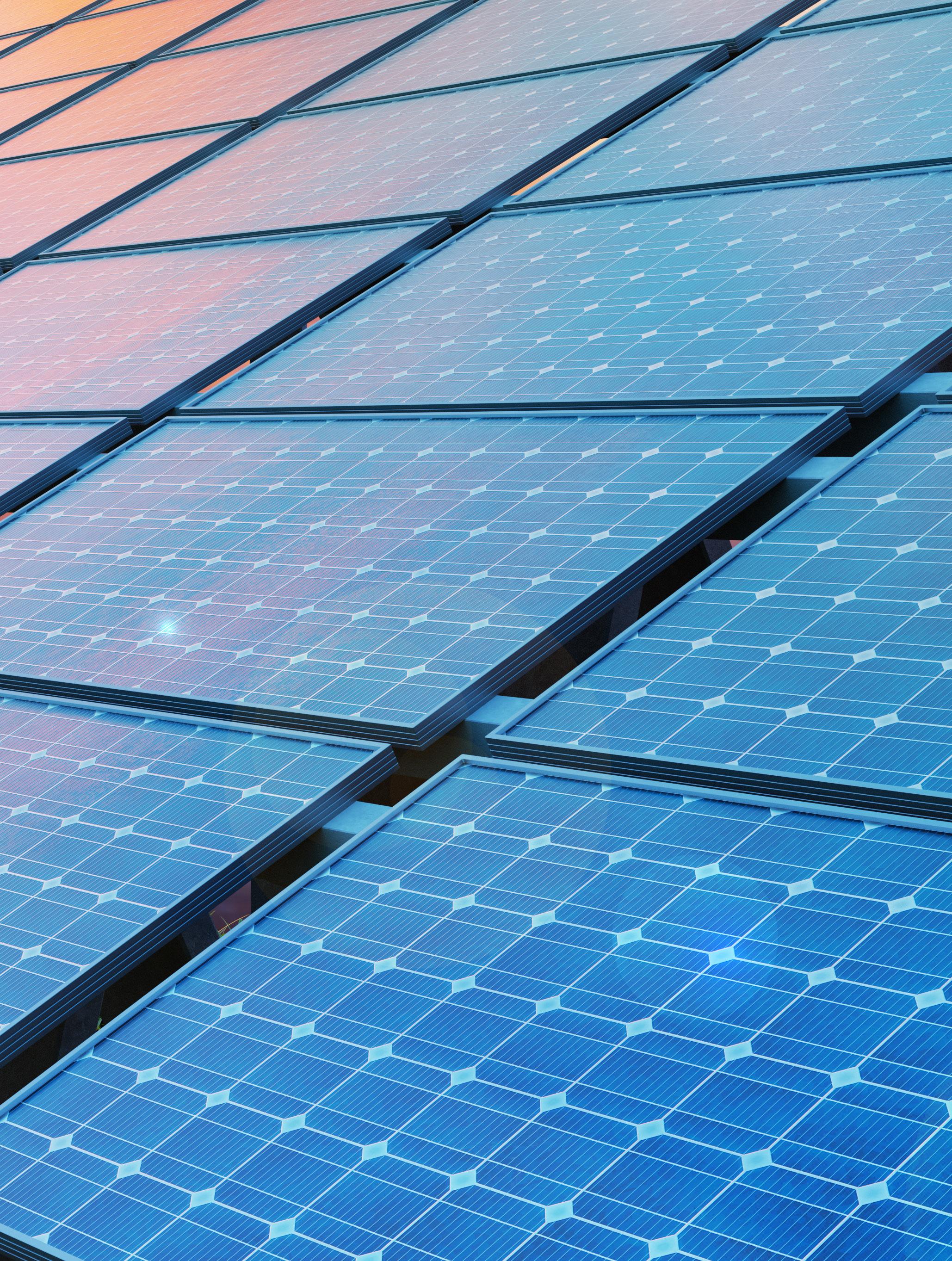
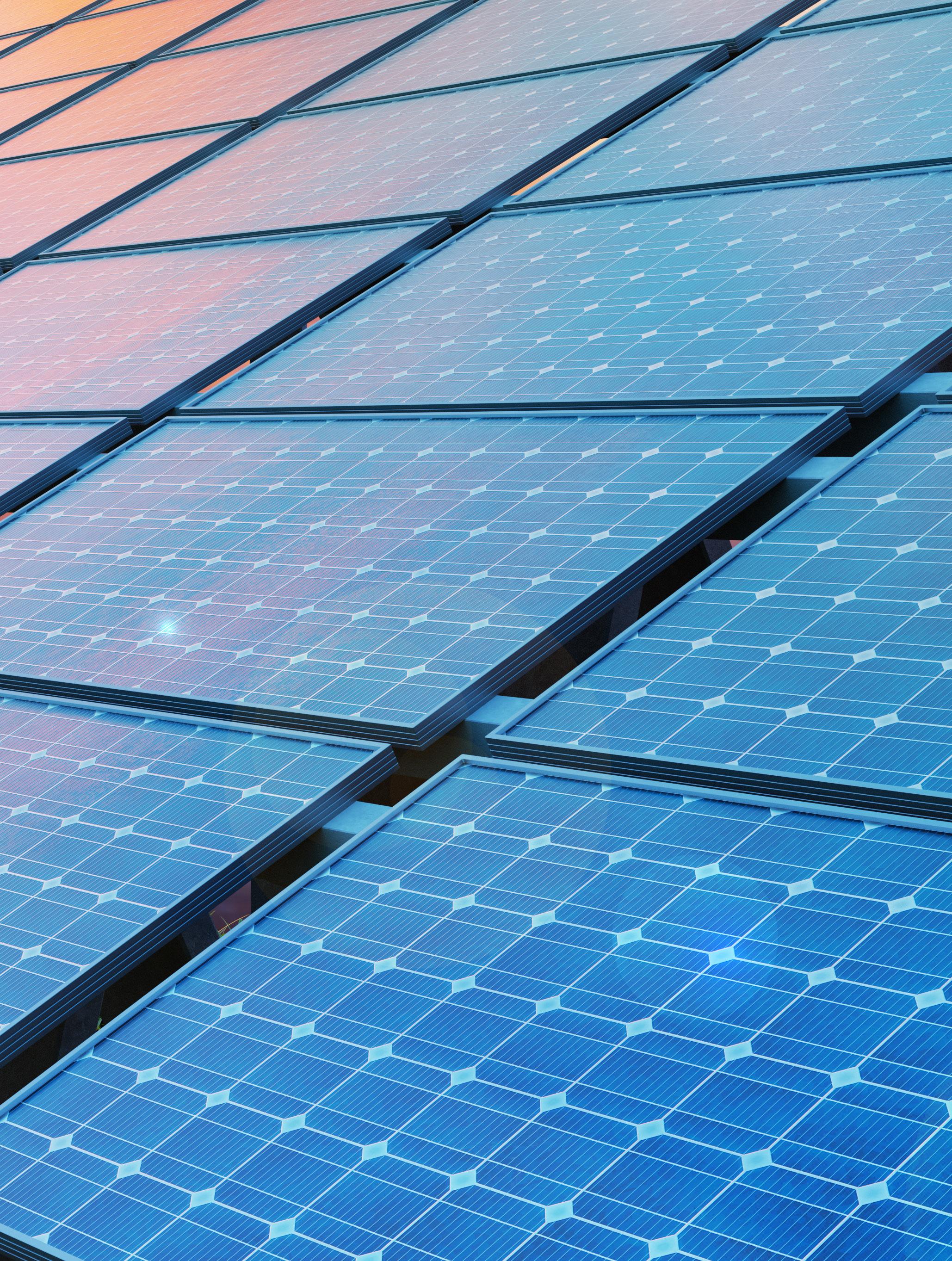
Proven Expertise in Decarbonization
About CMTA
CMTA was founded in 1968 and is recognized as a national leader in high performance, sustainable design within the engineering industry. Our firm has leveraged our expertise in high performance, energy-efficient design into a nationwide practice that includes consulting engineering, performance contracting and zero energy design, technology solutions, and commissioning services.
CMTA prides itself on its data-driven, performance-based design process. Performance-based design uses benchmarking of our projects’ real-world energy usage as a challenge to our engineers to continuously improve energy performance. CMTA’s first signature performance-based design project was Richardsville Elementary School, the nation’s first operational Zero Energy school. Since then, our Zero Energy projects have led our firm into the national spotlight.
Because we walk the talk, we are true partners vested in sharing our knowledge with our clients. Our corporate headquarters in Louisville, Kentucky and our Lexington, Kentucky offices are both zero energy buildings with perfect ENERGY STAR scores. And our CMTA Energy Solutions corporate office in Louisville is the first in the U.S. to operate as Zero Energy and achieve WELL Gold certification. CMTA strives to create strong relationships with building owners and managers while also focusing on the health and comfort of the people who live, work, and play in spaces we design.
CMTA Headquarters Campus Louisville, Kentucky

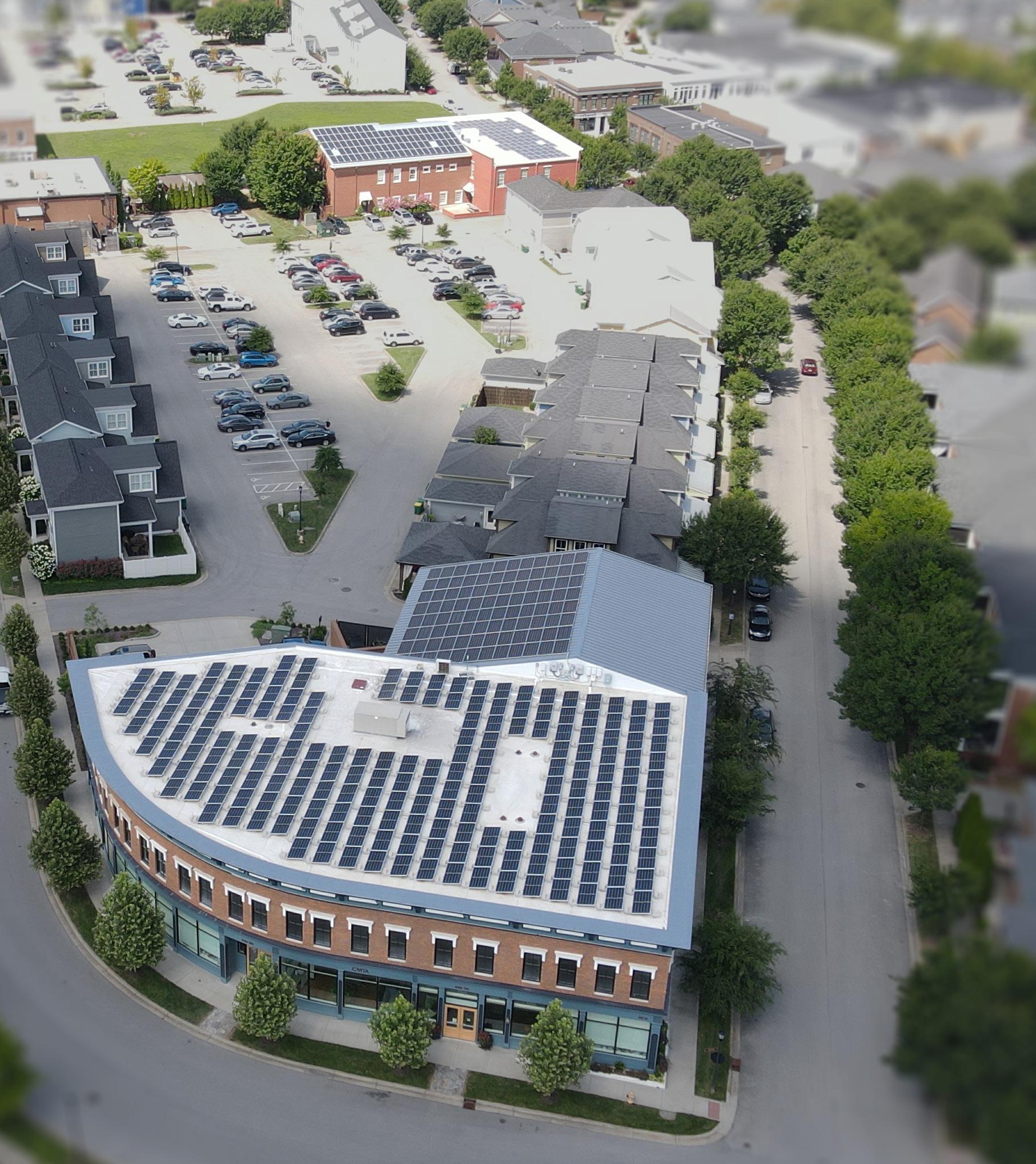
Approach to a Cleaner Future
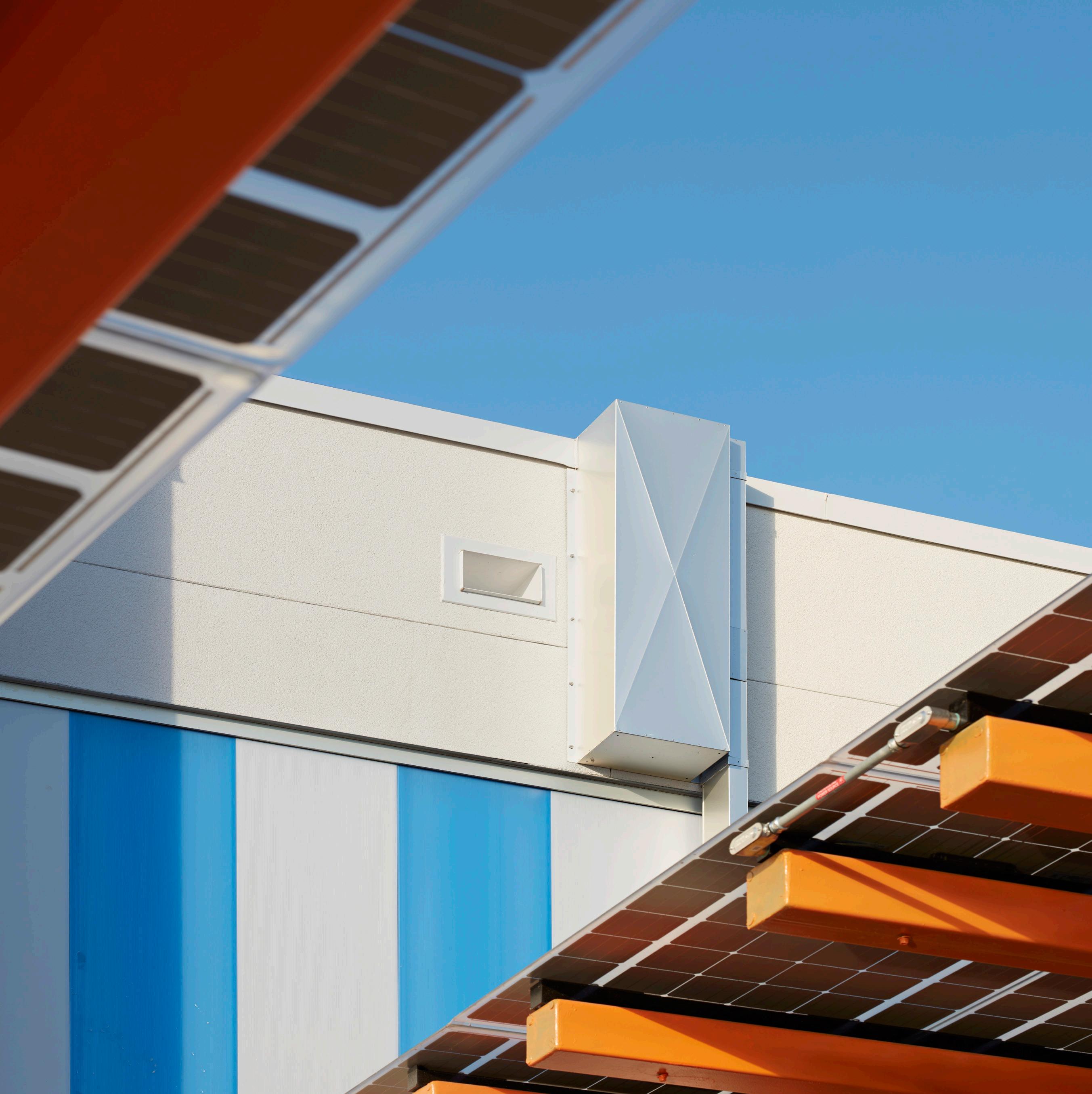
CMTA’s decarbonization approach is simple: by lowering the utility bill, we make direct impacts on decreasing carbon emissions. Our strategic focus on energy efficiency and grid harmonization results in a drastic reduction of the cost of going zero carbon.
Global Operational Zero Carbon Metrics
9+M SF in Zero Energy / Zero Carbon Facilities
180M+
Metric Tons of CO₂e Emissions Eliminated
202
LEED Certified / Targeted (21 Platinum; 87 Gold; 67 Silver; 27 Certified)
700+
ENERGY STAR Projects Scoring over 75
150MW Renewable Power Designed / Installed
5,500 Miles of Linear Geothermal
Wells Designed / Installed
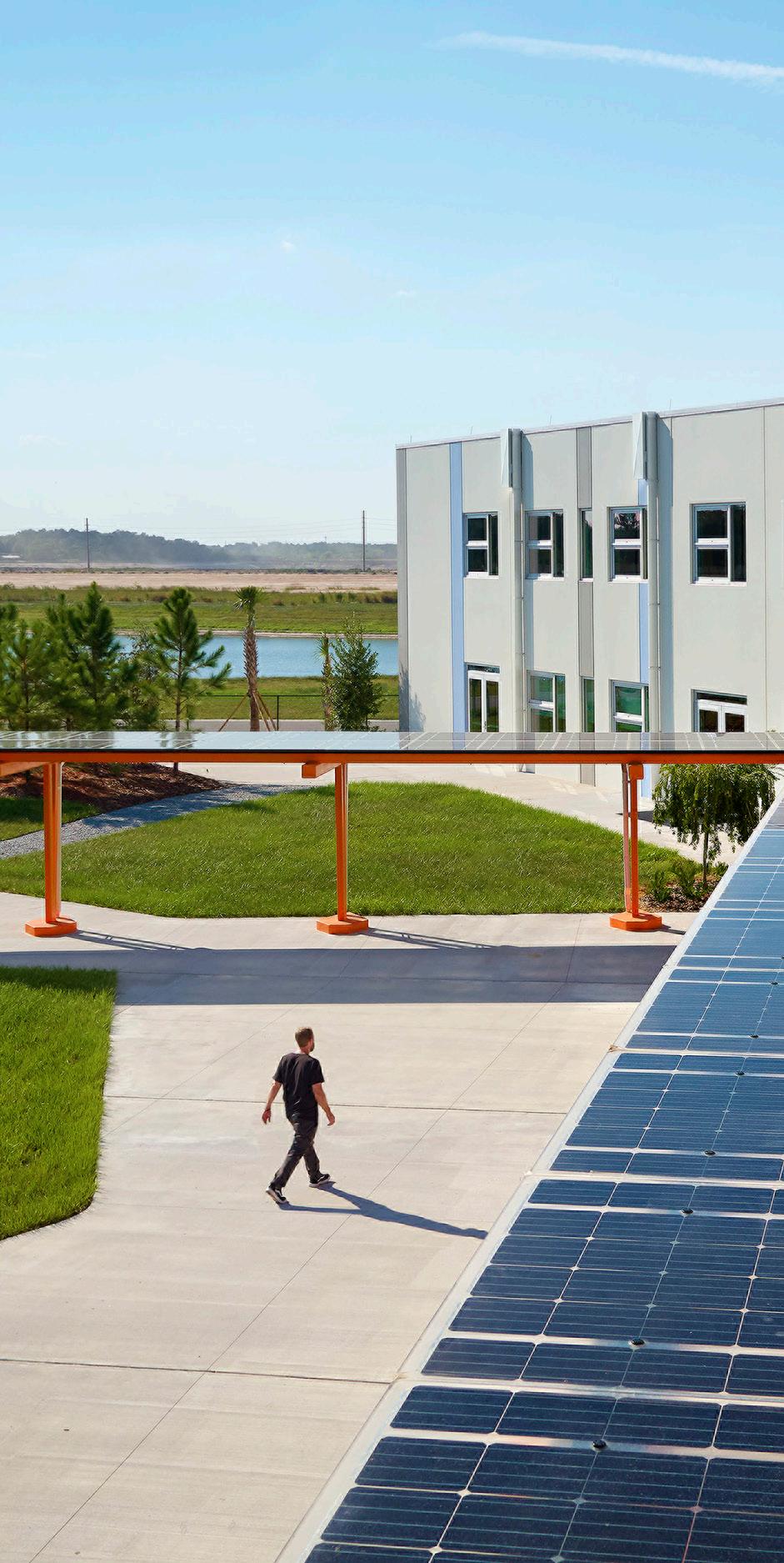
NeoCity STEM Academy First Zero Energy School in Florida, Kissimmee, Florida

Operational vs. Embodied Carbon
Operational carbon and embodied carbon are two different types of carbon emissions associated with the lifecycle of a building. Operational carbon refers to the carbon emissions associated with the ongoing operation of a building, including the energy used for heating, cooling, lighting, etc.
Embodied carbon, on the other hand, refers to the upfront carbon emissions associated with the materials and construction of a building. This includes the energy used to extract and process raw materials, transport them to factories, manufacture the product, and transport it to its destination.
By reducing operational and embodied carbon, we can reduce the environmental impact of our buildings.
Achieving Zero Carbon
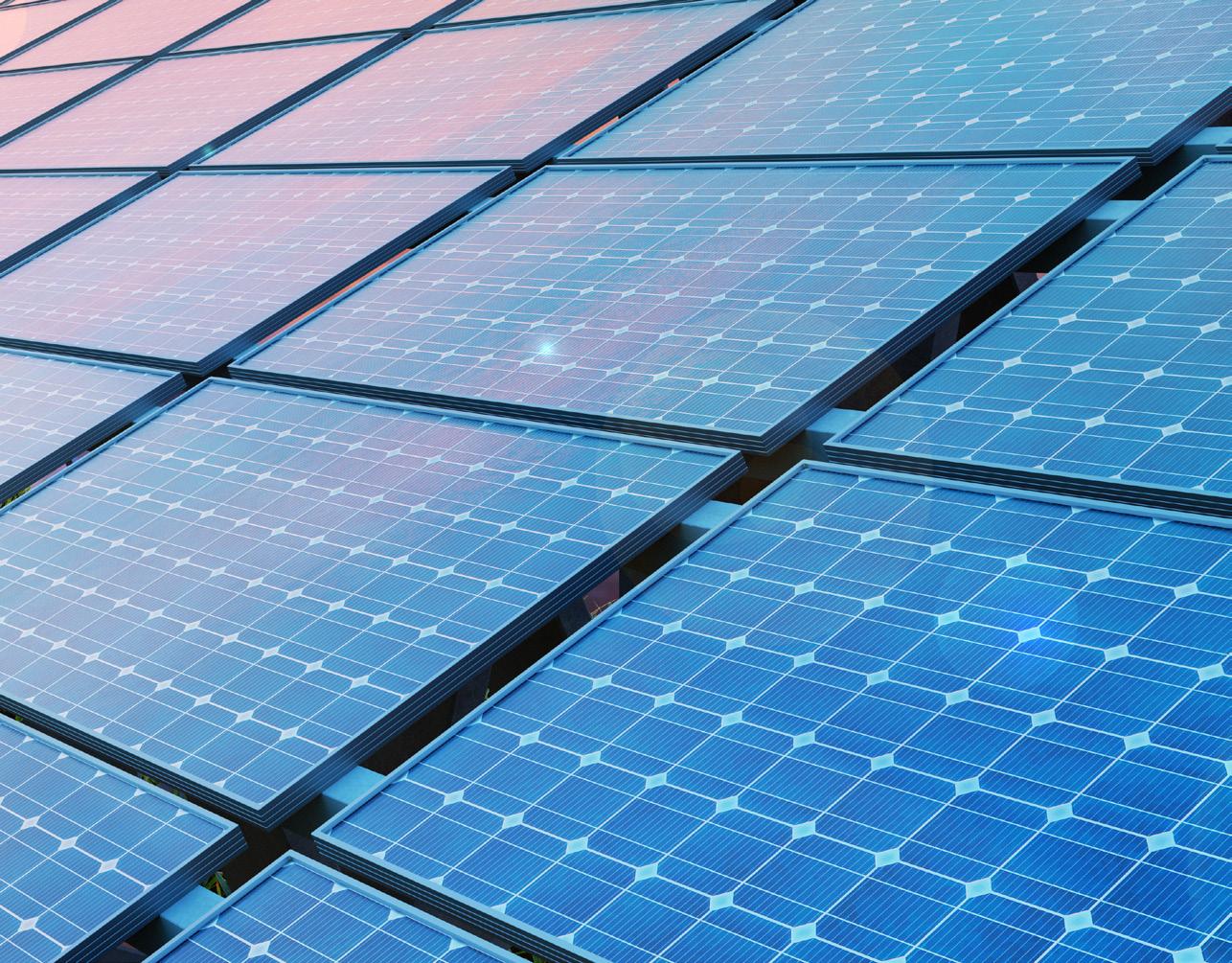
Reducing the carbon footprint of a facility starts with drastically reducing EUI well below national averages to eliminate carbon emissions.
Decarbonization of a building refers to the process of reducing or eliminating the greenhouse gas emissions associated with its construction, operation, and maintenance – including operational and embodied carbon. CMTA is partnering with industry giants, airports, academic institutions, healthcare systems, and more to develop roadmaps enabling their journey towards carbon neutrality.
Our comprehensive solutions leverage our building science leadership and Legence partners – planning and implementing systems tailored specifically for achieving zero emissions outcomes.
CMTA’s approach emphasizes drastic cost reduction through energy efficiency optimization and eradication of fossil fuels combustion on-site. This is complemented by a focus on incorporating on-site
renewable energy sources, ensuring grid harmonization, applying offsets where necessary, and minimizing upfront embodied carbon — all while accounting for the overall lifespan of the project. This approach includes, but is not limited to, the following strategies:
– Incorporating energy efficiency measures that directly impact the utility bill, such as high-efficiency HVAC systems, controls strategies, and LED lighting
– Improve building envelope thermal performance and reduce infiltration rates
– Use of on-site renewable energy generation, such as solar (photovoltaics), as well as procure renewable energy through utility contracts where possible.
– Retrofitting of existing buildings to enhance performance and reduce emissions
– Use of low-carbon building materials and construction techniques to reduce embodied carbon
– Carbon offsetting programs can be impactful, but are often of dubious quality, therefore, caution is advised.
Inflation Reduction Act
CMTA is the national leader in maximizing the impact of the IRA for facilities
The Inflation Reduction Act has the potential to be the single most influential legislation for energy efficiency and carbon reduction in our lifetime. The provisions detailed in the law will have significant impacts to upcoming new building and renovation projects across the country. At nearly $370B in direct funding, the Inflation Reduction Act represents the single largest investment in climate and clean energy solutions in American history. A major provision in the Inflation Reduction Act is the extension and expansion of tax credits for renewable and energy efficient technologies.
Investment Tax Credit
The Investment Tax Credit (ITC) will apply to the following technologies: solar energy, wind energy, geothermal energy, ground-source heat pumps, fiber-optic solar, fuel cell, microturbine, combined heat and power, energy storage, biogas, microgrid, and dynamic glass.
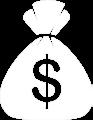
Direct-Payment for Private & Public Owners
Private owners and for-profit healthcare continue to qualify for the ITC. Public K-12 school systems, Universities, state and local governments that are tax exempt will qualify for the direct payment option in the ITC.
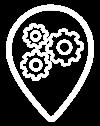
Domestic Manufacturing Incentive
The ITC base rate can be increased by 10% if certain domestic content thresholds are achieved. Those thresholds include at least 40% of the projects components and 100% of the steel and iron must be manufactured in the US.
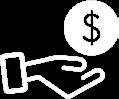
30% Base Tax Credit
ITC has a 30% initial base tax credit based on the efficiency or generation measure’s installed cost. To achieve this tax credit, prevailing wages and an apprenticeship program must be met. If these requirements are not met, the credit is reduced to 6%. These requirements have some exceptions, most notably, systems smaller than 1MW are exempt.
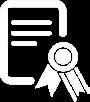
Tax Exempt Bonds
If a project is funded by tax exempt bonds, the ITC is fractionally reduced by up to 15% (eg. A 30% incentive is reduced to 25.5%). If only partially funded by tax exempt bonds, the reduction can be decreased.
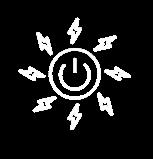
Energy Community Incentive
There is a potential for the ITC rate to be increased by 10% if the project is located in an “energy community.” External agencies and the US treasury are working to publish maps of these energy communities soon.

BIDMC Decarbonization Master Plan
Boston, Massachusetts
Beth Israel Deaconess Medical Center (BIDMC) is seeking to reduce their carbon usage by 50% by 2030 and by 100% by 2050. To achieve these aggressive goals, BIDMC engaged CMTA to develop a comprehensive plan to reduce energy consumption and provide creative ways to reduce its energy related emissions.
BIDMC is a world-class teaching hospital of Harvard Medical School and is located in the Longwood Medical Area of Boston. Their campus has 673 licensed beds, including 493 medical/surgical beds, 77 critical care beds and 62 OB/GYN beds with 5,292 births each year. The hospital has a Level 1 Trauma Center and rooftop heliport.
BIDMC is 2.8 million square feet, 28 building campus, with integrated inpatient care, outpatient care, laboratory and staff space.
CMTA is working with hospital staff to provide options and pathways to decarbonize utilities. As part of this effort CMTA is establishing a framework to identify and compare viable alternatives to the existing equipment and infrastructure that will enable BIDMC to achieve their longterm
emissions targets. CMTA is analyzing commercially available energy efficiency, energy supply, and distribution technologies to determine economic/sustainability benefits and associated costs.
CMTA is providing a utility decarbonization plan, in close coordination with BIDMC staff, using the data gathered in the exploratory/analysis phase. We are providing a prioritized list of alternative utility infrastructure upgrade scenarios that list capital and operating costs for each scenario together with expected emissions. Once completed, a final utility decarbonization plan report will be developed that compares these scenarios and provides recommendation on the best one to implement.
Project at a Glance Completion: 2023
Size: 2,800,000+ SF Examined Policy & Behavior; Collaborated with a variety of stakeholders; Renewable Energy Systems, Energy Conservation Measures
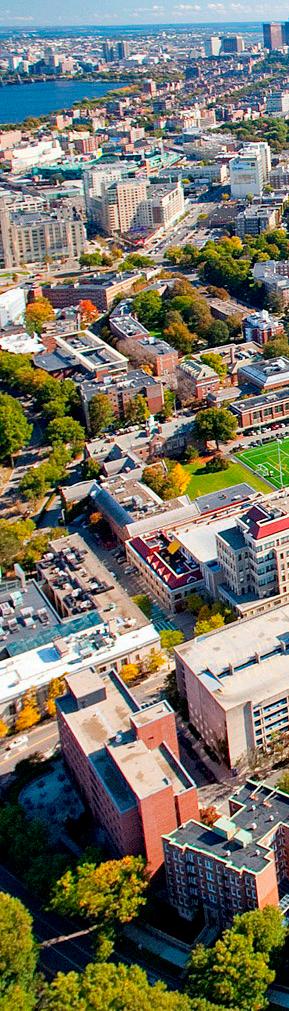

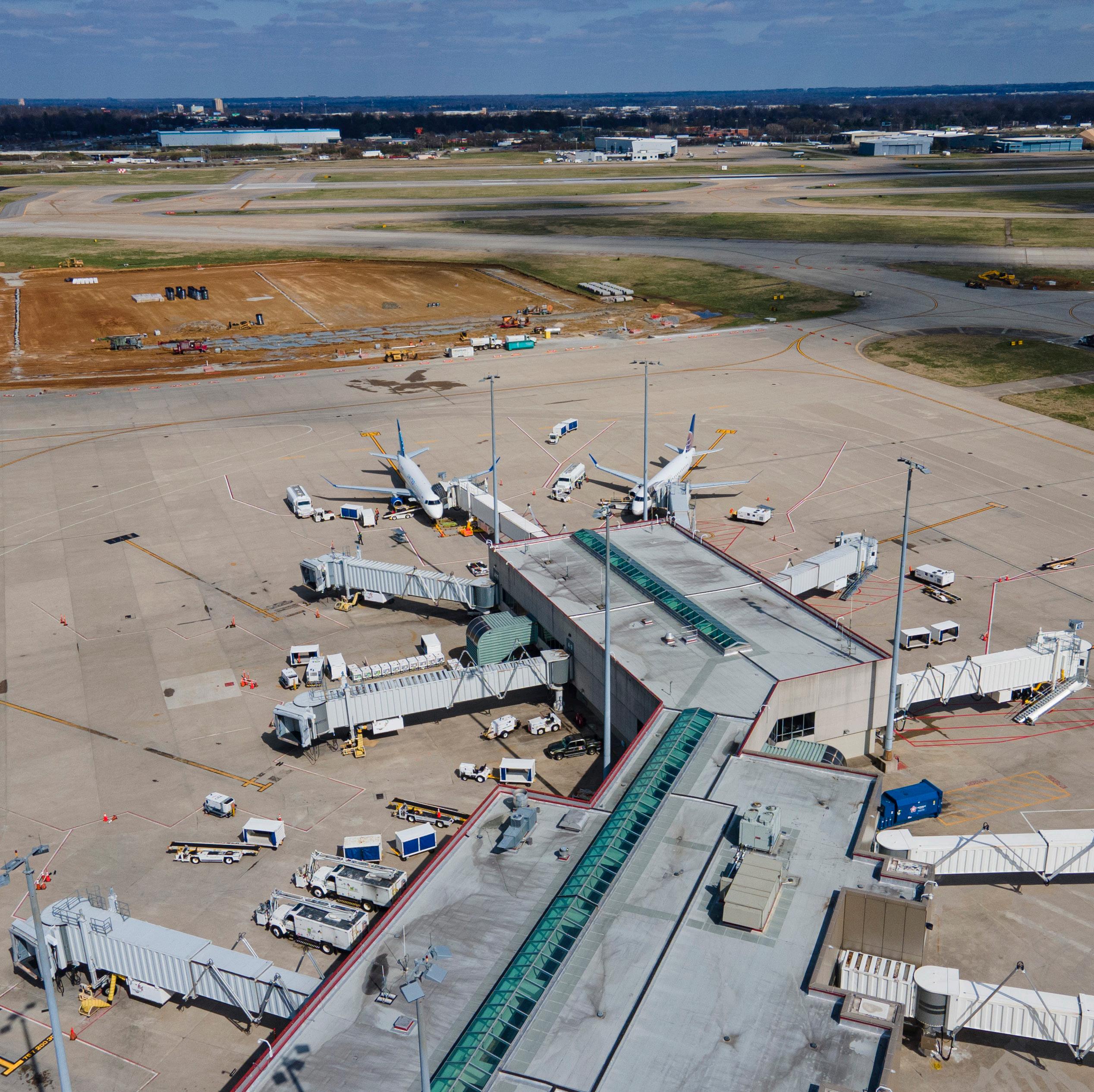
Carbon Footprint Reduction
Louisville Muhammad Ali International Airport Geothermal
Louisville Regional Airport Authority | Louisville, Kentucky
As Construction Manager at Risk (CMaR), CMTA is responsible for the design, acquisition, installation, and overall execution of current and future planned improvement projects for the Louisville Regional Airport Authority (LRAA), including architectural upgrades, energy management, energy conservation measures, and construction reporting services. The total project cost with all planned work phases is estimated to be between $60M to $100M.
As part of this multi-phased engagement, the team designed and implemented a large geothermal system for the Louisville Muhammad Ali International Airport — the largest of any airport in the United States. It includes 648 vertical wells each drilled 500 feet deep into the earth. The system saves
massive amounts of energy by using the earth’s natural temperature to heat in the winter and cool in the summer replacing the need for additional equipment. The HVAC system will increase the amount of outside air that is brought into the terminals and other spaces, which contributes to a healthier and more comfortable environment for travelers and airport staff.
This project will cut carbon emissions by more than 80% and reduce heating and cooling operating costs by nearly $400,000 per year. This geothermal system will use 40% less energy than traditional heating and cooling systems and will require less maintenance over the course of system life.
Project at a Glance
Completion: Ongoing
Cost: $60,000,000 to $100,000,000
Project Type: Renovation
Results:
– 80% Carbon Footprint Reduction
– $400,000 Operating Cost Savings – Decentralization of Equipment
– 100,000 SQFT of Future Expansion
– 14 Year ROI
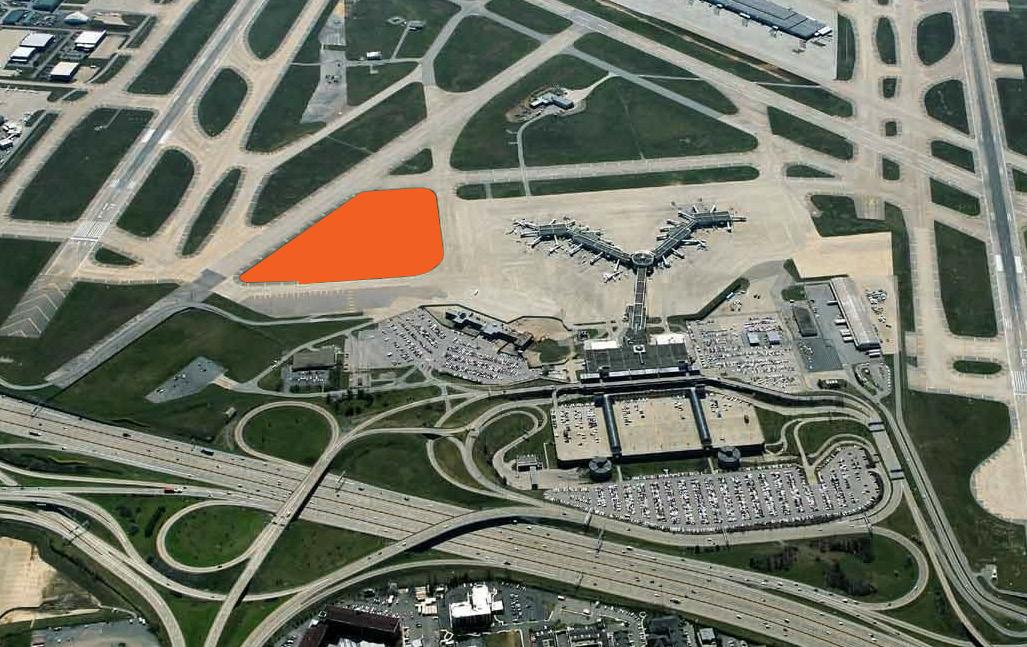
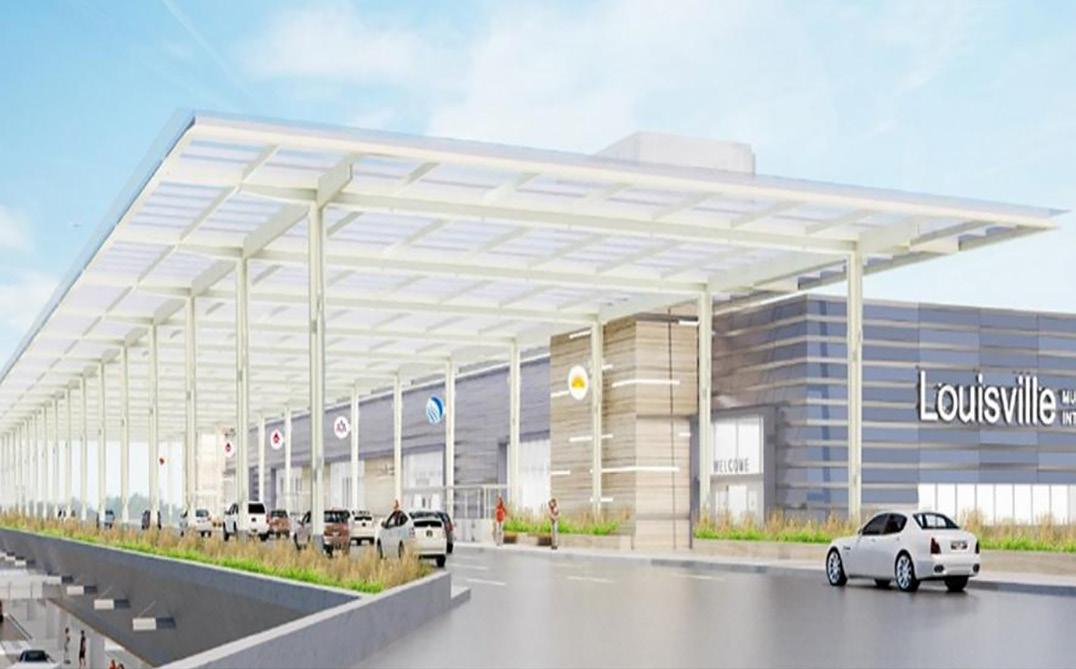
Research Campus Energy + Carbon Reduction Plan
Confidential R&D Lab Client | Minnesota
For this global R&D client, CMTA performed an engineering study of an undisclosed 600,000 SF, multi-building research campus. This engagement involved the assessment of existing campus infrastructure, operations, energy usage, carbon emissions and water usage.
Through a series of workshops, the team and stakeholders detailed potential facility improvements and energy conservation measures to create a campus masterplan focusing on drastic resource usage reduction, capital improvements, overall estimated cost of investment, and implementation schedule to meet the goals for a net zero energy campus. The resulting plan aligns with the client’s ESG goals to provide a roadmap to halve carbon emissions by 2030 and drastically reduce operational carbon and water usage to achieve net zero by 2050.
The team compared many options moving forward for optimization of onsite energy performance with respect to cost. This involved comparing the EUI of a planned 200,000 SF addition and its affect on the carbon neutrality roadmap. In addition, the team explored ways to apply the Inflation Reduction Act (IRA) to provide a savings opportunity for the client.
Ultimately, the team calculated the campus needs 9.5MW of generation to achieve on-site zero energy capabilities and building electrification. We calculated that the campus has a generation potential of 12.2MW of on-site renewable generation. The PV solution included various rooftop Photovoltaics (PV), parking canopies, and ground-mounted technologies. Max on-site solar harvesting potential
Project at a Glance
– Size: 600,000 SF across multiple buildings, 100-acre campus
– Assessment of Existing Campus Infrastructure
– Develop Strategic Plan for Capital and Infrastructure Improvements
– Integrate Energy Conservation Measures (ECMs) and Facility Improvement Measures (FIMs)
– Maximize 12.2 MW On-Site Renewable Generation Potential
Project Energy Goals
– 50% Site Operational Carbon reduction by 2030
– Zero Site Operational Carbon and 50% Potable Water Reduction by 2050
– 100% Renewable Electricity by 2030
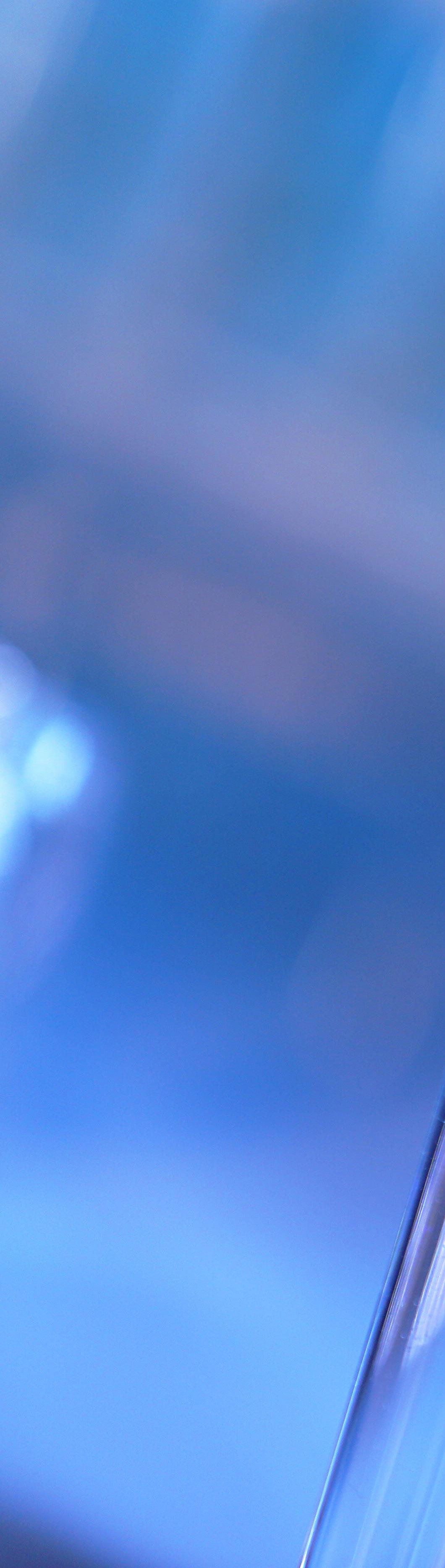
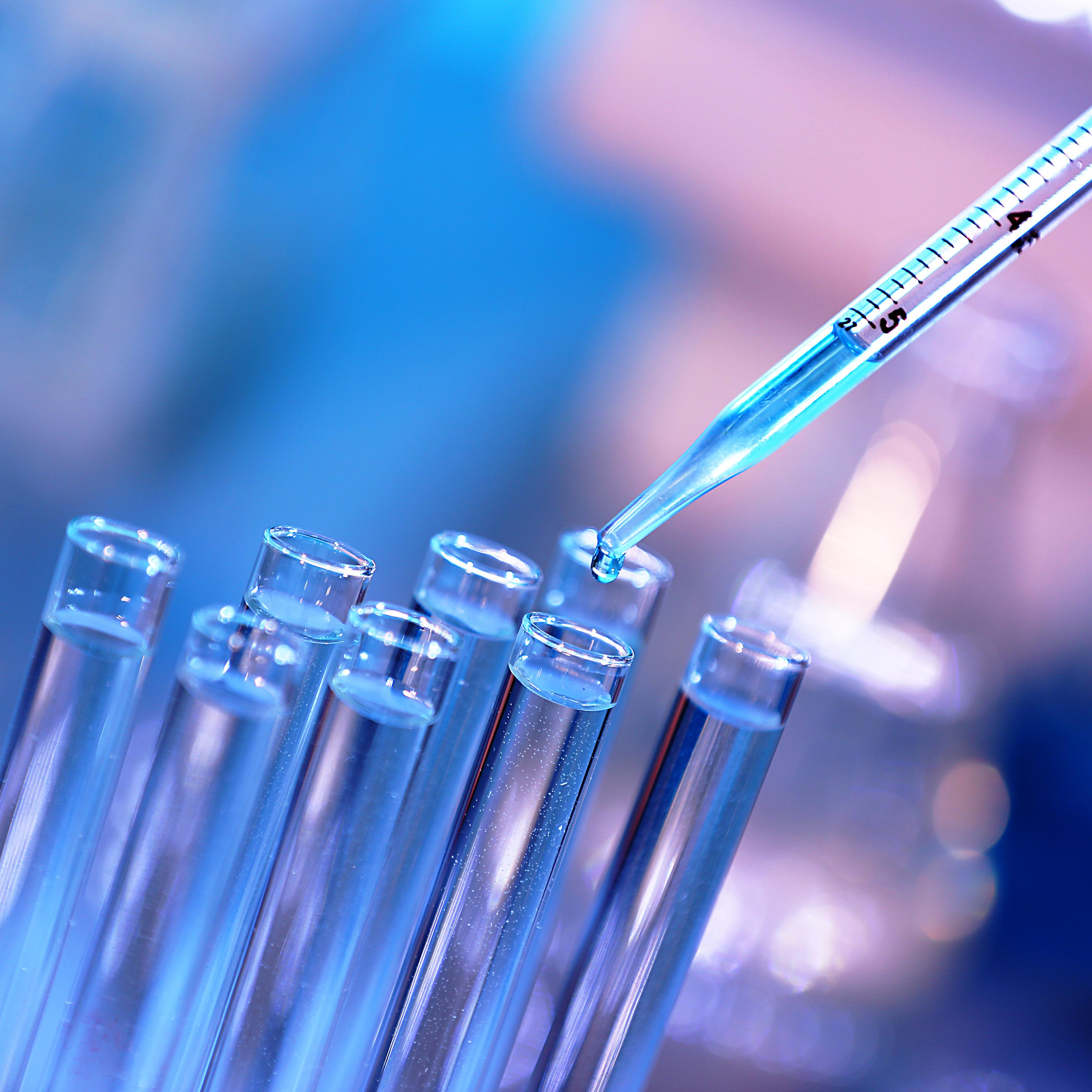
Boston Medical Center
Boston, Massachusetts

CMTA’s knowledge and attention to detail made this difficult project a major success with energy savings of $1.5M. Thanks to their expertise, we have the most resilient hospital cogen plant in Boston.
— Bob Biggio, Boston Medical Center
$1.5M Annual Utility Savings
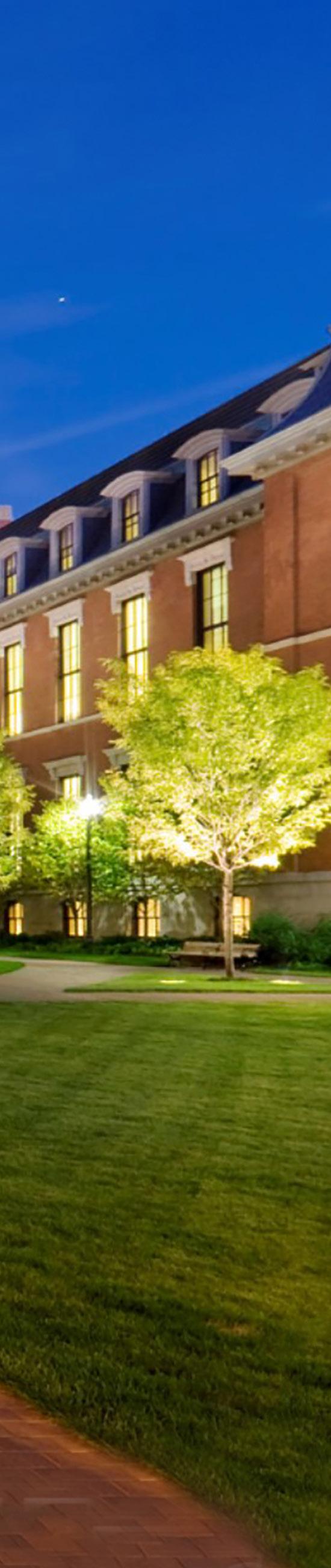
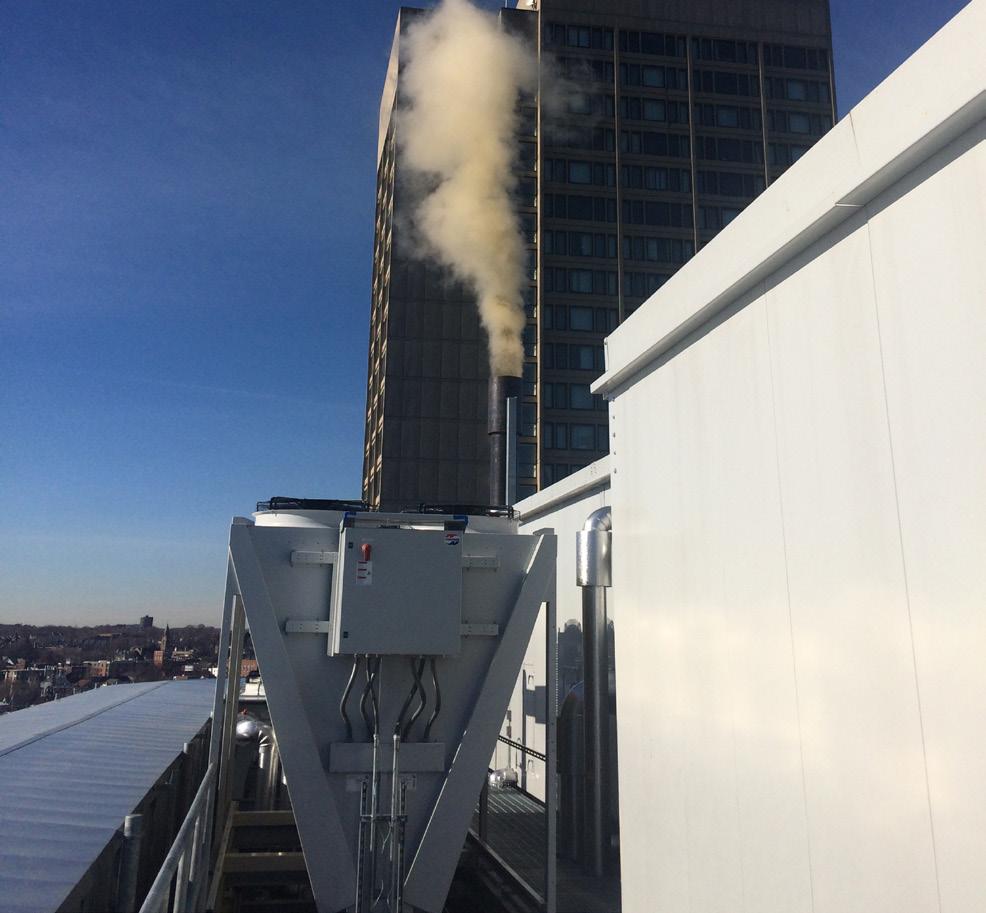
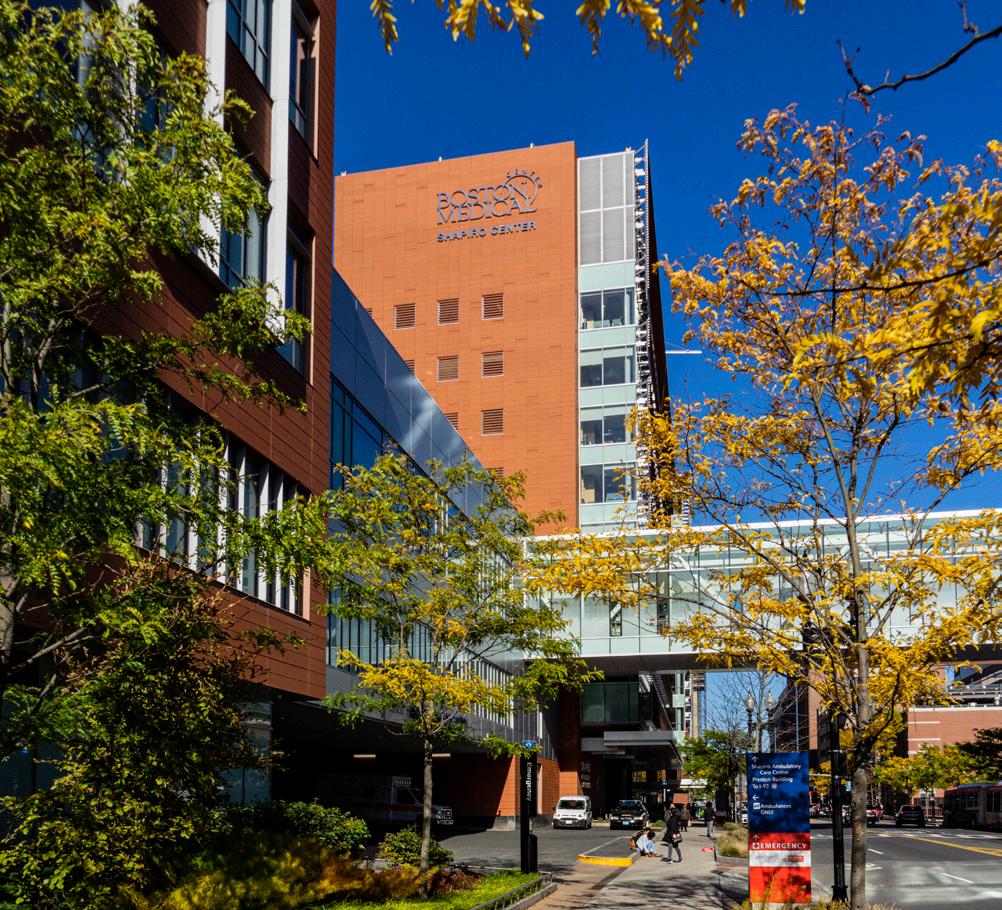
Boston Medical Center’s (BMC) main objectives for a cogeneration plant were to reduce energy cost, reduce their carbon footprint, and increase the resiliency of their inpatient care buildings, totaling 1.5 million square feet during a major campus consolidation effort. A single 2 Megawatt internal combustion engine cogen system offered BMC the best return on investment and enough power to keep their most critical inpatient care buildings energized and heated in the event of an extended normal electric power outage or another catastrophic event. This cogen system provides $1.5M of annual operating savings.
As significant energy reductions are a cornerstone goal for BMC, so is carbon neutrality. As a result, BMC engaged in the largest collaborative power purchase agreement (PPA) in the United States. 16 megawatts of the 60 megawatt solar field is allocated to BMC to make BMC a zero-energy campus. Through the cogen, PPA, and campus consolidation strategies, BMC has reduced its carbon footprint by 90% since 2011.
Project at a Glance
Completion: 2019
Size: 1,500,000 SF
Cost: $13,500,000
Project Type: Existing Facility Planning & Design Awards / Certifications: Zero Energy / Carbon Neutral
Practice Greenhealth: Top 25 Green Hospital Nationally Becker’s 60 Greenest Hospitals in America
Global Carbon Reduction and Sustainability Plan
Fortune 50 Aviation Manufacturing Company
CMTA, in partnership with Donovan Energy, has embarked on a multi-year evaluation of a global company’s domestic and international sites in the US, Italy, Singapore, Brazil, Europe, and India. The confidential company’s goal is to identify at least a 70% reduction in emissions across all the aviation division’s sites, which will encompass more than 10 million square feet. The reduction strategy will include infrastructure efficiency improvements and renewable energy procurement, ultimately aligning the company to their commitment to be carbon neutral by 2030.
At each site, the team will establish benchmarking by evaluating energy usage and utilizing baseline data. This will involve both on-site walkthroughs and remote audits of select manufacturing sites and testing facilities. Infrastructure efficiencies that have the highest impact on carbon reduction will be identified along with the associated supporting cost estimates and a return on investment. The assessment and resulting report will also include potential renewable energy systems, with local market and regulatory requirements, procurement, PPAs, etc. in mind.
The overall strategic roadmap developed will consider timeline, procurement and progress milestones as well as opportunities to leverage federal, state and local incentives.
Project at a Glance
20 Domestic and International Sites
Carbon Reduction Roadmap
Sustainability Plan
120,000 MTCO2e
Annual savings potential identified through efficiency improvements and electrification opportunites.
26,000 Cars
Equivalent to 26,000 Gas-powered Cars Driven for One Year
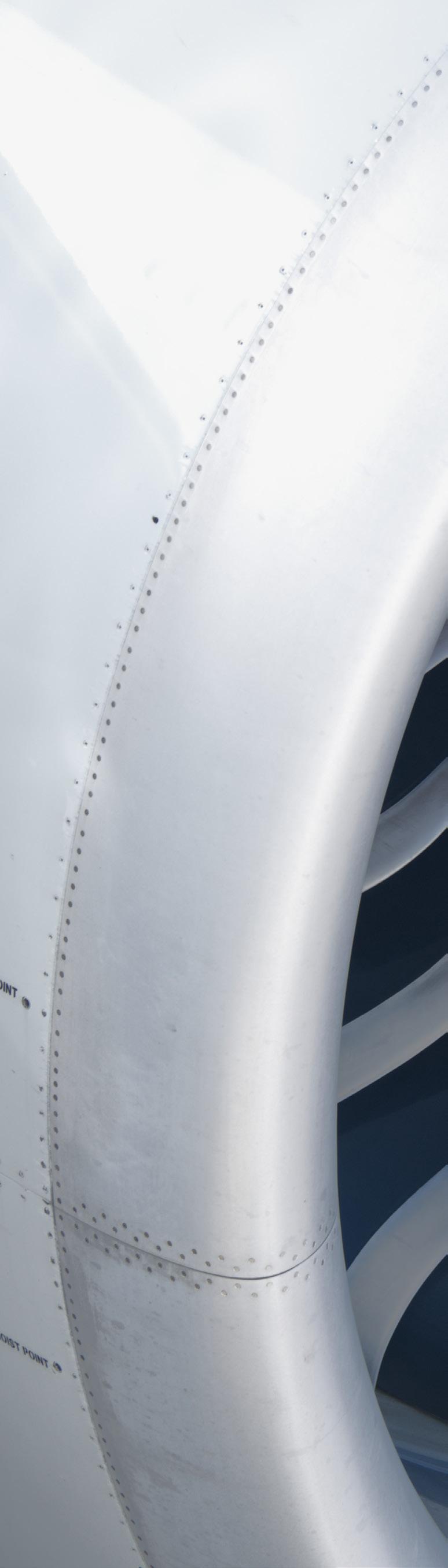
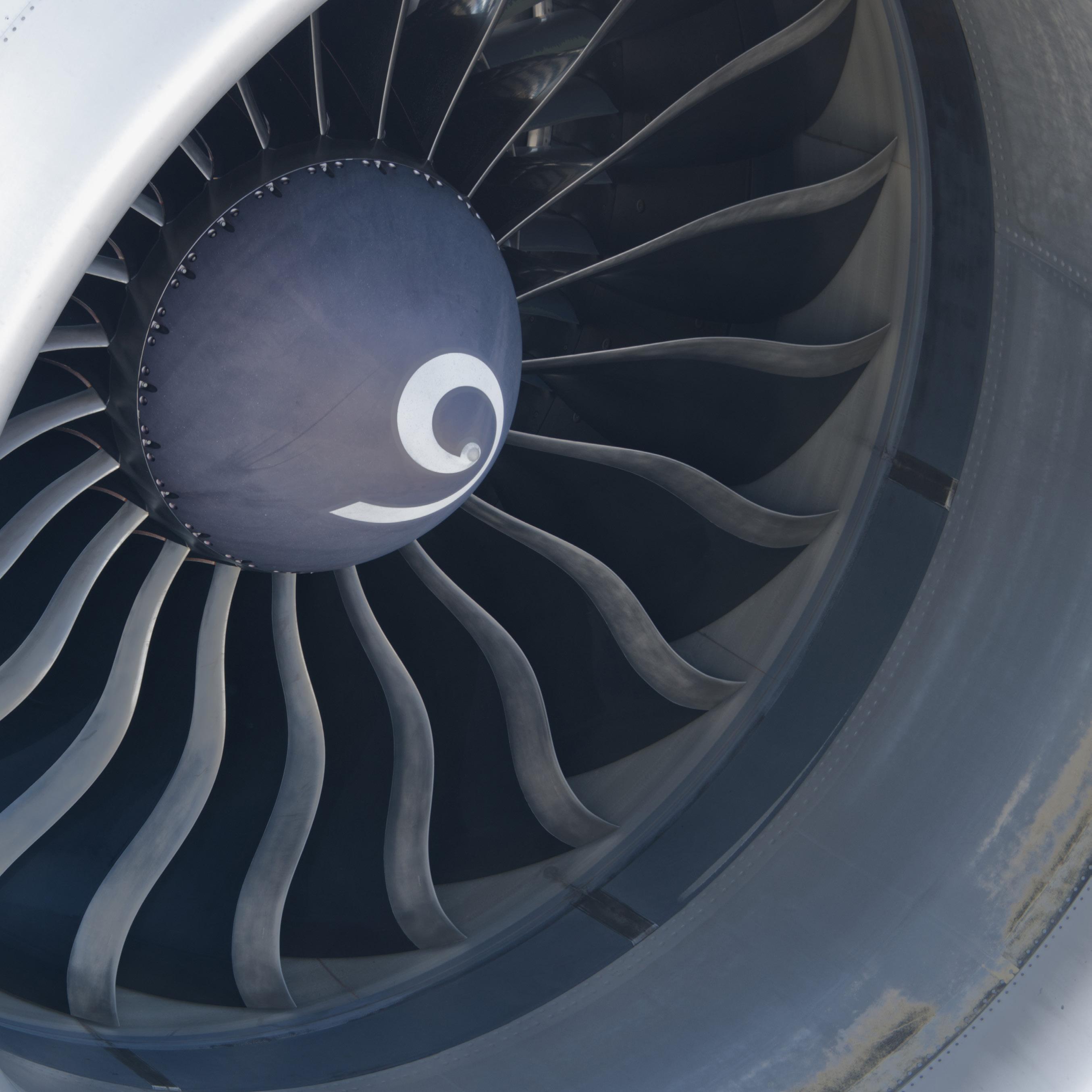
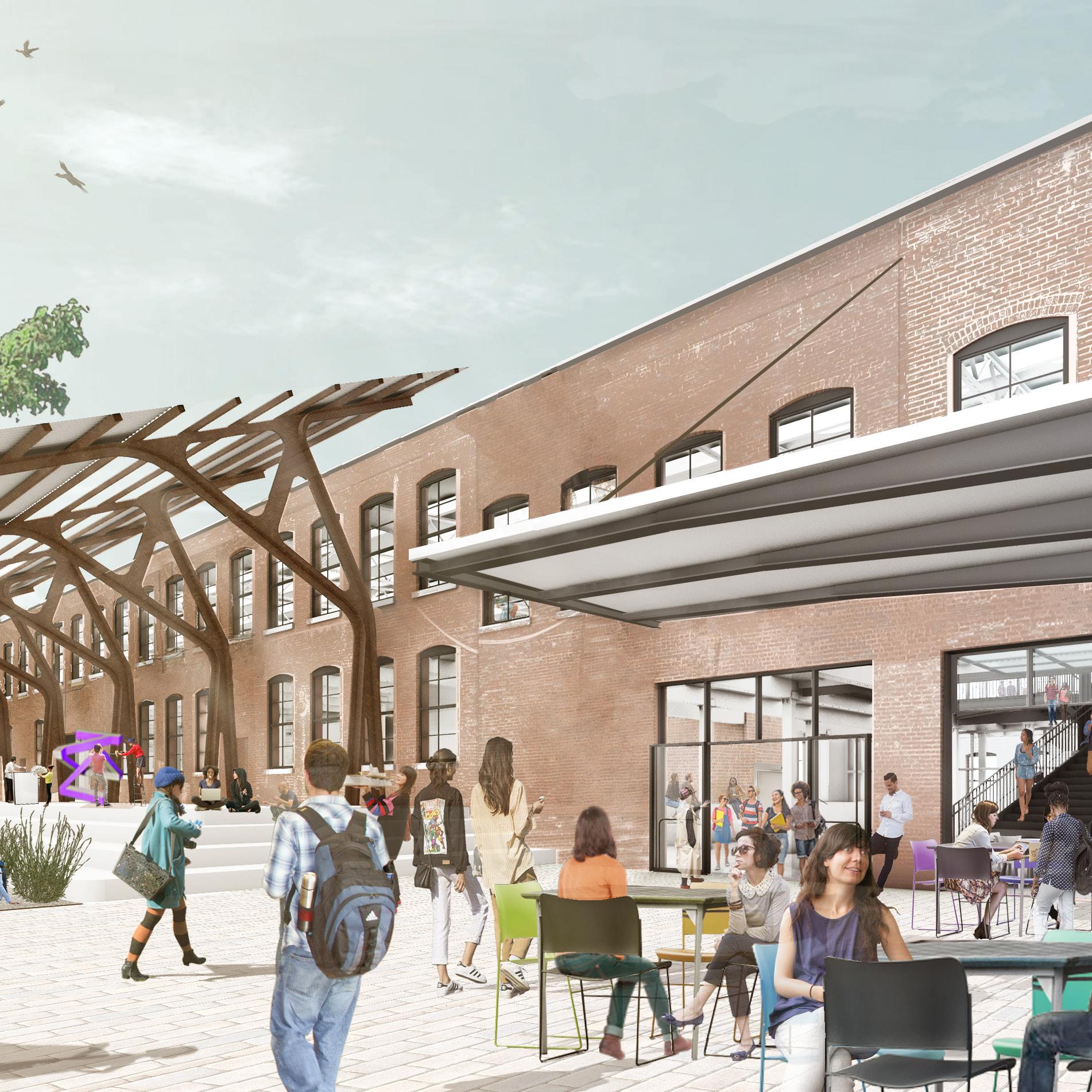
UK College of Design (Gray Design Building)
University of Kentucky | Lexington, Kentucky
Rendering courtesy of Studio Gang
Operational Carbon Comparison
50-year Life Cycle
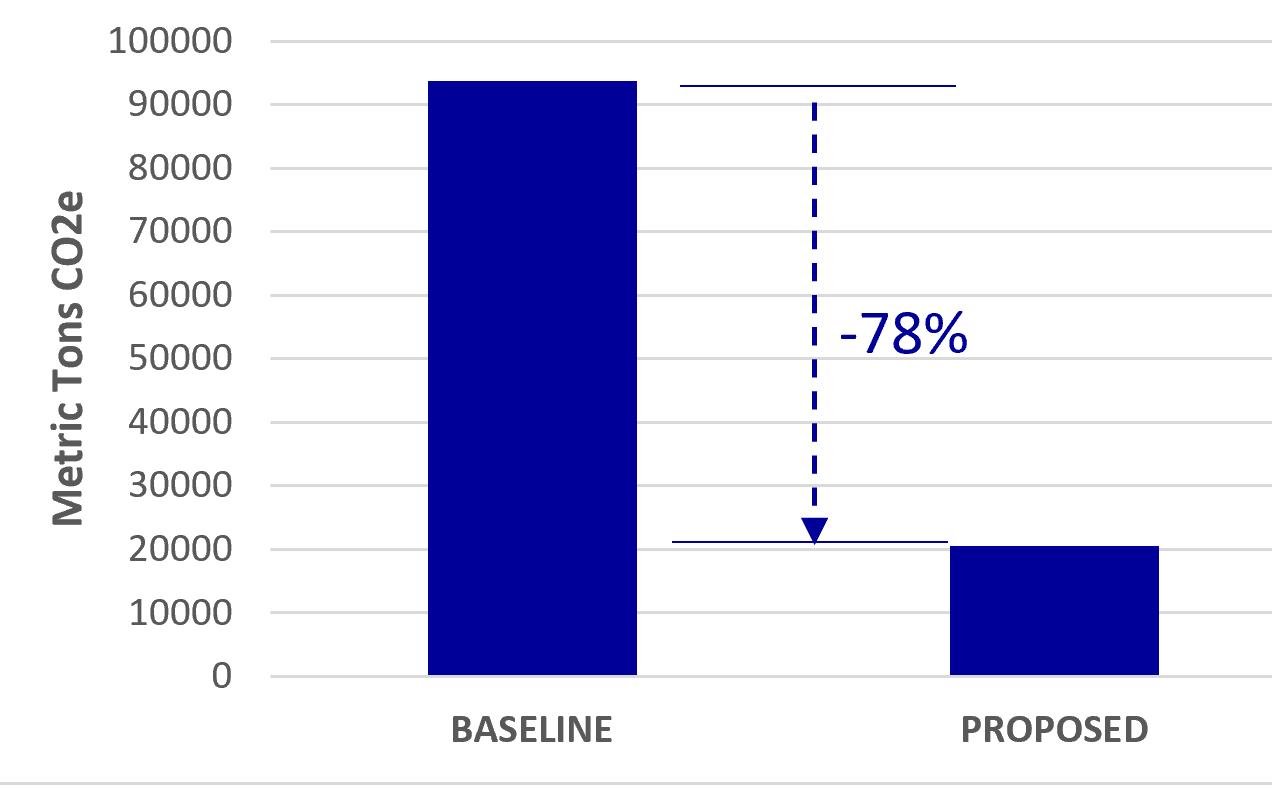
Embodied Carbon Comparison
50-year Life Cycle
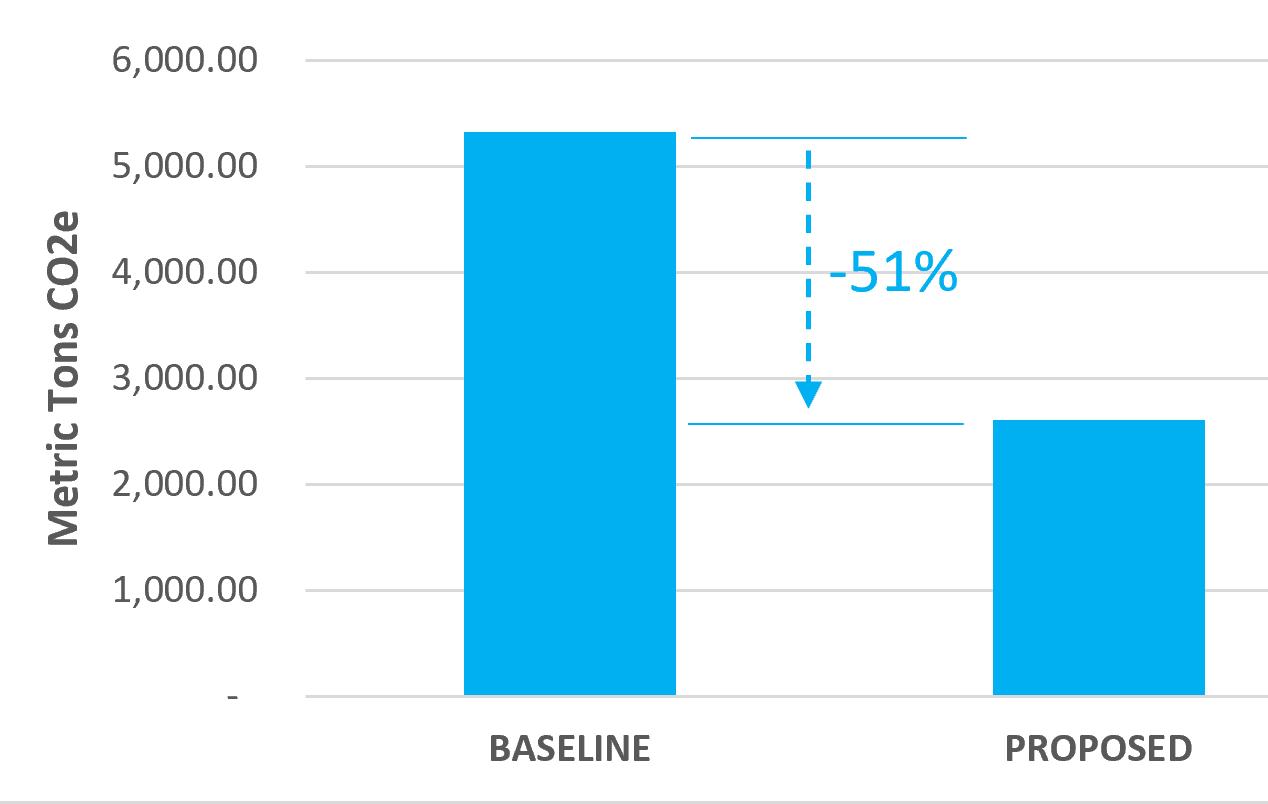
75,899 MT Reduced Total Emissions
over 50 Years
1,254,996 Trees
Equivalent to 1.2M Trees Planted and Grown for 10 Years
16,890 Cars
Equivalent to 16,890 Gasolinepowered Cars Driven for One Year
This adaptive reuse project creates the most sustainable building on campus by not only drastically reducing operational carbon emissions, but also the embodied carbon of the historic building. It will become a living example of an environmentally focused yet beautiful design provides the first electrified building on campus and showcases resiliency to the world’s future designers. Originally spread across six buildings throughout the UK campus, the University had a goal of consolidating the College of Design (CoD) into one building. Historic Preservation being one of the main programs at the CoD, it was natural to take on the renovation the abandoned Reynolds Tobacco warehouse.
CMTA provided MEP engineering, security, technology, and audio/visual services for this signature project. To enhance energy reduction, the project designers incorporated a geothermal system (the largest on campus) with 87, 550-feet deep wells will supply energy for heat pumps. The University plans to mark the well locations to showcase their environmental strategy to students and visitors.
Additionally, the enhancement of the building envelope reduces the overall energy consumption. The exterior walls and roof are being insulated, ensuring the building will have heating and cooling retention while lowering energy costs, lessening noise intrusion and providing an overall improved environmental impact. The windows are being replaced with energy efficient, high performance windows and will improve energy savings, protect from UV rays, reduce condensation, provide noise protection and be less maintenance.
Project at a Glance Completion: 2023
Size: 131,700 SF
Cost: $30,000,000
Project Type: Renovation, Adaptive Reuse
UMass Dartmouth Decarbonization Study
Dartmouth, Massachusetts
UMass Dartmouth has approximately 2 million square feet of space across 27 buildings. CMTA is helping DCAMM and the University evaluate and revise their energy goals and objectives. Currently, we are helping align a phasing plan to reflect and support the infrastructure needs of a large renovation of the Liberal Arts building. Additionally, CMTA is developing an operations plan that addresses near and far term energy improvements at multiple campus buildings. The scope of work includes:
– Developing a pragmatic plan to comply with Executive Order 594
– Reviewing Decarbonization Study and other project documents
– Developing recommendations for alternative approaches
– Developing a plan to eliminate steam systems
– Developing a plan to decommission the cogen plant while maximizing it’s useful life
– Developing implementation phasing plan that balances first costs, age/condition of infrastructure (deferred maintenance), and emissions reduction potential
– Providing construction estimates and savings
– Providing a final report and presentation materials
Project at a Glance Size: 2.7M SF
Project Features: Decarbonization Study, Phasing Plan, Operations Plan, Emissions Reduction Potential
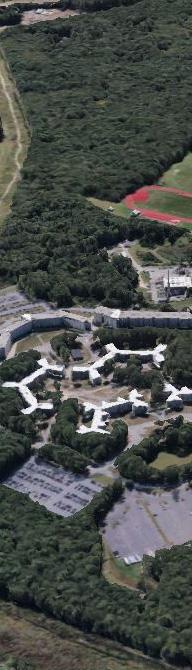
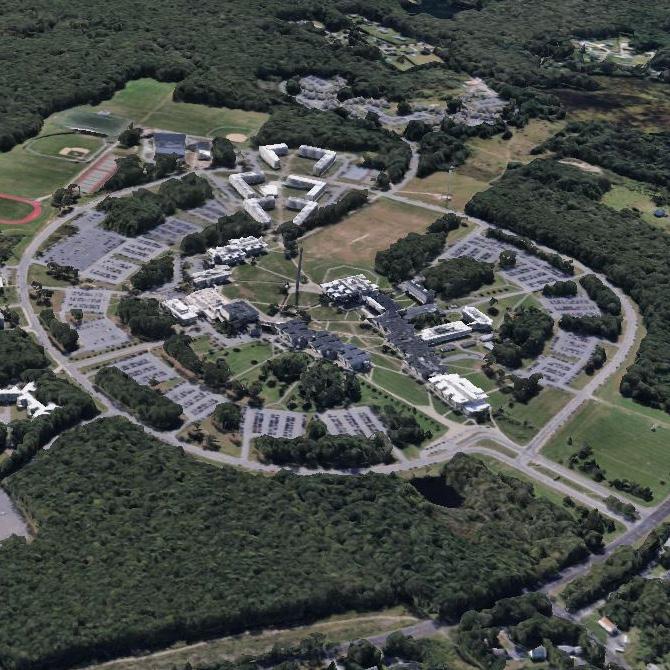
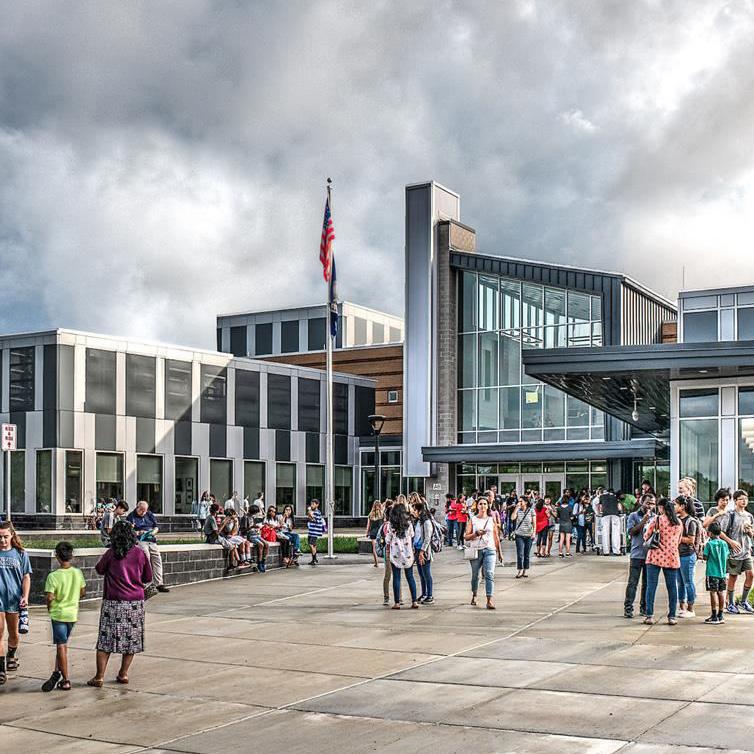
Sustainability Master Plan + Carbon
Analysis
Loudoun County Public Schools | Virginia
Loudoun County Public School’s (LCPS) long-term commitment to sustainability and efficient operations has allowed the school system to serve as a national leader in energy conservation and efficiency. As one of the largest school districts in Virginia, the system serves more than 78,000 students in over 100 facilities. LCPS’ commitment demands a strong focus on reducing its carbon footprint through decisions regarding capital improvements, energy use, transportation, and other polices within the Board’s control.
CMTA was engaged to develop a sustainability report that highlighted — from an energy, sustainability and emissions standpoint — how the district’s efficiency strategies and operational decisions have shaped its sustainability path. As such, the focus was specific to the historic and current energy and environmental impact of its facilities and operations.
To develop this comprehensive report, CMTA provided benchmarking and analysis for the energy usage of the district’s carbon emissions, water and sewer utilization,
and transportation division. In addition, we analyzed the energy consumption profile of existing buildings, which encompasses more than 11.7 million SF, to ensure LCPS is designing and constructing the most efficient facilities feasible in the future.
The data gathered from the report was used to outline next steps for the District’s Sustainability Master Plan. CMTA provided key approaches to energy conservation and efficiency including an energy savings performance contract, 8-year phased plan, new construction analysis, information about renewable energy credits, and step by step guidance for CO2 emissions reduction and water usage reduction.
Project at a Glance Size: 11,7000,000 SF (100+ facilities)
Completed: 2021
Sustainability Master Planning Carbon Benchmarking and Analysis
55% Reduction of CO2 emissions across all facilities by 2030 (with geothermal system selection)
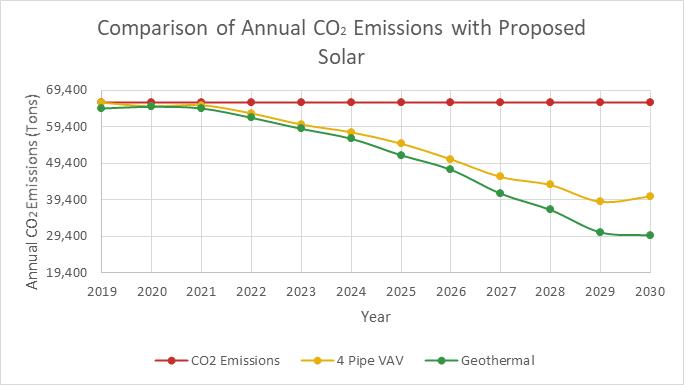