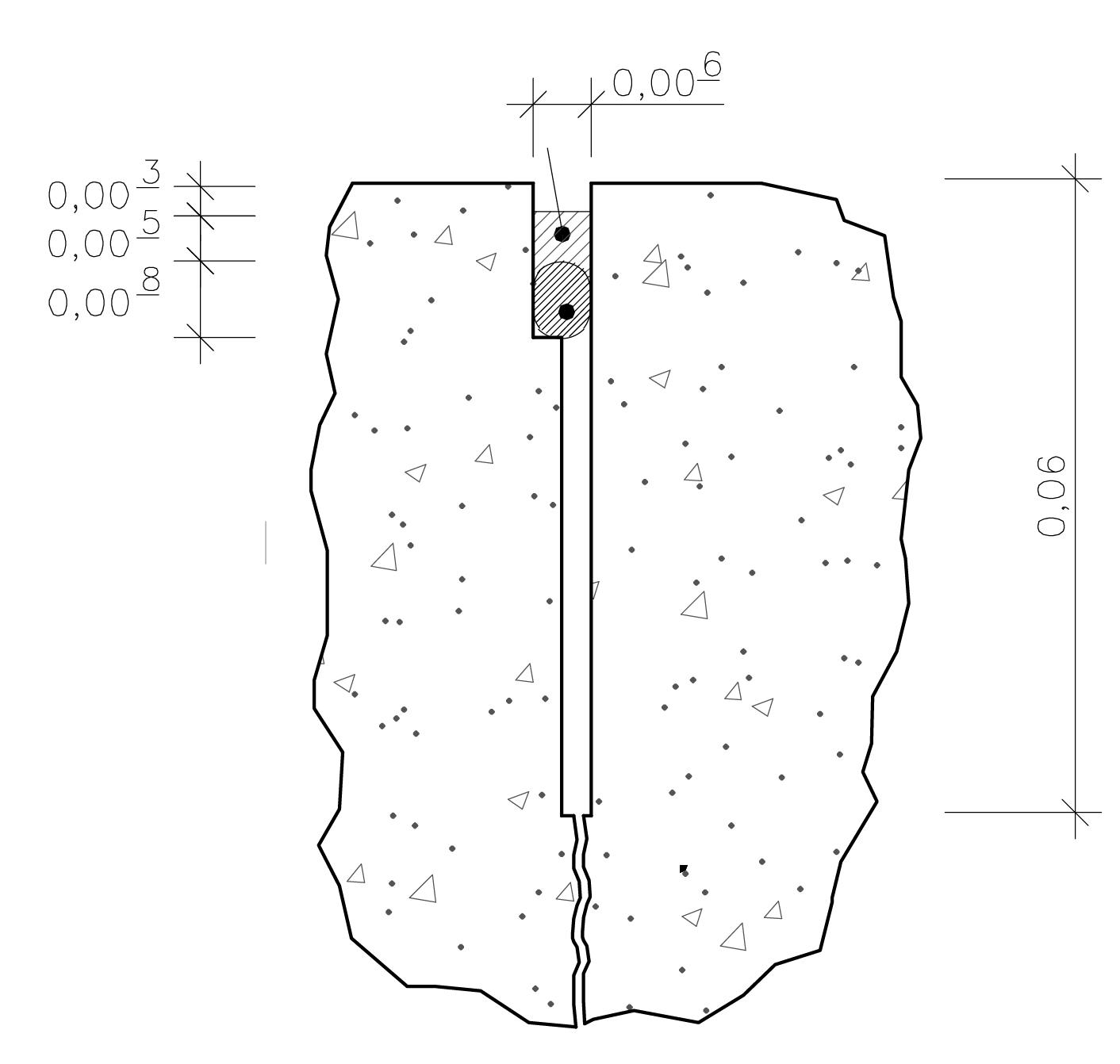
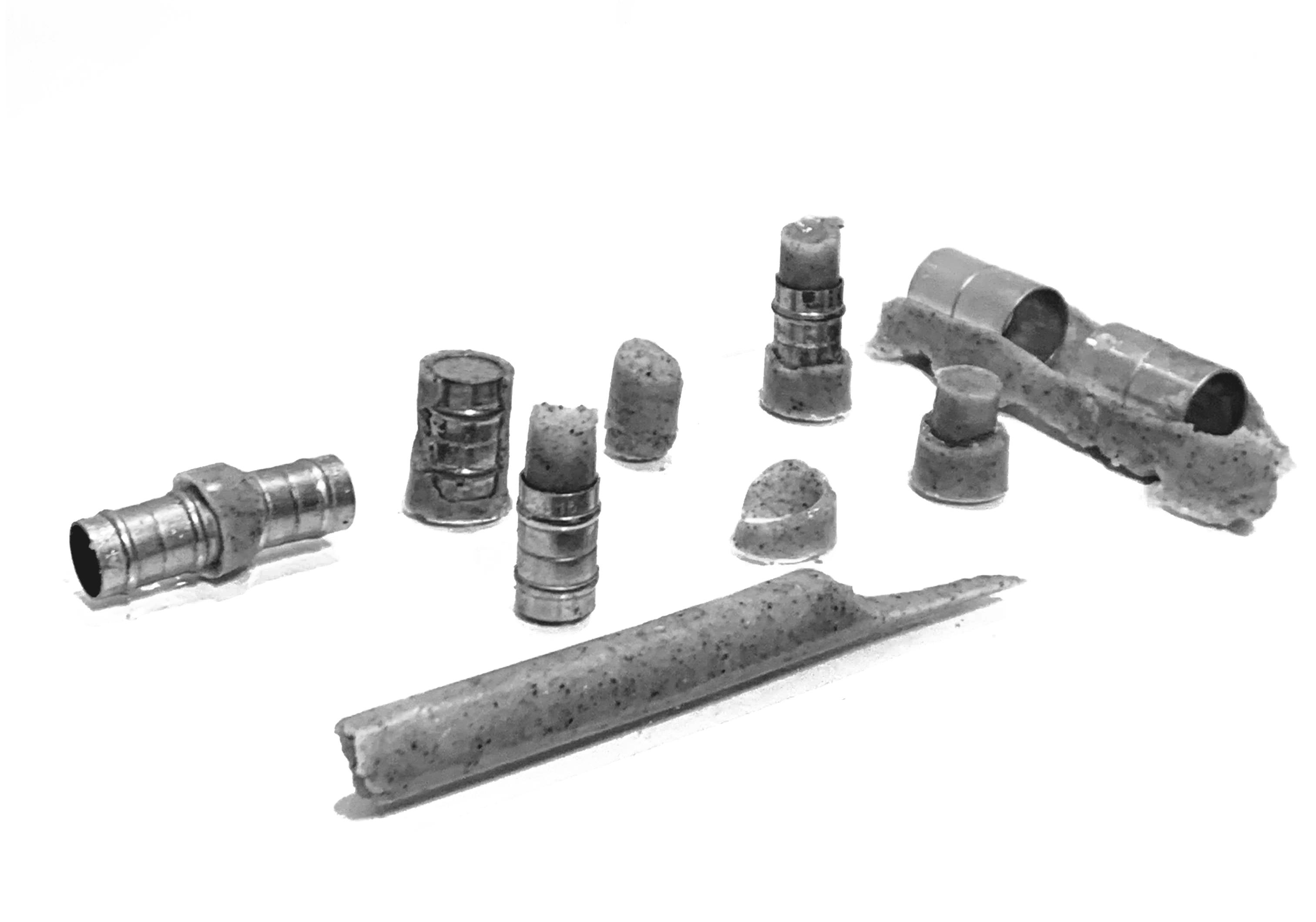
56 57
It is one continuous and intelligent system. Cartilage in the human body covers the ends of bones to create a low-friction environment and cushion at the joint surface. The cartilage effectively allows fluid bending and straightening motions and protects the joint against weight-bearing stresses.
Movement joints in construction - Concrete expansion joints
Learning Joints
Experiment description
In the second round (about 25 minutes later), the mix was already cooler and could be controlled better. This time, the robot set up to automatic printing (constant speed, no changes). This way, the robot didn’t stop the material extracted at a constant pace, and the printing was much more successful. No air pressure has been used, only gravity
(*Conclusionsforces.on the next page)
The experiment has been done twice. In the first round, the beginning of the printing was successful – the layers piled up very well and cured at a good pace. The initial speed was too slow, and too much material was extracted and expanded. After speeding up the printing pace, the nozzle was already too high, and the material started to splash around. No air pressure has been used.
58 59 3D printingRobotic
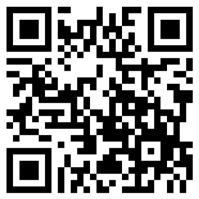
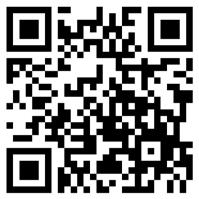
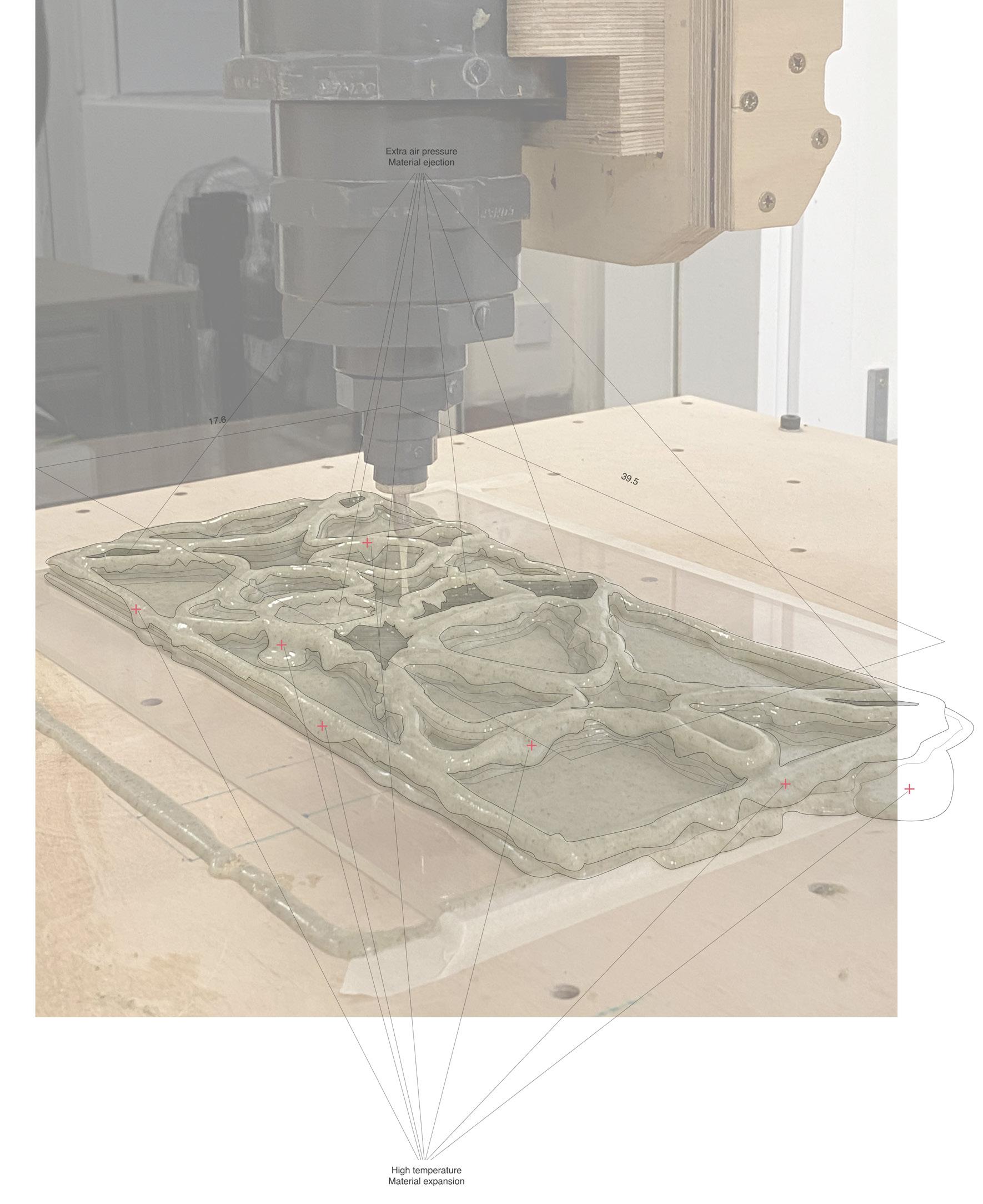
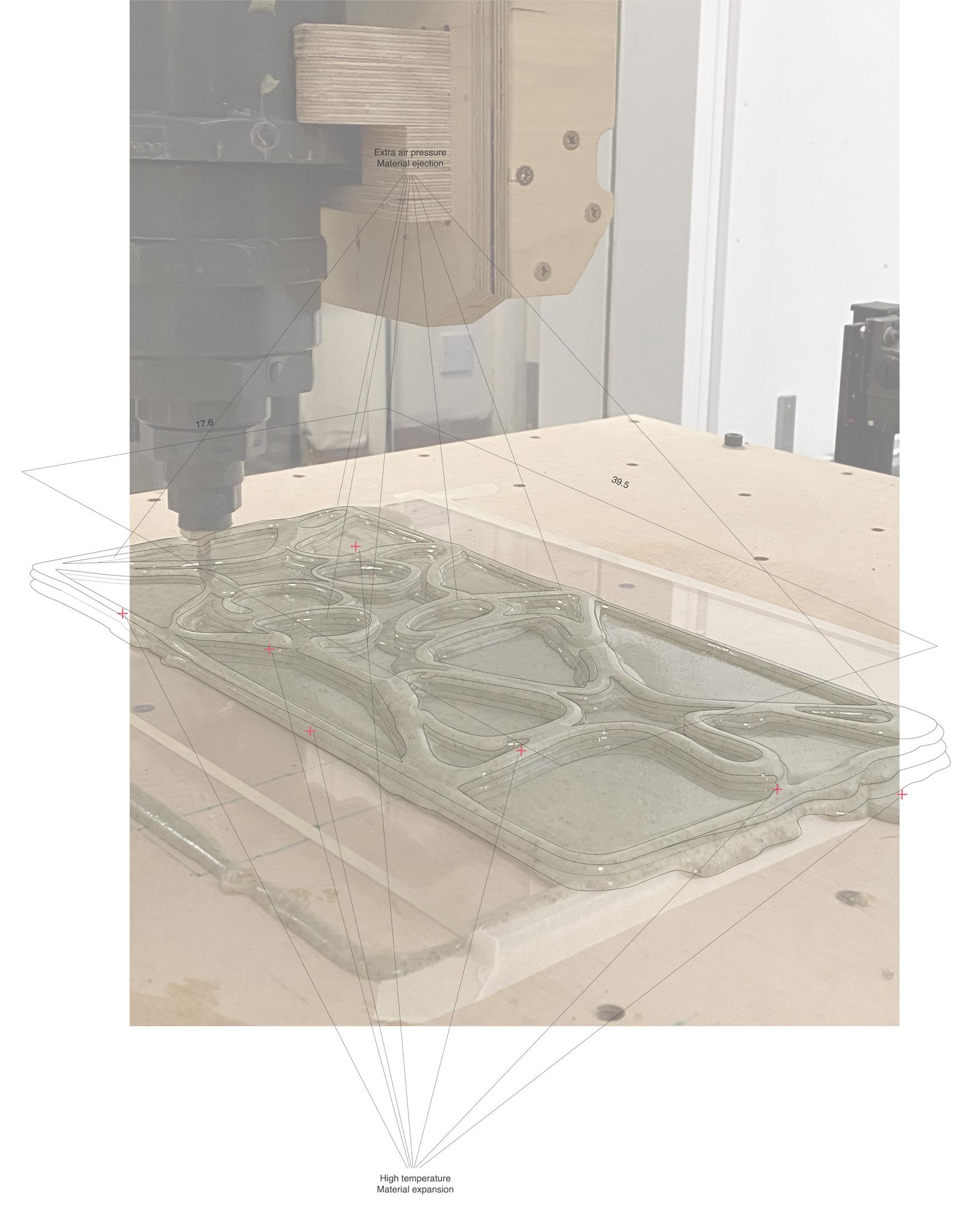
Strength 5.6
Shape and code
As shown in the last experiments with the new material, the possibilities now are much larger. After examining the possibilities of the new compound, it is time to go back to the lab. The mix has to be made in the lab. Otherwise, the material cures before printing. The aim of the experiment was to stretch the boundaries of the material and try to scale up from previous prototypes.
The intention of the shape is to print in the horizontal dimension and, after printing, try to flip the model 90 degrees to examine its inner tension strength. For that reason, the shape of the model is composed of tangent shapes, triangular with rounded corners to achieve a strong structure. The code generated from Grasshopper assembled from 25 layers when the shape gets smaller and smaller as the robot goes up. Each layer is 2.5 mm in height, but it is expected that the model would be lower due to the heat that would cause expansion of the material.
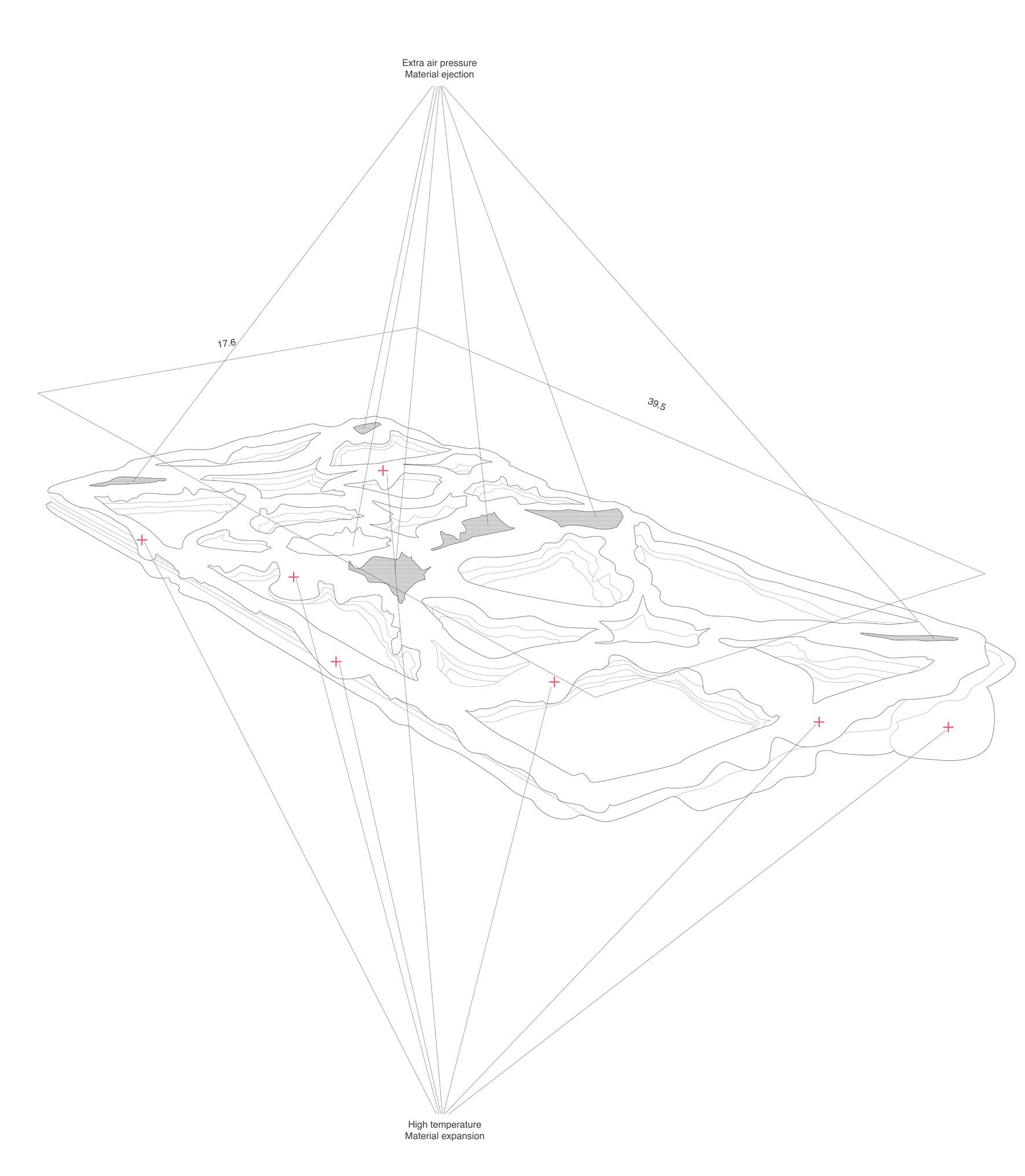
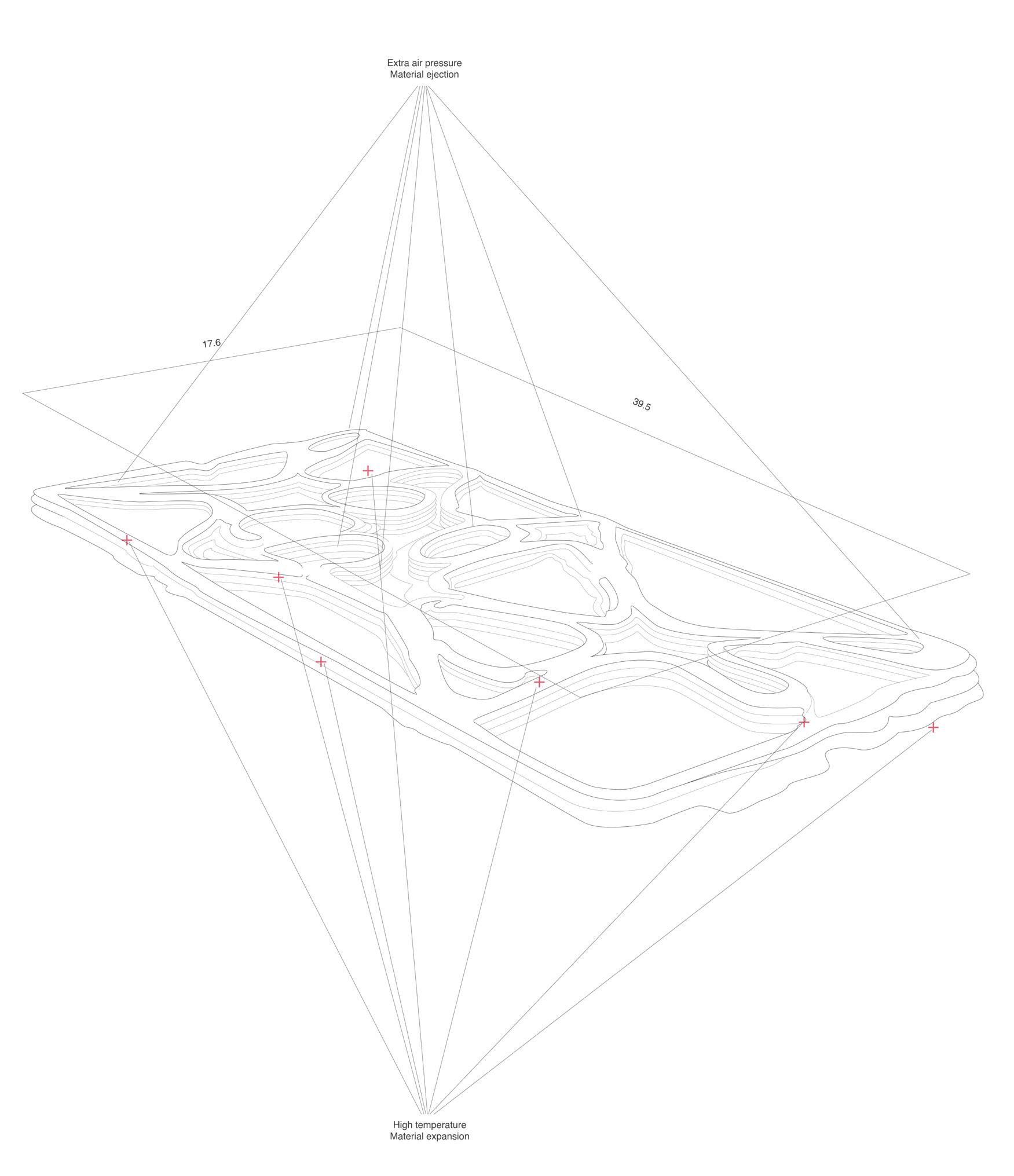
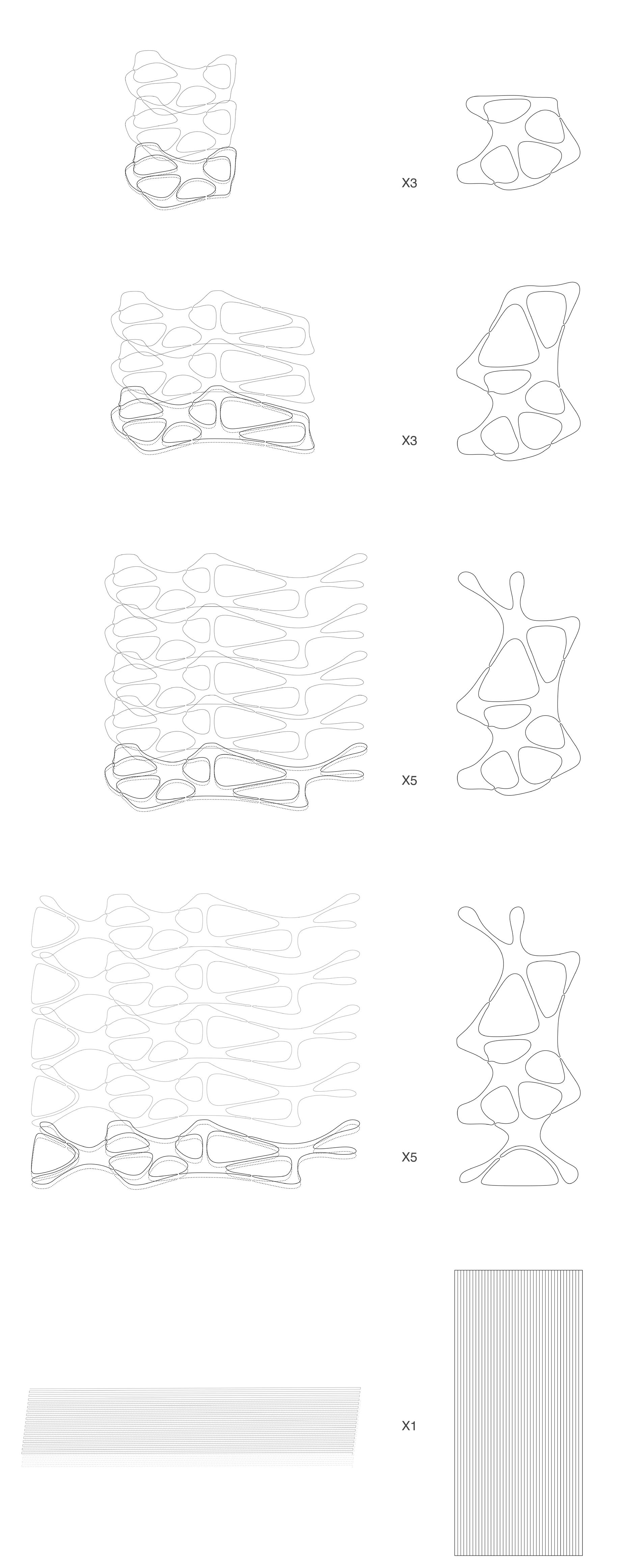
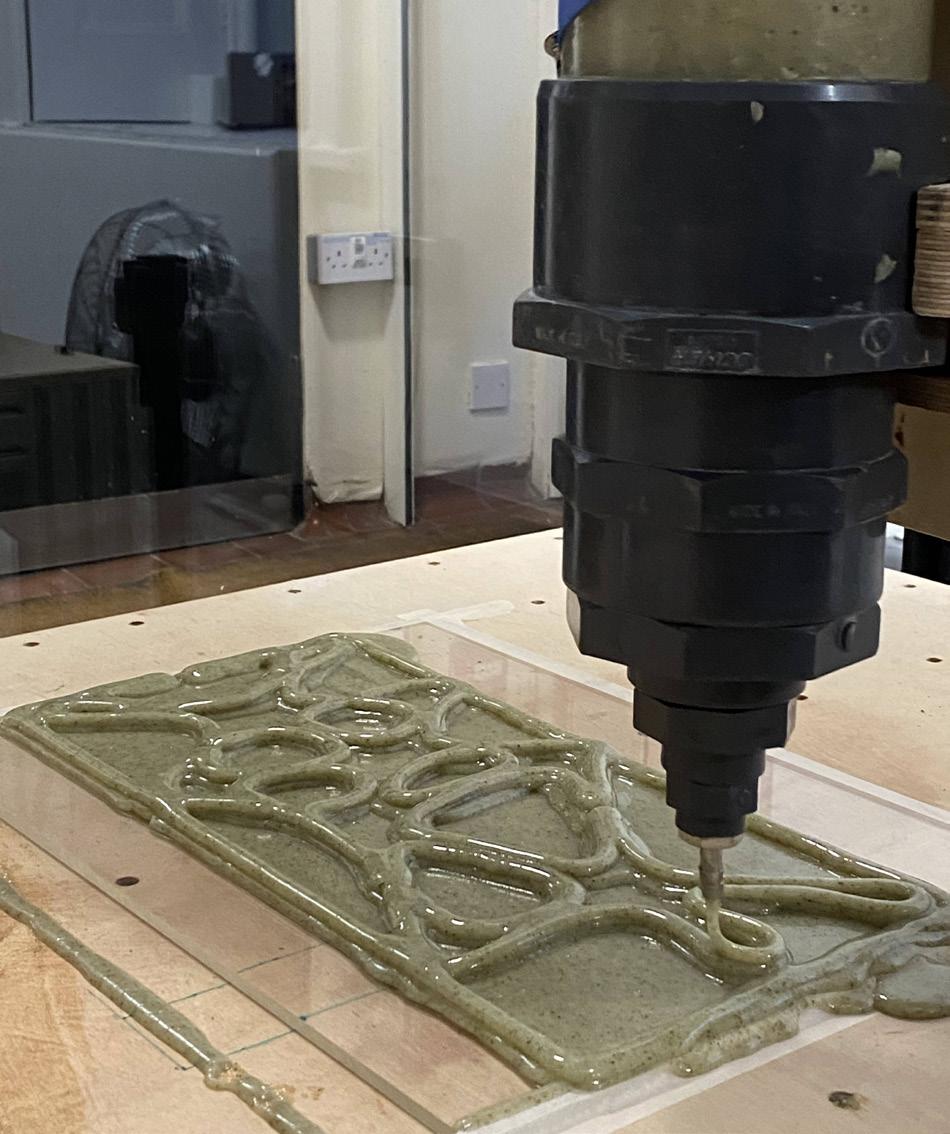
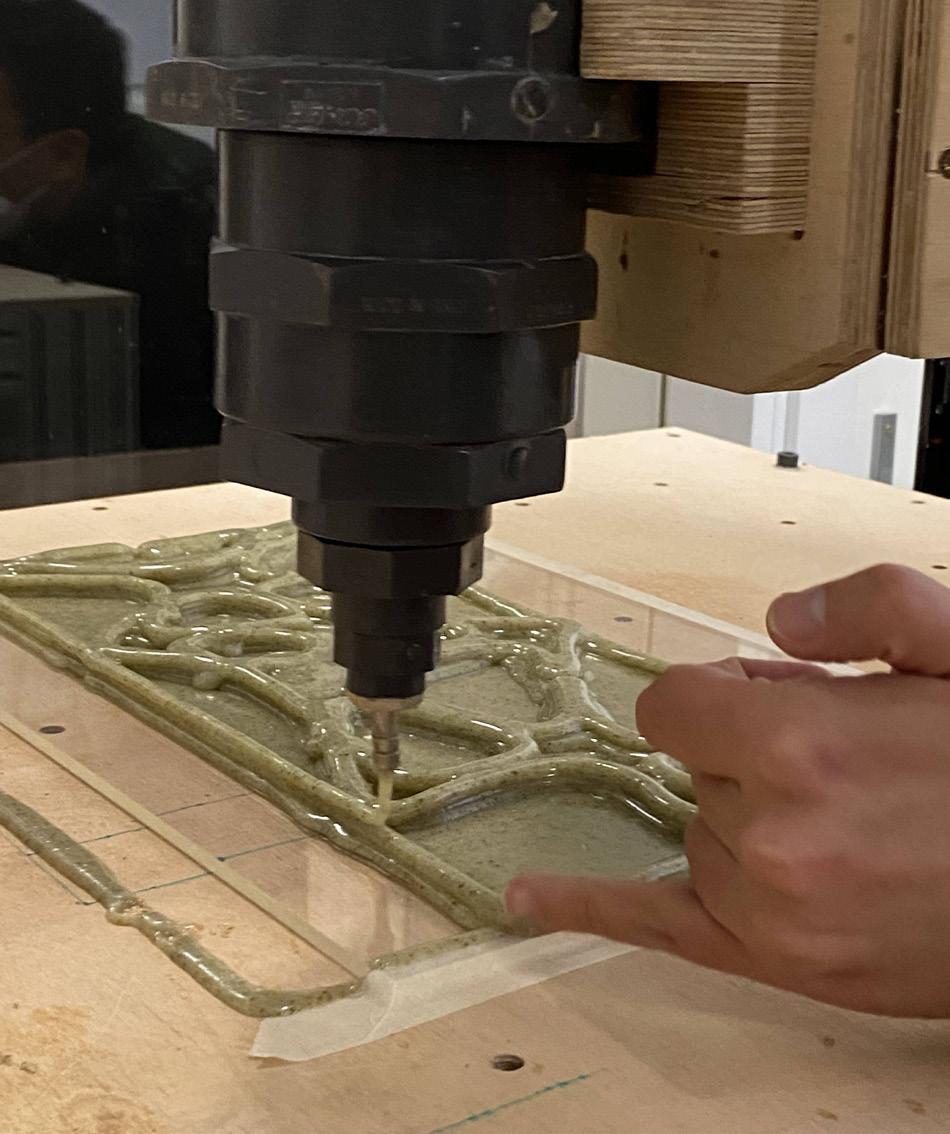

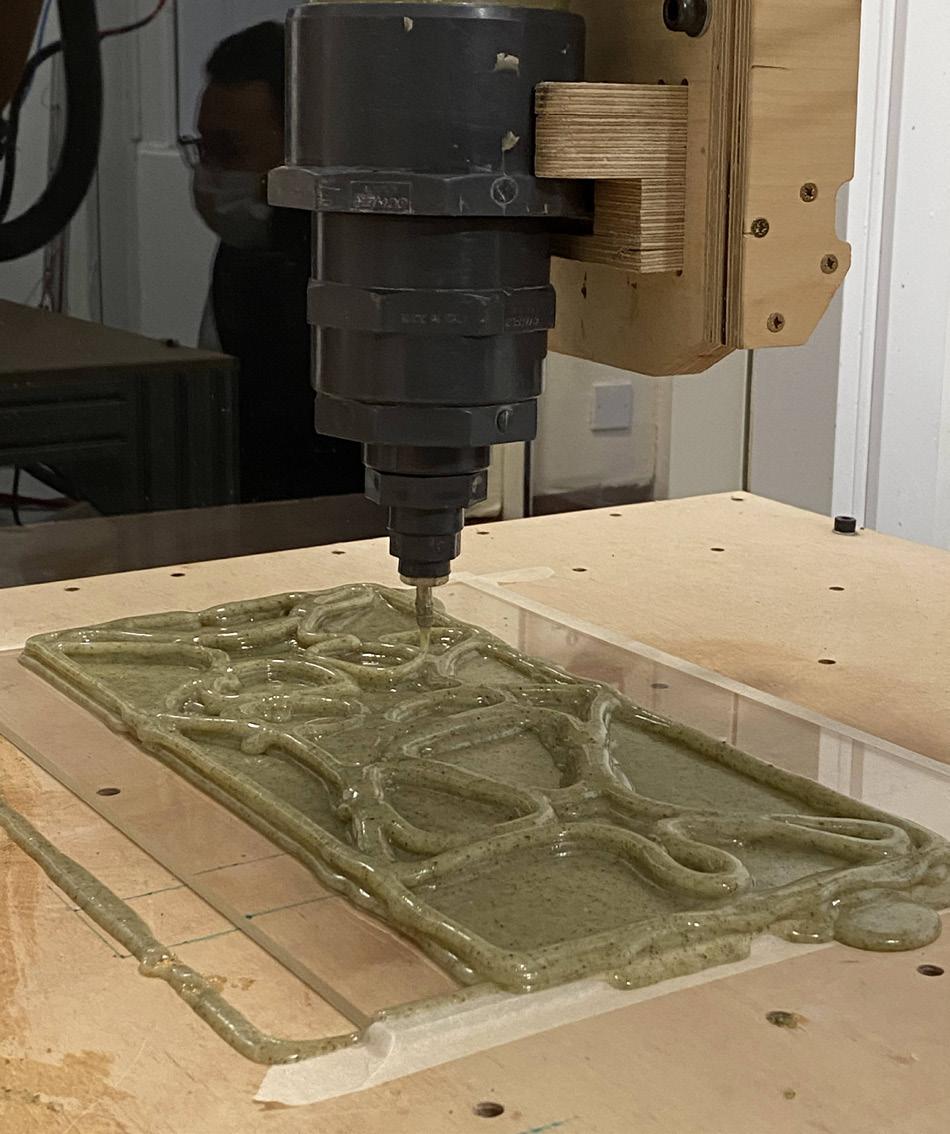
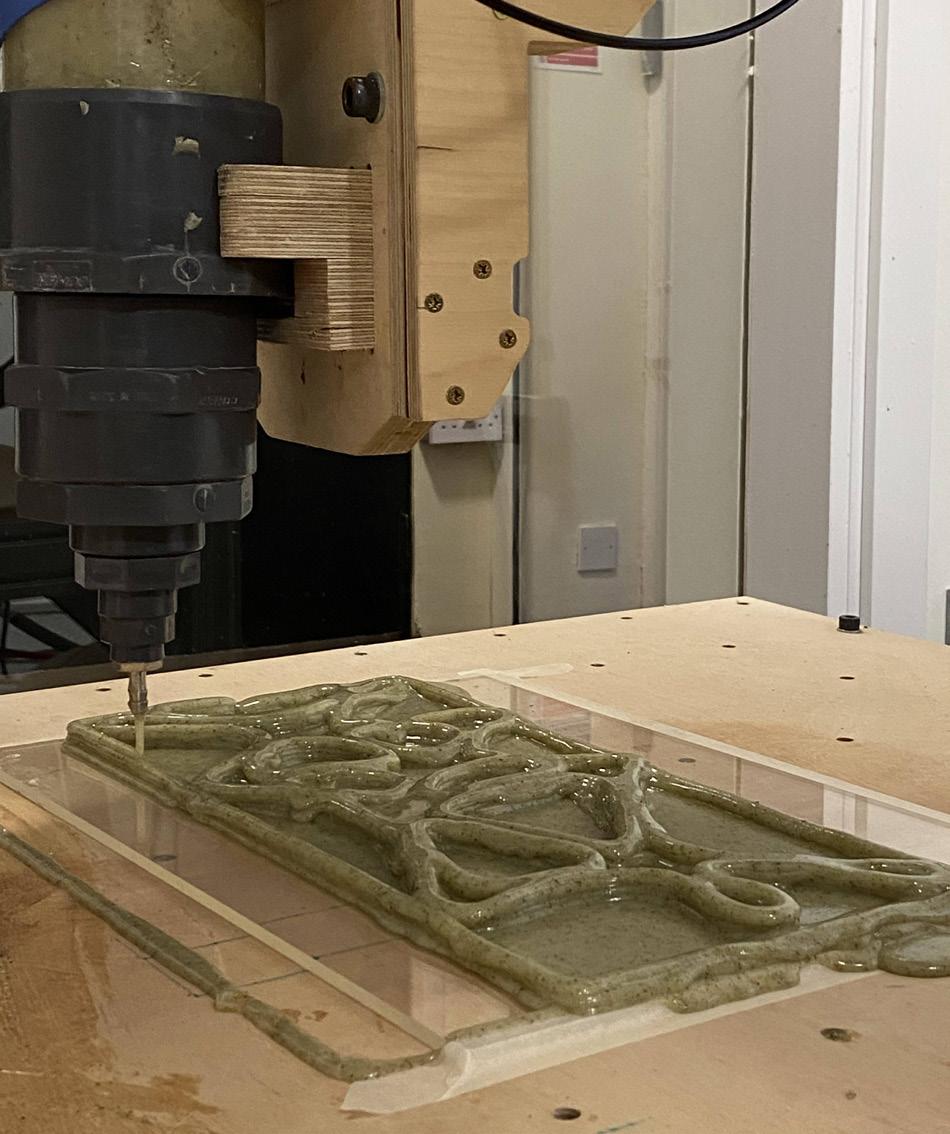
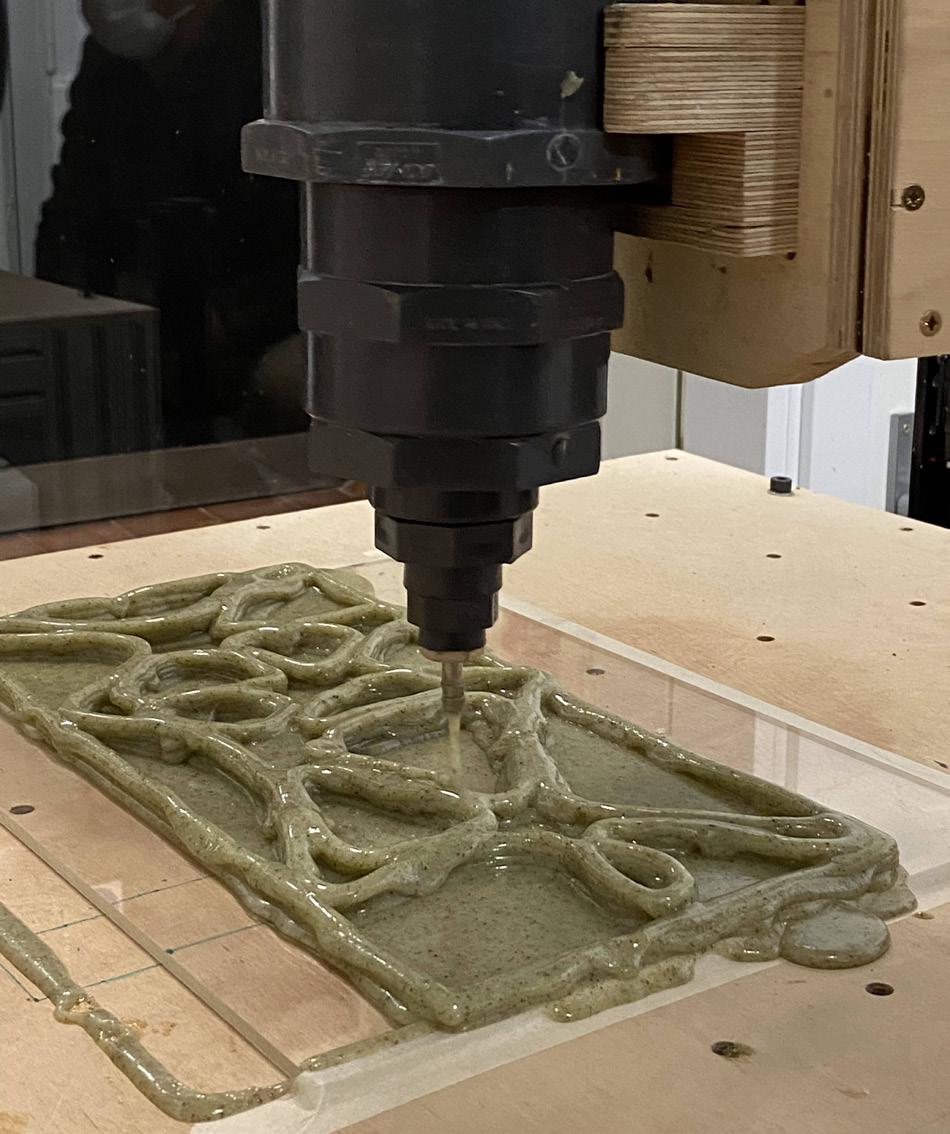
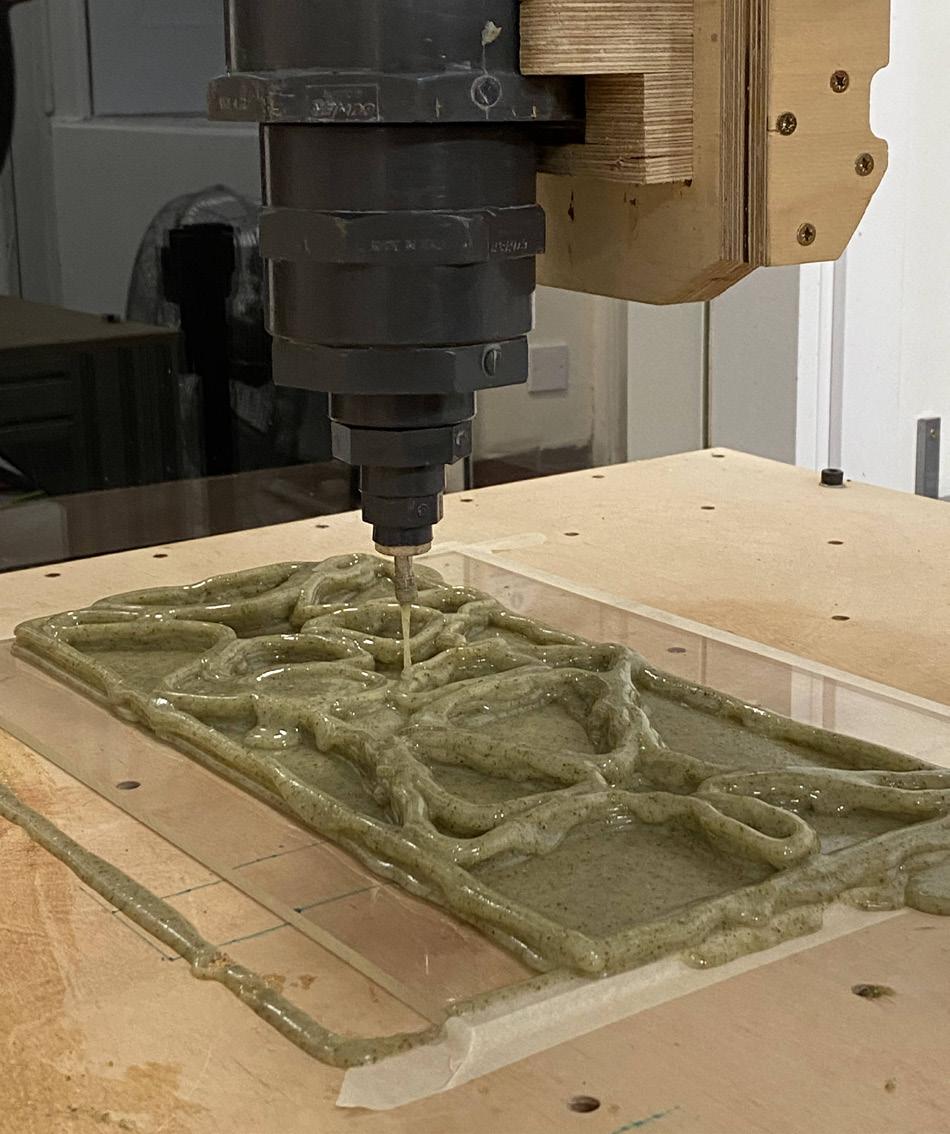
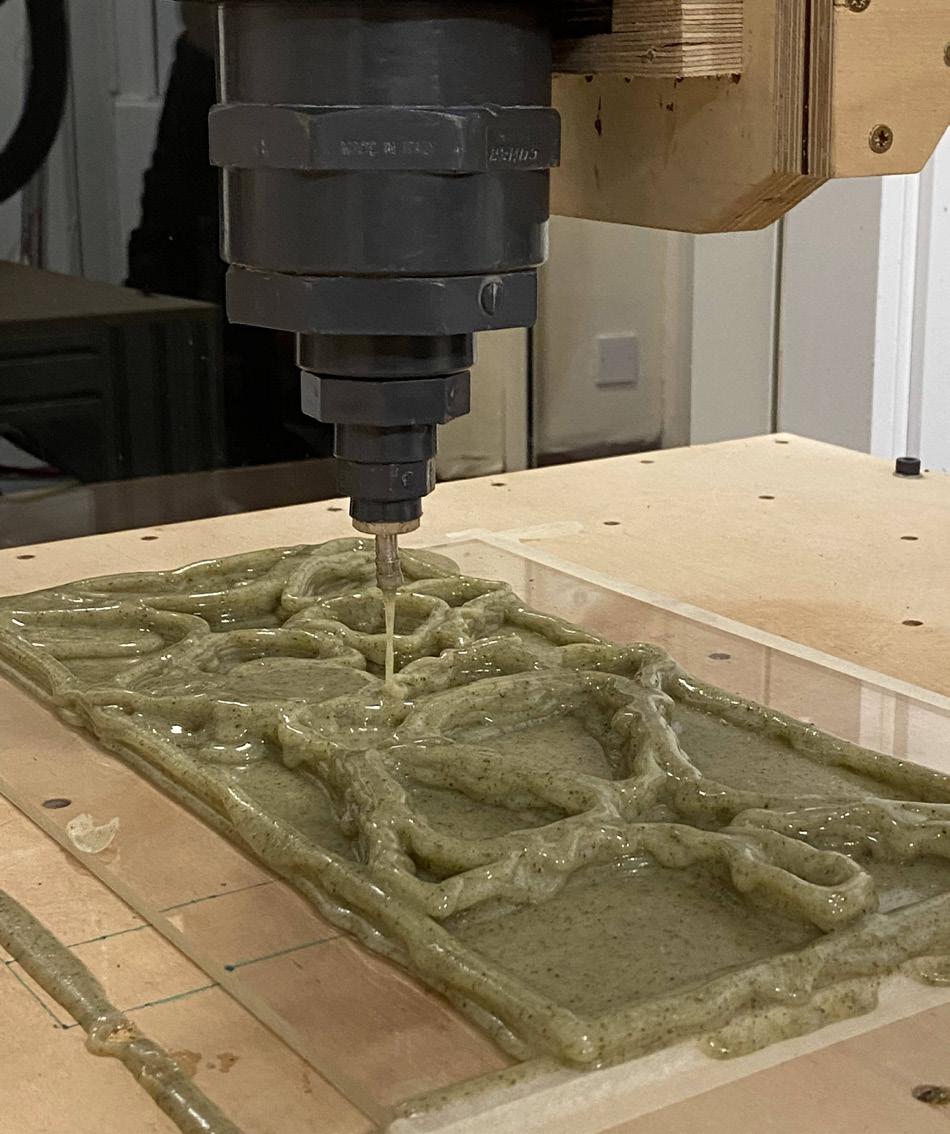
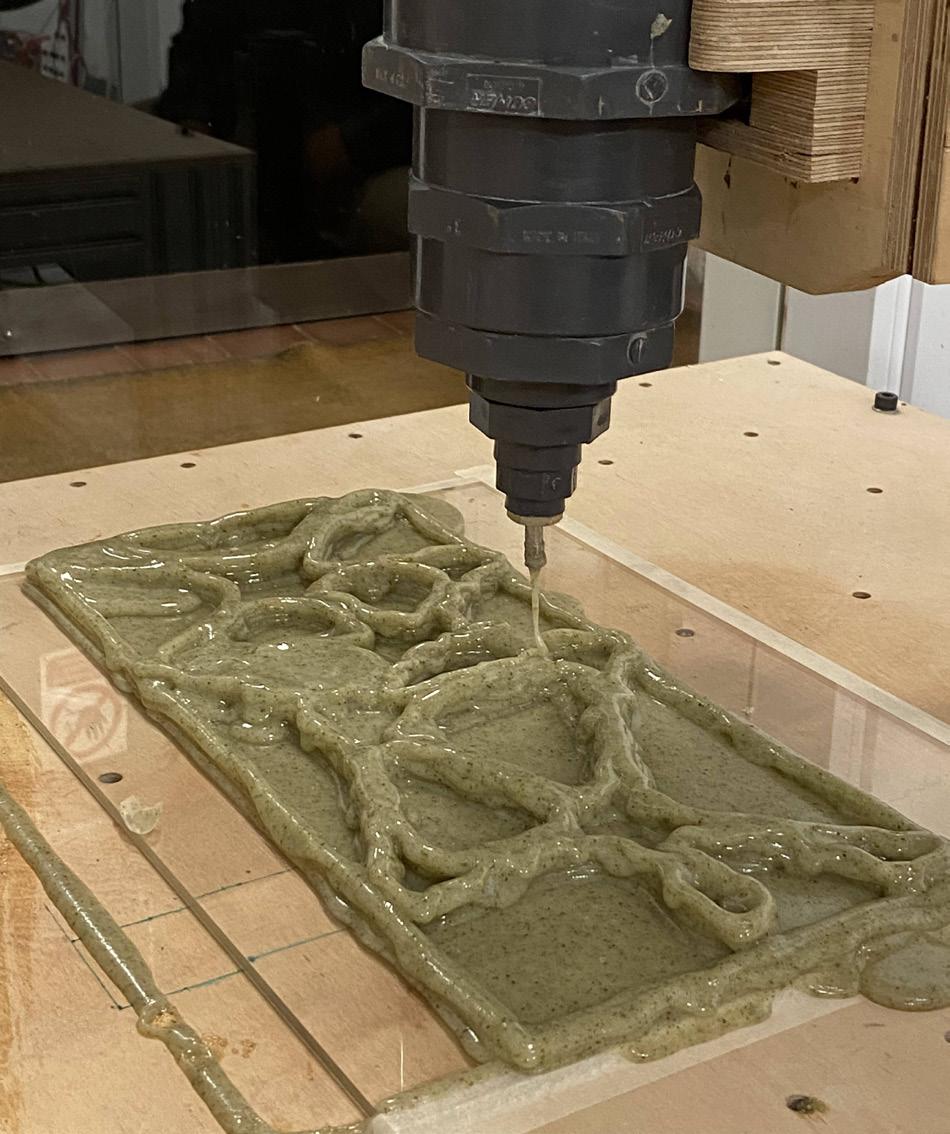
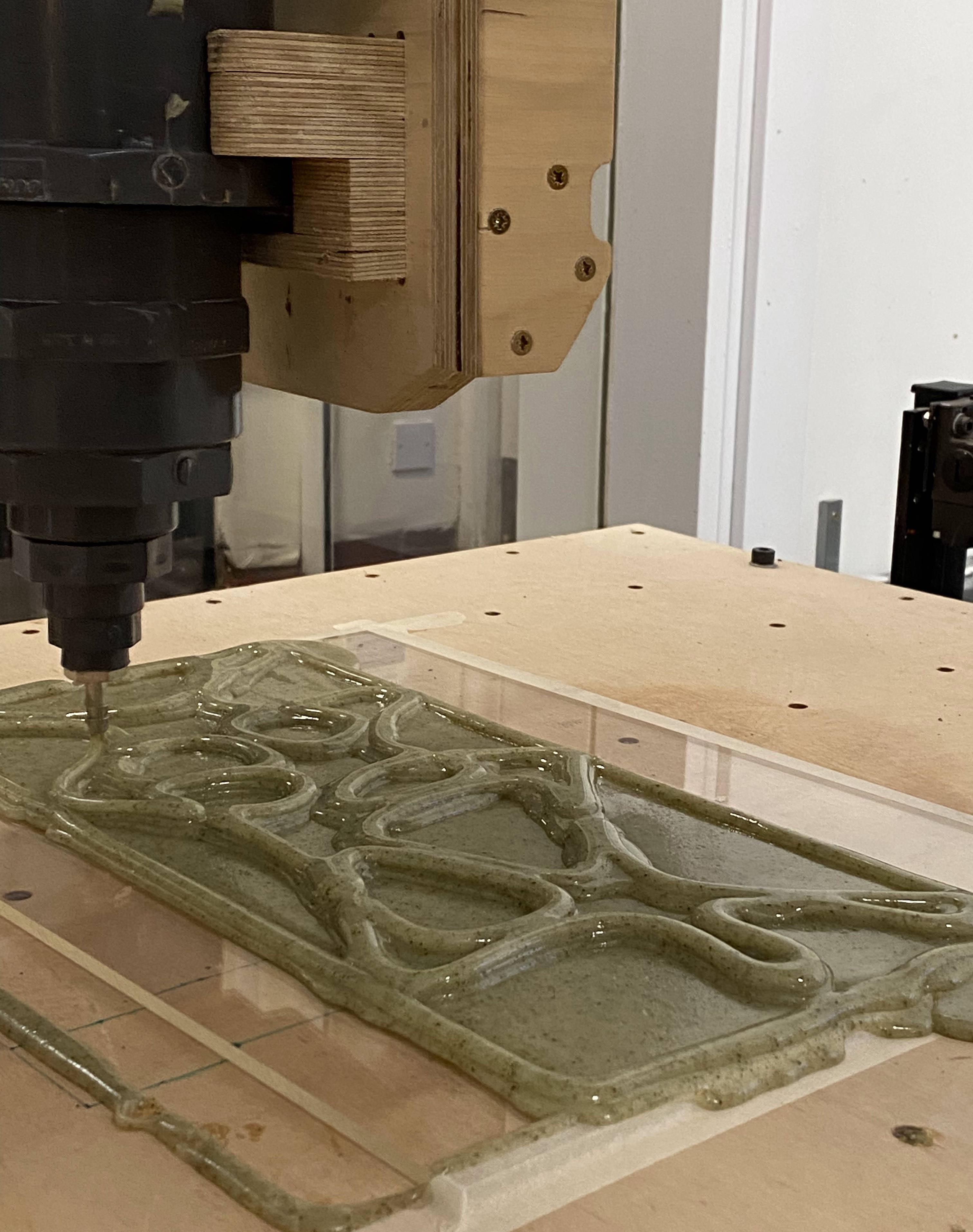
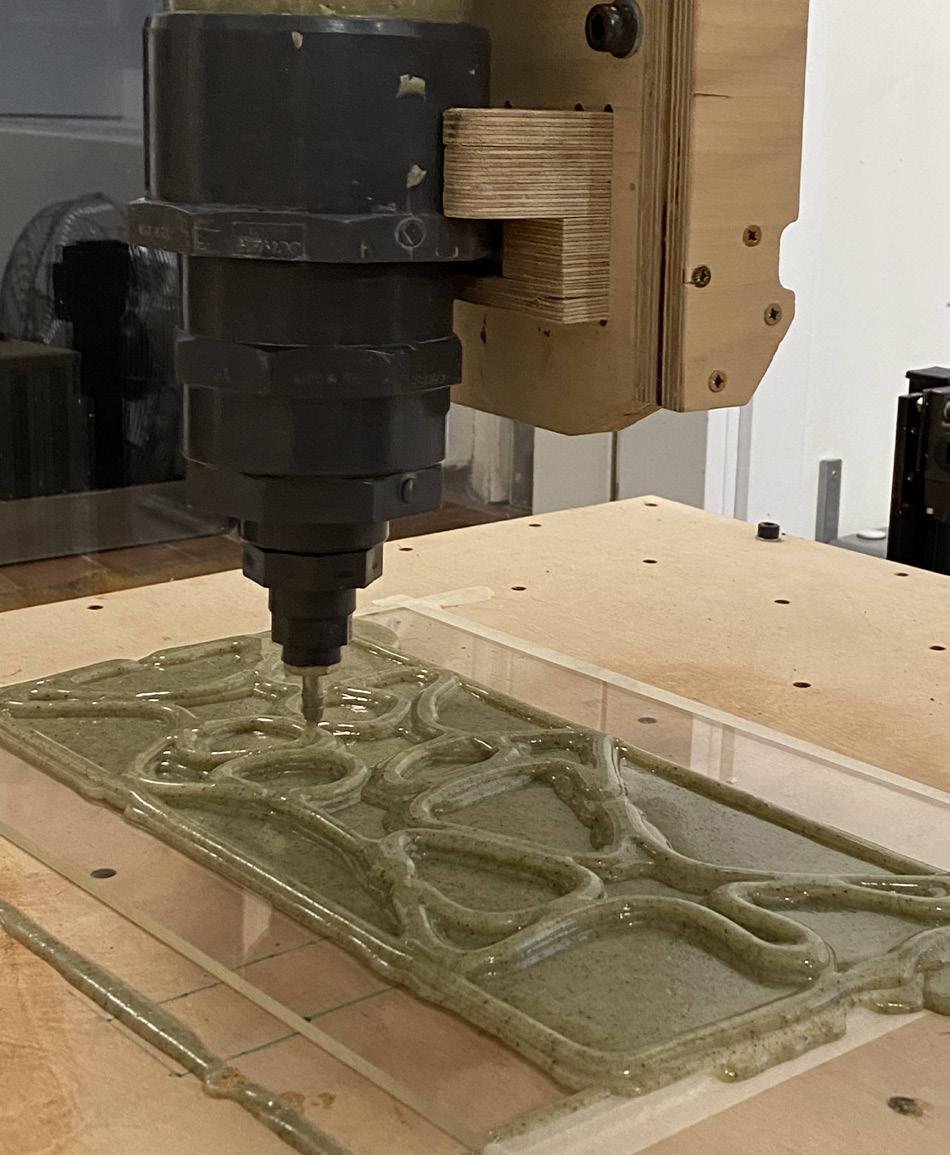

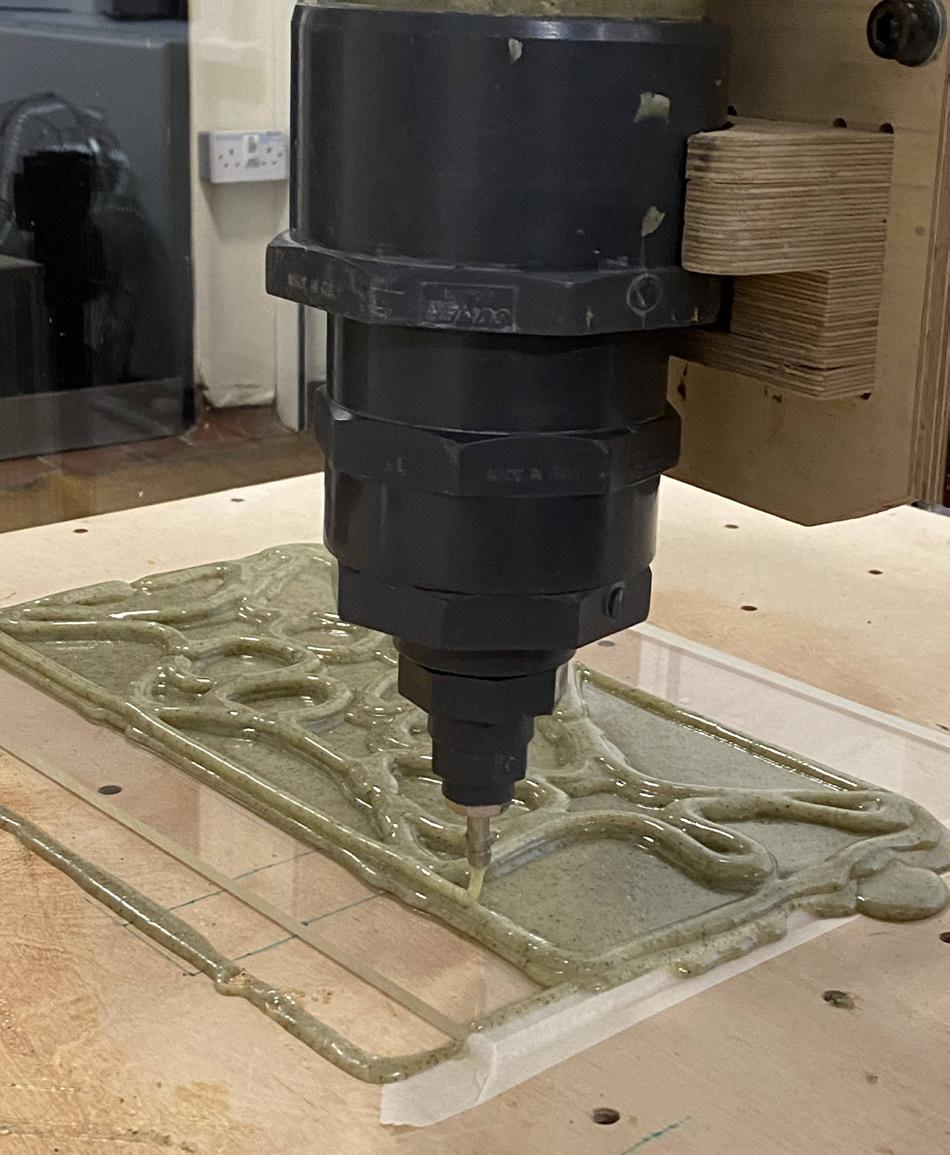
Experiment conclusions
62 63

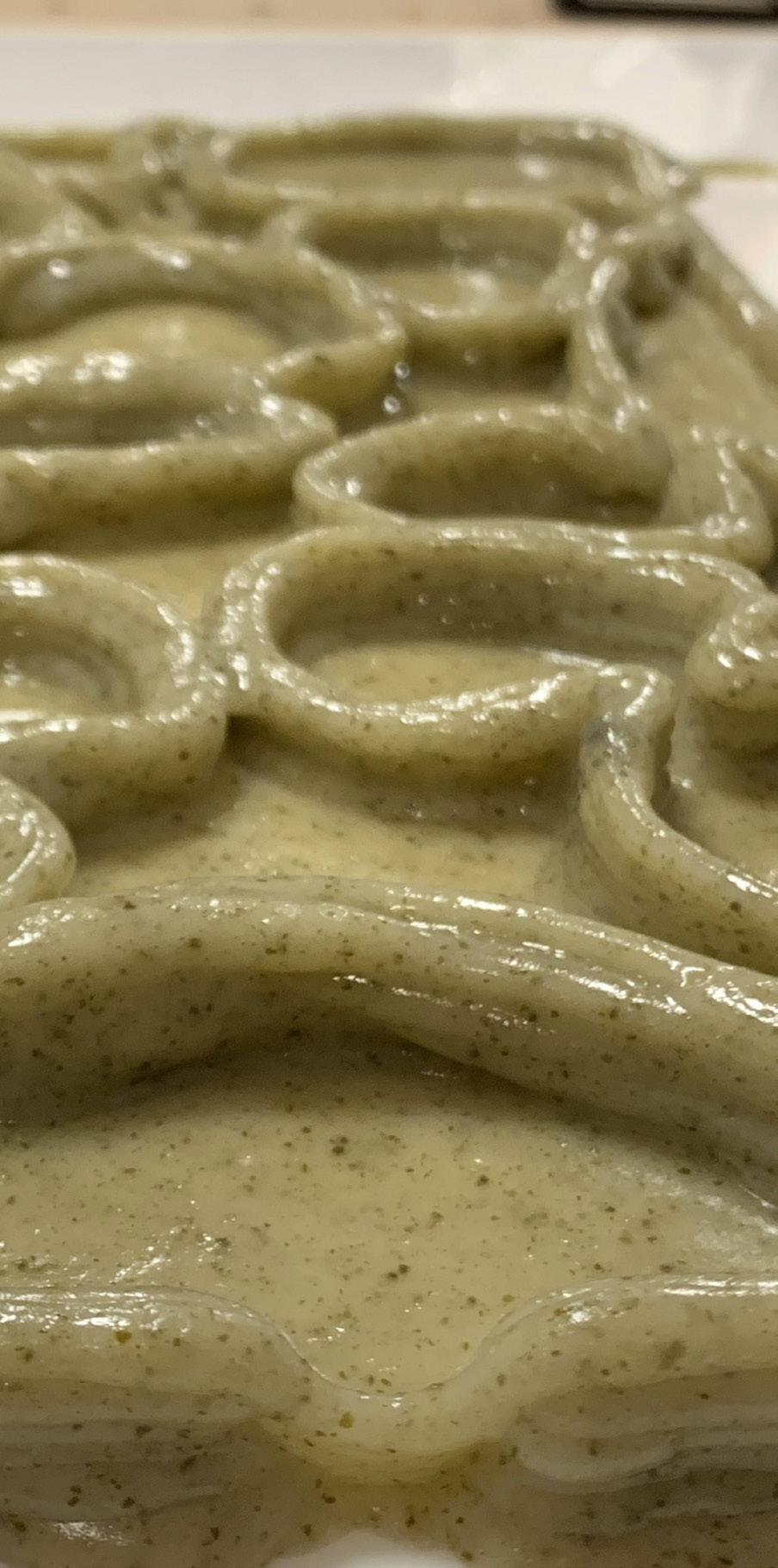
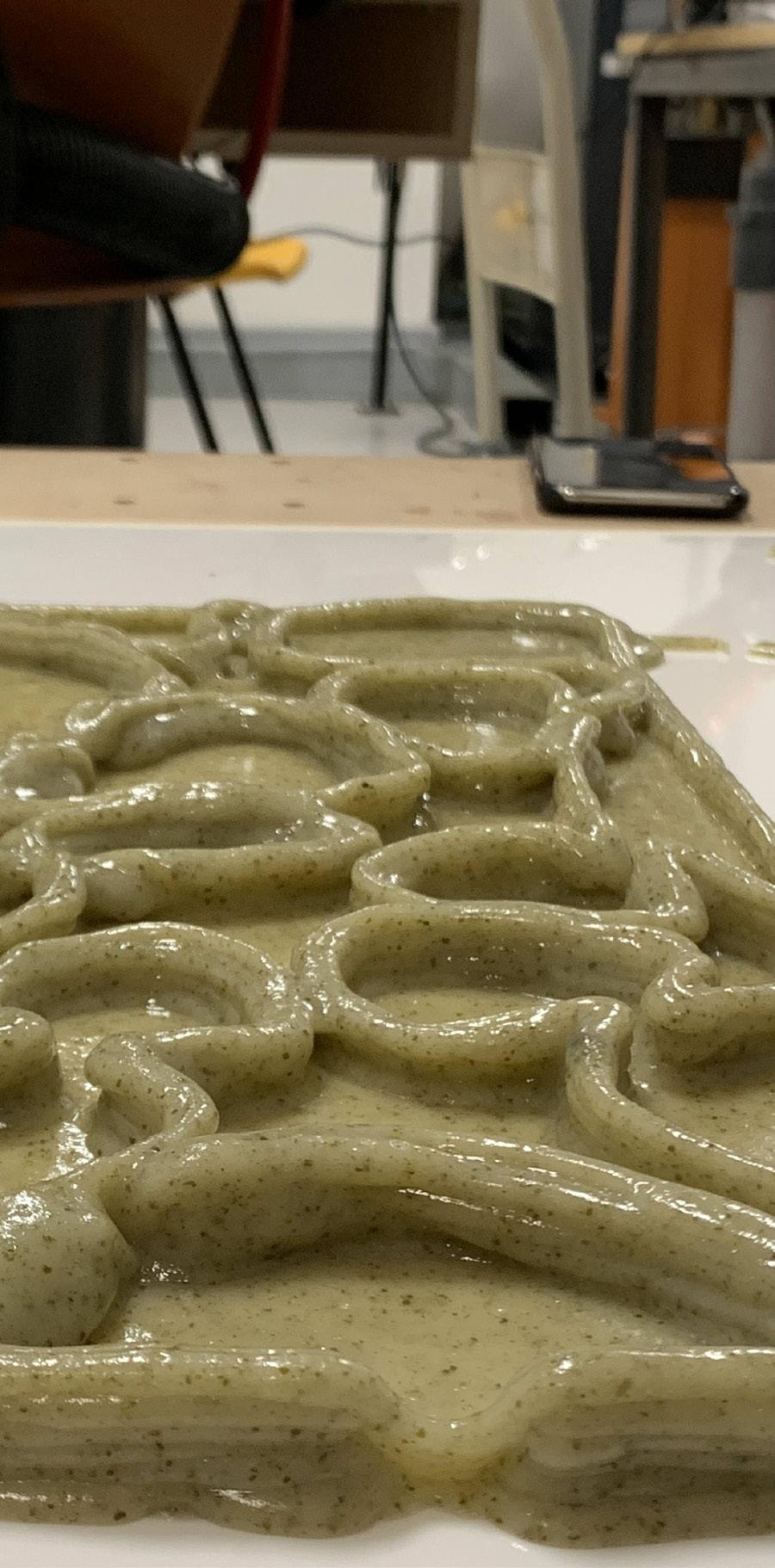


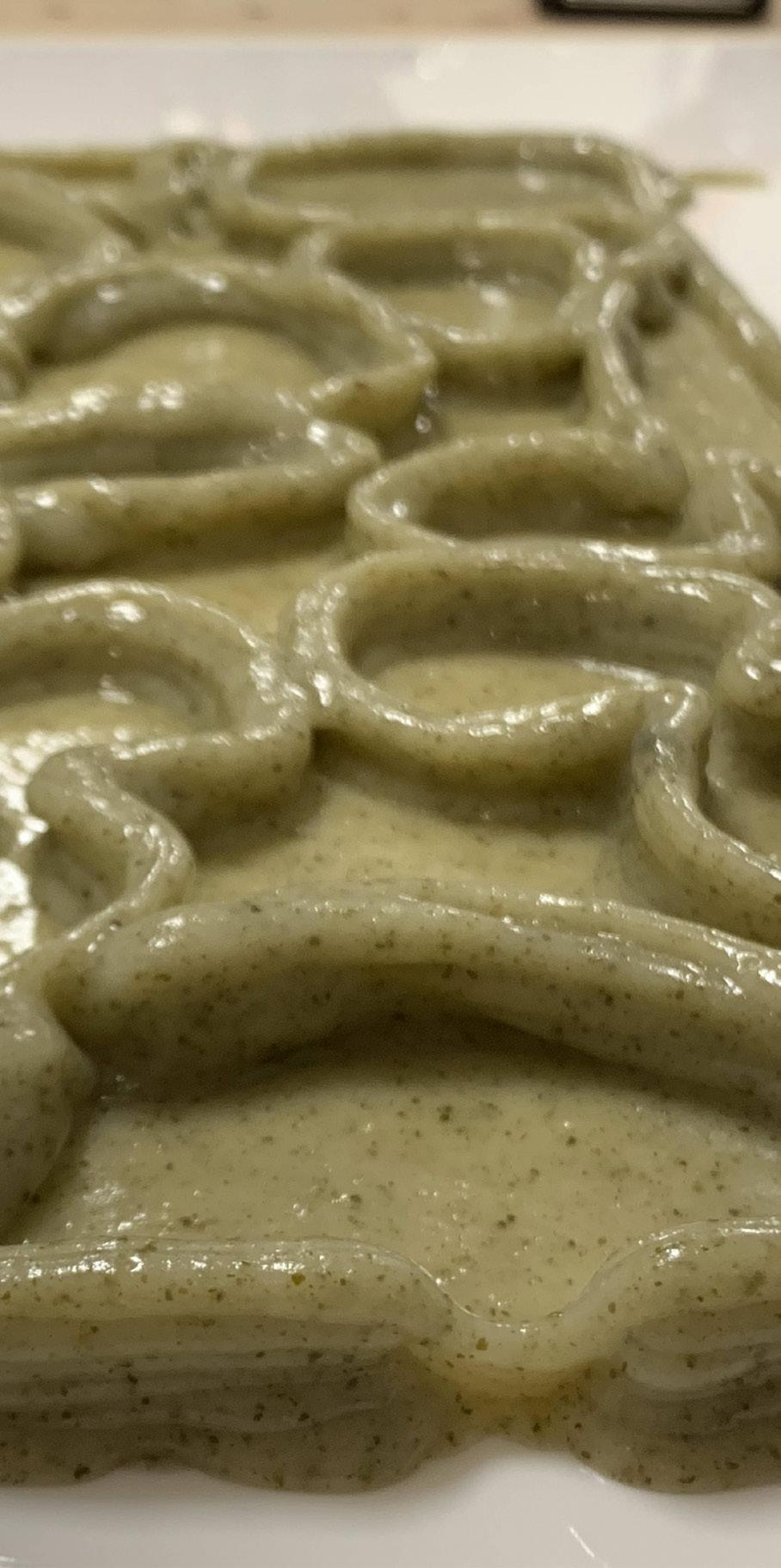
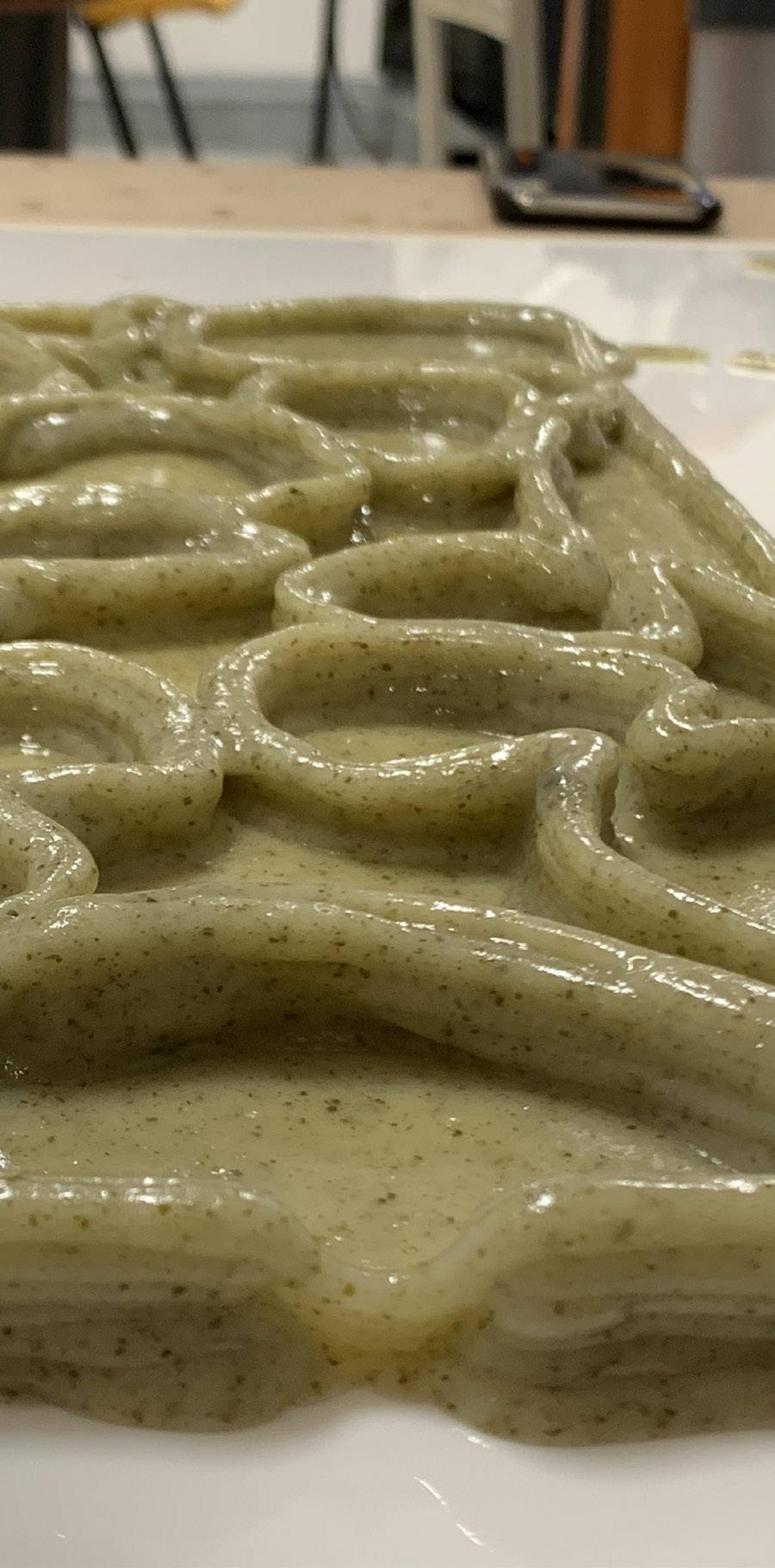
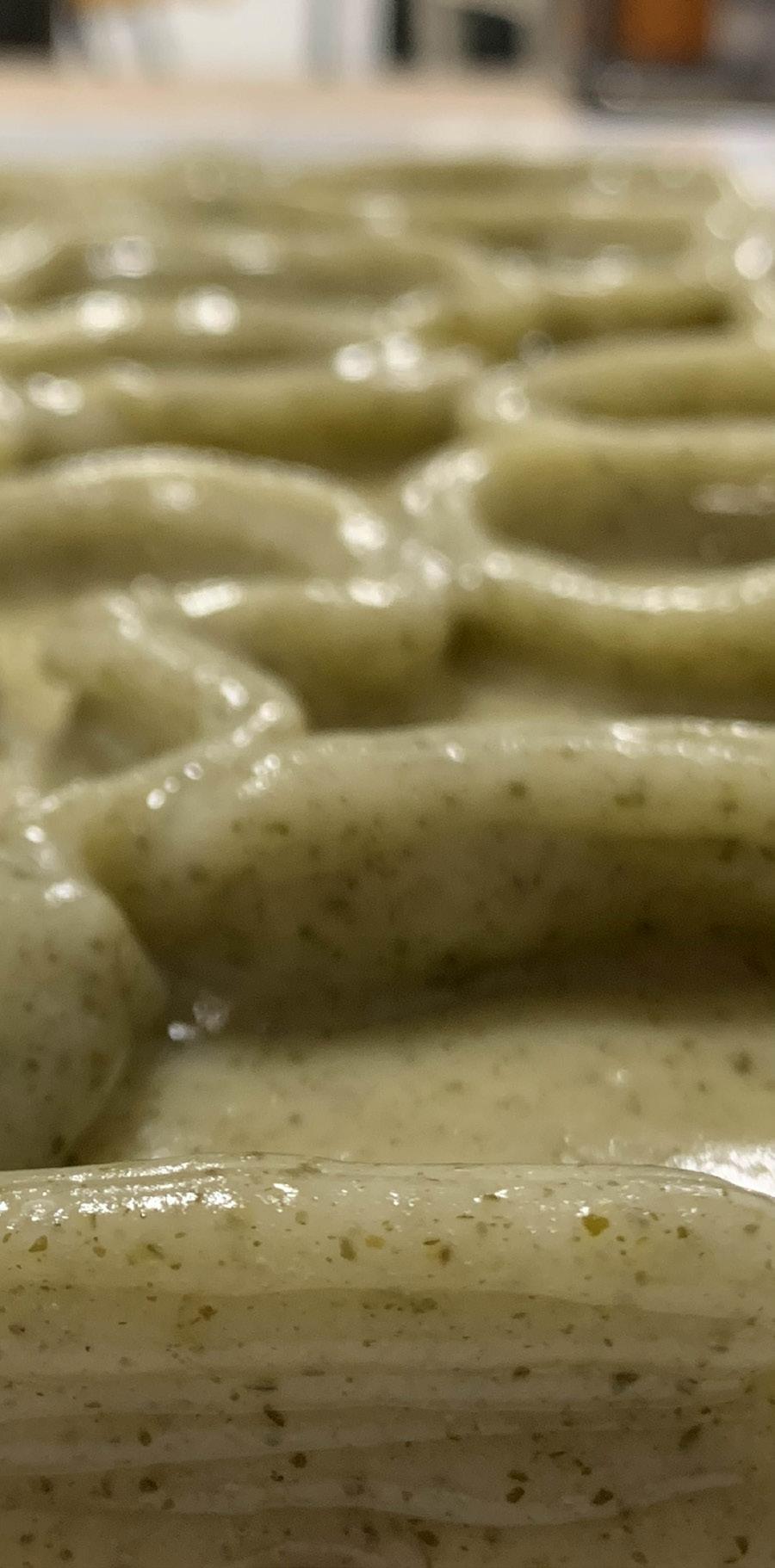
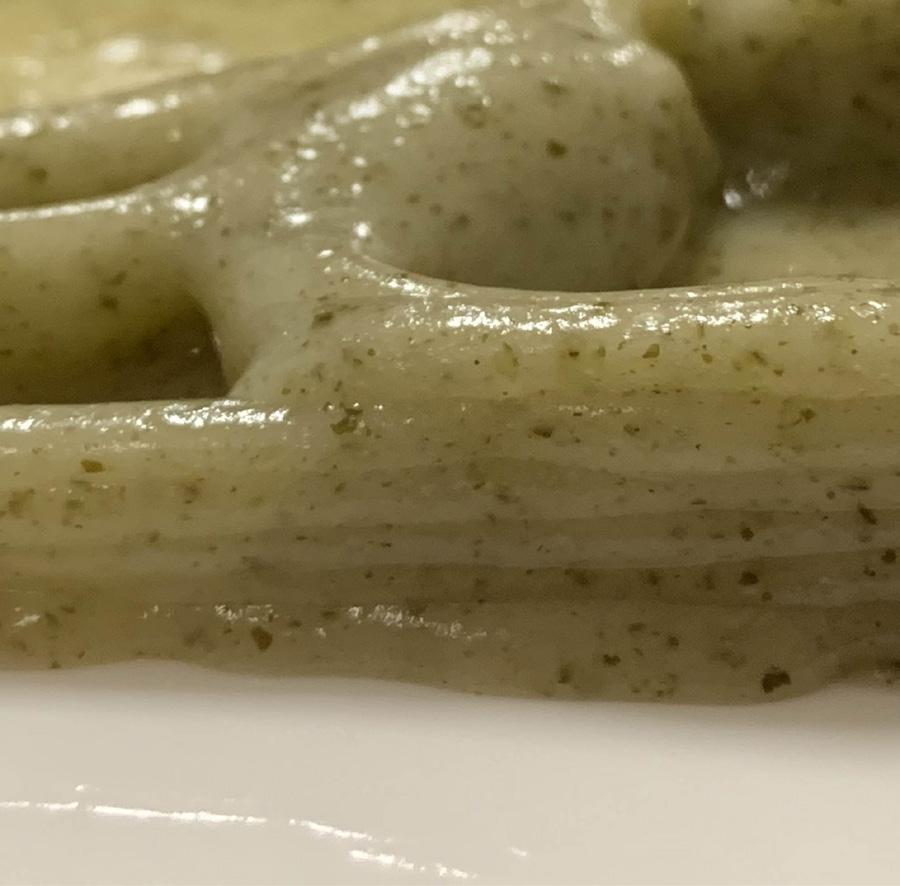

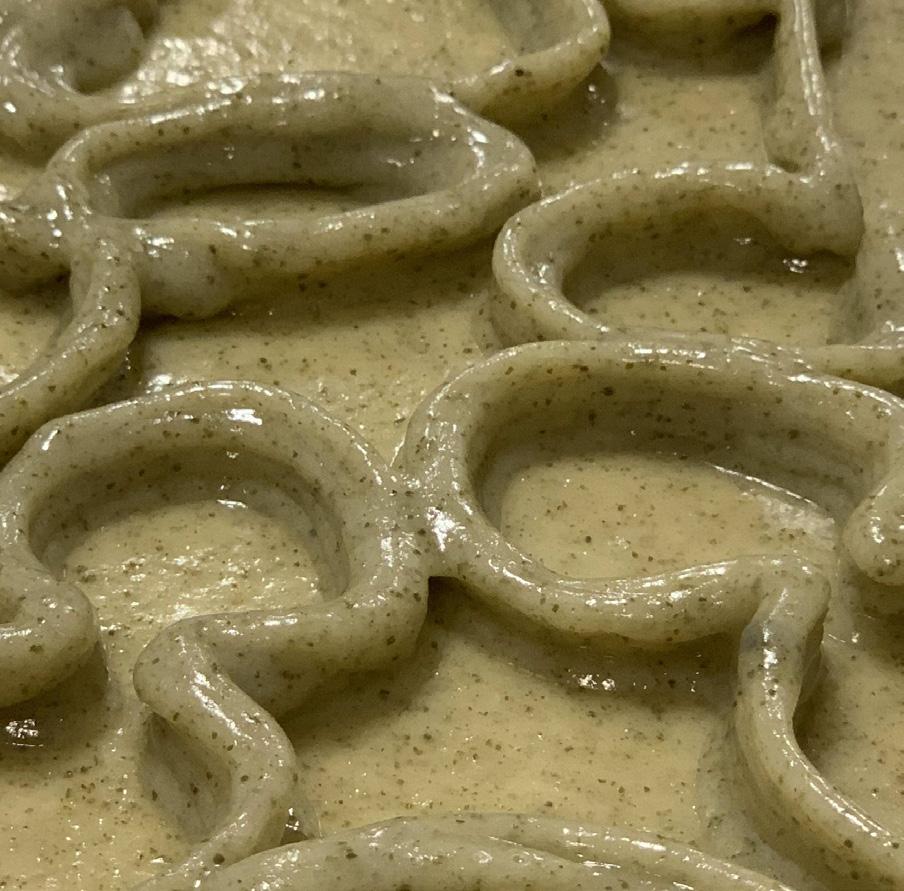
Set up – as the material properties could change from printing to printing due to minor changing in parameters that couldn’t be controlled (air moisture, room temperature, and so on), there is a need to control in many parameters as possible and leave the spontaneous behaviour to the mix. The next experiments would focus on idealizing the conditions while printing. Important parameters would be – best printing temperature – as the mix printed while it is still hot, check time range – what is the window for printing from the moment the mix is ready till the time the robot starts to print. Keeping the temperature inside the syringe identical in all parts to avoid curing inside the syringe. Controlling air pressure – the mix extracted as a hot liquid. It doesn’t need air pressure at all. On the opposite, a negative air pressure pipe is needed to install to manage the extraction better.

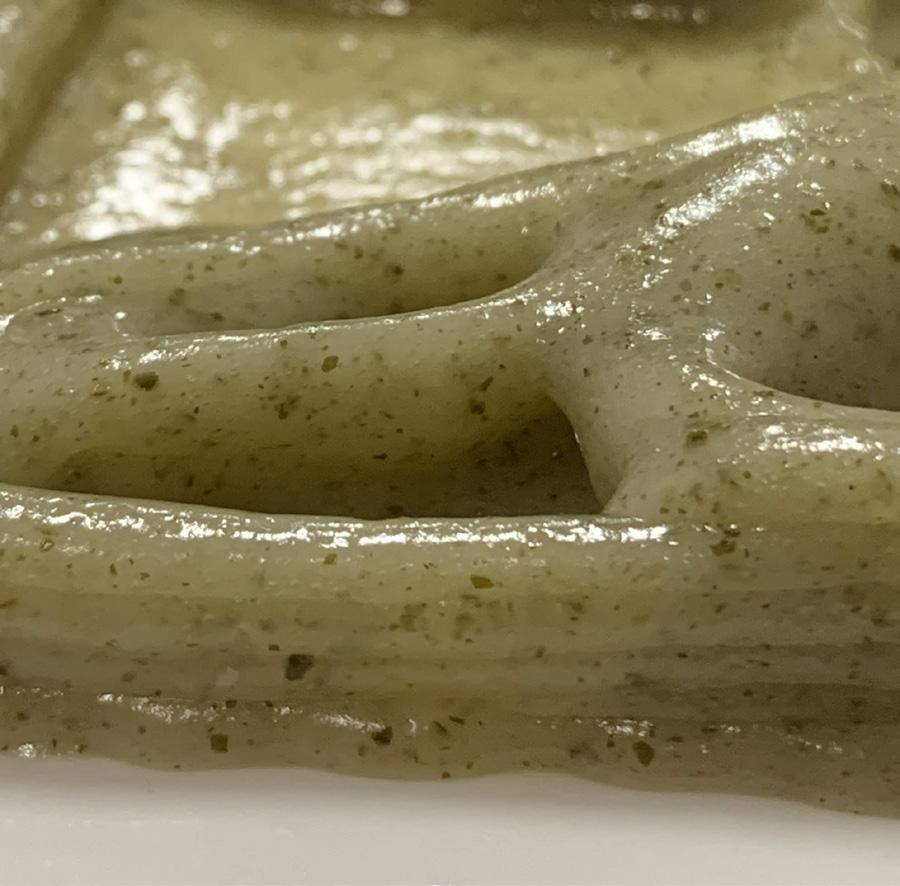
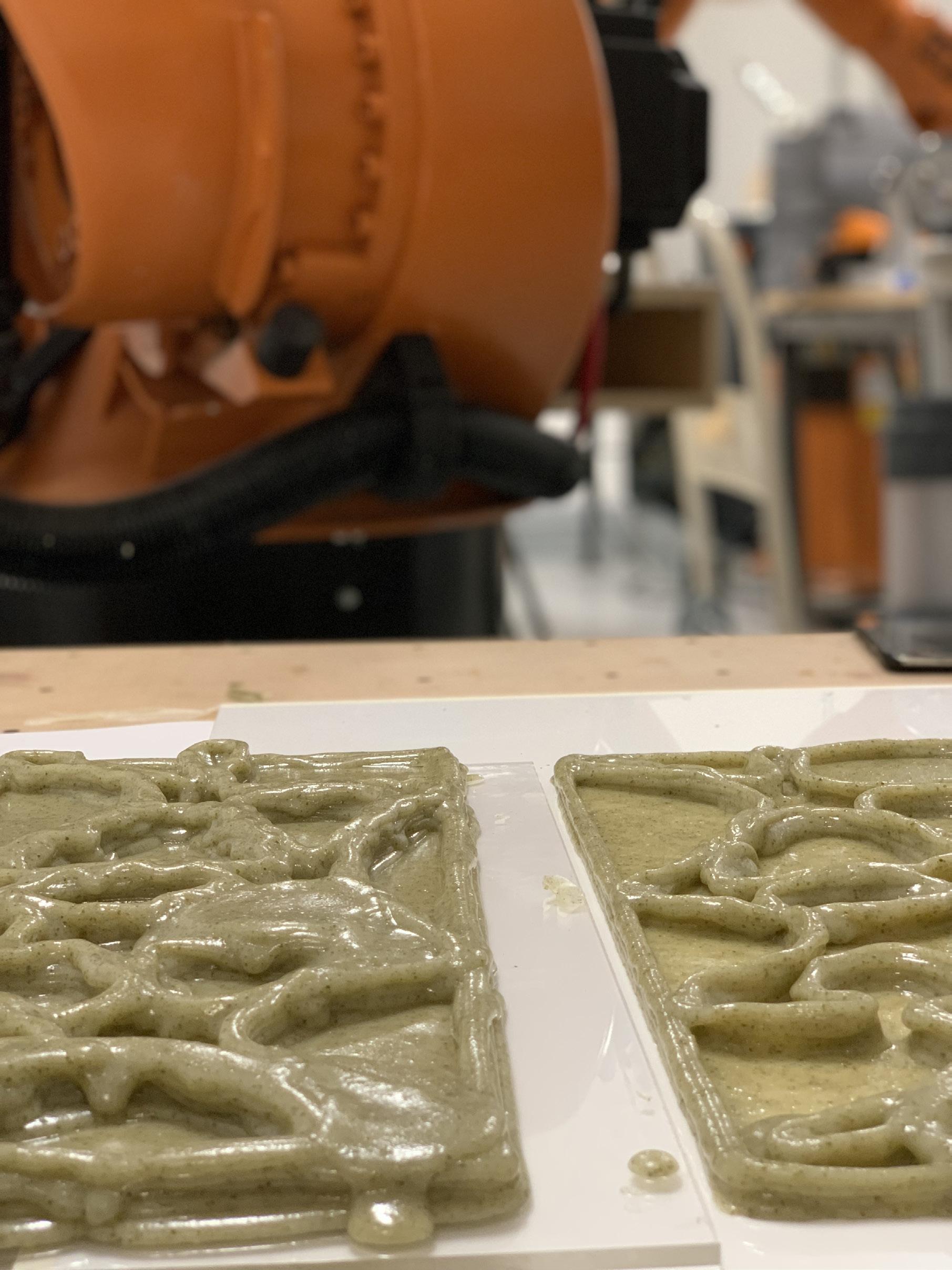
To avoid temperature gaps, a thermal blanket has been Beforeused. that, an experiment of ideal temperature for printing was tested. Results
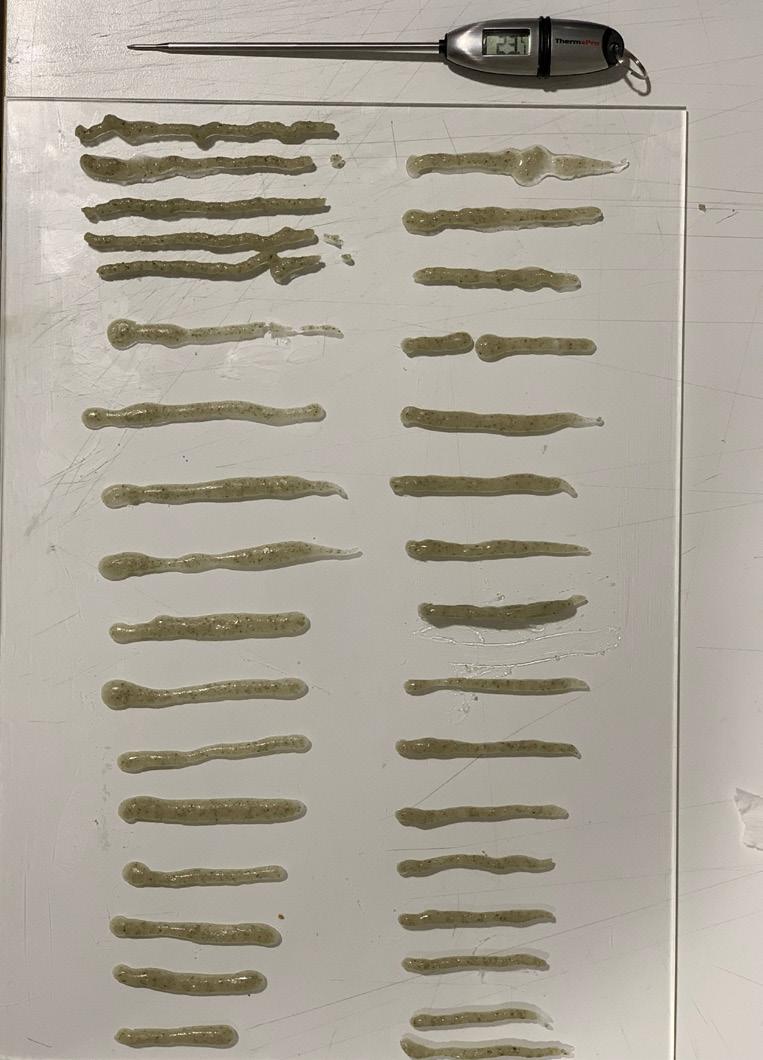
First, As the material is curated in a relatively short time when the temperature goes down (~85 seconds), there is a need to stabilize the temperature.

In this case, the material is hot and expanse after going out from the nozzle. Also, it isn’t very dense (a bit denser than water), so it doesn’t need any air pressure. At the start, the material was extracted only with gravity. To maximize the control on the pace of the extraction of the material, the air pressure tubes have been replaced with negative air pressure (suction).

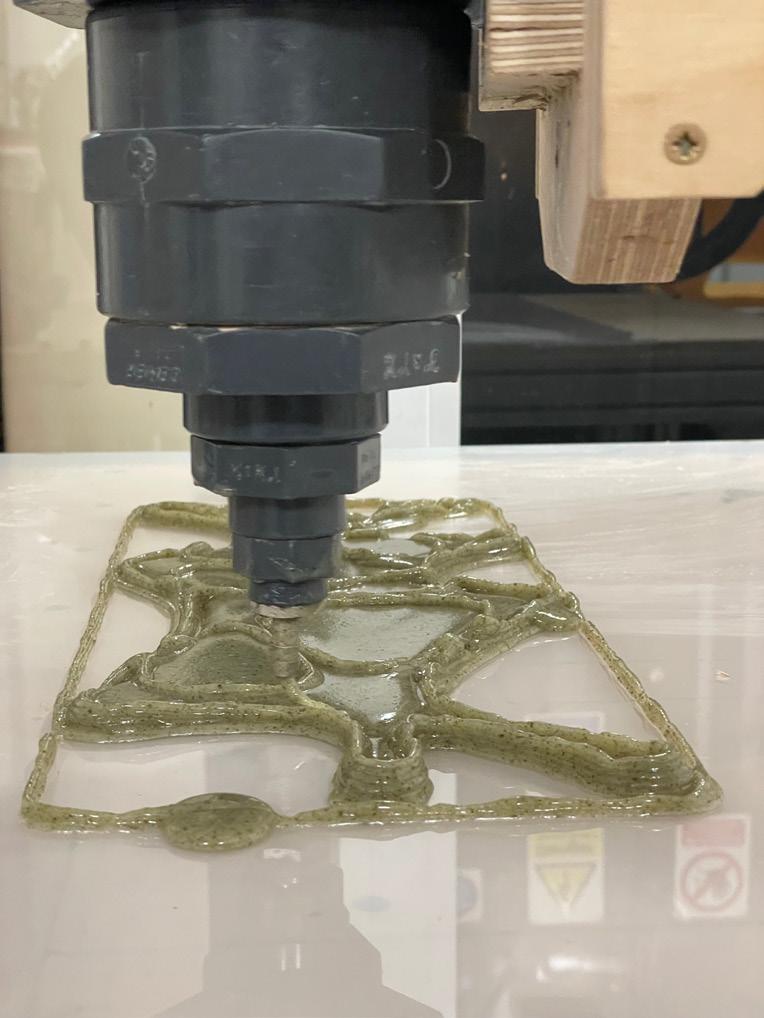
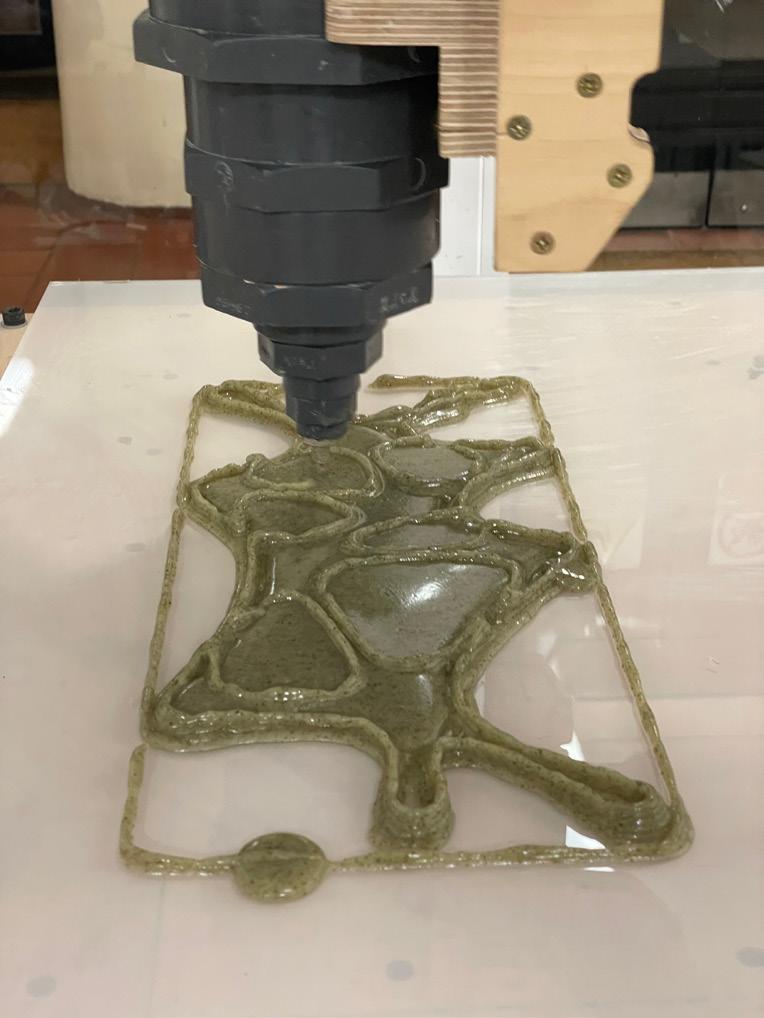
All these fine tunings of the printing brought to better results, but there are still some parameters that couldn’t be controlled, such as the expansion of the material. This parameter affects the height of the model, and when the robot goes up and up while printing, but the material stays low, it affects the printing accuracy.
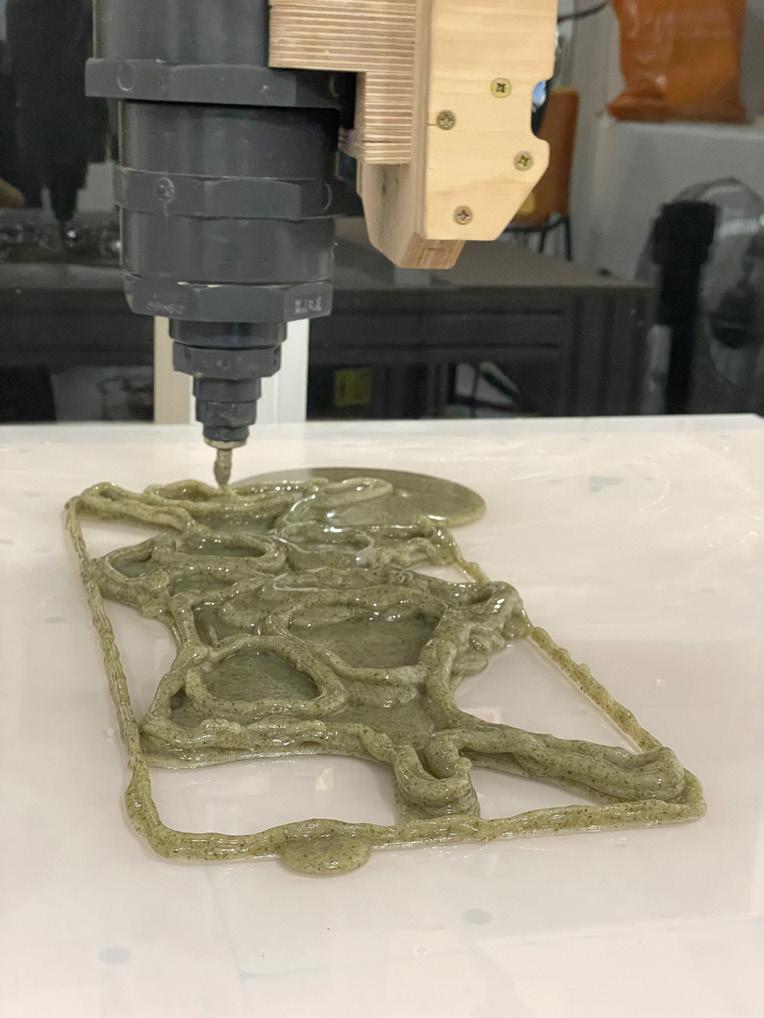
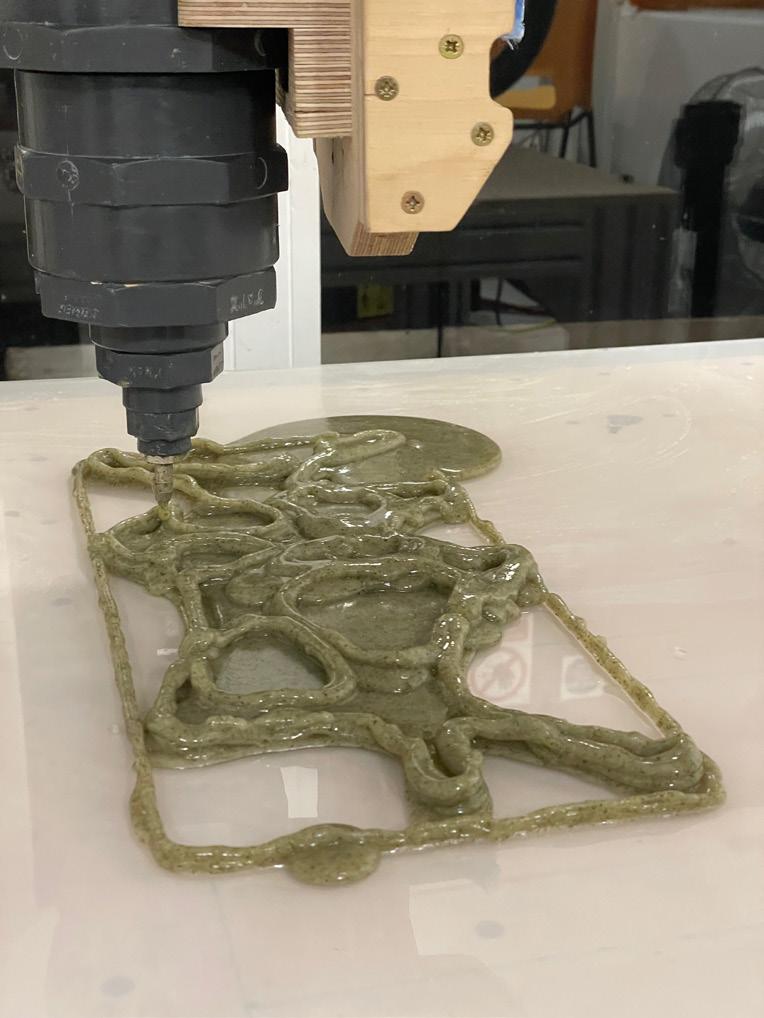
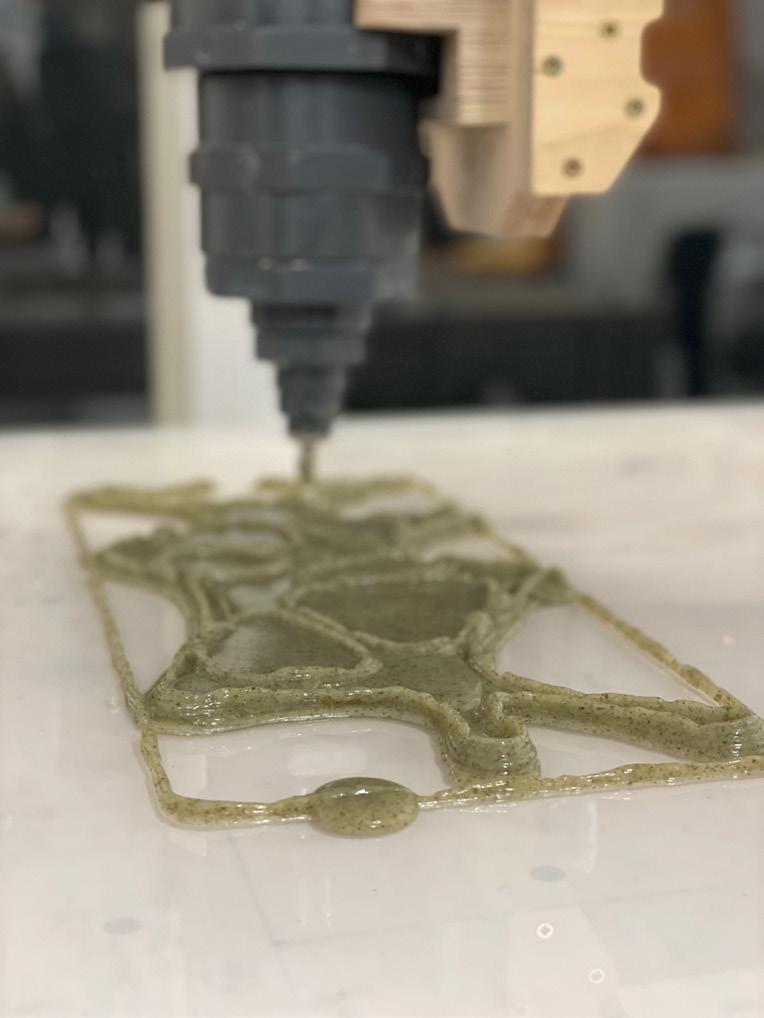
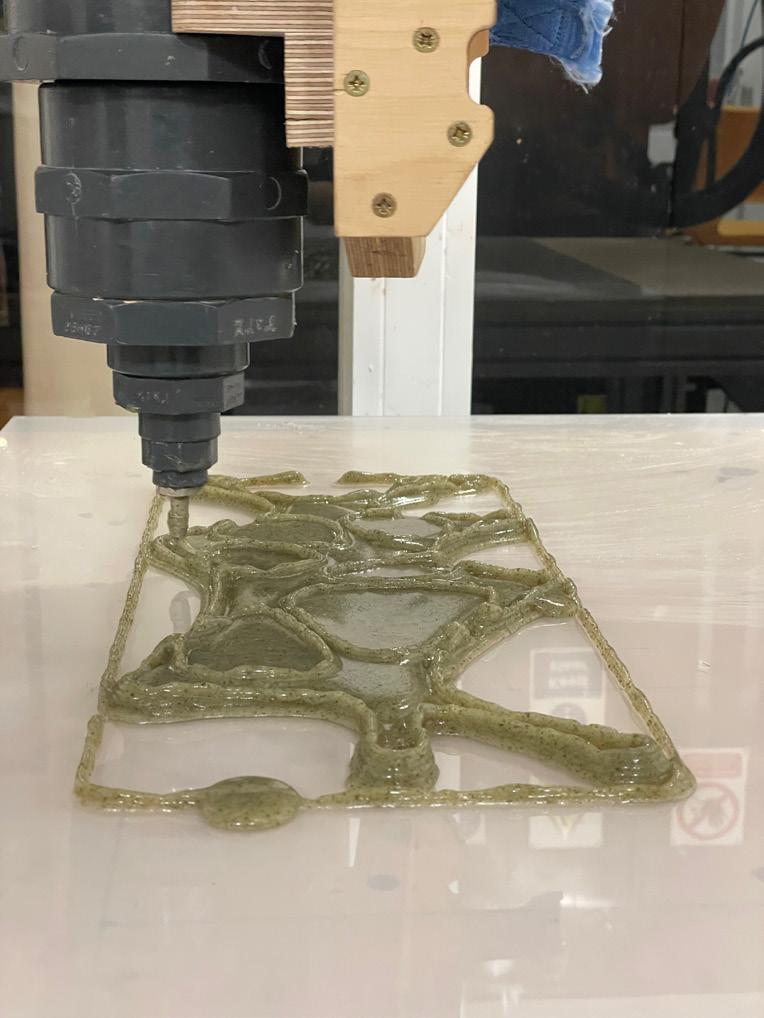
3
- The ideal temperature for printing is 42 degrees to 47 degrees. In this range, the material comes out smoothly and consistently, not too viscous. After realizing the best time range and the right temperature for printing, the blanket was set to this temperature and kept the mix from Anothercooling.parameter that has to be modified is the air
Thermometer following interior temperature in the syringe Thermal blanket keeping the temperature equal and the mix homogeneous, preventing the mix from curating Negative air pressure pipes installed C D Negative air pressure test
64 655.7
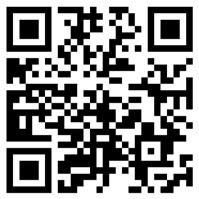
1A
Robotic Modifications
Modifications haven’t been managed yet to overcome this challenge.
C-D
Modifications of the robot have to be done to get ideal conditions when printing.
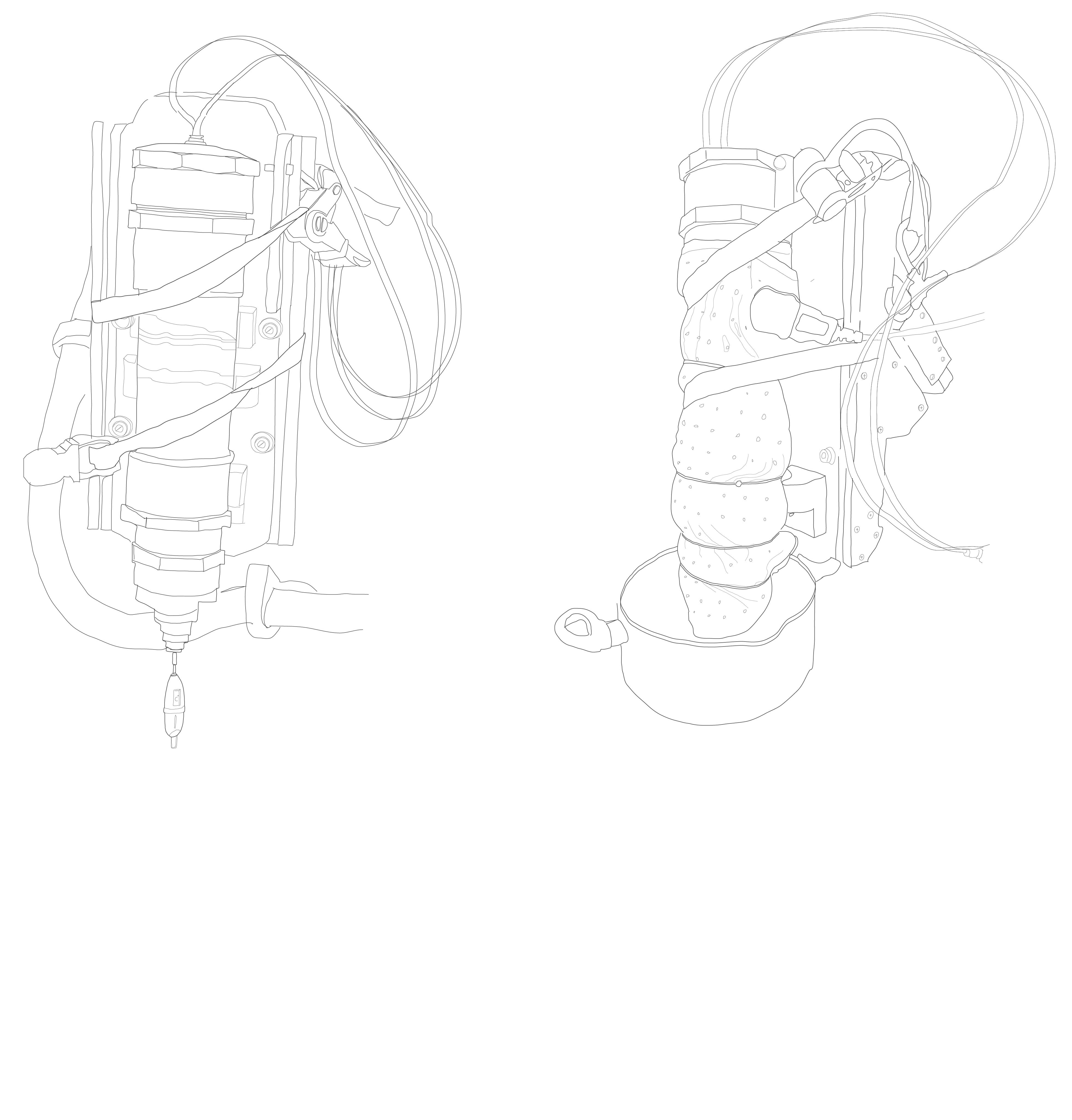
1 2 3 B
In the case of gaps in temperature when the mix stays in the syringe during printing, a non-consistent material is extracted, causing problems to the model.



Adaptation and optimization
Usually,pressure.robotic printing uses air pressure.
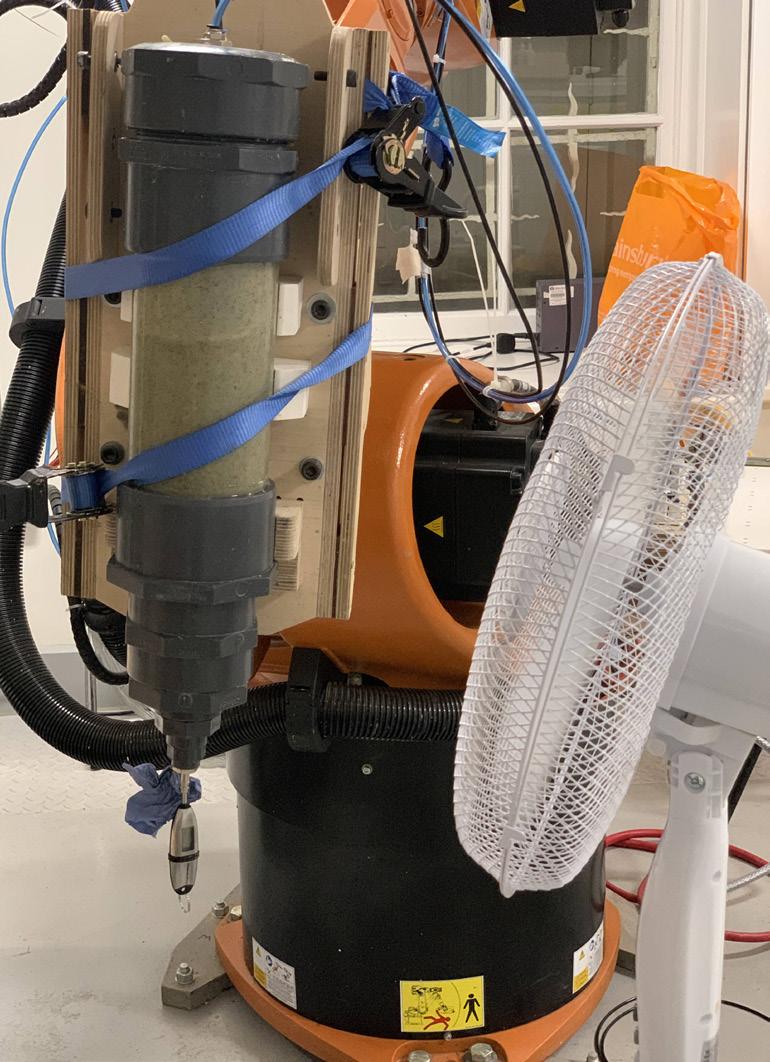
2
A-B Temperature idealization tests
CHAPTER 06
Thermal insulation capability is quite good – when the external temperature was up to 57 degrees, its inner temperature was kept as low as 27 degrees. The material is oil resistant and absorbs a small amount of water, more during the first week. Despite its biological nature to biodegradable it can stay in water without losing its properties for at least 30 min. Time to cure is ~85 seconds 100% biodegradable Range of translucencies
The mix density is a little bit more than that of the water. The melting point is around 62c° and can be reused after that.
Attached to surfaces easily (wood, concrete, metal)
6.1 Material data sheet 6.2 Potential uses catalogue
APPLICATIONSARCHITECTURAL
Carbon whenElasticitymanufacturingnegativemayberenewedputtinginwater.
The properties of the seaweed-based material have been tested after 7, 15, and 30 days. This is due to the understanding that the material tends to lose moisture over time. The most significant change happens during the first 7 days. After that, the material stabilizes.
V=9.5 1.3g/cm^3
Day (0) dry mass= 11 g Day (0) dry mass= 11 g A= 1-(m (dry) / m (submerged)) A= 1-(m (dry) / m (submerged))
Day (30) (45.25 mm thick)
Top surface heated to an average of 57 Measurmentc° of bottom surface taken after:
Attached to surfaces easily (wood, concrete, metal)
Shrinks in dry environment (9%-10%)
Day (30) 30 mm thick
1-(2.73/3) = 0.09= 9%
Time to cure ~85 seconds
Day (30) dry mass= 10 g Day (30) dry mass= 10 g Day (7) mass after oil submerssion= 16.2 g Day (7) mass after water submerssion= 21 g
Day (7) 30 mm thick
Testing and measuring
Temperature gap after 20 min =8.1 c°
A= 1-(10/10)=0 = 0% A= 1-(10/11)=0.091 = 9.1%
Day (0) dry mass= 22 g Day (0) dry mass= 14 g
Top surface heated to an average of 57 Measurmentc° of bottom surface taken after:
Seaweed compound age (days) Density M= 13 g M= 13 g M= 12 g V=10 cm^3 V=10 cm^3
Day (0) (50 mm thick)
Day (7) dry mass= 16.2 g Day (7) dry mass= 20 g
Carbon negative manufacturing
Day (30) mass after oil submerssion= 10 g Day (30) mass after water submerssion= 11 g
Material DATA Sheet
Day (30) (2.73 mm thick) Day (7) (45.25 mm thick)
Reuse by melting (melting point ~70 c°)
1-(2.73/3) = 0.09= 9% 1-(45.25/50) = 0.095= 9.5%
Elasticity may be renewed when putting in water
=X
material properties 6.1
Day (15) (2.73 mm thick)
Day (15) dry mass= 20 g Day (15) dry mass= 12.6 g
Thermal Properties 7 3015 (p = m/V) (C°) (C°)
Day (0) (50 mm thick)
0 min: 18 c° 10 min: 22.7 c° 20 min: 27.8
Oil absorbance (%) Water absorbance (%)Shrinkage/dehydration (%) Melting point
Day (15) (45.25 mm thick)
Range of translucencies
A= 1-(16.2/16.2)=0 = 0% A= 1-(20/21)=0.047 = 4.7%
100% biodegradable
68 69
Temperature gap after 20 min =8.5 c°
Mouladble - can mimic any shape and inclined surfaces
0 min: 18 c° 10 min: 21.9 c° 20 min: 26.1 c°
Glossy and squeegee
Day (0) (3 mm thick) Day (7) 3 mm thick ( 59.5 c° )
0 min: 18 c° 10 min: 22.2 c° 20 min: 26.5 c°
Day (15) 50 mm thick ( 62 c° )
Wet and moist after cures, losing the wetness gradualy
Day (15) 30 mm thick
Day (30) 50 mm thick ( 62.7 c° )
Day (0) (3 mm thick)
p=12 g/9.5 cm^3= 1.26 g/cm^3
1-(45.25/50) = 0.095= 9.5%
Day (15) mass after oil submerssion= 20 g Day (15) mass after water submerssion= 13.5 g
Day (0) dry mass= 18 g Day (0) dry mass= 21.8 g
Day (15) 3 mm thick ( 62 c° )
Day (7) 50 mm thick ( 59.3 c° )
Day (0) (50 mm thick)
1-(45.25/50) = 0.095= 1-(t(n)mm/t(0)mm)9.5%
Day (7) (2.73 mm thick)
Temperature gap after 20 min= 9.8 c°
p=13cm^3g/10cm^3=
Can dissolve in water (rate and time depend on the mix and age)
Top surface heated to an average of 57 Measurmentc° of bottom surface taken after:
1-(2.73/3) = 0.09= 9%
p=13 g/10cm^3= 1.3g/cm^3
Day (30) 3 mm thick ( 62.5 c° )
A= 1-(20/20)=0 = 0% A= 1-(12.6/13.5)=0.067= 6.7%
Day (0) (3 mm thick)
Material potential uses catalogue and measuring material properties
After getting a better understanding of the material’s capabilities, a catalogue of a series of potential uses has been Thesedone. elements have been chosen following the properties of the material. It can be a membrane or a skin, but it may also be joint absorbing movements and tolerances.
Learning the material, together with new manufacturing technologies, can lead to new aesthetics and values.
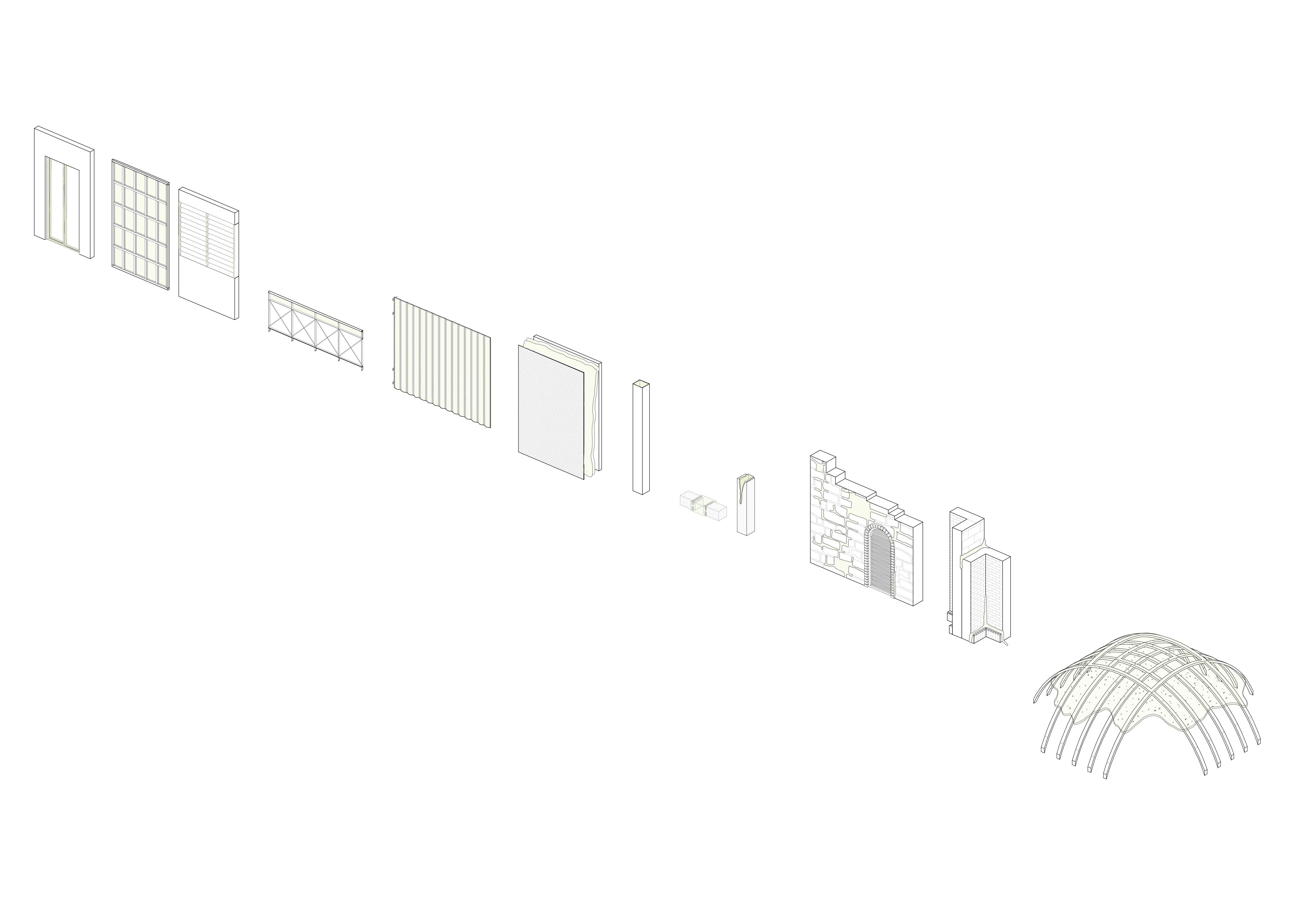
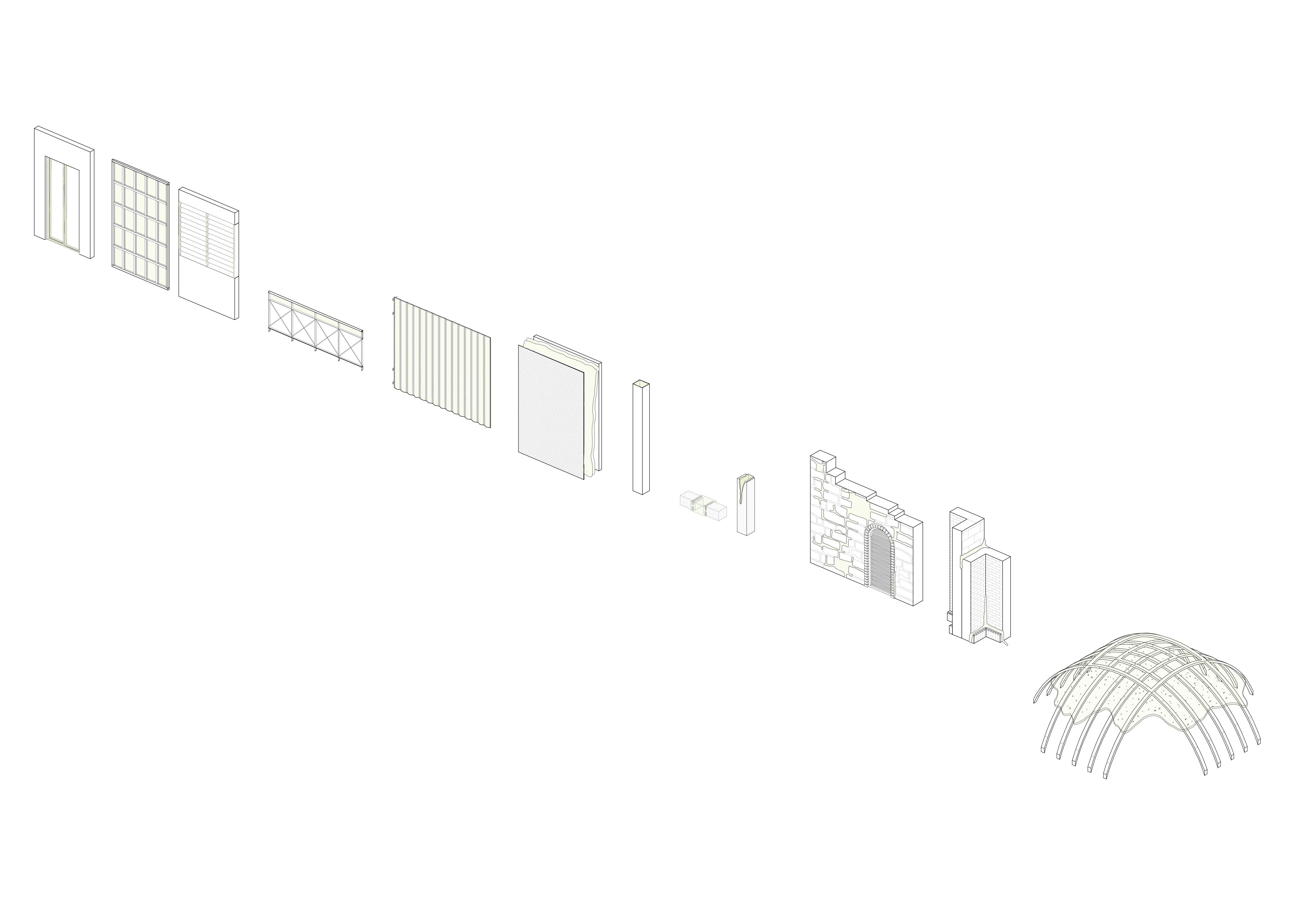
70 71
It may be translucent and light or opaque and dense. It can mimic complex forms, but it can also form bizarre and spontaneous shapes that stand on their own.
Testing
6.2
RangePartition/glazingoftranslucencies Flexibility,Vents movementsqueegeesabsorption Profile mould-ability fast cure Removable / temporary ChimneyFiltercomponents Angled Acousticpanelinsulation 07 08 10 1211 09 72 736.2
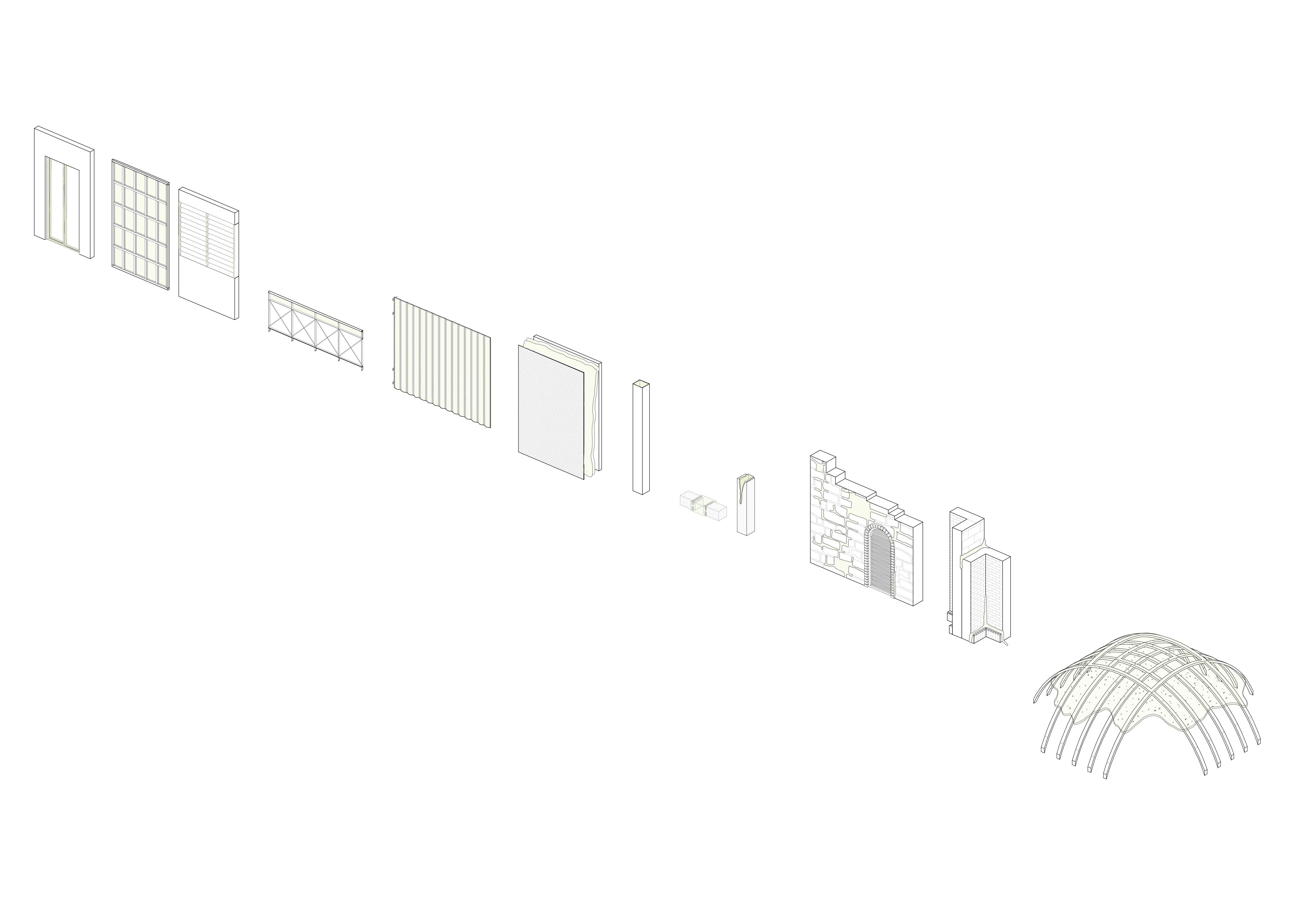
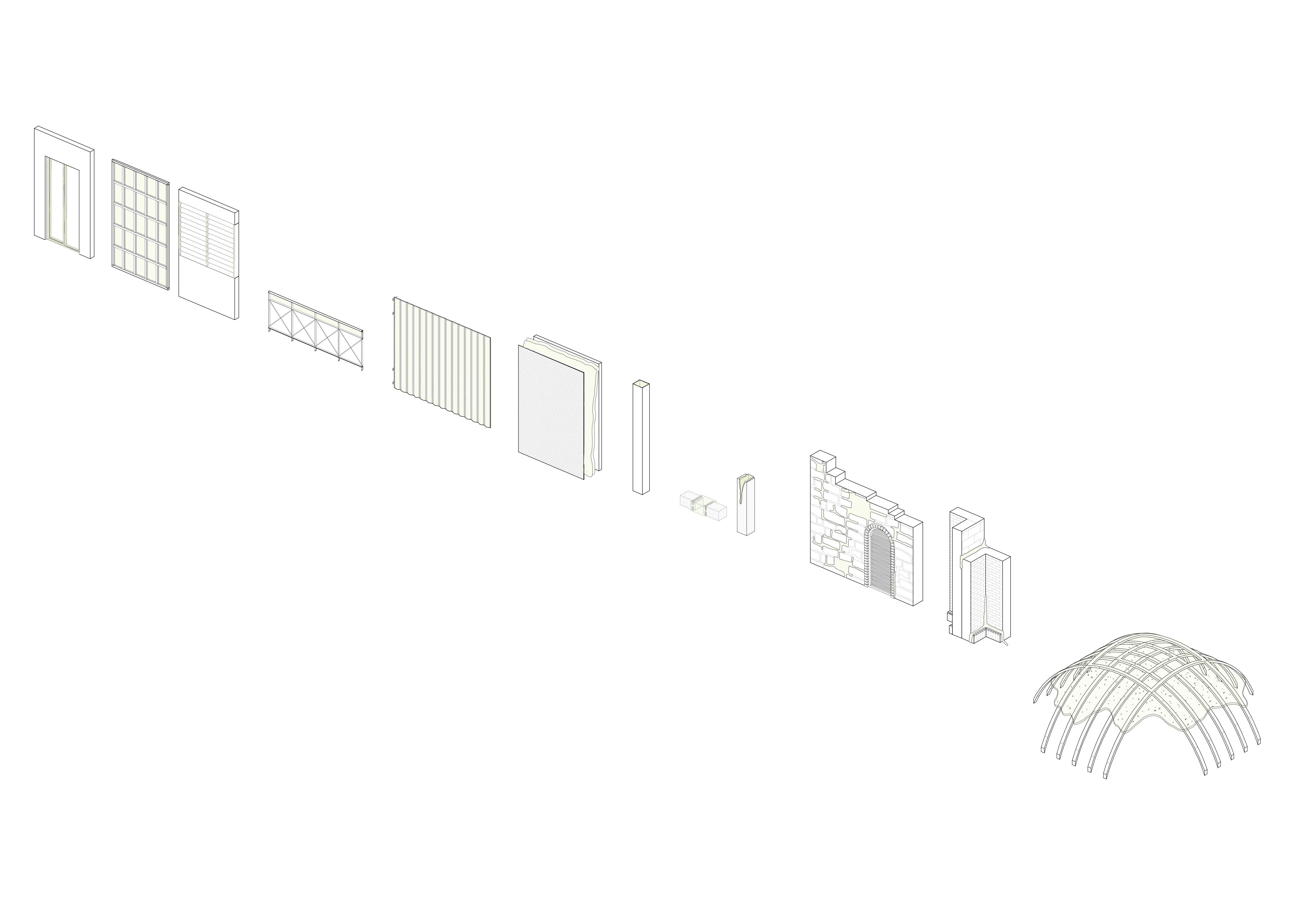
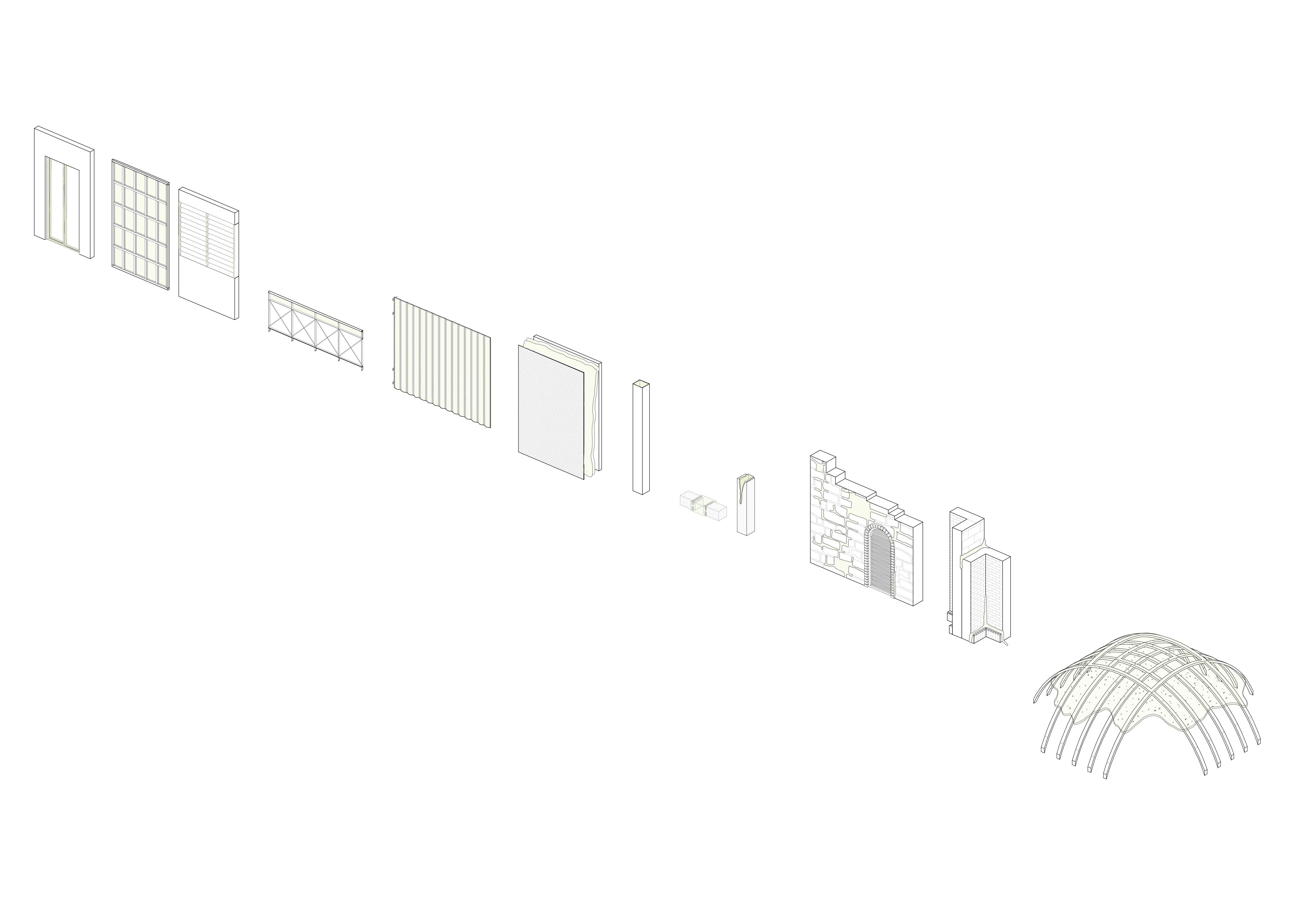
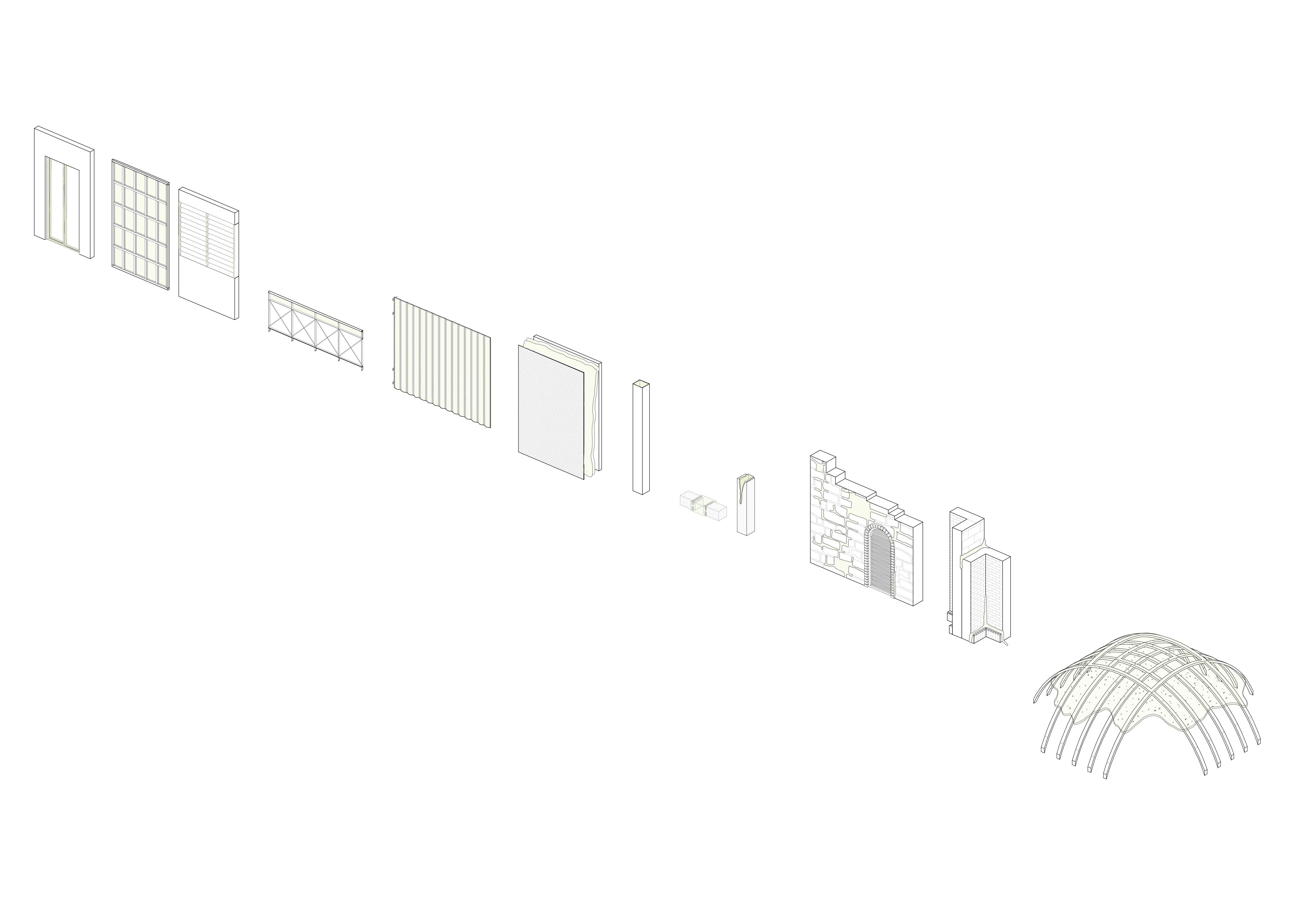
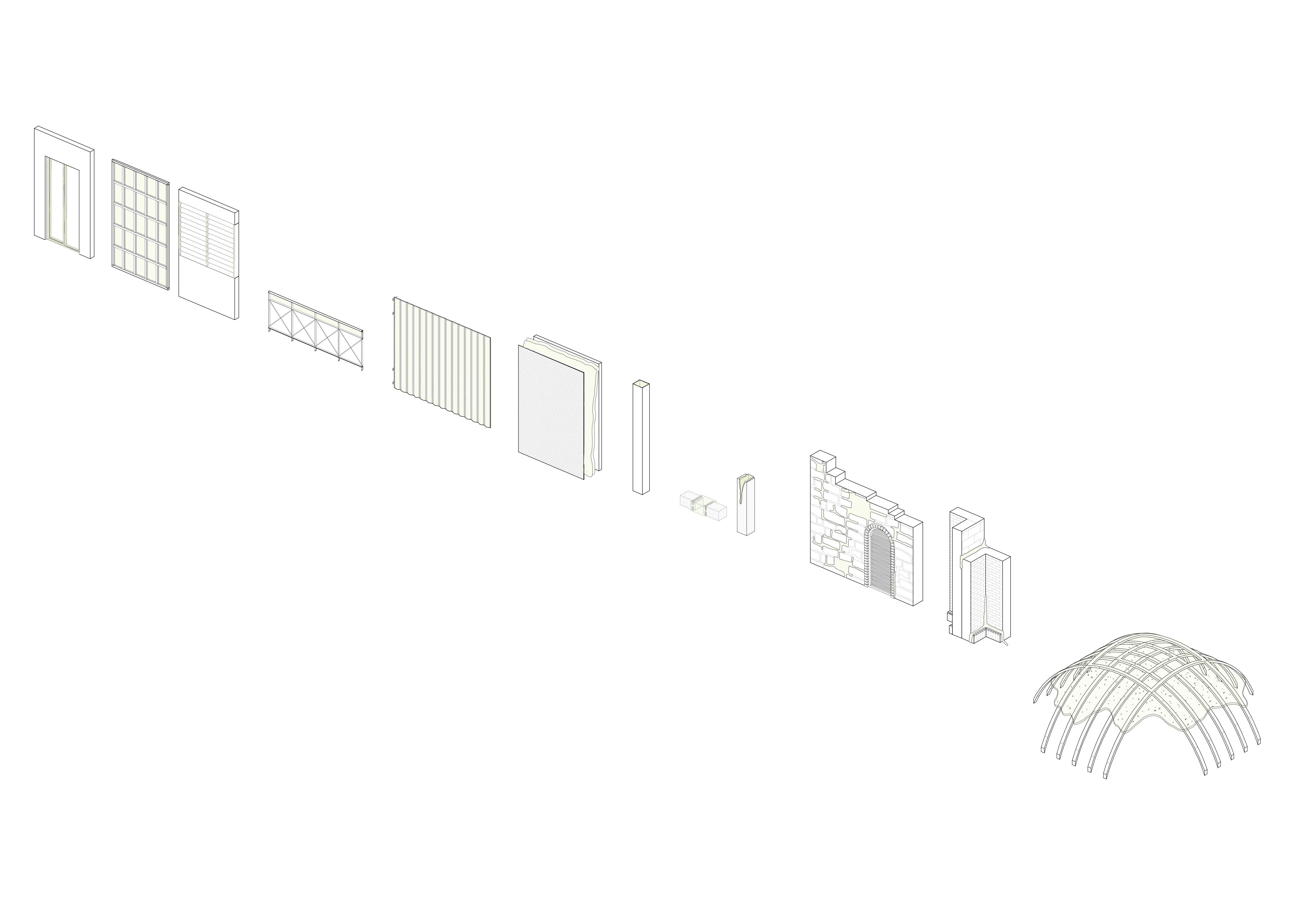
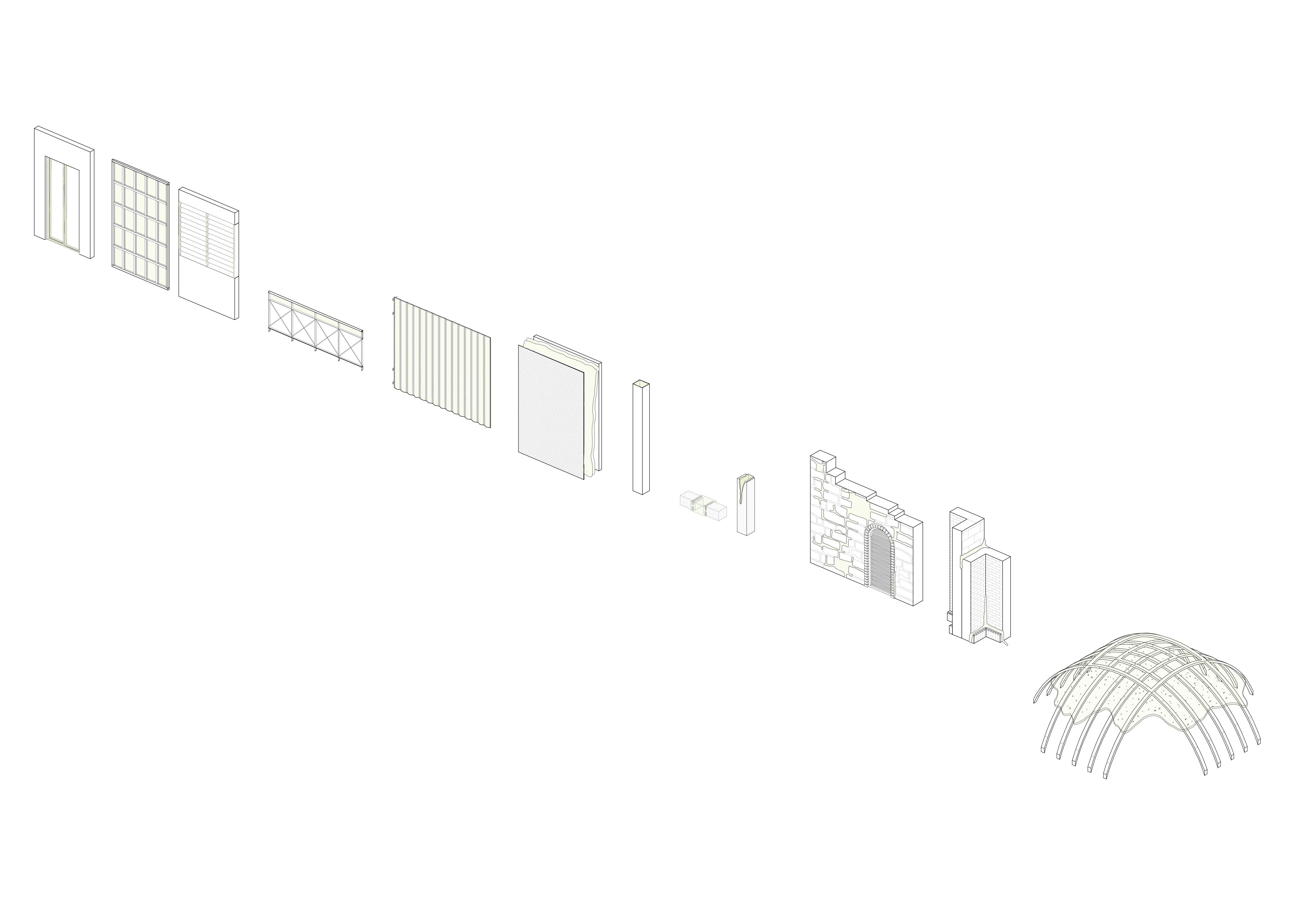
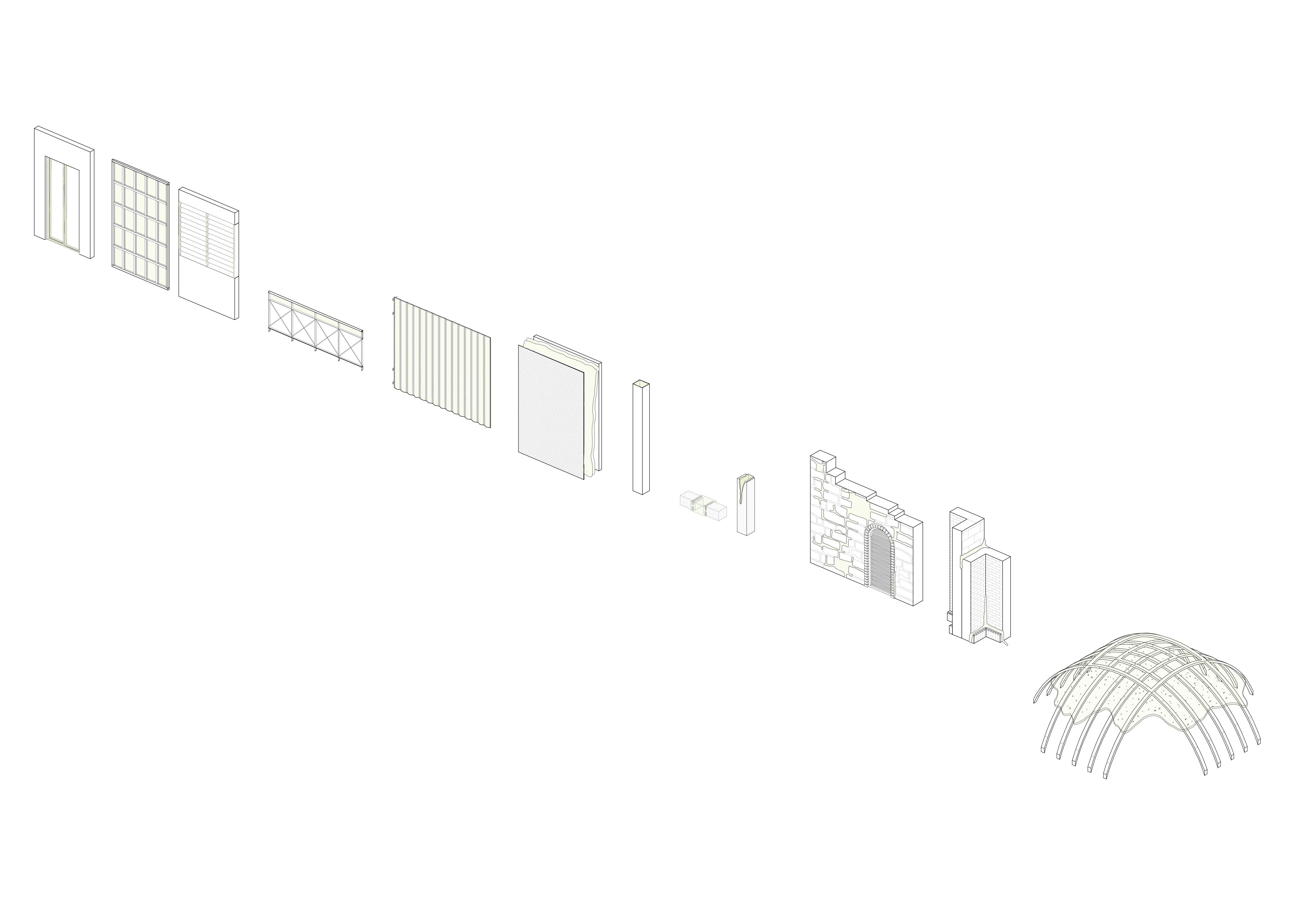
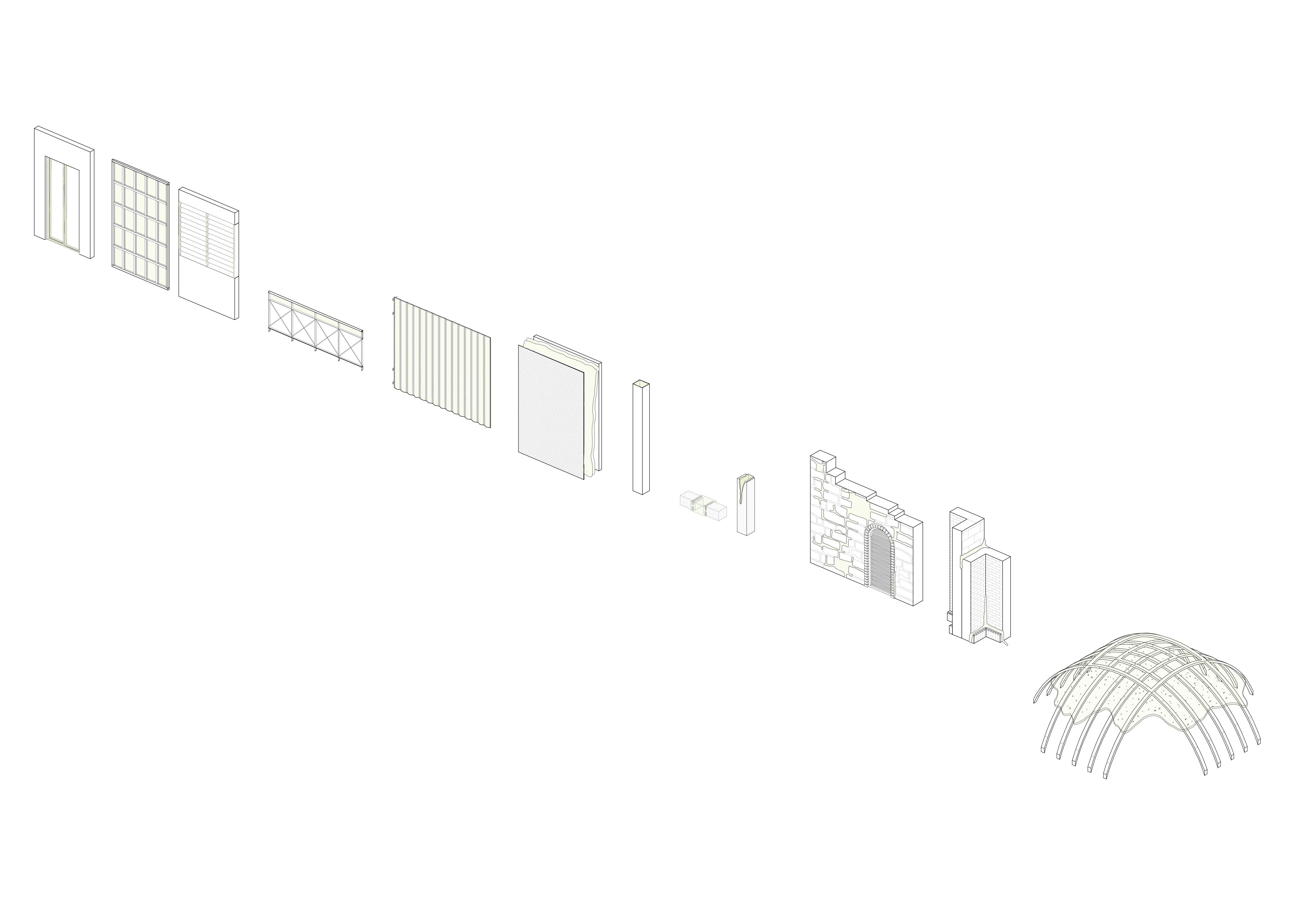
As the material has a short life span, constant maintenance and renew would be needed – and constant production and process of the material. This way, the moments of the necessity of maintenance become opportunities for design. The properties of the material, together with new technologies, create new aesthetics, symbolizing the challenges and the values of the 21st century.
In the years up to that deadline, parts of the existing building would be gradually replaced with a carbonnegative seaweed-based material.
For that need, a new 21st-century industry would be created. As the building slowly deteriorates over time, more and more parts would be replaced by seaweed-based material.
CHAPTER 07 Site Leith, Edinburgh 7.1 Flooding forecast of Leith 7.3 Industrial Heritage of Edinburgh Corn exchange building and Former Gas station 7.4 Preparing the building for flooding 7.2 Master plan - A cyclic holistic cleansing system
Heritage Building for the 21st century
By 2030, much of Leith - the port district of Edinburgh - would be submerged by rising sea levels due to increasing global temperatures. The project works with the accepted predictions of the flooding forecast and would prepare the building for flooding, suggesting a cyclic system – starts and ends in the sea.
Aggregate Industry 09 NewHeaven Lighthouse 010 55°58’.57” R=25 1.0 1.0 1.52.0 0.5 0.5 0.5 0.5 0.5 0.5 1.5 1.5 1.0 1.5 0.5 .5 1.5 1.5 1.5 2.52.0 3.5 0.5 0.5 0.5 0.5 -0.5 -0.5 -0.5 -0.5-0.5 -0.5 -0.5 -0.5 -0.5 -0.5 -0.5 -0.5 -0.5 -0.5 -0.5 -0.5 -0.5 -0.5 -0.5 -0.5 -0.5 -0.5 -0.5-0.5 -0.5 -0.5 -1.0 -0.5 -0.5 -0.5 -0.5 -1.0 0.00.0 1.5m 1.5 1.5m 1.5m 2.5 -1.0 -0.5 -1.0 -1.0 -1.0 -1.0 -1.0 -0.5-1.0 -0.5 -0.5 -0.5 -0.5 -0.5 -0.5 -0.5 0.0 -0.5 -0.5 -0.5 -1.0 -1.0 -1.0 -1.0 -1.0m -1.0 -0.5 -0.5 -0.5 -0.5 0.0 0. 0.0 0.0 0.0 0.0 0.0 0.0 R=35 R=25 Albert d. Wa reh ouses Water Cycling Centre Imperial Dock Grain Silo SwingVictoriaBridgeTowerForthSub-stationplaceports NewHeaven Lighthouse Corn BuildingExchange 02 04 05 09 010 55°58’48” 55°58’.57” 76 77 The project envisions how Edinburgh is being prepared to be “sustainably flooded” – There’s a shift thanks to the flooding- Harvesting the seaweed would be literally from around the building. By 2050, much of Leith - the port district of Edinburgh - would be submerged by rising sea levels due to increasing global temperatures. Leith, Edinburgh 2050 rising sea levels forecast 7.1








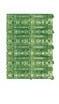
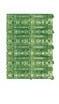








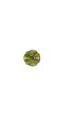


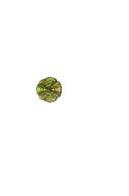
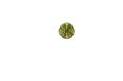
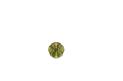
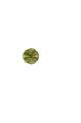
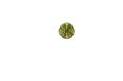
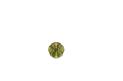

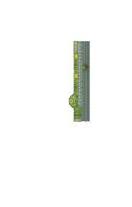

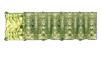
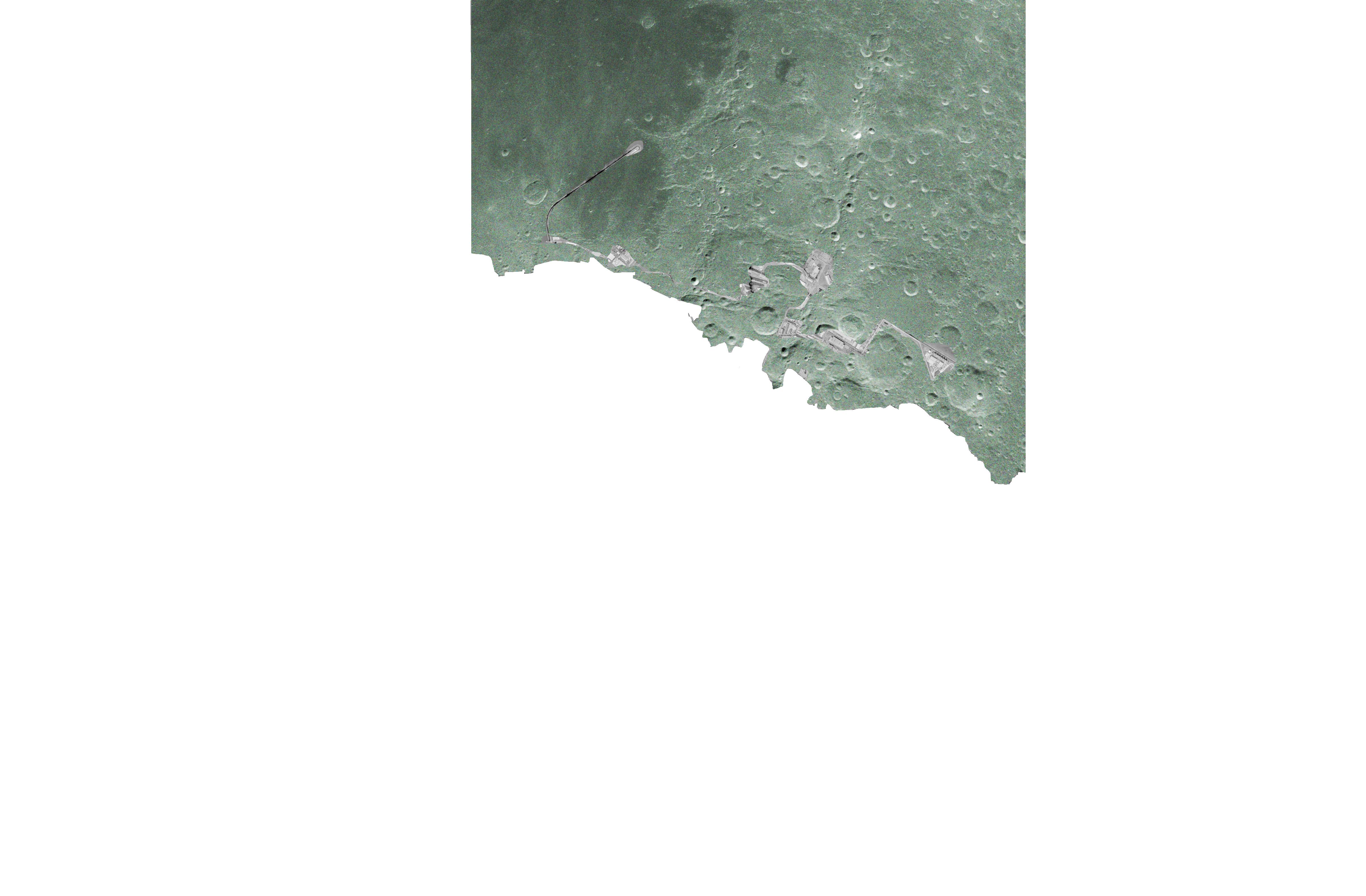


Isometric view Old city of Edinburgh via water of Leith to Leith industry area and docks
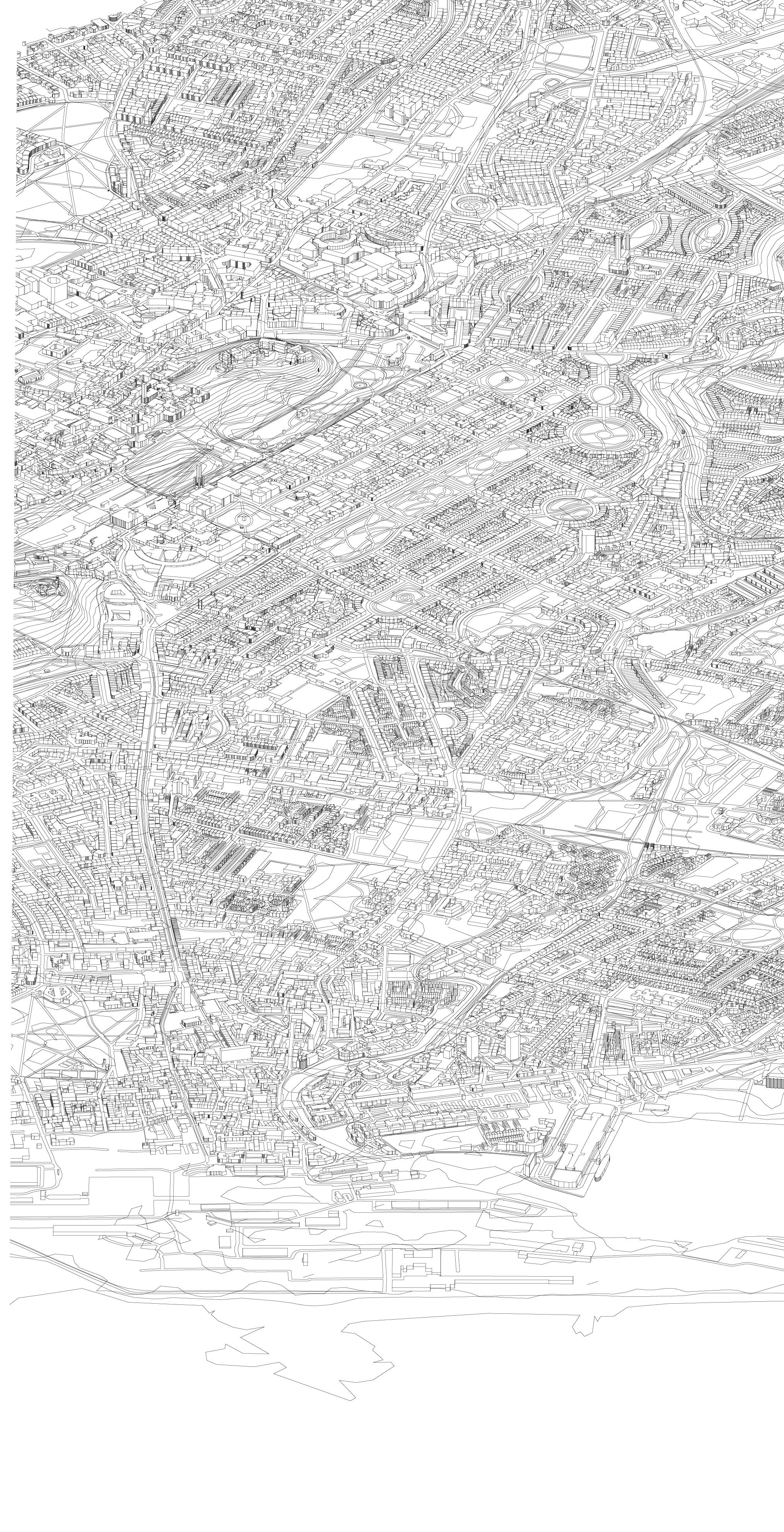
The project works with the accepted predictions of the flooding forecast and would prepare the building for flooding, suggesting cyclica system – starts and ends in the sea.
and wood scraps storage, and it is completely abandoned.
A group of early to late 19th-century gasworks buildings, and the Corn exchange building adjacent to it, would be the place for developing a new industry and testing the capabilities of the todaysiteThematerial.seaweed-basedformergasworksisformingayardusedasmetal
Post1853-1890Gasworks
plan

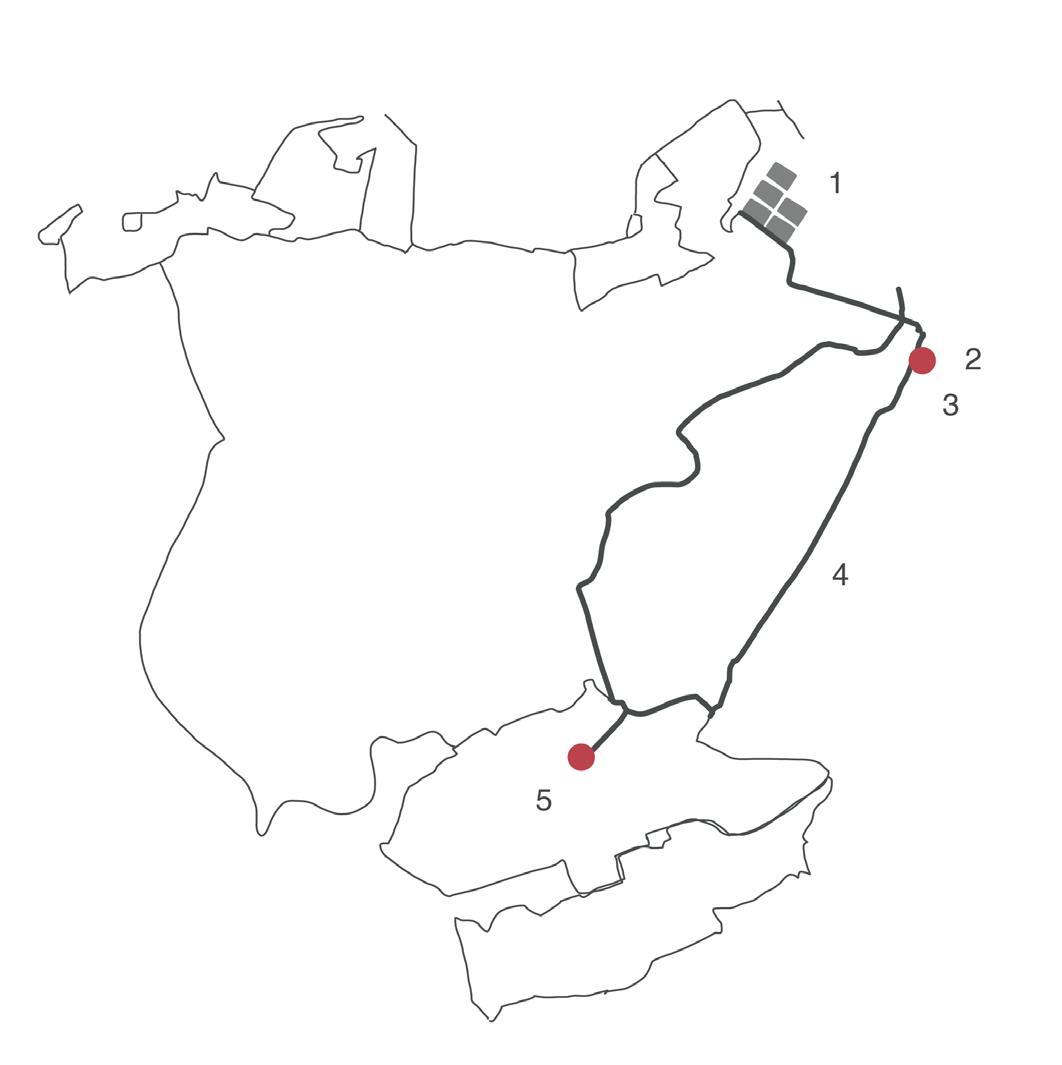
Cyclic cleansing system

The water of Leith conservation thrust, the council of Edinburgh, nature Scott, SEPA, and forth ports published a detailed plan towards the flooding predictions “ Leith management plan of 2020-2030.”.
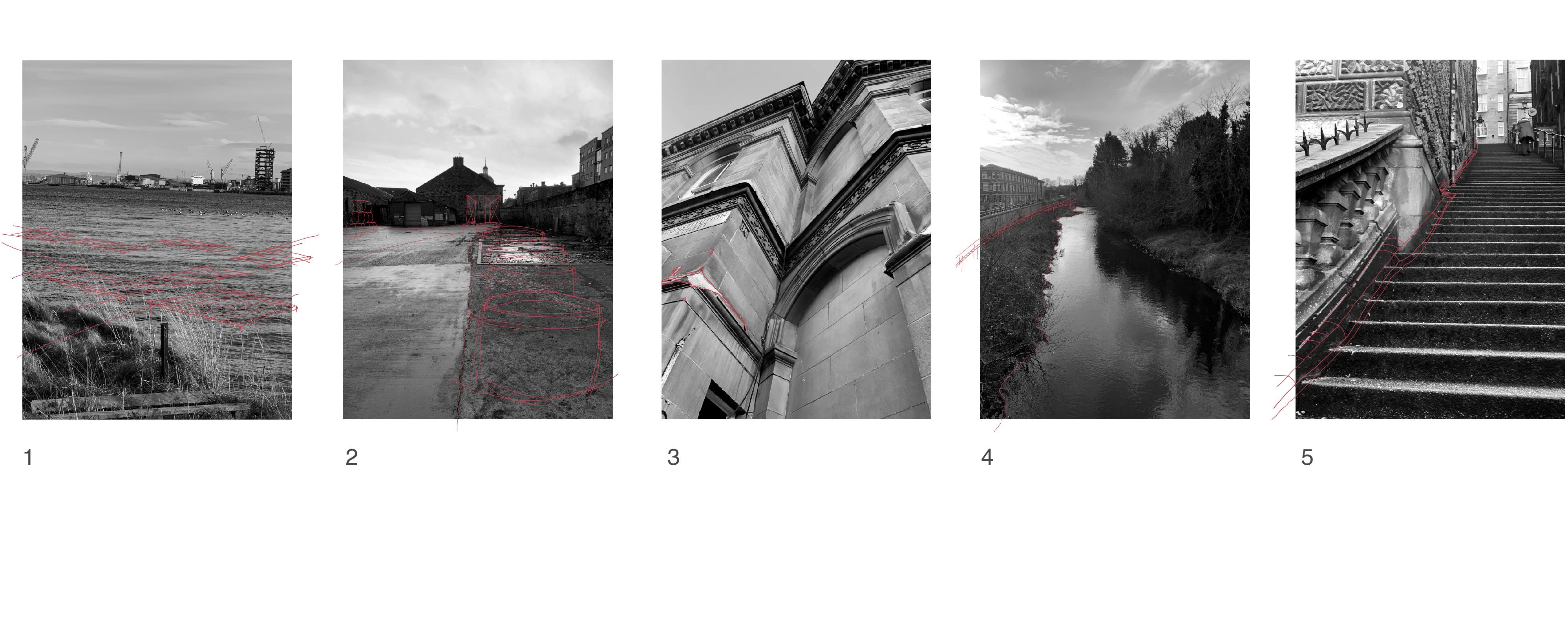
Master
Gasometer HouseA 1 B 2 C 3 4 D 65 Remains of early works Site of Gasometer House Development of pre-1853 period Retort House Offices Chimney
– is an important, rare, tangible reminder of the industrial history of TheLeith.”project would use the yard to be a place for the applyingprocessing,industry21st-century–harvesting,andtheseaweed
Leith Gasworks station0 25 50 m 7.2
Thecompound.yardwould be the industrial place for processing and applying the material. Over time, as the building would continue to deteriorate, more and more parts of the building would be replaced by the seaweed material. This
process, in fact, would prepare the building for flooding. The yard would use as a way to handle projectrisingchallenges21st-centurysuchassealevels.Thedemonstrates a system that is examined on a building in Leith but could also be applied in any other place in the world that is under threat of flooding.
Corn Exchange buildingPlan
78 79
The project aims to connect to this plan, specifically tackling the flooding issue –“To manage the river to minimise flood risk and reduce the impact of flooding whilst mimicking natural flow variations.”
The site today is at risk and found in asindividualgasworks“Thereports,Indeterioration.continuousoneofthesiteitiswritten,remainsofthe–bothbuildingsandagroupofbuildings
Corn
80 81
exchange building and Former Gas stationIndustrial Heritage of Edinburgh 7.3
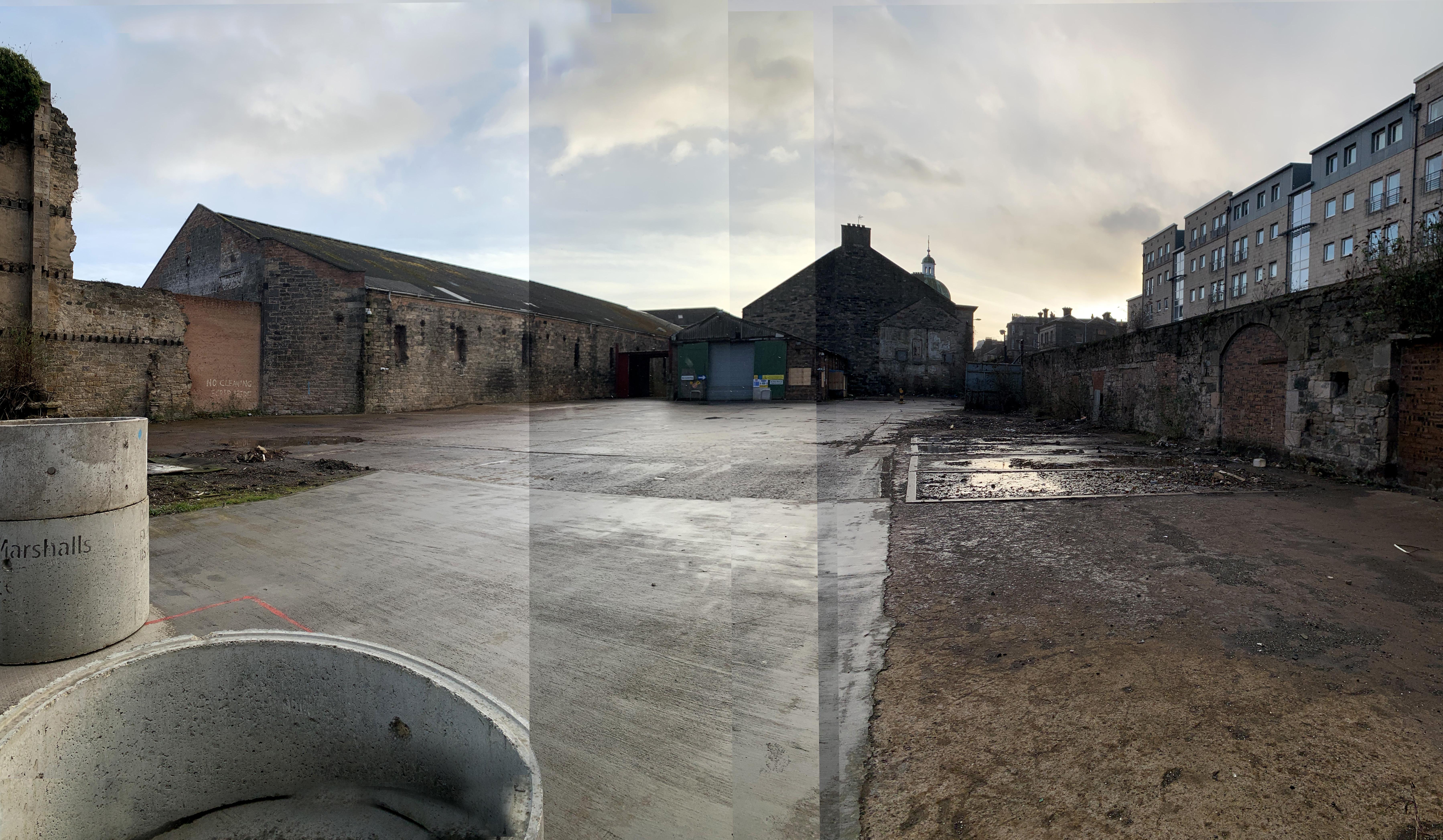
Sea Level
Leith's Baltic st gasworks opened around 1825, then a separate town from Edinburgh, and undergone a lot of changes and adaptations over the years.
The Southern border of the yard is the Corn Exchange Building built in 1861, used as a hall for grain merchants to exchange their goods.
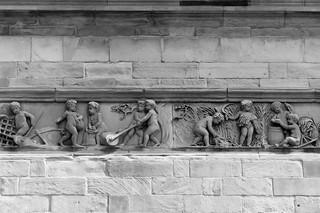
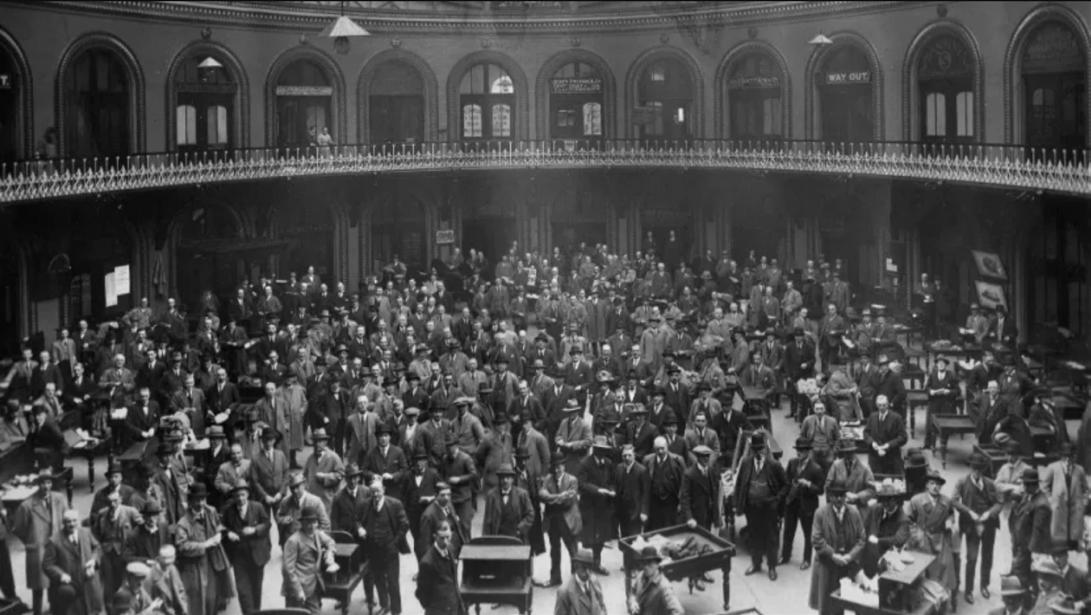
The historical and architectural interest of the gasworks in their current form as a group is a very rare survivor for this industrial building type in such a wide range. They are an important reminder of an industrial process that is now largely redundant.
Some of the buildings have been reduced in height, and formed an area now appearing as a courtyard, enclosed by tall boundary wall that has also been altered at various dates.
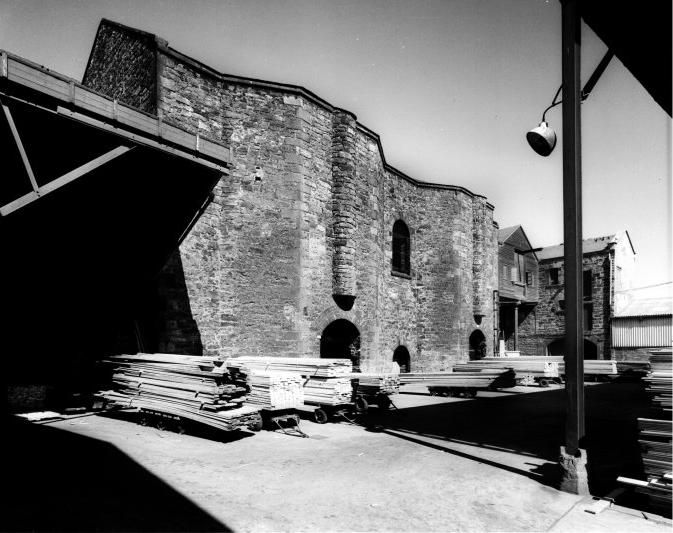
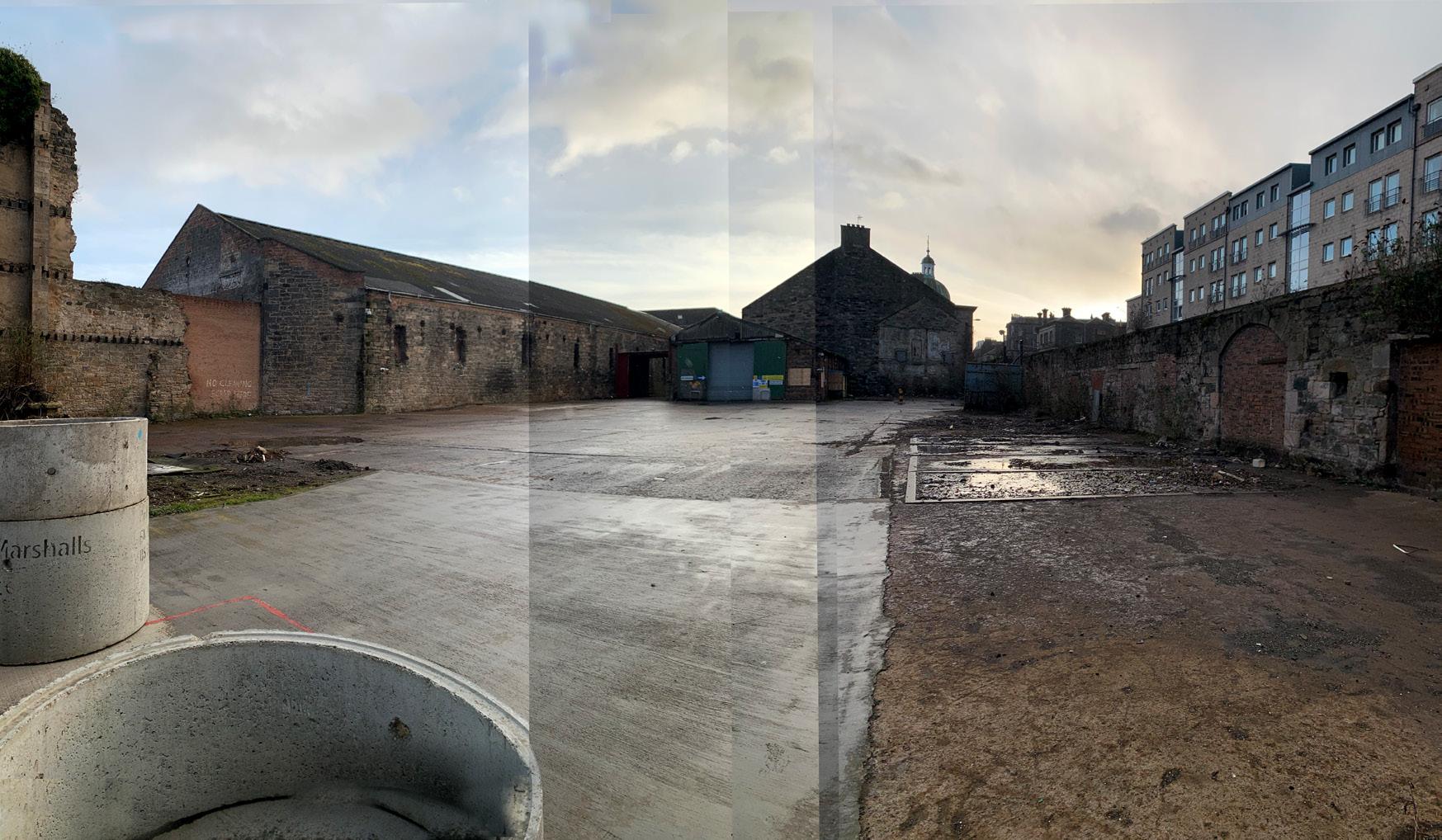
Today, the gasworks buildings are using for storage of metal and wood scrapes, mostly abandoned and deteriorating, and at March 2019 announced as at risk.
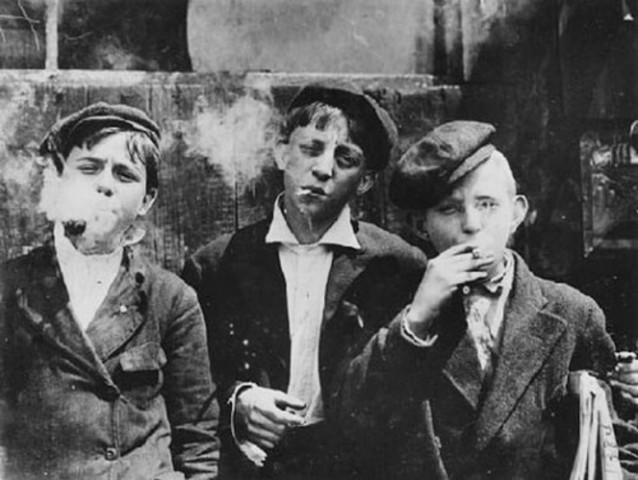
The gasworks site and the corn exchange building are a unique remnant for the trade and the industry and labor of the 19 century in Leith.
It was operated as a gas works until around 1906, and was latterly used as a sawmill and timber merchants.
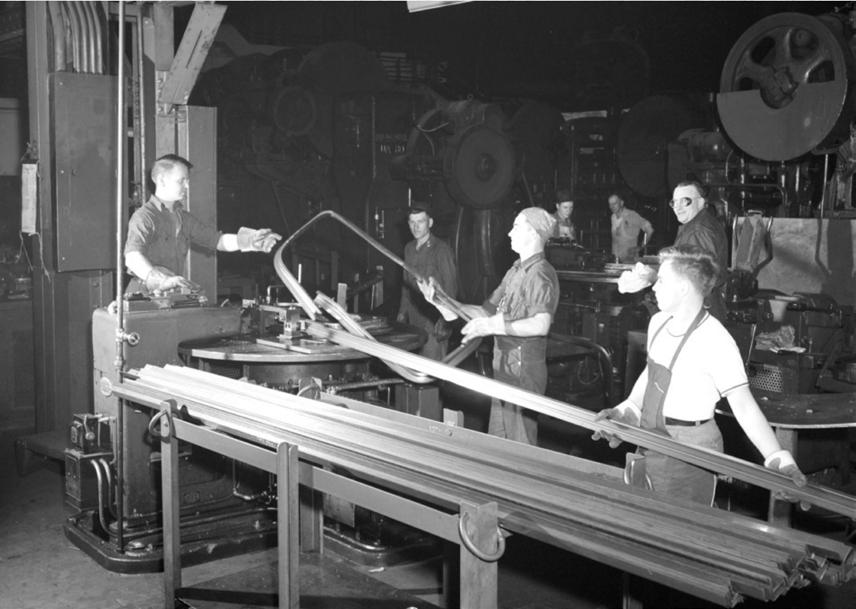

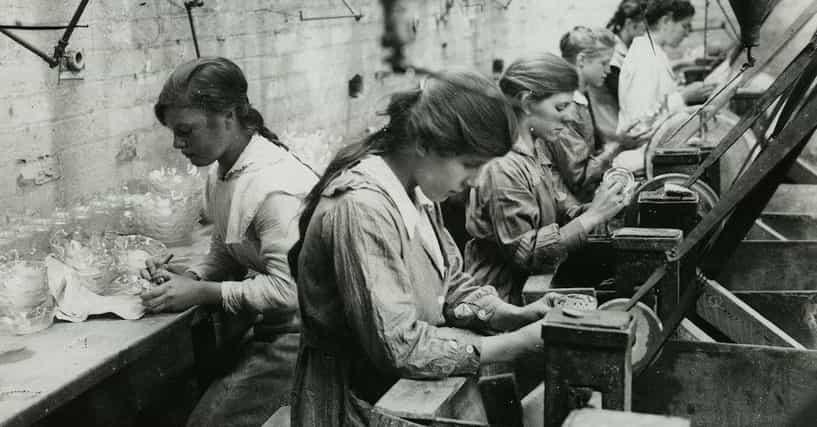
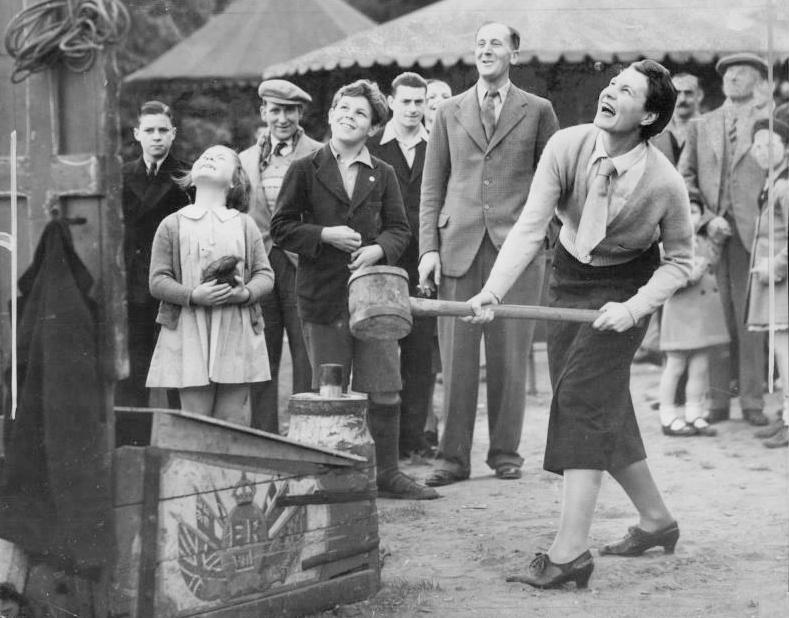
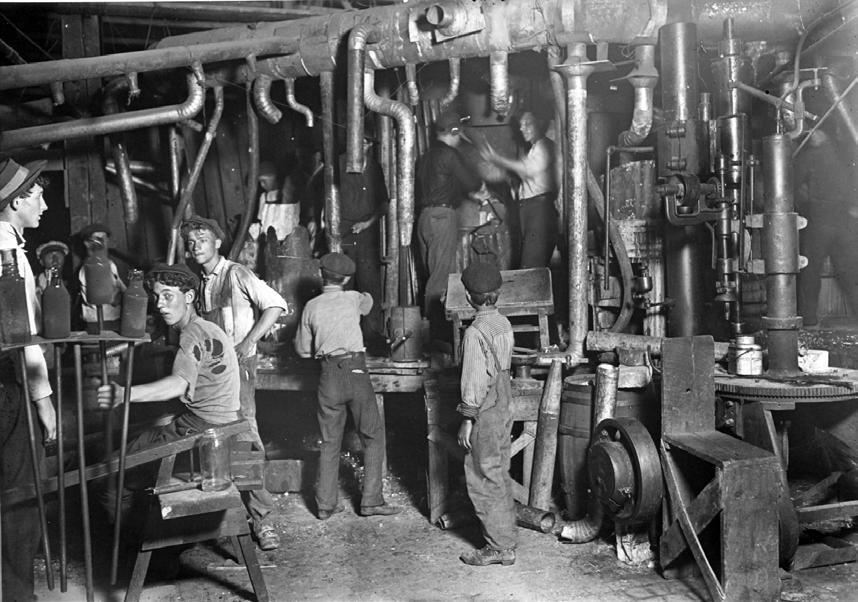
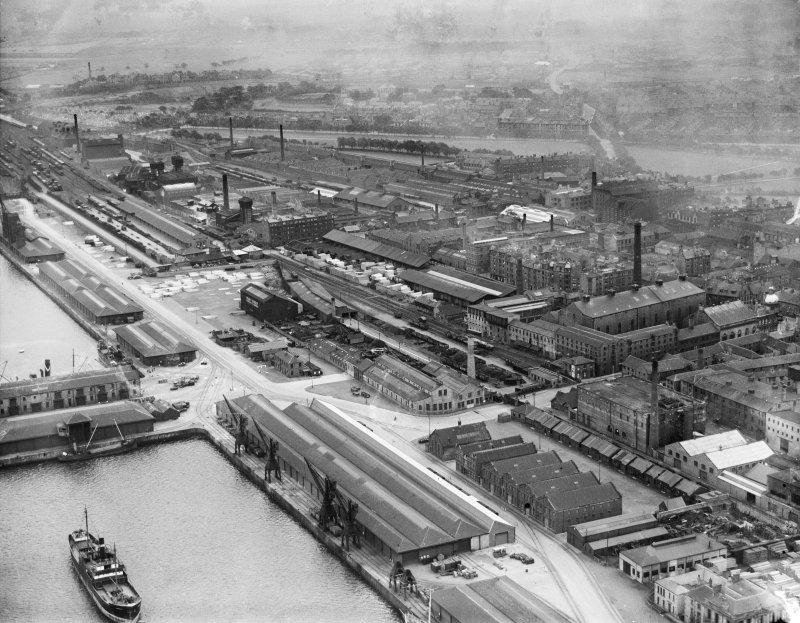
Sea Level 1825 1861 1906 20222019 2030 2050 823708 110.61 3.81 4.02 0.54 1.31 0.92 4.90 1.31 3.32 5.18 6.19 7.99 9.4310.17 3.10 4.19 2.60 4.33 8.48 9.08 10.17 13.31 19.35 6 1 4 1 7 0 2 2 2 0 9 5 9 2 1 3 7 6 8 0 9 2 0 0 6 1 5 2 1 0 8 1 4 2 1 4 0 7 2 1 9 3 1 4 0 3 2 0 2 3 8 8 4 1 8 1 3 7 5 2 1 1 6 2 0 936 110.19 4.46 888835544 13.31 82 83 Historical Survey Former Gasworks Station, Corn Exchange Building West Constitutionelevationst Balthic Gasworks station Timeline “The remains of the gasworks – both individual buildings and as a group of buildings – is an important, rare, tangible reminder of the industrial history of Leith.” 7.3
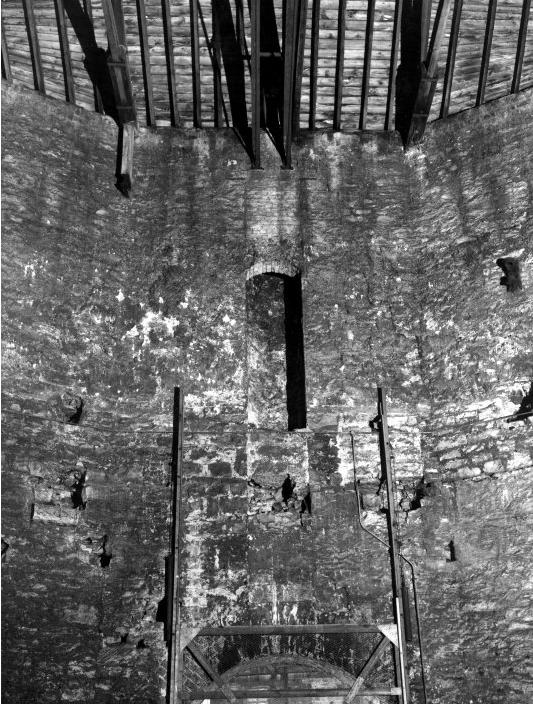
North-west elevation: 4-bay office block to right with doorwayopenings,arcadedsecondarytoouterright.
Top stage sidesrectangularcapitalswindowsround-archedwithbipartitewithfoliatesetinrecessedpanelsto4
22 3 4 5 7 10 11 12 13 14 15 16 17 18 19 20 21 22 23 24 24 25 26 27 28 29 30 31 32 33 3 4 5 7 10 11 12 13 14 15 16 17 18 19 20 21 22 23 24 25 26 27 28 29 30 31 32 33 4 6 9 1112 1212 22
The site operated as a gas works until around 1906, and was latterly used and primarilyadpatedasa saw mill and merchants.timber
5-bay hall to left with carved frieze (John Rhind) of putti in grain-related activities and eaves cornice. openings.andround-archedMoulded,keystoned Centre bay with cills.brackettedwithwindowstallrightbaysfanlight.elongatedwithdoorwaytall2towith 2 bays to left palcast-ironcornice,abovearsemi-circulsmalldoorsboardedwithdoorwayscornicedandarchitravedrectangularlargewithandfanlightsstones. 26 232325 27 28 29
The elevationwest can be toandalterationsevidencedisplayssiteoutsideviewedpartlyfromtheandlessofchangesopenings.
The elevationwest has at least latticecastdecorativeremainswindowsblockedfourwithofirongrilles.
Entrance tower: engaged octagonal 3-stage entrance tower; 1st and 2nd stage detailed as above with doorway to centre, 2-leaf panelled door and plate glass fanlight, consoled cornice blank arches to outer bays.
The blocked).(somewindowssixfloorfirsthassingle wallheadThe is capped by a later, cornice.projectingplain
dressings.somewithcoursedsandstoneandsquaredcoursedmaterialsconstructionPredominantincludeandcreamgreyandrubblebrickinfill,droved
GHFEDCBA GHFEDCBA 182836 110.61 3.81 4.02 0.54 1.31 0.92 4.90 1.31 3.32 5.18 6.19 7.99 9.4310.17 3.10 4.19 2.60 4.33 8.48 9.08 10.17 13.31 19.35 1 4 1 7 0 2 2 9 5 2 1 3 6 7 6 2 0 0 9 1 8 5 6 0 6 2 1 6 8 9 2 3 2 1 0 7 1 4 6 3 1 4 0 7 3 8 2 2 1 4 2 4 1 8 1 3 7 5 1 3 2 92 110.19 4.46 888835544 13.31 84 85 Existing Site Former Gasworks Station, Corn Exchange Building West Constitutionelevationst 7.4
Paterae frieze and bracketted eaves cornice; wallheadmetaloctagonalclassicaldomedroofwithstackto rear and octagonal domed bellcote openingsround-archedwithand ornate weathervane.
West northwestand ranges buldings date to before 1853 The inhavealteredrangessurvivinghavebeenandsomebeenreducedheight. The varioushasboundaryenclosedcourtyardbytallwallthatbeenalteredatdates
The west range is a long and prominent former gasometer house (reduced in height from four storeys approximatelyto two)
The interior is a mixture of relatively recently fitted and commercialsubdivided and industrial units, some operating as retail units and others as stores, warehousing or workshops.
It is places.brickwallheadwithdressedrubblefromconstructedmostlysandstoneandstoneabrickandinfillsin The gablenorthhas the remains of a openingarchedsegmental-stoneand a taller groundopeningarchedbrickatfloor.
The process starts in 2022 and will finish when the building floods (between 2030 to 2050).
The frieze carved by John Rhind designmainandgrain-relatedsculptureEdinburgh-basedanofactivitieseavescorniceistheinspirationfortheaesthetic.
The windows on the possibilities.material'sofonefacadewestareexamplethe
The gradual and constant repair of the building would eventually create more and more "seaweed"
From this perspective, if the 18th-century trade was grain a land-based resource, is 21st-centurythetrade is seaweed? ocean-basedanresource?
The andwouldwestopeningsblockedattheelevationbeopenedre-used.
The symbolizesbuildingexchangecorn a gathering space for grains.tradeandmerchantsfarmerstotheir
Using propertiesthe of the materialtranslucencyits and its good capability to attach differentwindowoperatesurfacesroughitwillasawithranges of light coming into the space.
When significantfloodedparts of the building would already replacedbeby the biodegradebuildingThiscompound.seaweedway,thecouldand go back to seaweed'sthe originsback to the sea, back to nature.
22 3 4 6 7 6 8 9 10 11 12 13 14 15 16 17 18 19 20 21 22 23 24 24 25 26 27 28 29 30 31 32 33 3 4 6 7 8 9 10 11 12 13 14 15 16 17 18 19 20 21 22 23 24 25 26 27 28 29 30 31 32 33 4 6 6 9 12 22 26 232327 28 29
Thisparts.repetitive process and maintenancecontinuouswould give the building a new aesthetic while keeping Renaissance decorative details from the late 18th century that could see from Constitution street.
The elevationwest has at least latticecastdecorativeremainswindowsblockedfourwithofirongrilles.
GHEDCBA GHFEDCBA 2022 2025 2030 2038 2045 2050 70631 110.61 3.81 4.02 0.54 1.31 0.92 4.90 1.31 3.32 5.18 6.19 7.99 9.4310.17 3.10 4.19 2.60 4.33 8.48 9.08 10.17 13.31 19.35 1 4 1 7 2 0 2 2 8 1 2 5 1 9 2 1 3 7 6 2 0 0 9 4 5 6 3 9 0 8 1 4 2 1 4 0 1 2 1 7 1 4 6 1 4 0 7 2 1 1 5 0 1 1 7 2 0 2 4 1 8 9 1 2 2 1 2 9 5 1 1 6 1 2 2 0 92 110.19 4.46 888835544 13.31 86 87 Preparing the Building for the Flooding Former Gasworks Station, Corn Exchange Building West Constitutionelevationst 7.4
The material can "break" the shape of the window and continue to grow beyond boundariesits - loyal to the aesthetic.material's
The material would attach to elementsarchitecturalothersuch as columns and walls and could use as a filler, as an insulator, or to demolishedrestore parts of the building.
New seaweed walls and columns are emerging from the stone wall. Robot room Space applicationsposibilitiesexperiments:forforof the material improvingandthe mix.
Working with the slow deterioration Gas stations in the years up to the flooding– parts of the existing building would gradually be replaced with the material.seaweed-based
The reversibility and temporality of this maintainingenablesmaterial a building without hurting said.building"authenticityhistorical"destructionavoidingmaterialsexistingandtheoftheoftheasRuskin
GHFEDCBA GHFEDCBA 2022 2025 2030 2038 2045 2050 88 89 Reversible Maintenance - Seaweed Factory Former Gasworks Station, Corn Exchange Building West Constitutionelevationst 7.4
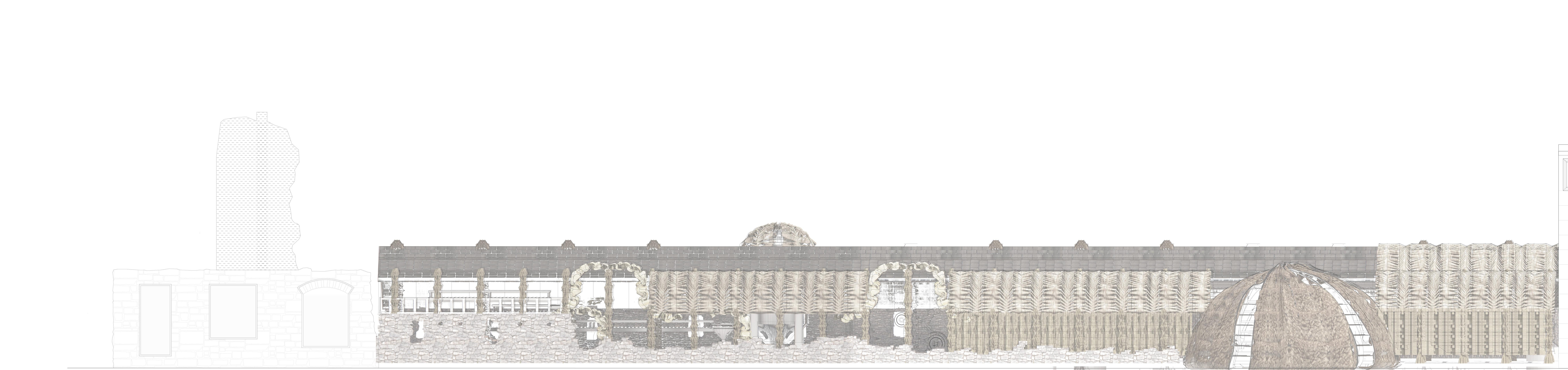
Parts of damagedtheroof are being replaced with translucenciesdifferentthankstheinsertskylightsseaweedandlightintofactory,tothe of the material. Each skylight is made from componentsfew that assembled by heating welding.material,thelike
The western wall of the building that has four deterioratedwindowsblockedandwalls, is partly replaced.
11 4 5 6 7 3 3 8 9 10 11 12 13 14 15 16 17 18 19 20 21 22 23 24 24 25 26 27 28 29 30 31 32 33 4 5 6 7 8 9 10 11 12 13 14 15 16 17 18 19 20 21 22 23 24 25 26 27 28 29 30 31 32 2233 26 232327 28 29 4 4 55 5 63
Isometric view | The project shows how at risk-19th century-gasworks factory- is being refurbished and transformed to a 21st century-seaweed material factory.
90 91
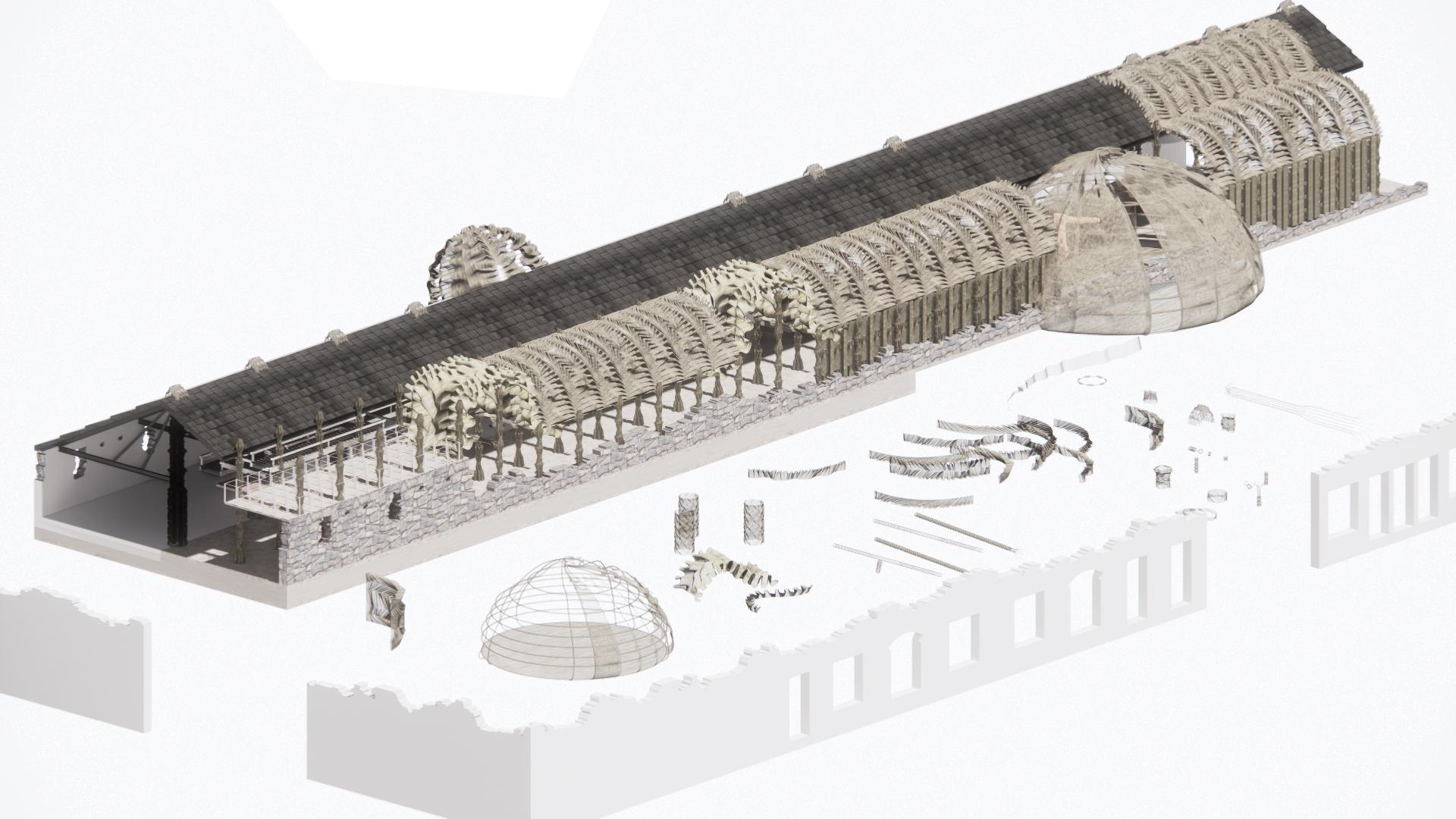
CHAPTER 08
Artefact Testing Applicabilitythe of the Material
8.1 Attaching the seaweed compound to other materials 8.2 Artefact - narrative and structure 8.3 Apply and assemble a system on site
The middle joint is a little wicker than the other two (marked in red), concluding that the depth and angles of carving have structural importance.
A-H examining different sections of the wood, creating a frame that could connect wood to itself and also hold the seaweed material in the best way B C1 C2 C3 D E1 E2 E3 F G H 1395 141062 151173 161284
Joints
Controlled and predictable to
Spontaneous and Unpredictable
Attaching to other Materials
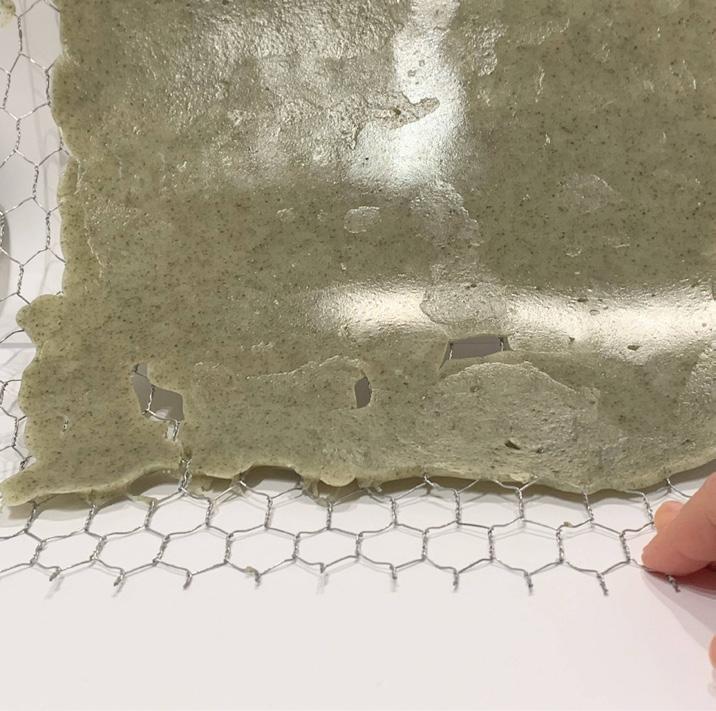
Controlled and predictable to Spontaneous and Unpredictable
material curate into a dense rectangular shape, exceeding the boundaries of the frame, and trickles between the carved wood.
The seaweed compound attached well to the wood pieces and tightly held them together. The rough and fibrous surface of the wood also helped the seaweed and the wood attach better.
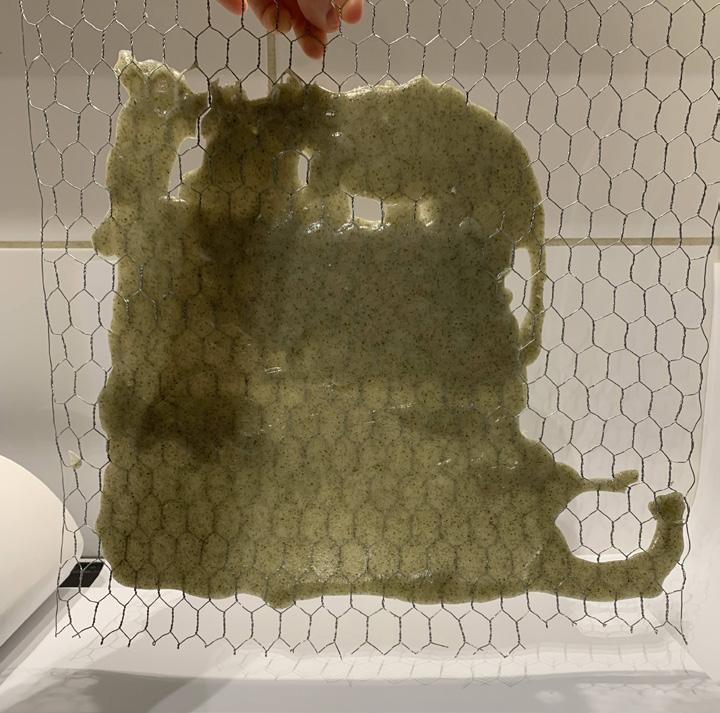
As the material would attach to existing materials on site, these experiments examine different joints in different techniques and aesthetics.

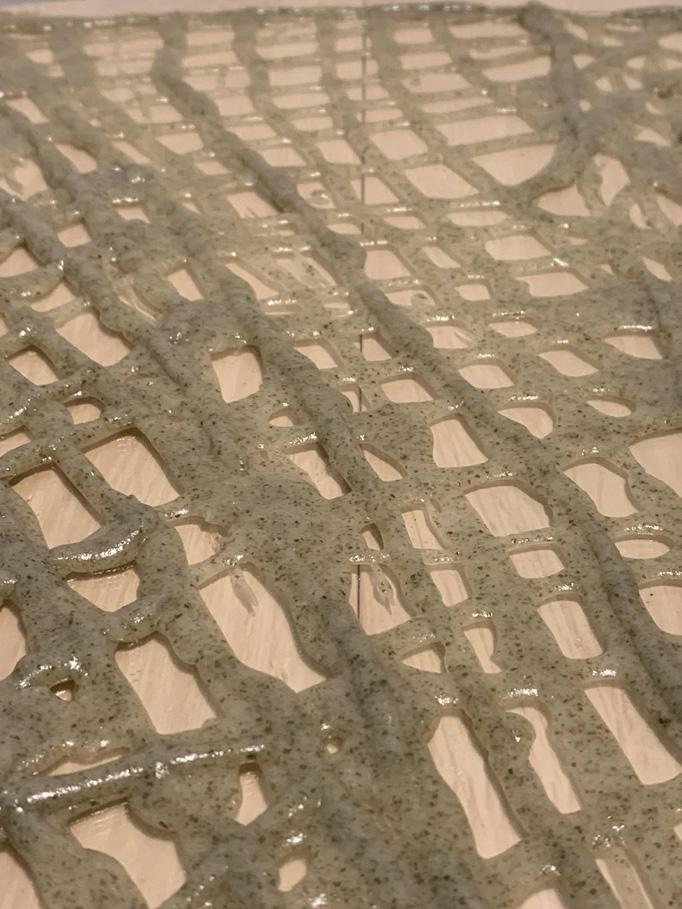
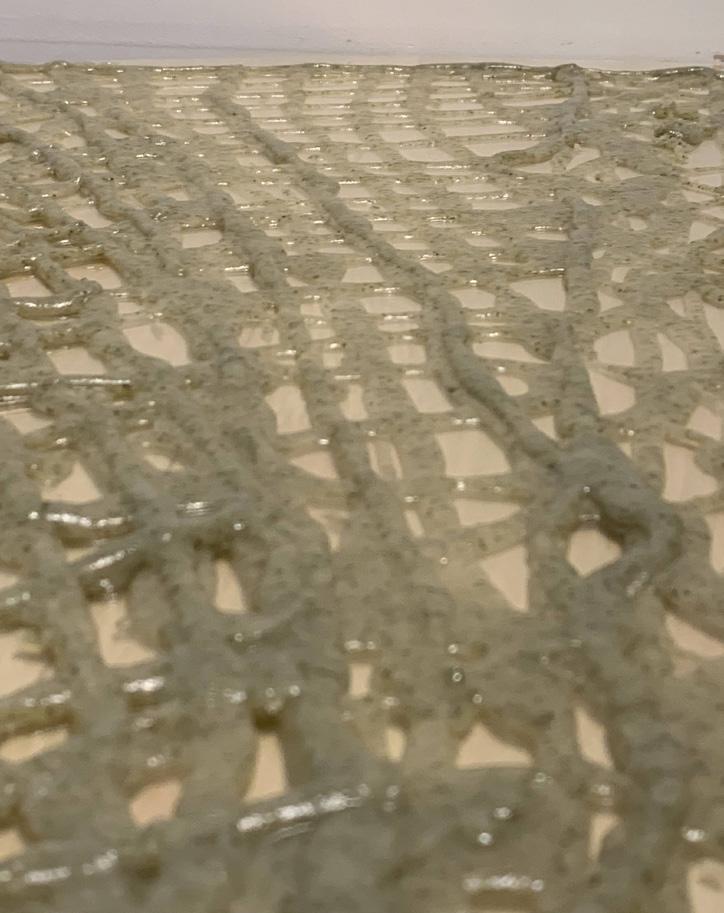
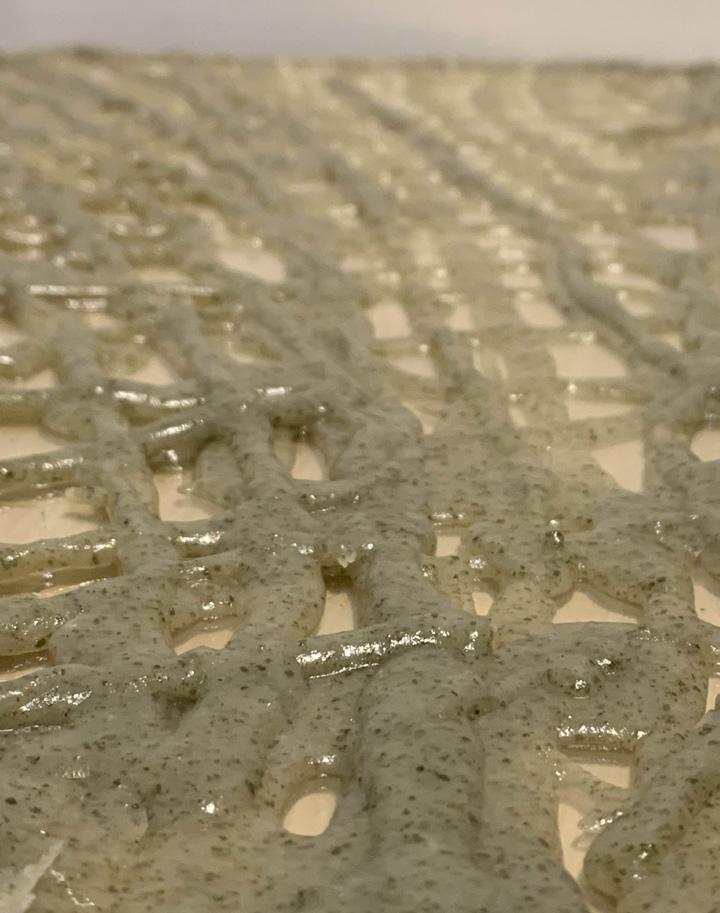

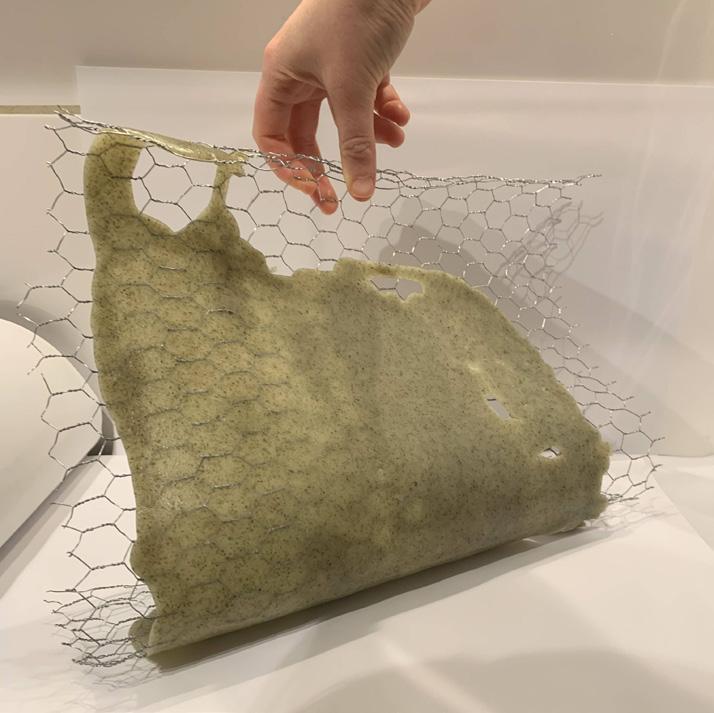

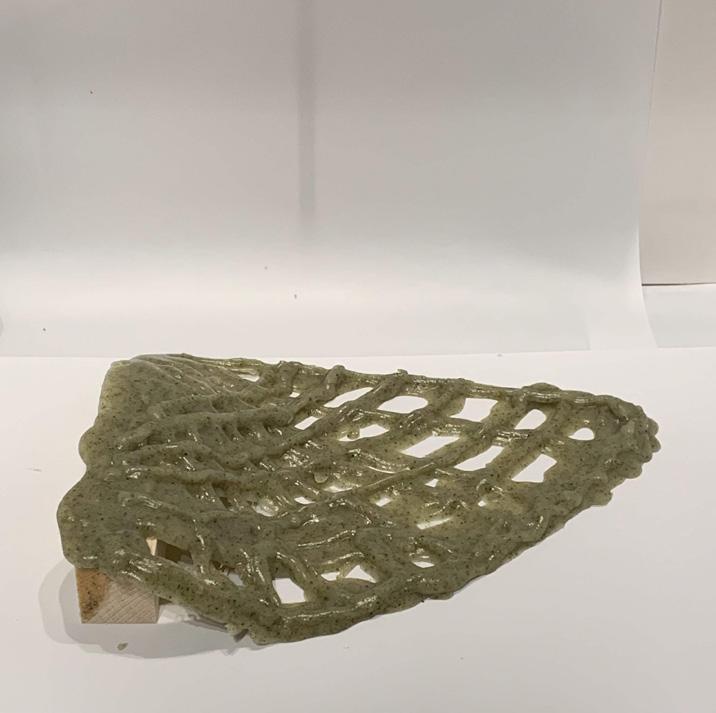
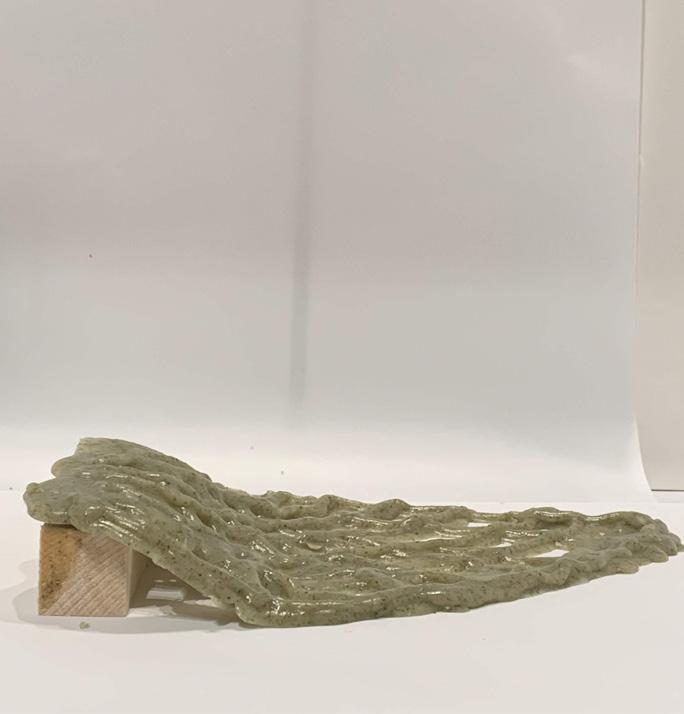
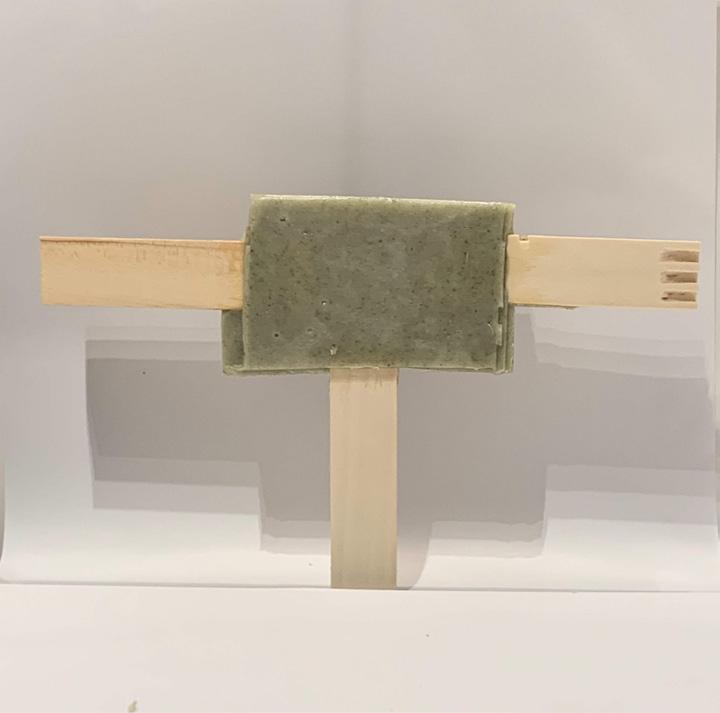
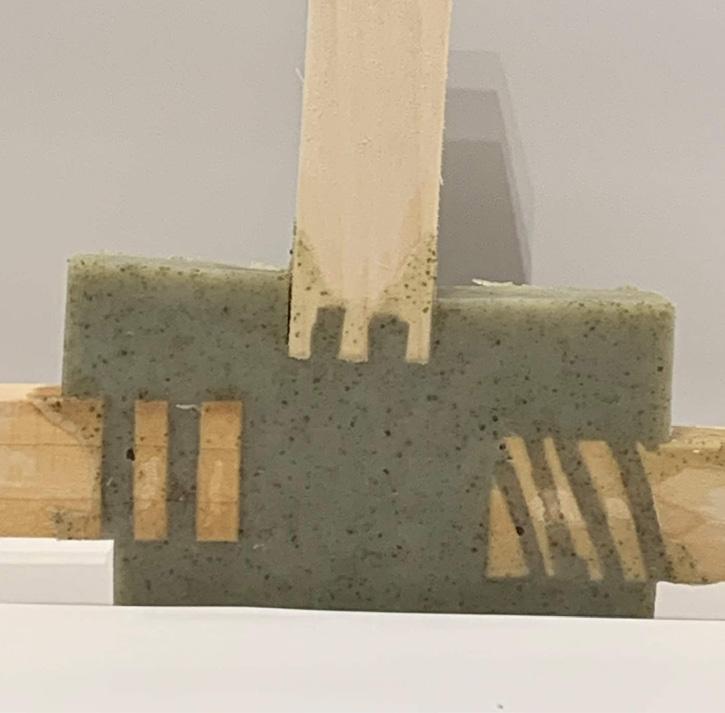
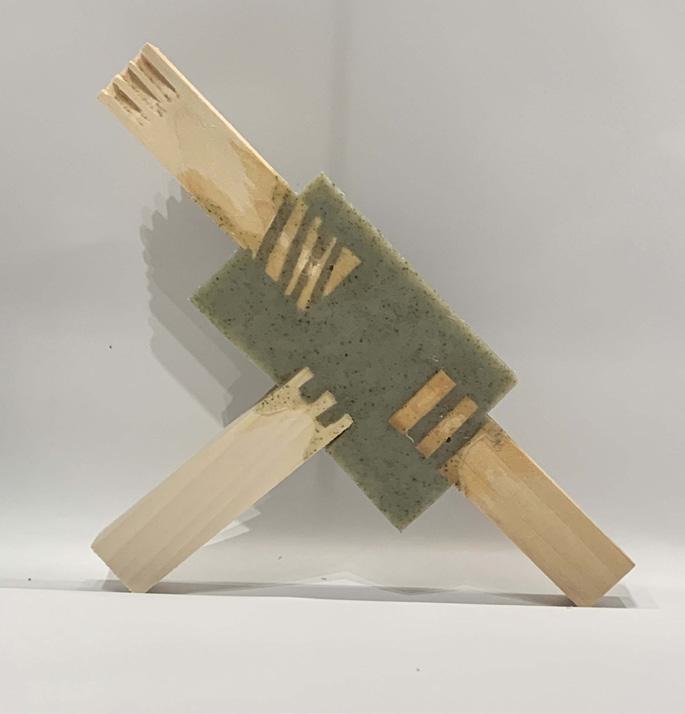
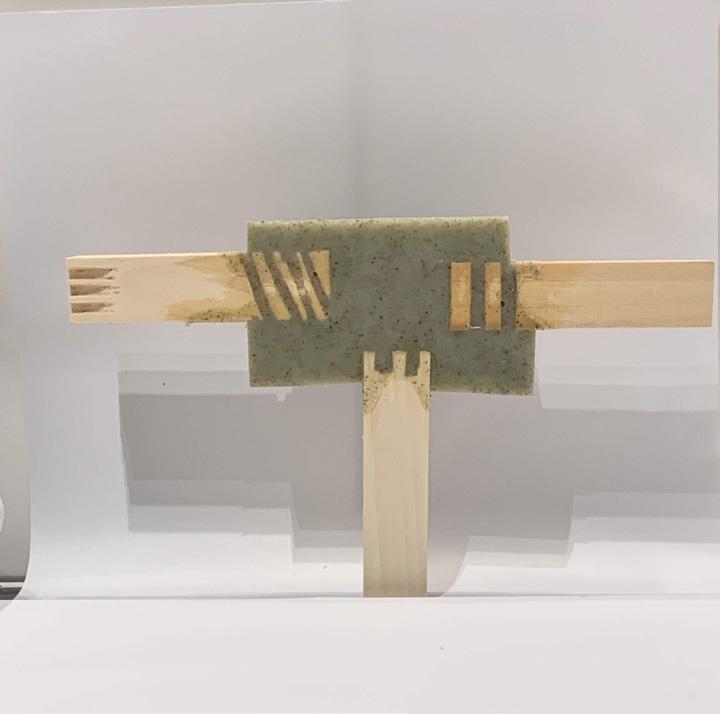
In the first experiment (images 1-4), the technique was casting the seaweed compound into a gap between three carved wood pieces. The
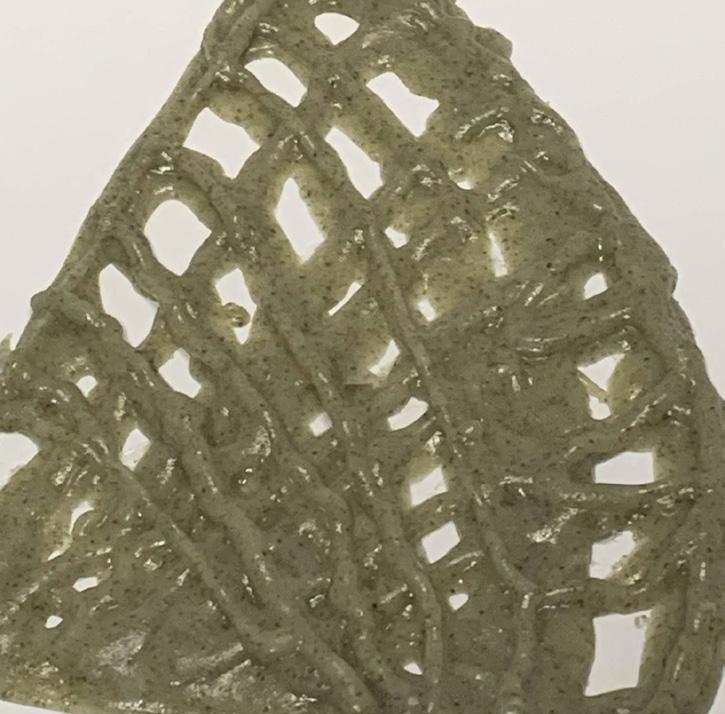

8.1
94 95 1 A
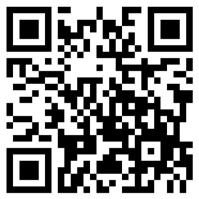
Narrative and Purpose 8.2
A detailed renaissance frieze on the façade of the Corn exchange building inspired the design of the pattern of the artefact.
96 97
Artefact
From a structural perspective, radial lines and crossing lines create a strong web. The lines spreading to the sides are penetrating into woodblocks like a piping system inside the wood frame. The wood bricks were numbered and held together in an inner structural reinforcing of an 8mm metal rod. The mould has been cut in a CNC machine.
The purpose of the artefact was to demonstrate how the seaweed compound is Theapplicable.design of the artefact is about its narrative and about its structure as one.

Artefact
demonstrates a formwork casting. The two halves of the mould are supposed to be compressed against each other, taking under consideration the thickness of the wall, and
8.3
then cast the material inside between them, creating a threedimensional shape. As the wood frame wasn’t stable enough, the material came into the woodblocks’ joints and couldn’t hold the surface. The holes need to be deeper, and the


TheApplicationmould
98 99
Apply and assemble a systemOn-site
frame must be stable. The material came out easily from the mould and created an accurate copy of the pattern. This experiment opens up new opportunities for casting and formwork methods on site.
100 101 Apply and assemble a systemOn-siteArtefact 8.3

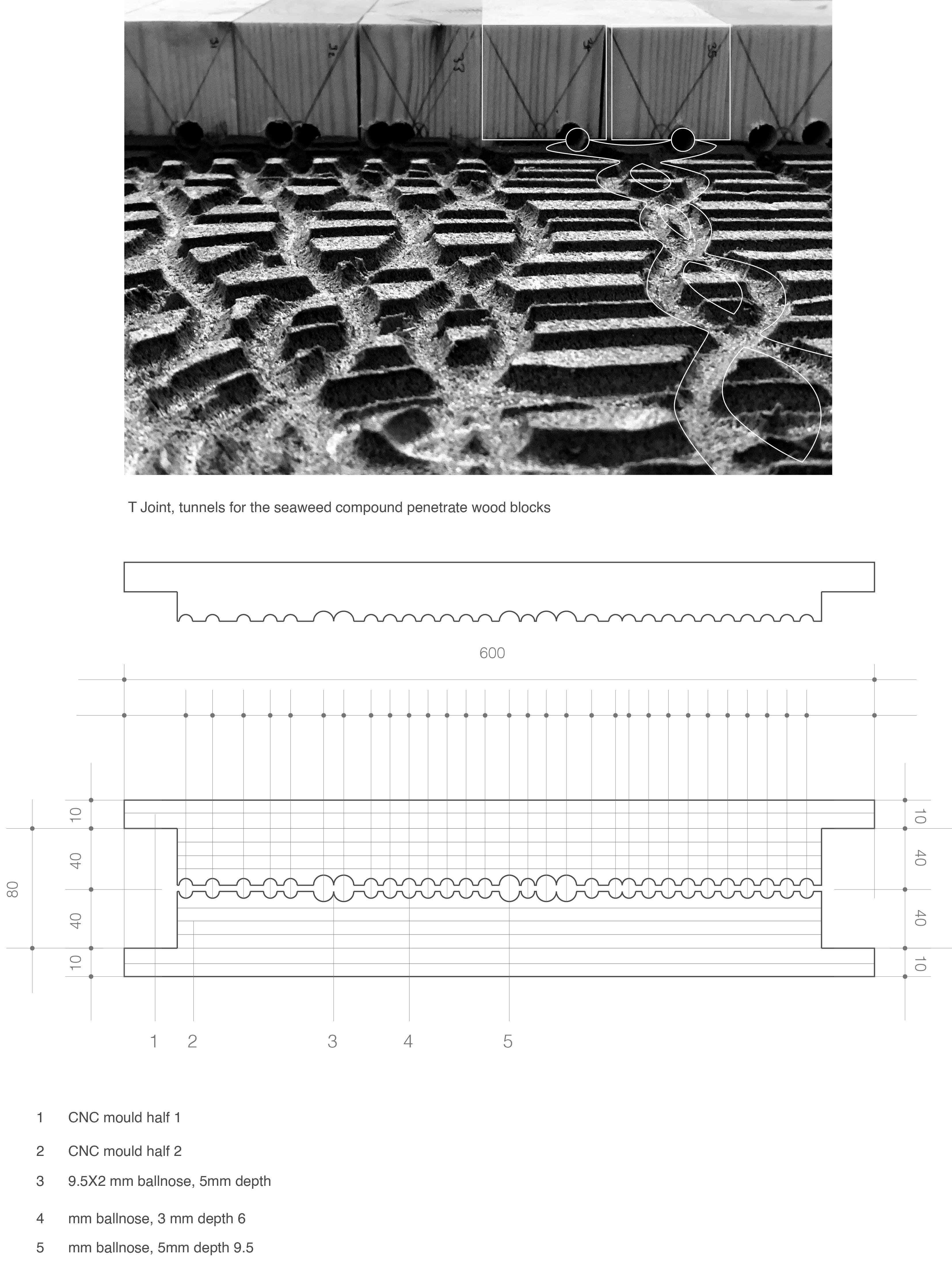
CHAPTER 09 Maintenance
The different material experiments that have been done so far are now directing the application in these scenarios. By that, the three scenarios are a culmination of all the experiments have done with the material. as for Design Between to
the controlled
the Random9.1SiteDamage Report - Mapping Opportunities for Design 9.2 Interpretation of material experiments to interventions 9.3 Refurbishing the yard - new industry 9.5 Details and application systems of the seaweed compound 9.4 Maintenance as opportunity for design
Working with the real damage report of the site (page 90) and planning within a building at risk. The necessity for maintenance in the site become opportunity for a new industry - the processing of seaweed compound as a new carbon negative building material. This is also an opportunity for new design for its specific aesthetic. From the damage report, three moments have been identified as opportunities to apply the material.
Opportunity
104 105 Site damage report Mapping opportunities for design 9.1
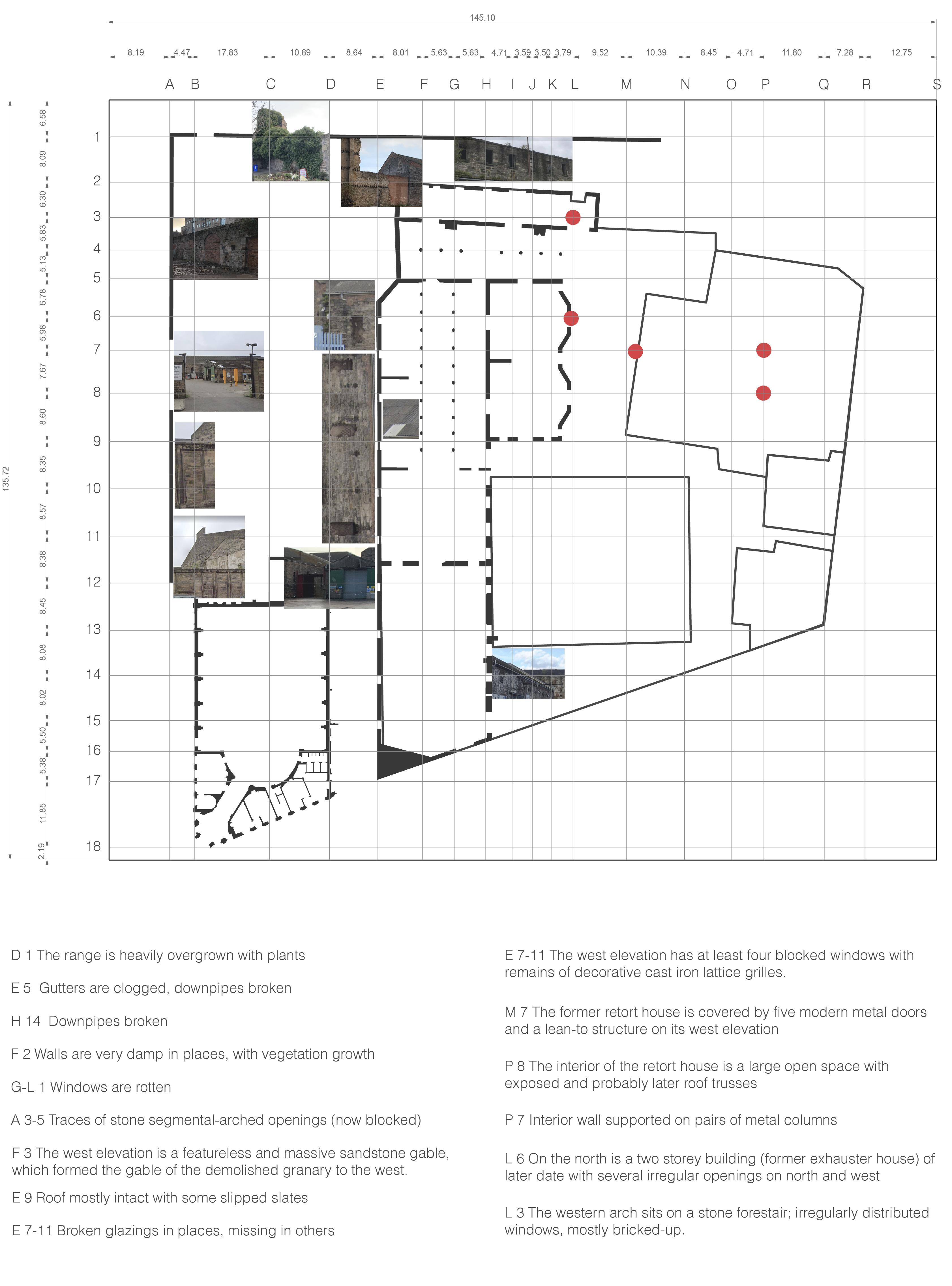
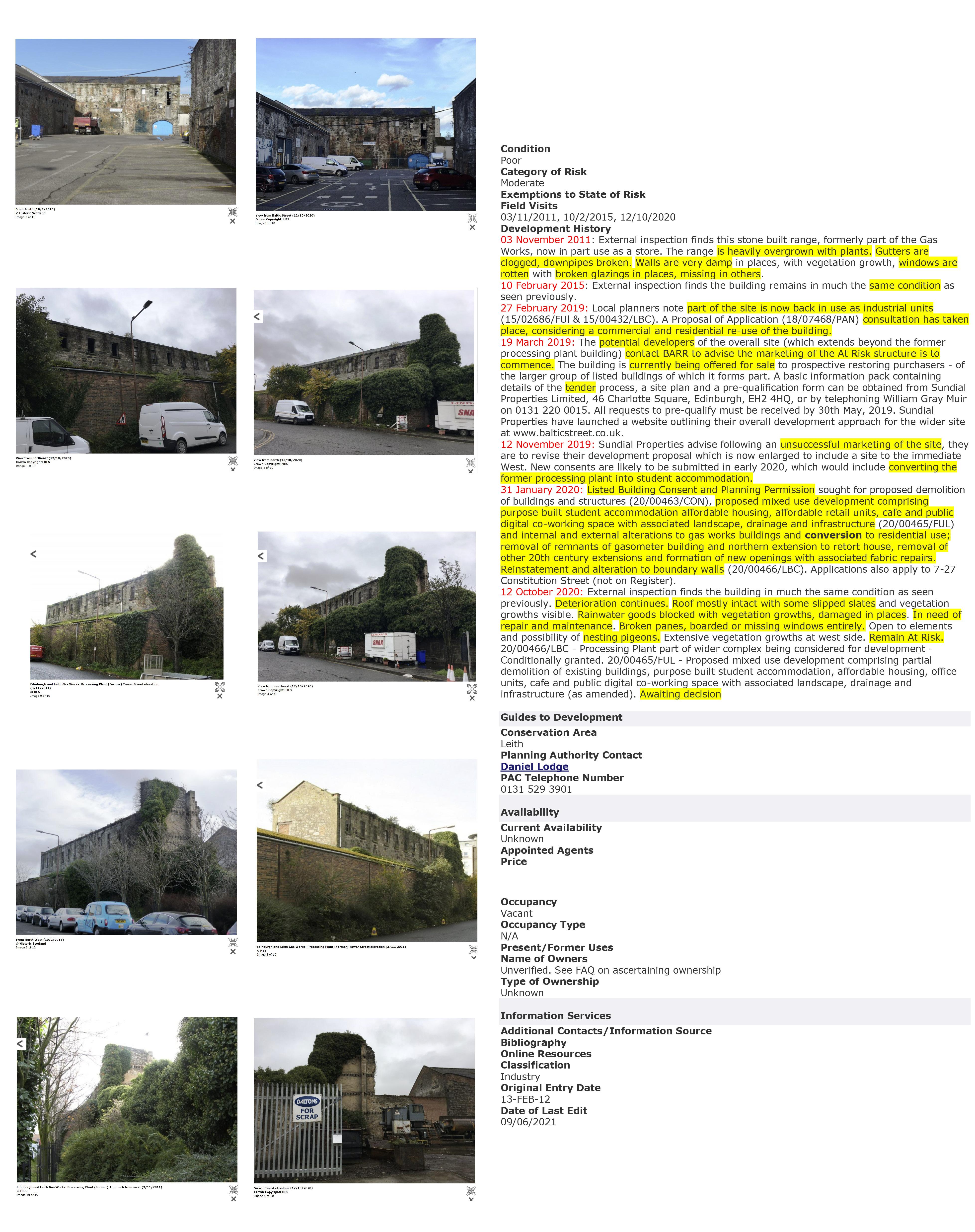
106 107 Site damage report Three Moments of New Design 9.1
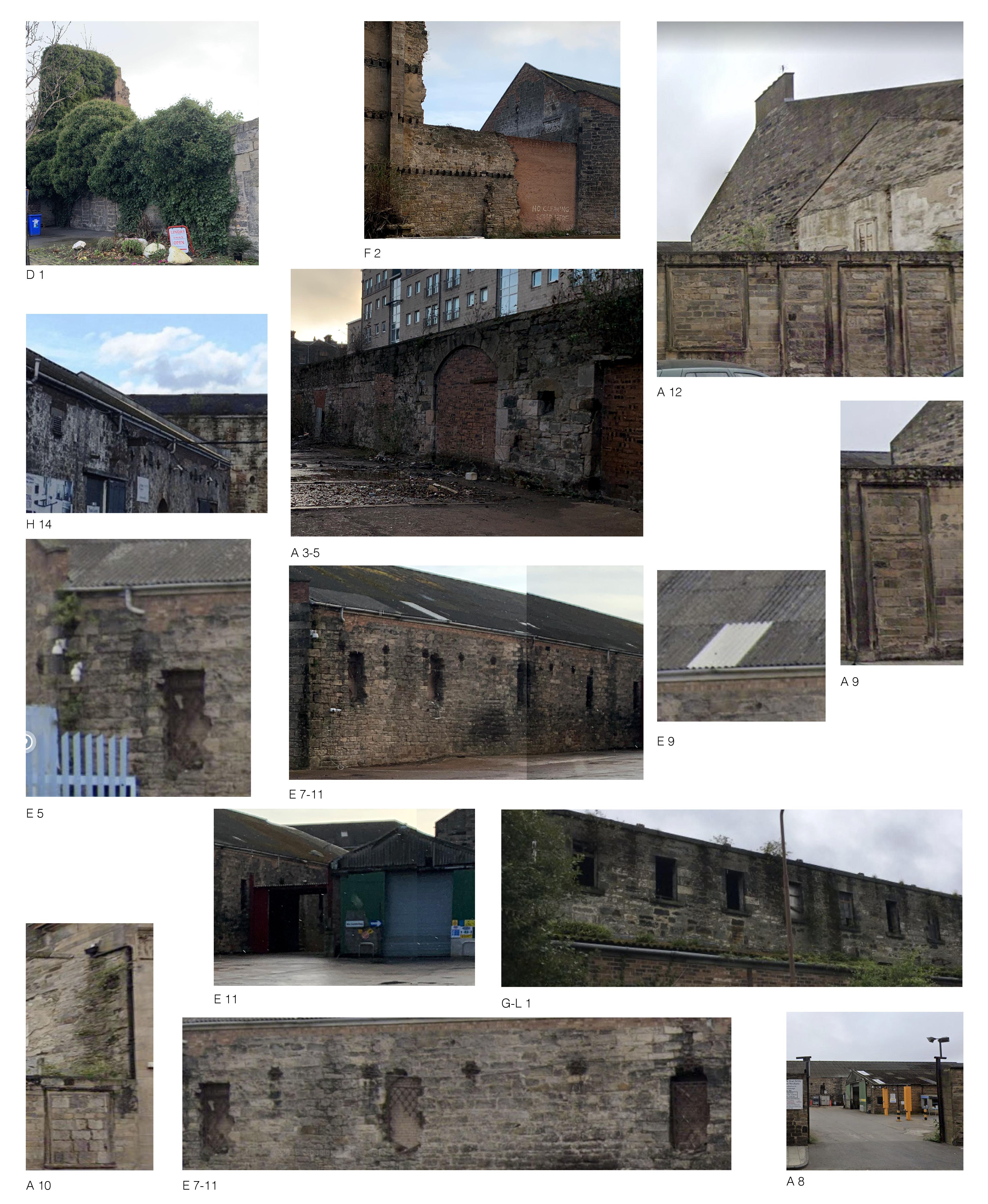
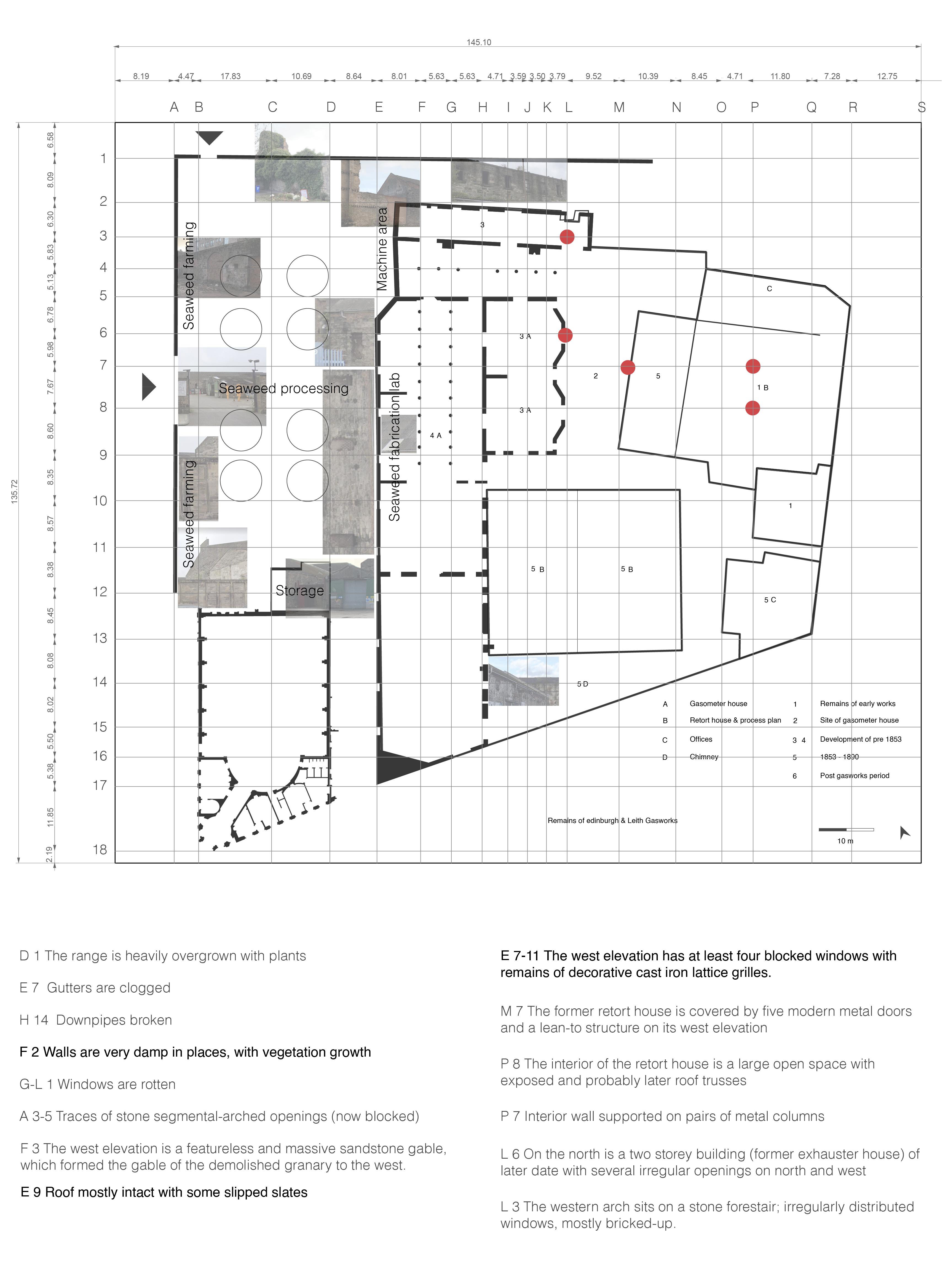
108 1099.2
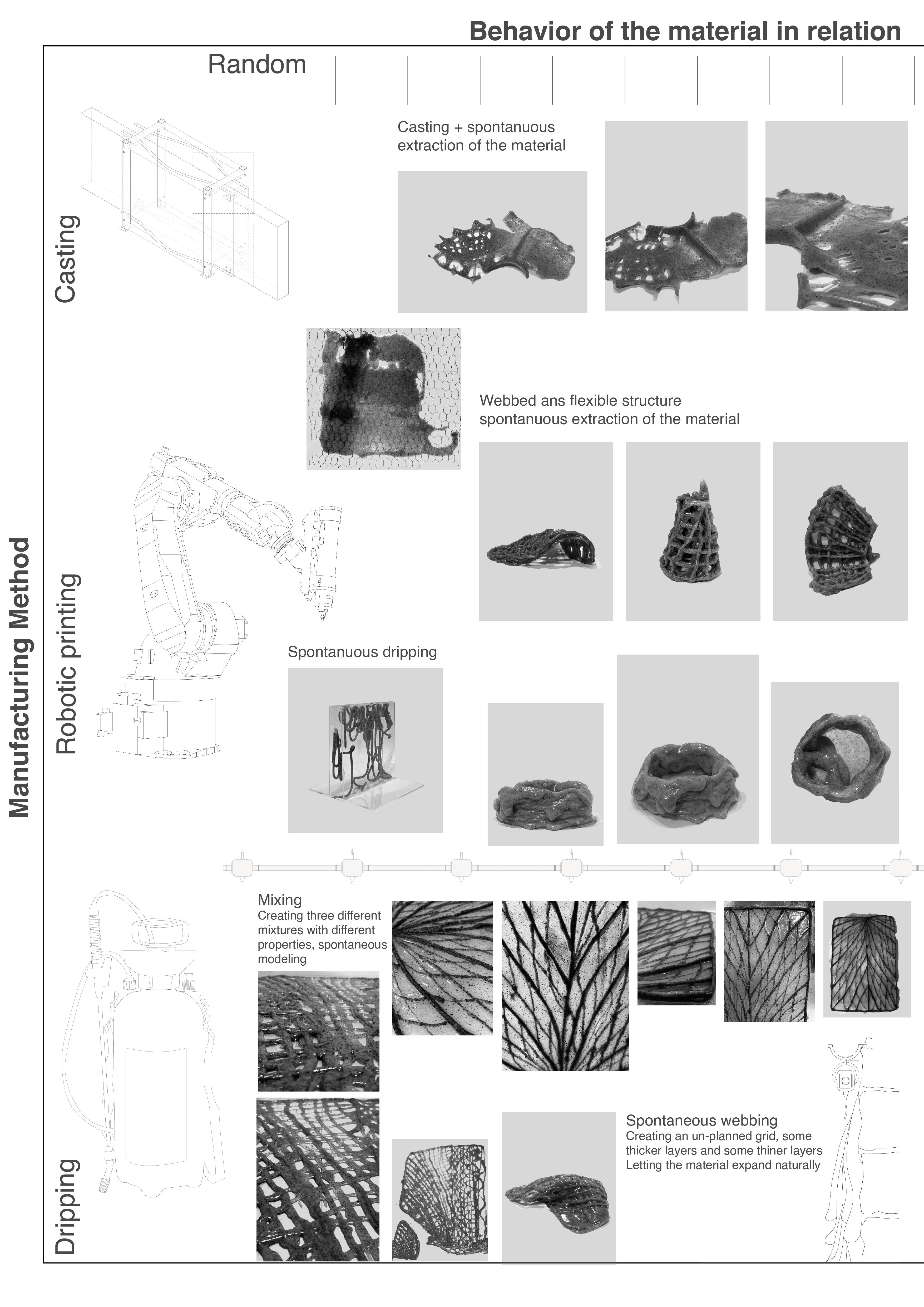
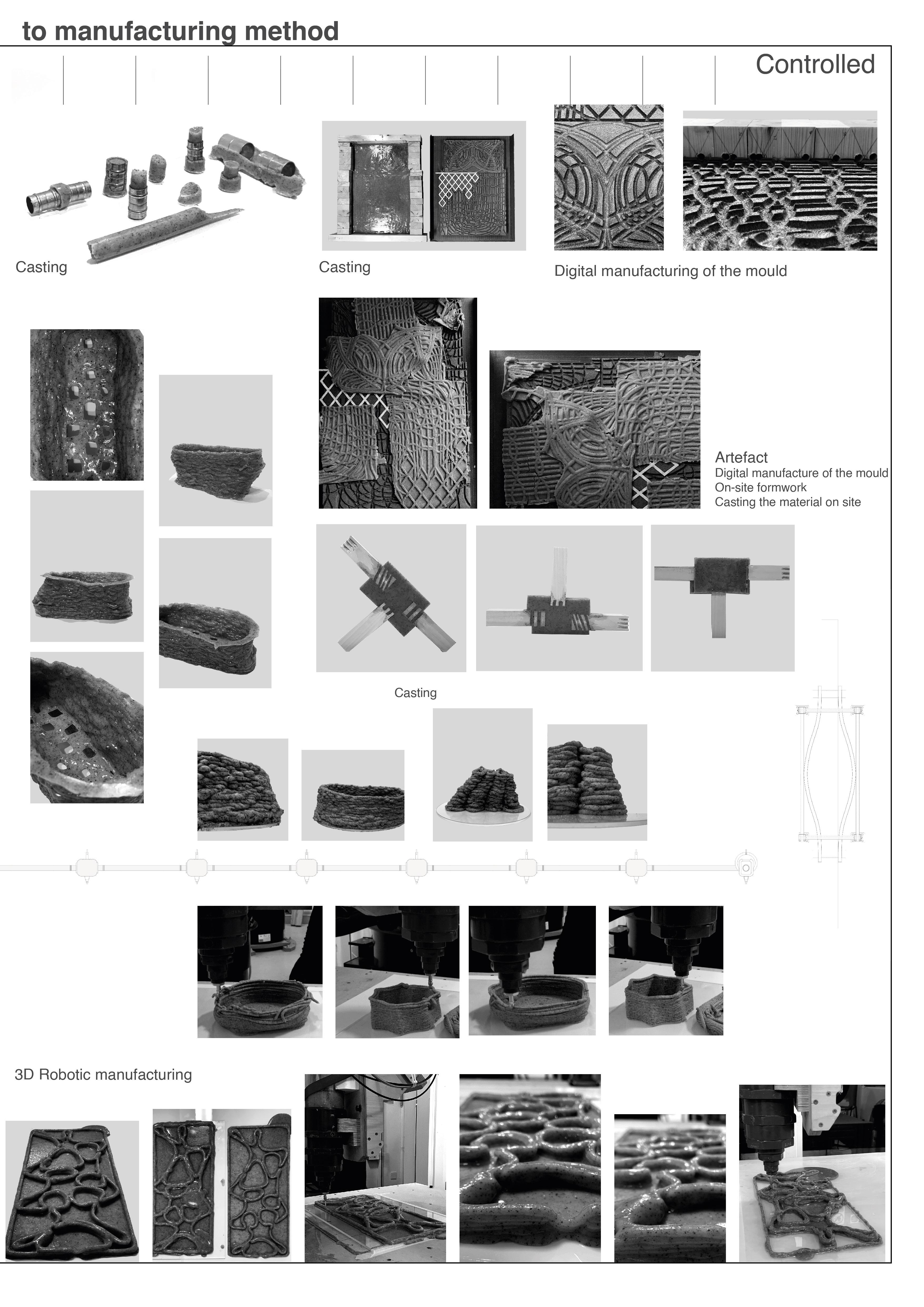
110 111
The material experiments that have been done so far are now dictating the design and the application of the material in these scenarios. By that, the three moments that have been chosen to be designed as new interventions in the building – are being expressed through the early experiments and are, in fact, the culmination of all the experiments done so far with the material.
9.2
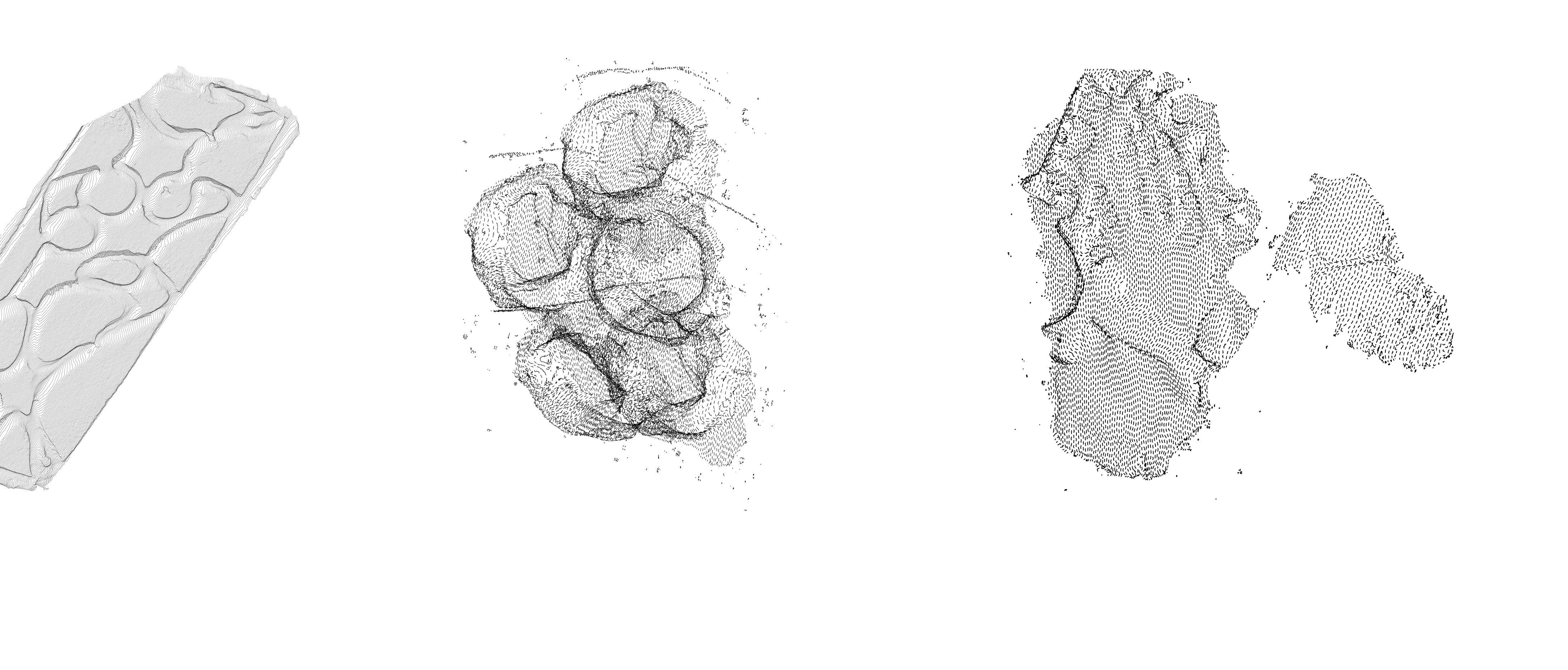
EntranceAreaDrying
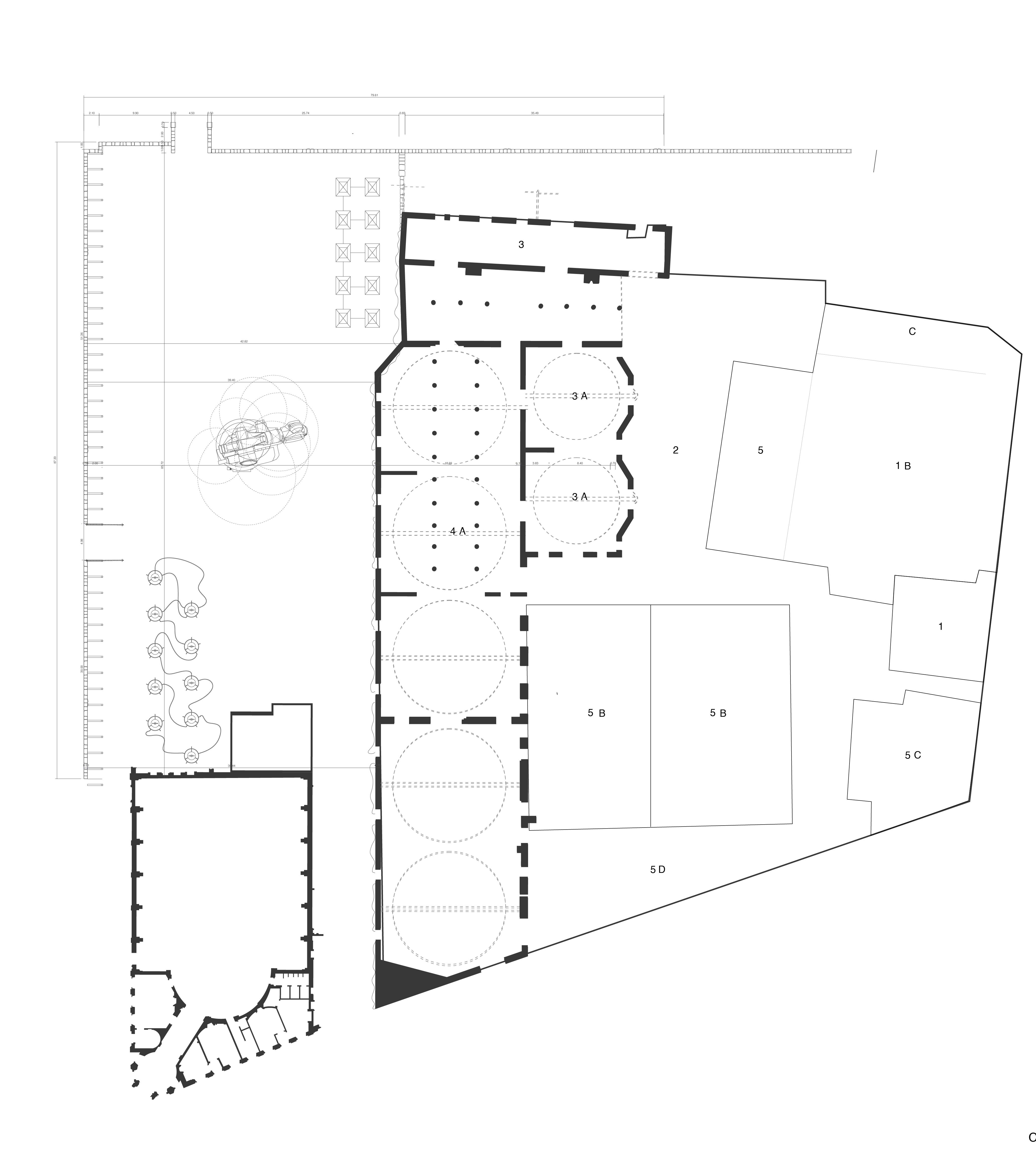
112 113
Tower st. st.ConstitutionEntrance MachinesGrinding Robot operation zone SystemPiping Office Workshop areaProcess Controlled and Uncontrolled Moments Plan, originally 1-100 | New Industry 0 25 50 m Gasometer HouseA 1 B 2 C 3 4 D 65 Remains of early works Site of Gasometer House Development of pre-1853 Post1853-1890Gasworks period Retort House Offices Chimney Refurbishing the yard - New Industry 9.3
114 115
Existing condition - continuous deterioration 9.4
Refurbishing the yard - New
Choosing Moments of Maintenance as opportunities for Design Industry
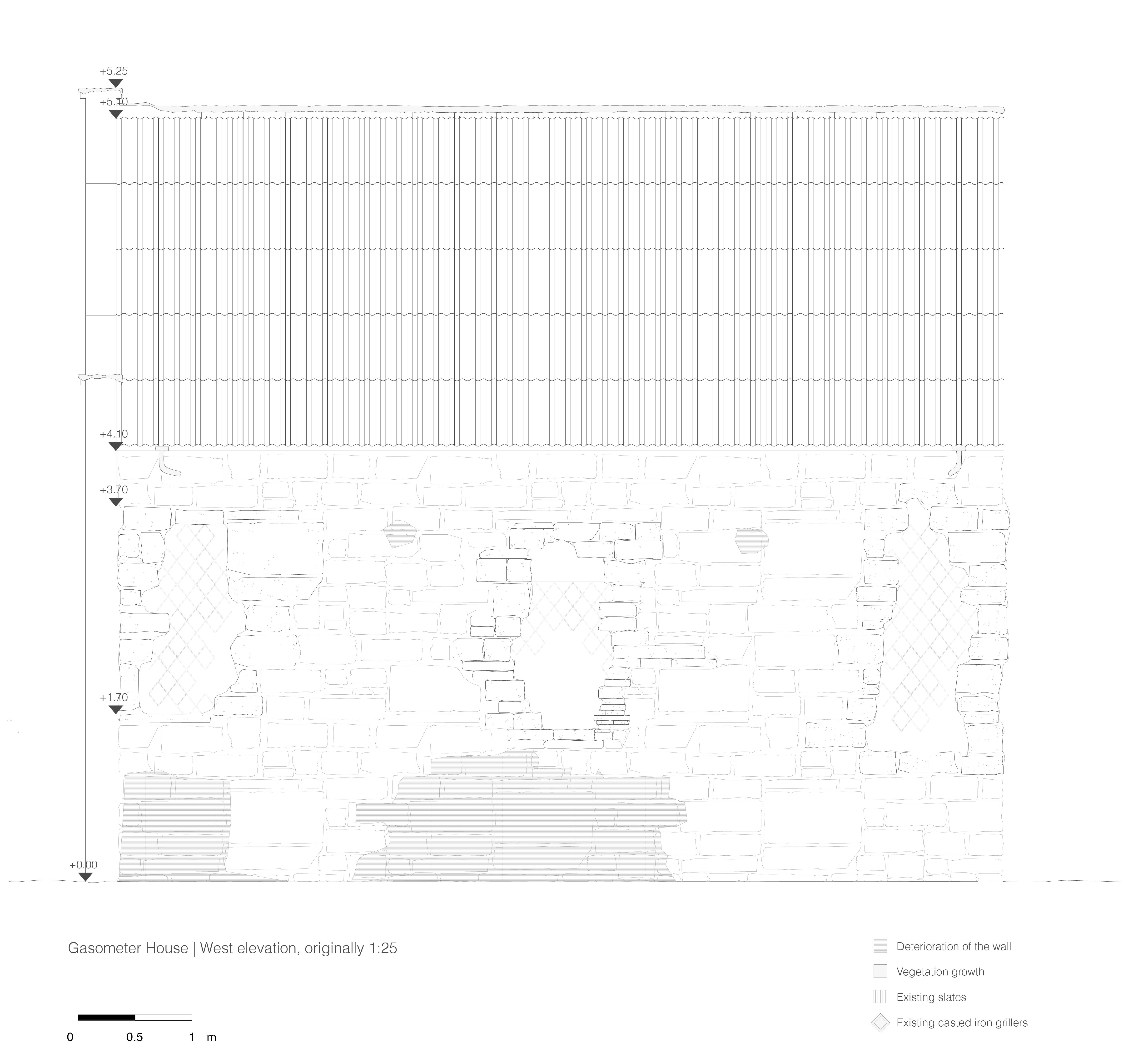
116 117
Refurbishing the yard - New Industry Designing uncontrolled moments 9.4
Choosing Moments of Maintenance as opportunities for Design
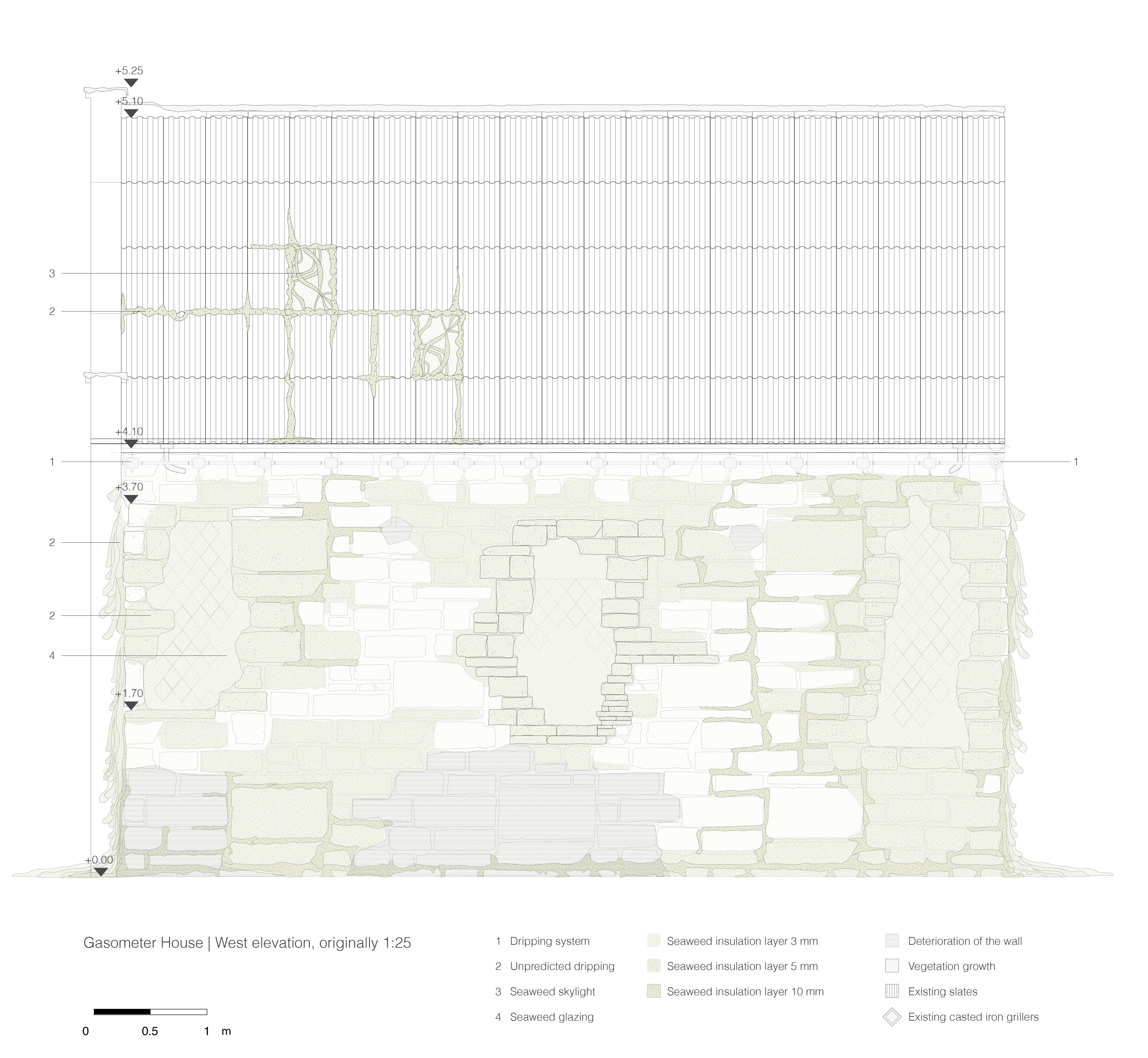
These experiments show how the material can operate as a joint, how it can be caste and how it can be printed, and how it is possible to combine these methods to create new aesthetics.
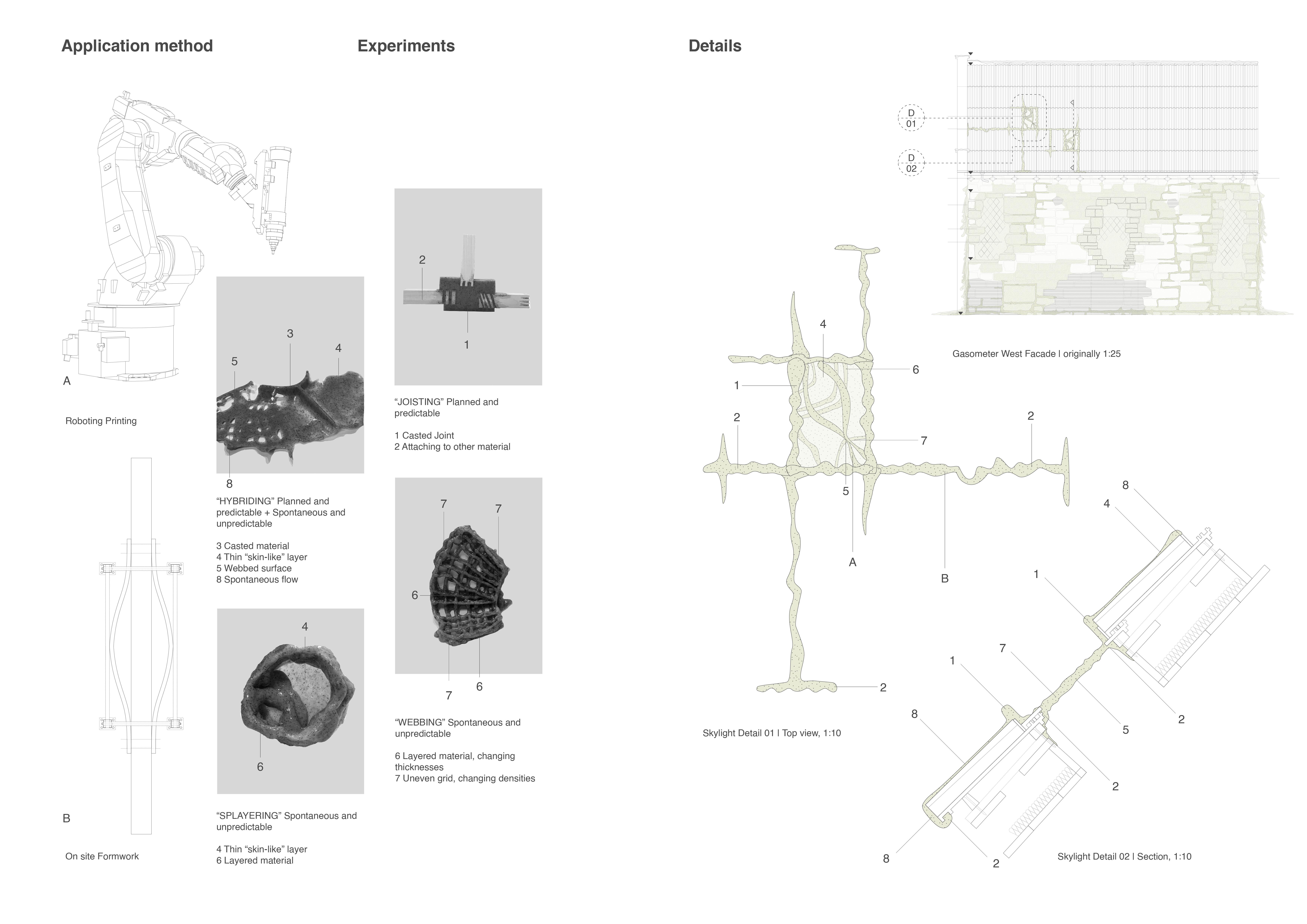
Controlled method - The missing slates become opportunities for light insertion and would function as skylights inserting filtered light. It would be applied by casting the material (detail no. 1), the Controlled method, together with the robot.
9.5
Missing Slates
118 119
Deteriorating walls
On site: Random method -
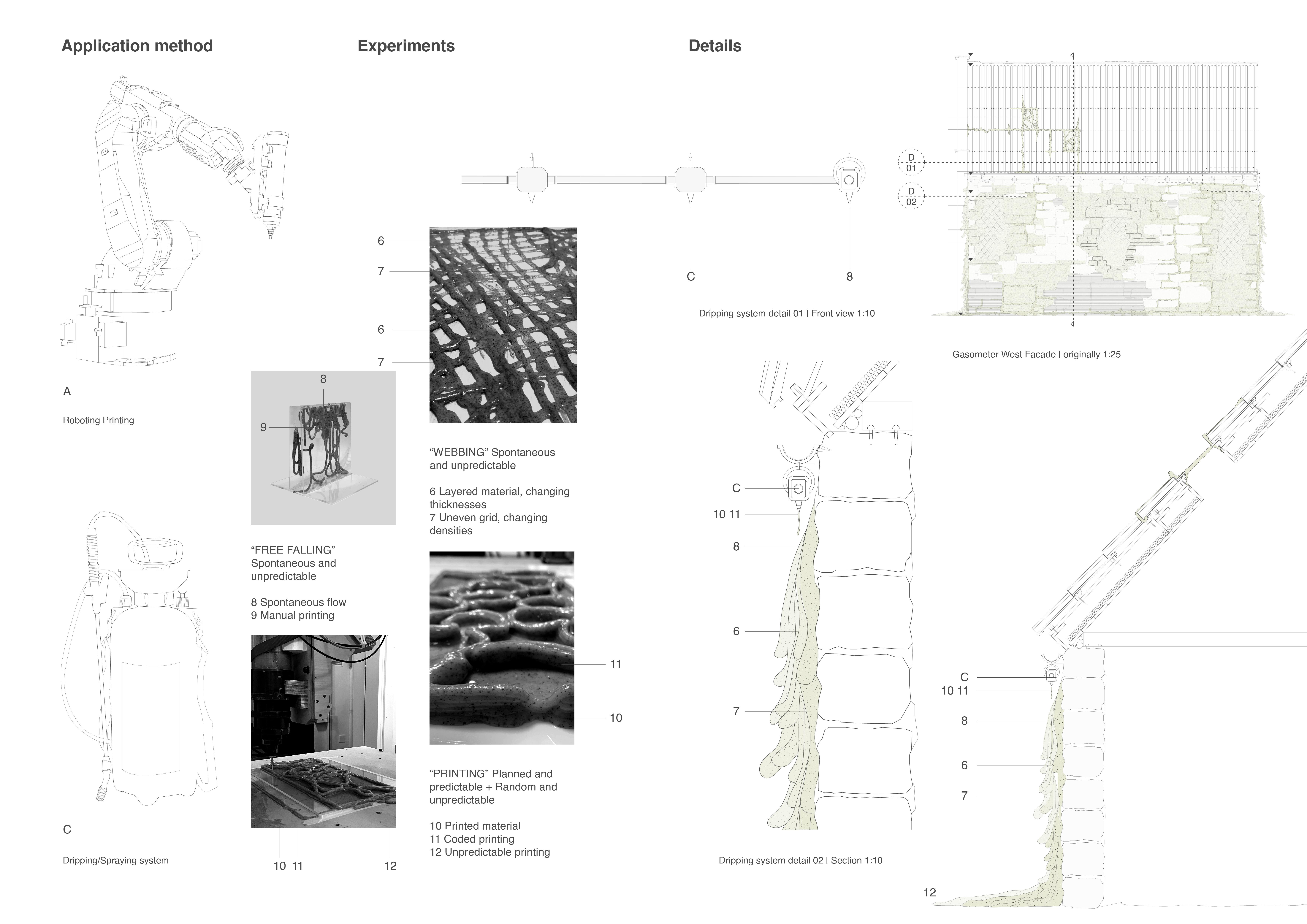
The experiments that have shaped the design of the wall are the printings with the robot and the dripping experiments as well. Although working with the robot and coding seems to be very accurate process, it also has an amount of uncontrolled or unpredictable parts. The wall would be covered by the material with a dripping system that would hang from the gutter in the top of the simultaneouslywall, with the robot spraying the material in a more specific way.
120 121
9.5
The gutters would be fixed, and a new dripping system would be applied on it (detail no. 2). The dripping system would extract the seaweed material in a regulated way. Here the material would function as an insulator (material data sheet), and gradually cover the wall, using its natural dripping –grips between cracks let it flow between the uneven surface of the stones.
122 123
The windows would come back in function, using casting and then using the robot, (as you can see in experiment robot and artefact), attaching the wall by curving the stone and filling the gaps with the material.
On site: Controlled and random -
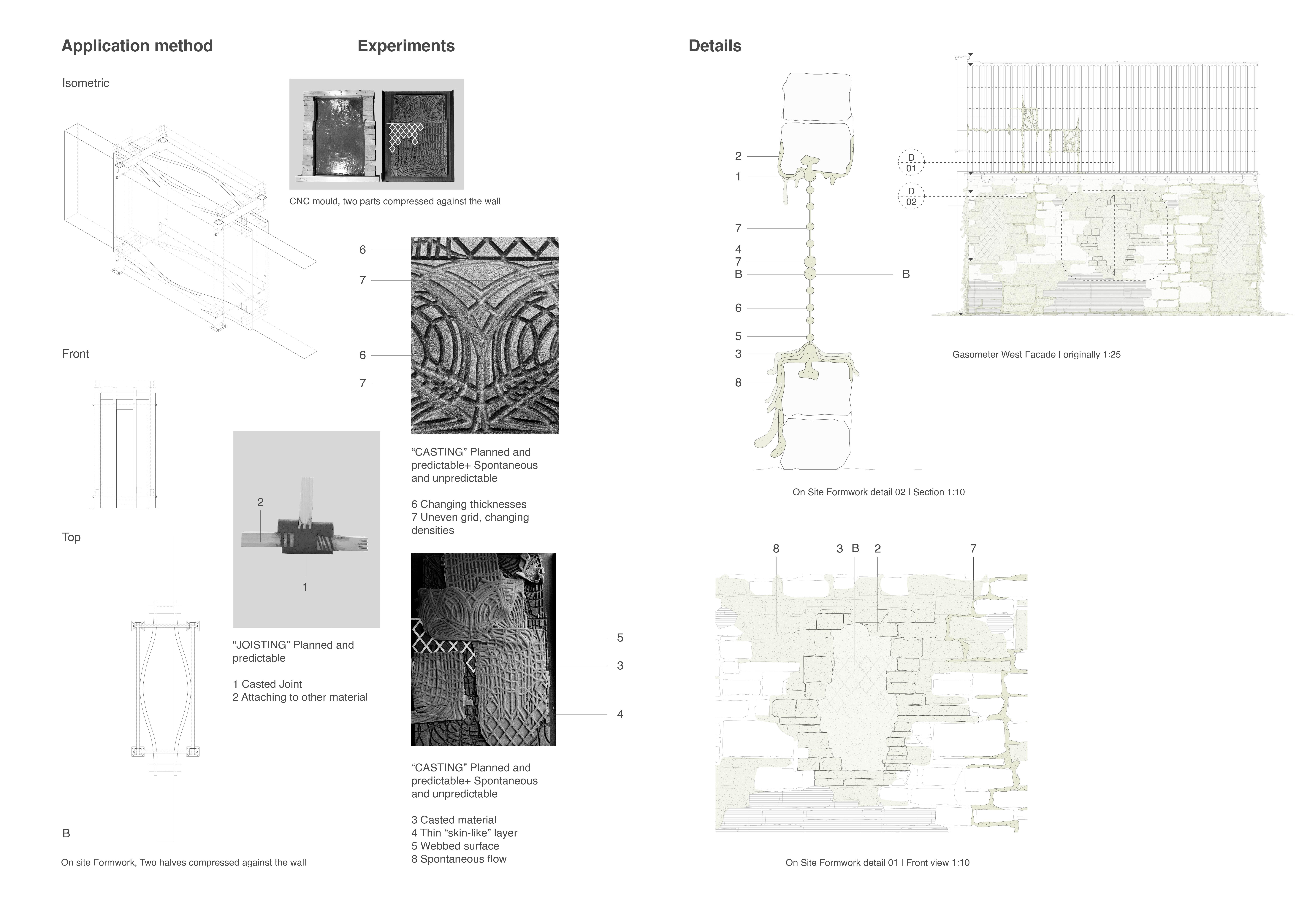
9.5
Blocked Windows
Making the artefact was a test of how to apply the material on site. It helped me realize that I can plan a mould that would be compressed against the wall or the roof using formwork. This is the predictable part, and then, letting the material flow on the surface in a spontaneous way, between the crevices.

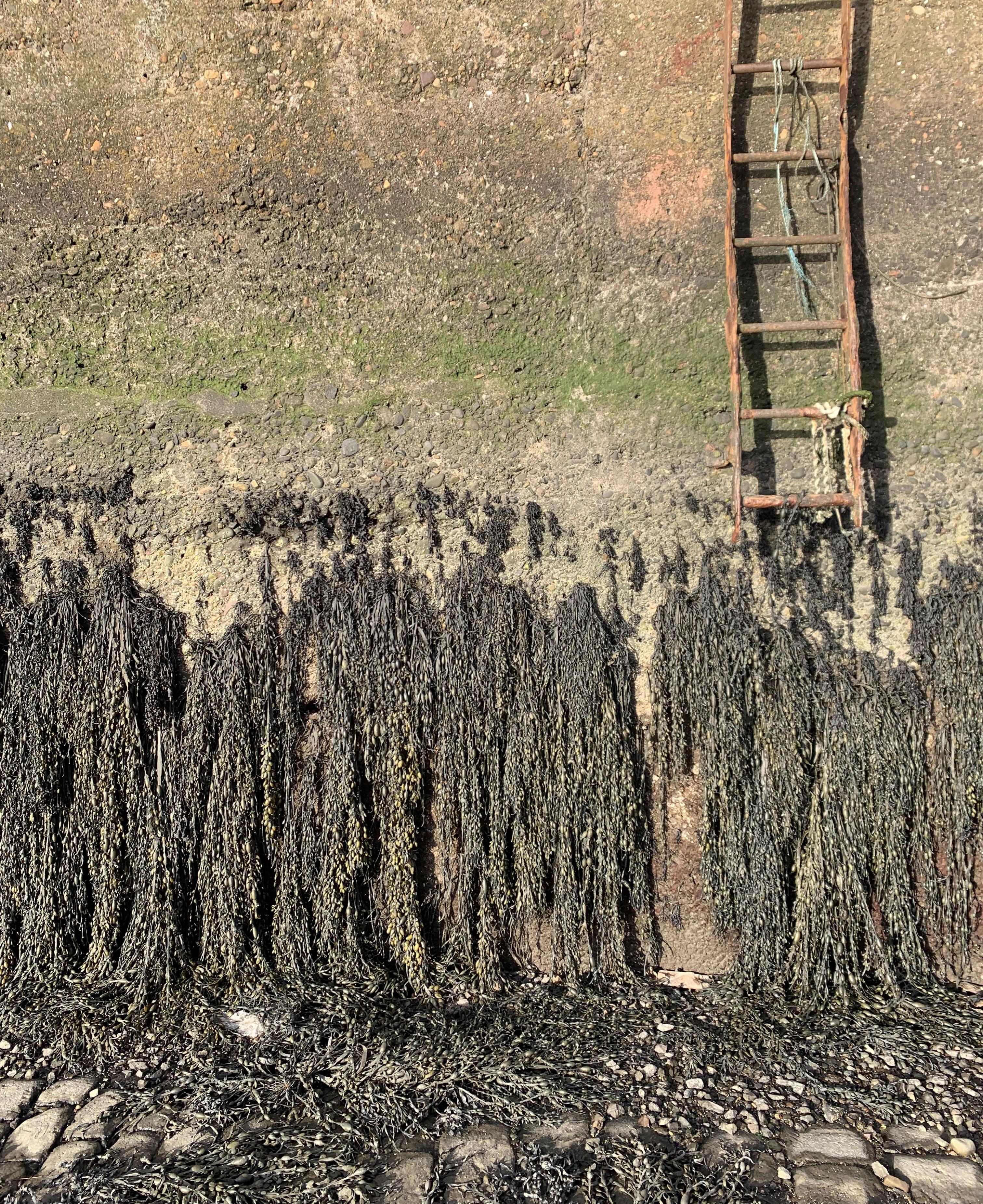