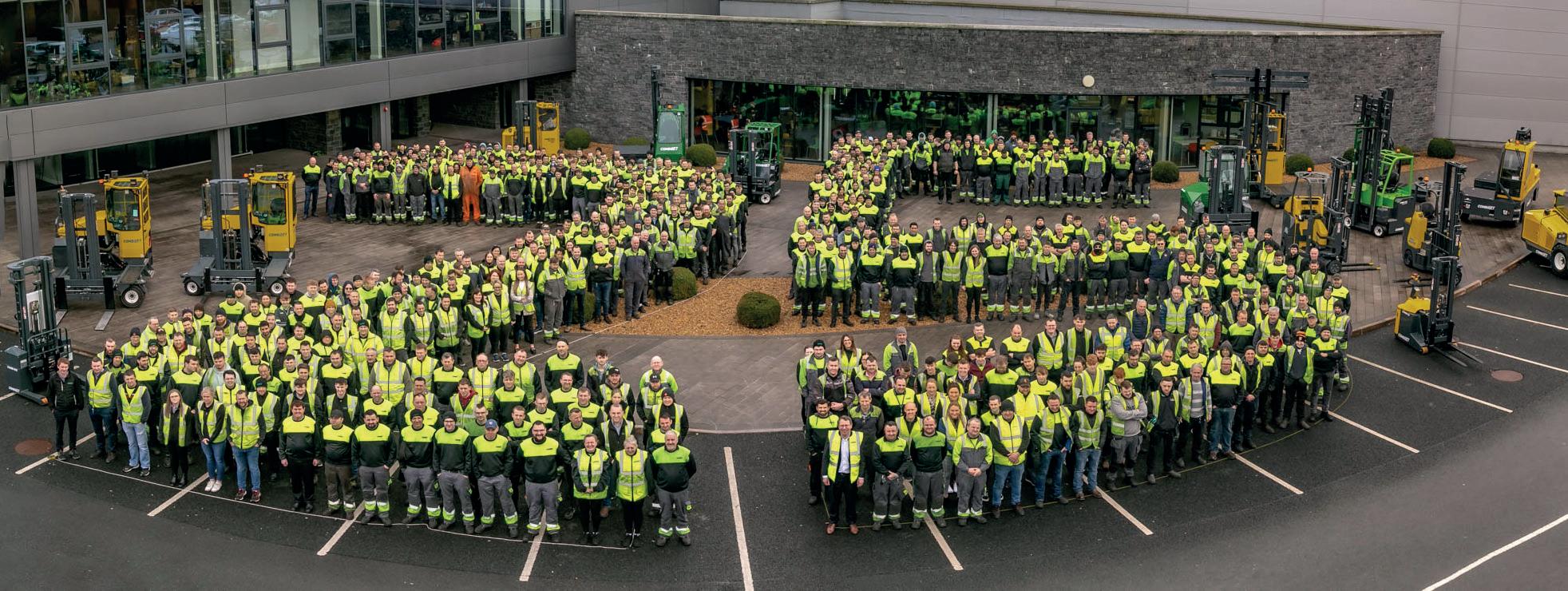
4 minute read
A quarter century at the forefront of forklift truck innovation
As handling solutions specialist Combilift celebrates its 25th anniversary, MEPCA spoke to the company’s Managing Director, Martin McVicar, about how its customers’ needs have evolved over that time and how its solutions have developed to meet those needs.
MEPCA: When you founded Combilift in 1998, what were the key challenges facing the users of load-handling solutions and, in particular, forklifts?
Martin McVicar: The mainstream forklifts on the market at the time - reach trucks, counterbalance forklifts and sideloaders, could each carry out a specific task, such as offloading from delivery trucks, putting goods into racking and carrying loads across large distances, but did not lend themselves well to other truck’s tasks. Added to these limitations was the fact that they could only travel either forwards or in reverse. This made the handling of long and bulky loads problematic, particularly in tight spaces. Getting a 6m long load through a 3m wide doorway, for example, involved a lot of risky and tricky juggling and manoeuvering, if it was at all possible.
M: How did Combilift’s solutions overcome those challenges?
MV: Feedback from contacts and potential customers in the materials handling sector indicated the opportunity for us to develop a niche versatile one-truck solution to replace multiple types of forklifts and enable the safer, space-saving and, therefore, more productive handling of long and bulky loads.
So the Combilift C4000 3-wheel, all-wheel drive multidirectional forklift was born. As its name implies, as well as forward and reverse, sideways travel was also possible thanks to push button change of wheel direction. The lateral transportation of oversized products suddenly became much more straightforward, and companies could reduce the number of forklifts needed, which led to reductions in capital expenditure, insurance premiums, fuel consumption and maintenance costs. Our aim was to help companies do more with less, so to speak, and this has proved to be the case. A further major benefit our solution offered was the much better use of available space as aisle widths in storage areas, and production facilities could be narrowed down to pretty much the depth of the truck, whatever length of load was being carried. Space has become an ever more valuable commodity, and optimum use of it can avoid costly and disruptive expansion and relocation of premises in times of growth. Customers in many industry sectors have also been able to buy and store raw materials in bulk quantities for more costeffective purchasing, which enabled them to be competitive on price for their customers. The ability to rest potentially dangerous loads on the integrated platform of the multidirectional models for stable low-level transportation also contributed to enhanced occupational health and safety practices.
M: In the 25 years since those first machines were launched, how have the market’s needs evolved, and how has Combilift adapted its offer in response?
MV: We have closely followed the needs of the market since we launched our original model, and nearly every product we have developed in the past 25 years – and there have been dozens of them – has been the result of direct feedback or requests from customers. Our portfolio now encompasses trucks with lift capacities from just 1t to over 100t, which can handle almost any product that you can think of. Over the years, we have seen an increase in the size of products that companies want to manufacture and move, the offshore and green energy sectors being good examples. We have not only followed the market but have led it too, as we have been instrumental in enabling evolving market needs to be realised due to the development of new models such as the straddle carrier (Combi-SC) and mobile gantry (Combi-MG) ranges. These have solved the challenges of moving the most extreme loads, such as 100m+ long wind turbine blades or machinery for subsea operation that weighs in at over 100t.
M: So, what are the key load-handling needs that the Combilift portfolio meets today?
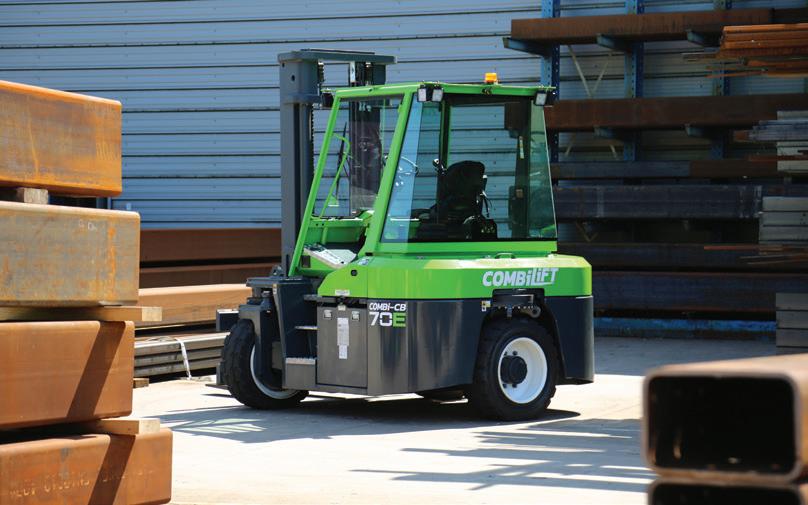
MV: Across every industry, safety is higher on the agenda than it ever was, and our main focus for any new product is to ensure the safest possible working practices. Over the past decade there has been a move towards replacing ride-on forklifts with pedestrian-operated stacker trucks as these are considered to be safer, particularly in busy manufacturing plants. Combilift’s pedestrian models, first introduced around 12 years ago, all feature its patented offset tiller arm, which means that operators are no longer required to be in the dangerous crush zone behind the truck but can now safely operate the truck from the side, where they also have excellent visibility of the load. Our pedestrian range is also not just for lighter capacities; we designed the high capacity Combi-PPT powered pallet truck for Cummins UK, who wanted to enhance operational safety and product flow at its Daventry site when moving 16t assembled engine units from production to the testing and despatch areas.
M: Finally, what does the future hold? What emerging requirements do you see for load-handling solutions in the coming years, and how will Combilift support its customers’ needs?
MV: There is a lot of buzz around automation at the moment, but the reality is that there will always be a need for forklifts with operators, and we are committed to continual development in this sector to ensure that safety is maximised not only for operators but also for surrounding personnel.
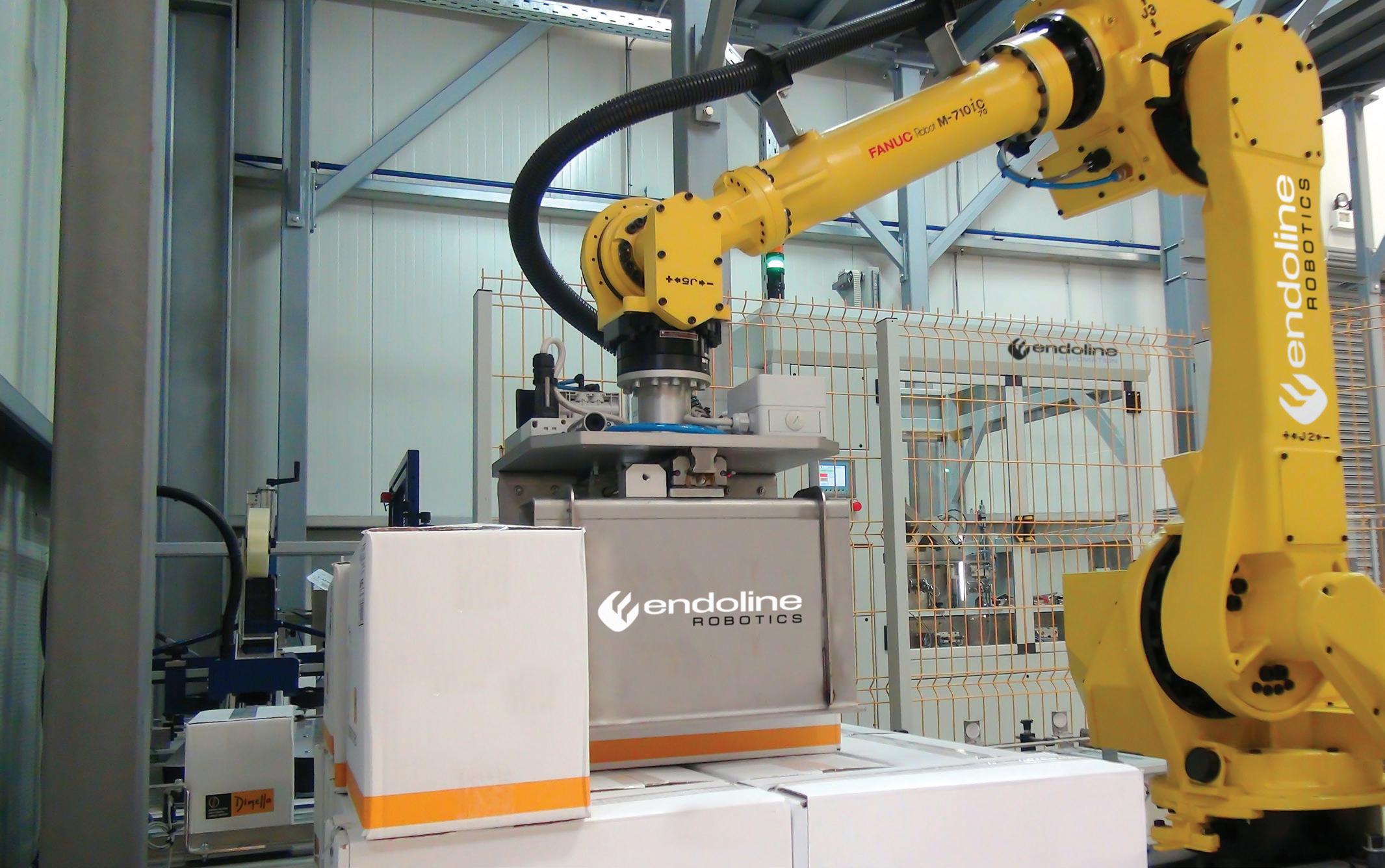
Sustainability is a big issue, and forklift truck users increasingly want to ensure that their carbon footprint is reduced whilst benefitting from powerful and productive performance. The advances in battery technology mean that forklifts will be able to lift ever heavier capacities using electric power. Already this year, Combilift has launched two new electric trucks, with the high-capacity CBE70 opening up an entirely new market segment, while enabling our existing customers to take advantage of electric power in these higher-capacity trucks. More and more customers are looking for emission-free and quiet operation and are therefore switching to electric fleets. Ground engineering specialist Roger Bullivant for instance, has replaced its fleet of dieselpowered trucks with five Combi-XLE 5t capacity electric models, chosen for their ability to efficiently cope with the vast yearly output of around one million metres of precast concrete piles. Currently, 70% of Combilift’s output is electric, and this is set to rise in future. combilift.com