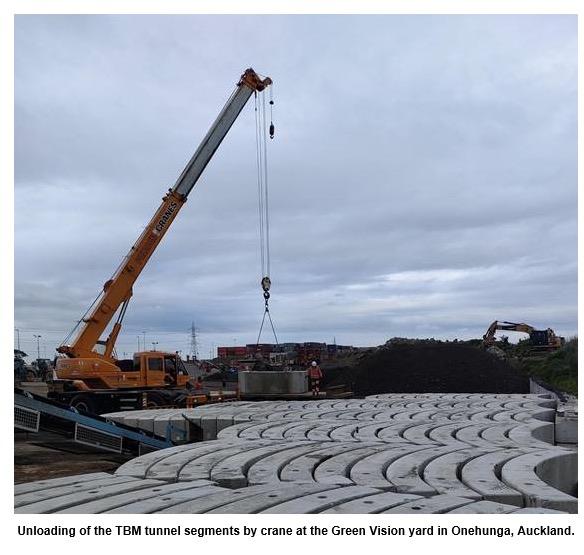
2 minute read
CASE STUDY
Tunnel Boring Machine 'false' segments
The TBM is designed to move forward on the curved tunnel ‘invert’ it has just laid. However, at the start of a tunnel, and when it is passing through previously constructed caverns such as at Karanga-a-Hape Station, temporary or ‘false’ segments need to be installed. The project needed almost 350 false segments, which are 4m wide, 1.1m deep, 5-tonne pieces of concrete reinforced with steel. However, once the tunnel boring was complete these false segments became redundant.
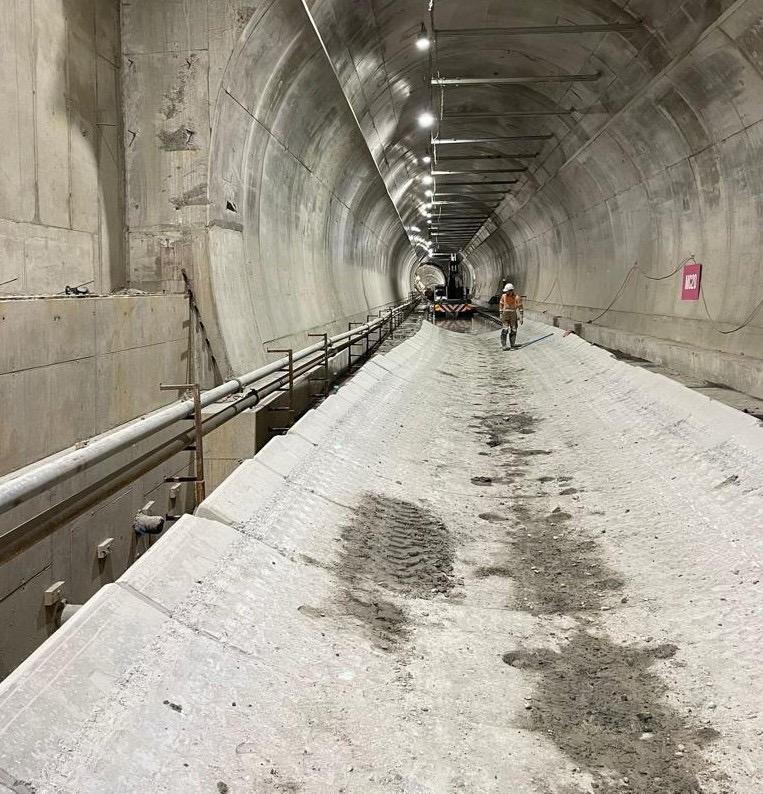
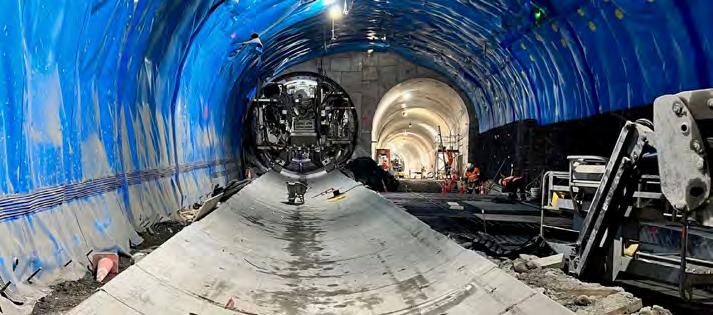
Unable to find a reuse option for them and to prevent them from ending up in landfill, Link Alliance sought a way to recycle these. The solution was found by engaging recycling suppler, Green Vision Recycling, which specialises in recycling and repurposing materials for use in construction and infrastructure projects.
Green Vision crushed the segments, extracted the steel for recycling and graded the crushed concrete to be used as a replacement for virgin aggregate, which may well be supplied back to the CRL as backfill for the tunnels. Green Vision have undertaken an Environmental Product Declaration (EPD), which shows that recycled crushed concrete supplied by them reduces the carbon footprint by around 75% in comparison to using quarried aggregate, with the reduction in trucking distances a particularly important factor.
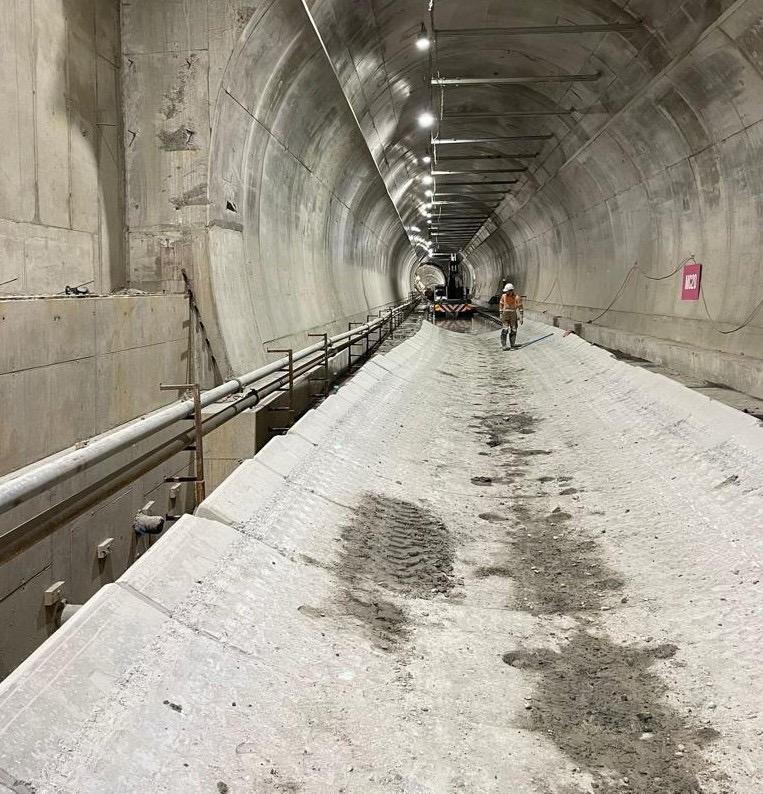
Case Study
Contract 8: Sustainability Case Study
Contract 8 is delivering wider network improvements at The Strand, Ōtāhuhu and Newmarket to support City Rail Link operation. Ōtāhuhu works were completed in 2020, Newmarket works are now 80% completed and The Strand will shortly have upgrades to pedestrian mobility access and walkways in time for December 2023.
The main contractor Libbet has made a commitment to supplier diversity and social outcomes. With a diverse team continuously involved on this project, 25% of their workforce identifies as Māori or Pasifika.
These include Tohiora Te Ahuru who joined the team as a Person In Charge (PIC) for works completed over summer, where he played an integral role delivering a complex scope within tight timeframes; two carpenters working on their apprenticeships and a junior quantity surveyor was also actively involved with this project assisting with progress claims, attending work scope meetings and taking part in the reviews.
Battery powered tools and equipment that do not rely on fossil fuels are also being used on site, with the triple benefit of lower carbon emissions, less noise and no harmful odours normally associated with gas-powered alternatives. Libbet is using an Appenate™ app to monitor fuel use and the Toitū Envirocare Travel Calculator to calculate and track travel and transport emissions (kg CO2e).
Other resource efficiency initiatives include a single more energy efficient generator and re-use of existing subgrade and formation material. Following testing and sign off from site engineers, 60-tonnes of existing subgrade/ formation material were diverted from landfill, eliminating the need for 60-tonnes of imported virgin aggregate materials. Soakage pits have also been used to allow water produced from core drilling to safely and slowly soak into the ground rather than removing water from site.
Libbet has worked to find innovative ways to trim carbon emissions, partnering with their Personal Protective Equipment (PPE) supplier to divert 100% of staff uniforms and most PPE from landfill.
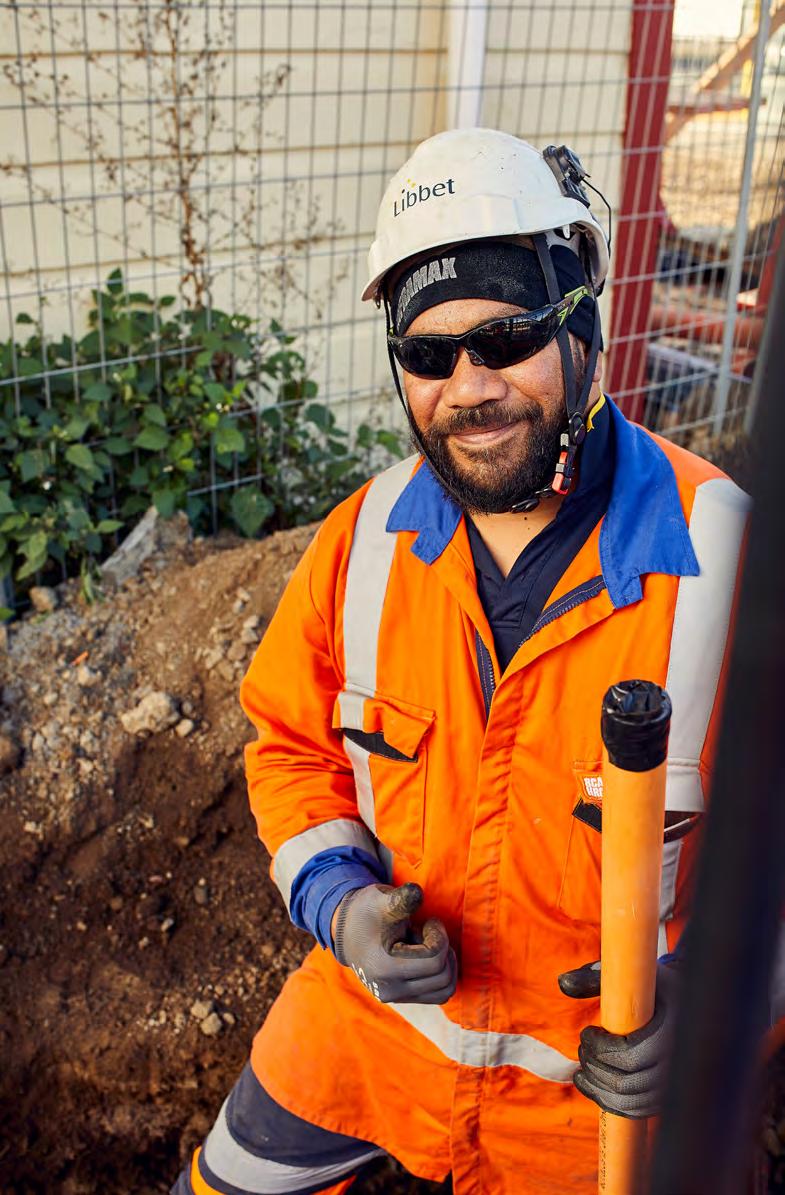
For every kilogramme of used uniform/PPE diverted from landfill, 3–4kg of CO2 emissions are eliminated. In December alone, 17kg of uniform and PPE was diverted from landfill, removing around 68kg of CO2 from the environment.
Most clothing and PPE no longer suitable for use has been shredded and repurposed as fibre that is used for insulation and wadding materials in Auckland, replacing virgin plastic use.
Libbet has been able to divert 0.5 tonnes of mixed recyclables from landfill over the course of the project.
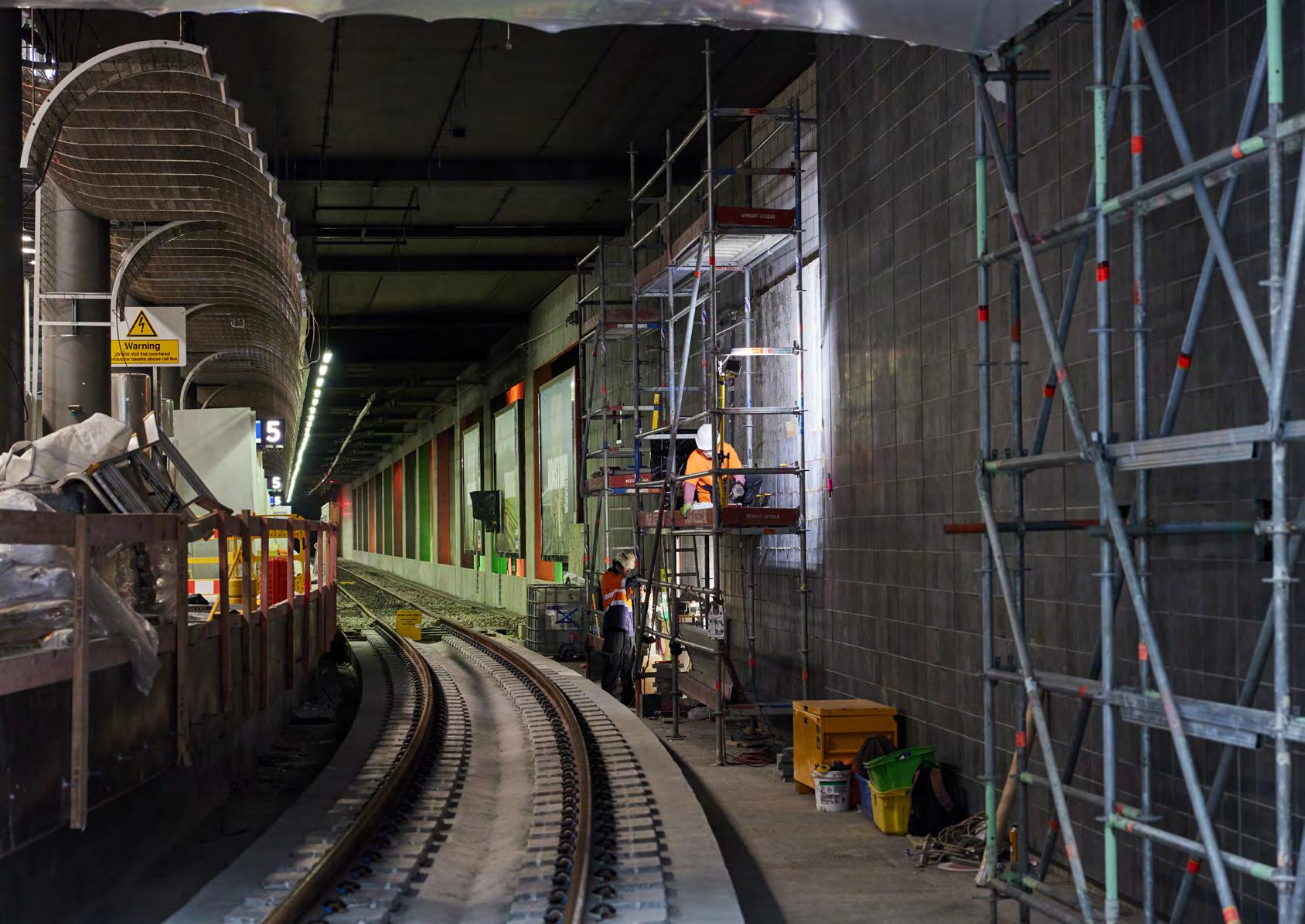