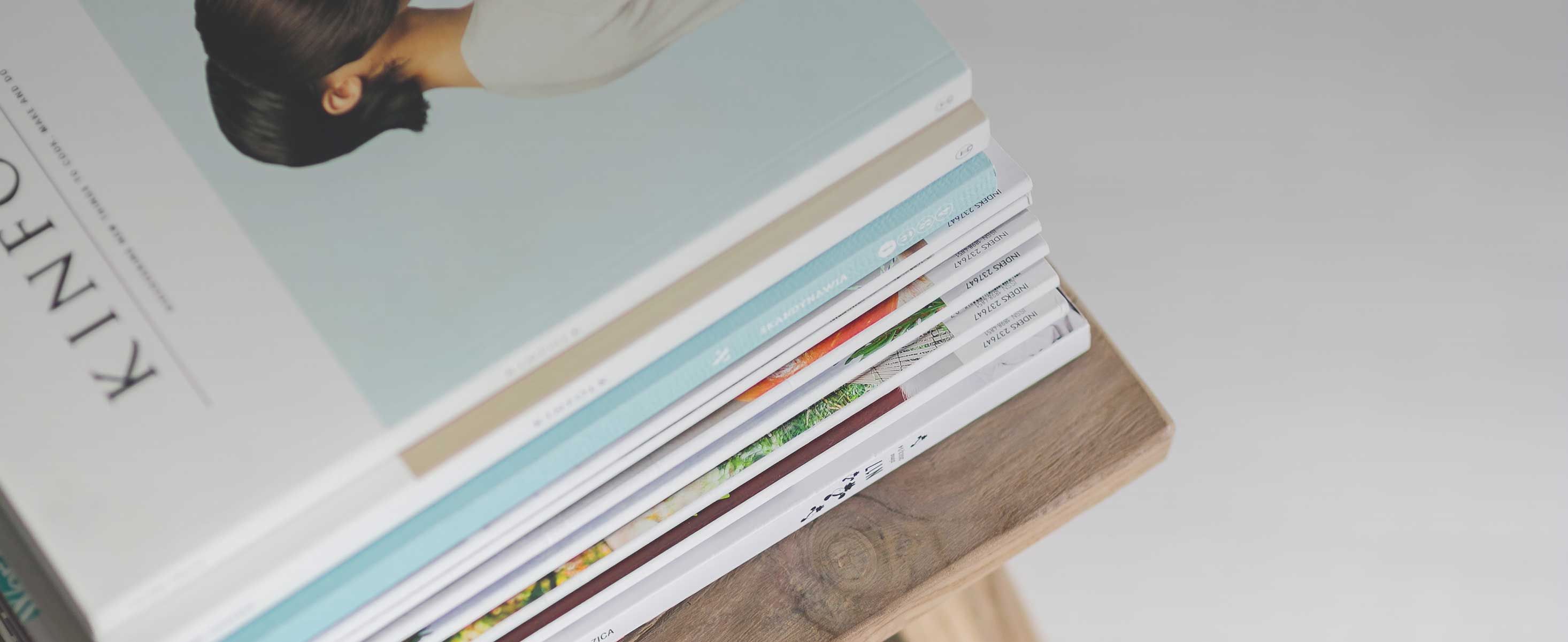
4 minute read
General information Product overview
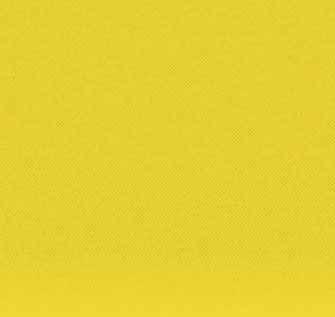
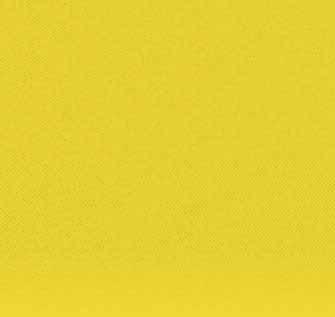
Coated abrasives Applications guide
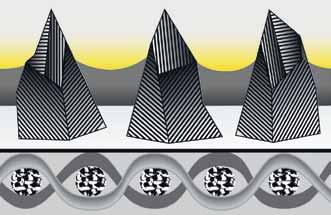
Coated abrasives are abrasive products that are made out of more or less flexible backing material upon which grit is anchored with a bonding agent. The product family “coated abrasives” includes abrasive belts, rolls, sheets, strips and discs. They comprise of the following four, optionally also five, components (please refer to the illustration on the right).
1. Backing
2. Base coat
3. Grit
4. Topsize coat
5. Optional: additional coating
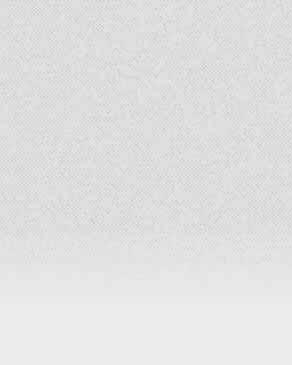
Structure
1. Coated abrasive backing
The backing is coated with grit and transfers stock removal forces onto the workpiece. The following backings are primarily used in the manufacture of coated abrasives:
Paper Cotton cloth Polyester cloth
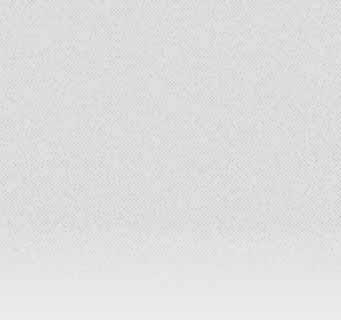
In addition, at Klingspor the following backings are used exclusively for individual products and/or for specific requirements/applications:
Fibre (is used exclusively for fibre discs on portable angle grinders) Film (is used exclusively for the products FP 73 W and FP 73 WK)
GX-blended cloth (special cotton/polyester blend for flexible yet highly tear resistant belts)
Coated abrasives Applications guide
Backing Description
Application examples
A – paper approx. 95 g/m² profile + surface finishing (hand)
B – paper approx. 105 g/m² profile + surface finishing (hand and machine)
C – paper approx. 110 g/m²
D – paper approx. 130 g/m²
E – paper approx. 250 g/m²
F – paper approx. 300 g/m²
G – paper approx. 400 g/m²
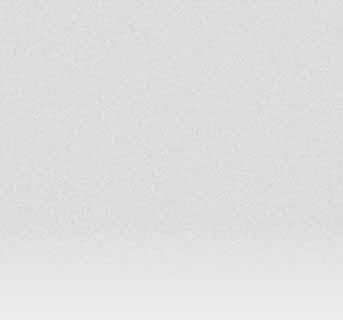
JF – cloth
GX – blended cloth
J – cloth
XF – cloth
X – cloth
Y – polyester
Z – polyester light, highly flexible surface finishing (hand and machine) surface finishing (hand and machine) surface grinding and sanding (machine) surface grinding and sanding (machine) surface grinding and sanding (machine) high profiled workpieces (hand and machine) light, flexible profiled workpieces (machine) light, flexible profiled workpieces (hand and machine) heavy, flexible hand tool belt grinder heavy, firm heavy, highly firm surface and edge grinding and sanding (hand and machine) surface and edge grinding and sanding (machine) heavy, highly firm, can be segmented surface grinding (machine)
Film polyester film finishing
Fibre vulcanised fibre grinding and finishing
2. Base coat
In the base coat step the grit is anchored. The basic bond is the connection between the grit and the backing. It is primarily formed using resin, this provides it with its consistent high quality properties. Glue is only added to a few abrasive papers that are used with hand operated machines and applications.
3. Grit
Grit is responsible for stock removal. When selecting the correct grit two properties are particularly important:
Bond
Toughness
All Klingspor grit types are produced synthetically. This ensures a consistently high quality product. Four different grit types are used with coated abrasives:
Silicon carbide
Aluminium oxide
Zirconia alumina
Ceramic aluminium oxide
Hardness
Zirconia alumina
Super alloys
Chipboard
Composite materials
Toughness
Grit classification in relation to bond, toughness and their primary applications
Coated abrasives Applications guide
Silicon carbide (SiC) very hard / less tough crystalline sharp-edged, brittle, highly friable / micro-wear
Aluminium oxide hard / tough crystalline, irregular wedge-shaped, block grain, even wear
Zirconia alumina hard / very tough crystalline, even wedge-shaped, block grain / micro-wear, self-sharpening
Ceramic aluminium oxide hard / very tough micro-crystalline
Grit type properties and their specific wear properties sharp-edged, pointed grit / micro-wear, self-sharpening
Definition Description
Close coating The entire surface of the backing is coated with grit Semi-open coating Approx. 75% of the backing surface is coated with grit Open coating Approx. 50% of the backing surface is coated with grit
In addition, there are also so-called grit agglomerates. This is not an independent grit type, rather it is a grit agglomeration which is comprised of many individual aluminium-oxide or SIC-grits mixed with a resin bonding agent, which together form a large grit. Agglomerates are used almost exclusively on abrasive belts.
The advantage of agglomerates is that they provide an even finish from the first use to the last. Dull grit breaks off from the agglomerate and creates space for new, sharp grit. The objective is to attain an even finish through continual stock removal and an extremely long service life.
Coating
Moreover, the coated abrasives are coated with different grit coverage densities. The term “grit density” describes the grit coverage density distributed on the backing.
One differentiates between: close coating semi-open coating open coating
Open coated grit has a large space between the individual grits, such that the stock removal and the grinding dust can be extracted more easily from the grinding surface. This prevents premature clogging when working on long-chipping materials, such as wood.
The decision as to which grit density to use is primarily dependent upon how great the likelihood is that the grinding dust will clog the space between the grits.
Coated abrasives Applications guide
Grit size chart
4. Size coat
The size coat supports the base coat in the anchoring of the grit on the backing and against forces which affect the grit during grinding. The cover bonds are produced exclusively from resin and also provide the product with its typical colour (exceptions are coated abrasives with additional coatings).
5. Special coatings
Special coatings with grinding aids provide the grinding tool properties that positively affect the grinding process and extends the service life of the coated abrasive. Special coatings are applied as an additional layer.
Stearate coating
The stearate on a coated abrasive prevents the clogging and loading of the belt and is specifically suited for high quality varnish surface applications. Paints, varnishes and plastics can become so and sticky through the heat generated from grinding, this can result in the premature clogging and loading of the belt. The dust clogs the space between the grits and this can result in additional “negative bond“. This clogs the grits and the sharp edges are no longer effective. To prevent this from happening or to slow the process down, the coated abrasives can be coated with a non-stick material, so-called stearates.
Multibond
The multibond, like the stearate coating, is applied in an additional production step to the cover bond layer. This allows the cool grinding of stainless steel and high alloy steels, which in turn increases the stock removal rate and service life.
ACT – Advanced Coating Technology
Klingspor uses this technology to improve the properties of the coated abrasives. When working on metal, ACT provides significantly higher grit adhesion, e.g. for aggressive belt grinding of the edges of punched parts and castings. This significantly increases the life of the grinding belt. For belts that are used for wood and varnish sanding, ACT prevents the premature clogging of the coated abrasives and significantly increases the service life.
Antistatic
Electrode migration is the result of friction i.e. grinding between different materials, and in turn causes charge separation, which in the case of non-conductive materials, such as wood, results in the load differences not being balanced. In these cases, the coated abrasive is equipped with antistatic properties that ground the electrical charge through the coated abrasive and the machine. This prevents the grinding dust from adhering to the workpiece, belt and machine.