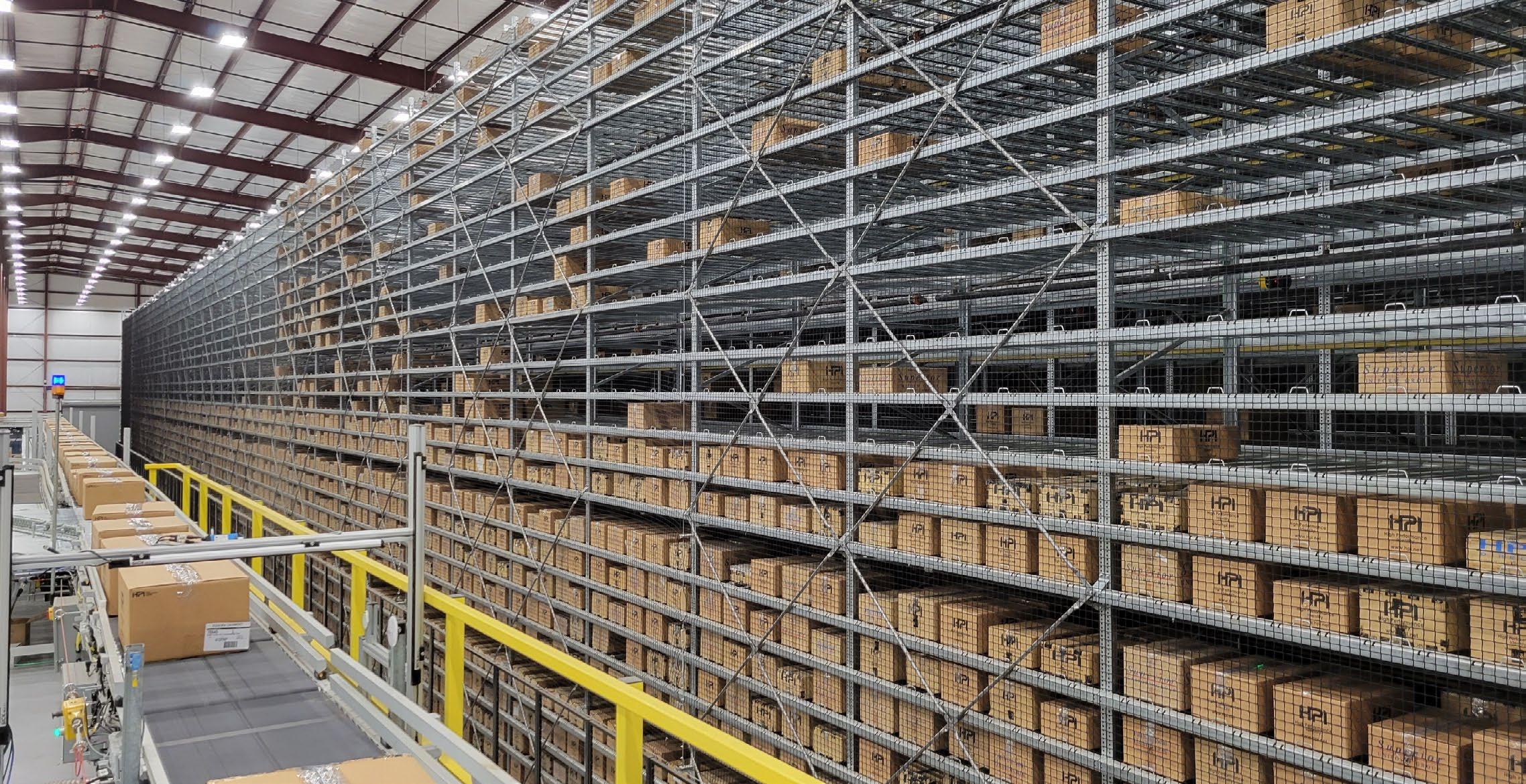
2 minute read
FACILITY OPTIMIZATION
Energy Efficient Buildings, Led Lights, Policies/Practices, Etc.
Our shared distribution facilities endeavor to reduce the environmental footprint of their operations by improving internal processes and implementing facility optimization practices. Several facilities have optimized efficiency and reduced waste by investing in lighting upgrades. Through these efforts, we continue to divert waste from landfills, reduce our energy consumption, and increase overall efficiency.
As our older facilities begin to need repairs, we have taken steps to retrofit them with energy efficient technology and other upgrades to optimize operations. Aging facilities have been updated with modern LED lighting with motion detectors, new heating and air systems, and conveyor and box retrieval cranes with low voltage controls, replacing outdated equipment. We implemented automated robots that pick products in order to enhance our employees’ production efficiency and reduce distribution costs. We also implemented modern sustainability practices and technologies into all our new facilities to maximize energy efficiency and reduce waste and cost. For example, in 2022 we completed construction of a new distribution center at our Eudora, Arkansas campus that is built to current energy-efficiency standards.
Our facilities must also meet certain strenuous client requirements. With the production of our new sustainable Carhartt™ collection, two of our new production plants were approved for use in 2022. In addition, all our CID Resources vendors renewed their Worldwide Responsible Accredited Production (WRAP) Gold Certificates in 2022.
Product Quality Management
To manage our environmental impact beyond our day-to-day operations, we have expanded our environmental sustainability efforts to encompass our supply chain. All nominated textile mills used by SGC are Oeko-Tex® certified and continue to purchase only Oeko-Tex® certified fabric for all apparel manufacturing, which means we can ensure our products are manufactured using fabrics that are free of harmful levels of toxic substances. To further engage our supply chain, we have extended the Oeko-Tex® certification requirement to all of our trim suppliers. Many of our products also bear the Oeko-Tex® “Standard 100” label, verifying that every component of a garment — including thread, buttons, and other accessories — is free of harmful substances.
In 2022, we progressed in our continued partnership with HeiQ®, a company that invests in sustainable applications for apparel fabrics. HeiQ® designs numerous innovative products, such as HyProTecht®, an antimicrobial and antiviral technology fabric initially developed in response to COVID-19. HyProTecht® is EU REACH- and US FIFRA-compliant, Oeko-Tex® certified, and ZDHC- and BlueSign-homologized. HyProTecht® also is certified as safe and sustainable as its ingredients are cosmetic-grade and the material is entirely biobased. SGC has licensed the rights to use HeiQ® fabrics in our products to develop unique apparel for use in hospitals, clinics, and other similar environments. In 2022, SGC received more than 367,000 units and distributed more than 125,000 units of HeiQ® apparel.
PFAS per- and polyfluoroalkyl substances
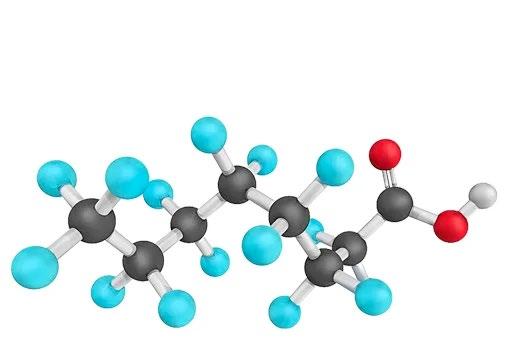
PFAS Spotlight:
There has been growing concern over the last several years related to better understanding and managing the impacts of per-and poly-fluoroalkyl substances (PFAS). These human-made chemicals have been used to make a variety of household and commercial products with a variety of applications since the 1960s and can now be found throughout the environment in soil and water. SGC is taking steps to address PFAS in our products by working with a European chemical manufacturer and a Korean fabric supplier to substitute a common PFAS containing fabric finishing chemical with a PFAS-free formula. Our efforts also extend into the broader apparel industry as well. We stay current on the latest state and federal PFAS regulations through our membership in the American Apparel and Footwear Association, and are working with members of the Textile Rental Services Association of America and American Reusable Textile Association to create a PFAS tool kit for laundries.