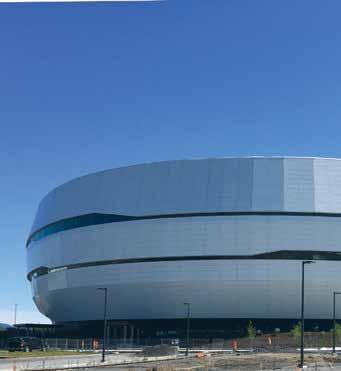
35 minute read
Subsurface conditions and risk allocation
Introduction
The scope of this paper is to review and compare domestic and international standard form construction contracts (SFCC) with respect to subsurface conditions, to understand how risk is usually allocated, if the allocation is fair, and how risk should be allocated. Subsurface conditions are often thought of as, or associated with, the geological state of the ground below the earth’s surface. In the context of SFCCs, as is further evidenced by the interrelated structuring and classification of same, subsurface conditions are not necessarily limited to the preceding definition, and may include other subsurface conditions located below (or behind) the surface of existing structures, and are included as a subsection of concealed, unknown, or otherwise unforeseeable conditions. Notwithstanding that the latter definition is ostensibly broader than that related to geology, subsurface conditions within the framework of this paper will include other matters which are otherwise located below (or behind) the surface of existing structures; collectively referred to as the ‘Subsurface Conditions.’ A central theme amongst Subsurface Conditions is the general uncertainty with respect to the state of the Subsurface Conditions prior to the commencement of the work on a construction project, and the general propensity of the primary parties of a construction contract (the Owner, the Architect, and the Contractor) to attempt to allocate the associated risks to the other parties.
“[W]e know, there are known knowns; there are things we know we know. We also know there are known unknowns; that is to say we know there are some things we do not know. But there are also unknown unknowns – the ones we don’t know we don’t know. And if one looks throughout the history of our country and other free countries, it is the latter category that tend to be the difficult ones.” - Donald Rumsfeld, February 12, 2002
Standard form construction contracts, domestic and international
The Canadian Construction Document Committee (CCDC)1 , and the International Federation of Consulting Engineers (FIDIC)2, are the most widely recognized industry Organizations with respect to the production and use of SFCCs in Canada, and Internationally (located in 34 countries). The two SFCCs produced by the foregoing organizations referenced in this paper are as follows; 1. CCDC 2 – 2008 Stipulated Price Contract (CCDC 2); and 2. FIDIC Conditions of Contract for Construction for Building and Engineering Works Designed by the Employer (FIDIC Contract).
Standard Form Construction Contracts in Canada
The CCDC 2 is an SFCC between the Owner, and the Contractor that establishes a fixed price for the work associated with a construction project (pre-determined scope of work and construction schedule), irrespective of the Contractor’s actual cost of construction.
The CCDC 2 is organized into an Agreement between Owner and Contractor, Definitions, and General Conditions of the Stipulated Price Contract (12 Parts). Part 6 Changes in the Work, GC 6.4 Concealed or Unknown Conditions, 6.4.1 states;
“If the Owner or the Contractor discover conditions at the
Place of the Work which are: 1] subsurface or otherwise concealed physical conditions which existed before the commencement of the Work which differ materially from those indicated in the Contract Documents; or 2] physical conditions, other than conditions due to weather, that are of a nature which differ materially from those ordinarily found to exist” CCDC 2 allocates the risk of Subsurface Conditions to the Owner (subject to the Subsurface Conditions not having been identified in the Contract Documents, therefore forming part of the Work). Part 6 Changes in the Work, GC 6.4 Concealed or Unknown Conditions, 6.4.2 states;
“The Consultant will promptly investigate such conditions and make a finding. If the finding is that the conditions differ materially and this would cause an increase or decrease in the Contractor’s cost or time to perform the Work...will issue appropriate instructions for a change in the Work...” The Ontario Superior Court of Justice dealt with the issue of Subsurface Conditions in Inscan Contractors (Ontario) Inc. v. the Halton District School Board and Decommissioning Consulting Services Ltd. (Inscan v. Halton).4 Ultimately, the Court held that Concealed Conditions were the responsibility of the Halton District School Board (the Owner); however, the court applied an inherent onus on Inscan Contractors (Ontario) Inc. (the Contractor) to have been proactive in its discovery of Subsurface Conditions, as indicated below;
Chart No. 1 provides an overview of some of the types of standard form construction contracts which are utilized throughout the world, including the two listed above. Chart No. 1: International Standard Forms of Construction and Engineering Contracts3
Country Common forms of contract for large projects Common forms for international projects Common forms for engineering contracts
Brazil Bespoke contracts common, especially for large projects. Standard form contracts, especially FIDIC contracts more popular in recent years due to the influence of international players, multilateral investment agencies and promotion by FIDIC. The Red Book and Silver Book contracts are particularly common. Canada Local standard forms published by the Canadian Construction Documents Committee (CCDC), Canadian Construction Association (CCA), Royal Architectural Institute of Canada (RAIC), and both local and national governments and authorities. Germany Bespoke contracts. Local contracts containing standard terms and conditions (STC), whose content is governed by the Civil Code (BGB). Parts of the General Contract Provisions for the Performance of Construction Works (VOB) are usually included.
Russian Federation
FIDIC contracts common, with significant modifications for mandatory local law. FIDIC contracts common. Other various international standard form contracts sometimes used. Same contracts apply as for construction projects.
United States
Local standard forms used, published by the American Institute of Architects (AIA), Engineers Joint Contract Documents Committee (EJCDC) and Associated General Contractors (AGC). Bespoke contracts commonly used for large projects. FIDIC contracts common. Local engineering, procurement and construction (EPC) form of contract used for a design and build (D&B) projects. EJCDC contracts used for non-D&B projects.
FIDIC contracts common.
Bespoke and FIDIC contracts common. Local Canadian forms available but rarely used.
FIDIC contracts common. Same contracts apply as for construction projects.
Local standard forms developed by the RAIC, Association of Consulting Engineers of Canada and other provincial and architectural associations.
FIDIC contracts common. Engineering contracts have more content than traditional construction contracts so the VOB are generally not agreed on, and build, operate, transfer (BOT) models are becoming more popular.
[93] [I] am satisfied that the provisions of section 6.4.1 apply to the present matter. In order to be triggered, section 6.4.1 requires satisfaction of the following: 1. the condition must be substantially different from that detailed in the Contract; 2. the condition must be substantially different from that described or observed during the pre-tender site investigation; 3. the condition must differ significantly from those conditions ordinarily found to exist on asbestos abatement projects; 4. the condition must differ substantially from that which could have reasonably been determined to exist or inferred from available information; and 5. the plaintiff shall have notified the Board or DCS prior to disturbing the condition and in no event later than five working days after the first observance of the condition. [94] The plaintiff has demonstrated satisfaction of these conditions on a balance of probabilities. I will address each in turn. [95] Before doing so, I should address the defendants’ argument that the plaintiff had a duty to investigate the site by virtue of the provisions of section 5 of the instructions to tenderers included in the Contract Documentation, that it failed to do so and that, therefore, the risk of the concealed condition falls upon the plaintiff rather than the defendant. I agree with the defendant to the extent that the plaintiff cannot assert a claim if it could reasonably have undertaken an investigation which would have revealed the condition and failed to do so (underscored for emphasis)5 or was presented with information from which it ought reasonably to have understood that an unusual condition existed at Lord Elgin. However, the defendant has failed to demonstrate either of these circumstances.
[96] [T]he defendant was unable to identify an investigation that the plaintiff could reasonably have undertaken that would have revealed the condition...Had he observed the residue, the only reasonable investigation he could have undertaken would have been to ask DCS about the residue. The only answer DCS could have given, based on its understanding from the results of the McGowan test removal, was that it was easily removable... [97] Similarly, it is unreasonable to suggest, as defendants’ counsel urged on the Court, that the plaintiff should have investigated by asking the other prospective bidders at the pre-tender meeting, who were its competitors in the market generally as well as for the Project, whether they had any experience with this residue. [98] It is also unreasonable to expect that each bidder would have conducted its own test removal at one or more other areas during or after the meeting prior to submitting a tender rather than rely on a competent environmental consultant, who had supervised a test removal for this very purpose, to advise it of any unusual conditions. [99] The evidence of the other contractors was that they had never seen an enclosure at a pre-tender site meeting relocated at the request of a prospective bidder...It is also of some significance that none of the other prospective bidders felt the need to conduct their own test removal, although this should be given less weight, because most of the bidders may have been satisfied that they knew the site conditions from previous experience. [100][T]here was no information available to the plaintiff from which it might reasonably have concluded there was a problem condition...The only possible information was the package of photographs handed out at the pre-tender meeting...These photographs convey no information with respect to the degree of difficulty of removal of the residue. In any event, as mentioned above, while the fact of the test removal might well prompt questions of prospective bidders, in the circumstances of the present action, the answers to those questions would not have alerted the plaintiff to any unusual difficulty associated with the residue. [101] Turning to the five provisions of section 6.4.1, the plaintiff has demonstrated that the underlying conditions for asbestos removal were substantially different from those detailed in the Contract. The presence of the residue was not set out in the Contract Documentation and, accordingly, the difficulty of removal was also not addressed...The evidence of the other contractors satisfies me that the contractual documentation customarily used in the industry does not address this rare possibility. [102][A]s set out above, the defendants have not satisfied the Court that the enclosure at the pre-tender meeting was set up under the McGowan test removal site... It was therefore unreasonable to conclude that if Kelly had seen it the plaintiff would have understood that the residue presented a difficulty in removal. DCS also made no mention of the difficulty of removal at the meeting. On this basis, the condition was substantially different from those described and observed at the pre-tender site meeting. [103][A]s mentioned, the evidence demonstrates that the problem residue was rarely found outside Lord Elgin, and at that location it was found only in the original section of the school... [104][A]s set out above, there was also no other information available to the plaintiff from which the presence of this residue could reasonably have been determined to exist or inferred. It did not have access to any reports or previous environmental consultants to the Board or to the exposure sheet or any report relating to the test removal site... In a strictly literal interpretation of CCDC 2, coupled with the Court’s decision in Inscan v. Halton, the risk of Subsurface Conditions is allocated to the Owner, not the Contractor; however, if a claim for Subsurface Conditions should be asserted by the Contractor, it should be in a position to justify, and substantiate how the Subsurface Conditions differ materially from those indicated in the Contract Documents, or physical conditions differ materially from those ordinarily found to exist and generally recognized as inherent in construction activities of the character provided for in the Contract Documents (CCDC 2). In addition, the condition must be substantially different from that observed during the pre-tender site investigation, and the condition must differ substantially from that which could have reasonably been determined to exist or be inferred from available information (Inscan v. Halton), failing which, a court may determine that the Contractor is responsible for Subsurface Conditions, with all that that entails.
Standard Form Construction Contracts in international countries
The FIDIC Contract is an SFCC (General Conditions only; the Agreement Between the Owner and the Contractor is a separate document, which forms part of the Contract Agreement) between the Owner, and the Contractor that establishes a Bill of Quantities (unit price) for the work associated with a construction project (having a pre-determined scope of work, not quantities, and predetermined construction schedule). The FIDIC is organized into 20 Clauses. Clause 4, 4.12 Unforeseeable Physical Conditions, states;
“In this Sub-Clause, “physical conditions” means natural physical conditions and manmade and other physical obstructions and pollutants, which the Contractor encounters at the Site when executing the Works, including sub-surface and hydrological conditions but excluding climatic conditions.
If the Contractor encounters adverse physical conditions which he considers to have been Unforeseeable, the Contractor shall give notice to the Engineer...This notice shall describe the physical conditions... and shall set out the reasons why the Contractor considers them to be Unforeseeable.
The Contractor shall continue executing the Works...shall comply with any instructions which the Engineer may give. If an instruction constitutes a Variation, Clause 13 [Variations and
Adjustments] shall apply.” The FIDIC Contract allocates the risk of Subsurface Conditions to the Owner (subject to the Subsurface Conditions being “unforeseeable”, therefore, forming part of the Work). Clause 4, 4.12 Unforeseeable Physical Conditions, further states;
“If and to the extent that the Contractor encounters physical conditions which are Unforeseeable, gives such a notice, and suffers delay and/or incurs Cost due to these conditions, the Contractor shall be entitled subject to notice under
Sub-Clause 20.1[Contractor’s Claims] to: (a) an extension of time for any such delay, if completion is or will be delayed, under Sub-Clause 8.4 [Extension of Time for Completion], and (b) payment of any such Cost, which shall be included in the Contract Price. Upon receiving such notice and inspecting and/or investigating these physical conditions, the Engineer shall proceed in accordance with Sub-Clause 3.5 [Determinations] to agree or determine (i) whether and (if so) to what extent these physical conditions were Unforeseeable, and (ii) the matters described in subparagraphs (a) and (b) above related to this extent. Unlike CCDC 2, the FIDIC Contract places a stringent burden of proof on the Contractor as to why the Subsurface Conditions were unforeseeable, as opposed to unknown, or concealed. In addition, the FIDIC Contract contains a mechanism which would permit the re-evaluation of other parts of the work to determine if they were conceivably “more favourable” than what could have been reasonably foreseen. This would be required prior to any final valuation of costs, and could be used as a means of offsetting the unforeseeable costs (but not resulting in a net credit) with those which were determined to be more favourable. Clause 4, 4.12 Unforeseeable Physical Conditions, further states;
“However, before additional Cost is finally agreed or determined under sub-paragraph (ii), the Engineer may also review whether other physical conditions in similar parts of the Works (if any) were more favourable than could reasonably have been foreseen when the Contractor submitted the Tender. If and to the extent that these more favourable conditions were encountered, the
Engineer may proceed in accordance with Sub-Clause 3.5 [Determinations ] to agree or determine the reductions in
Cost which were due to these conditions, which may be included (as deductions) in the Contract Price and Payment
Certificates. However, the net effect of all adjustments under sub-paragraph (b) and all these reductions, for all the physical conditions encountered in similar parts of the
Works, shall not result in a net reduction in the Contract
Price. The Engineer shall take account of any evidence of the physical conditions foreseen by the Contractor when submitting the Tender, which shall be made available by the Contractor, but shall not be bound by the Contractor’s interpretation of any such evidence.” Unlike CCDC 2, in the FIDIC Contract, the risk of Subsurface Conditions is not inherently allocated to the Owner; there is a test which the Contractor must satisfy with respect to transferring the risk to the Owner, part of which is to prove that the Subsurface Conditions were not foreseeable. This remains with the Contractor in advancing its claim, and is subject to further review by the Engineer.
Allocation of risk, for better, or worse
In the Canadian model (CCDC 2) the allocation of risk related to Subsurface Conditions is borne by the Owners; however, in the International model (as highlighted in-part in Chart No.1), the Contractor bears the initial risks, with an opportunity (and the onus) of transferring it to the Owner. The FIDIC Contract creates a notion that should one part of the Work become more difficult (costly) as a result of Subsurface Conditions, than other parts of the Work related to Subsurface Conditions which may have been easier (less costly), could become subject to a cost adjustment (credit). In theory, this approach seems reasonable enough; however, in practice, this approach has the potential to upset one of the fundamental characteristics of competitive bidding: calculated risk (one that the Contractor bears). Contractors may take certain calculated risks in responding to tenders based on their previous experiences, regional knowledge, and other environmental (built and nonbuilt) conditions. If Contractors should become concerned that “easier” parts of Subsurface Conditions may result in credits, how will this affect the initial bid amount? It is fair to assume that this practice may result in an increase to the cost of the bid for the Contractor (as risk is increased, i.e. potential credits), and a decrease in value to the Owner. As a result, the risk/reward ratio may determine that fewer construction projects are viable, leading to fewer bids to any particular tender, leading to an overall increase in construction costs.
Conclusion
It is frequently said that the allocation of risk should be to the party which is best equipped to manage it. This may be true in a number of circumstances; however, the allocation of risks associated with Subsurface Conditions should not apply so freely to this general rule, as there is often an opportunity to eliminate the risk, prior to a requirement to manage it. Construction projects are often developed over several years, and in-turn, are frequently tendered over a period of several weeks. It would be unreasonable to suggest that a Contractor would be able to familiarize itself with a construction project to the same extent that an Owner may, given the significantly reduced timelines, and often restricted or limited access to potential Subsurface Conditions,6 as the Owner would have been afforded. For this reason, the onus should remain with the Owner to ensure that all material information is made available to Contractors so as to allow them to provide complete, competitive and transparent bids. Should the Owner elect not to address potential Subsurface Conditions proactively, in an up-front and transparent manner,
SFCCs should provide for equitable adjustments in the value and time of the construction contract, as required. It would be remiss not to draw attention to the fact that SFCCs are more often than not significantly altered through supplementary conditions; therefore, the allocation of risk associated with Subsurface Conditions will be borne by the party willing to accept it, for better, or for worse.
End notes:
1 The Canadian Construction Documents Committee (CCDC) develops, produces, and reviews standard construction contracts, forms and guides. It is a national joint committee, formed in 1974, and includes representation from across the
Canadian construction industry. The committee includes two construction owner representatives from each of the public and private sectors, as well as representatives from four national organizations. All CCDC Documents are endorsed by these national organizations: Association of Consulting
Engineering Companies – Canada (ACEC); Canadian
Construction Association (CCA); Construction Specifications
Canada (CSC); and Royal Architectural Institute of Canada (Architecture Canada). CCDC representation also includes a lawyer from the Canadian Bar Association (Construction Law
Section), who sits as an ex-officio member. 2 FIDIC is the International Federation of Consulting
Engineers. Its members are national associations of consulting engineers. Founded in 1913, FIDIC is charged with promoting and implementing the consulting engineering industry’s strategic goals on behalf of its Member
Associations and to disseminate information and resources of interest to its members. Today, FIDIC membership
covers 97 countries of the world. FIDIC, in the furtherance of its goals, publishes international standard forms of contracts for works and for clients, consultants, sub-consultants, joint ventures and representatives, together with related materials such as standard pre-qualification forms. 3 PLC Cross-Border Construction and Projects Handbook 2010/11 (Update) 4 Inscan Contractors (Ontario) Inc. v. Halton District School
Board, 2005 CanLII 8728 (ON SC) 5 “cannot assert a claim if it could reasonably have undertaken an investigation which would have revealed the condition and failed to do so”
This is interesting and important, as the Court suggests that if a reasonable investigation could have been undertaken, perhaps the risk of the Subsurface Conditions would have been that of the
Contractor, not the Owner. This obviously begs the question as to what constitutes a reasonable investigation, and could it have been undertaken at the time of tender. 6 This is particularly true with respect to Design-Bid-Build construction projects, whereas, a Contractor would not be permitted to perform bore tests, or remove portions of existing building components during the tender period to satisfy themselves with the Subsurface Conditions.
About the author
Arran Brannigan, LL.M., MBA, PQS, is a senior construction executive whose principal focus has been on General Contracting in the Industrial, Commercial and Institutional sectors of the Canadian Construction Industry.
GSNH Construction Law Group
Stanley Naftolin, Q.C., C.S. naftolin@gsnh.com Maurizio Artale artale@gsnh.com
Brian Campbell campbell@gsnh.com
Colin Campbell ccampbell@gsnh.com Leonard Finegold finegold@gsnh.com
Lori Goldberg goldberg@gsnh.com
Paul Hancock hancock@gsnh.com
Irwin Ozier ozier@gsnh.com Catherine Willson willson@gsnh.com
480 University Ave., Suite 1600 Toronto, ON M5G 1V2
www.gsnh.com
GSNH
We’re social. Follow Us.
ASPIRING PROFESSIONAL QUANTITY SURVEYOR MOHAMMED FARES, BEPD, MEPD, CEC
Chief Quantity Surveyor, Mechanics/Electricity, Macogep Inc.
As far as I can recall, I always wanted to work in the construction world. I began my studies at the Claude Bernard Lyon I University in France, where I graduated with a Licence, a Master Degree and a post-master in Mechanics, to finally obtain an Advanced Studies Diploma in Thermal and Energy. I started my professional career in design and construction of ventilation and air conditioning systems in Morocco, my birth country.
While studying in Lyon, I became interested in moving to Québec, Canada, an opportunity that many students in France were offered. I took the opportunity in 1999 without hesitation. Upon my arrival in Montréal, I applied for an internship as cost estimator with an HVAC contractor. Unfortunately, when the internship was completed, the province’s economic situation was not conducive to finding a permanent position in construction, so I decided to go back to school and acquire further qualifications – I was told this was the best way to penetrate Québec’s job market. I completed a degree in Building Estimating Technology at the Grasset Institute in 2006.
I had my first real Canadian experiences working for companies which specialized in post-disaster renovation and related markets automated regulation. There I discovered my passion for worksites and management. Although the nature of the work was highly interesting, I soon realized that the routine was far from my liking. I decided to go to work for a general contractor in the institutional sector where I was hired as Estimator and Project Manager. It was at that moment that my Program Manager from my days at the Grasset Institute contacted me to refer me for a position at Macogep.
Coincidentally, a major crisis exploded in Quebec’s construction industry leading to the creation of a Public Hearing Commission to look into the many allegations of corruption. This compelled me to accept the challenge and apply for the position at Macogep, a project management firm, especially as I knew that it had always positioned itself as completely independent from architects, engineering and construction companies. Two years later, I was promoted to Chief Estimator, Mechanics/Electricity. Today, I supervise the personnel in charge of preparing cost estimates in heating, ventilation, air conditioning, process mechanics and electricity.
My passion is to use my knowledge and skills to improve innovative projects which I can follow at each and every step, from planning to commissioning. Amongst those many challenges, I can mention: implementation of a biomethanization system at a wastewater treatment plant; redevelopment of life units at a residential and long-term care centre; and construction of a sports complex aiming for LEED Gold certification. My experience with Macogep and its multidisciplinary team led me to discover a profound interest in construction management and I recently had the privilege to actively participate in the construction of a brand new plant in Quebec City for Olympus NDT Canada (a manufacturer of test, measurement and imaging instruments).
Whether in project management or construction management, I firmly believe that cost control is mandatory – and so does Macogep, as the firm highly values the PQS certification – its team counts four PQS and five CEC professionals. I am thrilled to think that once I get my certification, I will be able to use my skills in the cost estimating field all over Canada, while at the same time helping Macogep to win challenging new projects. My new PQS title will not only be a personal achievement, but will be shared with the team.
I wish to thank the Construction Economist, for giving me the opportunity to write this article. It was a real pleasure sharing with you all the paths that are currently leading me to the PQS certification.
The dangers of misinterpreting contractual claim submission requirements
Richard Wong
(especially in standard form contracts)
Ethan McCarthy
Anyone who has been involved in advancing, administering or responding to a claim for a contract change should be aware of the recent decision of the Ontario Court of Appeal in Ross-Clair v. Canada (Attorney General), which upheld a determination of the owner denying the contractor’s claim for compensation. This decision provides important guidance from the courts on the proper interpretation of claims provisions within a contract, as well as useful commentary on the amount of deference that courts will give on appeal of a decision interpreting a standard form contract.
Background
Ross-Clair entered into a contract with Public Works and Government Services Canada (PWGSC) to construct office facilities for the Millhaven Institution in Bath, Ontario on a fixed-price basis with an original completion date of January 24, 2009. NORR Limited, as the Engineer, was the decider in first instance of any disagreements under the contract, and the Engineer’s decisions were final and a precondition to entry into the formal dispute resolution mechanisms under the contract.
The contract contained several interrelated provisions governing Ross-Clair’s entitlement to a change due to soil conditions or delays to the project. First, Ross-Clair was required to give the Engineer written notice of any intention to claim within 10 days of the occurrence of the originating event. Once such notice was given, GC 35.3 and 35.4 required Ross-Clair to give the Engineer a written claim within 30 days of the date that a Final Certificate of Completion was issued, noting that: A written claim referred to in GC 35.3 shall contain a sufficient description of the facts and circumstances of the occurrence that is the subject of the claim to enable the Engineer to determine whether or not the claim is justified and the contractor shall supply such further and other information for that purpose as the Engineer requires from time to time. If the Engineer determined that a claim was justified, then GC 35.5 required PWGSC to make an additional payment in an amount that is calculated “in accordance with GC 47 to GC 50” which addressed how costs for changes were to be determined. If Ross-Clair failed to give a notice referred to in GC 35.2 or a claim referred to in GC 35.3 within the times stipulated, then it lost its entitlement to compensation for such claim.
During the course of the project, Ross-Clair advanced two claims under GC 35.3 totalling $2,204,676. The correspondence is described in greater detail to better illustrate the sequence of communication as it unfolded:
First Claim
• December 5, 2008. Ross-Clair sent a letter to Engineer providing notice of claim in the amount of $1,437,976 due to delays in the start of construction caused by PWGSC. • December 16, 2008. Engineer stated in response that there was insufficient evidence to support the claim that the delay was caused by PWGSC and requested additional detail of projected costs and the impact on the project to support
Ross-Clair’s claim. • March 2, 2009. Ross-Clair replied to PWGSC explaining that the additional costs were as a result of delays due to, among other things, weather conditions, site conditions contract alterations, and disruptions to construction sequencing. Included in the letter was a document titled
Additional Costs Summary listing various costs attributed to the work of subcontractors. • April 2009 - October 2009. PWGSC wrote to
Ross-Clair on 3 occasions requesting additional documentation to support Ross-Clair’s request for an extension of time and associated compensation including specifically referencing provisions of the contract and requiring a more in-depth analysis of the delays in order to properly allocate responsibility.
Second Claim
• March 31, 2011. Ross-Clair submitted a second claim for compensation as a result of further delays to the project and change order work performed from September 13, 2009 to April 20, 2010 in the amount of $766,700. This letter provided no additional information in support of that claim. • April 20, 2011. PWGSC wrote to Ross-Clair advising that its second claim did not contain a sufficient level of detail to determine if the claim was justifiable and
requested supporting information to substantiate the costs on the two outstanding claims. • February 10, 2012. The Engineer certified Ross-Clair’s work as complete and a Final Certificate of Completion under GC 35.3 was issued. Finally, on May 28, 2013, Ross-Clair provided PWGSC with a report prepared by Knowles in support of both claims entitled Analysis of Delays and Additional Costs.
Initial decision
While PWGSC acknowledged that Ross-Clair properly submitted the required notices of intent to claim, it disputed that Ross-Clair provided sufficient information for the Engineer to make a determination on either claim under GC 35.4. Without a decision, Ross-Clair could not proceed through the dispute resolution process under the contract, so Ross-Clair brought an application for a court order compelling the Engineer to make a determination on both claims. The application judge identified the core issue of the dispute as the level of documentation required under GC 35.4 for the Engineer to consider a claim, deciding that the clause required more than mere notice of the claim but less than the proof of the claim an arbitrator would require.
Using that test, the application judge concluded that the first claim met the documentation requirements contained in GC 35.4 particularly given that the Engineer should have been an active participant in reviewing the progress of the project, but the second claim did not. Importantly, the provision of the Knowles report could not remedy the non-compliance of the second claim given that it was delivered outside of the timeline set forth in GC 35.3, a principle that the Ontario Court of Appeal had confirmed in an earlier decision in Technicore Underground Inc. v. Toronto (City). Therefore, the application judge ordered the Engineer to make a determination with respect to the first claim, which order PWGSC then appealed.
Standard of appeal
The Court of Appeal first considered which standard it would apply in reviewing the application judge’s order: a standard of deference unless there was a ‘palpable and overriding error’ or a less deferential standard to re-review the order under a strict standard of ‘correctness.’ The court, acting unanimously, held that the standard of correctness applied and ruled that the application judge committed an extricable error of law for the reason of having interpreted GC 35.4 in isolation without
Advice you can build on
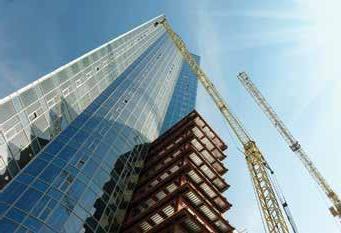
On complex construction and infrastructure projects, you can’t afford issues with the schedule, quality or cost. Osler’s specialized team of lawyers has the deep industry experience to help you anticipate problems, mitigate risks and stay on track to ensure your project success.
Osler, Hoskin & Harcourt llp osler.com
With more than 200 mandates completed in just one year, We’re at the top of our field. trust us for your governance and project management needs.
macogep.com
Tenant Representative & Project Manager - Videotron Centre.
construing the contract as a whole, violating one of the fundamental principles of contractual interpretation.
Note in passing that PWGSC had advanced an alternative argument that the court should review the order based on a standard of correctness for the reason that the underlying contract was in fact a standard form agreement, consistent with other legal precedent. However, the court declined to do so, in this particular case, on the basis that it had insufficient evidence before it regarding the formation of the contract and those portions of the contract that were alleged by RossClair to have been negotiated as opposed to being standard. Unfortunately, it is beyond the scope of the present article but there is much to be said on whether a given form of contract and its usage will be considered to be a standard form agreement for purposes of setting the standard of review.
Appeal decision and outcome
In reviewing the contract under a standard of correctness, the court set aside the application judge’s order and declared that both of Ross-Clair’s claims were barred by operation of the contract because the information submitted was not detailed enough, even considering that the Engineer was intimately familiar with the project.
The court specifically found that the application judge failed to consider GC 49 and 50 of the contract, which described how costs for changes were to be determined and specified the type of information that should be submitted by Ross-Clair. Therefore, even though the word “detailed” was not expressly used within GC 35.4, because the Engineer required proof that the claim is justified to make a decision as to the validity of the claim, GC 35.4 should have been interpreted that a claim submitted to the Engineer must have been supported by detailed information as contemplated in the rest of the contract including GC 49 and 50. Under this test, the court reasoned that the December 5, 2008 and March 2, 2009 letters noted above provided little support for the first claim, even considering the application judge’s finding that the Engineer was intimately familiar with the project, and found the letters to be lacking in specificity, confusing in terms of identifying the parts of the project affected by the delay and providing skeletal information of various sub-contractors costs but no breakdown.
However, the court did agree with the application judge’s finding that the Knowles report failed to meet the timeliness requirement of GC 35.3 and so could not be considered.
Lessons learned
The court’s focus on interpreting the contract as a whole in Ross-Clair should serve as an important reminder to contract drafters, contract administrators (both on the owner and contractor side) and independent engineers of the importance of observing the procedural and substantive provisions of a construction contract as they relate to claims as well as changes, wherever they may reside in the contract. Evidentiary requirements should be met, especially in circumstances where the claims procedure sets an express time limit to provide the entire claim rather than just notice of the claim, as failure to do so in the appropriate time limit may result in loss of entitlement to compensation.
Some commentators have criticized the court as overstepping its boundaries to substitute its own judgment for that of the application judge who heard all the facts. This criticism may be unwarranted since the court found that the application judge did not consider GC 49 and 50 when interpreting GC 35.4. GC 49.2 specifically provided a list of information that Ross-Clair was required to submit to facilitate the approval of a change including the costs for each subcontract, a breakdown of labour, plant and material costs, and percentage mark-ups. To not consider whether this list of requirements should inform the interpretation of the evidentiary requirement under GC 35.4, which also dealt
Please support these advertisers who help make Construction Economist possible.
To reach construction and quantity surveying professionals through Construction Economist and its targeted readership, contact Jeff at your earliest convenience to discuss your company’s promotional plans for 2016.
Jeff Kutny, Marketing Manager E-mail: jeff@kelman.ca Phone: 866-985-9789 Fax: 866-985-9799
Published for CIQS by:
with changes to the contract, was a fundamental oversight on the part of the application judge in the eyes of the court. This fundamental error meant that threshold for overturning the application judge’s interpretation of GC 35.4 dropped from palpable and overriding error to correctness. Once the court found that the application judge incorrectly interpreted GC 35.4 in light of the contract as a whole, it necessarily fell to the court to reweigh the facts before it based on the correct interpretation, which although not ideal, is not beyond the role of an appellate court.
Also note that the contractor’s documentation requirements appeared to be materially unaffected by the involvement and knowledge of the Engineer in the day-to-day activities of the project, essentially requiring the contractor to independently submit the relevant claim documentation as opposed to relying on assumed or imputed knowledge of the engineer. While some may criticize this approach as being unduly formalistic, in our view given the size, complexity, and duration of today’s projects with multiple stakeholders including procurement authorities, lenders, counterparties, and other stakeholders, and given the realities of the labour market where key personnel may retire or move on during a project, this approach will lead to the creation of a free-standing record that will provide greater clarity for any relevant party including outside counsel in assisting in the resolution of the dispute with maximum efficiency.
Finally, while not an express factor in the court’s decision, it could not have hurt that PWGSC, in the chain of correspondence above, appeared to reply promptly, repeatedly, and clearly in its requirements to Ross-Clair for further information, which emphasizes the need for effective communication by any party when it comes to addressing claims.
Note: These comments are of a general nature and are not intended to provide legal advice as individual situations will differ and should be discussed with a lawyer.
About the authors:
Richard Wong is a partner and co-chair of Osler’s Construction & Infrastructure Group, advising clients on project development issues from procurement to disputes. Richard has spoken at CIQS/RIQS events in 2015 and 2016 and is also engaged by Professional Engineers Ontario (PEO) to evaluate P.Eng Professional Practice.
Ethan McCarthy is an associate in Osler’s Construction & Infrastructure Group and a P. Eng (Civil). The key focus of his commercial practice is construction, infrastructure and energy, and has advised clients including Bruce Power, Atomic Energy of Canada Limited, and Pattern Energy.
QSM
MECHANICAL AND ELECTRICAL COST CONSULTING
Dennis M. Smith PQS
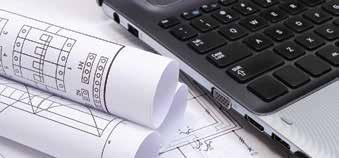
dennis@qsmcon.ca www.qsmcon.ca
CELL 416-949-8540 OFFICE 905-649-8540
Let QSM bring its experience to your next project!
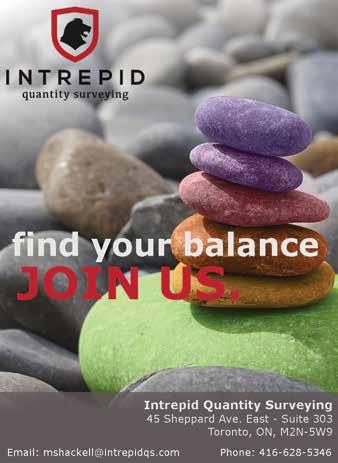
Tips on earning extra CPD points
Wendy Hobbs, PQS
or the most part, technology makes our lives easier. We have all experienced the joys of having a computer automate a task that used to take you hours, in mere seconds. Sadly, there are sometimes bumps in the road with any new technology. In this context, since users experienced some difficulties with our CPD web tracking system, we have decided to take it down from the webpage so that we can build a new and improved version. We hope to have it up and running soon and we look forward to everyone taking it out for a test drive.
With specific reference to CPD points, please remember that attending events is certainly not the only way
Fto attain more points. Serving on your affiliate board or with your local chapter provides a great opportunity to obtain CPD points. This would of course be a win/win by providing some assistance in organizing events. Many hands make light work! You can also contribute to the knowledge base by writing articles for the Construction Economist. Volunteering to speak on a topic is another great way of adding points, and I am sure your local Affiliate would be delighted to organize a location where that could occur and to email the members about the event. Another win/win! Hope everyone has a great Autumn — filled with more treats than tricks! About the author Wendy is a professional quantity surveyor with experience across all sectors of construction in construction loan monitoring, cost consulting, and risk management. During her office duties she was involved in a wide range of complex projects of values exceeding $100 million. Wendy has been a guest lecturer in construction financing and quantity surveying at SAIT Polytechnic and the University of Calgary. This experience reawakened the joy of teaching and led her to join the instructional team at SAIT’s School of Construction. She sits on the Board of Directors for the Canadian Institute of Quantity Surveyors – Prairies and Northwest Territories, as President. She also sits on the national board as the Prairies and Northwest Territories representative, CPD Director and as Registrar.
QS Online Cost Consultants Inc. Halifax, Nova Scotia p. 902 405-1504 halifax@qsonlinecostconsultants.com www.qsonlinecostconsultants.com
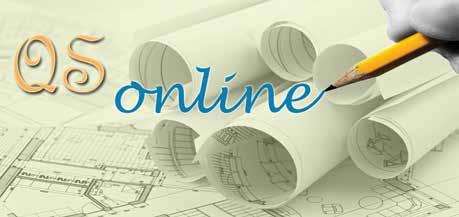
• Feasibility Study • Cost Planning & Control • Project Monitoring • Contract Administration • P3s Monitoring
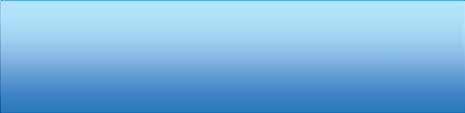

Alpha Cost Consultants Inc.