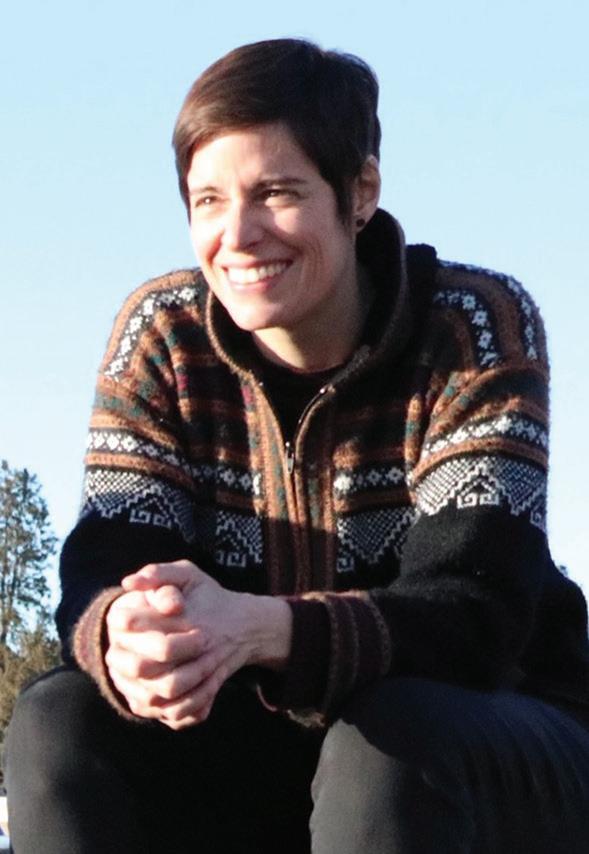
2 minute read
nial Building
by cinnes52
LEADER PROFILE
Karen Rugg: Affordable, sustainable and with beauty
Advertisement
Ashley Bice and I are co-owners of Perennial Building, a women-owned general contracting company based in Sisters, Oregon. Perennial Building provides GC services for new builds, remodels and hemp lime construction, as well as provides consulting for these types of projects. We’re on a mission to foster sustainability, equity and community through the built environment and to build beautiful things along the way.
What most interests you about hemp and hemp building, and why?
I’ve been interested in housing affordability, sustainability and health equity since graduate school. Hemp building has the potential to address all three of these issues. Availability of domestic material supply will need to increase in order to decrease costs, thereby making hemp lime housing more affordable, but once the supply and infrastructure is in place in the US, I believe we’ll have a robust industry that can make great strides in these three areas.
What was a win for your company in the past year?
Perennial Building completed a large material importing transaction that had several road bumps and delays along the way. Now we’re in the position to pull the trigger on a large hemp build without worrying about material delays.
What is something about hemp building/construction/processing you didn’t know a year ago?
Karen Rugg and Ashley Bice are co-owners of Perennial Building, a general contracting company based in Sisters Oregon.
Karen Rugg, co-owner of
Perennial Building
I learn new things about hemp building all the time, specifically regarding the finer details of constructing with it. One of the great things about building with hemp at this moment is there are so many possibilities. It’s a new industry in this country and everyone in the hemp building space is looking for ways to do it as well as possible. This encourages the development of many great building techniques.
What challenges does the hemp building industry face that it must overcome in the next five years?
Three main challenges this industry must overcome are: 1) Education: educating farmers, processors, AEDs, vendors, subcontractors, building officials, and people that live in homes... essentially, most everyone. We need to make hemp building a part of the standard building vernacular in the US 2) Supply Chain: a robust farming and processing infrastructure will need to be developed in order for hemp building to be more easily accessible to those building. 3) Building Certifications: while some jurisdictions will allow for hemp building based on information provided during a specific project’s permitting approval process, this requires additional effort and information on the part of the person applying for the permit. In some cases, this additional information still won’t be enough to convince the jurisdiction to give the okay to build with hemp. Inclusion into standard certifications (i.e. ICC, IRC, et al) will be key to make the permitting process successful across the United States.