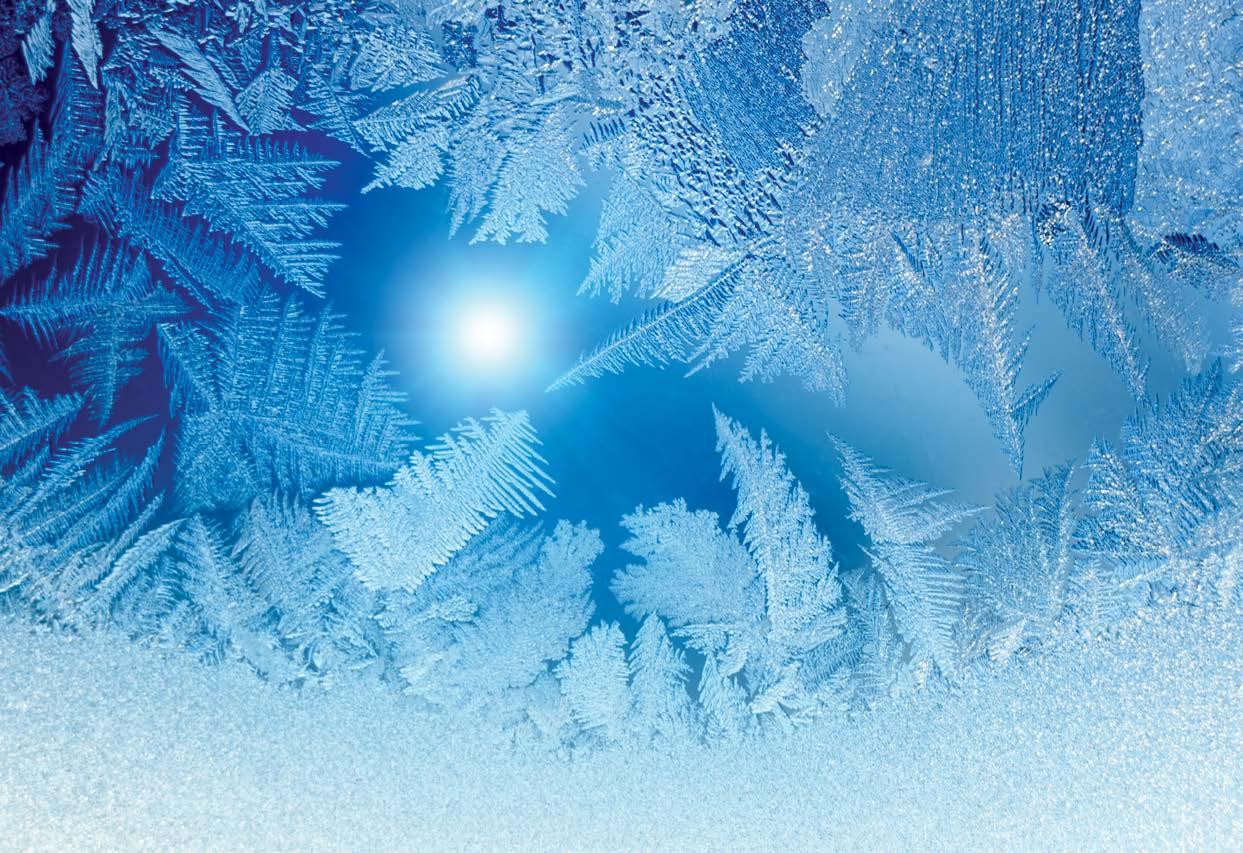
21 minute read
Cold weather concreting
By Pat Cantin, PQS
AUTHOR’S NOTE:
The following article has been assembled in the hopes of summarizing a plethora of winter concrete placement ‘do’s and don’ts’ as a result of my personal experiences from across Northern Ontario in the past 20 years. Some projects went really well, while others were not so well. In the end, the contents of this article are designed to educate and enlighten the reader from my experiences.
EDITOR’S NOTE:
The photograph shown to the right was actually taken from the author of this article, while driving to a construction jobsite in lovely Northern Ontario. The noted outside air temperature (-39°C) does not take into consideration the dreaded wind chill factor, which probably ended up feeling more like -212°C!!!
What is cold weather concreting?
All the reports and articles I have come across essentially provide the following definition of cold weather concreting:
A period when, for more than three consecutive days, the following conditions exist: 1. The average daily air temperature is less than 5°C; and 2. The air temperature is not greater than 10°C for more than one-half of any 24-hr period.
Main objectives to attain during cold weather concreting
If you are a contractor, the last thing you want to hear during the early days of any project are the dreaded words of your Site Supervisor saying to you on a Monday morning that the heaters ran out of fuel over the weekend, or that the site lost power and that the heaters were off-line!
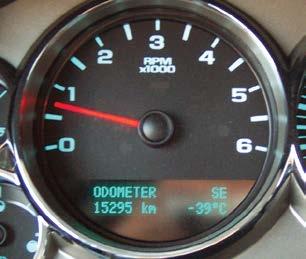
What you are essentially trying to avoid are situations such as: 1. Preventing damage to concrete due to freezing at early ages (within the first 48-72 hours after pouring); 2. Assuring that the concrete develops the required strength for safe removal of forms, for safe removal of shores and re-shores and for safe loading of the structure during and after construction; 3. Maintaining curing conditions that promote normal strength development without using excessive heat and without causing critical saturation of the concrete at the end of the protection period;
4. Limiting rapid temperature changes, particularly before the concrete has developed sufficient strength to withstand induced thermal stresses.
Do not forget that rapid cooling of concrete surfaces or large temperature differences between exterior and interior members of the structure can cause cracking, which can be detrimental to strength and durability. At the end of the required period, insulation or other means of protection should be removed gradually so that the surface temperature decreases gradually.
Interesting fact
The first two days of concrete curing are critical. Should the concrete be overhydrated, you exponentially increase the risk of freezing your concrete. Too little water and you run the risk of accelerating the hydration period, thus potentially exposing your concrete to dry out too quickly. Too much hydration could cool your concrete too quickly. Too many external sources of heat could dry out your concrete too quickly, should you have mass cross-sectional profiles of concrete to pour and place.
Economy scale
Experience has shown and taught us all who have been there that the overall costs of adequate protection for cold weather concreting are not excessive is taken into consideration the costs required to repair frozen or damaged concrete. The contractor must decide whether the extra costs involved in cold weather concreting operations are a profitable investment, or if it is more cost effective to wait for mild weather. My personal experience has shown that one could easily spend up to 20% of the concreting budget on heating/hoarding expenses. Such expenses are proportional to factors such as duration of exposure, degree days, area of hoarding, etc. Consult with your local rental shop for rental rates and fuel consumption ratings of rented equipment. Also consult with your local fuel distributors for their experiences so that you may make an informed decision versus just guessing what you think your jobsite will require.
An interesting note to remember for all you new contractors and QS members: Short-term construction economy should not be obtained at the expense of longterm durability. In other words, when assembling your estimates for winter concrete, heating and hoarding, spend the necessary time and effort to educate yourself about using the right materials in the right locations and for the right durations. Too often (and I am guilty of this also), we attempt to limit the amount of time or materials for winter concrete protection in order to save a buck. There is a saying in French that says: “si ça vaut le temps d’être fait, ça vaut le temps d’être bien fait.” Translation: “If that is worth the time (weather) to be made, that is worth the time (weather) to be done well.”
Planning and scheduling
It is recommended that the General Contractor, concrete contractor, concrete supplier and owner (or architect/engineer) meet to define in clear terms how cold weather concreting methods will be used. This meeting will hopefully provide the group with a basis for the contractor to select specific methods to satisfy the minimum requirements during cold weather concreting. Discuss a plan, agree to that plan and stick to it. Should you need to adjust or re-focus, do the team a favour and keep them ALL informed. Trust me on this. As an owner, I much prefer being informed and consulted as it shows to me that you care about the project and that you have equally expressed an overall interest in the project.
Contractors, consultants and owners alike are almost always faced with the ever-troubling dilemma of whether or not to continue on-site activities during the winter months. For some, this means easily up to six months of the year while for others, this period may be a little as three months.
Plans to protect fresh concrete from freezing and to maintain temperatures above the recommended minimum values should be made well before freezing temperatures are expected to occur. Necessary equipment and materials should be at the work site before cold weather is likely to occur, not after concrete has been placed and its temperature begins to approach the freezing point. If you are attempting to rent or purchase any type of heating or hoarding equipment in the peak of the winter construction season, you will end up spending endless hours you do not have attempting to find materials. What little materials or equipment you do find will likely cost you more than the average. Consult your local rental supplier and discuss your winter needs well in advance.
Protection during fall and spring
During periods not defined as cold weather, all concrete surfaces should be protected from freezing for at least the first 24-hours before and after placement. Concrete protected in this manner will be safe from damage by freezing at an early age. If the concrete is air-entrained and properly cured, the ultimate strength and durability of the concrete will be unimpaired. Protection from freezing during the first 24-hours does not assure a satisfactory rate of strength development, particularly when followed by considerably colder weather. Protection and curing should continue long enough and at a temperature sufficiently above freezing to produce the strength required

for form removal or structural safety. Avoid leaving forms unprotected as per the following photograph. Attempting to schedule a pour when you have a situation such as this only compounds the issue and your relationship with your local concrete supplier.
Temperature records
Here is a little bit of interesting information. The actual temperature at the concrete surface determines the effectiveness of protection, regardless of air temperature. Temperature recording and monitoring must consider the following: a) The corners and edges of concrete as they are more vulnerable to freezing and usually are more difficult to maintain at the required temperature; b) Inspection personnel should keep a record of the date, time, outside air temperature, temperature of concrete as placed and weather conditions.
Temperatures of concrete and the outdoor air should be recorded at regular time intervals, but not less than twice per 24-hour period.
The record should include temperatures at several points within the enclosure and on the concrete surface, corners and edges. There should be a sufficient number of temperature measurement locations to show the range of concrete temperatures. Temperature measuring devices embedded in the concrete surface are ideal, but satisfactory accuracy and greater flexibility of observation can be obtained by placing thermometers against the concrete
under temporary covers of heavy insulating material until constant temperatures are indicated; c) Maximum and minimum temperature readings in each 24-hour period should be recorded. Data recorded should clearly show the temperature history of each section of concrete cast. A copy of the temperature readings should be included in the permanent job records. It is preferable to measure the temperature of concrete at more than one location in the section cast and use the lowest reading to represent the temperature of that section. Internal temperature of concrete should be monitored to ensure that excessive heating does not occur.
Such information will go a long way on any jobsite regardless of its size or complexity.
Heated enclosures
Heated enclosures must be strong enough to be windproof and weatherproof, otherwise, proper temperatures at corners, edges and in thin sections may not be maintained despite high energy consumption. Combustion heaters should be vented to the exterior and they should not be permitted to heat or to dry the concrete locally. Fresh concrete surfaces exposed to carbon dioxide, resulting from the use of salamanders or other combustion heaters that exhaust flue gases into an enclosed area, may be damaged by carbonation of the concrete.
In addition, strict fire prevention measures should be enforced. Fire can destroy the protective enclosures as well as damage the concrete. Does the shelter illustrated in the image below look familiar? Regular inspections (including on weekends) are essential in order to avoid a similar situation from happening on your jobsite.
One other thing to remember when heating and hoarding concrete is that all fuel sources freeze. Propane will turn from a gas to a liquid at around -42°C, diesel fuel will wax or gel at approximately -8°C without the use of winter diesel or diesel conditioners. There are strict regulations as listed within the Ontario Health and Safety Act when it comes to storage of such fuels on any construction site and as such, it would be wise to consult with your local Ministry of Labour representative or the Act should you not be familiar with your limitations.
Exposure to freezing and thawing
If, during construction, it is likely that the concrete will be exposed to cycles of freezing and thawing while it is in a saturated condition, it should be properly air-entrained even though it will not be exposed to freezing and thawing in its final service. The concrete should not be allowed to freeze and thaw in a saturated condition before developing a compressive strength of 24 MPa. Therefore, new sidewalks and other flatwork exposed to melting snow during daytime and freezing during night-time should be air-entrained and protected from freezing.
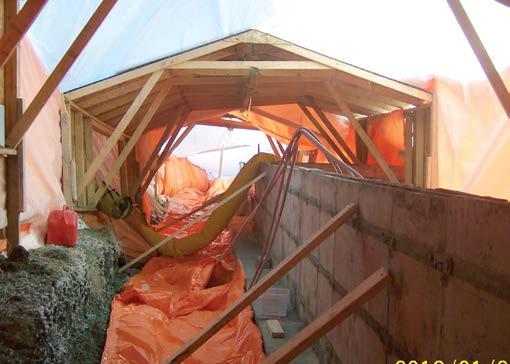

TABLE 1 – Minimum length of protection period for concrete placed during cold weather
Service Category Type I or II cement Type III cement, or accelerating, admixture added 1 - no load, not exposed 2 days 1 day 2 - no load, exposed 3 days 2 days 3 - partial load, exposed 6 days 4 days 4 - full load
Placement temperature
During cold weather, the concrete mixing temperature should be controlled so that when the concrete is placed, its temperature is not below the values identified with CAN CSA 23.1. The placement temperature of concrete should be determined according to the above-noted standards. The more massive the concrete section, the less rapidly it loses heat; therefore, lower minimum placement temperatures are recommended as concrete sections become larger. For massive structures, it is especially beneficial to have low placement temperatures. In addition, higher temperatures require more mixing water, increase the rate of slump loss, may cause quick setting and increase thermal contraction. Rapid moisture loss from exposed surfaces of flatwork may cause plastic shrinkage cracks. Rapid moisture loss can occur from surfaces exposed to cold weather because the warm concrete heats the surrounding cold air and reduces its relative humidity.
Condition of subgrade
Concrete should not be placed on frozen subgrade material. The subgrade sometimes can be thawed acceptably by covering it with insulating material for a few days before the concrete placement, but in most cases external heat must be applied. Experimenting at the site will show what combinations of insulation and time causes subsurface heat to thaw the subgrade material. If necessary, the thawed material should be re-compacted. Far too often have we seen sites prepared to receive concrete during acceptable weather all week long only to see an overnight temperature drop or snow storm arrive just prior to pouring. It is essential to any great team to prepare and be ready for the worst. There is no excuse with today’s technology to get caught in an unexpected storm. From experience, consult more than one weather website on a 24-hour basis at least 48 hours prior to each pour. Review forecasts and radar maps in order to better understand what weather is heading your way. Subgrades can freeze quickly and require considerable efforts to thaw once frozen. Spending the time and effort to keep subgrades from freezing is well worth its weight in gold.
Length of protection period
The length of the required protection period depends on the type and amount of cement, whether an accelerating admixture is used and the service category (Sturrup and Clendening 1962).
Table 1 has been provided to illustrate the minimum length of time concrete placed during cold weather requires protection. The table is only a guideline and as a result, must be used with caution.
For structural concrete, where a considerable level of design strength must be attained before safe removal of forms and shores is permitted, additional protection time must be provided beyond the minimums given.
Category 1: No load, not exposed - This category includes foundations and substructures that are not subject to early load, and, because they are buried deep within the ground or are backfilled, will undergo little or no freezing and thawing in service. For concrete in this service category, conditions are favourable for continued natural curing. This concrete requires only the protection time recommended for Category 1.
Category 2: No load exposed - This category includes massive piers and dams that have surfaces exposed to freezing and weatherings in service but have no early strength requirements. Interior portions of these structures are self-curing. Exterior surfaces will continue to cure when natural conditions are favourable. To provide initial curing and insure durability of surfaces and edges, the concrete should receive at least the length of protection recommended for Category 2.
Category 3: Partial load, exposed - The third category includes structures exposed to the weather that may be subjected to small, early-age loads compared with their design strengths and will have an opportunity for additional strength development prior to the application of design loads.
Stripping of forms
I have witnessed projects where forms were stripped as early as 12 hours after a winter pour while others were left in place for up to three days. During cold weather, protection afforded by forms, except those made of steel, is often of great significance. In heated enclosures, forms serve to evenly distribute the heat. In many cases, if suitable insulation or insulated forms are used, the forms,
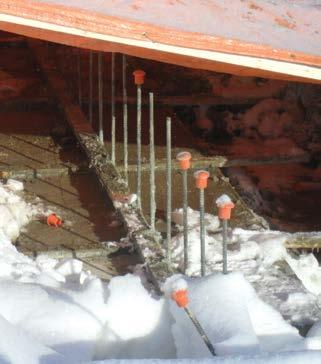
including those made of steel, would provide adequate protection without supplemental heating. As a result, it is often advantageous to keep forms in place for at least the required minimum period of protection. However, an economical construction schedule often governs their removal at the earliest practicable time. In such cases, forms can be removed at the earliest age that will not cause damage or danger to the concrete. I realize this is a loose statement; however, onsite judgement is always best. There is no such rule one can follow that will apply to all circumstances.
After removal of forms, concrete should be covered with insulating blankets or protected by heated enclosures for the time recommended as stated above. In the case of retaining walls, basement walls, or other structures where one side could be subjected to hydrostatic pressure, if one attempts to remove the forms to soon while the concrete is still relatively young, they may dislodge the form ties and create channels through which water can flow.
Insulating materials
Since most of the heat of hydration of the cement is generated during the first three days, heating from external sources may not be required to prevent freezing of the concrete if the generated heat is retained. Heat of hydration may be retained by using insulating blankets on unformed surfaces and by using insulating forms (Tuthill, et al. 1951; Wallace 1954; Mustard and Ghosh 1979). Insulation must be kept in close contact with the concrete or the form surface to be effective. Some commonly used insulating materials include:
Urethane foam - This foam may be sprayed onto the surface of forms making a continuous insulating layer. Good weather-resistant enamel should be sprayed over urethane foam to reduce water absorption and protect it from the deteriorating effect of ultraviolet rays. Urethane foam should be used with caution because it generates highly noxious fumes when exposed to fire.
Foamed vinyl blankets - These materials are pliable blankets of foamed vinyl with an extruded vinyl backing. They also may have electric wires embedded in the foam to provide additional heat. Blankets without embedded wires are available in rolls of standard widths. Heated blankets must be custom ordered.
Mineral wool or cellulose fibers – Generally mineral wool or cellulose fibers are encased in heavy polyethylene liners and formed into large mats or rolls. The plastic liners are sometimes given a rough surface finish to reduce the risk of slipping. They may be laid flat to cover slabs or they may be draped over other structural elements.
Straw - Straw is still popular although it is not as effective as blankets or mats. Disadvantages of straw are its bulk, its flammability, and the need to protect it from moisture. Tarpaulins, polyethylene sheets, or waterproof paper must be used as a protective cover to inhibit wind convection and to keep the straw dry and in place.
Blanket or batt insulation - Commercial blanket or batt insulation must be adequately protected from wind, rain, snow, or other moisture by means of tough, moisture-proof cover material because wetting will impair its insulating value. Closed-cell material is particularly advantageous because of its resistance to wetting.
In Northern Ontario, the common footing and foundation wall insulating materials would be a combination of straw and foamed vinyl blankets. For those of you who have not used straw, then you are in for a real treat. Straw is cheap (usually around $3-$5 a bale) and is locally and readily available in large quantities. Its insulating properties are great.
Another interesting fact
In its plastic state, concrete will freeze if its temperature falls below about -4°C. If plastic concrete freezes, its potential strength can be reduced by more than 50% and its durability will be adversely affected. (NRMCA CIP 27 Cold Weather Concreting).
In closing, I share with you the following common sense tips for concreting in cold weather: a) Discuss with your ready-mix producer their procedures and limitations for cold weather concreting. The use of hot water, heating the aggregates,
increasing the cement content, or adding an accelerating admixture will help you better understand how to prepare on site. b) Order air-entrainment if the concrete is exposed to freeze-thaw conditions during or after construction. c) Plan ahead. Have insulation and heaters ready and inform your ready-mix producer of what concrete temperature you’ll need for your project. d) Do not place concrete on a frozen subgrade; thaw the subgrade with steam or protect it with insulation.
Ground thaw units have become the norm for subgrade thawing and are amazingly efficient and productive at completing this task. e) Provide triple insulation thickness at the corners and edges of walls and slabs. f) Protect fresh concrete against the disruptive effects of freezing until the concrete attains a compressive strength of about 3.5 MPa. Concrete gains very little strength at low temperatures. g) Do not expose concrete surfaces to a sudden temperature drop; gradually reduce the insulation or enclosure temperature to control concrete cooling (no more than a 10°C drop in 24 hours). h) Avoid using unvented heaters. i) Keep heaters attended at all times; they are a fire hazard when burning and are of no value when out of fuel. j) It is good practice in cold weather to leave forms in place as long as possible. Even within heated enclosures, forms serve to distribute heat more evenly and help prevent drying and local overheating.
ABOUT THE AUTHOR:
Patrick Cantin, PQS, is the Plant and Property Manager for Le Conseil scolaire public du Nord-Est de l’Ontario as well as the sole proprietor of Cantin Construction Cost Consulting located in North Bay, Ontario. In addition, Patrick is the current CIQS-Ontario National Board representative and the CIQS-Ontario Northern Chapter representative.
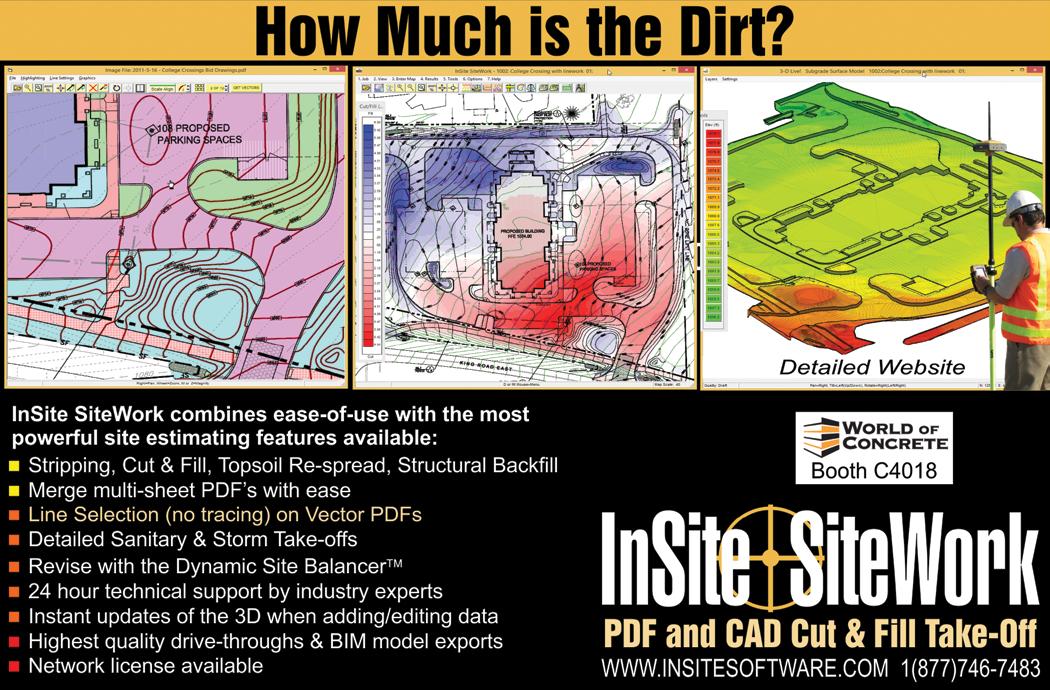
We are seeking a PROJECT MONITOR
Candidates should have a minimum of three (3) years related experience in the Project Monitoring field and possess (or be working towards) an appropriate professional accreditation. The successful candidate will be offered a full-time position with a competitive salary that recognizes your professional experience and unique skill sets. To pursue this opportunity, please forward your resume in confidence to: Mary Fujs PELICAN WOODCLIFF INC. 100 York Blvd., Suite 608 Richmond Hill, Ontario L4B 1J8 Tel: (905) 889-9996 Fax: (905) 889-9950 Email: mary@pelicanwoodcliff.com
www.pelicanwoodcliff.com
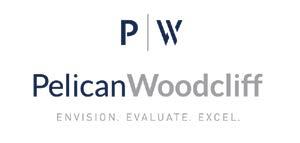

with preferred insurance rates and personalized service.
Home insurance program recommended by
Take full advantage of your benefi ts.
We have worked with your organization to make it possible for you to save on both your home and auto insurance. That’s why, as a Canadian Institute of Quantity Surveyors member, you have privileged access to the TD Insurance Meloche Monnex program, which offers you preferred insurance rates and various additional discounts. Make the most of your benefi ts — get a quote today and fi nd out how much you could save!
On average, members who have home and auto insurance with us save $400. *
HOME | AUTO
Ask for your quote today at 1-866-296-0888 or visit ciqs.tdinsurance.com
The TD Insurance Meloche Monnex program is underwritten by PRIMMUM INSURANCE COMPANY. It is distributed by Meloche Monnex Insurance and Financial Services Inc. in Quebec and by TD Insurance
Direct Agency Inc. in the rest of Canada. Our address: 50 Place Crémazie, Montreal (Quebec) H2P 1B6.
Due to provincial legislation, our auto and recreational vehicle insurance program is not offered in British Columbia, Manitoba or Saskatchewan. *Average based on the home and auto premiums for active policies on July 31, 2014 of all of our clients who belong to an employer group that has an agreement with us when compared to the premiums they would have paid with the same insurer without the preferred insurance rate for groups and the multi-product discount. Savings are not guaranteed and may vary based on the client’s profi le. ® The TD logo and other TD trade-marks are the property of The Toronto-Dominion Bank.
Projet : Annonce TDI 2015
Client : TD Assurance
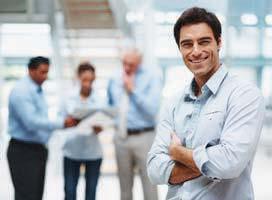
CB Ross Partners is a consulting firm located in Toronto, Ontario providing Dossier # : 09-MM9486-14_TDI.EM1.EN•ciqs(7x4.625) a full range of services to the development/real estate industry including: Project Monitoring Project Management Cost Planning Development Management We have job opportunities in our Project Monitoring and Cost Planning/Estimating departments. Candidates must have: Relevant Experience in the construction industry Strong communications skills Time management skills Be working towards (or have interest in) RICS and CIQS memberships In return, we offer an extensive employee package commensurate with expertise, qualifications and skills. If you are interested, please submit your resume: By email: mail@cbross.ca By fax: 416-487-3017
Province : Ontario Publication : Construction Economist Format : 7x4.625 Couleur : Quad
Épreuve # : 1 Date de tombée : 12/08/2014 Graphiste : Marie-Josée Proulx
Hamelin-Martineau Inc. • 505, boul. de Maisonneuve O, Bureau 300 • Montréal (Québec) H3A 3C2 • T : 514 842-4416 C : mariejosee.proulx@hamelin-martineau.ca ATTENTION : MERCI DE VÉRIFIER ATTENTIVEMENT CETTE ÉPREUVE AFIN D’ÉVITER TOUTE ERREUR/PLEASE CHECK THIS PROOF FOR ERRORS
Only select candidates whose resumes best match our requirements will be contacted.
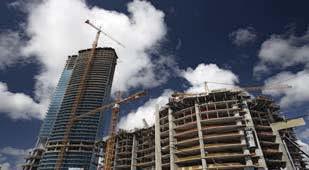