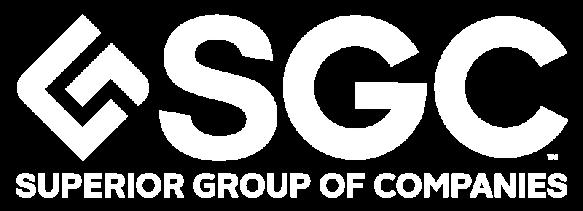
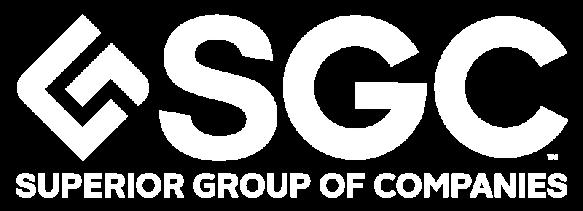
SUPPLIER
June 2024
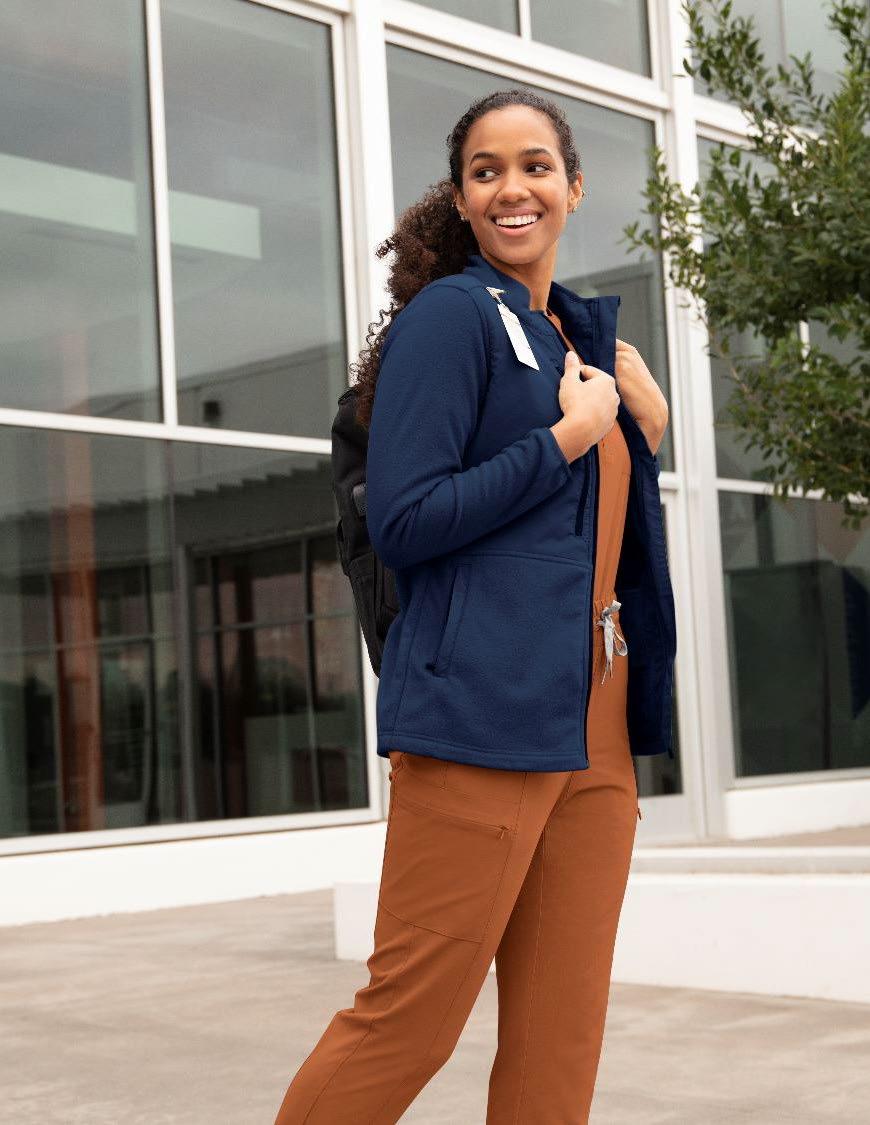
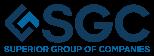
Supplier and Vendor Compliance Manual
Updated: April 2024
Requirements
• Suppliers and their manufacturing facilities, including all subcontracting facilities, are required to operate in full compliance with all local laws, rules, and regulations in the countries in which they operate.
• Suppliers and Factories are required to adhere to all compliance requirements of the SGC Supplier and Vendor Compliance Manual.

Health and Safety
Environment
Security
Working Hours
Social Insurance Requirement
Subcontracting
Business Integrity, Anti-Corruption, Anti-Bribery
Closing of Findings
Supplier Status Change
Supplier Quality Assessment Cotton Traceability
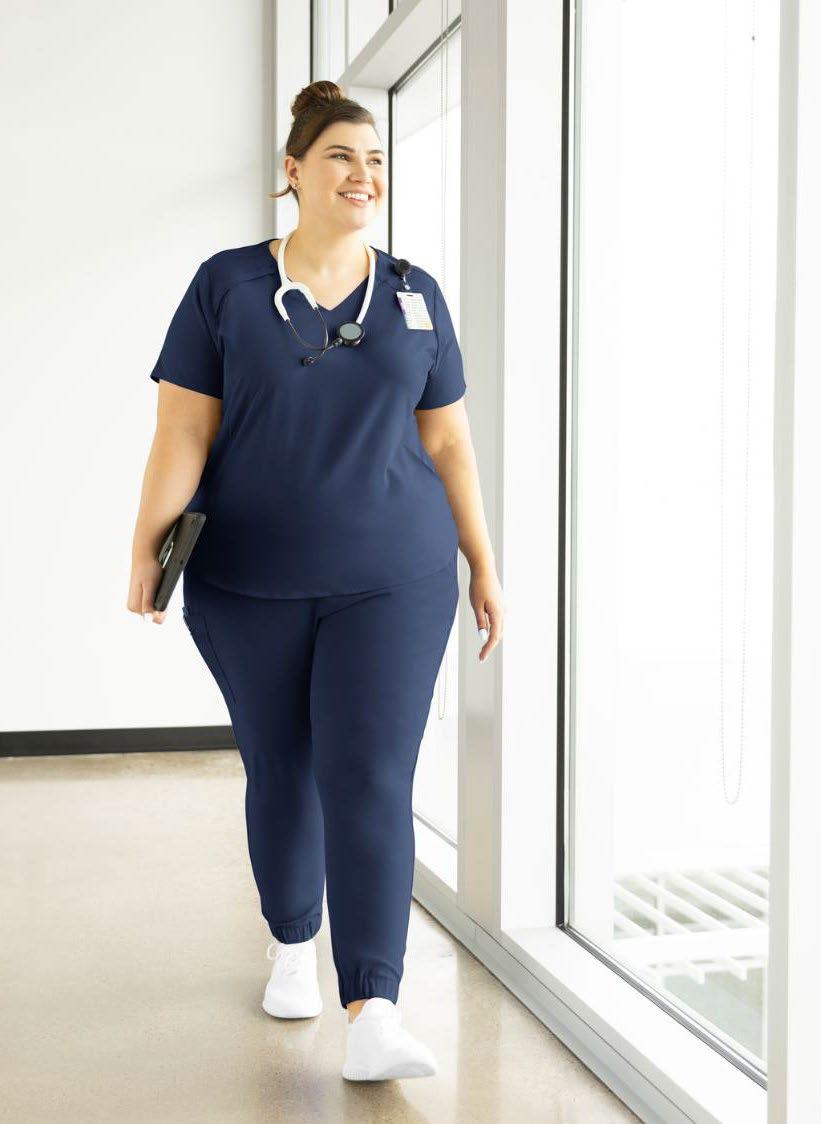
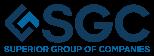
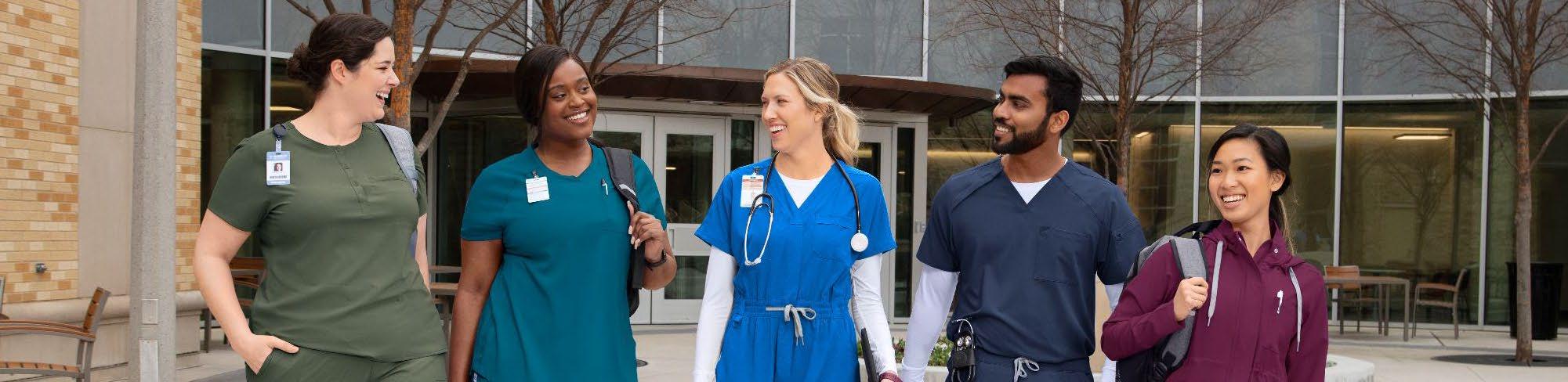
Social Compliance
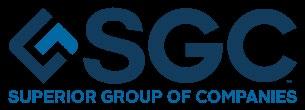
Superior Group of Companies spearheaded the social compliance movement when the matter came to the forefront of the U.S. textile and apparel industry. We were acknowledged nationally as “trendsetting” by the U.S. Government, and have remained steadfast in our commitment to excellence in corporate social responsibility practices.
We utilize globally-recognized 3rd party inspectors and certifications, such as SGS, BetterWorks, and Worldwide Responsible Accredited Production (WRAP).
Acceptable Third Party Audits
Amfori BSCI
BetterWorks
Bureau Veritas
Elevate
Intertek
SA8000
Sedex SMETA
SGS
United Laboratories (UL)
WRAP
Others, please check with SGC
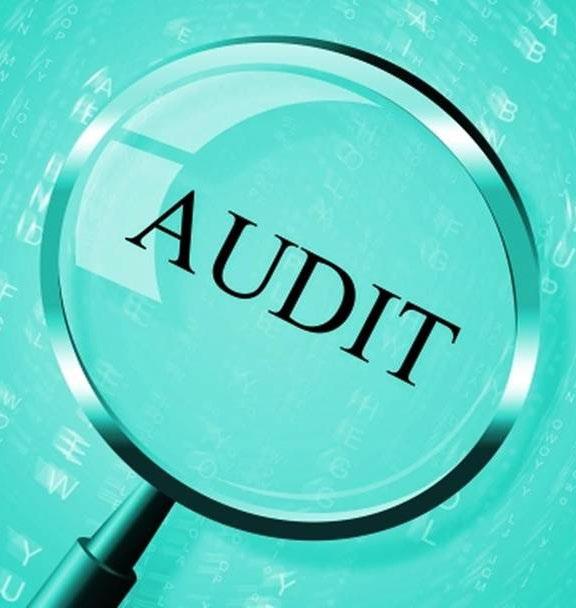
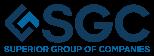
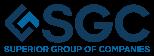
Acceptable
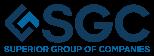
Re-Audit Cycles
Primary factory
Suppliers must allow unannounced inspections and audits of their records and facilities by SGC or a SGC approved third party to verify compliance with SGC Compliance Manual.
A yearly audit of a facility is required. Full audit report and certificate must be submitted on or before expiration of previous audit.
A high risk country may require a building assessment by a customer’s nominated auditor or engineering firm.
Subcontractor
Suppliers must disclose the identity, physical location, and ownership of all factories that will produce products for SGC, including those operated by subcontractors.
A subcontractor performing substantial or partial production may be subject to a yearly audit.
Certain SGC customers require Surface audit of Subcontractors.
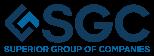
Zero Tolerance Policy
Child Labor
Forced, Prison Labor, Human Trafficking
Abuse & Harassment
Life Threatening Conditions
Confirmed falsified audit report and/or business license
Health & Safety
Suppliers must provide all their workers with a safe and healthy work environment and comply with all applicable Laws and regulations regarding working conditions, including, but not limited to:
• Access to potable drinking water; sanitary food preparation, storage, and eating facilities; emergency medical care; and first aid kits
• Appropriate personal protective equipment, available at no cost to all applicable employees
• Instruction and enforcement of proper use of protective equipment
• Appropriate safety training for the use of machinery and other equipment, and the handling of chemicals
• Proper labeling of machinery, hazardous materials, and other potentially dangerous items
• Workers are not permitted to engage in the manual transport of a load which, by reason of its weight, is likely to jeopardize a worker’s health or safety
• Adequate lighting, ventilation, cooling, heating, and clean toilet facilities in all work areas
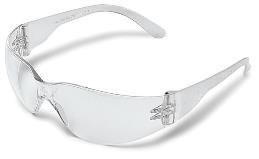
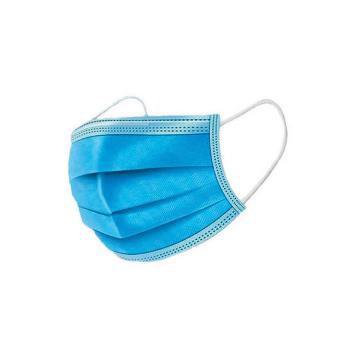
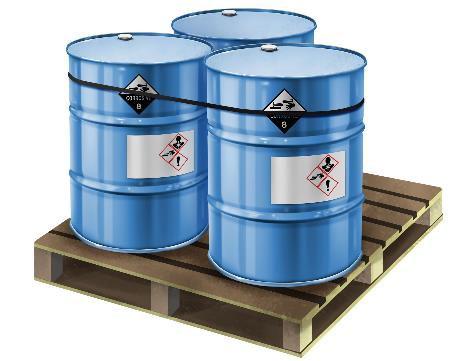
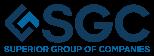
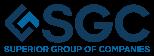
Health & Safety
• Doors and other exits must be well marked, unobstructed, and unlocked from the inside during all working hours for orderly evacuation in case of fire or other emergencies.
• Evacuation drills are conducted at least annually.
• Maintain written standards for a safe and healthy environment.
• Work environment and the prevention of accidents and injuries to workers must include emergency reporting, evacuation procedures, and appropriate fire detection and suppression equipment.
• Where dormitory is provided for workers, facilities must comply with all housing laws, occupancy requirements, and health and safety Laws.
• Ensure a factory has the correct number of toilets against the number of employees as required by law.
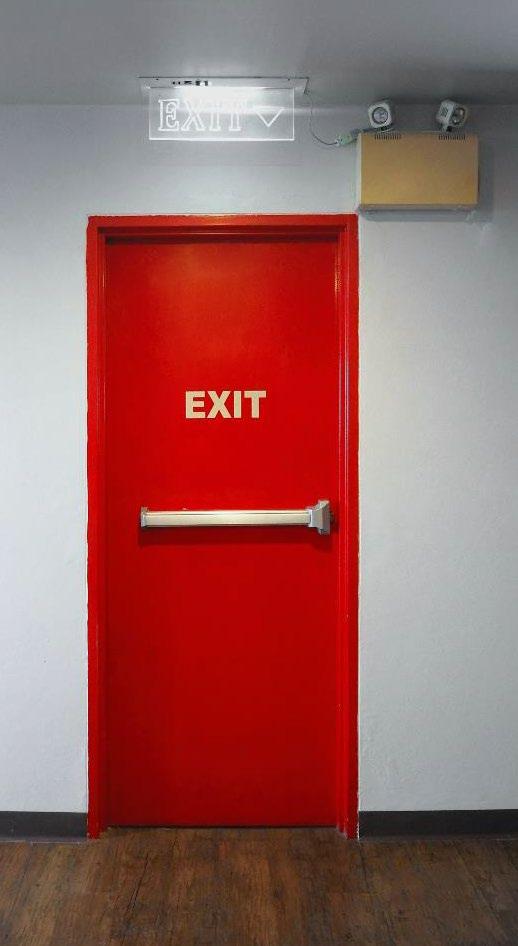
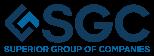
Examples of Blocked Evacuation Pathway & Emergency Exit
Emergency exits, stairways and aisles must be clear of any blockage.


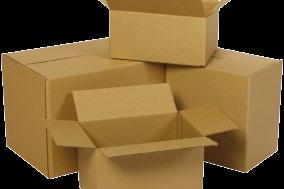
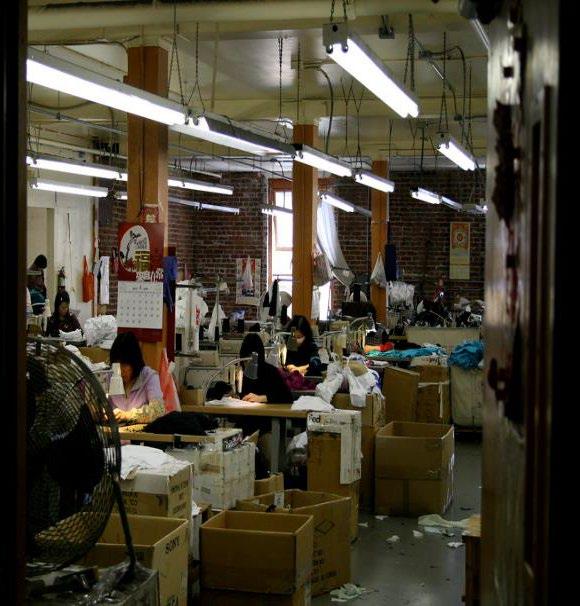
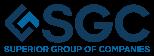
Emergency Exit
Unlock Emergency Exits at all times during work hours.
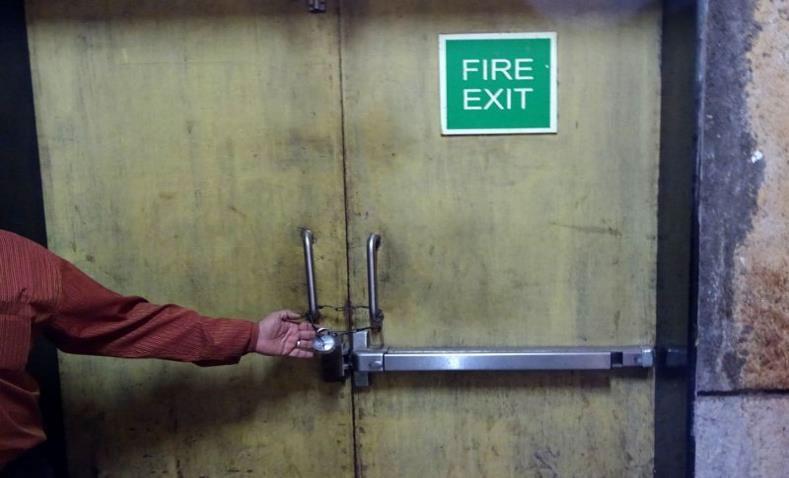
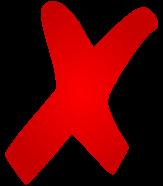
Remove the chain & padlock during work hours.
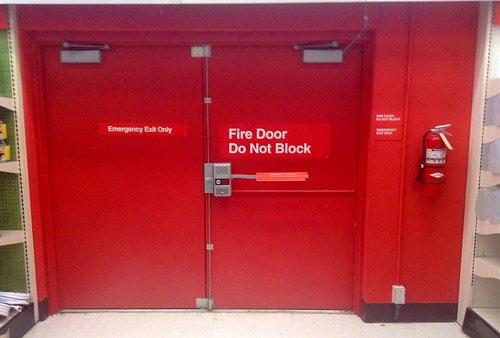
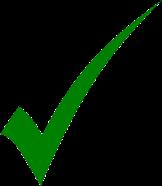
Has push bar lock. Workers can use their bodies to open the door by using the push bar lock. Sliding doors as emergency exits are not acceptable because sliding doors are not easy to open in case of an emergency.
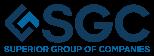
Fire & Safety
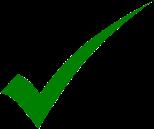
Facility must have a valid inspection certificates issued by local fire service authority.
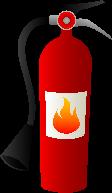
Fire extinguishers must meet local legal requirements, properly located and labeled in languages spoken at the factory.

Fire alarms are audible/visible in any section of the facility. Fire Alarm system is inspected and tested regularly.
Fire & hazard early warning system such as smoke detector must be installed & regularly tested.
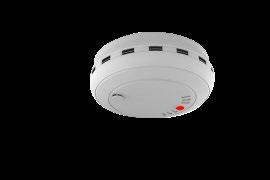
An effective fire extinguishing system such as fire hydrant/fire hose or sprinkler system must be installed at each factory floor, inspected & maintained properly per local law requirements.
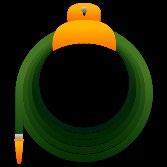
Fire exits & escape routes must be adequate at each facility floor, unblocked, unlocked and easy of access.
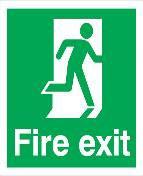
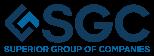
Fire & Safety
Facility must have an adequate emergency lighting system installed at each factory floor.
Correct evacuation plots are posted at all floors of the factory.
Welding operators must be trained & qualified per local regulations.

Hot work permit procedure must be implemented for welding, cutting, and open flame operation.
Number of fire accidents that took place in the past 12 months at the facility (if any) must be recorded.

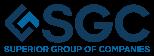
Fire & Safety
General Chemical Management Machinery Safety
• A safety committee must be established with members representing the various shifts, functions and levels.
• Must conduct regular training & awareness programs on health & safety for all employees.
• Site buildings (including both production & dormitory) must be maintained in good condition and physically sound.
• Must be suitable working environment in respect to ventilation, temperature, lighting cleanliness.
• Adequate guards and/or devices installed on moving/rotating parts of machine, pulleys and belts or any other dangerous parts of machines.
• Prohibit loose clothing, jewelry and long hair near moving machinery.
• Perform regular preventative maintenance of machines including safety devices.
• Must have a written procedure for safety storage & handling of dangerous/hazardous chemicals.
• Must properly label all chemical containers.
• Must have a current inventory and list of dangerous/hazardous chemicals.
• Must install Emergency eyewash stations.
• Safety Data Sheets (SDS) must be available at chemical storage and operating area in the local language.
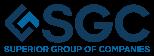
Fire & Safety
• Employees must wear Personal protective equipment (PPE) such as goggles, masks, safety shoes, earplugs etc. to control safety hazards.
• Signs and Warnings posted in corresponding areas to remind employees to wear PPE.
• Licensed Internal & external electricians must be qualified per local regulations.
• Electrical procedures implemented effectively to ensure safety precautions such as grounding, discharging and testing.
• Covers in place for junction boxes, electrical outlets, panel boards and are free from obstruction with proper warning signs.
• Adequate first aid supplies must be located at each floor and marked with signs.
• Adequate trained employees on first aid.
• If required by law, an in-house clinic/first aid station established with competent doctor/first aider employed at the facility.
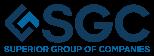
Environment
A factory must have:
A copy of valid laws and regulations on environment protection or understand its requirements. Check with local government if need to post valid laws around the factory.
An environmental policy signed by top management.
An environmental emergency procedure related to risk identified (such as reporting, tank filling, chemical use).
Environmental impact analysis of its operations and put in a mechanism to minimize negative impact on environment.
Must have a proper waste water, gas etc. treatment before releasing.
Must monitor the emission of waste water, gas, noise etc. as per legal requirement of the factory’s country.
Must segregate, store and dispose hazardous waste properly.
Must have an energy efficiency plan to reduce resources used.
Must have all approvals, permits and licenses required by local law.
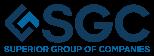
Security
U.S. Customs and Border Protection (CBP) recognizes that a safe and secure supply chain is the most critical part of our work, keeping our country safe.

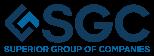
Transportation Security
Conveyance and Instruments of International Traffic Security
• Smuggling schemes often involve the modification of conveyances and Instruments of International Traffic (IIT), or the hiding of contraband inside IIT.
• At the point of stuffing/loading, procedures need to be in place to inspect IIT and properly seal them. Cargo in transit or “at rest” is under less control, and is therefore more vulnerable to infiltration, which is why seal controls and methods to track cargo/conveyances in transit.
• Inspect an empty container before loading cargo – Front wall, left side, right side, outside undercarriage, floor, ceiling/roof. Use a 7-Point Container Checklist.
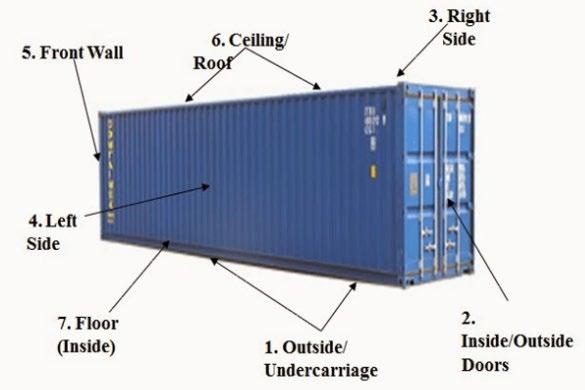
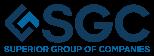
7-Point Container Checklist
• A 7-Point container checklist must accompany each sea shipment.
• A 7-Point container checklist must be filled out and signed by 2 employees of the factory – by the person who filled out the form and a person who verified the integrity of the seal.
• Any suspicious containers that may result to replaced containers, please notify SGC of new sailing schedule and revised delivery date.
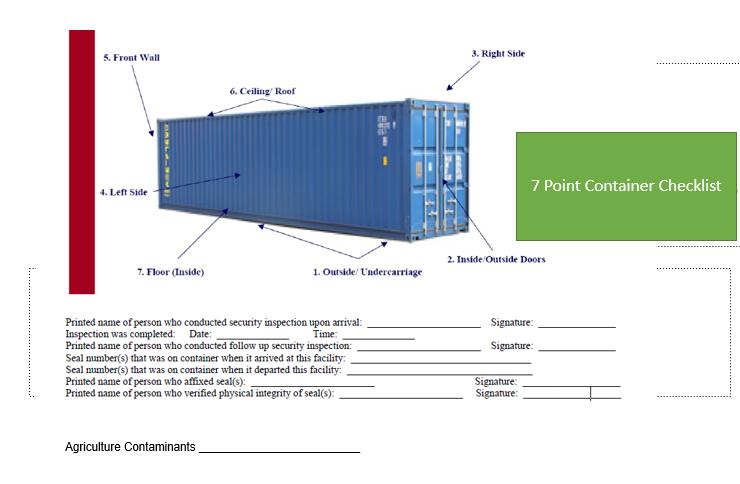
Agricultural Security
• Pest contamination is defined as visible forms of animals, insects or other invertebrates (alive or dead, in any lifecycle stage, including egg casings or rafts), or any organic material of animal origin (including blood, bones, hair, flesh, secretions, excretions); viable or non-viable plants or plant products (including fruit, seeds, leaves, twigs, roots, bark); or other organic material, including fungi; or soil, or water; where such products are not the manifested cargo within instruments of international traffic (i.e. containers, unit load devices, etc.).
• Clean up and document the container prior to loading a cargo.
• Any suspected container of agricultural contamination will be returned to the origin.
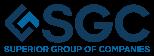
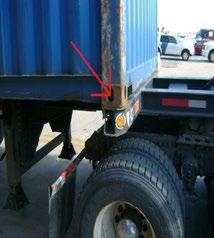
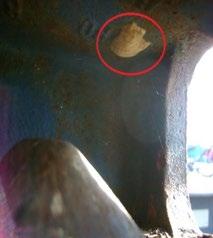
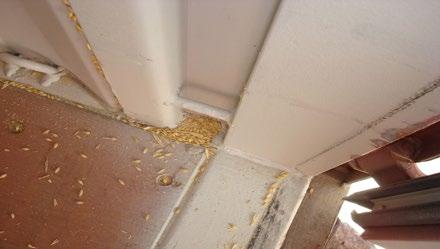
Signs of Pest Contamination provided by CBP
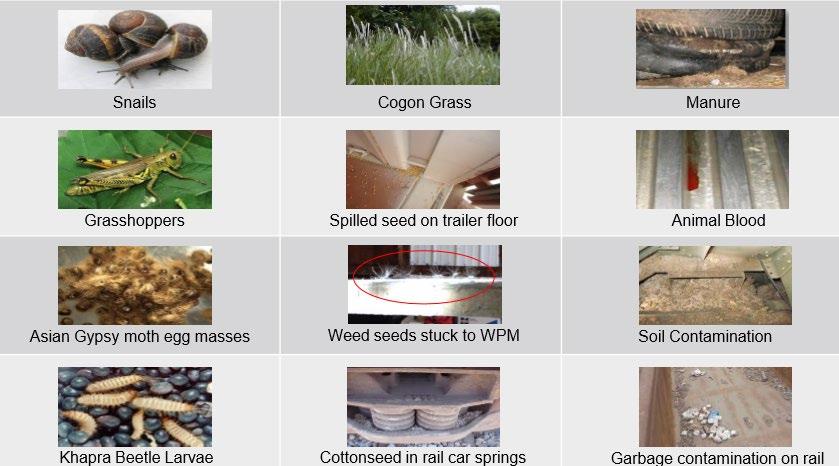
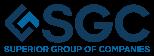
Clean and Inspect a Shipping Container Prior to Loading Cargo
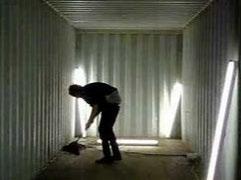
Sweep the interior of a shipping container prior to loading to remove any agricultural contaminants.
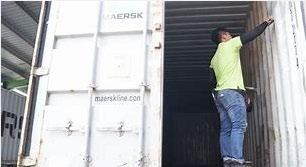
Inspect a container for hidden compartment & concealed contraband.
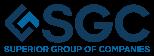
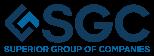
Check a Container Prior to Loading Cargo
Visually check the interior and exterior of a container for:
• Fresh repair or weld marks on the floor.
• Condition of the ceiling/roof.
• Newly painted wall.
• False wall.
• Tap the floor, ceiling or wall with a broom or rubber mallet. If the sound changes, investigate.
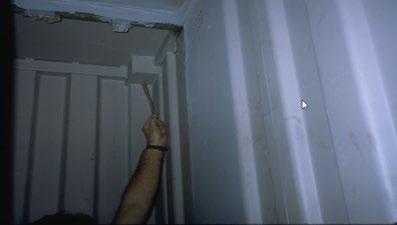
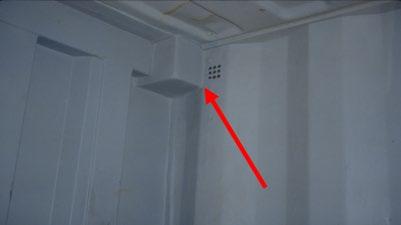
Check Outside a Container
Check under a container. Use a mirror to ensure under carriage is inspected.
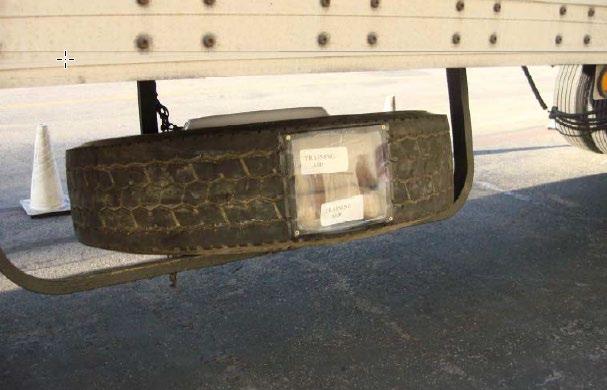
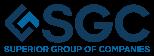
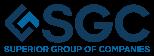
Container Seals
• Seal security includes a comprehensive written seal policy to address seal security, applying correct seal, properly placing a high security seal on a container and verifying that the seal has been affixed properly.
• Management of seal is restricted to authorized factory personnel only.
• Secure storage of seals in locked area.
• Record the receipt of new seals, issuance of seals recorded in log.
• When picking up sealed container, verify the seal is intact that no signs of tampering.
• Confirm the seal number matches what is noted on shipping documents.
• Take pictures of the new seal before shipment departs.
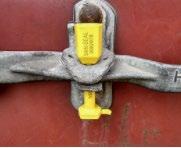
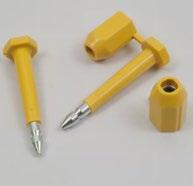
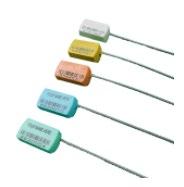
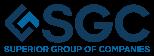
Attaching Container Seals
• V – View seal and container locking mechanisms.
• V – Verify seal number for accuracy.
• T – Tug on seal to make sure it is affixed properly.
• T – Twist and turn seal to make sure it does not unscrew.

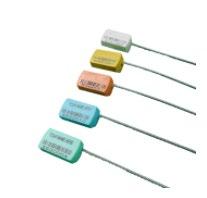
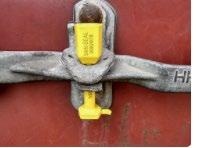
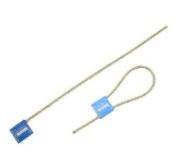
Working Hours
• Suppliers must comply with applicable Laws and industry practices on working hours.
• Workers must not work more hours in one week than allowable under applicable Laws or regularly exceed the recommended maximum of 56 hours per week, whichever is less.
• Workers must be properly compensated for overtime work and must be allowed at least one uninterrupted, 24-hour rest period every seventh (7th) day.
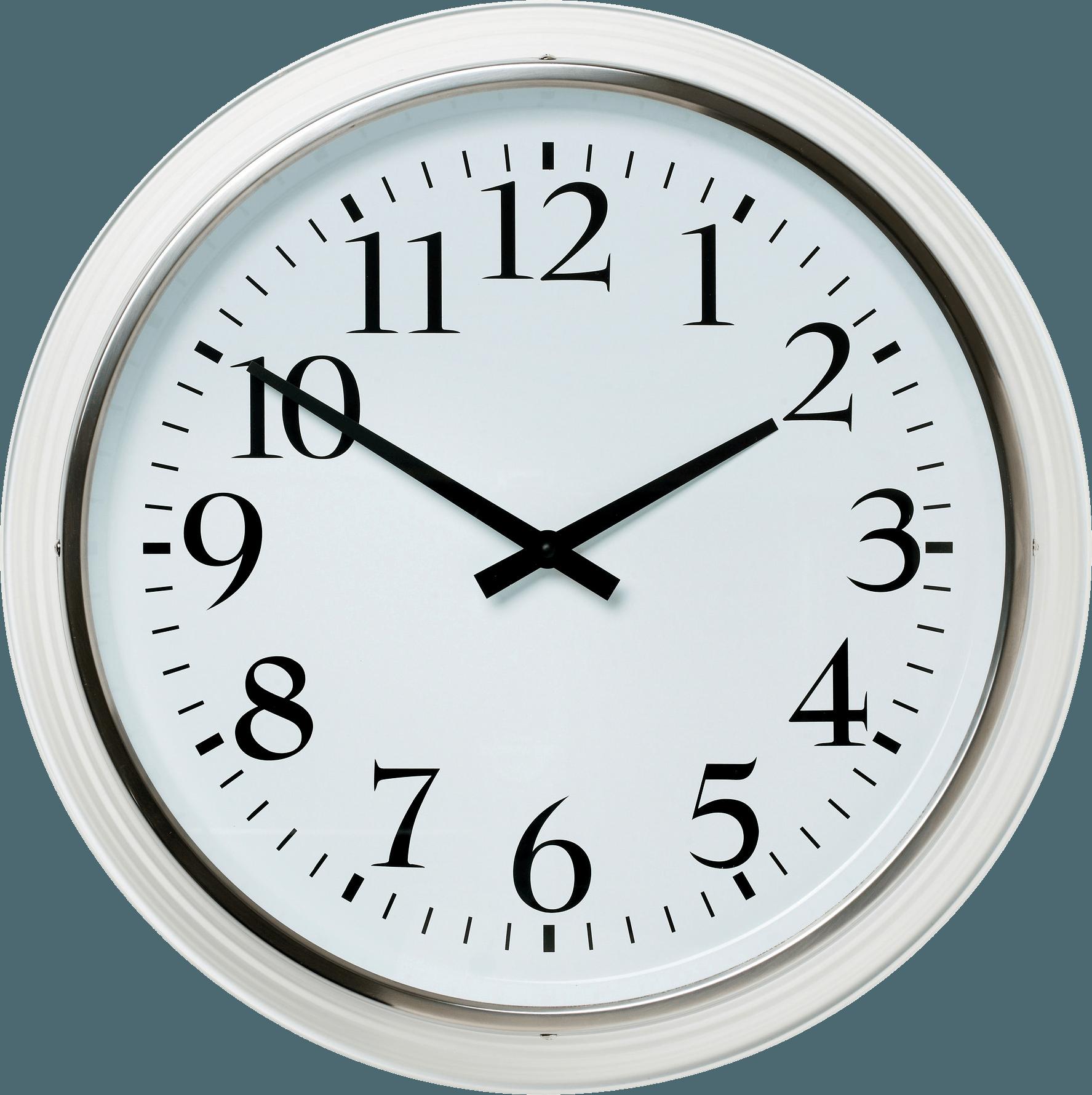
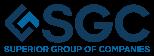
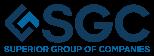
Working Hours
• Must have a copy of valid laws and regulations on working hours or understand its requirements.
• Factory must establish a written policy on working hours, rest and vacations as per legal requirement.
• Factory must communicate related policy with their employees.
• Must comply regular working hours (weekly, daily, hourly, night shift) with legal requirement
• Working hours of employees must be recorded accurately & documented completely.
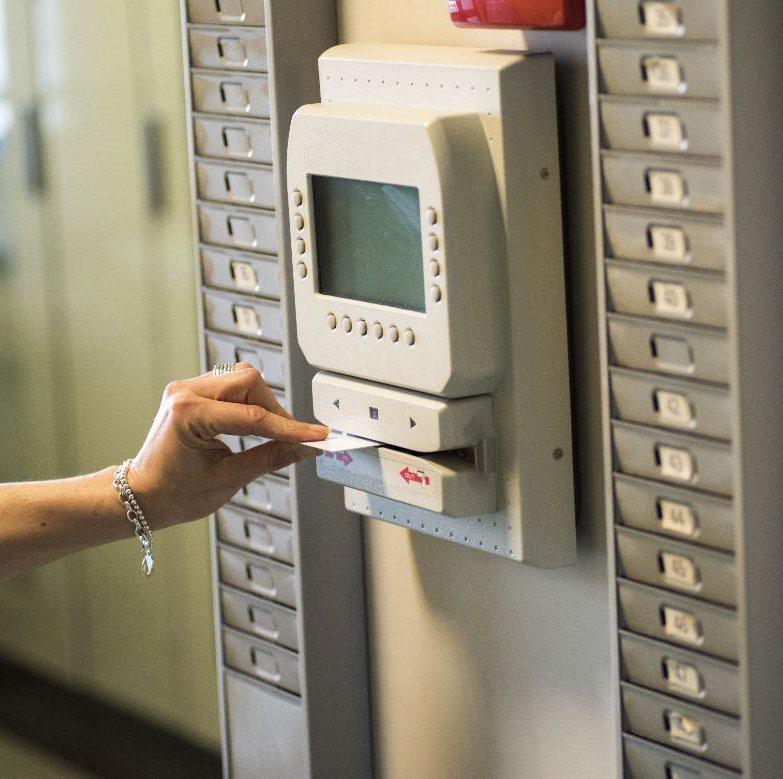
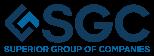
Working Hours
• Do employees have at least one day (24 consecutive hours) in seven days as day off?
• Do employees have time for rest & meal breaks per employee contracts and compliant with legal requirements?
• Is the system for recording hours of piece-rate employee is the same as all other employees?
• Employees overtime must not exceed legal requirements.
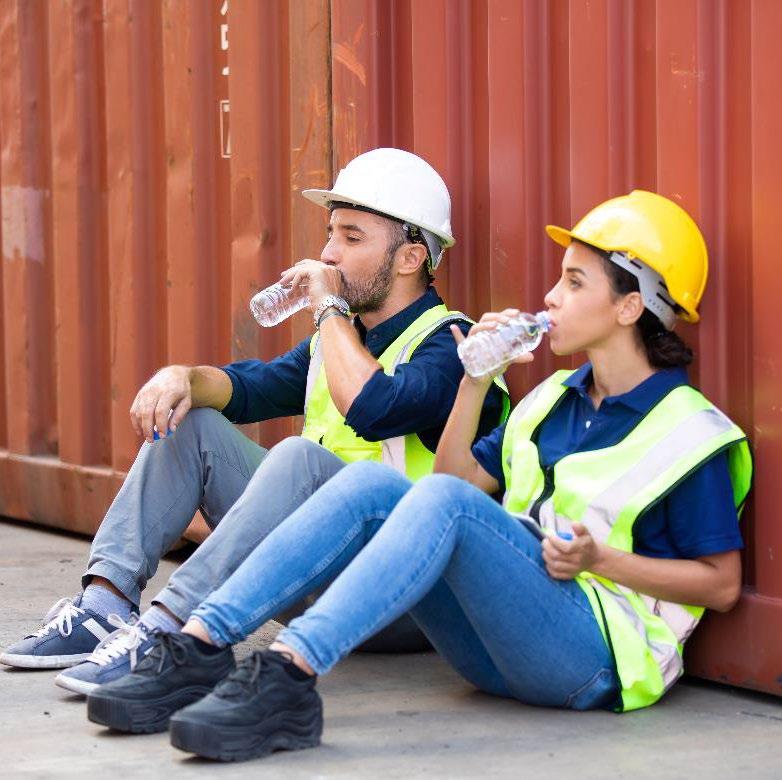
Social Insurance
• Suppliers must comply with applicable laws and industry practices on social insurance.
• In accordance to the law, social insurance benefits include:
• Retirement
• Illness or injury
• Disability cause by work -related injury or occupational disease
• Unemployment;
• Child-bearing
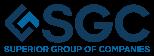
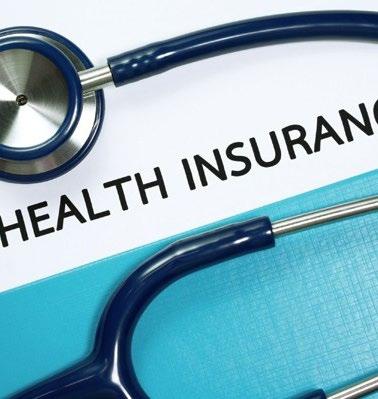

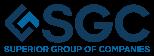
Social Insurance
• A factory must provide social insurance to its employees.
• A factory must encourage their workers to participate in social insurance by conducting meetings to explain its benefits and law requirements.

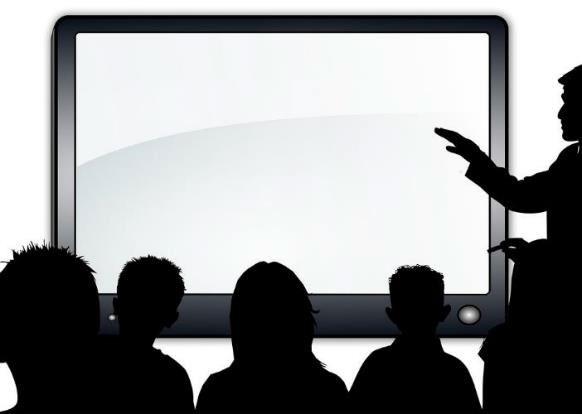
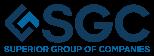
Subcontracting
SGC expects its Suppliers to provide transparency into their operations, policies, processes, and relevant records to SGC or its designated third party. Suppliers are required to disclose in writing to SGC conditions that are or may be in conflict with anything in this Manual or any applicable Laws in facilities that produce, store, or handle SGC products or provide services to SGC.

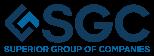
Subcontracting
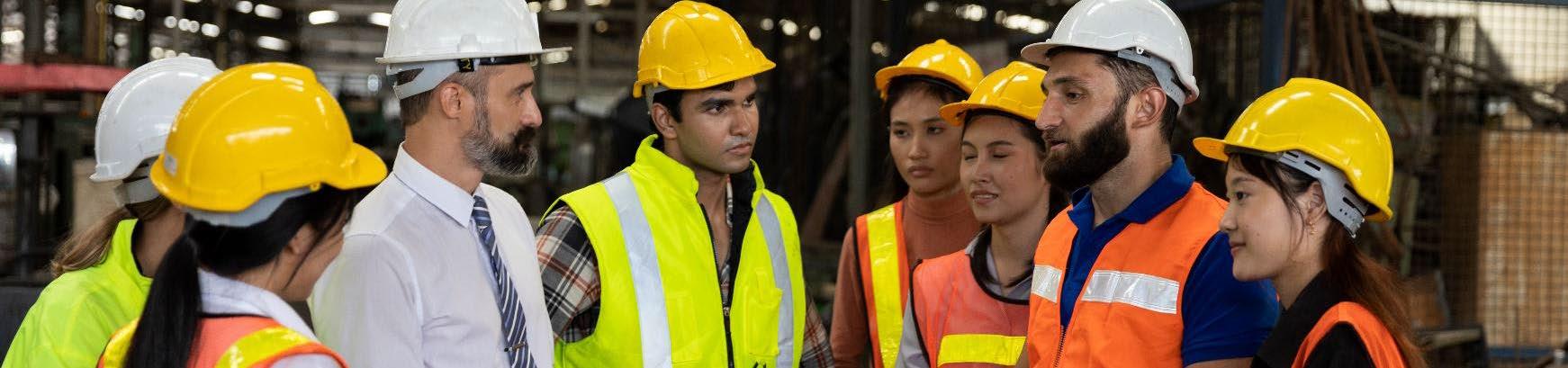
Any proposed change from one factory to another or the use of subcontractors must be approved by SGC in writing before production begins.
Any Supplier of SGC that uses a subcontractor, even if approved by SGC, shall be responsible for the acts and omissions of its subcontractor(s), including, but not limited to, any violation of SGC Manual by the subcontractor.
Any Supplier that utilizes subcontractors without the prior approval of SGC will be subject to order cancelation upon, and for a reasonable amount of time after, SGC becomes aware of the use of the unapproved subcontractor. SGC shall not be required to compensate Supplier for any services performed or products provided (or which are in process) by an unapproved subcontractor.
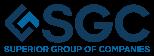
Definition of Subcontracting
• Producing finished merchandise (consumer ready items) where substantial manufacturing occurs.
• Production operations outsourced such as coating, dying, drying, bleaching, laminating, embroidery, printing and sewing, etc.
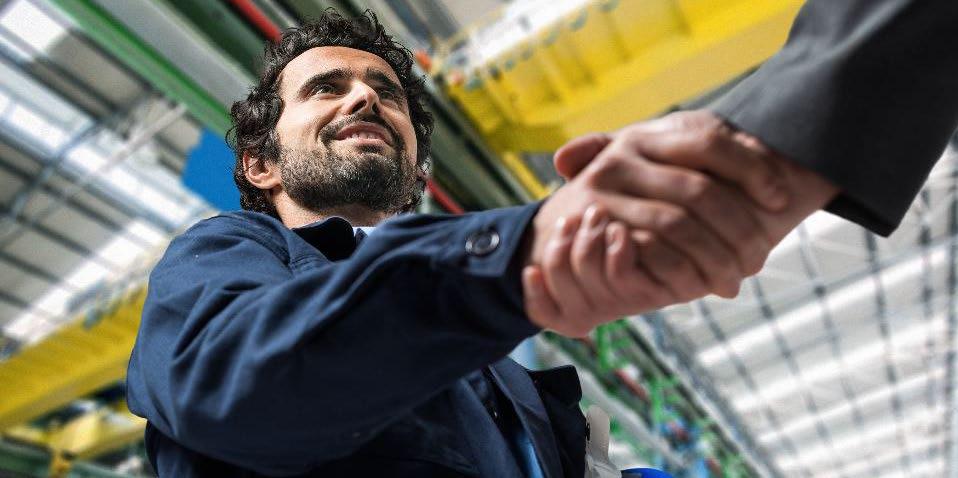
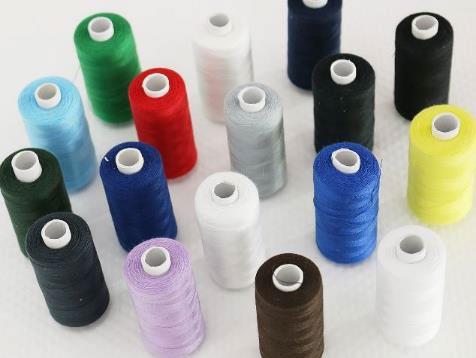
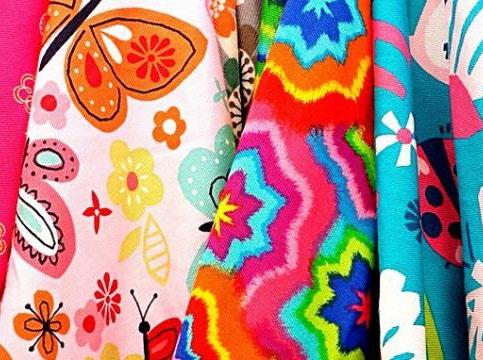
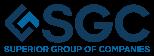
Business Integrity, Anti-Corruption, Anti-Bribery
SGC expects its Suppliers to conduct business responsibly and with integrity, honesty, and transparency.
Corrupt arrangements with customers, suppliers, vendors, government officials, or other third parties are strictly prohibited.
“Corruption” generally refers to obtaining, or attempting to obtain, a personal benefit or business advantage through improper or illegal means.
Suppliers shall implement procedures to ensure compliance with anti-corruption and anti-bribery Laws, including the United Kingdom Bribery Act and the United States Foreign Corrupt Practices Act, when applicable.
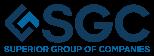
Business Integrity, Anti-Corruption, Anti-Bribery
Suppliers shall implement procedures to ensure compliance with anti-corruption and anti-bribery Laws.
A FACTORY MUST:
• Have a written policy on anti-bribery & corruption
• Communicate & train all employees about antibribery & corruption
• Develop a system to discuss employee concerns about anti-bribery & corruption
• Develop a written procedure in the event of bribery and corruption
• Record disciplinary measures for attempted bribery cases or corruption practices
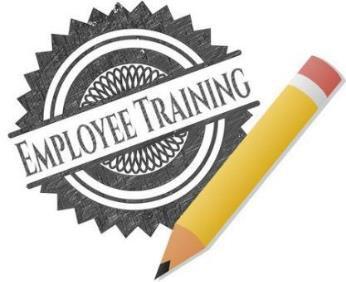
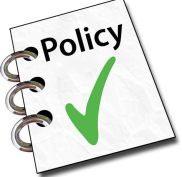
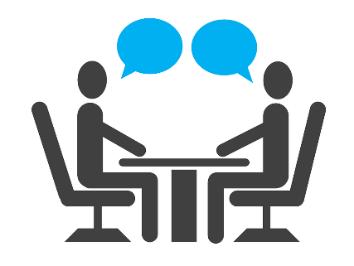
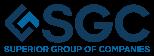
Human Rights, Recruitment, Forced Labor, Wages
• SGC will not tolerate the use of child labor in any of its global operations or facilities.
• SGC will not tolerate the use of any forced or involuntary labor, either directly or indirectly, by any of SGC’s Suppliers or any of their suppliers or vendors. This includes the use of slave labor, bonded labor, indentured labor, or involuntary convict labor. Nor will we tolerate the trafficking, physical punishment, or abuse of any worker.
• As part of the hiring process, workers must be provided with a written employment agreement in their native language that contains a description of terms and conditions of employment prior to the worker departing from his or her country of origin. Workers cannot be required to surrender their identity papers or other original personal documents or pay deposits as a condition of employment.
• Suppliers must pay wages and benefits that meet or exceed the legally required wages and benefits or, where no wage or benefits Laws exist, the local industry standard.
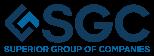
Corrective Action & Preventative Action (CAPA) Plan
SGC will work with the factories to close findings using a 5-step process. A customer registered factory must submit their corrective actions thru a customer’s portal within the required timeframe to avoid penalty. The CAPA plan is to allow the factory to detail how they intend to resolve a findings. SGC will review and may revise any responses according to customer’s requirement before submission.
Policy
Step 1
Communication
Step 2
Training
Step 3
Monitoring
Step 4
Governance
Step 5
Establish a written policy & procedure describing course of action to protect the health & safety and rights of employees, community and environment.
Inform the responsible workers about the policy/procedure or legal requirements.
Establish a training program for senior management and responsible employees.
Monitor the policy/procedure by establishing a checklist or daily tour of the factory.
A supervisor, General Manager or Human Resources to govern and ensure policy implementation.
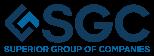
Corrective Action & Preventative Action (CAPA) Plan
Review the root cause of the non-compliance finding to prevent re-occurrence. Apply immediate action to correct the finding and review a 5-step process to close a finding. Some findings may require documented evidences as proof of corrective action.
Root Cause
Analyze
• Analyze the root cause to prevent a finding from happening again.
• Examples are but not limited to:
• No authorized staff to monitor the implementation of policy.
• Lack of training of responsible staff.
• Lack of system to make certain all responsible staff has understanding of the policy and requirements.
Immediate Action
Solution to the issue
Communication
Document
• Is either a short term or permanent corrective action depending on the finding.
Examples of documented evidences are, but not limited to –
• 2 - 4 Photographs
• Certificates
• Completed Checklist
• Licenses
• Training Attendance Sheets
• Employee Time Cards
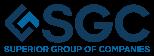
Examples of responses to Corrective Actions
Root Cause
No Safety Data Sheet Posted
Immediate Action
No Fire Drill
Poor Response
We are not aware MSDS is required.
Poor Response Pending schedule
Communication
Missing Eye Guards On Sewing Machine
Poor Response
Employees are reminded to check their machines before use.
Correct Response
Lack of policy and procedure to identify chemicals and to post Material Safety Data sheets on bulletin outside of Chemical room.
Correct Response
Fire Drill is scheduled on June 15, 2022. Compliance Coordinator schedules & records regular fire drills every 6 months.
Correct Response
New hires during orientation & current employees are trained yearly on machine inspection prior to use to ensure eye guards are in place. In the event of missing eye guard, notify their immediate supervisor for correction.
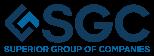
Factory Change of Status
It is the responsibility of the Supplier/Factory to notify SGC immediately in the event of the following:
• Change of factory manufacturing locations
• Closing business with factory manufacturing locations
• Major construction or renovation at factory manufacturing locations
• Catastrophic event affecting factory manufacturing locations (fire, flood, tsunami, typhoon, power outage, infrastructural damage, etc.)
• Restrictions on production to meet air/water quality requirements at factory manufacturing locations
• Strikes, other worker protests, government closure/seizure at factory manufacturing locations.
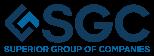
Vendor Profile
A vendor must fill out & submit a yearly Vendor Profile to track social compliance of current and new factories for SGC production.

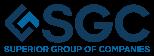
Supplier Quality Assessment
A new factory must be visited, assessed & approved by Director of Fabric Sourcing & Testing prior to production.
Attached is image of SGC Supplier Quality Assessment form used during an onsite visit of a factory.
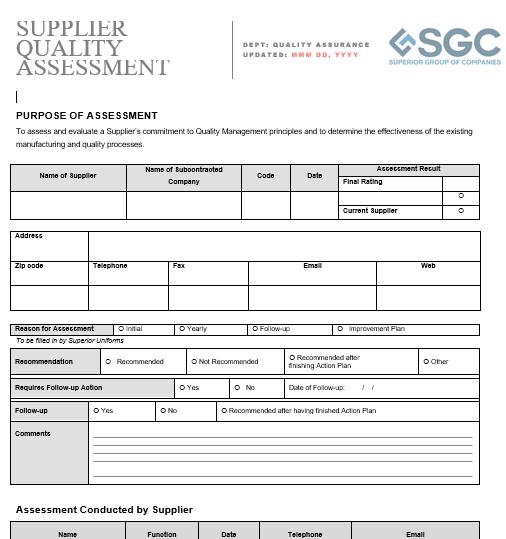
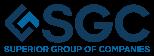
Cotton Traceability Requirement
Flowchart of Production Process
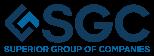
Cotton Traceability Requirement
Examples of supporting documents for the source of cotton include, but are not limited to affidavits from:
• The origin of raw cotton
• Factory that ginned the raw cotton, which includes input and output information to verify no other cotton was used in the process
• Yarn and/or thread producer regarding the origin of the cotton bale
• Where and who spun the cotton
• Where and who wove the greige fabric (e.g. documents which trace the bale)
• Where and who made the finished fabric
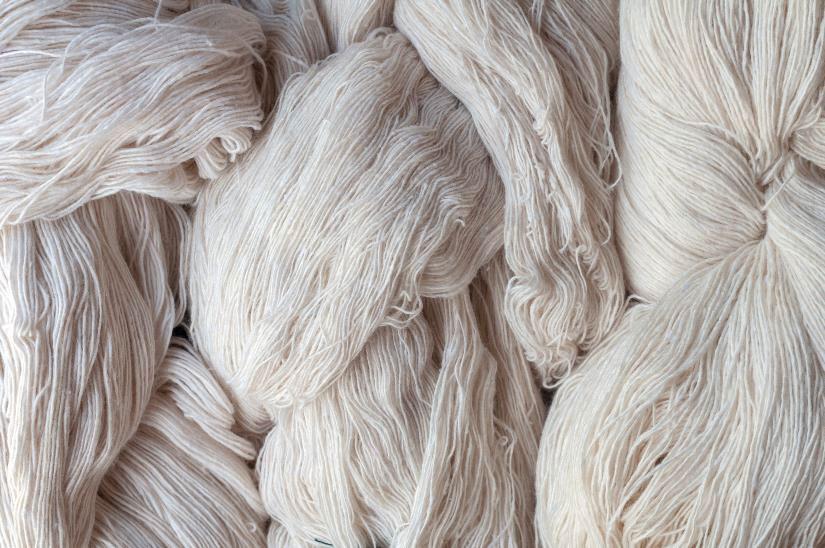
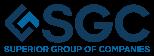
Cotton Traceability Requirement
Evidence Pertaining to Overall Supply Chain
Detailed description of supply chain including imported merchandise and components thereof, including all stages of mining, production, or manufacture.
The role(s) of the entities in the supply chain, including shippers and exporters: for example, CBP will need to determine whether a supplier is also a manufacturer.
A list of suppliers associated with each step of the production process, including names and contact information (addresses, email addresses, and phone number).
Affidavits from each company or entity involved in the production process.
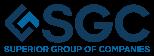
Cotton Traceability Requirement
Purchase Orders
Evidence Pertaining to Overall Supply Chain
Fabric Suppliers
Commercial Invoice and Packing List
Bill of Lading
Scheduler gives a “Work Order” to production as a task
Production Contract
Fabric Production Records
Threads/Yarn
Inbound & Outbound
Fabric Certificate of Origin
Invoice & Proof of Payment Foreign Customs Clearance Documents
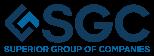
Cotton Traceability Requirement
Evidence Pertaining to Overall Supply Chain Purchase
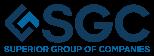
Cotton Traceability Requirement
Evidence Pertaining to Overall Supply Chain
Raw Material Suppliers (Cotton, Hemp, etc.)
Purchase Orders Production Contracts Commercial Invoices
Packing Lists
Proof of Payment
Certificate of Origin
Declaration Forms and Way Bills Foreign Customs Clearance Documents
Delivery Orders
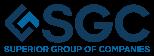
CBP Supply Chain Tracing Information
• Documents must be translated into English;
• Documents must be well organized – indexed and contain an explanation of the relevance of the documents provided.
• Each document must be labeled and organized alphabetically.
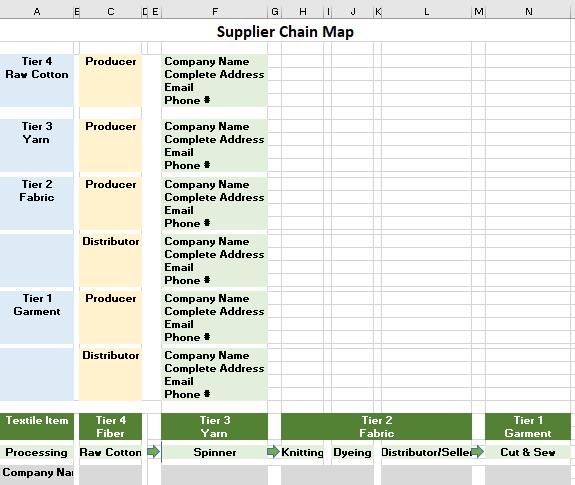
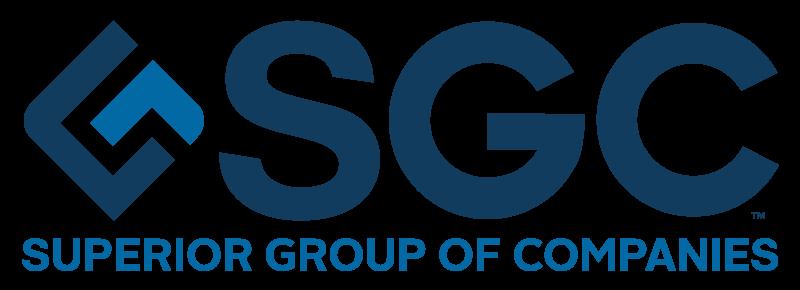
https://www.surveymonkey.com/r/MPJWRFP
Charles Sheppard
Senior Vice President, Supply Chain
Email: csheppard@superiorgroupofcompanies.com
Edwin Lee
Vice President, Sourcing, CID Resources & FSH
CONTACTS
Email: elee@cidresources.com
Jay Ogburn
Vice President, Inventory Management & Sourcing, Branded Products
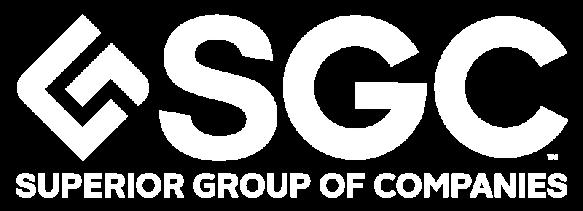
Chris Flinn
Global Production Administrative Manager
Email: cflinn@superiorgroupofcompanies.com
Markus Haerri
Director, Fabric Sourcing and Testing, Sourcing
Email: mhaerri@superioruniformgroup.com
Email: jogburn@superiorgroupofcompanies.com
Joyce Zafra
Production & Compliance Coordinator
Email: jzafra@superioruniformgroup.com
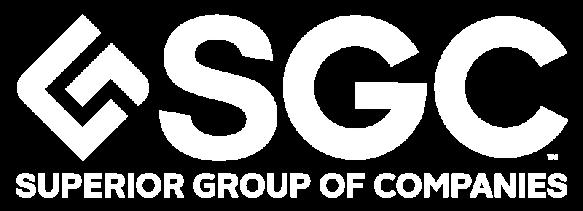
References & Sources
Bing for online pictures
SGC Vendor Compliance Manual
SGS audit platform
U.S. CBP pictures
U.S. CBP website
HireAPartner training
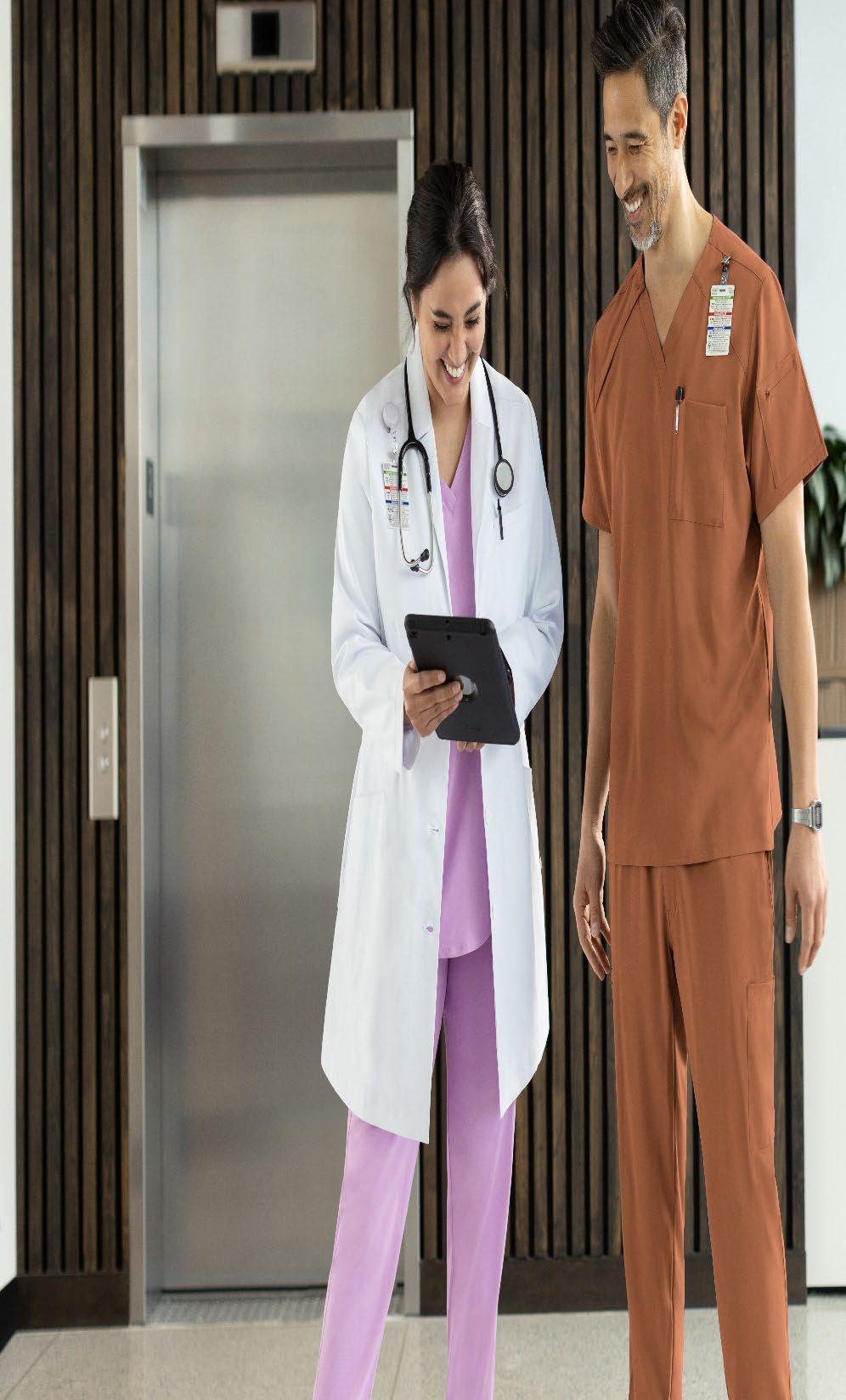