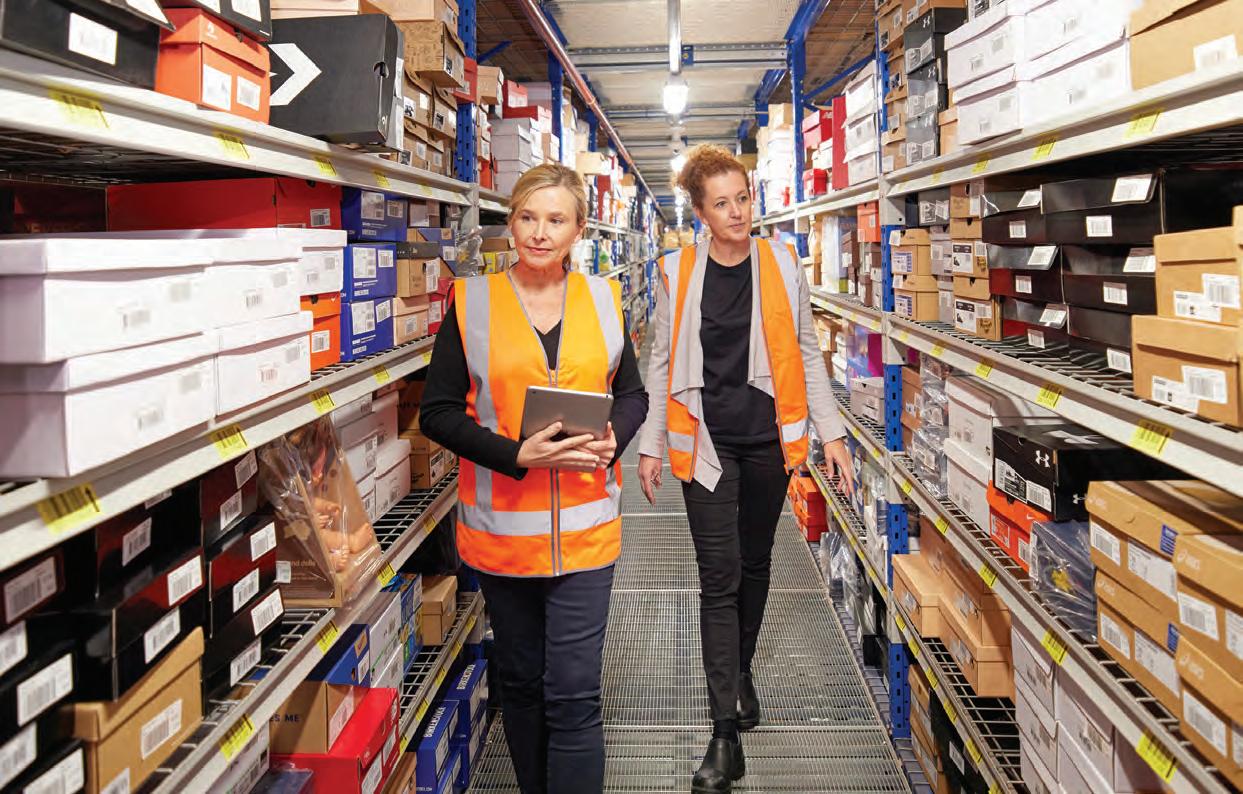
5 minute read
How innovation can save warehouse tenants millions in reduced leasing costs
by CILTNZ
The logistics property market is struggling to cater for the growth in e-commerce as well as other business sectors. Therefore, the way in which facilities are designed, built, and operated must change. Photos: Prological
Future-proofing organisations’ greenfield sites by engaging with a combination of design, architecture, and logistical experts at the beginning of the build process will be crucial to counteracting the impact of rising rent prices and low land availability.
So says supply chain consultancy Prological in its newly published whitepaper ‘Rethinking warehouse design: Integrating innovation, from concept to delivery’, which discusses pressures of the industrial property market, as well as the limitations of traditional approaches to new warehouse and freight depot development.
“With a significant number of Greenfield sites due to be developed in the next five years, we want to share the key principles to help organisations future-proof their operation and counteract the impact of rising rent prices and low land availability,” Managing Director and Founder Peter Jones says. how this new way of thinking can reduce tenant costs and expand developer return on their assets, while bringing relief to the constrained property market in Australia and New Zealand’s larger cities.
For clarification, greenfield sites are undeveloped areas within or outside a city, typically on agricultural land. They are often sought after for the construction of manufacturing plants and other commercial projects because they are uncomplicated and straightforward for construction.
Advantages of such a location includes design flexibility for meeting project requirements; room to expand for future growth; and construction timelines are typically faster. However, infrastructure installation is often required due to its location away from the city and its services, meaning workers also have to commute further.
On the other hand, brownfield sites are abandoned, underutilised or contaminated properties. Redeveloping these properties into productive projects mitigates environmental impacts, provides tax revenue and improves the social foundation of these communities. However, brownfields may take longer to develop and could involve more risk.
By 2026, the total value of investment-grade industrial property in Australia is set to surpass the office sector, by which time the Australian industrial and logistics industry is forecast to reach $424 billion, the whitepaper states.
Here in New Zealand, the Reserve Bank estimated our commercial property stock is estimated to be worth approximately $180 billion back in 2015, about a quarter of the value of residential property. Interestingly, the Government announced that interest on residential mortgages will no longer be taxdeductible in 2021; a policy that will be phased in over the next four years. This will have a significant cash-flow impact on residential investors, particularly those who are highly leveraged.
According to NAI Harcourts, this policy – along with a string of others such as the Bright Line Test and the Healthy Homes Act – have made the residential property market less appealing: “Some investors are exiting the sector and
looking at commercial/industrial real estate as a more viable option.”
“In 2022, we expect industrial rents and values to continue to move forward, although it is still too early to determine the impact of rising interest rates on everdecreasing yields. Market sentiment in the residential arena has softened, and it remains to be seen if this will flow over into other asset classes such as industrial property. For the short term at least, the music looks set to keep playing.”
Prological believes innovation in this environment is critical as occupier costs have reached record highs, as have rents for both super prime and prime grade assets. The logistics property market is struggling to cater for the growth in e-commerce as well as other business sectors. To address these issues, the way in which facilities are designed, built, and operated must change.
“Until now, the most common process for site development begins with estimating the footprint of the facility, choosing an adequate size property site, with consideration of the internal workflows and fit-out last,” the whitepaper states.
“However, with the rapid pace of innovation, scarcity of available land and the proliferation of agile automation, this approach is no longer optimal. Indeed, it has always been flawed, but now the consequences of this flawed approach are more profound.
“Today, traditional warehouse layouts are no longer fit for purpose and rents are driving costs in the wrong direction, while innovative architecture and engineering are introduced too late in the current development process, if they are introduced at all.”
Innovation, therefore, must come down to answering a few questions:
• What if the fit-out and detailed workflows were designed first, and the building was designed next, both before the land was even looked at?
• What if automation and its infrastructure requirements were considered early and designed as an integrated component of the building?
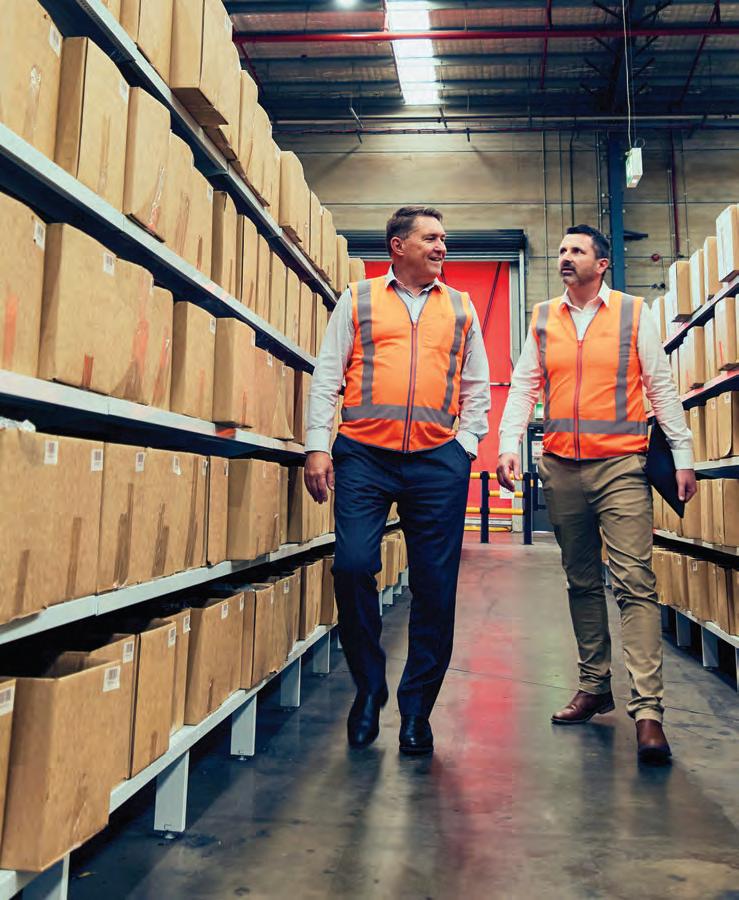
• What might it mean to build vertically, not just horizontally?
Next generation answers to these critical questions result in reduced land requirements, reduced building costs and in turn, reduced rents. While this approach provides the tenants with a much better outcome, it also provides developers with more revenue, while providing Logistics/ Industrial Real Estate firms with more transactions to prosecute, creating more revenue for the sector.
The whitepaper highlights several additional operational and personnel benefits for early adopters of this ‘next generation’ design including:
• Increased sustainability through warehouse positioning, thermal efficiency, reducing heat footprint and leveraging natural sunlight, of course with solar power, but that is just the start
• Improving customer experience with faster, more accurate delivery times
• Attracting, retaining, and optimising staff through human centric design
• Reduced travel time by optimising production and work zones from the outset (50-60 per cent of traditional warehouse staffing costs) The whitepaper examines how a commitment to innovation from the outset can produce significant benefits for customers who are faced with increasing market pressures. As land prices continue to increase in both Australia and New Zealand, materials handling designers are recognising that there is an opportunity to design vertically rather than horizontally.
“This is not just about going higher, but also value engineering the building and its more complex elements to support volumetric utilisation, optimisation of automation integration, shorter walking distances, and creating a more people-centric work environment all while lowering both CapEx (and subsequent rents) as well as the overall OpEx.”
Traditional warehouse layouts are no longer fit for purpose and rents are driving costs in the wrong direction, states Prolgoical's whitepaper.
To read the white paper in full, see https://indd.adobe.com/
view/997d00b8-f677-433a-a49a-
57456343e861.