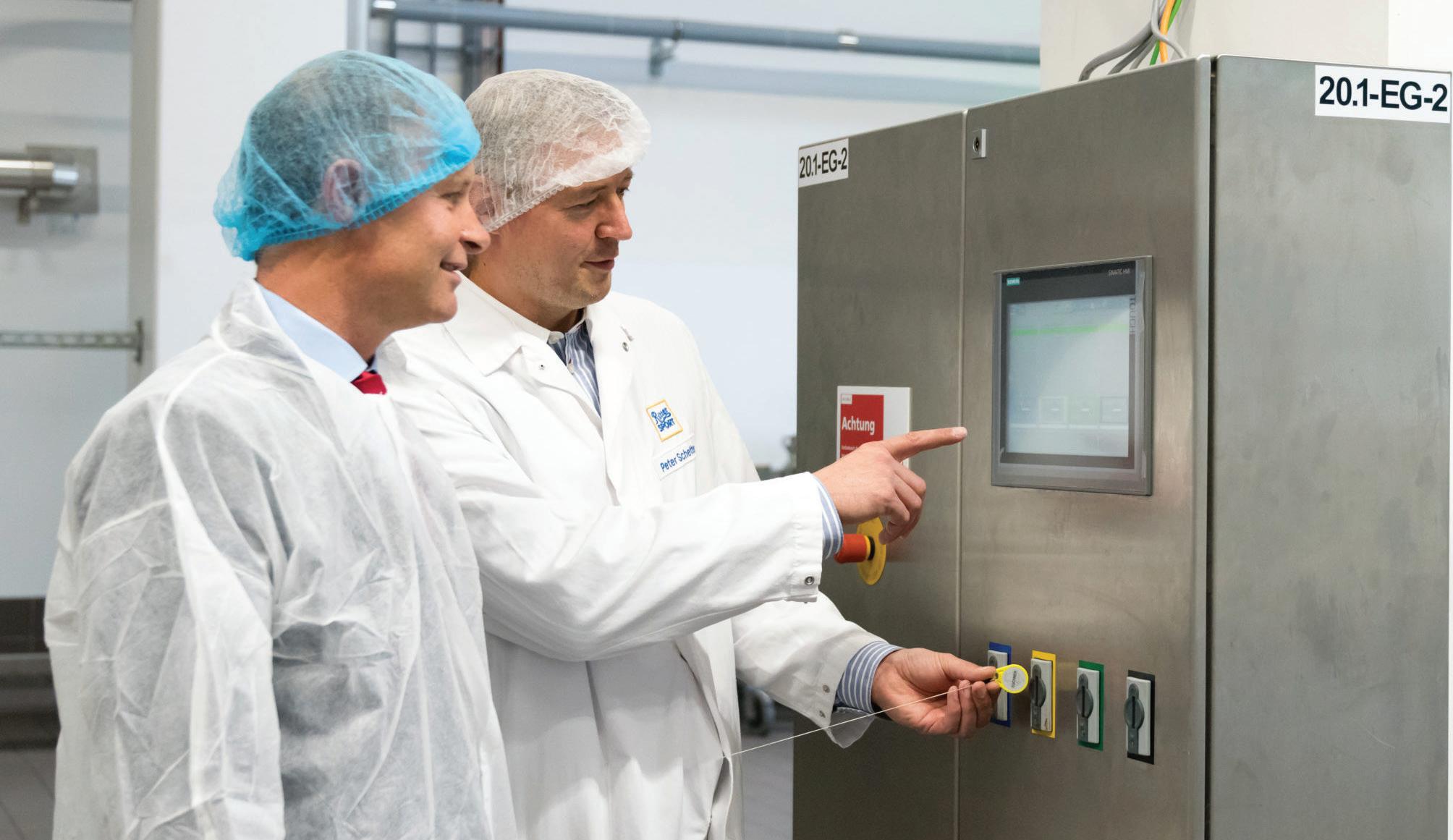
5 minute read
Have passwords had their day in factory operations?
David Dearden, UK&I Country Manager of safety specialist Euchner, offers a compelling argument for considering alternatives to passwords in factory operations. He presents a secure alternative - the Electronic Key System, capable of protecting people, processes, and increasing product safety in manufacturing and process industries.
In the age of industrialised digitalisation, the significance of managing processes and ensuring the safety of equipment and operators in modern manufacturing and process industries cannot be understated. For years, passwords have been the go-to method for access control and security in factories, with HMIs, touchscreens, industrial PCs, and robot controllers relying on login options and access levels based on passwords. However, as technology evolves and the demand for total traceability and transparency grows, questions arise around the efficacy of passwords in meeting these stringent requirements.
The pitfalls of passwords
Passwords, if used and managed effectively, can be a robust security tool. The key lies in ensuring they are not revealed, shared, or hacked. Unfortunately, human errors are common, leading to insecure practices like writing passwords on control panels, compromising product safety. Furthermore, poor password security can lead to the replication of passwords throughout the production lines, creating potential hazards where shared passwords can jeopardise individual traceability.
Moreover, many systems fail to automatically log users off after inactivity, enabling unauthorised access. For instance, incorrect recipe management due to open sessions can have severe safety implications in the food and beverage or pharmaceutical industries. As industries move towards more demanding traceability requirements, accurate identification of operators at specific times becomes paramount. Traditional password systems may not provide the necessary level of security and traceability in this environment.
The rise of electronic key systems
To address these challenges and enhance security and traceability in manufacturing processes, Euchner proposes the use of RFID-based Electronic Key Systems (EKS). Unlike passwords, electronic keys offer a secure solution for access control and data management while maintaining traceability within the existing plant control system.
EKS provides uniquely colour-coded inductive key tags that enable or control multiple processes, ranging from operations to maintenance, and even hazardous mode selection. The flexibility and versatility of an EKS makes it an ideal choice for manufacturing facilities seeking an enhanced level of safety for employees and customers alike.
The main advantage of Euchner’s EKS lies in its programmability, offering adaptability to various tasks within a manufacturing or processing facility. Some key features and benefits of EKS includes:
• Individual authorisations: The EKS allow for the precise assignment of individual authorisations to specific personnel, enhancing security and accountability.
• Traceability: The system facilitates tracking of actions and events, allowing manufacturers to identify who performed specific tasks and when.
• Recipe and batch management: EKS enable the saving and recall of recipes, batches, and other process parameters, ensuring consistent and high-quality product output.
• Electronic signatures: The system supports electronic signatures, streamlining authentication processes and increasing data integrity.
• Fast user profile switching: The EKS enables quick and secure switching between user profiles, minimising the risk of errors during equipment setup and operation.
• Customisable ergonomic/language data: Electronic keys can carry ergonomic and language data, allowing operators to set up their workplaces individually, reducing the likelihood of mistakes.
• Data acquisition for enterprise resource planning: The EKS facilitates data acquisition for efficient enterprise resource planning, enhancing overall productivity.
Enhanced safety and efficiency
The EKS significantly improve safety and efficiency in factory operations. With fast and secure switching between recipes, user profiles, and data, operators save time when moving between equipment or changing parameters. Additionally, the system’s colourcoded keys simplify identification, with different keys assigned to operators, access levels, or specific products.
By assigning process parameters to individual keys, EKS ensures product quality, preventing the use of incorrect settings and potential hazards. The systems are also invaluable in multi-language settings, allowing operators to easily select their preferred language, reducing errors and improving communication.
Robust design for challenging environments
The tag readers in the EKS are housed in compact, robust, and hygienic units, making them suitable for harsh industrial environments. These units offer a high ingress protection rating, including IP69, ensuring compatibility with cleaning-in-place (CIP) applications and high-pressure jet spray cleaning in food processing plants. The EKS can be configured to ensure correct CIP and maintenance procedures, saving costs and energy and enabling individual traceability of cleaning activities.
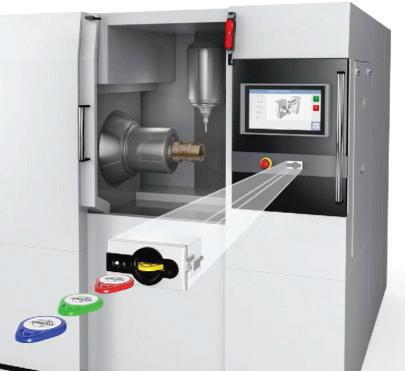
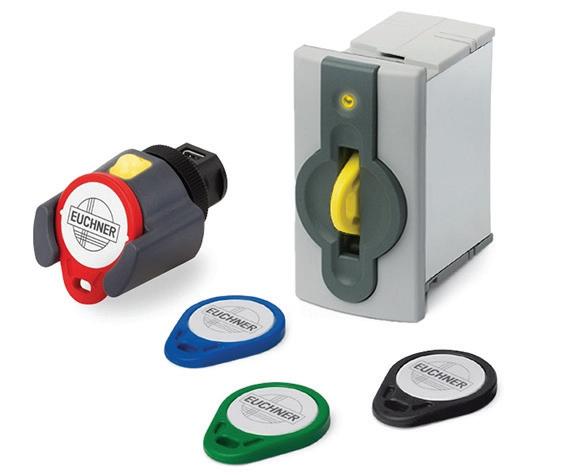
All crucial information, including batch codes and process parameters, can be stored in a central database. This ensures reliable data tracking and traceability. Unlike magnetic-coded swipe cards that can lose data, EKS tags are immune to such vulnerabilities. Moreover, in case of a lost or stolen tag, it can be blocked without the need for reprogramming the entire system.
While biometric and machine vision technologies are gaining traction as password replacements, they may not be suitable for all factory settings. For instance, fingerprint readers may face challenges in environments where operators wear gloves or have dirty fingers. Electronic keys, on the other hand, provide a flexible and effective alternative, eliminating human error and increasing safety across various systems and processes.
Electronic Key Systems in action
For one of the leading chocolate manufacturers in Europe, precise and safe delivery of the raw ingredients is essential, but unloading them is a complex operation and errors are costly. A total of 32 key-operated rotary switches would normally be necessary to direct the raw ingredients to the right station in the manufacturing plant. However, thanks to Euchner’s Electronic Key System, this number has been reduced to just four read stations, making the process of receiving the new raw ingredients into the warehouse much more effective. The confectionery industry is yet another food and beverage sub-sector where the EKS wins a (chocolate) gold medal.
Euchner’s innovative EKS not only makes the process of transferring the raw ingredients considerably safer but also significantly more efficient. All tasks are now carried out by one system with just four read stations, rather than a complex system requiring multiple keyoperated rotary switches and the potential for errors the original control system created.
The EKS works using an electronic key and a corresponding key adapter. The electronic key contains a transponder with data memory that allows it to transmit data without using any contacts to the read head. In contrast to conventional installations with key-operated rotary switches, it is not necessary to replace the entire system if one key is lost. This isn’t a problem with the EKS, which allows the customer to generate a new electronic key with just a few clicks.
The flexibility and features of the EKS system were taken advantage of during the integration of the system in the company’s new raw ingredients warehouse. The process is simple, when the raw ingredients arrive by truck, an EKS chip is issued, allowing the employees to unload the delivery at the right receiving station and into the right container. Each receiving station, path and target container has its own corresponding programmed and numerically marked chip, whose code is read by the RFID readers, which are connected via PROFINET for easy integration into the original control system.
The information is then stored in a central database, ready to be processed by the ERP and recipe systems.
Euchner’s EKS is currently responsible for managing the entire raw ingredients warehouse and all of the elements and PCs associated with it. “We hope to soon use the system for our production computers as well,” said the company’s head of electrical engineering, who was responsible for the implementation of the new technology. He added: “The EKS is user-friendly, reliable, forward-thinking, safe, easy to configure and manage, and good value.” Plans have already been drawn up to expand the application of the EKS into the production areas because the solution has proven so successful in the ingredients warehouse.
A secure alternative
Passwords have served as a common access control mechanism in modern manufacturing facilities. However, with the rise of industrialised digitalisation and increased traceability demands, it’s becoming clear that alternative solutions are needed. Euchner’s EKS presents a secure and versatile option for managing processes, protecting people, and enhancing product safety in manufacturing and process industries.
The EKS provides individual authorisations, traceability, fast user profile switching, and a range of other features to streamline operations and improve efficiency. A robust design, combined with a centralised database and colour-coded keys, ensures enhanced safety and security while minimising the risk of errors. As the industry continues to evolve, the EKS solution emerges as a reliable solution to meet the ever-growing demands for safety and traceability in factory operations. www.euchner.co.uk